CERATIZIT enhance precision at NDT
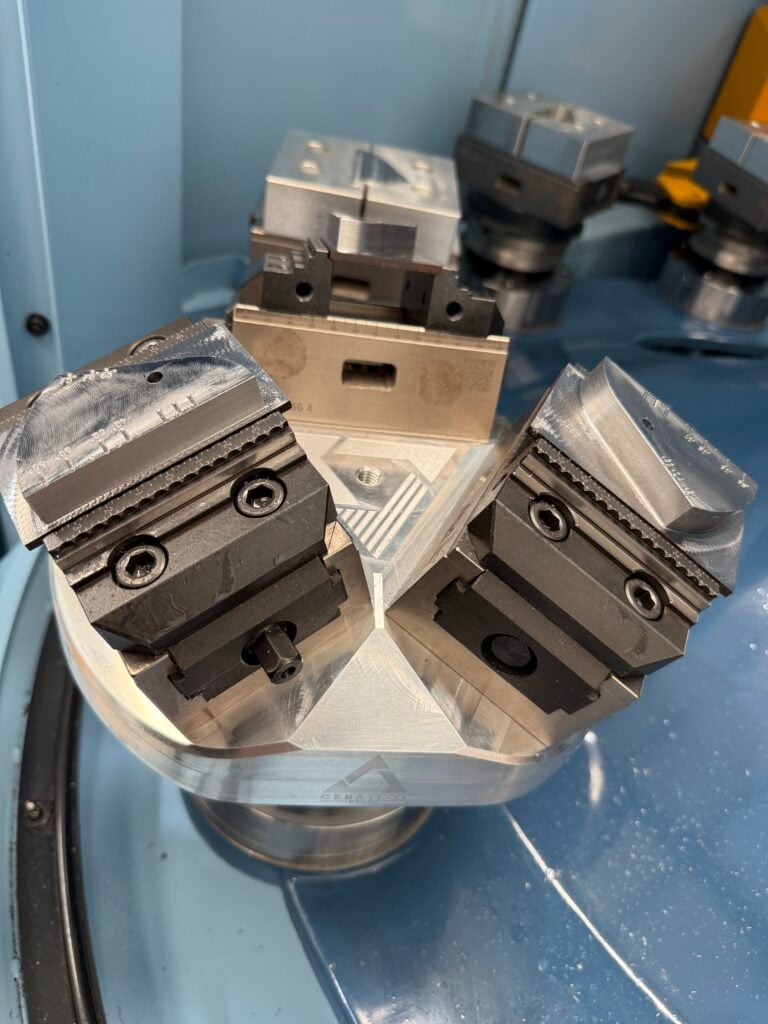
In the precision-driven world of non-destructive testing (NDT) manufacturing, selecting the right tooling and workholding solutions is crucial for ensuring product quality. NDT Equipment Ltd, a Northamptonshire specialist in manufacturing NDT calibration blocks and test pieces, has earned its reputation by delivering high-precision components with tolerances as tight as ±0.005mm. At the heart of their production capabilities is a strategic partnership with CERATIZIT, whose cutting-edge tooling solutions have been essential to NDT Equipment’s manufacturing excellence.
NDT Equipment Ltd specialises in producing ultrasonic calibration blocks and reference pieces that comply with international standards such as ISO 2400:2012, ISO:7963:2010, and ISO:16946:2017. These precision components are vital for non-destructive testing applications in various industries, including oil and gas, nuclear, aerospace, and automotive.
Non-destructive testing is a critical quality control methodology used to evaluate material integrity without causing damage. From ensuring that bridge components withstand structural forces to verifying that aircraft parts meet stringent safety requirements, NDT techniques provide necessary validation that can prevent catastrophic failures. Even in the food industry, NDT methods help identify potential metallic or glass contaminants during processing.
The calibration blocks manufactured by NDT Equipment Ltd serve as reference standards for NDT equipment, ensuring accurate and reliable testing results. These components boast precise dimensions, surface finishes, and material properties that must meet exacting specifications, making the manufacturing process particularly challenging.

To address these challenges, NDT Equipment Ltd, based in Long Buckby, maintains a modern CNC machining facility equipped with 3 to 5-axis machining, CNC surface grinding, EDM machining, and CMM inspection with technology from brands like Doosan, XYZ, and a Matsuura MX-330 with a 10-pallet loading system. This advanced equipment enables the company to manage everything from prototypes to medium and large batch production across various materials, from standard mild steel to specialised alloys like Inconel.
CERATIZIT Partnership: A Cornerstone of Quality
A key factor in NDT Equipment’s ability to uphold quality standards is its partnership with CERATIZIT for tooling and workholding solutions. The company relies heavily on CERATIZIT products throughout its manufacturing processes, and its production team has highlighted several specific benefits.
NDT Equipment utilises CERATIZIT vices and workholding systems on their machining centres, significantly streamlining setup procedures. The company specifically alludes to the benefits of the zero-point clamping system with centralised plates, which allows for quick and precise attachment of vices without requiring constant datum setting or alignment.
Director at NDT Equipment Ltd, Daniel Lenton, remarks: “We have a three-pot Centro system from CERATIZIT that makes it easy to attach vices without the need for constant datums, alignment, or setup. The system ensures the parts lock in place and align perfectly. This standardisation guarantees consistency across different machines and simplifies job transitions from one machine to another, reducing setup times and potential errors.”
“The precision alignment capabilities of the CERATIZIT workholding solutions also support our collision checking requirements, ensuring that our CAM programming accurately reflects the physical setup on the machine. This minimises the risk of costly crashes and maintains consistency in our manufacturing processes.”
Comprehensive Tooling Ecosystem
In addition to benefiting from CERATIZIT’s zero-point workholding technology, NDT Equipment has standardised nearly all of its cutting tools around CERATIZIT products. The extensive range of tooling solutions meets the diverse machining needs for the various materials and geometries involved in manufacturing NDT calibration blocks.
Exceptional Supply Chain Support
One of the most significant advantages of partnering with CERATIZIT is the robust supply chain support. NDT Equipment has implemented a CERATIZIT TOM vending machine system in its facility, allowing immediate access to commonly used tools. This just-in-time inventory system ensures that production is never interrupted due to tooling shortages.
Referring to this, Daniel adds: “With CERATIZIT, the supply chain is so good that we have one of their vending machines on site. If we need a tool, we can access it right away. When it comes to exotic materials and we don’t have the right tool in the vending machine, we know we can get it the very next day. CERATIZIT has even delivered from Sheffield on the same day for us. That’s where you’re only as good as your supply chain, and their supply chain is so reliable that we’re never really without.”
This reliability enables NDT Equipment to commit to demanding delivery schedules while maintaining its high-quality standards. “We use all the CERATIZIT turning inserts and holders; their EcoCut series is excellent. I love their EcoCut. You don’t need to drill parts at all – you can send in an EcoCut multifunction turning and drilling tool and continue boring the hole out. All our tooling, except for one or two select items, is supplied by CERATIZIT – all of their tooling fits our needs.”
NDT Equipment’s commitment to quality is reinforced by its ISO 9001:2015 quality assurance system. Every product manufactured by the company is delivered with full traceability and certification documentation, providing customers with confidence in the conformity and performance of the NDT calibration blocks. The precision and consistency delivered by CERATIZIT tooling solutions are essential for enabling NDT Equipment to achieve the tight tolerances and surface finishes required for their products.
The partnership between NDT Equipment Ltd and CERATIZIT exemplifies how advanced tooling solutions can empower precision manufacturers to deliver exceptional quality while maintaining operational efficiency. For NDT Equipment, CERATIZIT’s comprehensive tooling ecosystem, superior workholding solutions, and responsive supply chain support have become integral to their manufacturing success.
Optimising aerospace machining with Fuchs lubricants at ESL
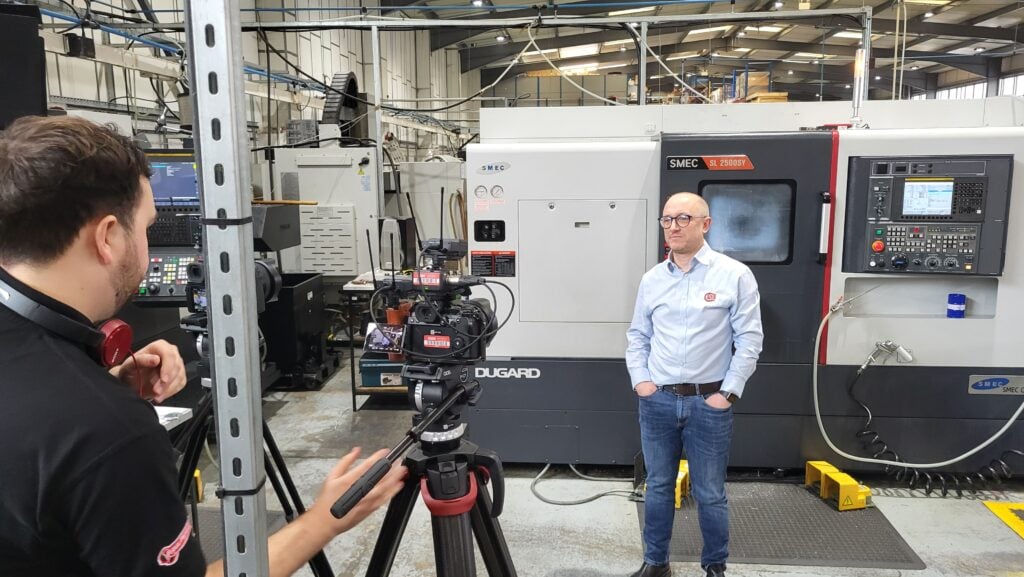
ESL Engineers Ltd is an AS: 9100 and ISO: 9001 accredited aerospace engineering company based in the UK, specialising in the production of critical components for major platforms like Eurofighter, Airbus, and BAE Systems. With over 60 advanced CNC machines, the company machines over 375 aerospace component types annually, leveraging its core capabilities in mill/turn, turning, milling, and gear cutting.
To maintain its stringent quality standards and meet the demanding requirements of the aerospace industry, Basildon-based ESL previously relied on a variety of coolant and lubricant products from different suppliers. However, the company recognised the need for a more streamlined and optimised fluid management strategy. “We had all different types of products, coolant, lubricant products, in the machine shop with different aerospace approvals,” explained Darren Perry from ESL. “We were looking for one supplier, one coolant source, one product.”
Seeking a Comprehensive
Fluid Management Solution
ESL’s search for a single, high-performance fluid supplier led them to Fuchs Lubricants, a leader in the development and manufacture of specialised lubricants and fluids. “We reached out to Darren at ESL,” said Ryan McCoy, a Territory Sales Manager at Fuchs. “We had conducted some previous work with them in the past with some older formulation technology, but I reached out to Darren when our new product Eco Core Globe 1000 got all the relevant accreditations for the Airbus specifications.”
The Eco Core Globe 1000 is a cutting-edge metalworking fluid that combines advanced lubrication technology with comprehensive environmental and safety credentials. “The main reason for choosing Eco Core Globe 1000 is obviously to do with the aerospace accreditations,” explained Ryan. “We needed to make sure that we adhered to the Airbus specification that they were looking for. ESL does much work with Airbus, so we need to make sure that the product that we supplied has the relevant accreditations, and also it provides them with a performance benefit as well.”
Rigorous Product
Evaluation and Approval
To ensure the Eco Core Globe 1000 met ESL’s exacting standards, Fuchs proposed a comprehensive 12-week trial period. “We then provide a barrel, initially on an FOC purposes for the trial,” said Ryan. “Run that on a course for 12 weeks where we’d come to the site once per week, we manage the concentration, the pH, the bacteria and the temperature control, ensuring that we take a 100ml sample each week, and send it to our labs to check the chemical makeup of the product and ensure that it’s sustainable.”
The successful trial of the Eco Core Globe 1000 at ESL’s facility yielded impressive results, with the company experiencing significant improvements in productivity and tool life. “The outcome of the trial was very successful,” Darren noted.
“It gave us a very high performance and lubricity with a tool life increase. We produce about 100 Airbus components weekly, and we were finding every day, we were getting another component from our tool life using the Fuchs products.” The enhanced lubricity and performance of the Eco Core Globe 1000 played a crucial role in these productivity gains. “The main reason for choosing Eco Core Globe 1000 is obviously to do with the aerospace accreditations,” explained Ryan. “We needed to make sure that we adhered to the Airbus specification that they were looking for.”
“ESL does a lot of work with Airbus, so we need to make sure that the product that we supplied has the relevant accreditations and also provides a performance benefit as well.”
Addressing Modern Challenges
The Eco Core Globe 1000 not only delivers superior performance and productivity benefits, but it also addresses the growing emphasis on environmental sustainability and worker safety in the aerospace industry. “It’s a high-performance product with great lubricity, which produces excellent tool life and ticks the boxes as a modern technology, health and safety, environmental product,” Darren explained.
The product’s advanced formulation and comprehensive approvals ensure that it meets the latest environmental and safety regulations while also providing the high-level performance required for critical aerospace components. “We needed to make sure that we adhered to the Airbus specification that they were looking for,” said Ryan. “ESL does a lot of work with Airbus, so we need to make sure that the product that we supplied has the relevant accreditations, and also it provides them with a performance benefit as well.”
Navigating challenges with precision and innovation
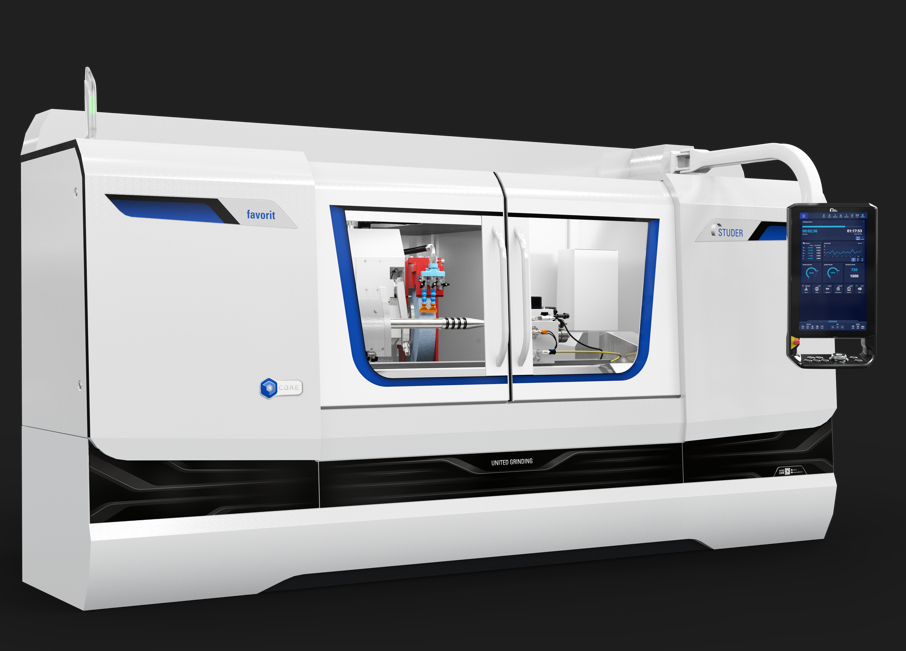
The global economic environment of 2024 presented unprecedented challenges for industrial manufacturers, yet Studer emerged not only as a survivor but also as a strategic innovator. At this year’s press conference, Studer once again delivered an insightful overview of the company’s performance and innovations. Always a highlight in the calendar for the trade media, the 2025 event was hosted online as opposed to a trip to the picturesque Steffisburg municipality of Switzerland – but the insights were no less impressive. By Rhys Williams
Outgoing CEO Jens Blaher set the tone for the annual press conference with a candid and compelling narrative of organisational resilience. “During the recently concluded 2024 financial year, we effectively navigated the deteriorating economic and geopolitical landscape,” he explained, his words resonating with a deep understanding of the complex challenges facing modern industrial enterprises.
Studer’s approach to these challenges was fundamentally different from that of many competitors. Rather than retreating or dramatically scaling back, the company embraced a strategy of diversification and targeted growth. Blaher emphasised this point by highlighting how the company’s multifaceted approach allowed it to grow in select markets, transforming potential obstacles into opportunities for expansion and innovation.
The company’s performance was nuanced and strategically calibrated. While incoming orders were slightly below the previous year, they precisely aligned with Studer’s carefully planned expectations. Geographically, the company maintained a robust presence, with Asia remaining its largest sales region and North America showing significant growth. Approximately 50% of incoming orders were generated outside Europe, underscoring the company’s global reach.
A remarkable highlight was the 43% increase in new customer acquisition, with strength in key sectors, including automotive and the respective supply chain industries, as well as tool and die manufacturing, the machine tool industry and aerospace manufacturing.
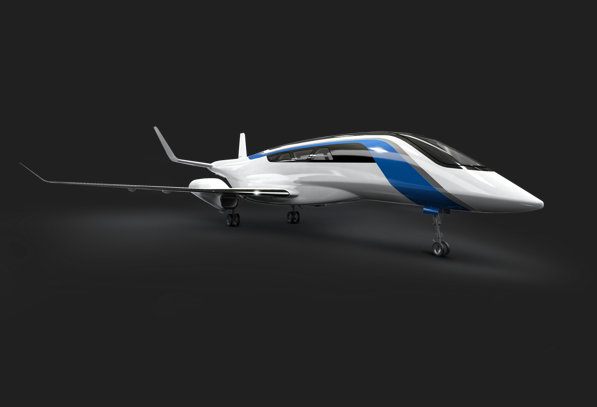
The New favoritCNC
At the heart of Studer’s 2024 innovations was the advanced favoritCNC universal cylindrical grinding machine, representing a significant leap in grinding technology. The machine integrates the latest FANUC 0i-TFP control system with a sophisticated engineering approach that demonstrates the company’s commitment to precision and user accessibility.
Technical specifications reveal a meticulously designed piece of equipment. The machine offers flexible wheelhead configurations, including a fixed wheelhead with manual positioning at 0°, 15°, and 30° and a universal wheelhead with a 2.5° Hirth coupling for seamless internal and external grinding capabilities. Its foundation is constructed from Granitan® S103 mineral casting, a proprietary material that provides exceptional thermal stability and vibration damping.
The machine’s physical capabilities are equally impressive. It can accommodate centre distances of 650mm or 1m, handle workpiece weights between 80 and 120kg, and accept grinding wheels up to 500mm in diameter. Perhaps most innovative is the machine’s intuitive StuderPictogramming and StuderGRIND grinding software, which provide modern digital solutions that allow even complex grinding processes to be set up and controlled intuitively.
Commenting on the machine, Sandro Bottazzo, the new CEO at Studer, said: “With numerous new features, optimisations, and automation capabilities, the favoritCNC is a future-oriented, economical solution for the external and internal cylindrical grinding of small to medium-sized workpieces in individual and series production. Both for high-quality contract manufacturing and in-house production and with the conventional mode, the new favoritCNC is an optimal solution for a wide range of different grinding applications.”
Pushing the Boundaries of Precision
Beyond the favoritCNC, Studer introduced several groundbreaking technological innovations that underscore its position at the forefront of precision engineering. The Universal W-axis represents a quantum leap in grinding technology, integrating directly onto the Z-slide to enable automatic machining of different workpiece lengths without operator intervention. The axis’s most revolutionary feature is its direct force measurement capability, which allows for a force-controlled clamping process that delivers maximum precision and repeatability.
Aerospace Industry: A Proving Ground for Innovation
The aerospace industry serves as a critical proving ground for Studer’s technological capabilities. Modern aviation demands extraordinary precision, with components requiring micron-level accuracy and the ability to withstand extreme conditions. Studer’s machines play a crucial role, with the S31 and S33 CNC universal cylindrical grinding machines capable of grinding landing gear components to microns.
Martin Hofmann, Studer’s Sales Director for North America and aerospace specialist, emphasises that the company’s focus remains on supporting human expertise. Hofmann explains that the entire industry is currently experiencing an increasing trend towards better materials, optimised aerodynamics, sensor technology and data analysis for more efficient engines. “We are therefore supporting our customers with innovative production technologies to be even more successful.”
The SmartJet® coolant concept demonstrates STUDER’s commitment to sustainable manufacturing. This advanced system reduces coolant consumption by up to 40% and energy utilisation by 50% compared to conventional methods. Its expanded application range includes sophisticated optimisations for thread grinding and innovative plug-in coolant nozzles designed for various grinding wheel profiles.
Another breakthrough is the WireDress® dressing process, explicitly developed for metal-bonded CBN and diamond grinding wheels. In 2024, Studer extended this non-contact dressing system to internal grinding wheel applications.
Hofmann also sees the future-proof C.O.R.E. hardware and software architecture and intelligent Studer software with comprehensive digital capabilities as a significant advantage of the new generation of Studer cylindrical grinding machines. This includes intuitive operation, process and data visualisation as well as standardised or customised automation systems. “Our focus is always on people; technology should support them,” he explains.
Operational Excellence and Sustainability
Studer’s 2024 strategy extended beyond technological innovation to encompass operational efficiency and sustainability. The company implemented comprehensive improvements, including the consolidation of spindle assembly locations, advanced testing and diagnostic systems, and a complete renewal of internal electrical pre-assembly.
Sustainability initiatives were equally impressive. The company converted extensively to LED lighting, replaced operational systems with energy-efficient devices, and designed a new logistics facility aimed at reducing energy consumption. Ongoing digitalisation projects across operations further demonstrate Studer’s commitment to efficiency and environmental responsibility.
A Commitment to Excellence
Studer’s 2024 journey represents a masterful blend of technological innovation, market adaptability, and strategic foresight. By investing in advanced technologies, expanding customer care, and maintaining a forward-looking digital strategy, the company has not just weathered global challenges but positioned itself for continued growth in the precision engineering market.
As Jens Bleher aptly summarised: “Know-how and commitment are the future of a technology company”—a philosophy that continues to drive Studer’s remarkable journey of innovation and excellence: novation and excellence.
Revolutionising machining efficiency with fast feed tools

In the dynamic world of machining, efficiency and precision are paramount. Most of the machining allowance is removed during rough cuts. Therefore, increasing productivity at this stage is crucial for reducing the machining costs of the entire manufacturing process. Even with improved capabilities in precise forging, die-casting, injection moulding, and other workpiece production methods that allow for obtaining a workpiece very close to the part’s final shape, a high metal removal rate during rough cutting continues to be an important factor in reducing total costs.
ISCAR has consistently pushed the boundaries to provide solutions that meet the ever-evolving demands of manufacturing. One of ISCAR’s standout innovations is the Fast Feed line of tools designed to enhance productivity while maintaining exceptional precision.
Fast Feed tools by ISCAR are designed to operate at high feed rates, significantly reducing machining time and increasing productivity. The concept hinges on the principle of shallow depth of cut combined with high feed, allowing for rapid material removal without compromising surface finish or tool life. This approach is particularly beneficial in roughing operations, where the primary goal is to remove as much material as possible in the shortest time.
ISCAR’s Fast Feed tools are engineered with advanced geometries that optimise chip evacuation and reduce cutting forces. This results in less wear and tear on both the tool and the machine, extending their lifespan. The Fast Feed tools are suitable for a wide range of materials, including steels, stainless steels, cast irons, high-temperature superalloys (HTSA), and titanium. This versatility makes the tools an attractive option for industries such as aerospace, automotive, and mould and die, where diverse materials are often encountered.
By allowing for higher feed rates, Fast Feed tools significantly reduce machining time. This efficiency results in cost savings and increased throughput, which are essential in high-volume production environments. While primarily focused on roughing, ISCAR’s Fast Feed tools are also designed to achieve suitable surface finishes, minimising the need for secondary operations and further enhancing productivity.
The combination of advanced cutting tool materials, wear-resistant coatings, and optimised geometries ensure that Fast Feed tools have a long tool life, even under the demanding conditions of high-speed machining.
Fast Feed tools are making significant impacts across various industries. In aerospace, where difficult-to-cut materials like titanium and HTSA are common, these tools help address the challenges of machining tough materials. In the automotive sector, they enable manufacturers to meet the fast-paced production demands while maintaining high quality. The mould and die industry also benefits from reduced machining times and improved surface finishes, which are crucial for producing complex shapes with high precision.
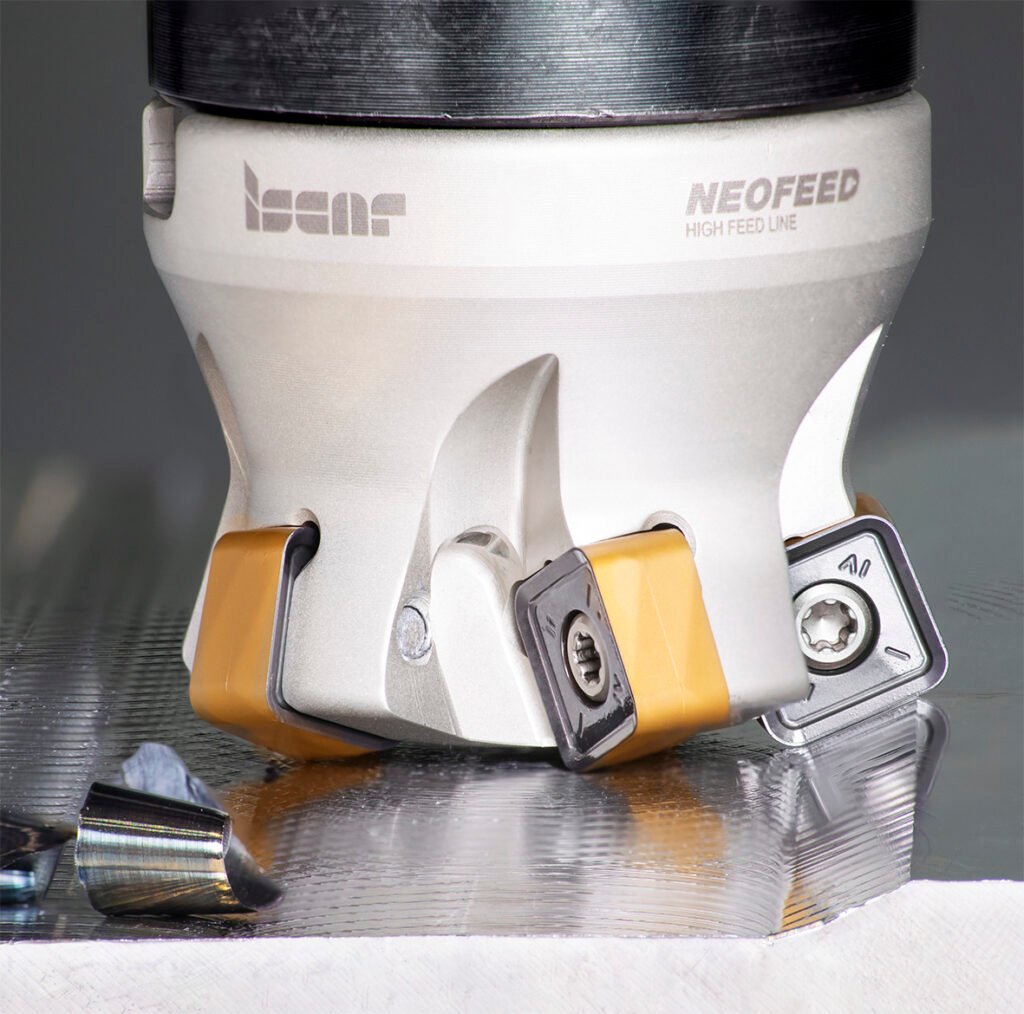
ISCAR offers a comprehensive selection of advanced cutting tools, including fast-feed turning and grooving tools. These tools are designed to enhance productivity, efficiency, and precision in various machining operations.
Fast Feed Turning Tools (Fig.1)
l High Feed Rates: These tools enable increased feed rates, thereby reducing machining cycle times.
l Durable Materials: Constructed from high-quality materials to withstand high-speed machining conditions.
l Precision Cutting: Engineered for accuracy, ensuring precise cuts with minimal tool wear.
l Versatility: Suitable for a variety of materials and applications, offering great flexibility.
Fast Feed Grooving and Parting Tools (Fig.2)
l High-Speed Performance: Designed to perform at high speeds, improving the overall efficiency of grooving operations.
l Reduced Cycle Times: High feed capabilities allow for quicker material removal, reducing overall cycle times.
l Enhanced Tool Life: Made from durable materials that extend the life of the tool, even under demanding conditions.
l Consistent Quality: Ensures consistent performance and high-quality results in various grooving applications.
ISCAR also provides an extensive range of fast feed milling tools designed to significantly increase efficiency and productivity. These tools are specifically engineered to deliver high material removal rates and reduce cycle times in various milling operations. Fast feed (FF) milling cutters are a key factor in high feed milling (HFM) techniques. The cutter geometry, designed for efficient chip thinning, must ensure the correct distribution of the cutting force.
There are two principal geometrical approaches. The first design requires the cutting edge of an FF milling cutter to be an arc of a circle. Another concept is based on using one or two straight edges that are chords of the arc. In both cases, the small cutting edge angle (usually 9-17°) meets the requirements of chip thinning and decreasing the total bending load on a tool.
Ensuring the geometry of solid carbide fast feed endmills and replaceable milling heads demands the specific shape of a cutting edge, while in indexable milling, it may be provided by the appropriate location of an insert of even a simple profile.
Although the introduction of innovative grades and advances in chip forming rake faces have improved progress in FF milling cutters, the essential element, the geometry, remains constant. If the cutting edge of an FF milling cutter is the arc of a circle (or the chords that approximate the arc), the cutting edge angle of the cutter is not a constant value but varies depending on the axial depth of cut from 0 to the mentioned 9-17°. In milling, the chip thickness is a function of the tool’s cutting edge angle. Under the same conditions, the smaller the cutting edge angle, the thinner the chip. Therefore, the programmed feed should be increased correspondingly to produce chips of the required thickness.
Features of ISCAR Fast Feed Milling Tools (fig.3)
l High Feed Rates: These tools are designed to operate at high feed rates, allowing for faster machining processes and reduced cycle times.
l Durable Structure: Made from high-quality materials that ensure durability and long tool life, even under demanding conditions.
l Precision and Stability: It is engineered to provide precise and stable cuts, minimise tool wear, and improve the quality of the finished product.
l Versatile Applications: It is suitable for a wide range of materials and applications and offers great flexibility in use.
l Innovative Design: It incorporates advanced geometries and coatings to enhance performance and chip evacuation, reduce heat generation, and increase tool life.
Popular Product Families
l HELI-6-FEED: Known for its double-sided indexable inserts, offering high feed rates and excellent performance in various milling applications.
l NEOFEED: Specifically designed for high feed milling, these tools carry cost-beneficial double-sided square inserts with 8 indexable cutting edges, providing outstanding material removal rates.
l MULTI-MASTER: This modular system with interchangeable heads allows for quick and easy tool changes, enhancing productivity and reducing downtime.
ISCAR’s Fast Feed tools exemplify the company’s commitment to providing innovative solutions that address the real-world challenges faced by manufacturers. ISCAR’s Fast Feed tools are a testament to the company’s forward-thinking approach and dedication to enhancing machining efficiency. As industries continue to demand faster, more precise, and cost-effective solutions, ISCAR’s innovations in fast feed technology are set to play a pivotal role in shaping the future of manufacturing.
Efficiency forecasting is ‘key’ to OEMETA results
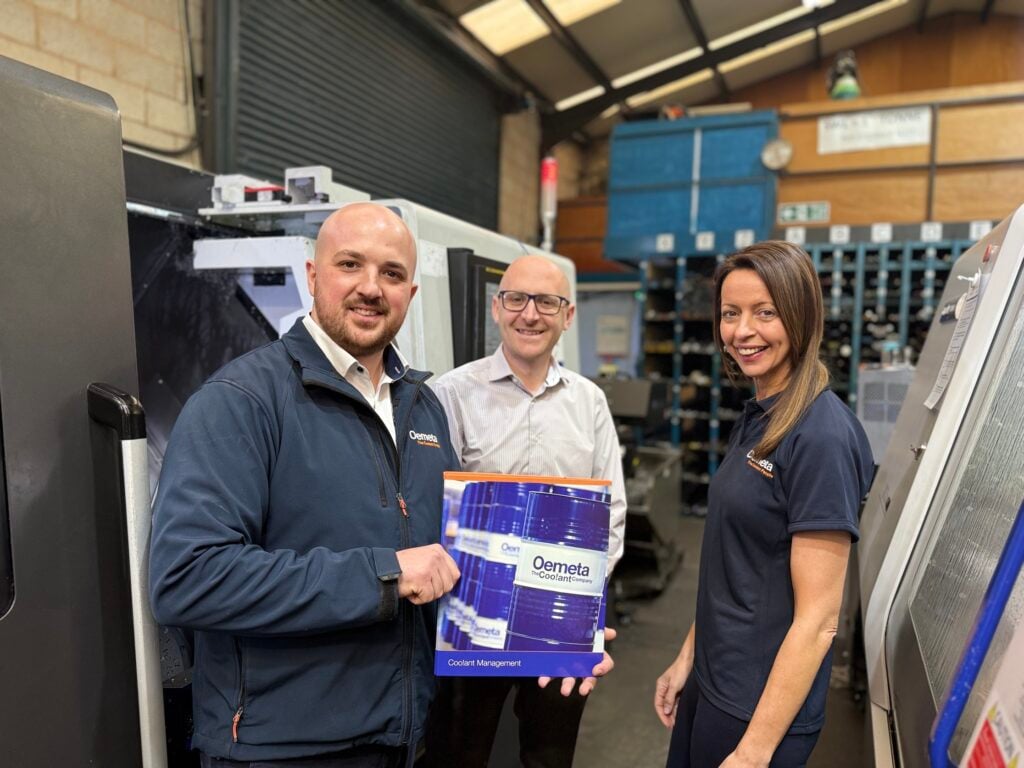
Key Precision is a subcontract manufacturer specialising in precision turned and milled components. Founded 21 years ago, the Cannock-based company focuses on driving efficiency throughout the business. Managing Director Greg Jackson identified cutting fluid performance as an issue needing attention—the solution was OEMETA’s ESTRAMET S95 coolant.
Greg says: “We have an impressive array of machines from sliding and fixed head turning to vertical machining centres.” The plant list boasts prestigious brands like Citizen, Hanwha, HAAS, DMG MORI, and Doosan.
Ryan Aviles from OEMETA explains: “Our relationship with Key Precision has been in place for years. Initially, we identified areas for improvement, and they invited us to trial.”
