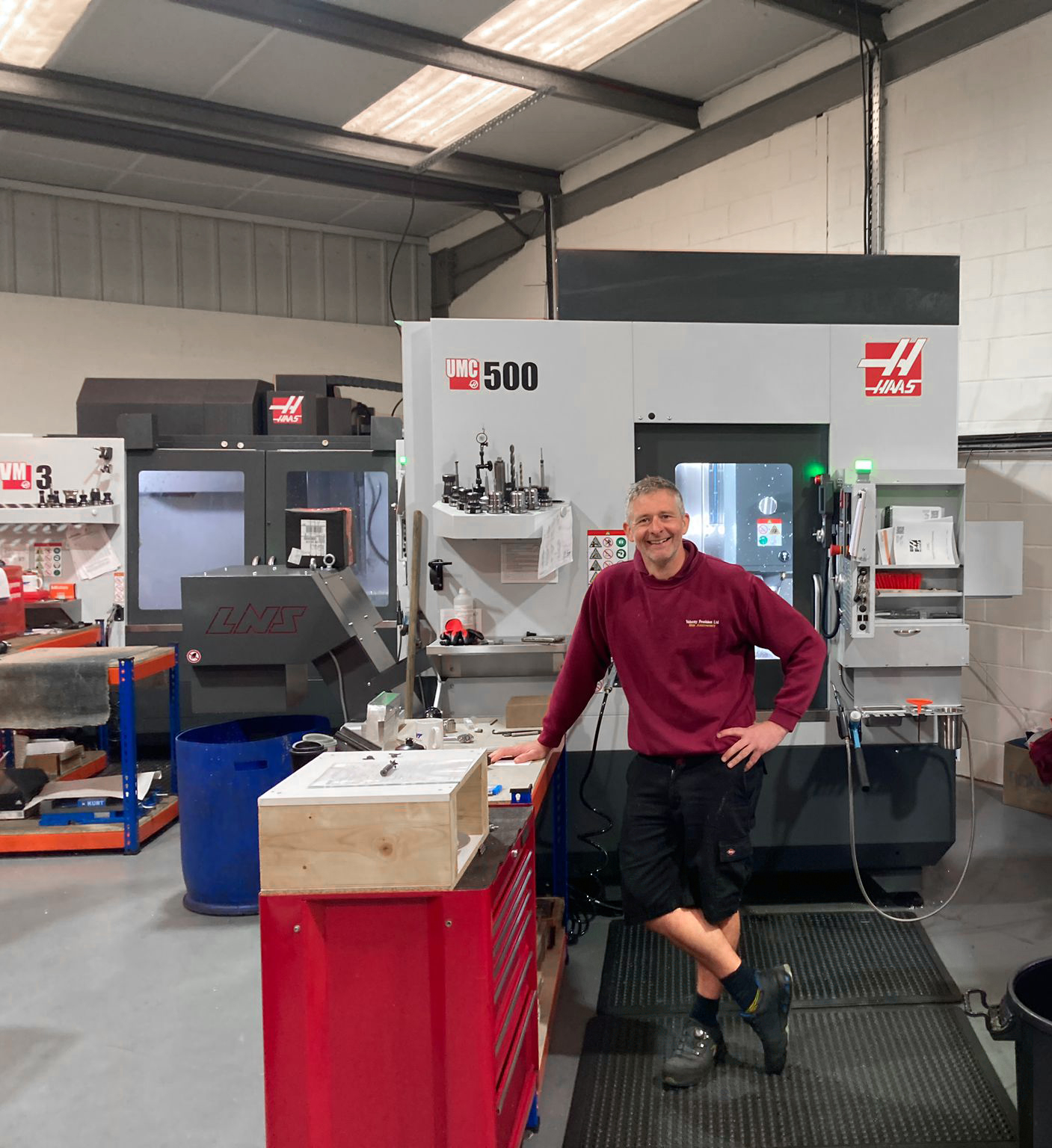
Located in the scientific hub of Cambridgeshire, Velocity Precision has recently undergone significant expansion under the guidance of its founders, James Brown and Glen Dawson. With a decade of experience and the initial purchase of its first HAAS machine funded by personal loans, the company has now grown to a team of 15 and has effectively doubled the size of its premises.
Specialising in prototyping for the high-tech and scientific industries, James and Glen work closely with design consultancy companies taking CAD drawings to the finished product. The pair were working together at a local company when they decided to set up their own business. “We wanted the independence to make our own decisions and to progress our careers. We had both worked on HAAS CNC machines previously, so we knew them to be dependable and user-friendly. HAAS was the obvious choice for us and our first machine purchase was a Mini Mill,” explains James.
Velocity Precision has a state-of-the-art facility and a focus on precision and innovation. This enables them to meet the needs of their clients with high-quality, dependable results.
“Our customer base is increasing, so we have been investing in more machines,” James stated. They began with their original Mini Mill and progressed to a HAAS VF-2 VMC, followed by a Super Speed VMC with a 12,000rpm spindle. They also installed two HAAS lathes, to make use of Glen’s turning expertise. Additionally, 4-axis rotary tables and 5-axis trunnion units have been added, and the latest acquisition, a HAAS UMC-500, uses the skills honed on their existing machines to gain the full potential from the machine’s 15,000rpm spindle, full 5-axis capability and 30-station side mount tool changer.
“Our first step into 5-axis machining was with the HAAS TRT160 trunnion. The impressive surface finish and increased speed it gave us translated into more enquires for that kind of work. We can use high feed rates on 3D machining and the speed is phenomenal; we can do so much more in one operation. Word gets around quickly, and we’re winning quotes simply by owning the machine. The footprint is the same as our VF-2, a small mill, so it takes up very little space for the parts it produces.”
HAAS’ Tool Centre Point Control (TCPC) and probing capabilities are powerful tools that enhance precision and efficiency in machining. TCPC allows the machine to precisely locate the centre of rotation for rotary axes, which is crucial for accurate 5-axis machining. Meanwhile, probing enables the machine to quickly and accurately measure workpieces, tool lengths, and even detect broken tools, all without manual intervention. By automating these processes, HAAS machines can achieve greater precision and speed, reducing setup times and minimising errors.
Velocity Precision’s prototyping services encompass a wide range of applications, from the development of specialised robots that can spray insulation under floorboards to the production of a torsion bar for the new Ford GT. “We made the prototype bar and the customer was so impressed they have just signed a massive contract. Being able to offer 5-axis machining has allowed us to win that business,” explains Glen.
“HAAS have always made machines which are easy to use; the controls are universal so moving from one to another is a breeze – even from mill to lathe. The bed is just the right height and the windows let in a lot of light. Now with the Next Gen control, they’ve gone to the next level. The increased memory means more programs can be stored and we can create directories now, which keeps everything tidy. We can keep all our regularly used programs on the machine, even for 3D parts. It’s like storage on a computer in that respect. We use the VM-3 for the highest tolerance work because it has the tightest ballscrew pitch. We’re machining up to 0.001mm.” The VM-3 vertical mould maker has a generous work envelope, a multi-fixturing table and a 12,000rpm inline direct-drive spindle.