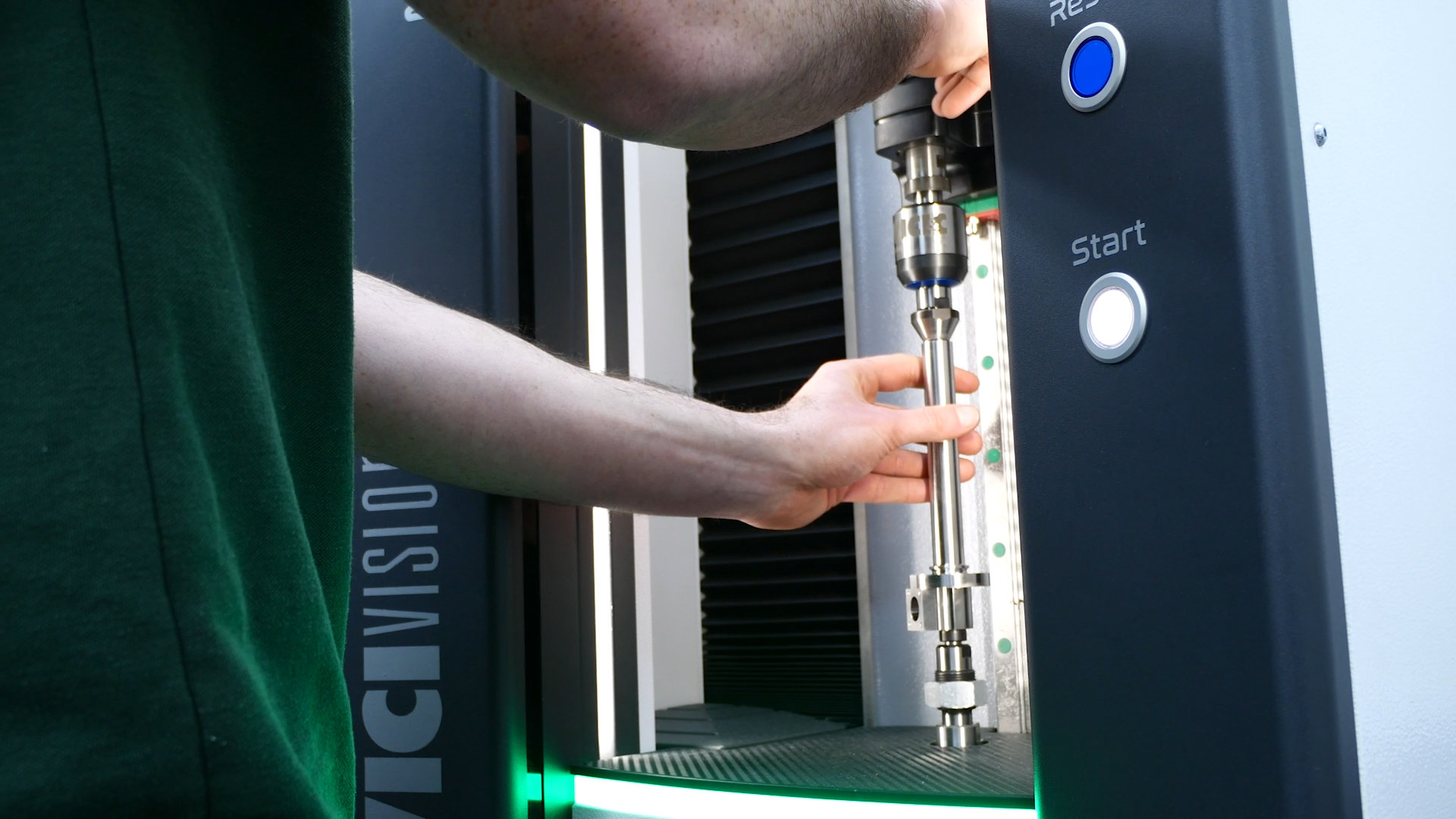
As a global supplier of complex components and assemblies to the aerospace sector, Benham Precision Engineering knows the meaning of quality. Its machining centres create parts such as manifolds, bodies, castings and casings – products that are critical to safety.
Based across the company’s two sites in Southampton, a team of engineers and an impressive technology suite is clear evidence of Benham’s ethos of continual improvement. That dedication has been a driving force behind the continued success. It has also played a major role in the decision to invest in the inspection side of its operations in recent years. It is the owner of three optical, non-contact measurement systems supplied by VICIVISION UK which, according to Programme Manager Joe Benham, has taken Benham’s metrology capabilities to a whole new level.
He said: “Speed, repeatability and accuracy were three things we are looking for. Obviously, on-time delivery is absolutely essential, as well as the quality of the parts. We need to make sure that our customers can satisfy their demand requirements, but also maintaining the fact that a lot of our product is critical to flight safety and therefore the quality needs to be absolutely 100%.”
“What VICIVISION has provided is a reliable, repeatable, accurate measurement solution. We work down to sub 10-micron tolerances and we’re able to reliably repeat those processes using the equipment around us and the technology to verify what we’re doing. The VICIVISION machines have become evident as tools for reducing different methods of verification. Previously we would be utilising micrometers, height gauges and shadowgraphs to check components, now we’re capturing all of that within a minute on a VICIVISION machine. It’s completely revolutionised the way we inspect parts.”
VICIVISION’s optical measuring solutions cater for turned, ground and cylindrical parts. Using a combination of video camera technology and light projection to automatically deliver fast, detailed and consistent results independent of the operator. Whether it’s diameters, angles, orthogonalities or thread pitches, coaxialities, cylindricities, axial runouts or dynamic parallelisms, the most complex features can be inspected in seconds.
Having initially installed an MTL1, Benham now also runs two systems from VICIVISION’s Techno range. The wide measuring fields, impressive load capacities, high-resolution and intuitive software make the M306 and M309 suited to both current and future manufacturing demands.
The improvements they can contribute to a significant reduction in rejects and rework, immediately increasing throughput and positively impacting profitability. Mr Benham said: “The benefits were immediate. We could see from the first moment that we utilised the VICIVISION machine that the rate we were inspecting work increased.
“We’ve seen reduced lead times, which has given us an advantage over other businesses within the sector in terms of enabling us to get the products to our customers quickly and efficiently. Going forward, we are looking to use the ProLink software in conjunction with the VICIVISION systems, so that we have real-time data for the operators at their work stations.”
Based at its Innovation Centre in Derbyshire, VICIVISION UK has a team of engineers with a knowledge of the full hardware and software range. By offering installation, calibration, fixturing solutions, programme creation, applications support and bespoke training, its turnkey packages make for smooth project set-ups so that customers will start reaping the advantages of optical measurement from day one. Mr Benham added: “The future looks very promising for Benham as we continue to invest in technology, people and processes. We want to very much focus on productivity through technology. We believe the use of optical measurement equipment to assist in that will be key. Having seen the capability of the VICIVISION equipment we knew it was a sound investment for Benham and we knew that the investment would be paid back. It’s enabled the business to move forward and up another level.”