OEMETA’s engagement began with a consultative process where technical representatives evaluated the shop floor and collected samples for analysis. By taking fluid samples and sending them to OEMETA Germany for over 50 different tests, the process remains non-disruptive to production. The six-step process includes sample capture, performance analysis, result review, trial, product transfer and partnership. From this analysis, OEMETA yields a 95% success rate in delivering performance-enhancing solutions.
Following a consultation, OEMETA identified ESTRAMET S95 as the most viable solution. Compatible with steel, stainless and high-alloy steels, aluminium, and aerospace-grade alloys, ESTRAMET S95 serves the entire spectrum of applications, from drilling and milling to grinding.
Ryan adds: “On our first consultations we take samples, send them to Germany for analysis, and discuss results with the customer. Once we have sample results, we examine opportunities in detail. From our testing, we can benchmark against existing products and forecast benefits with confidence—before our product reaches their shop floor.”
Seismic Benefits from OEMETA
With testing covering lubricity, corrosion, stability, foaming, water quality, safety, and environmental impact, Key Precision experienced efficiency gains ranging from 35% to 150% across various operations.
Greg continues: “We’ve seen tool life improvements from 70% up to 150%. Every operation has shown a minimum improvement of 35%. For long-running jobs, U-drills saw a 77% increase. Parting-off efficiency increased by 35% and turning operations by 300%.” The extended tool performance has allowed the company to recoup its annual OEMETA fluid costs in the first month. Machine and component cleanliness and quality have also improved.
Based on synthetic ester oils, the translucent ESTRAMET S95 is free from mineral oil, boron, formaldehyde, fungicide, and active sulphur. This makes it a bio-sustainable, operator-friendly fluid. As a highly stable fluid, it has increased tool life from 20% to 50% on most machines, generating significant cost savings.
The implementation strategy incorporated a comprehensive approach, including bi-weekly site visits, laboratory testing, and compatibility assessments. OEMETA’s service model includes monthly coolant maintenance checks far beyond standard industry practices, with concentration verification, pH monitoring, microbiology testing, and tank evaluations.
Ryan explains: “We regularly revisit the site every two weeks to collect samples. With the results, we update customers on performance. Once KPIs are achieved, we start the roll-out process, taking samples from all machines to ensure compatibility with existing coolants.”
The success has prompted Key Precision to implement OEMETA across all water-based machining. Plans are also in place for oil-based solutions on sliding heads.
Ryan adds: “We’ve run tests on the sliding head machines and will deliver similar savings with our GTL (Gas To Liquid) product.”
Greg concludes: “The trial results speak for themselves. We’re committed to rolling out OEMETA fluids across our full range of machines. The results have been fantastic, and we look forward to more efficiencies and savings from working with OEMETA.”
Cutting and Wear optimises manufacturing with Dugard Ibarmia machine
Cutting and Wear Resistant Developments Ltd, a leading manufacturer of specialised downhole tools for the oil and gas industry, has undergone a transformative shift in its production capabilities after investing in an Ibarmia machine from Dugard. The company, led by Managing Director Matthew Cooper, has followed a successful growth trajectory over the past 12 years, and the introduction of this advanced CNC machine has played a pivotal role in supporting its expansion.
Cutting and Wear’s unique selling proposition lies in its ability to manufacture tools with a hard-facing aspect and integrate innovative machining processes to deliver comprehensive solutions for its customers. Prior to the arrival of the Ibarmia ZVH 45 L3000 machine, the company encountered challenges related to the complexity of its tools, lead time constraints, and the efficiency of its manufacturing methods. However, the implementation of the new machine has revolutionised their operations.
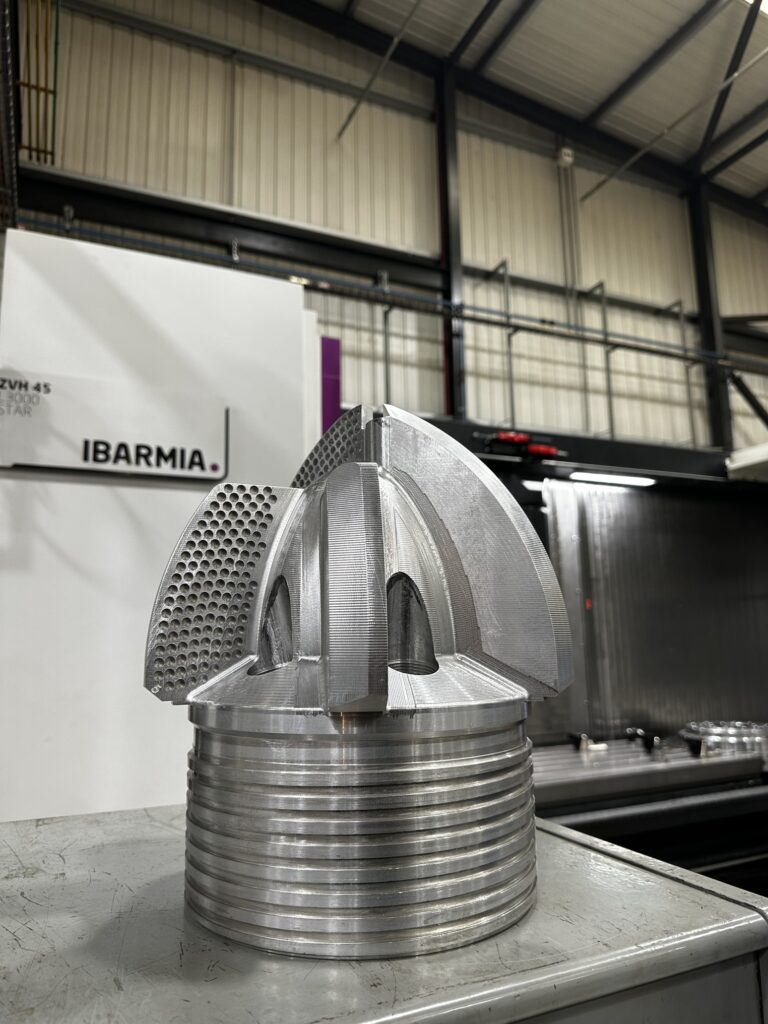
“In the 12 years I’ve been here, I’ve seen many changes, both in the company and the industry, but pleasingly, we’ve adhered to a successful growth plan, leading us to where we are today—continuing that growth and progressing in the right direction with new machine investments,” explains Matthew. The Ibarmia machine, equipped with a high-performance spindle capable of reaching speeds of up to 12,000rpm, has enabled Cutting and Wear to reduce lead times and machining times significantly.
Mark Taylor, a CNC Programmer at Cutting and Wear Ltd., highlights a remarkable example: “We had one tool that previously took us 11 hours to mill; on the new machine, it was reduced to just two hours.” That’s a massive improvement for us.” One of the standout features of the Ibarmia machine is its advanced probing capabilities. By integrating probing into the machine’s programming cycle, Cutting and Wear have eliminated the need for manual programming, further streamlining the manufacturing process. As Mark explains: “We can execute everything on the machine as it’s built into the programme, so there’s no need to remove it from the machine for inspection, and that’s a time saver as well.”
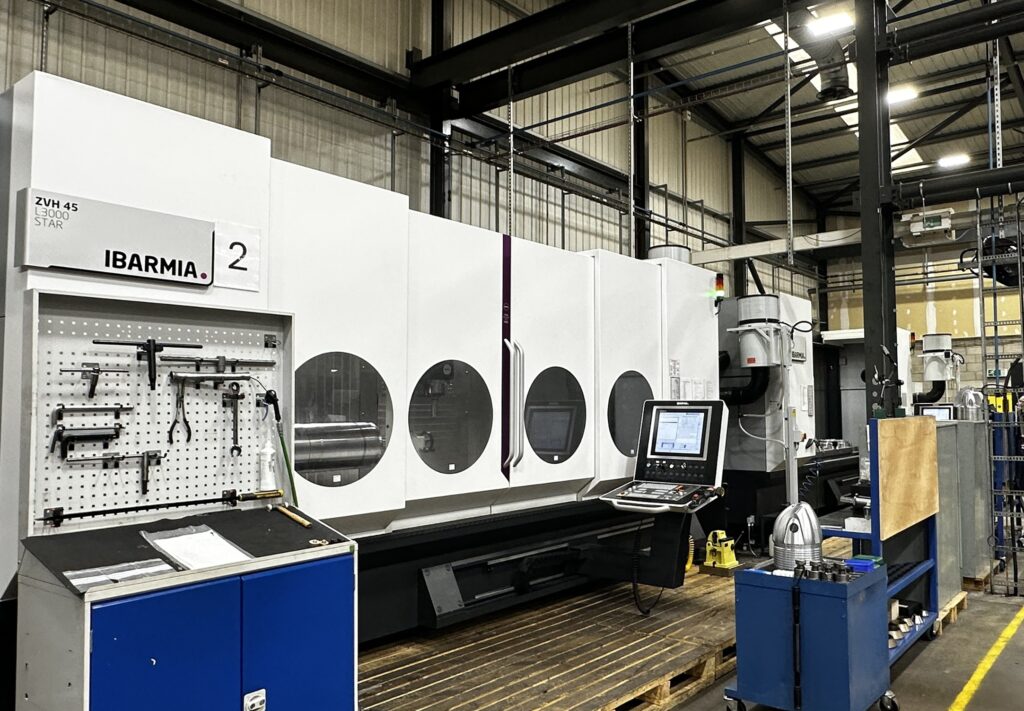
The Ibarmia ZVH 45 L3000 machine from Dugard is a 5-axis travelling column machine with an X, Y and Z axis travel of 3m by 1.2m by 800mm with a B-axis head range of +/-105 degrees. Supplied with an SK40 head as standard or HSK A-63 as an option, the ZVH 45 has a powerful 45kW spindle with 200Nm of torque. Provided with a FANUC or Heidenhain TNC control, the ZVH 45 L3000 is available with a multitude of options to maximise productivity for the end user.
The machine’s state-of-the-art graphics function has also significantly enhanced the programming experience. Mark notes that approximately 90% of the programming is now done offline, with the remaining 10% proven on the machine. “The graphics have been tremendously improved on these machines. A lot of the programming, I’d say 90%, is done through offline programming, and then we have to prove it out here, but with the graphics function on this machine, it just makes everything so much easier and reduces errors,” he says.
The advanced simultaneous 5-axis machining capabilities of the Ibarmia machine have been a game-changer for Cutting and Wear. This technology allows the machine to perform complex, multi-dimensional operations with a single setup, significantly reducing the need for manual intervention and enhancing overall efficiency. “It was a learning curve because it has a simultaneous head. We do have machines quite similar to it, but this one is a lot quicker,” acknowledges Mark, highlighting the initial challenges faced by the team in adapting to new technology.
The introduction of the Ibarmia machine has profoundly influenced the mindsets of Cutting and Wear’s machinists. Matthew explains: “The machines have assisted in that. Not only have they changed our manufacturing methods, but they’ve also shifted the mindset of the machinists. They’ve completely embraced the new technology, flipping their approach to the manufacture of downhole tools. The Ibarmia machine’s advanced features—including its high-speed spindle, integrated probing, and state-of-the-art graphics—have allowed Cutting and Wear to achieve notable improvements in accuracy, speed, and programming efficiency.” These enhancements have directly contributed to the company’s ability to meet the growing demands of the oil and gas industry.
In addition to its technical capabilities, the strong partnership between Cutting and Wear and Dugard has been instrumental in the success of this investment. Matthew emphasises: “Dugard came in, worked with us very closely, understood the tools we wanted to produce, and from then on, simply matched us with the appropriate machines. So it’s a well-suited relationship, and the machines are doing precisely as Dugard said they would.” The positive impact of the Ibarmia machine on Cutting and Wear’s manufacturing mindset, along with the resulting efficiency gains, has positioned the company for continued success in the years ahead.
As Matthew concludes: “It’s massively changed. As I mentioned, we were on this growth path, and with that, we aimed to adopt more modern machining techniques; the machines have helped facilitate that.”
Bringing manufacturing in-house
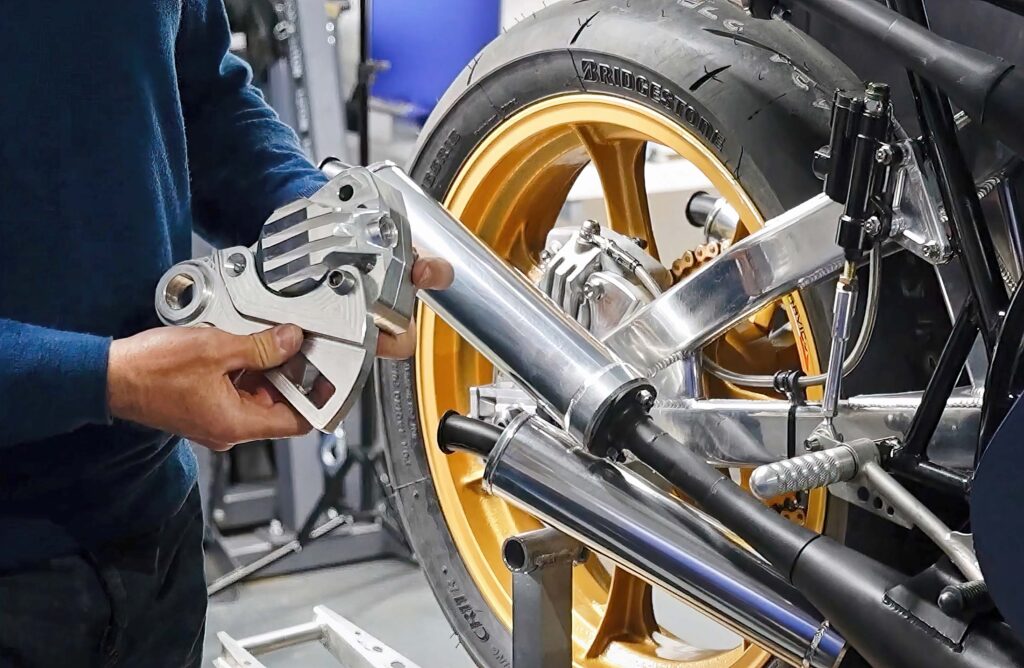
Duncan Dunbar established Dunbar Race Engineering in Dalbeattie in 2018 to design and supply prototype parts for the motorsport market. The company also reverse-engineers and remanufactures parts that are no longer available for historic and emerging classic racing motorbikes.
Initially, part production was outsourced to subcontractors. However, Duncan realised that to increase flexibility, reduce lead times, and ensure consistent quality, it would be necessary to transition from a home workshop to in-house manufacturing. Thus, in the spring of 2022, he relocated the company to an industrial unit and purchased a Hurco VM10i 3-axis VMC equipped with a 4th-axis rotary table.
Before deciding on the Hurco VMC, Duncan thoroughly researched the market. Hurco was recommended by a former colleague, which led to a visit to the supplier’s High Wycombe facility. As he was new to machining, he sought more than just a machine tool provider; he looked for a company with which Dunbar Race Engineering could partner. Critical to him was the assistance during the early stages of first-time CNC programming and a clear path to more advanced machining capabilities in the future. Duncan confirmed that Hurco’s training was excellent, and its applications engineers provided substantial support with programming and guidance on how different jobs should be set up.
Duncan described his experience with Hurco: “They are nice people to work with and the VM10i is a cracking machine. It has a large working area for its footprint and fits neatly into the space we had available.”
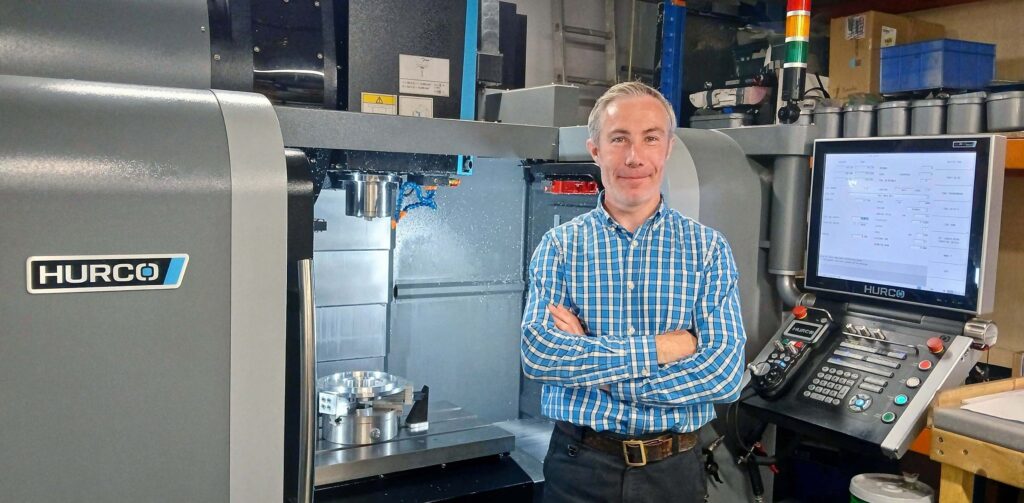
To produce excellent-quality parts with fine tolerances, sometimes as tight as ±10 microns, the manufacturer fully takes advantage of both the Hurco machine’s build quality and the conversational programming power of the WinMax control, which Duncan states is easy and intuitive to use. Most work, including complex jobs requiring 3+1-axis machining, is programmed directly at the control. Toolpath simulation and verification graphics help prevent potential input mistakes. “What you see on the screen is what you get on the part,” Duncan confirmed.
His career as a mechanical design engineer began with superbikes and MotoGP and continued with Mercedes AMG High Performance Powertrains. He retains a passion for all things motorsport but is keen to emphasise that Dunbar Race Engineering is not solely a racing company. He believes that the discipline, drive, and innovation that foster a career in motorsport can be applied to deliver design projects and manufacture products for a wide range of mechanical systems.
Additional expertise, including inspection and quality management system services using a Mitutoyo coordinate measuring machine, are offered. Customers also benefit from the experience of time-served manufacturing engineers who can be called upon at any stage of a project to analyse, redesign, and improve a process ahead of final sign-off.
Digital factories key to MedTech’s growth in tough conditions
Lifestyle-related illnesses, an ageing population and personalised health are some of the medical industry’s growth drivers. Manufacturers are using digital technology, from digital dental labs to polymorphic moulds, to win orders and battle tough trading conditions. Will Stirling reports.
Over 5.8 million people in the UK are living with diabetes, the highest number on record. The prevalence of type 2 diabetes has nearly doubled in the last 15 years, linked to lifestyle factors such as obesity and high-sugar diets. People are living longer and require mobility and care technology for extended periods. This exemplifies a growing and concerning burden on the NHS, while also presenting a significant business opportunity.
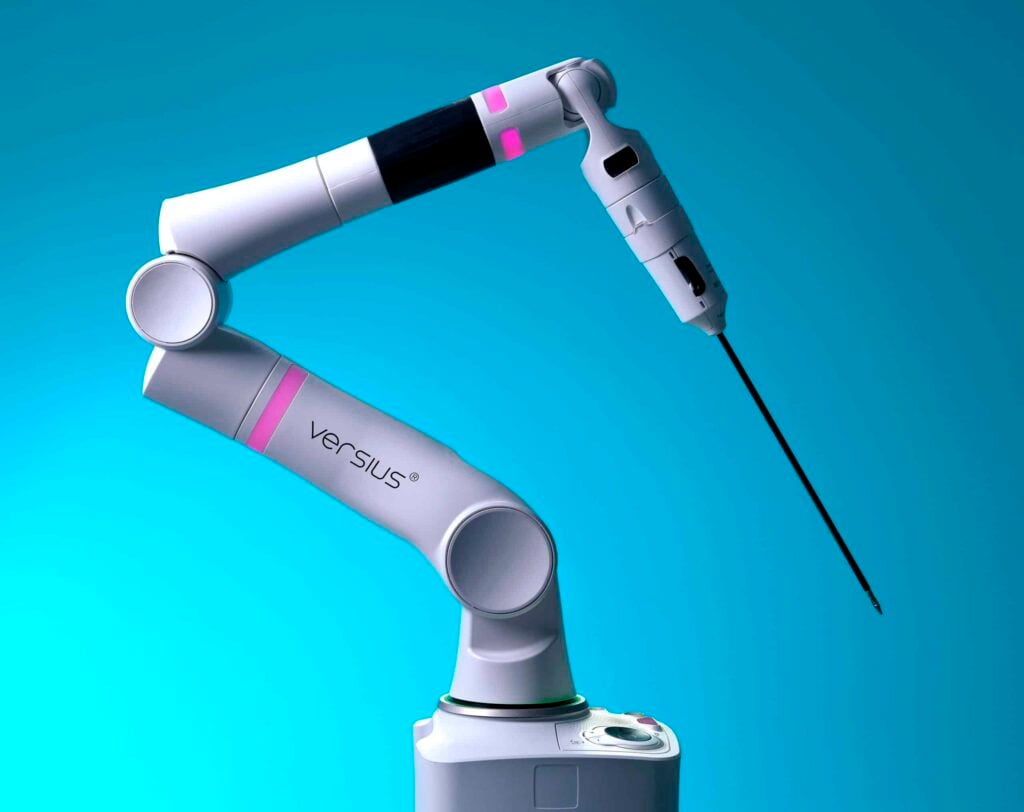
The manufacture of hard medical products – surgical instruments, tooling, prosthetics, orthotics, and devices like wheelchairs and beds – encompasses a broad range, particularly when including consumable devices such as single-use plastics. ‘MedTech’ typically refers to medical products with embedded digital technology, which includes diagnostic and monitoring devices. However, as more smart medical technology is developed, the division between machined or moulded parts and ‘digital tech’ is becoming increasingly blurred. The UK MedTech industry has an annual turnover of £27.6 billion, placing it just behind the aerospace sector (about £30bn).
The UK exports £10.1 billion worth of MedTech products annually (2023), but it still faces a trade deficit of £5.4 billion as imports exceed exports. High tariffs on UK-manufactured goods traded with the US increase pressure on this deficit, but there may be a twist. UK medical devices are subject to a flat 10% tariff, which is significantly lower than the high tariffs imposed on Chinese, Asian, Canadian, and Mexican imports, potentially benefiting some UK device exports.
The NHS spends up to £18bn annually on medical equipment, consumables, and MedTech—everything from syringes to MRI scanners, a vast domestic market for UK designers and manufacturers to access. So, it’s little surprise that it’s rich with engineering and business innovation.
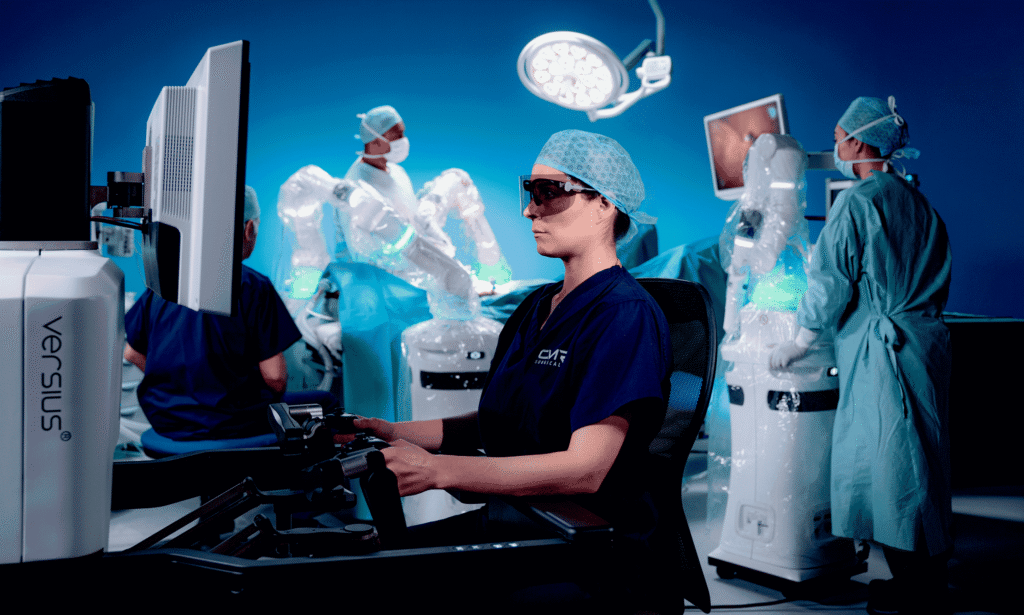
MedTech is being affected by the same trends as other manufacturing segments: digital technology, sustainability, cost reduction pressure, new materials, and new or fast-developing manufacturing technologies. 3D printing and polymorphic moulding are used increasingly in device manufacturing, such as in Prosthetics and Orthotics, aka ‘PO’, and specialist CAD/CAM software is utilised for digital dental manufacturing. The PO industry is worth £274m in 2024. Growth in prosthetics is fueled partly by amputations related to type 2 diabetes, and in orthotics by child mobility and disability needs. About 260 businesses operate in the PO sector, which surprisingly has 24% higher productivity compared to the entire healthcare sector (Source: BHTA, Healthtech’s economic impact in the UK).
Light the Fyous
Orthotics are externally applied devices used to influence the body’s function. They can be applied across the body but are most used to support the feet and lower legs. Foot orthotics are custom-made supports for the patient. Here, conventional mould tools used to make a plastic mould are uneconomic—short-run batches don’t cover the tool cost.
Fyous, the Sheffield-based polymorphic moulding technology provider, uses a proprietary pin tool with 28,000 pins to create a customised, ‘shapeshifting’ mould in around 20 minutes. It recently partnered with Peacocks Medical Group, the UK’s largest independent orthotics company, to use the polymorphic technology for its products.
“This collaboration shows how polymorphic moulding can help the production of lasts (foot orthotics), cutting waste and costs, and improving efficiency,” said Joshua Shires, CEO and Co-Founder of Fyous. “Early adopters like Peacocks will gain a competitive edge as the industry moves towards more sustainable, digital-first manufacturing.” Fyous is now developing its pin technology to address the diabetic foot care market, where the NHS spends nearly £1bn a year on diabetic care.
Several British MedTech companies are attracting big investments. In April, Cambridge-based robotics company CMR Surgical closed a US$200m funding round with a mix of equity and debt capital from investors Trinity Capital. The funds will be used to expand CMR’s flagship Versius Surgical Robotic System to more hospitals globally, with a focus on the US market, and to support the launch of the enhanced Versius Plus. In 2021, CMR’s private funding pushed above £1bn, valuing the company at $3bn.
“We are now at a pivotal stage, poised to capitalise on significant opportunities for market expansion, including in the U.S, while penetrating deeper into expanding markets,” says CEO Massimiliano Colella.
Cutting into the booming digital dental market
Digital technology has allowed the production of dental implants and restorations to change rapidly. Today, many digital manufacturing labs can provide uber-accurate dental implants, crowns, and tooth sets in multiple materials in quick delivery times from 3D models of teeth supplied by dentists. These labs need the best milling tools to machine these implants accurately.
Nine months ago, dental lab Optadent contacted high-precision tooling company Quickgrind to supply a two-flute, ball nose tool with 5mm extra reach. Optadent was compromising its CNC machining strategies; Managing Director Anthony Wainwright felt this could be improved by moving from standard tools from dental consumable distributors, to using a bespoke manufactured tool. Quickgrind’s Total Solutions Engineering Strategy, a custom-made tooling service, was a perfect match. Material versatility is key in dental implants, and these tools are designed to machine the main specialist dental materials – chrome cobalt, titanium, zirconium oxide, PMMA, PEEK and wax.
This engagement showed Quickgrind a relatively new and booming global, digital business – an industry within an industry.
“Since spotting the opportunity we have worked closely with digital machining dental lab owners & technicians, machine tool manufacturers, machine tool distributors, CAD/CAM developers, CAD/CAM resellers, CNC application engineers and academics, to build our knowledge and understand how the market is growing and what may limit the speed of growth,” says Technical Support Manager Mark Aspinall. You can read the full story on page 52 and 53.
Hold your nerve and keep innovating
Amies is a 96-year-old, family-owned injection moulded component and assembly manufacturer. Over the last 20 years, the company has steadily built its medical business so that it now exceeds 50% of turnover across a diverse customer base in medical devices and IVD products.
“Over our long history, we have learned that the best strategy is to maintain a solid and reliable technical base, such as the fleet of modern Arburg IMM machines we operate, while keeping fully aware of new technologies and materials as they develop, with a view to early adoption,” says Managing Director Simon Stewart-Smith.
As regards innovation trends, Amies is increasing its use of in-house additive manufacturing in the development phases of medical projects and even most recently, some early pre-series production runs of complete assemblies. There is a lot of interest in eco-materials, too. “We are delighted to be engaged in some exciting, top-secret projects around a promising bioplastic that are progressing well,” Simon adds.
“We are all operating in a challenging environment now, with many challenges coming from changes imposed by governments both home and abroad, but there is every reason to be optimistic that by remaining agile and focused, we can remain strong and continue to steadily grow.”
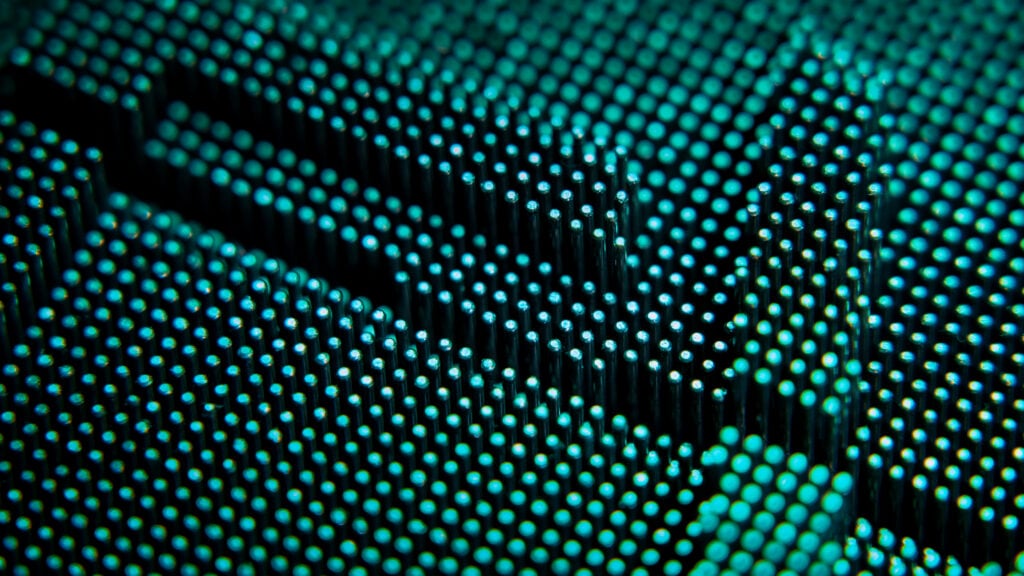
Tariffs and turbulence put the brakes
on medical’s potential
Like other sectors, medical devices face troubling conditions, not only US tariffs causing mayhem in supply chains. “The MedTech and HealthTech sectors currently face an unprecedented array of challenges; employers’ NI increases, trade tariffs, regulatory uncertainty, post-Brexit trading status with the EU, NHS reform, the need for social care reform, the list goes on!” says David Stockdale, CEO of the British Healthcare Trades Association.
“With so many moving parts and burdens placed on these sectors, it is an incredibly challenging market to be in. That said, there are opportunities, as innovations come into the market, coupled with an ageing population, there is growth potential here – it is just hard to see amid all the turmoil. It is important that the government better understands the sectors, who to support and to work with them at this time to help them flourish.”
Understanding government loan schemes
In today’s business environment, understanding and leveraging government loan schemes can be a game-changer for many firms.
Recent data from Close Brothers Asset Finance’s independent research sheds light on how businesses perceive and use these schemes, including the Recovery Loan Scheme (RLS) and the Growth Guarantee Scheme (GGS).
l 53% of SMEs know how to use government loan programmes
l 48% find the application process challenging
l 1 in 3 businesses would use these loans to purchase assets or improve cash
Awareness and understanding
A significant portion of businesses are aware of these government loan programs. According to the data, 58% of respondents have heard about the RLS and GGS. However, understanding how these schemes can be applied to their businesses is slightly lower, with 53% indicating they know how to use them.
Application process
When it comes to the application process, 58% of businesses understand how to apply for these loans, but despite this, nearly half of the respondents (48%) find the application process challenging.
Utilisation of loans
Businesses have diverse plans for utilising government-backed loans. The most common uses include purchasing assets (17%), improving cash flow (16%), and investing in sustainable initiatives such as solar panels and wind power (13%). Other notable uses include training existing staff (12%) and hiring more staff (11%).
British Business Bank loan schemes
Growth Guarantee Scheme (GGS): Supports UK smaller businesses with loans up to £2 million. It offers term loans, overdrafts, asset finance, invoice finance, and asset-based lending and it provides a 70% government-backed guarantee.
Recovery Loan Scheme (RLS): Provided loans up to £2 million for UK businesses to support investment and growth. This included term loans, overdrafts, asset finance, and invoice finance.
Coronavirus Business Interruption Loan Scheme (CBILS): Provided up to £5 million in financial support to UK businesses affected by COVID-19. It included term loans, overdrafts, invoice finance, and asset finance. The CBILS offered a government-backed guarantee to lenders, encouraging more lending.
Bounce Back Loan Scheme (BBLS): Provided loans between £2,000 and £50,000 to UK small and medium-sized businesses affected by COVID-19. BBLS offered a 100% government guarantee, a fixed 2.5% interest rate, and no repayments for the first year.
For more information please visit:
MSC cut cycle times with new tooling
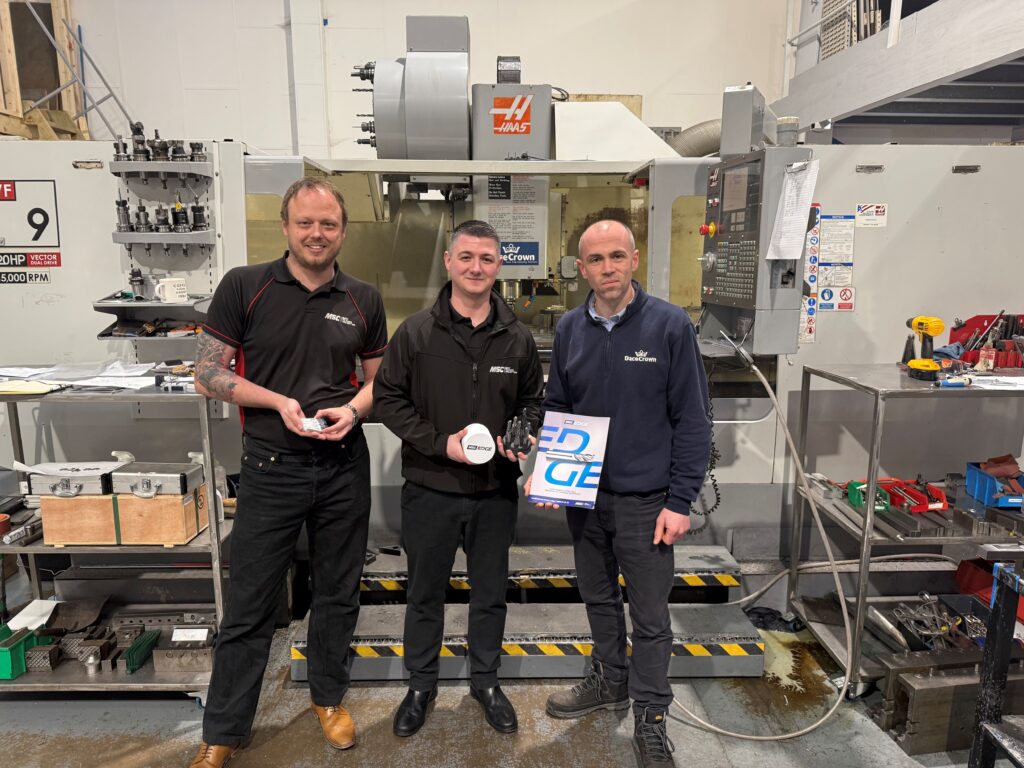
Longbridge-based DaceCrown Ltd has established itself as a leading supplier of precision components to the bottling and packaging industry. However, after 25 years of operation, a new generation of engineering talent has taken over and plans to elevate the company to new heights.
“Over the years, the company built a strong reputation among global brewing, beverage, and pharmaceutical brands for tackling the toughest packaging and handling challenges,” says Tom White, Co-owner at DaceCrown Ltd. Tom, whose background is in applications engineering and technical sales, purchased DaceCrown in 2023 with his business partner and Operations Director, Jake Harley-Arliss.
In less than a year, they transformed DaceCrown from a fully manual workshop into a facility with three HAAS machine tools: a VF-9 large-capacity VMC, a VF-2 VMC, and an ST10 high-performance turning centre.
“The previous owners primarily used manual lathes for production, a highly skilled but increasingly scarce method. Recognising the need to futureproof the business and expand the customer base, we made a strategic decision to transition to more modern production methods,” Tom explains.
“This change in approach very quickly opened the door to winning more jobs for high-value components with complex machining requirements, such as sharper tips, better corner radii and finer screw threads. You couldn’t do that work at scale on manual machines.”
However, as business grew, the DaceCrown team soon realised that the tooling on their HAAS machines was still potentially holding them back from reaching their true potential.
To help align the company’s tooling with its growth ambitions, DaceCrown turned to MSC Industrial Supply Co. UK. MSC application engineers visited DaceCrown over several weeks to immerse themselves in the business and gain firsthand experience of the tooling challenges facing Tom and his team.
The trials coincided with the testing stage of MSC’s newly launched MSC EDGE range of multipurpose solid carbide holemaking and milling tools. In turn, DaceCrown served as a vital field test site, providing important performance data to MSC throughout the testing process.
During the trial, a variety of materials and toolpaths were tested. Following its completion, DaceCrown was supplied with a set of 4, 8, and 12mm MSC EDGE endmills, which have enabled the team to handle a wide range of materials and applications without having to change tooling regularly.
“It was an instant game changer. We went from a 1 minute 50 second cycle time down to 10 seconds. It was a case of plug and play; put the tool in, set the speeds and feeds, and press go. We’ve used them on stainless steel, mild steel, structural steel, and aluminium. We can do pocket milling, milling into holes that were drilled too small, and we’ve also done some profiling work,” Tom adds.
“The best thing is, we can keep them in the tool magazine, which reduces our set-up times. And, even though we are running at higher speeds and feeds, we’ve found the MSC EDGE tooling to be very durable, so we don’t have to replace it as often as we used to with our previous supplier. This means we can not only complete jobs faster and turn around work for our customers quicker but also keep our own tooling costs down.”
“We’ve always strived to deliver the best possible quality for our customers. The parts we supply touch the end product last, so if we make a mistake, then the whole line can go down. Quality is everything for us and our customers; therefore, if it’s not right, it’s not leaving our facility,” Tom concludes, reassuring the audience about the company’s commitment to quality.
Renishaw AM & metrology provides flexibility for medical manufacturer
Croom Precision Medical has selected Renishaw as its partner for additive manufacturing (AM) and metrology. It will use Renishaw technology throughout the production and validation of its ISO: 13485 certified medical devices.
The company has found that using Renishaw’s AM technology enables them to incorporate complex features into their implant designs at a commercially viable cost. They also note that Renishaw’s integrated AM software, combined with its metrology solutions, helps them maintain traceability throughout their manufacturing process, which is vital in a heavily regulated environment.
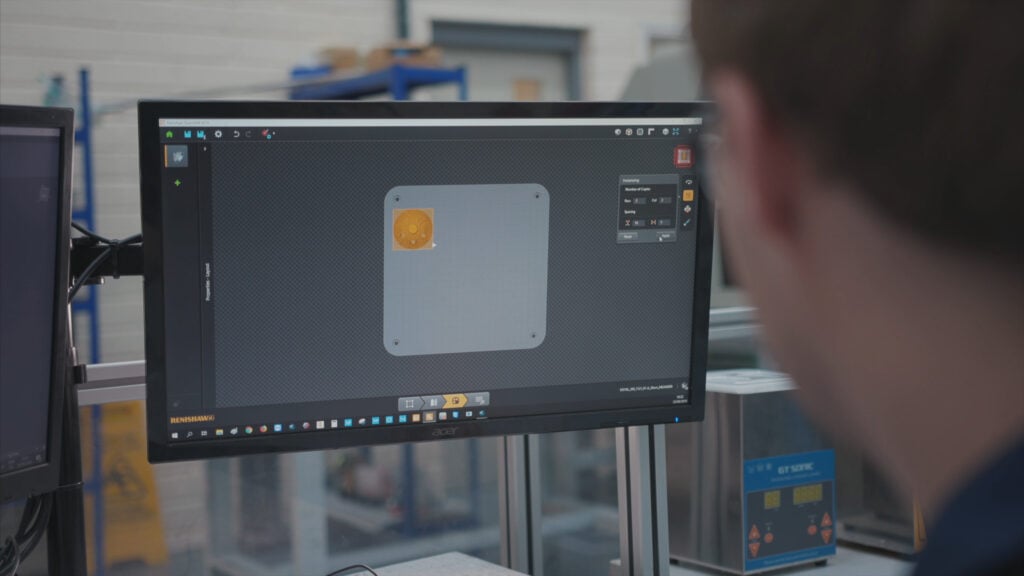
Background
Croom Precision Medical (CPM) is at the forefront of Ireland’s thriving medical device industry. Established in 1984, CPM has supplied Class I, II, and III medical devices to the orthopaedic market for over 35 years. Since these devices ultimately impact people’s lives, it is crucial to implement rigorous quality procedures to ensure their safety and effectiveness during and after implantation.
“We strive to achieve consistency and reliability in our manufactured products. CPM envisions becoming a centre of excellence for additive manufacturing in Ireland,” explains Patrick Byrnes, Research and Development Manager at CPM. CPM operates an integrated management system (IMS) that encompasses ISO: 9001, ISO: 13485, and ISO: 14001 accreditation. To demonstrate compliance with these standards, CPM must ensure transparency and traceability at every stage of the manufacturing process.
Medical implant designs are rapidly advancing. Manufacturers are increasingly integrating novel and complex structures into these designs to enhance performance and longevity. However, creating such structures with traditional manufacturing techniques can be challenging and may not always be economically feasible.
To evaluate the quality of parts, CPM conducts a series of offline tests to assess the implants’ chemical, mechanical, and morphological properties. While these tests are essential for measuring the mechanical and chemical consistency of the implants, they can be time-consuming and can raise the overall cost per part. CPM’s goal is to transform production so that more monitoring occurs during manufacturing. “We’re looking for a red or green light, indicating whether the part is good or bad. Currently, we perform extensive offline testing, aiming to minimise it to reduce our cost of goods. We have made substantial progress in that direction over the past couple of years; there’s still some work to be done, but we believe we are ahead of many of our competitors in the area of in-process monitoring,” Byrnes noted.
Solution
Emerging from the aerospace sector, Renishaw has a proven history of providing solutions that enhance manufacturing efficiency and part safety in highly regulated environments. CPM is applying Renishaw’s technology in the medical sector for the same purpose. CPM has invested in a RenAM 500M additive manufacturing system, which it uses to 3D print medical devices in titanium. Renishaw’s AM technology can create complex structures in a single manufacturing operation. For instance, CPM has begun to evaluate the use of gyroid lattices on acetabular cups, a design feature that was previously not economically feasible before their investment in AM. The resulting implants have undergone rigorous quality testing, and CPM reports notably good density and Young’s Modulus values.
In addition to the advanced manufacturing capabilities of AM, Byrnes emphasises that inline process monitoring is what truly sets apart Renishaw’s technology and provides CPM with a competitive advantage: “The Renishaw software equips us with all the necessary information to ensure the quality of our parts, from build reports to post-processing, enabling us to trace our parts from beginning to end.” To promote quality and consistency, CPM has also selected Renishaw as its partner for precision metrology equipment, employing Renishaw technology at various stages of their testing and part validation. The team has long recognised Renishaw’s reputation for producing reliable, robust metrology equipment: “When you visit multinational companies and see all the Renishaw products on the shop floor, they have a reputation for being repeatable, reliable, and capable of consistently operating in harsh environments,” commented Byrnes. CPM exemplifies how Renishaw can provide a comprehensive solution with technology that supports the manufacturing of technically ambitious parts and quality verification.
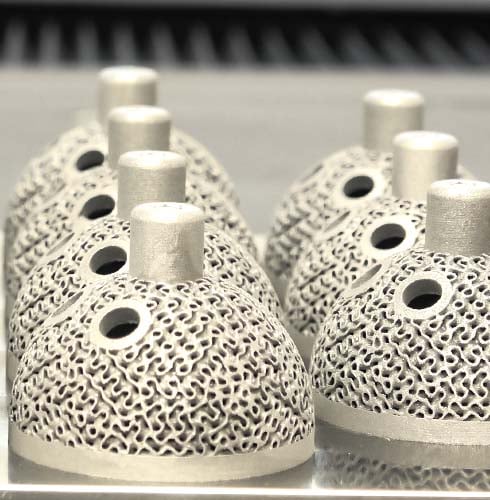
Results
CPM reports an increased market share, directly attributed to its investment in AM technology. “We have captured new market share in international markets, specifically in East Asia and North America, which were previously unattainable for us. Only in the last two years have these markets become accessible. We chose Renishaw as a development partner, not just as a supplier, envisioning the next few years as a strategic partnership to grow our additive manufacturing base here in Ireland.”
Healthcare stands out as one of the leading industries for AM development. Although significant progress has already been made, ample room for growth still exists. CPM views Renishaw as a strategic partner in advancing AM technology. Byrnes adds, “Approaching AM for us has been a journey; it’s an entirely different way of thinking. It’s a more laboratory-like environment, a more cognitive approach to the process as opposed to conventional engineering.”
In the coming years, CPM will continue to leverage the knowledge gained from its rigorous development programs and collaborate closely with customers and regulatory bodies to advance additive manufacturing technology and support enhancements in healthcare.
High-precision medical machining
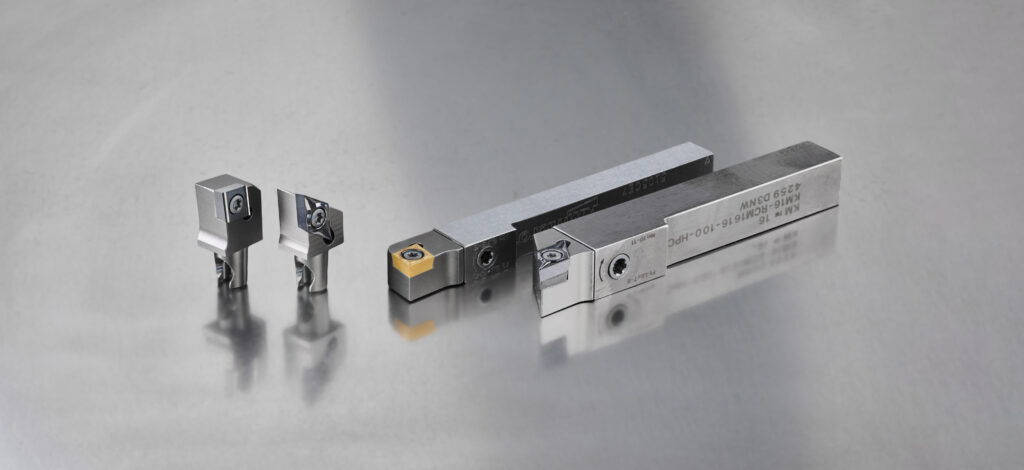
When it comes to the medical field, precision and reliability are crucial for producing high-quality biocompatible components. Kennametal’s TopSwiss™ line of tooling excels at meeting stringent requirements and close tolerances. This platform supports the development of cutting-edge medical technology, helping to improve the lives of those who rely on the latest medical innovations.
TopSwiss tooling features sharp cutting edges and aggressive geometries that create low cutting forces and excellent chip evacuation, ensuring longer tool life and superior surface finishes. The TopSwiss™ MBS (Micro Boring Solid) system is especially distinguished for its precision in machining extremely complex and small components.
“In regard to the TopSwiss MBS, especially for medical-grade applications, the tooling must be precise and reliable to manufacture components like bone screws, tulip heads, dental implants, and surgical instruments,” said Scott DeVinney, Senior Global Product Manager, Medical and Small Part Machining. “They have to meet the most stringent requirements for safety and compatibility with human tissue.”
Innovative Solutions
Finding the best results for customers is always a priority when designing the latest technology. When a prominent medical company is faced with the challenge of pinch-turning long instruments made of 17-4PH stainless steel, there is a struggle with tool life and chip control. To resolve this, the Kennametal team creatively adjusted parameters. They processed these instruments on Swiss-type turning machines using a standard TopSwiss ISO turning insert with advanced finishing wiper technology and a new coated cermet grade (KTP25S), designed specifically for Swiss-type turning. This resulted in excellent chip control and surface finish, and it increased tool life by 900%, from 50 to 500 pieces.
Additionally, a TopSwiss ISO turning insert with the new Light Finishing Swiss (LFS) geometry and grade KCP20S was used to enhance surface quality and chip control for a company needing a solution for turning PH stainless steel instruments. The TopSwiss tooling not only improved surface quality but also offered nearly 50% cost savings over the customer’s existing solution.
Advanced Coatings and Tool Holders
The TopSwiss™ MBS platform contains micro boring inserts specifically designed for machining medical components. These inserts feature a specialised KCSM25S coating for a smooth, polished surface that reduces chip adhesion and improves component quality. The inserts also have a unique lead and relief angle that can withstand high tool pressure. Additionally, coolant is delivered directly through the tool to the cutting edge, reducing heat and improving chip control. For optimal performance, the inserts can be paired with HP (High Performance) tool holders, which offer high precision and repeatability to the centerline of ±5 microns.
Versatility and Customisation
Kennametal’s TopSwiss™ platform stands out for its versatility in handling a wide range of applications, with nearly 1,000 inserts available. This extensive selection allows for precise customisation to meet specific machining needs, whether it’s boring, profiling, back boring, grooving, threading or multi-directional turning.
Low Feed and Speed Applications
Highly effective in low feed and speed applications due to their superior chip evacuation, the TopSwiss™ ISO inserts ensure smooth operation by efficiently removing chips and preventing build-up. They provide excellent surface finishes and extended tool life, thanks to their precision and sharpness. With nose radii ranging from 0 (sharp) to 0.80mm and close tolerances (+0/-0.05mm), these inserts offer precise cutting capabilities.
Material-Specific Inserts
The ISO platform offers specialised inserts in both carbide and cermet grades. These inserts come in fine finishing, light finishing, parallel positive, and finishing wiper geometries. Carbide inserts can be used on steels, stainless steels, high-temperature alloys, and non-ferrous materials with grades such as KCS25S, KCM25S, KCP20S, and KN10S. Cermet inserts are designed for carbon steels, alloy steels, and stainless steels with the grade KTP25S.
The Importance of TopSwiss Cermet Wiper
Cermet is highly effective for machining applications that require high surface quality, dimensional stability, and tight tolerances. It is particularly suitable for high-speed finishing. Offering significant improvements in surface finish and productivity, the TopSwiss Cermet wiper insert features a secondary radius (rw) that follows the primary corner radius (r), effectively reducing the scallop height (Ra) and greatly enhancing surface roughness.
Key Advantages of Cermet Wiper Inserts
- Due to the larger size of the secondary radius, wiper inserts can achieve higher feed rates while still maintaining or even improving surface roughness. This results in increased productivity without compromising quality.
- Wiper inserts are most effective when used to activate features that enable the secondary radius to follow the corner radius. This includes straight lines, small angles, and chamfers. However, they are less effective on steep angles or chamfers, where the geometry does not allow the secondary radius to follow the corner radius.
“When you’re using wiper inserts, it’s all about the details. Think about the lead angle and the specific feature you’re machining,” said DeVinney. “These details can make or break the effectiveness of the inserts. You must take the time to plan and set up carefully to achieve the best results.”
To avoid workpiece damage, it’s crucial to select the appropriate material and machining speed and use coolant to prevent overheating. This can be achieved by adjusting cutting speeds, feed rates, and the depth of cut, ensuring proper coolant flow, and selecting the right cutting tools. Kennametal’s Swiss-type turning platform is the perfect solution to enhance efficiency and provides a cost-effective, versatile solution applicable to various materials.
Kennametal’s TopSwiss™ platform stands out as a premier solution for precision turning. With its advanced tooling features, innovative solutions, specialised coatings, and material-specific inserts, TopSwiss™ ensures precise machining capabilities, particularly in the medical field.
Mitutoyo delivers missing link
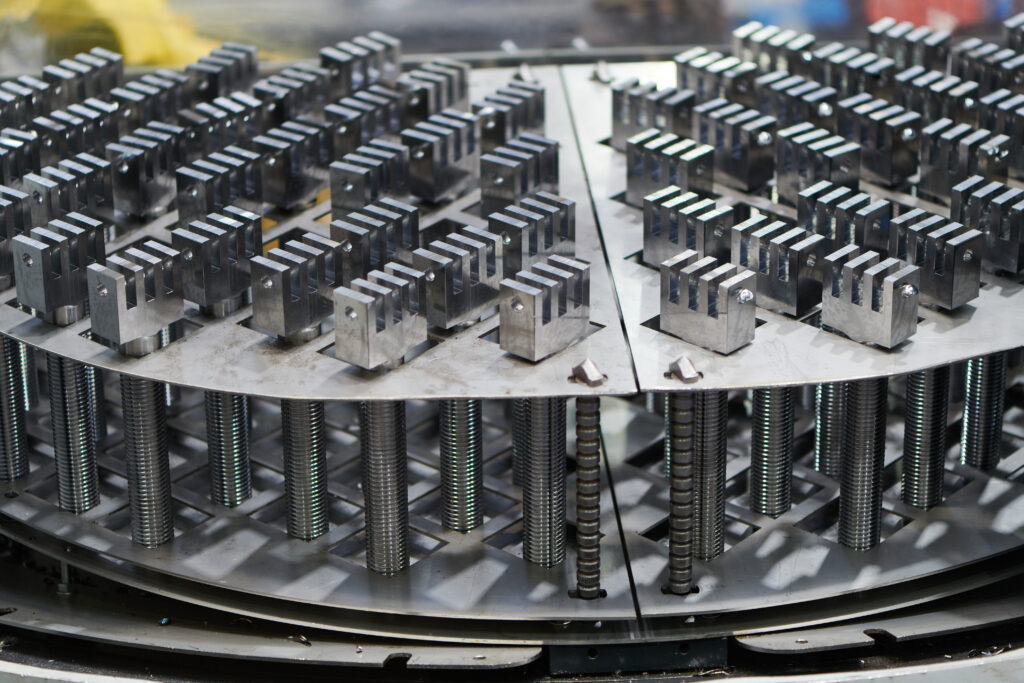
As a globally recognised manufacturer of leaf chains, FB Chain products are used in the automotive, material handling, and industrial machining sectors. The Letchworth Garden City company has earned a reputation for producing durable high-performance chains that support critical operations in demanding environments. To further this commitment, the company employs equipment from Mitutoyo.
The product range includes leaf chains, roller chains, anchor bolts, sprockets, and customised chain solutions. The company’s leaf chain kits include pre-measured components like chains, bolts, and attachments. FB Chain’s dedication is supported by a continuous partnership with Mitutoyo, which has been vital in maintaining the highest quality control.
With production volumes rising and the demand for tighter tolerances increasing, the need for faster and more automated measurement processes became essential. The company sought a solution that would enhance measurement accuracy while ensuring components were within the required tolerances.
FB Chain approached Mitutoyo for their Roundtracer Flash, an advanced, non-contact measurement solution. This optical measurement system is perfect for inspecting the intricate surface profiles and geometries of the produced anchor bolts and pins. The Mitutoyo Roundtracer Flash enables FB Chain to measure dimensional accuracy and geometric consistency down to microns. Additionally, the Roundtracer Flash provides precise process control for demanding customers.
The strong partnership between FB Chain and Mitutoyo was crucial in implementing the Roundtracer Flash system. Chris Cook, the Operations and Manufacturing Manager at FB Chain, visited Mitutoyo’s Coventry site, where he received invaluable experience and support from Mitutoyo, collaborating closely to customise the measurement processes and integrate the Roundtracer Flash into the existing production line.
Discussing this, Chris Cook stated: “Bigger customers require more accurate results, and we knew Mitutoyo could cover the range we were looking for. We sought a machine that would be easy to implement and provide static and dynamic measurements for our anchor bolts, blocks, and pins.”
With a Mitutoyo hardness tester, small tools, and gauges already in use at the facility, Chris and his team continued the Mitutoyo synergy while searching for a shop floor measuring machine. Aiming to operate 24/7, FB Chain has set an ambitious production target of 168 hours per week. It is eager to determine if this is achievable when considering measurement and loading/unloading times.
With more accurate and consistent measurements from the Roundtracer Flash, FB Chain can assess tool life limits, contributing to the 168-hour production target with increased unmanned working hours. With demand rising, FB Chain processes 25 to 30 tonnes of steel monthly. With 97% of manufacturing conducted in-house, their automated machining is being maximised to meet customer demands, necessitating the deployment of a high-priority, non-contact measuring machine. Initially, the Roundtracer Flash will be manually loaded, but as production increases, FB Chain intends to integrate another robot arm.
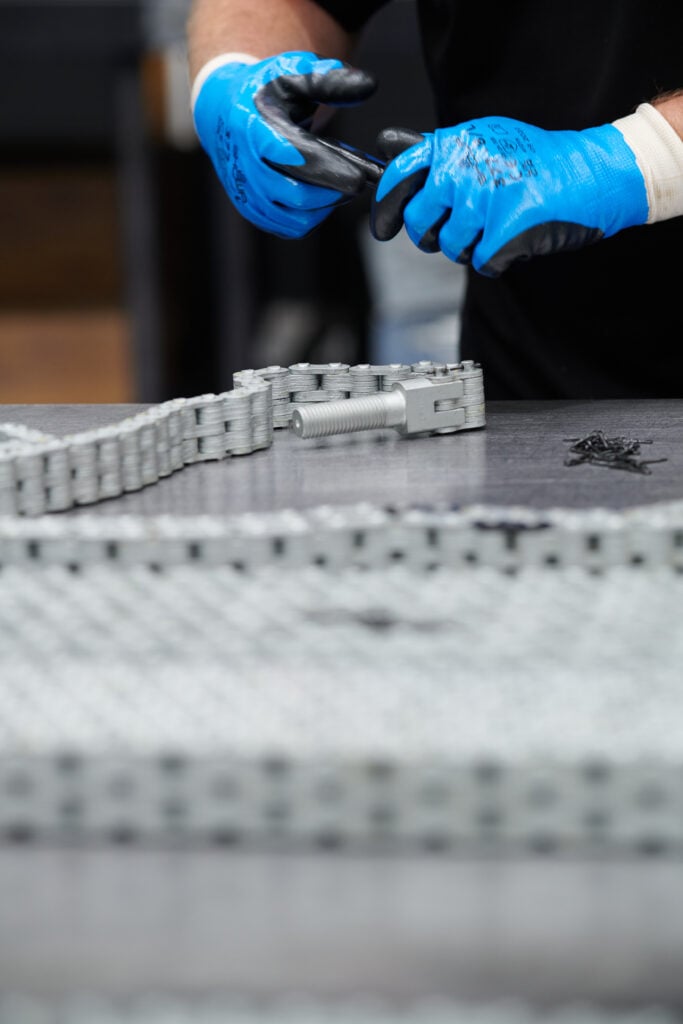
After installing the Roundtracer Flash, Chris remarked: “The machine is user-friendly, interacts well, and has enhanced measurement efficiency. We already had trust in Mitutoyo, but observing the performance of the Roundtracer Flash and its extensive capabilities has further validated our continued reliance on Mitutoyo products.”
With some initial guidance, both operators and inspectors can effectively use the machine. The speed of the Roundtracer Flash improves inspector efficiency by 97.5%, reducing a 10-minute inspection to just 15 seconds. Furthermore, the number of measurements has increased, enabling comprehensive dimensional checks during every batch. Not only is it capable of measuring cylinders, round parts, and turned components, but the machine has also been further programmed to assess milled flat surfaces and hole diameters/alignments. The Roundtracer Flash revealed that previous measurement methods using hand tools did not meet the requirements of specific customers, demonstrating that eliminating human error from the process has enhanced the inspection process.
Hurco empowers manufacturing success at RPH
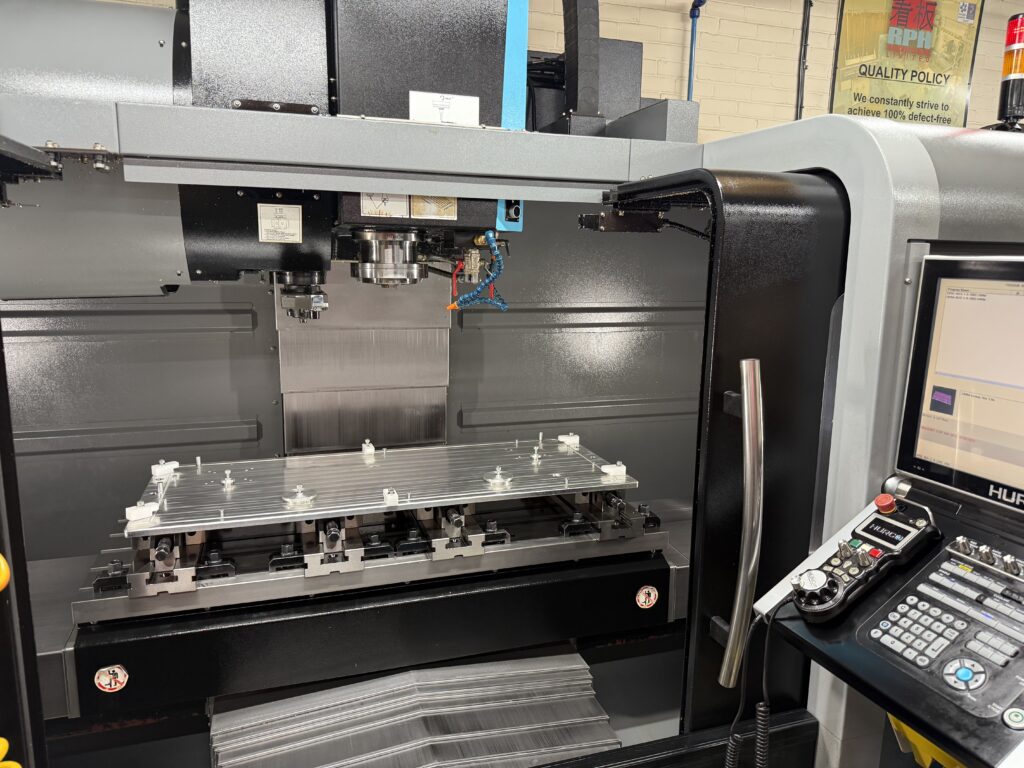
In the fast-paced world of precision manufacturing, staying ahead of the curve is crucial for maintaining a competitive edge. For Richard Haim, the owner of RPH Manufacturing Ltd, this realisation came early in his career, leading him to make a strategic investment in Hurco machine tools.
RPH, a company based in Bournemouth, has been a stalwart in the industry, delivering over 45,000 parts annually to its diverse customer base. At the heart of this impressive output lies Richard’s unwavering commitment to leveraging the latest manufacturing technologies, with Hurco machines.
Richard’s journey with Hurco began in 1999 when he acquired his first Hurco machine tool. Attracted by the brand’s reputation, he saw an opportunity to enhance his company’s capabilities. “I like Hurco because many of Hurco’s customers are Formula One teams. I am very interested in Formula One, so what better endorsement than purchasing a Hurco machine tool?” Richard explains.
One standout feature that has made Hurco machines invaluable for RPH is the seamless integration of the control system. Rather than programming directly on the machine, Richard uses Hurco’s desktop software, which allows him to create and refine programmes.
“I’ve got Hurco desktop software installed in my programming hub, and I program from there, then I import the programme into the control. I do very subtle editing, so as soon as it leaves the programming hub, it’s ready to go in the control.”
The versatility of Hurco has also been a significant factor in RPH’s success. Richard has invested in a range of Hurco models, including the VM10, VM20, and VM30, each offering unique capabilities for various manufacturing tasks. “I may have one operation on a VM30, and then I put a reverse operation on a VM10,” he explains, highlighting the benefits of having access to different machine sizes.
One of the key advantages of Hurco’s control system is its ability to facilitate seamless programme transfers between machines. This has been particularly beneficial for RPH, as the company often needs to move parts between different machines. “I can network all the machines by importing the programme into whatever machine I wish to use,” Richard explains. “Sometimes, I use one part on the same machine, and then I’ll move it around. With all that tooling, the Hurco machines are familiar and will recognise that tooling.”
Another crucial aspect is the control system’s graphics capabilities. “The first thing to consider when programming anything new is your stock geometry. You must have that perfect,” Richard explains. “Then, when you’re doing your animation, you can flip and ensure that you’ve got the machine correctly positioned around the stock geometry.”
The ability to dry-run programmes on the Hurco control system has also been a game-changer for RPH, particularly for fixture-based work. “I place a 50mm block on top of the work surface, and then I run the entire programme with a 50mm Z offset,” Richard explains. “This allows me to ensure that I won’t hit any clamps or bolts during the machining process.” As Richard looks to the future, his commitment to Hurco remains steadfast. “My mission is that I’ve been in business for 44 years now. Fifty years will be my milestone. That’s 2031. I will still be running Hurco CNC machines.”
Richard’s investment in Hurco machine tools has been a strategic decision that has yielded results for RPH. From the seamless integration of the control system to the versatility of the machine lineup and advanced graphics capabilities, Hurco’s technology has empowered RPH to maintain its competitive edge and consistently deliver high-quality parts to its customers. As Richard looks to the future, his unwavering commitment to Hurco underscores the value these machines have brought to his business and his confidence in the brand’s ability to support his continued success.
Dentists know the drill with Quickgrind
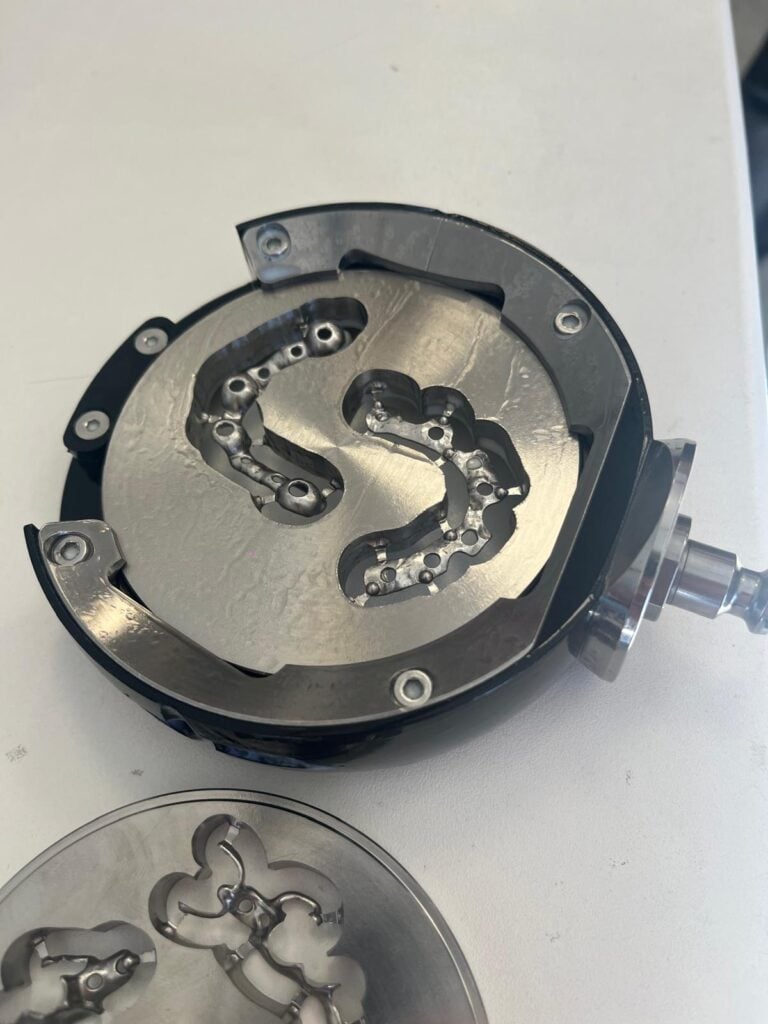
The dental industry has witnessed explosive growth over the last decade. Dentistry has become a lucrative field, with an ageing population retaining their teeth for longer, an increase in sugary foods on supermarket shelves, and a socially media-influenced population pursuing cosmetic enhancements. Over the last ten years, NHS treatments have incrementally increased by 1 to 2% per annum, private dental care by 5 to 7%, and cosmetic dentistry has boomed by as much as 35%. All these factors exert pressure on the supply chain, and it’s here that Quickgrind is making an impact.
By definition, high-street dentists, laboratories, and the supply chain supporting the sector are medical experts, not engineers. Engineering expertise becomes essential as more dentists perform scans, utilise 3D printing, and engage in micromachining at-source or through local laboratories. This is why Anthony Wainwright of Optadent contacted Quickgrind last year.
The company uses a range of small cutting tools and it required a 2-flute ball nose with an extra 5mm of reach. Optadent was compromising its machining strategies, and Anthony believed that processes could be improved with the right solution. Purchasing standard tools via a dental consumable distributor, Optadent, was confident that a better solution was available.
Commenting on the initial meeting with Optadent, Quickgrind’s Technical Support Manager Mark Aspinall says: “Discussing the dental CNC milling industry with Anthony, it was clear that Quickgrind’s Total Solutions Engineering Strategy (TSE) fitted perfectly with Optadent’s desire to improve processes. This initial meeting sparked Quickgrind’s desire to further investigate the digital dental market to reduce their total costs while optimising efficiency, productivity, and sustainability.”
Understanding the market
Quickgrind has collaborated with digital machining dental lab owners, technicians, machine tool manufacturers, distributors, CAD/CAM developers, CAD/CAM resellers, CNC application engineers, and academics. Discussing this research, Mark adds: “We have observed firsthand how and where the market is growing, the frustrations the dentistry industry faces regarding its manufacturing practices, and how these challenges impact the speed of market growth, future technologies, and materials. At Quickgrind, we have listened to the industry and support the sector through our advanced cutting technologies.”
Over the past 12 months, Quickgrind has seen the automation and digital workflow within the industry. This encompasses everything from models and materials to CAM programming of toolpaths, loading, tool databases and breakage detection.
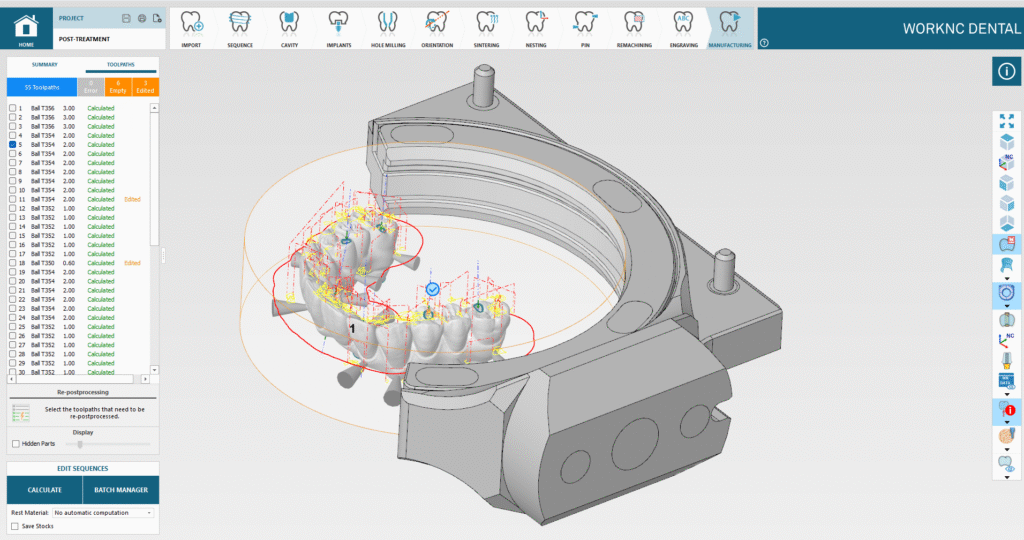
“The level of automation is impressive, and the manufacturing supply chain in other industries could learn a lot from it. The automation in dental milling laboratories enables them to program and rapidly produce complex dental components to specific quality standards, with minimal manual input. Therefore, cutting tool performance is even more critical for machine uptimes,” Mark says.
“Dental labs process a wide variety of materials, ranging from wax to titanium, and comprehending the terminology of the dental world is essential to meet clients’ requirements. CNC milling strategies, tool databases and ‘standard’ cutting tools are typically provided as a package from the distributor of the small and often bespoke machine tools. In many UK laboratories, expertise in cutting tools and machining strategies is often limited to what has been provided by the machine tool distributor.”
“While very complex components are machined, the full potential of the CAD/CAM software and the machine’s capabilities is not being utilised to maximise productivity. In this area, our experts are assisting with machining strategies, cutting parameters, and, of course, tools to extend tool life, optimise machine uptime while enhancing the quality of components and implants.”
Quickgrind recognises that the dental industry has been plagued by low-cost and low-quality cutting tools sold by dental consumables and machine tool distributors at inflated prices. Rather than exploiting this industry, Quickgrind’s approach is to collaborate with customers and support them through its Infinite Possibilities program. The Tewkesbury manufacturer has published a cutting tool brochure for the dental industry, with full support available for manufacturers.
In the past 12 months, Quickgrind has worked closely with manufacturers such as Optadent Solutions, Element Digital Solutions, PRO4 DENTAL, Beaumont Ceramics, Radiant Dental Laboratory, and countless others, including Bristol CADCAM and Hexagon.
Commenting on the relationship with Quickgrind, Antony Wainwright, Company Owner at Optadent Solutions, says: “We were getting frustrated with cutting tool issues when milling titanium and chrome cobalt dental restorations. Typical issues were tool breakage, poor tool life and inadequate reach. By partnering with Quickgrind, we now have a cutting tool supplier whose products have helped us achieve a 40% improvement on tool life, reduced production costs and more stable milling processes.”
“By utilising Quickgrind’s Infinite Possibilities® process, we have created our own tooling suite for which we can tailor our milling strategies. This has reduced cycle times significantly with no detrimental effect on quality. Quickgrind has helped us optimise our CNC milling strategies using the latest cutting tool technologies to improve quality, cycle times, and costs. This willingness to collaborate sets them apart from other cutting tool suppliers in the dental market.”
Adding to this testimonial, Dan Barber, Company Owner at Element Digital, says: “Quickgrind doesn’t just want to sell us milling tools; they want to work with us to understand our machining requirements, workpiece materials, and quality expectations and to ensure their tools provide improved performance. We have seen huge improvements in tool life and consumable costs using their Zodiac, Gladiator, and Ribcutter ranges across all materials from pre-sintered zirconia to titanium and chrome cobalt.”
We are now interested in applying Quickgrind’s Infinite Possibilities® methodology for producing non-standard tooling to maximise the capabilities of our CAM systems and CNC milling machines, thereby reducing our cycle times and improving our overall efficiency.
With end mill ranges from the Zodiac, Rib Cutter, and Typhoon to the Orbis, Spectre, and Lynx, along with the infinite possibilities of bespoke solutions, Quickgrind has an engineer and a solution to support the demands of this specialised industry sector. Quickgrind’s Mark Aspinall concludes: “Dental laboratory owners are open and willing to collaborate with a desire to learn and utilise their machining capabilities. There are lots of best practices that should be shared between industrial machining and dental labs that would benefit both sectors. The level of automation I have seen in dental milling has genuinely blown me away, and dental labs could benefit more from cutting tool and milling knowledge to utilise the machine capabilities they have. This will help reduce cycle times, improve tool life, minimise downtime, increase capacity, and reduce operational costs.”
Precision in medical practice Precision in medical practice
In the world of medical manufacturing, where precision is paramount, the production process is key. From crafting bone screws to fabricating complex hip replacements, there’s a high demand for accuracy, reliability, and efficiency. Annika Langéen, Vice President of Offer Management and R&D expert in metal cutting tools at Sandvik Coromant, explains how small part machining supports precise medical device manufacturing.
The medical device industry encompasses various products designed to diagnose, monitor, and treat medical conditions. From diagnostic equipment to implantable devices, the industry caters to the needs of healthcare professionals and patients worldwide. Today, according to the World Health Organisation (WHO), there are an estimated two million different medical devices, categorised into more than 7,000 device groups.
Manufacturing components for medical devices presents challenges that demand advanced machining solutions. End users rely on these devices being manufactured to the highest quality, as products that do not meet quality standards can cause massive disruptions.
Machining challenges
From a machining perspective, the size and complexity of components require micron-level precision, so any manufacturing process must offer accurate end products. The materials used for a wide range of medical device components—typically titanium, stainless steel, and special alloys are selected due to their resistance to corrosion and wear. However, machining must address issues around tool wear, heat generation, and surface finish.
There’s also the issue of productivity. Generally, there is an imbalance between the cost of development and what the market is willing to pay for in any industry. To bridge that gap, manufacturers must continuously increase efficiency and productivity. Sandvik Coromant estimates that manufacturers waste between 10% and 30% of material in their machining processes, with a typical machining efficiency of below 50%, which includes the design, planning, and cutting phases.
To overcome this, Sandvik Coromant focus on reducing non-cutting time to ensure maximum productivity. Tools are designed to be highly flexible and modular and make use of high-pressure coolant to maximise uptime. To illustrate Sandvik Coromant’s medical device tool and machine success, let’s take the example of bone screw manufacturing. Bone screws may be used alone in reconstruction or reparative surgery or with other hardware devices, such as plates, to fix them to the bones. With such a wide array of applications, bone screws are typically long and thin and manufactured for different body parts. They’re generally produced in quantities of between 30 and 1,000 using thread whirling. Here, a cutting tool is mounted on a rotating spindle, which is fed into the workpiece while it rotates. The cutting tool typically has multiple inserts.
During thread whirling, the workpiece rotates on its axis while also being moved longitudinally along its axis. Meanwhile, the cutting tool rotates around the workpiece.
Sandvik machining solutions for sliding head machines use the CoroMill® 325 whirling system, a dedicated whirling unit, and a high-pressure coolant pump with a filter. The CoroMill® 325 is designed specifically for medical device manufacturing, producing special thread forms at high tolerances. The machine completes single-pass machining from stock diameter to reduce the cycle time by minutes and is easily set up to minimise downtime. All Sandvik Coromant thread whirling inserts are available in GC1105 — the first-choice medical grade.
Sandvik Coromant also offers an extensive range of advanced tooling and machining solutions for many additional devices, including hip joints, pedicle screws, and bone plates. Precision machining is essential as medical device manufacturing continues to evolve and become more competitive, driven by advancements in materials, design, and manufacturing technologies.
Hexagon enhances hip prosthesis production
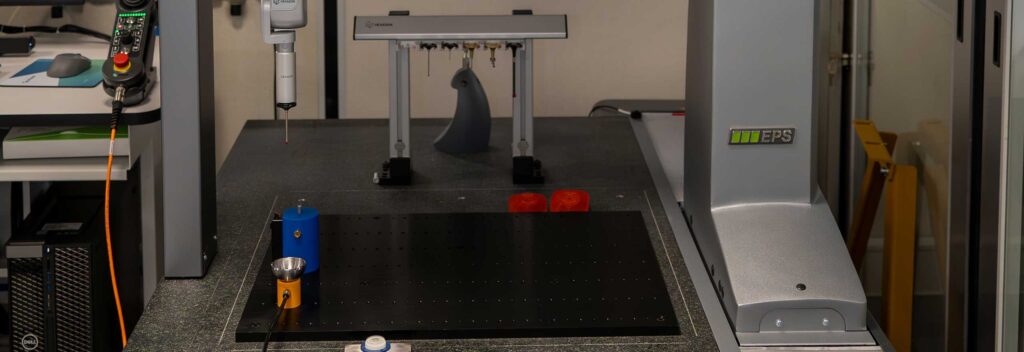
Dedienne Santé, a French medical device manufacturer specialising in hip prostheses, has significantly improved its quality control process by implementing three advanced Hexagon CMMs. These technologies have enhanced measurement accuracy and reduced inspection times by 20%, setting new standards in medical device manufacturing.
Founded in 1986 and based in Mauguio, France, Dedienne Santé is a leading SME specialising in surgical products, particularly dual-mobility hip replacements. As a manufacturer of high-precision prostheses, the company must adhere to strict industry standards, where any deviation can lead to serious consequences. Ensuring complete conformity at every stage of production is essential.
Improving quality control
with precision technology
To enhance the quality control process for its hip prostheses, Dedienne Santé aimed to automate the dimensional measurement of critical components such as the cup (half-sphere part), liner, femoral head and stem. These parts must be measured precisely during production and final inspection to ensure conformity with strict medical standards.
Previously, these measurements were conducted manually, which required significant time and effort. Dedienne Santé collaborated with Hexagon to address this challenge and provide reliable, accurate, and swift measurement solutions.
To meet Dedienne Santé’s needs, Hexagon deployed one GLOBAL Scan+ CMM and two retrofitted CMMs. These machines are equipped with highly accurate HP-S-X1 scanning probes and rotating probe heads, which are ideal for measuring roundness and sphericity. The systems also feature PC-DMIS metrology software that simplifies the measurement process, along with an Eco Mode that automatically shuts down the system when not in use, promoting energy savings.
The user-friendly software, combined with automated and visual execution methods, enables operators to assess part conformity with just a few clicks. “We chose Hexagon CMMs for their ability to measure dimensions and circularities down to a hundredth of a millimetre. The scanning sensor is essential for checking our prostheses, where high precision is crucial,” says Alexis Lecomte, Quality Control Manager at Dedienne Santé.
Significant gains in productivity and precision
The implementation of Hexagon’s solutions has brought multiple benefits to Dedienne Santé. It has increased precision as the CMMs meet the high-precision demands of the medical sector, ensuring each part conforms to stringent dimensional standards. The automated measurement process has resulted in a 20% reduction in inspection times, allowing operators to focus on other value-added tasks. For example, operators can run the inspection program and return to machining the parts, optimising the workflow.
The intuitive PC-DMIS software simplifies the inspection process, enabling operators to perform quick self-checking and automated in-process inspection and final control, improving ease of use.
“Hexagon’s solutions have significantly improved our productivity. For instance, inspecting a hip replacement cup now takes 20% less time, and we can perform inspections without constant supervision,” adds Lecomte.
Dedienne Santé values Hexagon’s precision, speed, and simplicity, as well as the ongoing support they receive. They also appreciate how Hexagon helps maintain high-tech manufacturing capabilities at their French Mauguio facility, ensuring they meet evolving production requirements.
“We must partner with suppliers who can help us maintain fast, productive manufacturing in France. Hexagon plays a key role in supporting our operations and ensuring we stay competitive in the global market,” says Ludovic Toledo, CEO of Dedienne Santé.
Dedienne Santé’s Commitment to Sustainability
Dedienne Santé is also committed to sustainable development and reducing its carbon footprint, as evidenced by its Coq Vert label, which recognises its efforts to minimise greenhouse gas emissions throughout manufacturing. With Hexagon’s solutions, Dedienne Santé can further its commitment to sustainability while maintaining top-tier manufacturing quality.
“We’re proud to have earned the French Tech label and the Coq Vert label, which reflect our ongoing dedication to innovation and sustainability. Hexagon’s support is crucial in helping us meet these high standards,” concludes Toledo.
Starrag ensures precision without compromises
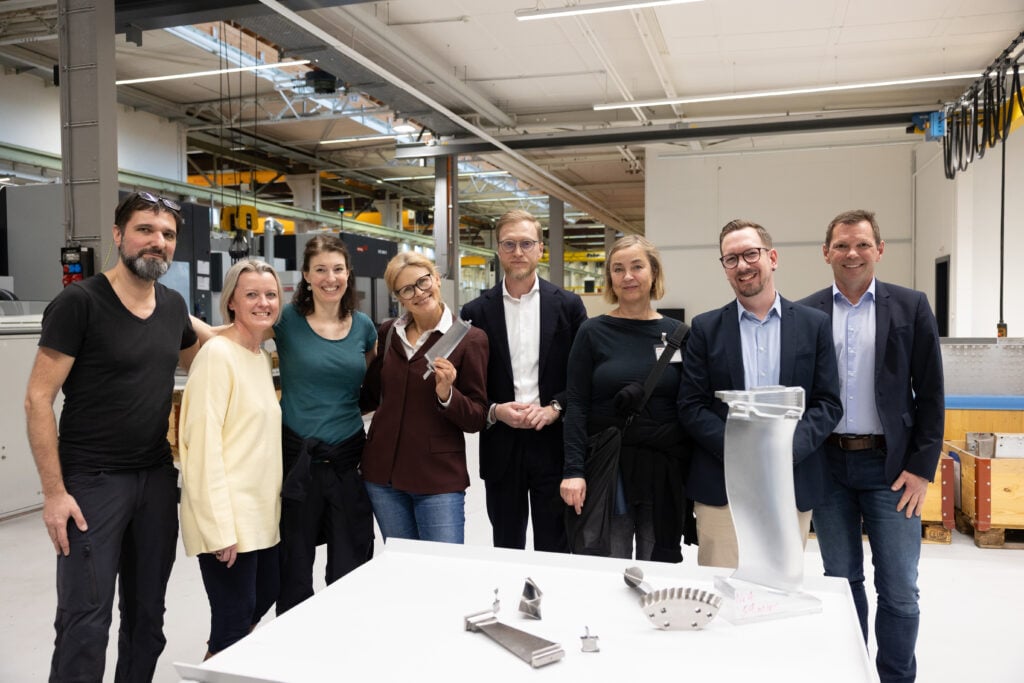
Starrag develops and produces manufacturing solutions for many of the aerospace industry’s leading manufacturers. As part of a pilot project to shorten the measuring times for turbine blades, the Swiss company was the first in the world to work with the ZEISS PRISMO fortis CMM.
Customers react with fascination and great amazement when they see how accurately and quickly turbine blades can be measured on a ZEISS PRISMO fortis with ZEISS CMM Acceleration Mode for aerospace applications. Roland Ziltener, Plant Director at Starrag AG, Rorschacherberg, says: “Speed and maximum precision didn’t go together for a long time.”
Customer requirements have top priority
Customers from all over the world come to Rorschacherberg with their specific tasks to obtain suitable machining centres to produce turbine blades and other aircraft applications. Starrag designs the respective production solution with the appropriate fixtures based on the specified requirements for the number of units or running time of the components. Customers often want a complete solution that ranges from machine and tool to metrology programming.
For Ivan Nytsch, Head of Global Customer Segment Aerospace at ZEISS, Starrag is ‘an ideal pilot customer’. This is also because the provider of complete solutions is very familiar with its customers’ processes. ZEISS has responded to the aerospace industry’s challenge of measuring aerospace components with high precision, reliability and speed by expanding the PRISMO family with the ZEISS PRISMO 7/12/7 fortis CMM
Fascination for a new solution
Roland Ziltener, who was Head of Quality Management at Starrag says: “We had a look at the machine and were immediately impressed.” To check whether the new development delivers the required precision despite the considerable optimisation of the measuring time, all turbine blades manufactured by Starrag on behalf of partner customers were measured with the ZEISS PRISMO fortis over 18 months. As the size, material and geometry of the turbine blades are different, the machine was “widely tested”, according to Ziltener. To evaluate the accuracy of the ZEISS PRISMO fortis, the measurement results were compared with reference values from the ZEISS PRISMO navigator.
During the pilot phase, Ziltener and Nytsch agreed that Starrag and ZEISS worked closely together. For example, the measurement data was discussed together in regular meetings. ZEISS used this information to optimise further the start-up and acceleration behaviour of the rotary table and the machine. ZEISS also simplified the usability of the machine and the creation of test plans during the pilot phase.
Turbine blades and blisks are not only subject to stringent requirements but also cost companies a lot of money. Experience has shown that quality assurance accounts for 20% of total production costs and 25% of total production time. The pilot project showed that productivity in the measurement of turbine blades can be significantly increased with ZEISS PRISMO fortis. The standard measurement, which took four minutes and 30 seconds at Starrag and delivered accurate and reproducible results, was reduced to 70 seconds during the pilot phase. This saves time, “which gives us greater flexibility in the selection of parameters and workpieces to be measured and helps us to optimise our production processes,” emphasises Ziltener.
Starrag acquired the measuring machine at the end of the pilot project to measure turbine blades, which are produced as a proof of concept during the acceptance of the machining centres assembled at the site by the customer. The turbine blades, which are machined for a handful of customers at the Aerospace & Turbine Competence Centre, continue to be inspected using the ZEISS PRISMO fortis.
R&G makes triple Mazak investment
ANorthamptonshire-based precision engineering firm has invested significantly in Yamazaki Mazak machine tools to enhance the productivity of its turning operations. Established in 1974 as a supplier to Northampton’s iconic shoe industry, R&G Precision now specialises in producing complex parts for various sectors, including motorsport, aerospace, general subcontracting, and oil and gas.
Shortly after taking over R&G Precision from his retiring father-in-law in 2024, Managing Director Vincenzo Chiarelli decided to revamp the company’s turning operations after identifying the adverse impact of lengthy set-up times for its previous lathes on both productivity and profitability. “I took the decision to close our turning section and effectively start from scratch,” Vincenzo explains.
“Someone came in to price up our old machines and, in stages, we got rid of them completely. “We then sat down and said to ourselves, ‘where do we go from here?’, and that’s when Mazak came in. Two of our employees had already worked with their machines before and told me they were the gold standard, so we decided to go for it.”
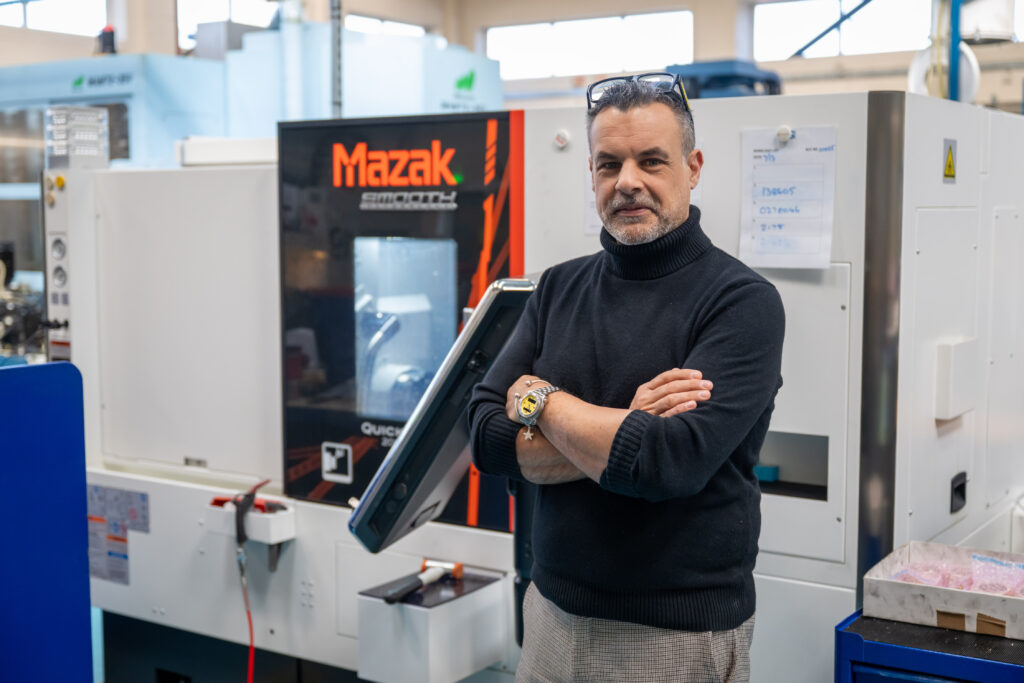
To date, Yamazaki Mazak has delivered two turning centres to R&G Precision, a QT-200MSY and a QT-250MSY, both of which have allowed the firm to significantly boost its manufacturing output. “At first, I was quite sceptical about what these new machines could do. But after Mazak installed the first machine, we were getting jobs up and running in as little as three hours, more than twice as fast as our old machines. At this point, I was completely sold on the idea, so we then got the second Mazak machine in, and it’s had exactly the same impact on productivity as the first,” Vincenzo continues.
Following the successful integration of both the QT-200MSY and QT-250MSY, R&G Precision has now ordered a QT-250MSY turning centre as part of its ongoing investment in Mazak’s high-performance machine tools. “Given the speed with which the first two Mazak machines are operating, and the ease of setting up and using them, it’s made total sense to invest in a third machine, and we’re looking forward to its arrival,” Vincenzo adds. “We’re so impressed with what Mazak has delivered to date, and with all the technical support that they’ve given us. We’re delighted to have them as our turning supplier of choice.”
Jason Butler, Sales Director at Yamazaki Mazak UK & Ireland, said: “R&G Precision provides a prime example of the transformative impact that our world-class CNC turning centres, coupled with stand-out service support, can have on productivity. “As a successful and long-running engineering firm, R&G understands just how important it is to evolve with the times, and this investment is reflective of that fact. We look forward to working with Vincenzo and his team in the coming months and years to help the business meet its ambitious.”
Atkinson Equipment slashes lead-times by automating prismatic machining
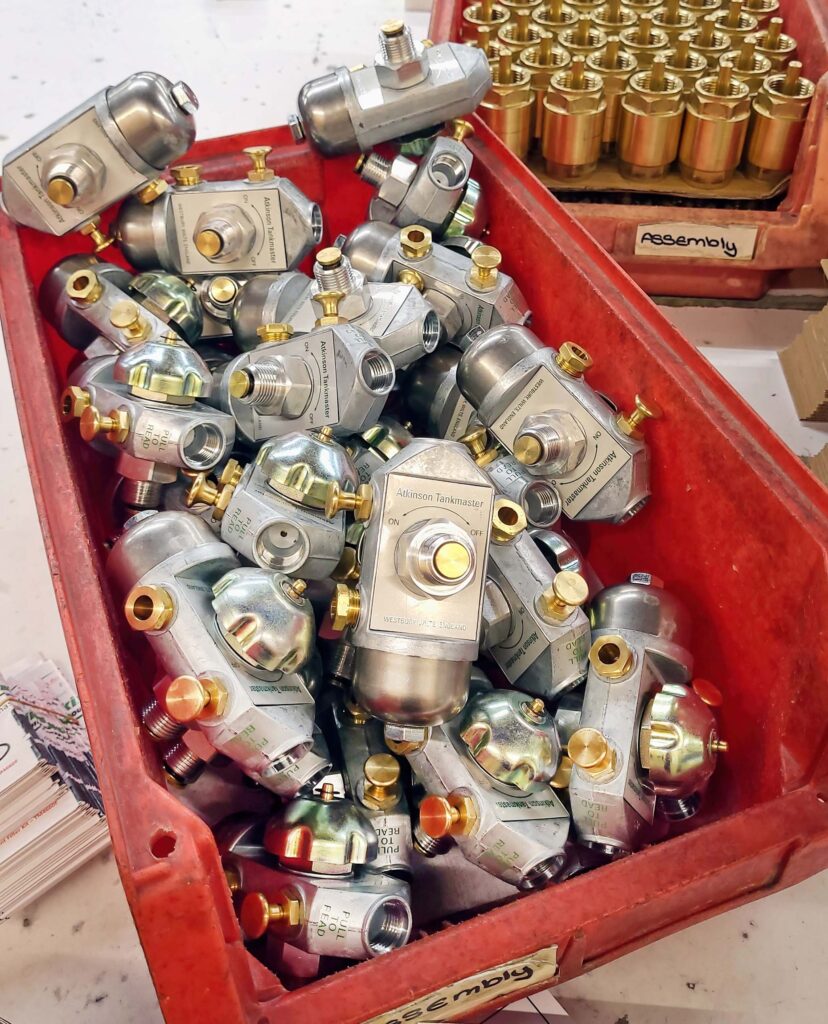
Aleading OEM specialising in the design and production of equipment for oil heating and diesel tank applications, as well as being a subcontract engineering firm, Atkinson Equipment has dramatically reduced lead-times following investment in a Brother Speedio U500Xd1 5-axis machining centre equipped with Tezmaksan CubeBox automation from Whitehouse Machine Tools.
Adam Walford, Engineering Group Sales Manager at Atkinson Equipment explained: “The automation solution from Whitehouse has increased our productivity dramatically. We have typically halved lead-times from 12 weeks down to six for complex subcontract parts and reduced them even further when making components for our own products, say from a month down to one week.”
“Since automating the milling side of the business, we have also seen a reduction in the bottleneck we previously had when parts arrive from our turning section for prismatic machining. Our ability to get product out of the door to our customers is through the roof. It is helping us to win new business in the subcontract area, as well as to grow our OEM division.”
Based in Westbury, Wiltshire, Atkinson Equipment is required to manufacture large volumes of parts for its own refuelling and liquid transfer products, which it has been doing for over 50 years. It also needs to produce a high mix of smaller volumes for the subcontracting division, which has been running for half that time, but which is growing rapidly. This dual role places significant demands on its manufacturing capabilities and was pivotal in the investment in the automated Brother-Tezmaksan cell.
The relationship with Whitehouse Machine Tools began in 2019 with the purchase of a Brother 5-axis CNC machining centre, a Speedio S700X1 equipped with a Lehmann rotary-swivelling compound table. This initial investment allowed the company to machine complex parts on multiple faces in a single set-up, significantly improving efficiency. Having experienced the benefits, Atkinson Equipment went on to buy a Brother Speedio M200Xd1 trunnion-type 5-axis machining centre in 2023, initially to manufacture a complex aerospace part.
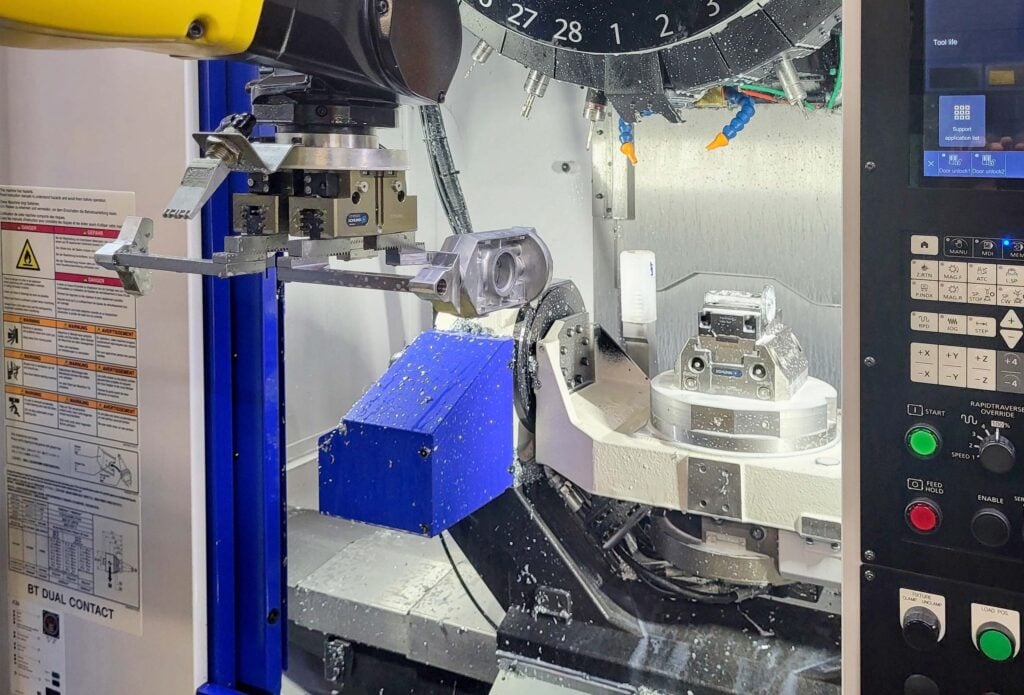
At first, the idea was to automate the existing S700X1 on site with the Tezmaksan CubeBox, but this would have necessitated an upgrade to the Lehmann equipment to provide pneumatic supply for automatic clamping of parts. However, a visit to the Whitehouse showroom in Kenilworth revealed the potential of automating a Brother U500Xd1 5-axis machining centre instead, as this was the configuration being demonstrated.
Mr Walford explained, “Looking at the cost differential between just the Tezmaksan compared with the automation plus the U500Xd1, it made sense to go for the automated set-up complete with the new 5-axis machine. We needed extra capacity anyway, so it made absolute sense for us, especially as it was more affordable than we anticipated.”
The Brother U500Xd1’s large working volume for the compact footprint, 28-tool ATC capacity and integrated rotary joint for pneumatically actuating the fixtures proved ideal for the Westbury firm’s production needs. Whitehouse provided comprehensive support during the set-up process, assisting with tray template design for holding raw material and finished components, as well as the end-of-arm tooling with double grippers for handling them. The automated cell’s sensors create a safe working environment, without the need for traditional guarding.
Mr Walford concluded: “It was quite daunting at first taking on a completely new piece of technology like this, but we were confident with the support that we would get from Whitehouse and their ability to guide us through the process to where we are now.”
“The relationship with this machine supplier is key. We’re very happy with their service and support, it’s really brilliant, and it gives us confidence to keep buying from them.”
TaeguTec unlocks the productivity potential for machining superalloys
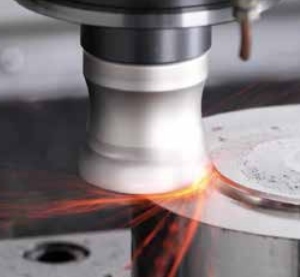
As manufacturers strive to push the boundaries of what’s possible, the role of cutting tool technology has become increasingly crucial. One company at the forefront of this revolution is TaeguTec, a global leader in developing innovative ceramic cutting tools.
In an interview, Jae-Wook (Jay) Lee, the Milling Product Manager at TaeguTec’s world headquarters in Daegu, South Korea, discussed why ceramic tools are increasingly penetrating sectors such as aerospace and power generation.
Traditionally, machining high-temperature alloys such as Inconel has posed significant challenges. These materials are notoriously difficult to machine. Carbide tools often struggle to meet the demands, resulting in premature wear, reduced tool life, and compromised productivity.
Ceramic tooling has developed over the past 20 years, with initial applications focused on machining cast iron and hardened materials using silicon nitride ceramics. However, as the industry shifted towards machining tougher alloys like nickel-based superalloys, new ceramic grades are necessary. This led to the creation of SiAlON ceramics, specifically engineered to address the unique challenges associated with machining HRSA.
The key difference between traditional silicon nitride ceramics and SiAlON is their ability to withstand chemical reactivity and extreme heat. Where silicon nitride tools would rapidly degrade due to early wear, SiAlON ceramics remain stable under thermal loads.
“For machining HRA and HRSA materials, like Inconel, the silicon nitride ceramic inserts we have developed are a game-changer,” explains Lee. “The properties of our latest ceramic materials vastly differ from those used for machining cast iron or hardened steel. We’ve engineered our SiAlON-based ceramics to excel in these challenging applications.”
The key advantages lie in the ability to withstand extreme temperatures and stresses encountered during machining of superalloys. “Carbide tools tend to react with the workpiece at high temperatures, leading to rapid wear despite the low cutting speed. “Our ceramic inserts are much more resistant to this thermal wear, allowing us to push cutting speeds to unprecedented levels.”
Boosting Productivity with Ceramic Inserts
One of the most striking benefits of TaeguTec’s ceramic cutting tools is their ability to dramatically increase productivity. “We’ve seen cases where our ceramic inserts can achieve cutting speeds at a minimum of 20 times faster than traditional carbide tools,” Lee reveals. This translates to a massive boost in metal removal rates and overall efficiency.”
The secret behind this performance lies in the design and geometry of TaeguTec’s ceramic inserts. “We’ve developed a high-feed shape that allows us to increase both the cutting speed and the feed rate,” explains Lee. “This, combined with the inherent properties of the ceramic material, enables us to push the boundaries of what’s possible in terms of productivity.”
To illustrate the point, Lee shares a case study from a leading aerospace company in Brazil. “They previously used solid carbide tools for machining Inconel 718 components, with a cutting speed of around 35m/min and a metal removal rate of just 10.5cm³/min. After switching to our ceramic inserts, they increased the cutting speed to 1000m/min and the metal removal rate (MRR) to an astounding 213cm³/min – a 20-fold improvement in productivity!”
Overcoming the Mindset Barrier
Despite their advantages, ceramic tools have faced resistance in markets such as the UK and Western Europe. Many machinists remain cautious about potential tool breakage and short tool life. There is a strong preference for the perceived durability of carbide tools, even though carbide struggles with high-temperature alloys and requires substantial coolant use to manage heat.
Ceramic inserts have proven themselves in global aerospace hubs and power generation sectors. While tool life for ceramics may be limited (sometimes as little as five minutes), the incredible increase in cutting speed and productivity far outweighs the trade-off.
Typically, a cutting tool averages 3% of the machining cost, with labour, hourly machine rates, power consumption, and business overheads absorbing the remaining 90+%. If a ceramic insert can deliver stratospheric machining results that drastically improve the machine utilisation rate, reducing the 90+% of machine cost whilst slightly increasing the 3% tooling cost, it doesn’t take a rocket scientist to work out the benefits of ceramic tooling.
For example, some aerospace manufacturers keep 50 identical ceramic tools preloaded in their machines. This strategy optimises throughput by more than tenfold, rendering the shorter tool life irrelevant. After all, the tool life is only shorter in minutes – in terms of material removal rate (MRR), ceramic tools far exceed the performance of carbide.
To address challenges related to perception, TaeguTec has made significant investments in robust clamping systems and insert geometries. “We’ve designed ceramic inserts with a high-feed shape that boosts productivity but also enhances the stability and reliability of the cutting process,” explains Lee.
“It’s not just about the tool – it’s about changing the entire machining strategy,” says Lee. “We work closely with our customers to help them understand the benefits of running at higher speeds and lower depths of cut.”
In a recent case, a new screw-type ceramic insert- claimed to be the first of its kind globally- was tested in aerospace manufacturing. Despite initial concerns about clamping stability and heat transfer, the insert performed flawlessly in high-temperature machining trials.
Expanding the Ceramic Frontier
Modern ceramic tooling isn’t just about material composition. Geometric innovation is crucial in maximising the performance of ceramic inserts. TaeguTec has introduced high-feed geometries and unique clamping designs like the screw-type inserts that further push the boundaries of what ceramics can achieve.
Taegutec has not only developed industry-leading ceramic grades that outperform rival products, but it has also utilized its position as a world leader in high-feed machining to incorporate innovative cutting geometries into its ceramic product lines.
TaeguTec has expanded its ceramic ranges to include round inserts and high-feed geometries, tailoring its ceramic product lines to cover a broader array of machining scenarios. The latest addition to the indexable CeramicSFeed line features a range of 16, 20, and 25mm diameter tool holders with two or four insert pockets that accommodate TaeguTec’s latest BNGX 06 size inserts. These smaller inserts enable more insert positions per tool, allowing for higher productivity.
“We’re constantly pushing the boundaries of what’s possible with ceramic technology,” says Lee. One focus area is developing ceramic grades suitable for machining a wider range of materials, including stainless steel and titanium alloys.
TaeguTec has also developed what is claimed to be the industry’s first screw-type insert clamping system for indexable ceramic tools. “This is a true breakthrough in ceramic cutting tool design,” Lee enthuses. “By incorporating a unique screw-type clamping mechanism, we’ve addressed the common concerns about insert breakage and clamping issues that have historically held back the adoption of ceramic tools.”
“Not only does it provide a secure and stable clamping solution, but it also allows us to make the cutter diameter smaller. In the end, it can replace solid carbide end mills by increasing the cutting speed and feed rate further, unlocking even greater productivity gains for our customers,” explains Lee.
The Future of Ceramic Cutting Tools
As the aerospace and power generation industries continue pushing boundaries, Lee believes ceramic cutting tools will play a pivotal role. “The trend in the industry is clear — manufacturers are increasingly focused on maximising productivity and efficiency while also considering the environmental impact of their operations,” he says.
“Ceramic inserts are perfectly positioned to meet these demands, with their ability to deliver unparalleled metal removal rates and their inherent eco-friendliness, as they eliminate the need for copious coolant usage.”
Looking ahead, Lee envisions a future where ceramic cutting tools become the norm rather than the exception in high-performance machining applications. “We’re already seeing a significant shift in mindset, particularly among more forward-thinking manufacturers willing to embrace new technologies,” he says.
Ceramic cutting tools represent a paradigm shift in machining difficult materials like Inconel and other superalloys. By overcoming the traditional limitations of carbide tooling, ceramics unlock unprecedented productivity, efficiency, and sustainability. For industries focused on high-temperature applications, ceramic tooling is not just an alternative; it’s the next standard.
Kern automates production at WLR
With a skills shortage in the manufacturing industry, WLR Precision Engineering Ltd. had a burning desire to automate its high-precision production while maintaining the skill levels of its highly qualified team of engineers. The opportunity to increase throughput, precision, quality and consistency prompted the Wilford-based subcontractor to purchase a 5-axis Kern Micro Vario machining centre with an Erowa Compact 80 automated pallet loading system from Rainford Precision.
Located just south of Nottingham, WLR undertakes everything from prototype work to small and medium batches for manufacturers in the oil exploration, medical and pharmaceutical sectors, to name a few. As a company ‘dedicated to precision’, the ISO: 9001:2015 certified manufacturer is already an existing Kern user, reaping the rewards of unparalleled precision and performance. In 2013, WLR installed a Pyramid Nano machining centre. Discussing why WLR invested in its second Kern machine, the automated Kern Micro Vario, Kevin Callon, Managing Director at WLR, said: “One of my regrets was not having some form of automation on the Pyramid Nano when we first bought it, despite having the option. There was no way we would have bought another Kern without some form of automated loading to maximise the running hours of the machine.”

Based on the precision of the Pyramid Nano, this regret was founded upon the realisation that the company needed extremely precise machining capacity for a range of higher quantity runs of extremely accurate components. With an 80-component Erowa pallet loading system and a 90-position automatic tool change, the Kern Micro Vario was the perfect solution.
Installed in September 2022, the introduction of the automated Micro Vario now enables WLR to run production continuously ‘lights-out’ whilst utilising the existing Pyramid Nano for smaller batch runs and one-offs during daytime working hours.
Kevin explained: “The consistency of the components produced on the new Kern is amazing and repeatable to the micron. The precision is so impeccable that we now channel as much work as possible through the Kern Micro Vario. It’s not only doing the really demanding high-accuracy work that it was purchased for but also undertaking the less demanding work that would normally be done on less precise machining centres.”
The Kern Micro Vario precision and repeatability are built upon the foundations of its thermally stable Ultra-High-Performance Concrete (UHPC) base that yield precision and repeatability of <1.5µm and <1µm, respectively.
From a specification perspective, the Kern Micro Vario has a compact X, Y, and Z-axis work envelope of 350 by 220 by 250mm, a -110° to +110° swivelling B-axis, and a 360° continuous C-axis. The tool changeover is less than 3 seconds, and the chip-to-chip time is 4.5 seconds – all feeding a high-speed 42,000rpm HSK 40 spindle. Incorporating the powerful Heidenhain TNC640 CNC control, 30m/min rapid rates and acceleration of 10 m/s², the Micro Vario demonstrates astounding flexibility, speed and precision in a compact floor area.
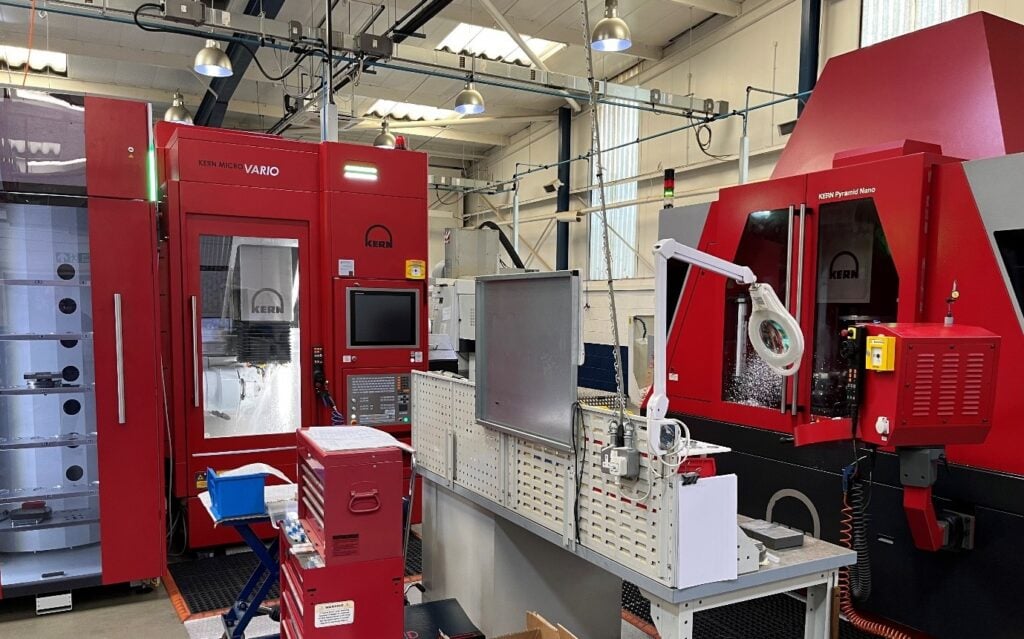
On another level!
Highlighting what distinguishes the Kern from other machine tools, Kevin states: “It’s definitely the accuracy and repeatability. There’s also a significant improvement in surface finishes. The Kern truly excels, particularly with harder materials. This excellence isn’t solely due to spindle concentricity but rather the entire package. It’s a very robust machine engineered to deliver remarkable repeatability.”
Kevin added: “Previously, we didn’t have enough of the right kind of work to keep it occupied. We began assigning other tasks to the machine to utilise its capacity. We now appreciate the advantages of this approach, given its repeatability. The tolerances we find difficult to maintain on other machines are effortlessly attained on the Kern. This level of precision and repeatability optimises operations further downstream in our business.”
Alluding to the Kern machine’s cost per part, Kevin adds: “Based on cost per part, the machine more than pays for itself. It completes jobs in one hit, faster and easier than other machines, and to tighter tolerances.”
Fast, versatile machine wins
Michael Phillips, joint owner with partner Wayne Robins of contract machining firm Atomic Precision, describes their recently purchased, Japanese-built Brother Speedio U500Xd1 as ‘a Swiss army knife of 5-axis machining centres.’ His comment is due to the 30-taper machine’s high quality, versatile functionality, compactness, and ability to complete an extensive range of jobs quickly and efficiently. Brother machines are sold and serviced in the UK and Ireland by Whitehouse Machine Tools, Kenilworth.
Founded in East Hendred, Oxfordshire, in 2020 by the two time-served mechanical engineering apprentices, who both previously worked in the machine shop at nearby Rutherford Appleton Laboratory’s space development facility, Atomic Precision specialises unsurprisingly in manufacturing components and assemblies for the space and scientific research sectors.
Over the next four years, a succession of 40-taper VMCs from another supplier arrived on the shop floor: three 3-axis models and two 5-axis machines. During that time, the subcontractor enjoyed an impressive growth rate of 50% yearly.
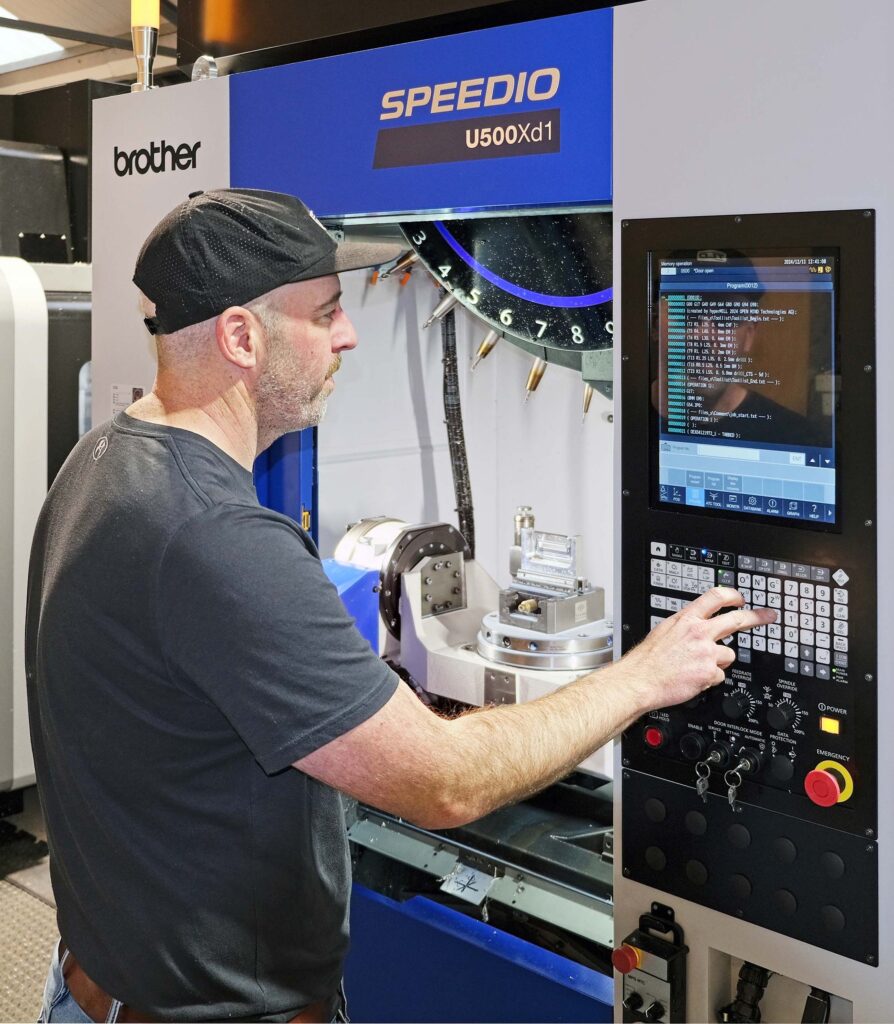
It was clear to the two partners, who work alone that the ongoing rate of growth was unsustainable without progression on the shop floor to more efficient machine tools and perhaps also automation to gain substantial periods of unattended production. They operate a single-day shift, and working longer hours is not part of their game plan.
As a first step to raising productivity, Whitehouse Machine Tools installed and commissioned the high-speed Brother U500Xd1 in September 2024. The partners learned of the machine at the Southern Manufacturing exhibition in Farnborough in early 2023. The order was placed after early hesitation regarding the smaller spindle interface, which later proved to be a non-issue and benchmarking a couple of other 30-taper machines on the market.
Mr Phillips commented: “The area taken up on our shop floor by the U500Xd1 is half of the space that one of our 40-taper 5-axis machines occupies, yet the 30-taper VMC produces larger parts. Not only that, but the Speedio finishes an identical component in two-thirds of the time, as the non-cutting elements of cycles are incredibly short, so tools are in-cut for typically 90% of the time during a cycle.”
“The linear axes accelerate at 2.2 g up to 56m/min, and chip-to-chip time is 1.3 seconds. Rotary positioning by the trunnion and table is similarly fast, and parts come off complete, resulting in rapid floor-to-floor times.”
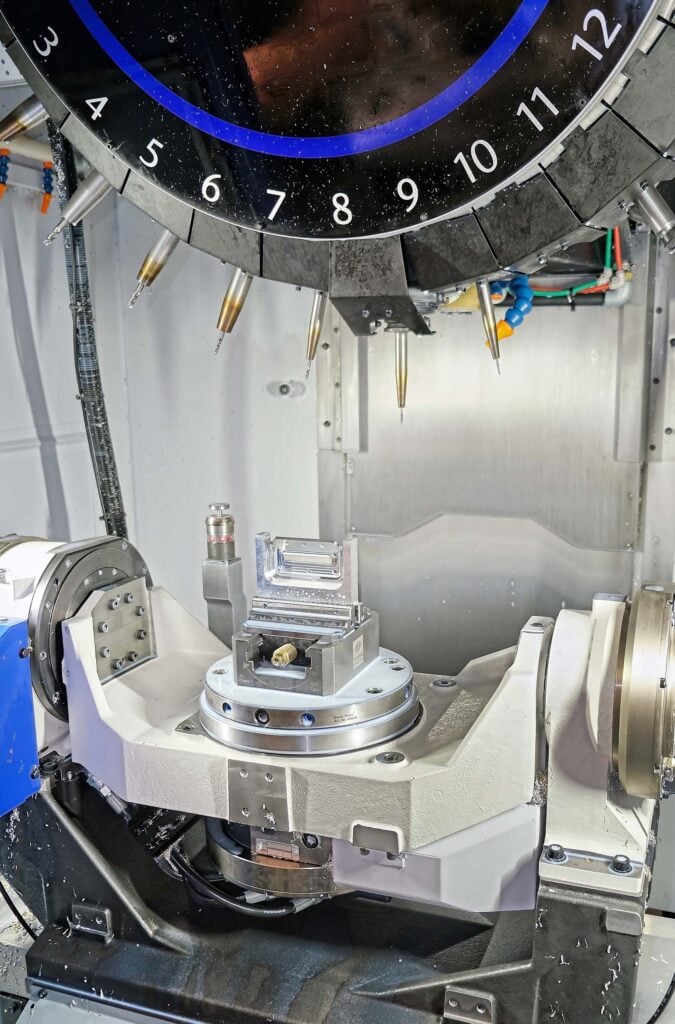
The machine installed in East Hendred is a well-specified version of the Speedio model, with a 16,000rpm 15kW spindle, 28-position tool turret, high-pressure coolant, and Blum tool and part probing. Axis strokes are 500 by 400 by 300mm, but multi-face machining of components up to 500mm in diameter by 270mm high and weighing up to 100kg is possible owing to the layout of the machining area.
As well as producing parts up to the maximum working envelope, the Speedio also machines tiny components requiring complex features cut with a 0.2 mm diameter end mill, hence the decision to opt for the highest speed spindle Brother offers. Towers are extensively used for fixturing multiple smaller parts to extend the walk-away time from the machine if individual cycle times are short. Batch size is usually up to 10-off, although often single prototypes are machined.
However, in November 2024, Atomic Precision received a huge order from a new customer for 400-off aluminium brackets requiring a 3+2 machining strategy, using the rotary axes to position the part. The subcontractor could not have accepted the contract if it had been unable to use the elevated speed of the Brother machine. A 5-axis, 40-taper VMC would have been too slow to meet the three-week lead time, so the subcontractor would have had to turn down the work. If more jobs involving quantities of several hundred starts coming in, automating the Brother and other VMCs on-site will go ahead imminently.
The factory processes various materials, including aluminium, stainless steel, brass, copper, tungsten, and tantalum. Mr Phillips advises that it is possible to hold ± 10 micron dimensional tolerance ‘comfortably’ on the Speedio, even without climate control in the factory.
Production times cut 50% with Heckert 5-axis
With the new Starrag HEC 800 X5 MT machining centre, the machining team at Neuson Hydrotec GmbH in Linz can machine complex housings with numerous holes at different angles with maximum precision – in a single clamping position and in half the time.
With around 50 employees, contract manufacturing is the largest business unit at Neuson Hydrotec GmbH. Walter Füreder, one of the two Managing Directors responsible for this division, says: “We generate around half of our turnover with our contract work. Twenty percent of this involves doing the groundwork for other business units.”
Components for injection moulding machines are also part of the recurring contract work, such as shredder shafts and bearing blocks, all supplied to machine tool manufacturers. Karl Kordik, Sales Manager for contract manufacturing, says: “We supply the largest proportion of our work, around 40%, to the plastics recycling sector.”
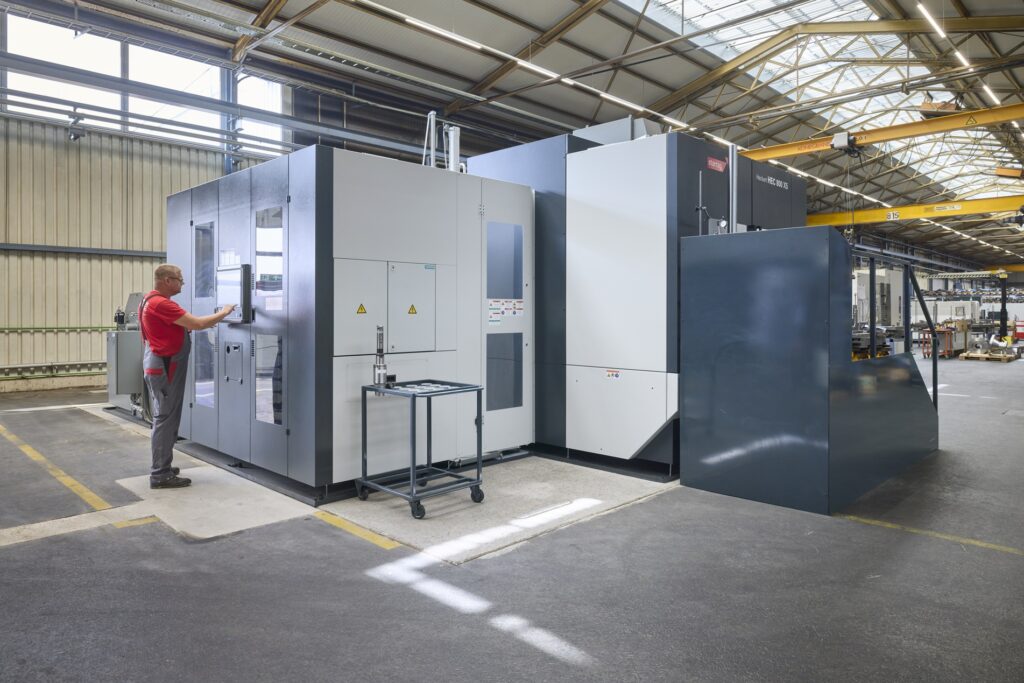
The services range from procuring raw material to CNC milling, grinding, lapping, honing, welding and superfinishing to pre-assembly. The contract manufacturing department has various CNC turning and grinding machines and several machining centres with pallet pools. The highlight is the HEC 800 5X MT 5-axis machining centre purchased in May 2024. This investment was triggered by a complex component for a plastics recycling machine that requires turning and milling, and numerous holes have to be drilled at different angles. In this recycling plant, the used plastics are heated to around 400 degrees after shredding. A spindle presses the liquefied mass through a plate with tens of thousands of holes about 0.2mm in diameter, which retains contaminants. It contains intricate contours and numerous channels through which the contaminated and cleaned plastic first flows. “One hole runs through the entire component, and other channels meet at a certain angle,” says Karl Kordik.
High precision is required for fluidic reasons where the channels must not be offset when they meet. “We manage this because we achieve a positioning accuracy per hole of less than 0.03mm. Although that doesn’t sound particularly difficult, the value corresponds to only a few μm per axis if the holes are drilled at 45 degrees.”
Until recently, the contract manufacturers were producing this housing on a vertical turning and boring mill and a three-axis milling machine, in seven clamping positions. When the customer ordered significantly larger quantities, Neuson Hydrotec decided to modernise production to reduce manufacturing times.
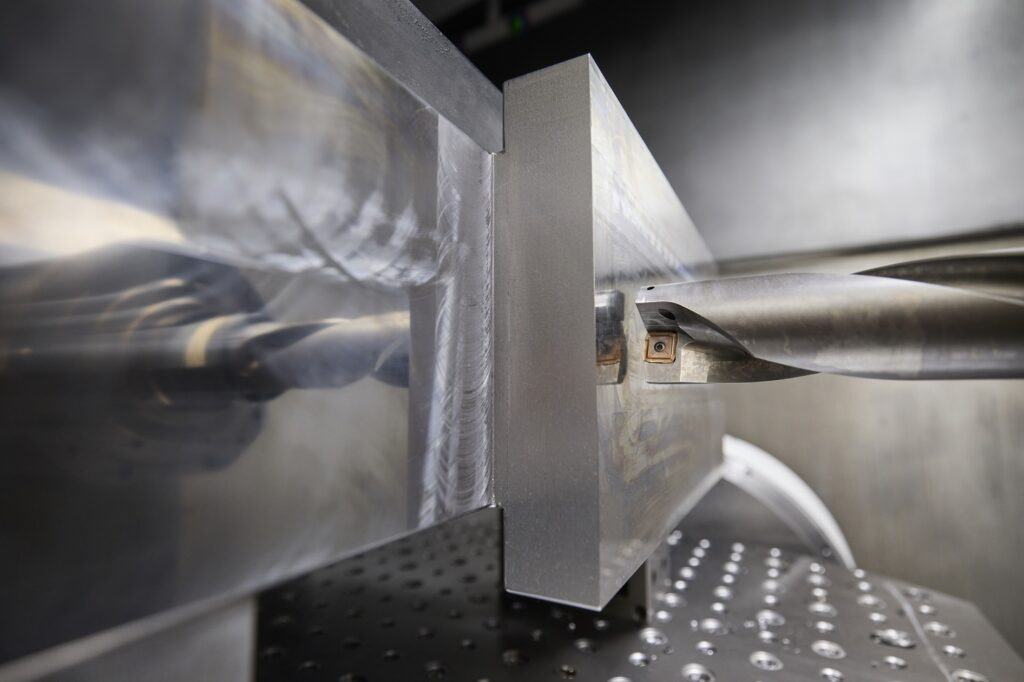
There were several reasons why the decision was made in favour of the HEC 800 5X MT. According to Kordik, one crucial factor was that the HEC 800 allows the component to be clamped vertically: “These components can only be clamped on a horizontal turning and milling centre with great difficulty. Fast, automated workpiece replacement is even more difficult. The HEC 800 has a standard dual pallet changer, enabling setup parallel to the primary processing time.”
On the HEC 800 5X, the 5th axis is located in the workpiece, not the tool. The decisive factor was the possibility of obtaining a bed extension along the Z-axis and an extended Y-axis. Kordik describes the background: “We want to clamp components with a length of 1.1m and drill through. The standard Z-axis path of 1.3m is insufficient for this.” Starrag supplied the HEC 800 5X MT with travel paths of 2,050mm along the Z-axis and 1,300mm along the Y-axis. “No other machine manufacturer had offered such extensions. We would have had to switch to much larger machines.”
The control software for interpolation turning was also on our ’to-buy list’. This is because the laser filter housing requires a 350mm hole offset from the centre by 8mm. “Thanks to the precisely controlled interpolation of the X and Y-axes, we can create this without any problems,” confirms Karl Kordik.
Producing the eccentric hole using interpolation turning saves more time. In the case of the filter housing, reducing the number of clamping positions from seven to one was possible. The time saving is 48%.
Longer production runs dictate move to sliding head
SFC (Europe) manufactures, stocks and supplies safety-critical and high-performance stud bolts, bolts, and nuts in ASTM and ASME grades for onshore, offshore, and subsea applications. They are mainly destined for global energy customers but are also used in the automotive, valve, heat exchanger and pump sectors. The Wolverhampton company has enjoyed impressive growth, from a turnover of £1 million when it was formed in 2013 to £15 million in 2024.
In the early days, the company served mainly the oil and gas, petrochemical, valve and renewable energy sectors, which involved turning batch quantities of anything from five to 500 parts, with the occasional run of 1,500. Then, in 2018, other industries started to show interest in the products, and today, the original markets account for only around half of the manufacturer’s turnover. Some of the more recent customers ask for similar, small to medium quantities, but frequently, they request 50,000 off, forcing SFC (Europe) to change how it viewed its turning and milling equipment.
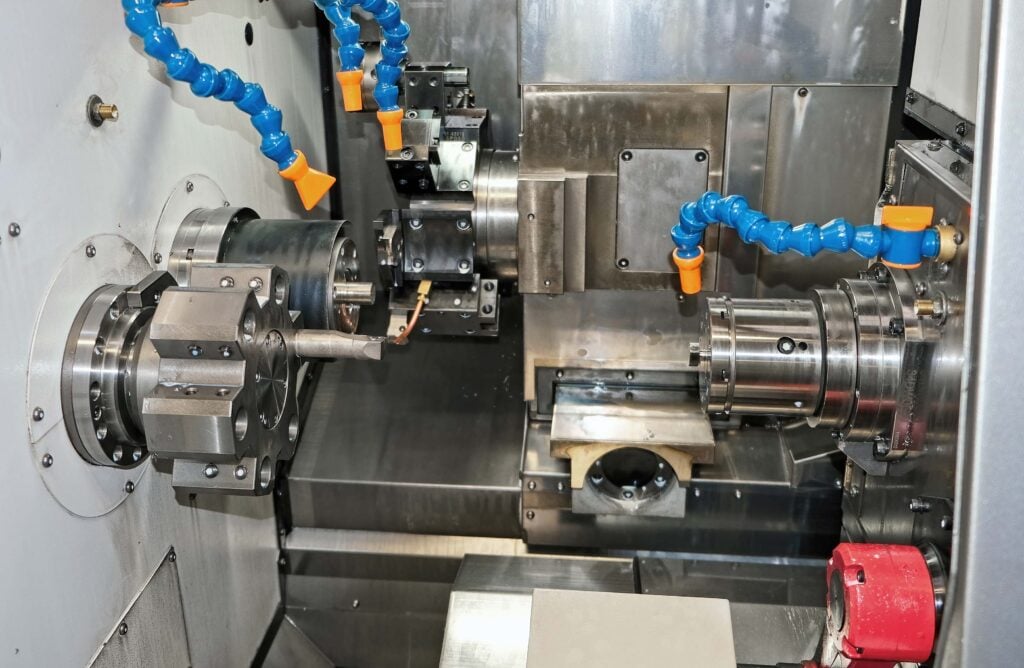
Operations Director Mark Edmonds said: “In the early days, we bought fasteners for stock and sold them worldwide, but within six months, we gained ISO 9001 and started manufacturing products, either to customer specification or international standards.”
“Our machine tool count was boosted in 2016 by acquiring another fastener producer. The capacity was sufficient for the quantities we were producing at the time. Still, a couple of years later, the larger quantities were being ordered by customers, necessitating a rethink.”
Part of the deliberations was shaped by the metals that needed to be machined. Along with carbon steel, they include stainless and superalloyed steel and nickel and titanium alloys. One nickel-copper alloy, Monel K500, is difficult to machine due to its ductility and abrasiveness. Any new turn-milling centre had to be robust enough to process these materials. It also had to be versatile and quick to set up, as urgent short runs were frequently ordered for next-day delivery while long-running jobs were in progress.
Since 2019, Mr Edmonds and his colleagues have been considering sliding-head bar turning owing to its suitability for producing large quantities of components, including unattended overnight. Covid delayed things somewhat, but by mid-2022, SFC (Europe) was ready to invest in new turning centres. It was, however, a pair of fixed-head lathes that was bought, as production staff in the Wolverhampton factory was unfamiliar with operating sliding-head equipment, and management wanted modern, productive lathes that would come on-stream quickly.
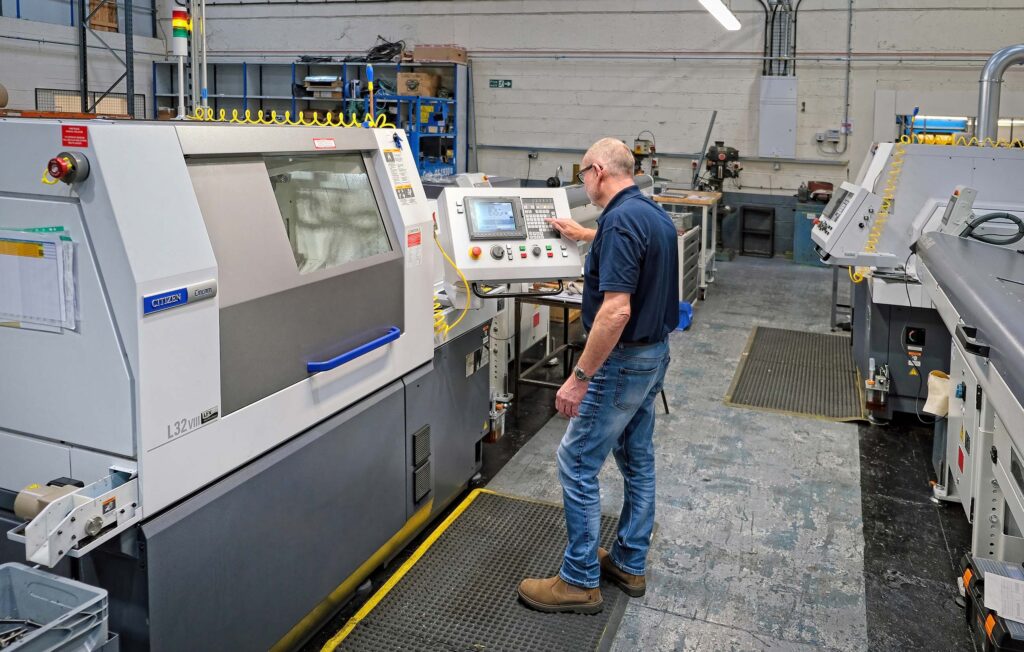
Two identical 7-axis Miyano BNA-42DHY twin-spindle, twin-turret, and bar-fed lathes were duly installed, the manufacturer’s first machines sourced from Citizen Machinery UK. The supplier was chosen after subcontractors within the fastener industry had been consulted, as well as Google, plus Citizen at one of its open houses. Demonstrations at the Brierley Hill Technical Centre, where faster than expected, one-hit cycles were shown to replace three or four separate operations successfully, clinched the deal.
A few years later, SFC (Europe) was ready to revert to introducing sliding-head, bar-fed lathes. The Miyanos had performed so reliably in terms of uptime and accuracy that Mr Edmonds looked no further than Citizen for the supply of two Cincom L32-VIIILFV turn-mill centres. Delivered and commissioned in April 2024, they mainly fulfil orders for higher volumes of parts. As traceability is often essential, the ability to engrave them in-cycle on the fast, nimble machines saves a separate operation and contributes to maximising production output.
The nominally 32 mm bar capacity lathes can machine components from up to 38 mm bar with the guide bush removed, which saves material due to shorter remnant lengths. Accordingly, one L32 is permanently set up without the guide bush for producing parts up to about 2.5 times diameter, while the other has the guide bush in place for turning longer components.
Direct route to success with Dugard
When Direct Engineering & Site Services Ltd opened its doors in Sheepbridge, it was a small fabrication shop. Fast-forward 28 years, and the Chesterfield company operates from a 40,000sq/ft premises with five divisions that deliver diverse services to customers throughout the UK and Europe.
Direct Engineering specialises in the installation of material handling equipment, vacuum conveying, and chiller pipework systems. It has evolved from a fabrication company, adding services such as machining. Dugard has supported the company with its exceptional range of machine tools with the latest acquisition being a Dugard SMEC SL 3000LM turning centre.
Ray Woolley from Direct Engineering says: “We started in 1997 as a fabrication company that initially machined on a smaller scale. As time progressed, we saw the need to expand our machining operations as our customers requested more machining services, as well as welding and fabrication. So, we grew on the milling and turning side and invested in CNC machines.”
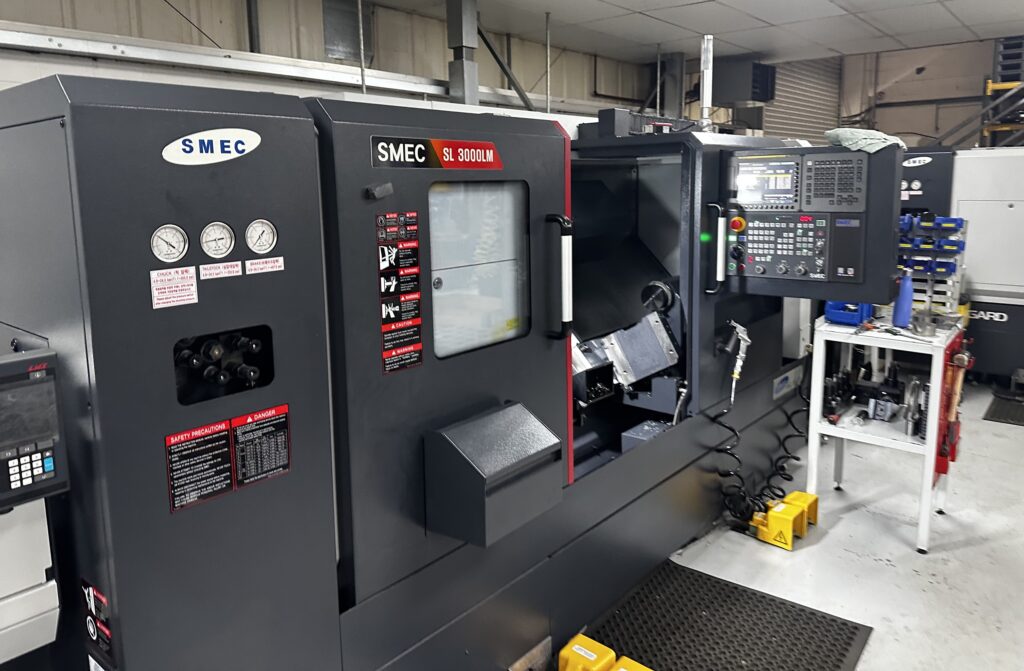
To accommodate a variety of materials, the versatility of the Dugard SMEC SL3000LM machine is reaping rewards for the Chesterfield manufacturer. Ray continues: “Each material has its challenges and how it cuts, but with a wide listing of materials and types of work, Dugard helped us with a machine breakdown and quickly got us up and running. For that reason, we continued our relationship with Dugard. We’ve had a lot of good productive advice from Dugard on how to deal with this diverse range of materials.”
However, the latest SMEC SL 3000LM was not the first Dugard machine to arrive at the Derbyshire company. Direct Engineering has a range of Dugard machines, including the SMEC PL2500, PL35 and PL45 turning centres. Discussing the purchase of specific options on its machines, such as steady rests and live tooling, Ray says: “Having very capable machines has given us much diversity in what jobs can go on what machines. We can also get finished products from the Dugard machines with the live tooling facility. Previously, these jobs may have gone from a turning centre to a milling operation.”
Actively working to enhance its customer service, Direct Engineering is ISO:9001 and ISO:1090 certified. The company has increased its plant list from one to four Dugard machines that are all installed in a machine shop with a limited floor area. As Ray says: “It’s a compact machining cell. To maximise our space, we spoke to Colin and Eric at Dugard about what machines are the best fit for our company to maximise our output. They’ve given some very constructive advice. This advice enables projects to progress through the machine shop very well, and in an organised manner, so we appreciate all the support we’ve had over the years.”
Looking closer at the Dugard machines the company has acquired, Ray confirms: “We started with the biggest machine first, which we needed for large billet work. We bought the Dugard SMEC PL45LY for this work, which has a large machining capacity. As we slowly phased out older machines, we invested in the SMEC PL2500 and the PL35, which are bigger machines. Then came our most recent addition, the SMEC SL3000. This has a bar feed and steady rest, which ensures we can cover most applications in this machine shop. The Dugard machines with live axial and radial tooling have enabled us to keep jobs on the machines rather than transferring parts to a milling machine.”
Looking at the current workload, Ray adds: “The parts we produce go from small high volume up to your big billet work that can be machined on the Dugard SMEC PL45LY machine. Our parts range from one end of the size scale to the other, and we’ve got the machines here to accommodate that. Additionally, we are machining to tight tolerances on some of the shaft work, especially regarding the concentricity required on parts before finishing.”
Automation delivers results
Mills CNC has recently supplied Ayrshire Precision, a subcontract specialist based in Ayrshire, with two new SYNERGi systems. The systems, both derivations and highly customised versions of Mills’ standard SYNERGi ‘SPRINT’ solutions, were installed at Ayrshire Precision’s 14,000sq/ft site. In 2023, the first system was retrofitted to a Puma 2600SY lathe, and six months later, the second was retrofitted to a Puma 2100SY.
SYNERGi Sprint automation systems are compact, flexible, and cost-effective. Mills’ dedicated automation experts can integrate them with DN Solutions’ lathes, machining centres, and mill-turn machines to create high-productivity automated manufacturing cells.
The essential elements of a SYNERGi Sprint system comprise an industrial FANUC robot with varying payloads and reaches, a two- or three-jaw pneumatic gripper, a 900 by 900mm part loading/unloading grid plate, and industrial safety guarding positioned around the system. Mills can also supply customers with multi-socket inserts to optimise each system’s capacity. These are sheet metal fabrications that customers can also choose to manufacture for themselves.
Ayrshire Precision serves customers in the oil and gas, subsea, renewables, power generation, and aerospace sectors. It has a well-resourced machine shop and regularly invests in its people, plant and equipment, processes, and systems as part of its ongoing continuous improvement programme. Since 2012, Ayrshire Precision has invested in various Doosan machines, from two-axis and multi-tasking lathes to large-capacity, heavy-duty vertical machining centres and horizontal borers.
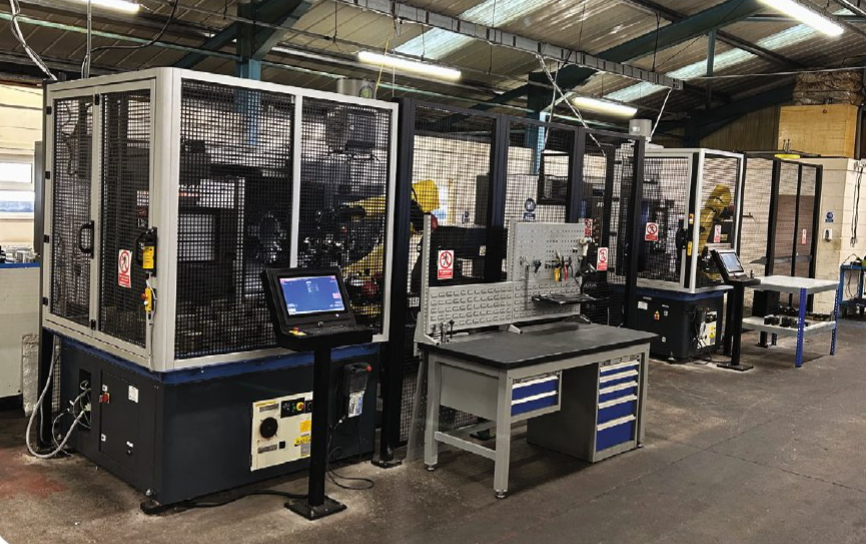
“We rely on machine tools from Mills. They are powerful, fast and accurate and enable us to meet the highly-regulated, tight-tied up tolerances and exacting surface finishes that characterise a majority of the components we machine,” says Chris Hepburn, Ayrshire Precision’s Managing Director.
Ayrshire Precision’s decision to invest in automation was made for several reasons. The volatility of the markets served by the company and, as a consequence, fluctuating customer demand for the company’s machining services, combined with difficulty recruiting and retaining skilled labour, all contributed to Ayrshire Precision’s decision to ‘think outside the box’ and begin its automation journey.
“It’s either feast or famine in the markets where we operate. We can either be swamped or, due largely to external macro-economic factors that impact our customers’ business, can experience order cancellations and/or postponements that make it difficult to match our production capabilities and resources with changing customer requirements,” explains Chris Hepburn.
Rather than be at the mercy of market forces and to protect the company’s long-term viability and profitability, Ayrshire Precision decided in 2020 to explore new ways to improve its flexibility, performance, and competitiveness. The company’s focus was initially on its small part-turning operation, which, at that time, comprised two Puma lathes, running over two shifts and operated by four staff members.
To increase the productivity of its Puma lathes, the company had previously considered integrating a bar feeder into each machine. However, the diameters of the machined drop forged parts, the batch sizes required, and the limited diameter capacity of the bar feeders prevented this approach.
Ayrshire Precision discussed its requirements with several automation system suppliers, focusing on the proposed system’s configuration, availability, and cost. As part of its decision-making process, Ayrshire Precision visited Mills CNC, which had previously supplied it with eight Doosan machines.
After discussing its plans further with Mills’ automation application specialists and seeing a couple of different SYNERGi systems in action at Mills’ Technology Campus facility in Leamington, it was confirmed that two separate SYNERGi Sprint systems would better meet Ayrshire Precision’s manufacturing requirements.
“We liked the design and build of the SYNERGi Sprint system,” remembers Chris Hepburn. “It was simple.”
“We asked Mills to put forward their plans and proposals for two SYNERGi Sprint cells – one incorporating our existing Puma 2600SY for larger parts, and the second incorporating our Puma 2100SY for smaller components.”
Says Chris Hepburn: “Mills’ approach was responsive and helpful. They worked with us to tailor-make the SYNERGI Sprint systems and offered useful advice. We placed the business with Mills, not just because of their technical and automation expertise, but also because they had originally supplied the two Puma lathes and knew the machines inside out. We also thought that dealing with one supplier for our machine tool and automation system requirements would be easier and would simplify communications, servicing, training, etc.”
Ayrshire Precision’s first manufacturing cell was installed in March 2023. The cell comprises a Puma 2600SY multi-tasking lathe and a FANUC 35kg industrial robot with dual Schunk 3-jaw grippers. Other elements include Renishaw probing systems, safety caging, and the system’s HMI control driven by Mills’ proprietary SYNERGi software.
With individual part cycle times of approximately 10 minutes, Ayrshire Precision is now benefiting from up to an additional 16 hours of unmanned operation of its Puma 2600SY lathe. Since installation, the company has manufactured different sheet metal pocket inserts to accommodate larger parts and different batch volumes.
Ayrshire Precision’s second SYNERGi cell was installed in September 2023. This cell incorporates the Puma 2100SY lathe, a 20kg payload industrial robot and a 900 by 900mm table for processing smaller components. The automation process for both cells involves the robot picking up a workpiece from the grid plate in a programmed sequence and, using the lathes’ auto door opening facility, loading the part into the machine’s main spindle. The door closes to enable the machining of the part’s front end.
After all machining operations are finished, the robot picks up the next sequenced workpiece from the table and, in one continuous movement, loads it into the main spindle. Then, it removes the finished part from the sub-spindle and returns it to its designated position on the table.
Says Chris Hepburn: “Every time the auto door opens, a completed part is removed from the sub-spindle and a new part is loaded into the main spindle. The process is fast, seamless and continuous. Furthermore, one staff member can operate both cells simultaneously.”
With less labour intervention required, Ayrshire Precision’s small part turning operation is now more efficient and profitable. Creating its two cells has also helped free up a couple of its operators, enabling them to be deployed to other machine shop areas.
Chris Hepburn concludes: “The investment in our two SYNERGi cells is paying dividends. We have two inherently flexible automated cells that have not only helped us future-proof our small-turned-part operations but have also increased our overall capacity. Although there was initially some anxiety concerning our move towards automated production, the results exceeded our expectations.”
High-volume holemaking mastered
Next-generation CoroDrill® DE10 redefines plug-and-play in short-hole drilling.
Sandvik Coromant now introduces its second-generation exchangeable-tip drill, CoroDrill® DE10. Engineered for high-volume drilling across all materials, CoroDrill® DE10 sets new standards in productivity, efficiency and sustainability. With its innovative geometry, this tool delivers true plug-and-play functionality and uncompromised performance.
Building on the success of CoroDrill® 870 for H9-H10 hole tolerances, CoroDrill® DE10 introduces advanced features that enhance versatility and operational ease. Users will appreciate the familiar pre-tension clamping interface, thoughtfully designed to align with operator experience while delivering enhanced security. The solution prioritises robustness, enabling quick tip changes, reliable high-speed drilling, and extended drill body life with more tips per tool. Its unique M5 tip geometry delivers unmatched performance across diverse materials and cutting conditions.
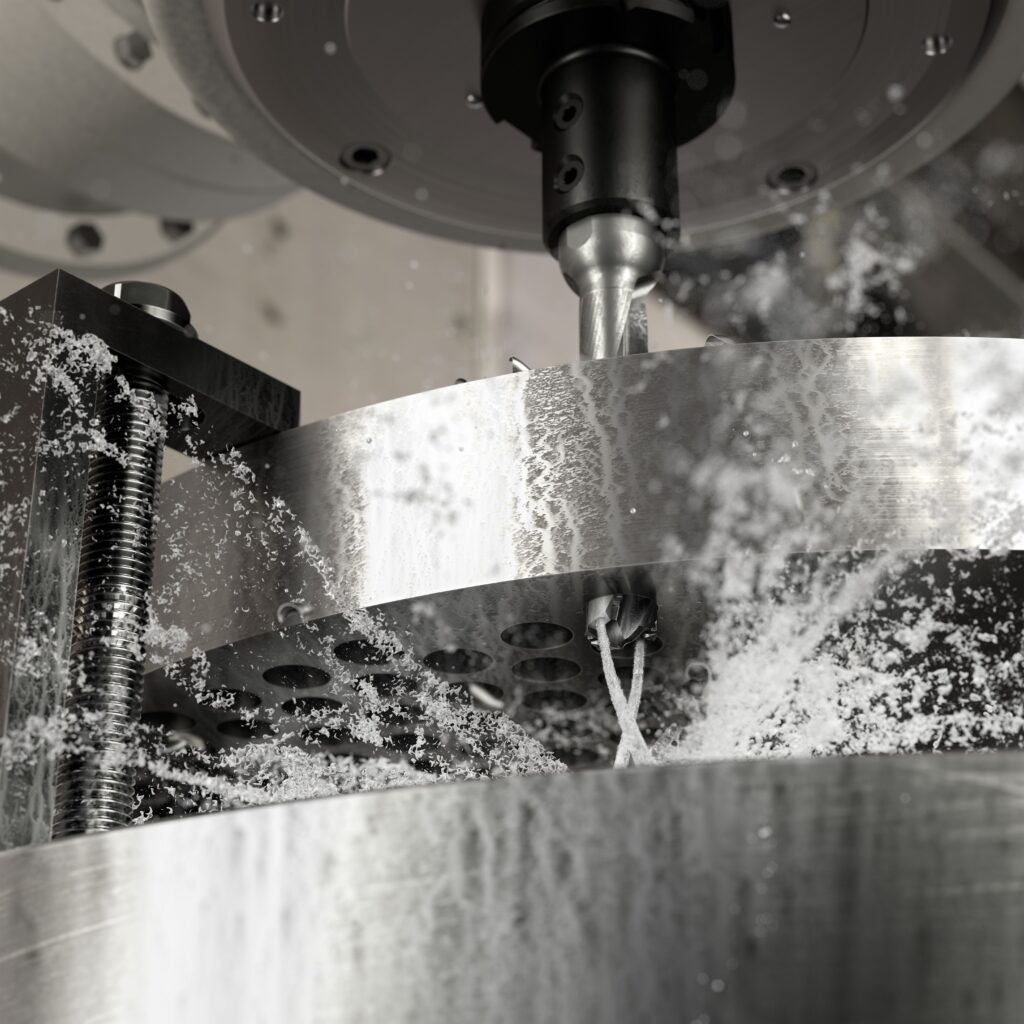
oroDrill® DE10 addresses several common drilling challenges, particularly for manufacturers tasked with producing large quantities of holes in a single operation. With high feed capabilities, the tool achieves superior penetration rates, boosting productivity and lowering the cost per hole. Additionally, both tool inventory and cycle times can be significantly reduced, as CoroDrill® DE10 eliminates the need for a pilot hole to guide the drill into place.
As a true plug-and-play solution, CoroDrill® DE10 integrates seamlessly into existing setups, offering unmatched ease of use while enhancing operational efficiency and performance. This innovative tool is designed to streamline manufacturing processes, delivering consistent results with minimal downtime.
“CoroDrill® DE10 marks a new era in exchangeable-tip drills,” said Mikael Carlsson, Global Product Specialist for Indexable Rotating Tools at Sandvik Coromant. Testing against competing solutions has demonstrated its superior robustness, faster and easier tip changes, enhanced feed capacity, extended tool life and reduced cost per hole. It’s an ideal solution for high-volume hole making across all industries, with typical components including heat exchanger plates, automotive components, shafts, pumps and valves and I and H beam drilling.”
CoroDrill® DE10 also enhances sustainability by enabling higher cutting parameters, faster metal removal and lower cutting forces, which reduces CO2 emissions. Its durable design minimises waste through predictable wear patterns and maximises tool longevity, further supporting responsible manufacturing goals.
The tool has been tested against multiple competing tools, showing a significant advantage each time. “One customer testing CoroDrill® DE10 overcame the challenge of high cutting forces generating deformation on the drill body of their previous solution,” continued Carlsson.
”When using CoroDrill® DE10 to drill holes for a batch of gearbox housing, the customer experienced no wear on the drill tip and a 17 percent increase in productivity. Another customer, this time machining stainless steel plates, saw a 43 percent increase in tool life and a 57 percent increase in productivity when switching to CoroDrill® DE10 from a competing tooling solution. These are just two of many successful tests we have conducted, and for each one, customers have already seen unprecedented productivity gains.”
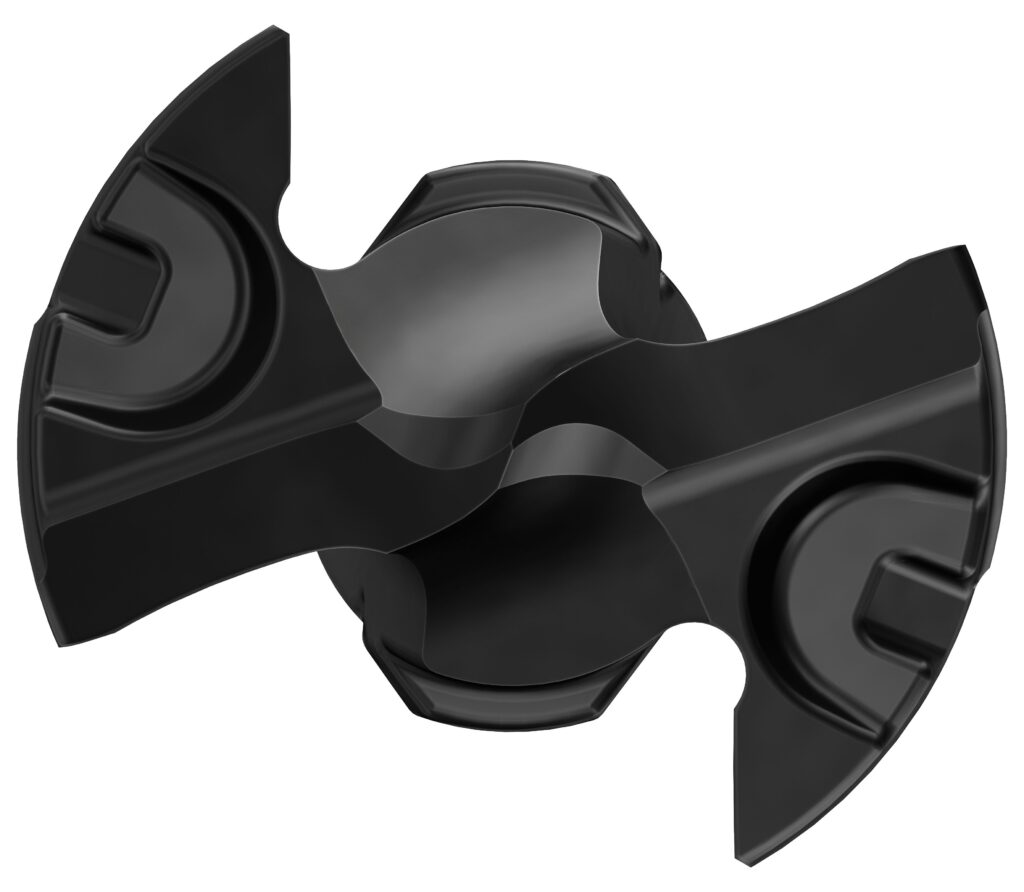
For comprehensive tool data and optimised machining practices, CoroDrill® DE10 is compatible with the CoroPlus® Tool Guide, providing users with precise cutting data recommendations from the outset. To discover how this solution can transform high-volume drilling operations, customers are encouraged to contact their local application specialist or visit the website for further details.
Horn introduces PCD milling cutters for aluminium

Horn has expanded its DM range of polycrystalline diamond (PCD) cutting tools by adding a range of mills specifically aimed at manufacturers looking to machine aluminium efficiently. The cutting geometries of a variety of tools, from simple end mills to complex and modular combination tools, have been optimised to meet the challenges of machining aluminium, taking into account factors like chip formation, cutting forces and surface finish.
The tensile strength, elongation, hardness and yield strength of aluminium can be influenced by alloying elements such as silicon, magnesium, copper, zinc and manganese. The material can become soft during machining due to the development of heat, causing it to adhere to and even destroy the tool. It is therefore important that the cutting feed rate and spindle speed, as well as the type and quantity of coolant, are properly matched to the material. Horn’s experienced engineers can provide expert advice on selecting the correct machining parameters for specific aluminium alloys.
The DM range from Horn is also suitable for processing other non-ferrous metals and technical plastics. The PCD grade consists of an advanced mixture of diamond grains of different sizes. As the volume percentage of diamond increases, so do the effective hardness, toughness and edge quality. Strict quality standards are in place in the Tübingen factory in southern Germany to ensure that the tools, with their precision-lasered cutting edges, deliver a high level of performance and long service life.
Rebirth of a classic British motorcycle
The Brough Superior, a classic British motorcycle designed by George Brough in 1919 and manufactured in Nottingham, was of such high quality that it was dubbed the Rolls-Royce of motorcycles. One famous customer, T.E. Lawrence (Lawrence of Arabia), owned eight and died in 1935 from injuries sustained when he crashed number seven.
The design was beautiful and practical, and a sidecar was often added. Although the factory closed after the Second World War, enthusiasts have ensured the name survives. In 2004, around 1,000 original Brough Superior motorcycles still existed. The brand is regularly seen in period movies and television series, as well as in classic bike shows, hill climbs, and motor races.
In 2014 the Brough Superior brand was purchased by a Jersey-registered corporation, which engaged Thierry Henriette to create a Brough Superior factory in St Jean, Southern France, near the aerospace capital of Toulouse. The factory produces luxury motorcycles at the pinnacle of exclusivity and distinction. Although production is in France, the British design spirit has been maintained through a joint venture with Aston Martin to create the AMB 001 Pro, a limited-edition, high-performance motorcycle.
To support the R&D process, bringing in-house the manufacture of some complex prismatic components was necessary. A Hurco VMX42SRTi 5-axis VMC was chosen due to its ability to achieve the accuracy and surface finish required. It can also accept 3D models directly into the proprietary WinMax control, renowned for its suitability for high-mix, low-volume production.
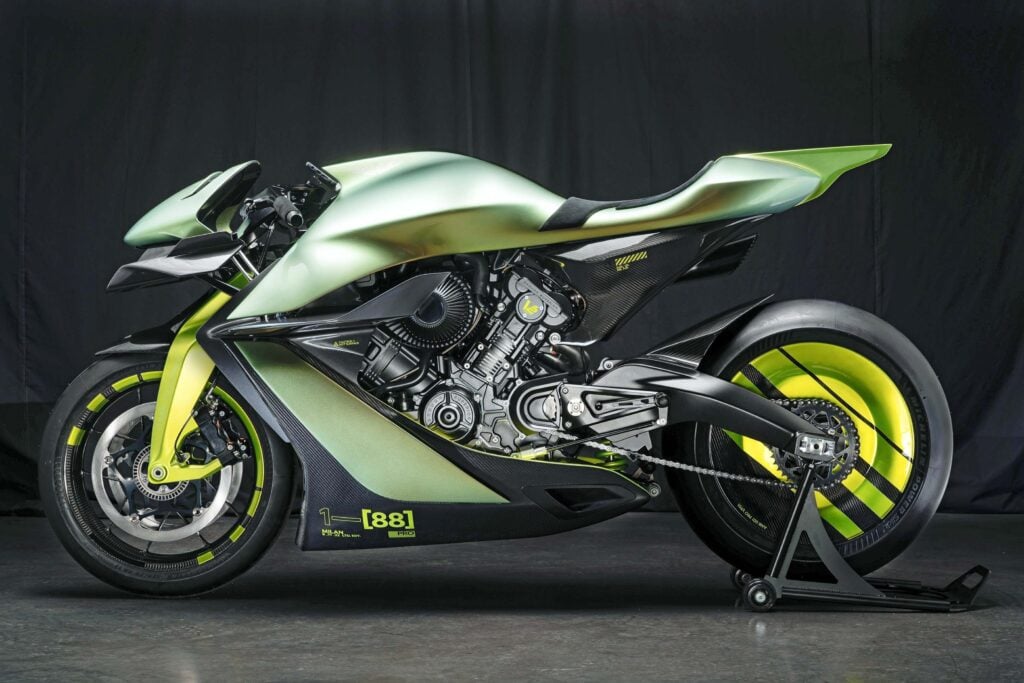
Additionally, and most importantly, it enabled the manufacturer to go even further in customising motorcycles for its discerning clientele, offering different machining finishes and engraving possibilities and assuring the impeccable quality of parts.
The VMC also supports CNC machining of a new, dual-cylinder, 997cc engine for the AMB 001 Pro, a high-performance, turbocharged, track-only motorcycle born from a collaboration between Aston Martin and Brough Superior. It draws inspiration from Aston Martin’s Valkyrie AMR Pro hypercar, which has a power-to-weight ratio comparable to a Formula One car.
Manufactured from solid aluminium billet, the engine is lighter, stiffer and more powerful than in previous Brough Superior bikes. In addition to powering the AMB 001 Pro, it has been engineered to fit perfectly into contemporary versions of the classic Lawrence and Dagger motorcycles. Most metal removal and finishing are completed in a single set-up on the Hurco VMX42SRTi.
Fast, versatile machine wins
Michael Phillips, joint owner with partner Wayne Robins of contract machining firm Atomic Precision, describes their recently purchased, Japanese-built Brother Speedio U500Xd1 as ‘a Swiss army knife of 5-axis machining centres.’ His comment is due to the 30-taper machine’s high quality, versatile functionality, compactness, and ability to complete an extensive range of jobs quickly and efficiently. Brother machines are sold and serviced in the UK and Ireland by Whitehouse Machine Tools, Kenilworth.
Founded in East Hendred, Oxfordshire, in 2020 by the two time-served mechanical engineering apprentices, who both previously worked in the machine shop at nearby Rutherford Appleton Laboratory’s space development facility, Atomic Precision specialises unsurprisingly in manufacturing components and assemblies for the space and scientific research sectors.
Over the next four years, a succession of 40-taper VMCs from another supplier arrived on the shop floor: three 3-axis models and two 5-axis machines. During that time, the subcontractor enjoyed an impressive growth rate of 50% yearly.
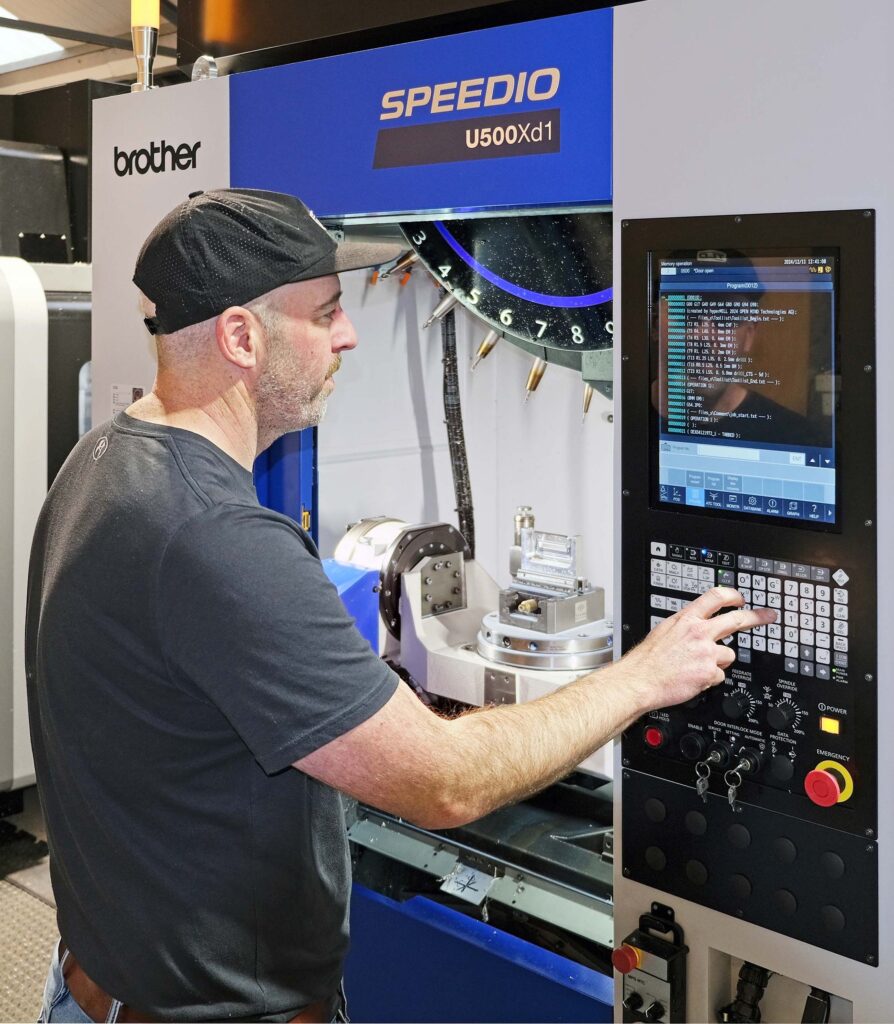
It was clear to the two partners, who work alone that the ongoing rate of growth was unsustainable without progression on the shop floor to more efficient machine tools and perhaps also automation to gain substantial periods of unattended production. They operate a single-day shift, and working longer hours is not part of their game plan.
As a first step to raising productivity, Whitehouse Machine Tools installed and commissioned the high-speed Brother U500Xd1 in September 2024. The partners learned of the machine at the Southern Manufacturing exhibition in Farnborough in early 2023. The order was placed after early hesitation regarding the smaller spindle interface, which later proved to be a non-issue and benchmarking a couple of other 30-taper machines on the market.
Mr Phillips commented: “The area taken up on our shop floor by the U500Xd1 is half of the space that one of our 40-taper 5-axis machines occupies, yet the 30-taper VMC produces larger parts. Not only that, but the Speedio finishes an identical component in two-thirds of the time, as the non-cutting elements of cycles are incredibly short, so tools are in-cut for typically 90% of the time during a cycle.”
“The linear axes accelerate at 2.2 g up to 56m/min, and chip-to-chip time is 1.3 seconds. Rotary positioning by the trunnion and table is similarly fast, and parts come off complete, resulting in rapid floor-to-floor times.”
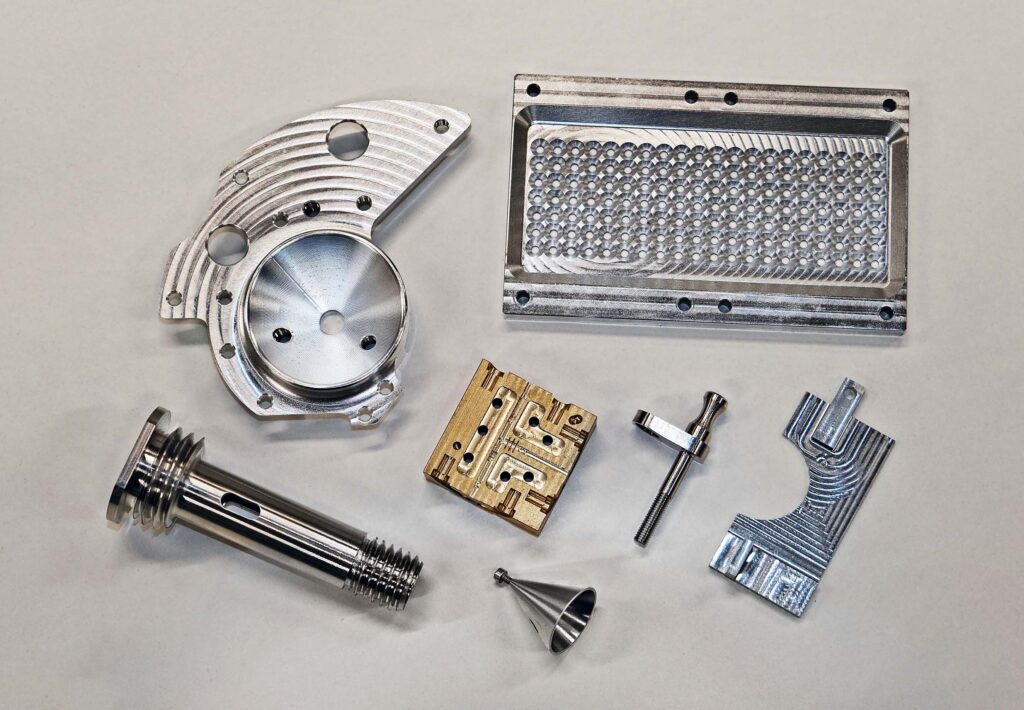
The machine installed in East Hendred is a well-specified version of the Speedio model, with a 16,000rpm 15kW spindle, 28-position tool turret, high-pressure coolant, and Blum tool and part probing. Axis strokes are 500 by 400 by 300mm, but multi-face machining of components up to 500mm in diameter by 270mm high and weighing up to 100kg is possible owing to the layout of the machining area.
As well as producing parts up to the maximum working envelope, the Speedio also machines tiny components requiring complex features cut with a 0.2 mm diameter end mill, hence the decision to opt for the highest speed spindle Brother offers. Towers are extensively used for fixturing multiple smaller parts to extend the walk-away time from the machine if individual cycle times are short. Batch size is usually up to 10-off, although often single prototypes are machined.
However, in November 2024, Atomic Precision received a huge order from a new customer for 400-off aluminium brackets requiring a 3+2 machining strategy, using the rotary axes to position the part. The subcontractor could not have accepted the contract if it had been unable to use the elevated speed of the Brother machine. A 5-axis, 40-taper VMC would have been too slow to meet the three-week lead time, so the subcontractor would have had to turn down the work. If more jobs involving quantities of several hundred starts coming in, automating the Brother and other VMCs on-site will go ahead imminently.
The factory processes various materials, including aluminium, stainless steel, brass, copper, tungsten, and tantalum. Mr Phillips advises that it is possible to hold ± 10 micron dimensional tolerance ‘comfortably’ on the Speedio, even without climate control in the factory.
Aero manufacturer is clear for take-off
In the aerospace industry, compliance is not just a requirement, but a culture. Senior Aerospace Weston places significant importance on workplace standards—which is why it has installed more than 50 Filtermist oil mist filters.
Working primarily with OEMs like Rolls-Royce, Airbus, MTU Engines, Spirit Aerosystems, and many other prestigious clients, Senior Aerospace Weston manufactures a variety of aerofoil and aerostructure components for various platforms in the commercial aviation market. Founded in 1937 and acquired by Senior plc in 2011, the Earby-based manufacturer is now part of an FTSE 250-listed group with over 6,800 employees in 12 countries.
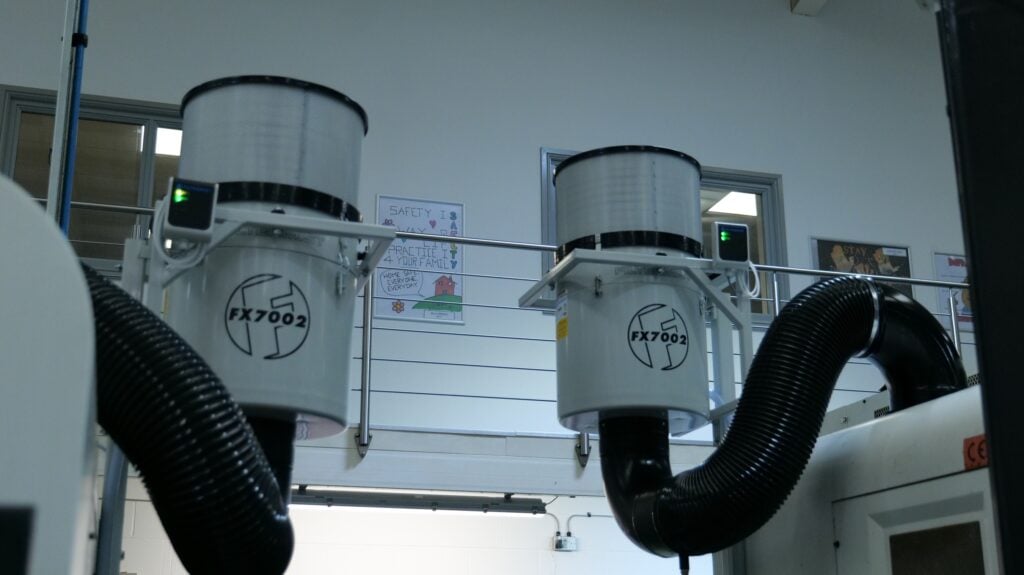
As part of a global group in the top echelons of aerospace manufacturing with 3 to 5-axis machining and grinding, CAD/CAM, assembly, NDT, surface treatment, robotic polishing, and much more – achieving standards is critical. Gary Bell from Senior Aerospace Weston says: “Here at Senior Airspace Weston, we believe in maintaining good, orderly, clean standards, housekeeping, and a good working environment. A clean working environment is essential to ensure that we produce our high-specification components.”
Providing more detail on the machine shop, Gary adds, “We make a variety of aerospace components for different aircraft programmes and work with a range of materials. This is predominantly aluminium, but we also work with titanium, bronze, nimonic, inconel and steel. We have lots of different types of CNC machining centres with 3, 4, and 5-axis machines. Each machine is specified to manufacture certain types of components, and this is why we have such a wide variety.”
With Filtermist extraction units, including the FX6002 and FX7002 on 58 of the company’s machine tools, it is imperative that oil mist is extracted from the machines. As Gary adds: “The type of high-speed machining that we undertake produces oil mist that needs removing from the working environment. Our first thought was to look at the industry-leading standards, and Filtermist was the name that first came up. We engaged with them straight away, and they were extremely helpful in giving us some advice and support. They were able to come on-site and carry out a free survey so that they were able to specify exactly what equipment would be available to support our needs.”
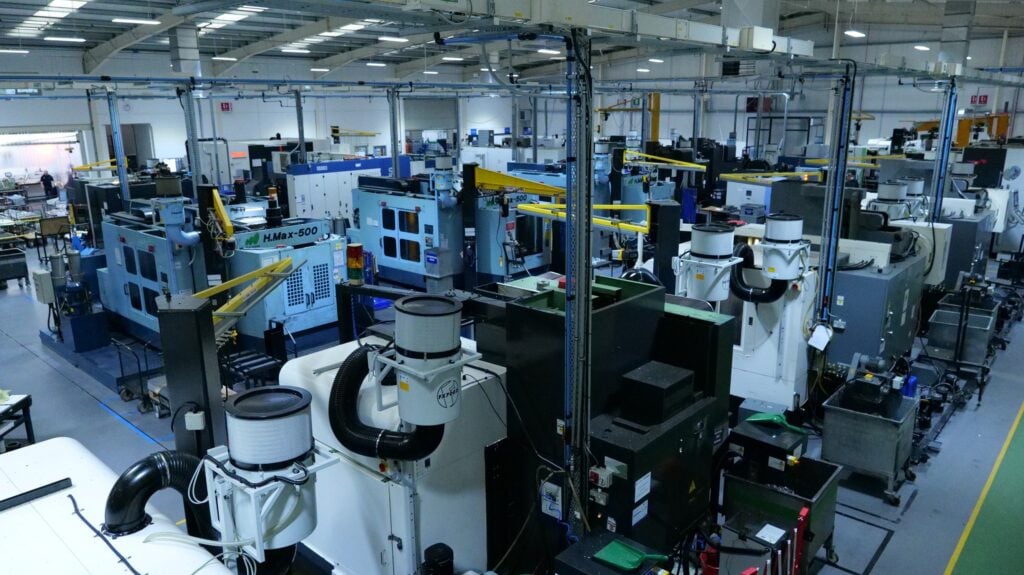
With machine tools from leading manufacturers such as Matsuura, DN Solutions via Mills CNC, Grob and Hermle among others on-site, Gary continues: “In total, we have 58 Filtermist extraction units. Some machines require multiple Filtermist units to be installed to ensure the volume is extracted quickly and efficiently. We have a huge variety of machines, and the Filtermist units are flexible enough to accommodate the different types, sizes and requirements of those machines. We have machines that are large in scale, so we needed something that was able to extract from all those different types of scenarios effectively.”
Discussing the maintenance requirements and the ongoing relationship with Filtermist, Gary says: “The beauty of the Filtermist system is it’s easily serviceable, so we can specify whether the Filtermist units are standalone or mounted to the equipment. They are easily accessible for the service engineers to come in and replace any components effectively and quickly. The Filtermist units are fitted with F monitors, which are a really easy-to-use system. The operators can see at a glance using the traffic light system whether there are any issues with the effectiveness of the extraction.”
Using the globally recognised ‘traffic light’ system of coloured warning lights to alert machine operators when the unit needs servicing, the F Monitor measures velocity pressure to check the airflow through the Filtermist oil mist collector is correct. The Bluetooth-enabled F Monitor 2 measures airflow and time, and the F Monitor 2+ also monitors vibration and motor temperature – making it even easier to identify when the Filtermist unit needs servicing. For existing customers, the F Monitors can be retrofitted to the complete Filtermist range and are available as an optional accessory on all Filtermist units.
A pilot drill that’s up to any challenge
Manufacturers could only drill on inclined or curved surfaces with pre-chamfering using a milling cutter in the past. Those days are now behind us and you only need one tool – the newly developed WTX Micropilot from CERATIZIT. It can even pull off 90° countersinks at the bore entry in a single operation —saving tool changes, cycle time and costs.
Micro machining has rules and practices that are different to everyday machining. Simply put, what works well with standard tool dimensions does not necessarily hold true with small diameters. “To this end, we have revised our micro drilling program and developed a genuine time saver. The WTX – Micropilot is small in stature, but big in performance. Perfectly matched to our WTX – Micro micro drill from 8xD to 30xD, the pilot drill is used at drilling depths of up to 2.5xD,” says Manuel Keller, Product Manager at CERATIZIT.
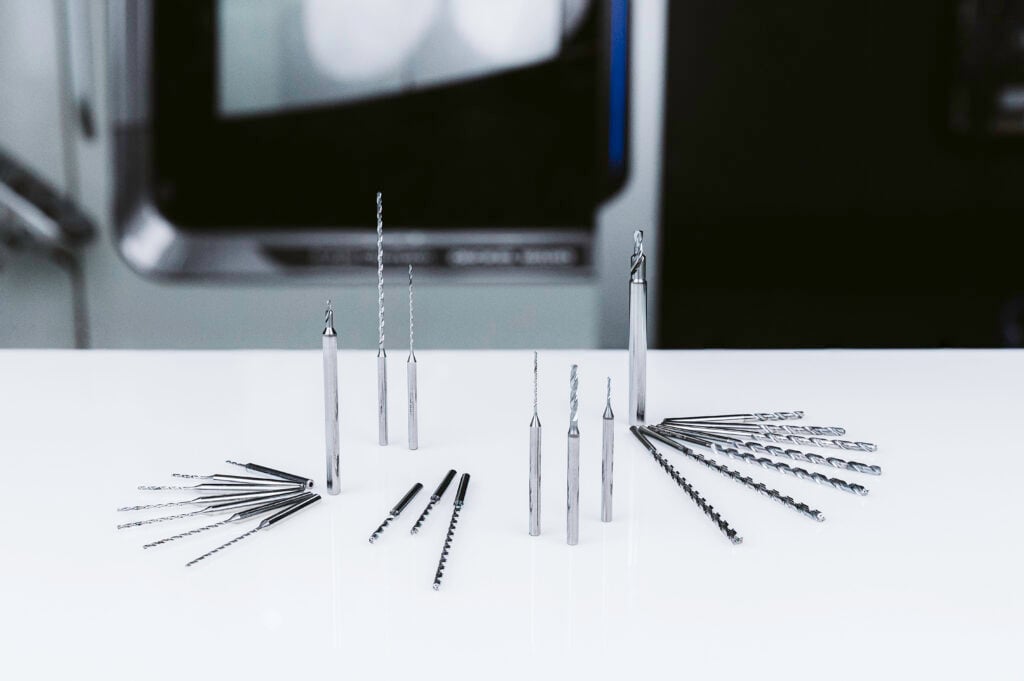
When faults occur in complex, micro-sized components, they quickly end up dumped in the recycling can. The truth is that a number of things can go wrong. Drills can run off, drill holes get crooked or tools break—including damage to the workpiece itself. “Efficient machining of small components presents its own set of challenges,” says Manuel Keller. “Our customers want process reliability, the shortest possible machining times and demand extremely high-quality standards. Fortunately, our WTX – Micro series is up to the task.” Thanks to its ingenious face geometry with a 160°-point angle, the tool ensures the follow-up drill can plunge in cleanly and without running. And with the special Dragonskin coating, clean chip removal and a longer tool life are guaranteed.
The WTX – Micropilot is developed from the latest technologies from the substrate to the geometry to the coating. It is also perfectly designed to work together with its ‘best buddy’ WTX – Micro. This drill duo can handle the most common as well as the most demanding tasks. “One special feature of the WTX – Micropilot is that it circumvents the usual mirroring required if drilling inclined and curved surfaces with an inclination of up to 50. This eliminates one processing step, saving time and tool changes. When piloting on straight surfaces, a 90° countersink at the bore entry is also possible,” reveals Manuel Keller.
What all WTX micro drills have in common is their special pointing. This maximises positioning accuracy and excellent centring properties. Their lapped surfaces and the patented chip space grinding also guarantee safe and fast chip removal. Additionally, the spiral internal cooling channels of the WTX Micro drill have been optimised to ensure maximum flow of cooling lubricant, which, in turn, secures improved surface quality of the holes. Among other things, this is thanks to a power chamber, which is fitted to the micro drills from 5xD over the entire shank length, which increases the amount of coolant at the tip while maintaining uniform pressure—thus improving tool life.
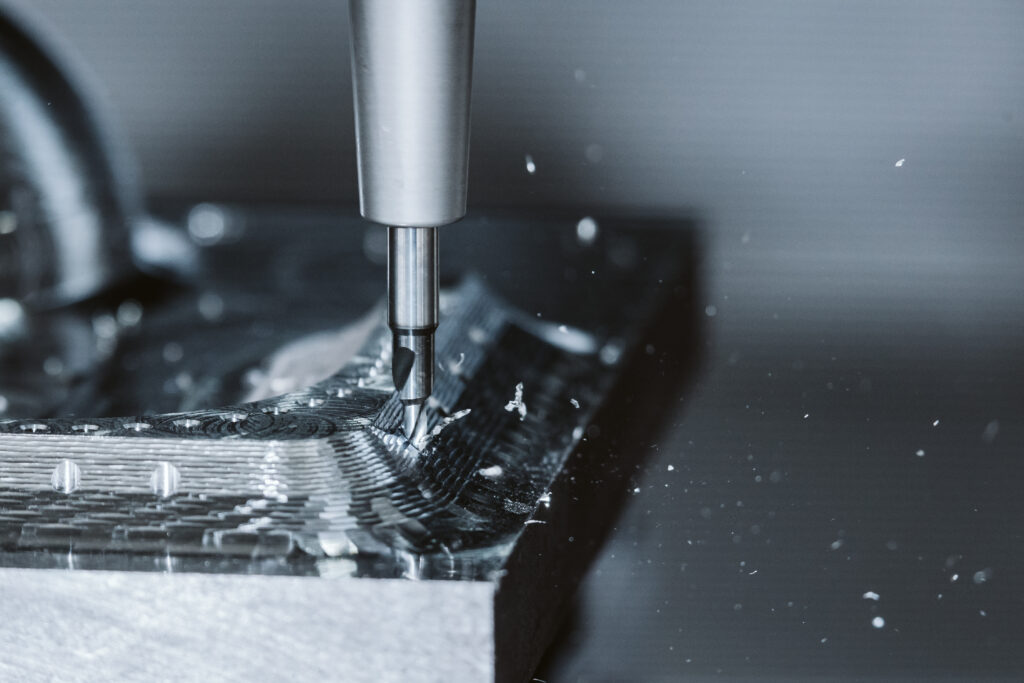
Made for maximum precision
With its micro-tool portfolio, CERATIZIT covers most micro-machining applications with high-quality solutions. “This also applies to the WTX – Micro product range, including the new WTX – Micropilot, which makes the impossible possible. On both inclined or curved surfaces with an inclination of up to 50°, there is no need for prior mirroring. And if 90° countersinks are required at the bore entry point on straight surfaces, WTX – Micropilot can easily handle the task in a single operation, saving tool changes, time and costs—without sacrificing quality,” says Manuel Keller.
UK’s SMEs say ‘apprentices are the solution to UK’s skills gap crisis’
Over 80% of the UK’s SMEs believe apprenticeships are at least partly the solution to the UK’s skills gap crisis, with a further 69% of the view apprenticeships are a ‘valuable alternative to university’
Four in 10 (44%) feel not enough is being done to encourage young people to consider apprenticeships.
The findings are taken from the latest independent research commissioned by Close Brothers Asset Finance and are in support of National Apprenticeship Week (NAW), which highlights the positive impact that apprenticeships make on individuals, businesses and the wider economy.
According to a survey by the Learning and Work Institute, around 70% of employers reported a skills shortage in their workforce. The Close Brothers Asset Finance research confirms that 50% of business owners are concerned there’s a skills gap in their sector while a further 16% say the issue is regionally based.
Over a third (37%) of responding firms report having an apprenticeship scheme of their own, with many (65%) stating that if financial assistance were available from either the government or the private sector to help contribute towards wages and/or training, they would put someone from their company forward to participate in an apprenticeship scheme.
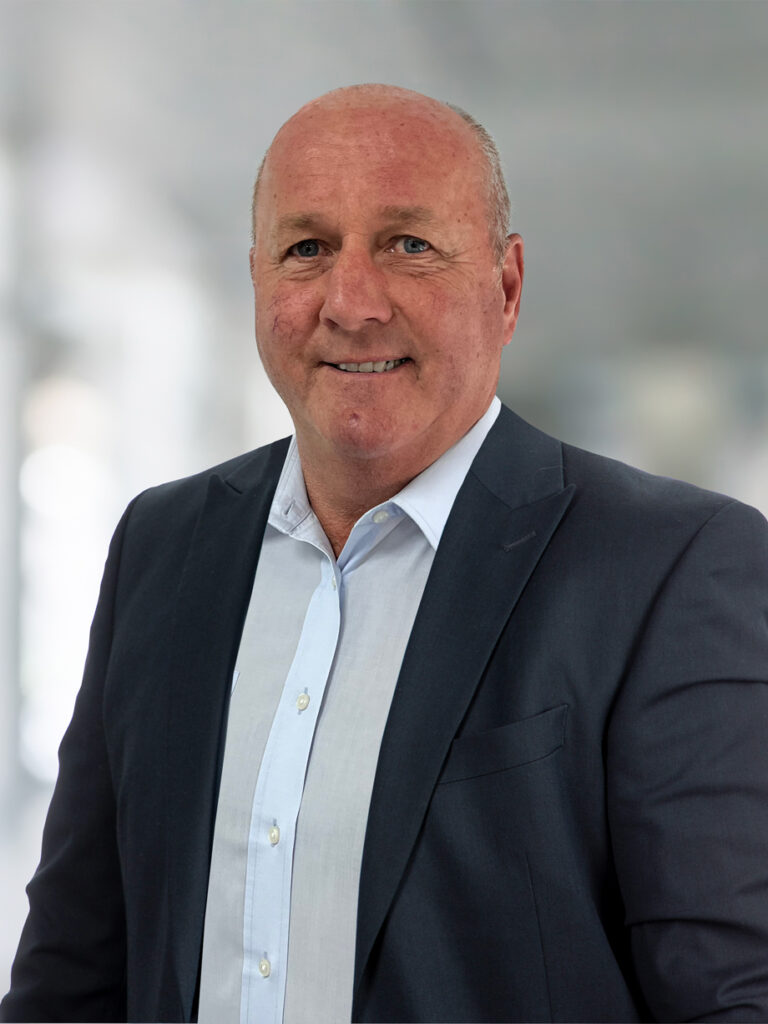
The National Apprenticeship Service states that 96% of employers with apprentices have experienced at least one benefit from taking on apprentices, and most can count at least eight benefits. In addition, 74% of employers say that apprentices improved products or service quality, and 78% say that they improved productivity while 73% say that staff morale is improved by having apprentices.
Steve Gee, CEO of Close Brothers’ Asset Finance’s Industrial Equipment Division, said: “As a funder of a number of sectors that rely on apprentices, we’ve long seen the need and value of apprenticeship schemes, which encourage new talent into industries that really need them.”
“As part of our commitment to the SME community, we’ve been funding an apprenticeship scheme since 2015, in partnership with the University of Sheffield’s Advanced Manufacturing Research Centre (AMRC). Under the scheme, we contribute towards the wages of the apprentices in both the first and second year, with all training costs also covered.
“The reality is, it’s not cheap for an SME to invest in apprentices – and its important small business owners see it as an investment and not a cost. Handled correctly, apprenticeships can help an SME flourish and, at the same time, develop the individual apprentice.”
“I believe we all have a duty to look at where, as ‘UK PLC’, we need to concentrate our efforts and money. I would strongly encourage firms to support apprentices – we know first-hand what a hugely positive impact they can have.”
Nikki Jones, Director of the University of Sheffield AMRC Training Centre said: “At the AMRC Training Centre, we’re transforming lives through apprenticeships. We combine classroom learning and shop floor industrial experience to equip new, young talent with all the skills they need to become the advanced engineers of tomorrow.
“It is crucial to invest in apprenticeships and support employers to take on apprentices to help close the huge skills gap in the industry currently. We’re proud of our relationship with Close Brothers and acknowledge their constant support in delivering apprenticeships throughout the years, helping apprentices kick-start their careers.”
For more information please visit: closeassetfinance.co.uk
Mastering difficult-to-cut aerospace materials
Difficult-to-cut materials are defined as engineering materials with significantly lower machinability than typical. These materials are often referred to in shoptalk as ‘hard-to-machine,’ ‘tough-to-cut,’ or even ‘nasty.’ It is important to note that high hardness is not the only characteristic that makes these materials challenging to machine; several other factors contribute to their machining difficulties.
Every industrial branch, in one way or another, must deal with such materials. However, the leading consumer of these materials is the aerospace industry. It is in this sector—whether in the production of turbine engines, landing gear components, or primary airframe elements—that difficult-to-cut materials have found their most significant application. In the aerospace industry, the key characteristics of required materials are strength-to-weight ratio, robustness, fatigue life, and resistance to corrosion and hot temperatures. It turns out that materials meeting these characteristics are difficult to machine, posing a serious challenge for production. When speaking about such materials, the following information should be considered:
l High-alloy high-strength steel,
l Titanium alloys,
l Hot temperature superalloys,
l Composites.
High-strength steels are used in elements subjected to extreme mechanical load, such as landing gear. They are also the primary material for various fasteners.
Titanium alloys, with their excellent strength-to-density ratio, high corrosion-proof, and creep resistance, have become the preferred material for producing the main parts of a jet engine’s cold section. These alloys also provide a suitable alternative to steel and stainless steel for weight savings.
Hot-temperature superalloys (HTSA), which can maintain their strength in high-temperature environments, are common in the components of a jet engine’s hot section.
Composites offer impressive specific strength, helping to decrease an aircraft’s weight and opening new prospects for aerodynamic fairing. In military aviation, composites contribute to improved aircraft’s stealth characteristics.
However, machining these materials presents numerous challenges for several reasons. The main challenges are as follows:
l High material strength results in significant cutting forces that increase the mechanical load on the cutting tool.
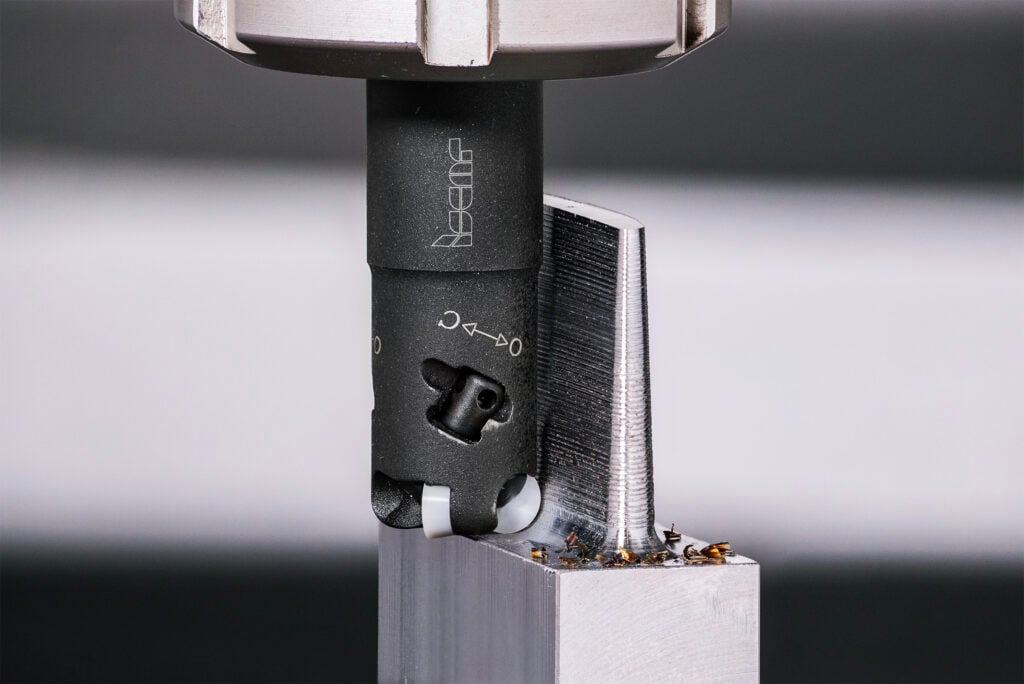
l Intensive heat generation and low thermal conductivity of the material (for example, when machining titanium alloys) cause poor heat transfer. This leads to a growing thermal load on the tool and increases the risk of build-up on a cutting edge.
l Work hardening of materials (specifically HTSA) increases the strength and hardness of the workpiece surface during cutting, making machining difficult.
l The high abrasion factor (when machining composites) intensifies the galling of the tool’s active area.
Additionally, other specific material features affect machinability. For example, the ‘springiness’ of titanium alloys contributes to vibration, worsening machining accuracy and surface finish. The inner structure of composites is associated with material delamination during machining.
All the mentioned aspects accelerate tool wear and diminish tool life.
The trends in the aerospace industry distinctly point to the increased usage of difficult-to-cut materials. This is manifested by introducing new alloys with higher strength and heat-resistance characteristics, the broad application of composites, and the utilisation of hybrid-structure (metal-composite) materials.
To meet these challenges, the metalworking industry introduces new cutting strategies based on the impressive capabilities of modern CNC machines and CAM systems. However, the cutting tool is the final link in the entire machining chain, which directly contacts the material and removes its layer during operation. This link is the most ‘conservative’ part of the chain, and its development is slow, often hindering the full utilisation of advanced machines’ capabilities. To overcome the existing difficulties, it is necessary to reduce machining data, which leads to low productivity and increased machining costs. Understandably, every step forward, even a small one, in the tool field can significantly improve machining ‘nasty’ materials. Therefore, the metalworking industry welcomes the latest advances in cutting tools, hoping they will radically change the situation.
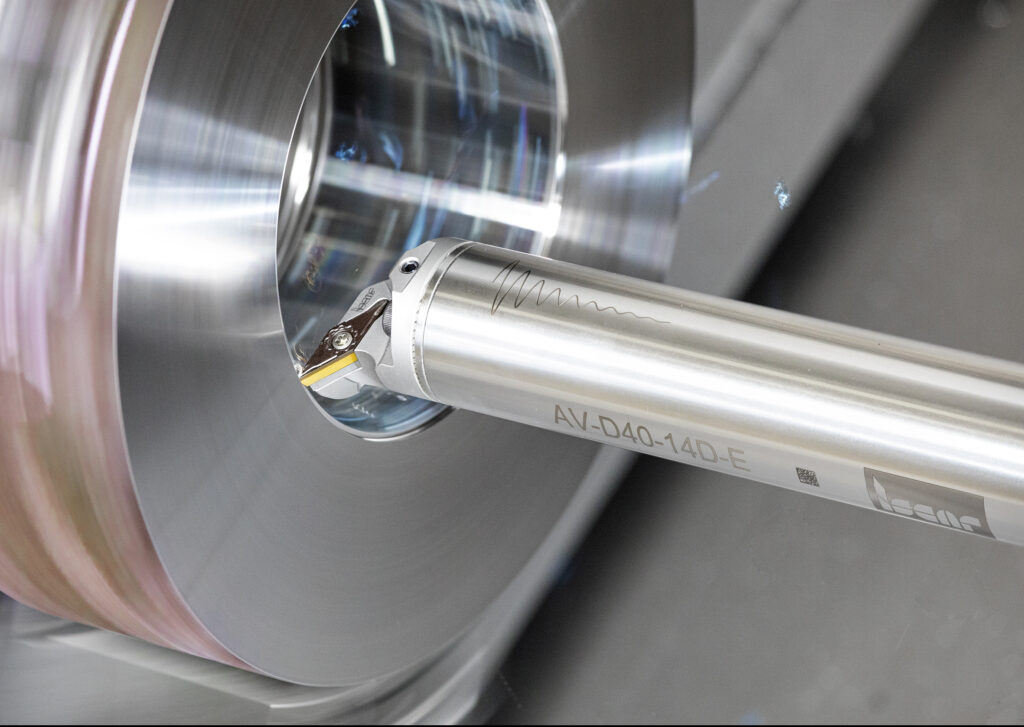
What are the main requirements for tools intended for efficient machining of tough-to-cut aerospace materials? In brief, they need to be hard, durable, and precise to enable productive machining while ensuring predictable and stable prolonged tool life and the required accuracy level. However, meeting these understandable and reasonable demands requires significant efforts, and even small progress in this direction faces challenges. Every new advance involves serious R&D work and extensive testing.
Hence, tool development focuses on the following areas:
- Cutting material grades.
- Tool design.
- A tool’s digital component.
The emphasis in cutting materials is on improving hardness, wear resistance, and high-temperature strength. This is achieved by introducing new coatings, particularly those based on nanotechnology, and expanding the use of extra-hard cutting materials like cubic boron nitride (CBN) and ceramics.
In tool design, enhancements optimise macro and micro-geometries, such as the cutting edge design and cutting edge preparation, to improve cutting capabilities. Computer modelling, combined with computational dynamics and the impressive possibilities of additive manufacturing (AM), provides new opportunities for shaping flutes, chip gullets, and internal coolant channels. This contributes to better chip evacuation and coolant supply, improving tool performance. A key area is increasing the vibration resistance of the tool through advanced cutting geometry, enhancing the rigidity of the tool structure, and using vibration-damping toolholders.
The tool’s digital component includes the digital twin and various software products, which allow for virtual assembly, machining simulation, cutting data selection, tool life estimation, and necessary calculations such as machining power and cutting forces. ISCAR expects that this component will be compatible with data exchange standards to meet the requirements of Smart manufacturing. The noted trends are evident in the new developments from ISCAR, one of the leaders in tool manufacturing, presented within the framework of the latest LOGIQUICK campaign.
The company has introduced two new carbide grades with PVD coating: IC1017, which ISCAR created for turning Ni-based HTSA, and IC716, which is intended for high-performance indexable milling titanium alloys. The range of chatter-dampening solid carbide endmills has been expanded with contemporary designs made from the bronze-coloured IC608 carbide grade, which is the first choice for the ISO S group of applications (cutting superalloys and titanium). Another carbide grade, IC5600, has been developed by ISCAR’s prolific R&D Materials Sciences engineers for milling steel (ISO P group). The combination of the grade’s submicron substrate, CVD coating, and post-coating treatment aims to enhance resistance to abrasive wear and thermal loading, increasing cutting speed, particularly when machining high-strength steel.
CERAMILL, a new family of endmills with indexable single-sided round inserts (Fig. 1), is interesting from two points of view. First, the family utilises an ingenious mechanism for high-rigidity insert clamping. This mechanism allows for an increased number of teeth compared to a typical design of similar tools in the same diameter. Additionally, it enables simple indexing and insert replacement without removing the endmill from the toolholder. Second, the inserts are produced from ceramic grades specially engineered for machining HTSA.
ISCAR has expanded its range of anti-vibration products based on the innovative built-in damping mechanism, which features a heavy mass supported by a rubber spring element containing oil for enhanced dampening. The turning line now includes vibration-absorbing boring bars for machining depths of 12 and 14 times the shank diameter (Fig. 2). Additionally, the milling line has incorporated anti-vibration shanks with MULTI-MASTER adaptation.
The QUICK-X-FLUTE is a family of extended flute shell mills developed to achieve high metal removal rates (MRR) in rough milling of challenging materials such as HTSA and titanium (ISO S), austenitic and duplex stainless steel (ISO M), and steel (ISO P). These ‘porcupines’ utilise cost-effective, double-sided square inserts with 8 indexable cutting edges. A key aspect of the mill design is the optimised flute geometry (Fig. 3), which balances mill rigidity and the necessity for adequate chip flow when cutting at high MRR. The QUICK-X-FLUTE mills also feature an inner coolant supply option. Using high-pressure pinpointed coolant with replaceable nozzles and face frontal outlets ensures a direct supply of coolant to the cutting zone. This enhances the cooling and lubrication action, contributing to optimal chip control.
Effective coolant supply has become a primary emphasis in contemporary tool designs. In the PICCO line of miniature turning tools, ISCAR has introduced new inserts with internal coolant channels (Fig. 4). In hole making; the company has unveiled new 3-flute solid carbide drills for machining flat-bottom holes featuring three coolant outlets. The latest additions to tool holding include holders with coolant channels along the shank bore. Additionally, in ISCAR’s classical HELIMILL indexable milling family, the company’s R&D engineers have upgraded the design to maximise flow rate with minimal pressure drop using computerised fluid dynamic (CFD) software.
Improvements have also been made to NEOITA, an integral part of the company’s digital tool component. NEOITA, an expert system that recommends optimal tooling solutions and forecasts tool life for a specific application, now includes new features. One of these is the AI-powered information search, specifically designed to retrieve detailed data on workpiece materials, including their metallurgical composition and typical uses.
Enhanced performance in machining difficult-to-cut aerospace materials is a complex challenge. Tool manufacturers continually strive to provide more advanced and productive solutions to address this. While no radical breakthroughs have been observed, recent developments indicate steady evolutionary progress in this area.
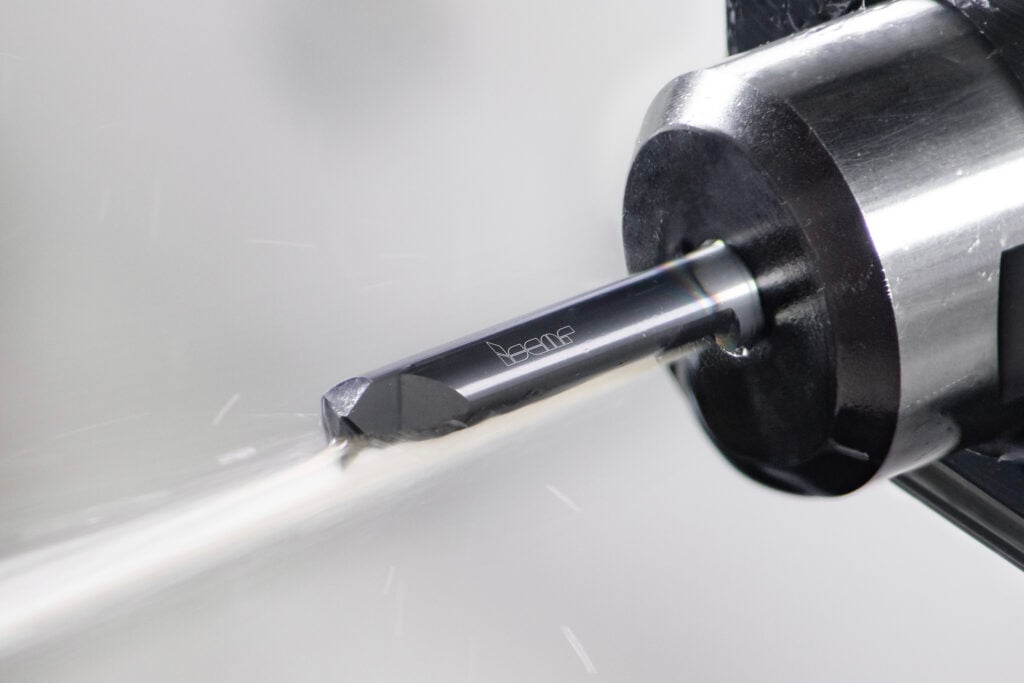
Engineered in record time
Engines were already being built at the site in Zafra in 1875, where DEUTZ today has its main factory for processing engine components. Around 500 employees in modern manufacturing facilities produce engine blocks, cylinder blocks, connecting rods, and gears for the Group’s assembly lines in Cologne and Ulm.
DEUTZ’s new 3.9-litre diesel engine is mostly used in agriculture but also in the construction equipment segment. As an industrial engine, it is designed for long service life and is to be built until at least 2035. Series production starts in 2025.
This engine, which will be available in a power range from 75 to 130 kW, represents an important future project for DEUTZ. As it is the same size as its 3.6-litre predecessor, it can be installed in the same vehicles where it will provide very efficient performance.
“Our engines are typically deployed in off-highway applications like agricultural and construction machines, which are in constant use and move heavy loads. We’ll continue to need an internal combustion engine to move those machines. For now, it will be in the form we use today: the diesel engine. Synthetic fuels or hydrogen can considerably prolong their deployment,” explains Alejandro Castilla De La Hoya, Zafra Plant Manager.
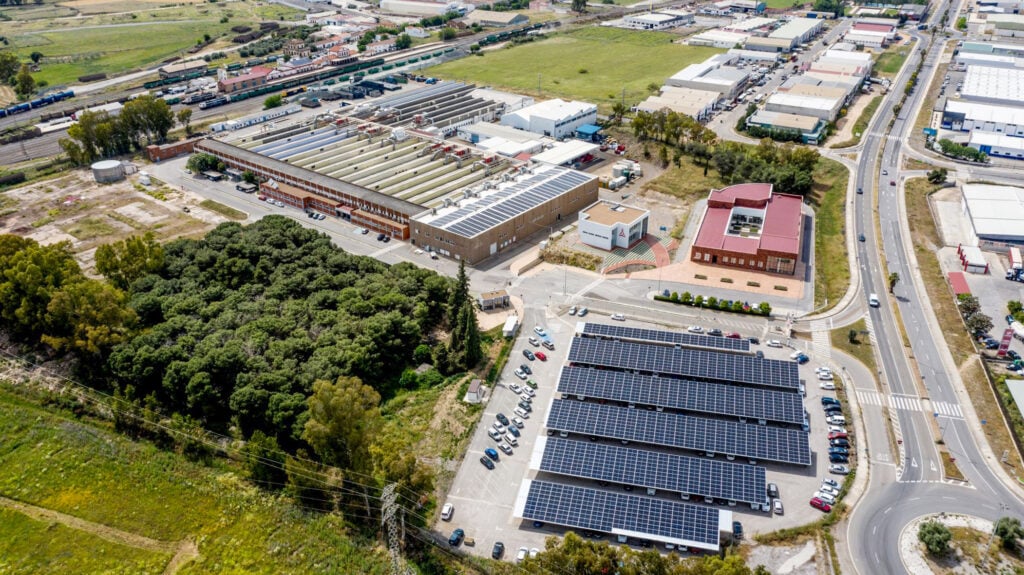
He points out that the income from this area finances DEUTZ’s investments in the green segment, which is dedicated to the transformation of mobility. The 3.9-litre diesel engine is already set to run on gas or hydrogen in the future. “Based on today’s design, this diesel engine can become a green engine in the long run,” says Manuel Rodríguez López, Industrialisation Manager. This is possible thanks to small modifications, particularly to the cylinder head. However, the engine remains mostly the same. MAPAL is already collaborating on DEUTZ’s first hydrogen engine – a huge 7.8 litres.
Two weeks from design freeze to offer
“Our clients’ development periods for new parts are becoming shorter and shorter,” explains Thomas Spang, Global Head of Tool Management at MAPAL. This represents a growing challenge for tool manufacturers or complete suppliers like MAPAL. This is true if plans change at the last minute while the deadline for the tool design remains the same. For the engine block of the new 3.9-litre diesel engine, MAPAL only had two weeks after the design freeze to complete a final offer.
An ardent team of experts in Aalen completed this ambitious task on time. Well-tuned workflows and many years of experience with the client’s production methods proved advantageous for the team. MAPAL has been conducting tool management for DEUTZ in Spain for 18 years and several projects have been completed together over the years.
MAPAL already engineered the machining of the engine blocks for the predecessor 3.6-litre diesel engine, which meant they could draw on practical experience and didn’t have to start from scratch. For example, the tool experts already knew which machines the engine manufacturer had from previous projects. DEUTZ has equipped its assembly line in Zafra with new 5-axis machines over recent years so that they can easily switch to new products.
When DEUTZ sent their request, the Tool Management department, in collaboration with the Technology Expert Team (TET) in Aalen, first gave some thought to the production process. “To be quick here, we don’t concern ourselves with detail at this early stage, but instead pull together reference tools and concepts from previously completed projects,” explains Harald Traub from TET. As a project engineer, he is responsible for planning the entire process. “In this way, we can specify an approximate budget and the rough scope of the tool package for the client.”
One hundred different tools for an engine block
After this rough planning, the concrete tool design followed in the second week. In the end, MAPAL’s offer for the series production of the motor block included almost 100 different tools. Many custom tools achieve short machining times and, thus, high economic efficiency. Aside from these, standard tools are used mainly for milling.
A few close-to-standard tools were also used to produce prototypes quickly. Series production can then begin with the optimal set of tools. As part of their original delivery, MAPAL supplied consumable tools as well as the required tool holders and adapters to DEUTZ. All other consumables will be handled by the tool management on-site. From now on, the client no longer pays per tool but per completed part—i.e., the cost per part is billed.
The unit costs at first correspond to the price determined during engineering. Certain ratios have been agreed upon for the following years. The client receives an increasing rebate percentage and pays a bit less per unit every year. For this business model to work out, MAPAL has to implement continual improvements to save costs. This is done with new tool technologies and corresponding optimisation. The costs per part are fixed over the contract term, after which a reassessment occurs. Such contracts run over four to five years and offer the client planning security.
“With our engineering expertise, we support DEUTZ beyond the tool-setting area and cultivate a close partnership,” Spang highlights. After helping to build the prototype, it is the tool management’s turn to shine on-site during series production. DEUTZ uses approximately 1,300 different tools in total. Thousands of tools are available from stock and must be managed in Zafra. To keep inventory optimal, MAPAL uses its warehouse management systems and digital solutions with the cloud-based software c-Com for tool management. The Digital Tool Management 4.0 doesn’t only handle procurement processes, which are initiated semi-automatically; it also acts as a reporting tool to analyse cost drivers and stocks.
Industrialisation Manager Manuel Rodríguez López praises the good collaboration with MAPAL regarding tool management: “Over the course of our cooperation, we have developed extensive technological concepts, which go far beyond mere logistics. Besides achieving cost reductions, tool setting is particularly important for us. The MAPAL employees working on-site have much know-how and ensure that production has exactly the tool they need at the right time.”
MAPAL’s tool manager on site is David Castaño. MAPAL also employs tool setters permanently in Zafra. They make sure that a dozen different parts are produced without a hitch. “It is very beneficial to have David here on-site with us,” emphasises Manuel Padilla Fernández, Manufacturing Engineering Manager at DEUTZ. “We can talk about any opportunities for optimisation directly at the machine. We don’t consider David Castaño an external service provider but a part of our team. It’s a very strong cooperation.”
Developing together to solve problems
If required, new tool solutions can be developed in Aalen via the local MAPAL team. That was the case in Zafra when it became necessary to optimise the tools for machining the bore in the crankshaft and camshaft. A new machining concept from MAPAL with the HPR400 reamer was implemented in cooperation with DEUTZ. David Castaño is convinced of its advantages: “The tool life of the previous tool was 350 units, and resetting was required every 100 units. With the HPR400, we achieve a tool life of 1,000 parts without resetting. The resulting machining quality is exceptionally good.”
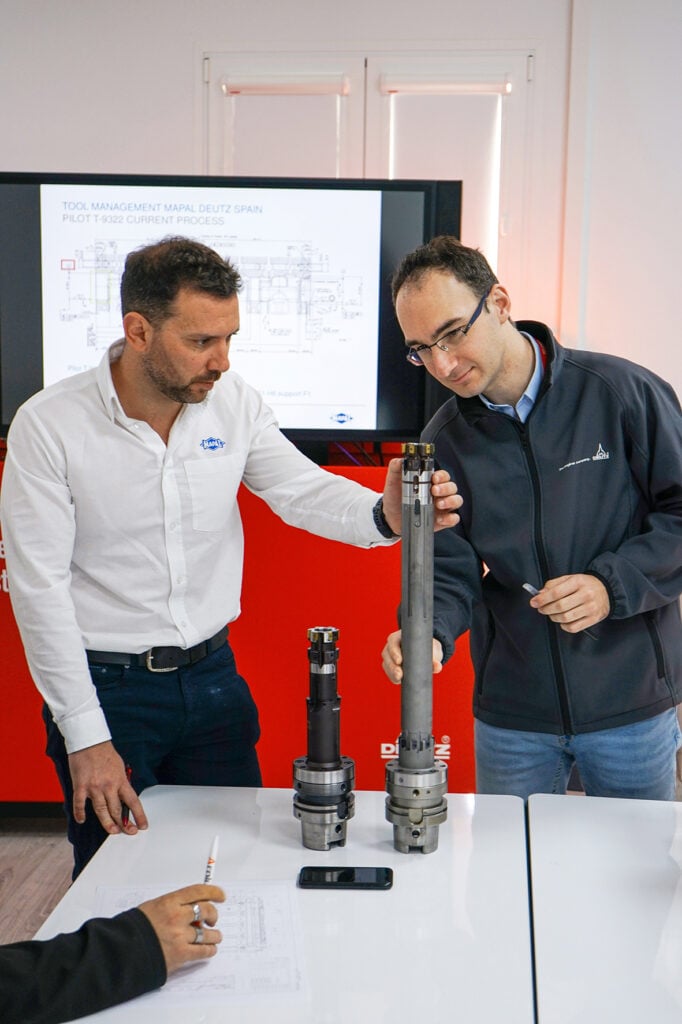
Incentives needed to ease bumpy ride along Electric Avenue
The electrification transition and inflexible EV production quotas are taking a heavy toll on the automotive industry, but buses and commercial vehicles posted their best years since 2008. Will Stirling reports.
MTD magazine is unwaveringly positive in its coverage of manufacturing news, but facts are facts: automotive manufacturing is on a downward slide. Combining cars and commercial vehicles (CVs), the UK produced 905,233 units in 2024, -11.8% from 2023, and slipping below the psychologically important one million units mark. Electric vehicles now comprise over one-fifth of all new car registrations, but the EV market contracted by 2.5% to 139,345 units. The bright spots are in the commercial vehicle (CV) and bus markets. Production in the UK rose 4% to 125,649 units, and both buses and CVs have had their best years since 2008.
Carmakers face a multitude of challenges to produce both ICE (combustion engine) and EV cars in high volume. Higher energy and material costs, shortage of skilled people and potential tariffs on exports to the US, but the two most significant factors affecting the production of cars are the costly transition to electric and globally softer demand. The government has set onerous targets for the proportion of EVs that car companies make in Britain, from 22% last year to 28% this year – a tall order that experts believe won’t happen – and 80% by 2030, after which the ICE car ban kicks in. The problem is that these targets are running ahead of demand.
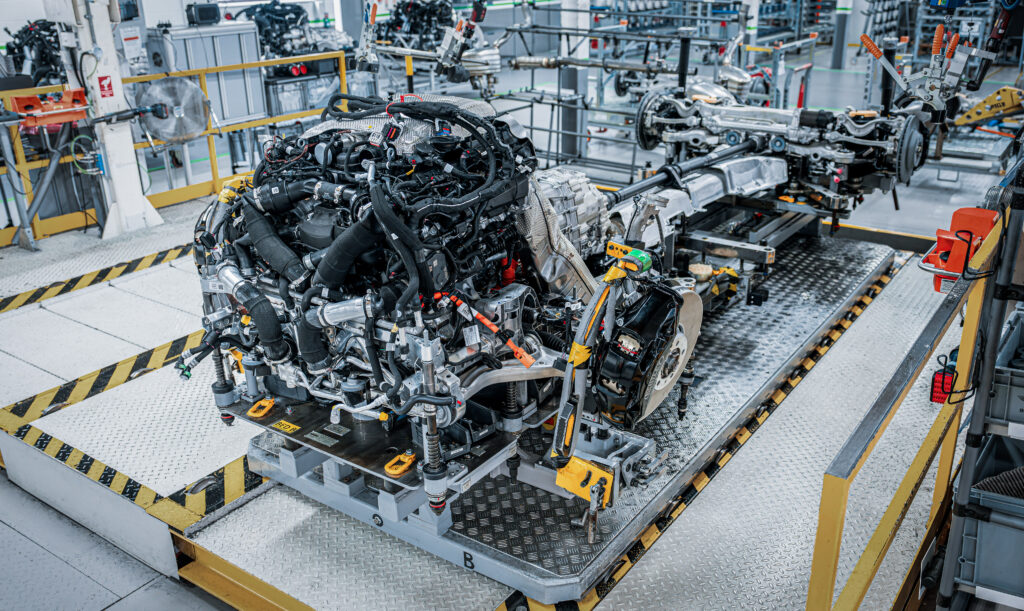
“The targets were set when demand forecasts were much higher; we know there’ll be a significant shortfall,” says Professor David Bailey, an automotive business expert at the University of Birmingham. “Car firms are going to struggle to shift that volume of cars without very significant discounting, and therefore losses.”
He adds: “Our two biggest producers, Nissan and Jaguar Land Rover, will struggle to meet that kind of stretched targets as they get bigger, so they will potentially be fined, and they may well have to buy credits from Chinese all-EV makers who can hit the target. So what a perverse policy that is – that you’re subsidising the Chinese and fining domestic manufacturers.”
Electric vehicle production and net zero targets have not been intelligently assessed. The government intends to phase out new petrol and diesel cars by 2030, and although the car industry was invited to consult on this in December 2024, many think the target is too early to hit.
“The 2030 ban on ICE policy was plucked out of thin air to try to differentiate the UK from the European Union while signalling to investors that the UK is serious about decarbonisation to encourage investment in the UK. But it hasn’t worked – because Brexit has made the UK less competitive and attractive, because of high energy costs, and it hasn’t worked because we don’t have a proper industrial strategy to support that transition,” David says. The government is now consulting on the industrial strategy, but it should have been firmly embedded in 2025 to help hit the 2030 ICE ban effectively.
Stimulate demand; cost of electrification bites
Demand for electric vehicles needs to be higher. The government has proposed cheap loans for EVs, but it sounds too complicated for the average car buyer, who wants to know the price, not a complex subsidy and loan. And a VAT break on EVs has been proposed, although this is a pro-tax government. “The government’s problem is that it has boxed itself in agreeing to continue the fiscal rules that the Conservatives put in place, which I think was a bad mistake all along, and that has limited their room for manoeuvre. The industry wants a fiscal incentive for EVs, which could either be an upfront discount if you buy one or a VAT reduction on purchases and charging, to stimulate demand,” Bailey says.
Demand for vehicles aside, car production volumes are also lower because factories spend millions of pounds and months retooling their lines for EV manufacture, affecting their ability to produce.
Internalisation of component manufacturing
Some tier one and smaller suppliers to UK automotive have gone, due partly to the complications and costs of Brexit. GKN Automotive moved its Birmingham factory capacity to Poland in 2021/2022. A lot of smaller companies have been cut out of European supply chains post-Brexit, and several auto suppliers have struggled or gone out of business, unable to cope with the export and reimport bureaucracy when some components may cross the English Channel several times before being assembled here.
In addition, several big carmakers are internalising the manufacture of key components as these companies aim to be more vertically integrated. “Partly, this is in reaction to the semiconductor crisis where firms were caught out,” says David Bailey. “For example, Jaguar Land Rover will be making its new electric drive train in-house, probably at the i54 plant. Previously, for internal combustion engine cars, JLR would have bought the drives from GKN Driveline, but it is internalising it. We are seeing that shift broadly as well.”
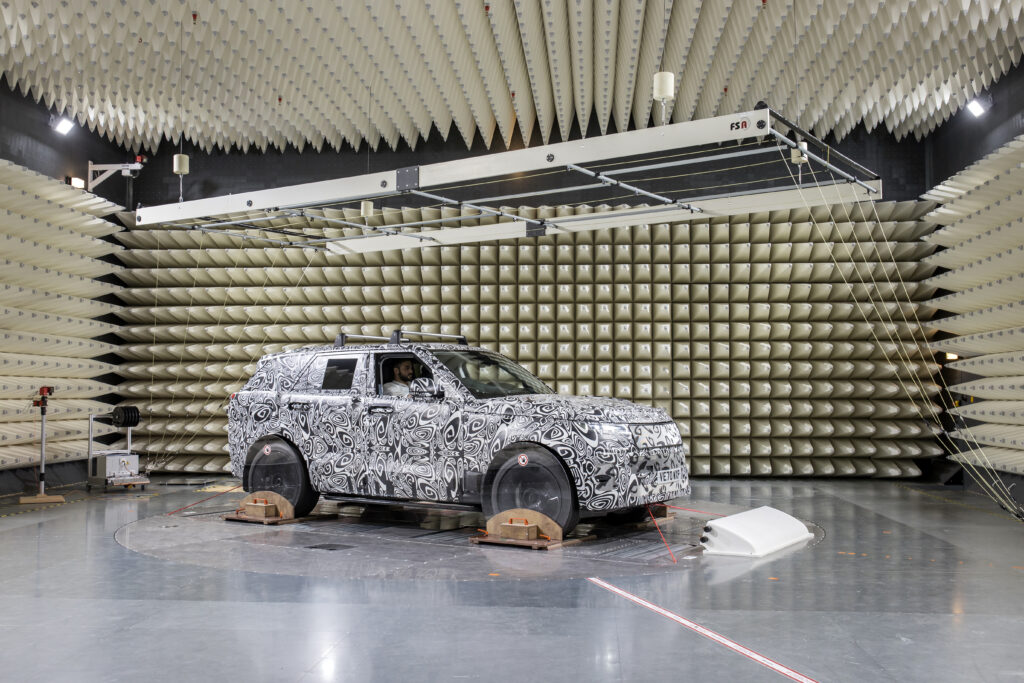
A good example is Nissan’s partnership with battery company AESC, which supplies directly to Sunderland. This year, Nissan is expected to open a new 360m long, 23x football pitch-sized battery gigafactory in Sunderland. When operational, it will employ over 1,000 people and deliver a sixfold increase in UK electric vehicle battery production. The plant is basically an extension of Nissan’s car factory, a tier-one supplier part-owned by Nissan right next door.
Pay attention, subbies: Bus bonanza
Deliveries of new buses, coaches and minibuses reached a 16-year high in 2024, with 8,390 new units hitting the UK’s roads (total buses produced were higher due to healthy exports). Demand rose across the three main segments: minibuses, single-deckers and double-deckers, with minibuses posting 102.5% year-on-year growth. Zero emission is the main story in buses, and the UK is still Europe’s biggest zero-emission bus market, with deliveries up by more than a third in 2024.
As of 2023, Ballymena-based bus manufacturer Wrightbus reported a turnover of £283.4m, a significant 71% increase from £163.3m in 2022. Despite this, profits in 2023 were negative, probably reflecting the big investment in transitioning to net zero powertrains and new tooling. Wrightbus exemplifies the switch to zero emissions. “Alongside our market-leading EV bus, 95% of all buses produced by Wrightbus in Ballymena are now zero emissions – a marked change on 2019, when 95% of all orders were for diesels,” said Jean-Marc Gales, CEO of Wrightbus, when unveiling the new Streetdeck Hydroliner Gen 2.0 hydrogen-powered bus on 20 February.
Wrightbus says production will increase to 1,200 this year and then again to 1,400 in 2026 – a record in the company’s proud history of bus manufacture. Dozens of suppliers from across the UK and Europe visited the Wrightbus factory in February to hear how the firm’s continued growth will act as a shot in the arm for the manufacturing sector, with the expected creation of up to 1,000 new supply chain jobs in the next two years.
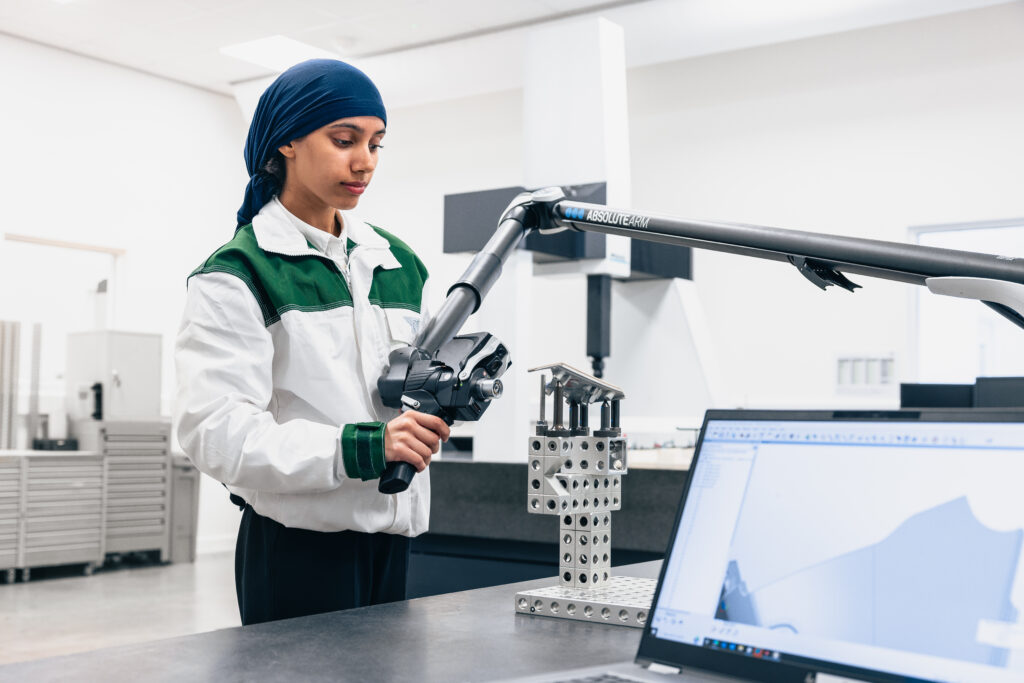
When will car making recover?
Industry body The Society of Motor Manufacturers and Traders forecasts vehicle production to fall further in 2025 (cars and light vans to 839,000 units in 2025). Still, it adds that while the EV transition is affecting production, this will be temporary. While the volumes of all electrified technology cars were down 20.4% in 2023, with more than £20 billion worth of investment announced in 2023 and a further £3.5 billion in 2024 to support the UK’s transition, the decline will be temporary; the SMMT stated in February. Car and light van output will increase to circa 930,000 units by 2027, it says.
However, potential tariffs from the US are a real threat (second biggest UK car export market), and the lingering cost of living crisis affects EV sales. “Charging at home overnight is cheap but can be 10 times the cost at some public charging points. Plus there is 20 percent VAT at a charging point, but just five percent at home – so the one third of people who have no ability to charge at home will struggle with the transition,” says David Bailey. And while the Dept for Transport has said it is on track to install the target 300,000 charging points by 2030, many people have range and charging speed anxiety, so much more PR is needed to persuade a cash-strapped, conservative public to go electric.
Tooling Intelligence supports ITC at Progressive Apprentice Academy
Edging closer to its 50th anniversary, the Progressive Technology Group has enjoyed a meteoric rise over the last decade. Founded in 1977, the relocation to larger premises in 2013 was one of the many catalysts for the Newbury company’s decade-long growth.
Opening multiple new divisions and branching into new markets, the company now employs more than 250 staff. Among its accolades are many prestigious awards from AMG Petronas and Rolls-Royce, to name a few. However, this pedigree cannot be bought; it is embedded in the company’s culture, with Progressive Technology opening its Apprentice Academy in 2015. In this bedrock for developing the talent of tomorrow, Tooling Intelligence Ltd has just donated a SmartDrawer® vending solution.
The impressive Apprentice Academy at Progressive Technology enlisted 18 apprentices as part of its 2024 cohort, and this production line of talent nurturing has contributed significantly to the business’s ongoing success. Aiming to mirror the high-tech manufacturing facilities, the Apprentice Academy has a complete range of technologies, from simple two and 3-axis manual machines to high-end 3 to 5-axis multi-functional machine tools. Three full-time trainers and a classroom with PCs support academic and computer-based training. Part of this progression from apprentice to a skilled engineer in an advanced manufacturing facility includes using high-end cutting tools and the associated inventory management systems.
With technical partner Industrial Tooling Corporation (ITC), Tooling Intelligence installed its first vending solution at the ISO:9001 and AS:9100 subcontract outfit in 2014. The success of this first SmartDrawer® system led to a second installation in 2016 and a third in September 2024.
The versatile SmartDrawer® system from Tooling Intelligence is a drawer system that is completely configurable to the end user’s requirements. Using smart technology, the SmartDrawer® can dispense single or multiple items with reliable, accurate, and monitored inventory control, giving the end user complete visibility and control of its supply chain. The benefits of the SmartDrawer® were evident at Progressive Technology, and this is why the company rapidly adopted additional systems when shop floor inventory management required them.
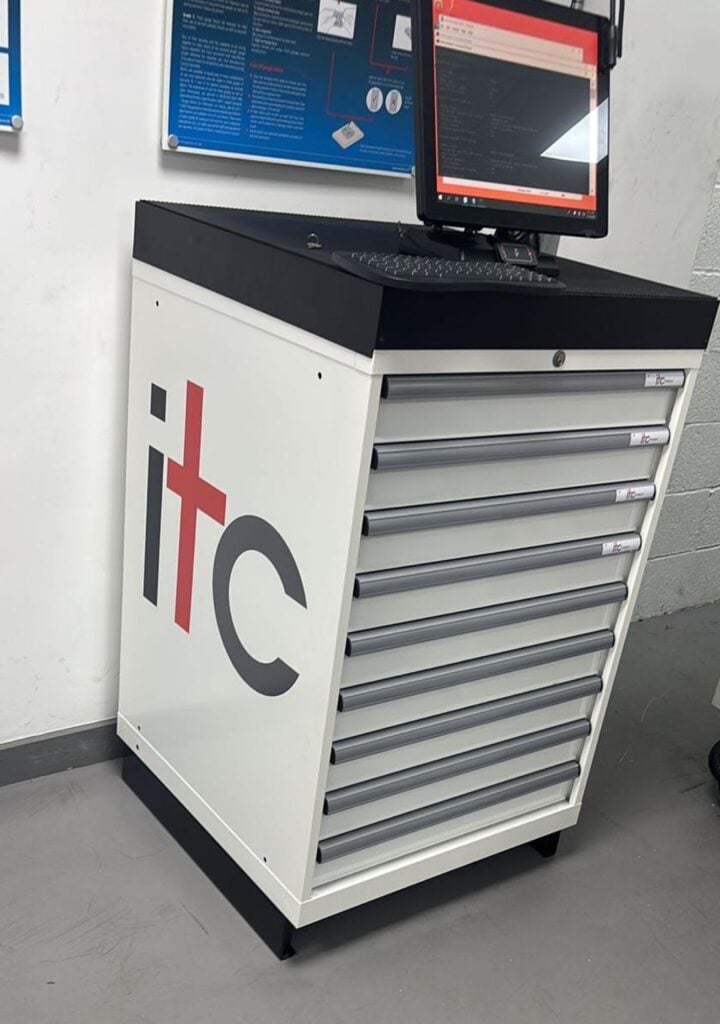
The SmartDrawer®, which comprises individually locked compartments controlled by a user-friendly touchscreen interface, provides ‘self-serve’ access to consumables, equipment, and cutting tools. This has enabled Progressive Technology to manage, monitor, and control its cutting tool consumption with greater visibility while automatically re-ordering stock to ensure the right tool is always available. With a complete audit trail, the SmartDrawer® provides visibility regarding which employee uses which specific item and where and when it is used. With apprentices destined to enter the advanced production facilities in the future, understanding the inventory management process at the West Berkshire company is essential. This is why Tooling Intelligence has made such a generous contribution.
The December 2024 arrival of the SmartDrawer® in the Apprentice Academy was installation number four, with the fifth SmartDrawer® being installed simultaneously on the shop floor of the 24/7 manufacturing site. As part of Tooling Intelligence’s donation, ITC has supported the installation with a selection of regularly used cutting tools for the Apprentice Academy. Included are a complete selection of solid carbide and indexable milling and turning tools. The apprentices now have access to the consumables they require as and when they need them from a single source system.
Commenting upon the installation, Tooling Intelligence’s Managing Director, Richard Swaffield, says: “We are delighted to support such a valuable customer in their growth journey over the last 10 years. An industry-leading subcontract manufacturer’s repeat business for over a decade is a testament to how our SmartDrawer® system delivers an inventory management system that is bespoke to the demands of each customer. Since investing in its first SmartDrawer®, Progressive Technology has witnessed cost savings, improved inventory management and control, and complete visibility over what products are used and when. This level of insight is essential for the future of any modern manufacturing business. This is why we have donated a SmartDrawer® to the Apprentice Academy at Progressive – the talent of tomorrow needs a complete understanding of the benefits of effective inventory management as well as the implications of not managing your supply chain.”
Kennametal revs up innovation with 3D printed tools
Building on the success of their award-winning 3D-printed stator bore tool for electric vehicle machining, Kennametal has developed an innovative 3D-printed transmission housing tool for Voith that cuts weight by approximately 45% and reduces machining time by approximately 50%.
As transportation components become increasingly more sophisticated and the requirements more stringent, manufacturers need complex tooling solutions to machine those components. That poses a challenge as the weight of such tooling can become too heavy for efficient operation on machining centres, tool changers and tool magazines. Machine operators may also have difficulty managing the tool.
A recent collaboration by Kennametal, an industrial technology leader, and Voith, a leading supplier of drive technologies, shows how 3D printing offers a pathway to novel, lighter-weight tooling solutions that overcome these challenges while improving productivity and efficiency.
The Challenge: Machine multiple, tight tolerance, large diameter bores with
existing machining centres
Voith wanted an innovative solution to optimise its machining processes for transmission housings further. To achieve the required tolerances, the company needed a multi-stage tool capable of machining multiple bores in one operation. The tool also needed to have two effective cutting edges on the main diameters to achieve the specified cycle time. Finally, the tool had to weigh less than 12kg to meet the requirements for tool changing and tilting moment on the toolchain.
“Finish machining a large aluminium housing with multiple bores up to 350mm and IT7 tolerance grade is a demanding application,” said Werner Penkert, Manager of Product Engineering. “To machine these large bores with such tight tolerances, we need very rigid tools, which typically means they are heavy weight. When manufactured using conventional methods, a typical tooling solution for this type of application could weigh as much as 25kg, which is too heavy for the existing machines or for an operator working with the tool.”
Intrigued by how Kennametal leveraged 3D printing to produce a lighter-weight stator bore tool for electric vehicle machining, the Voith team turned to the industrial technology leader to collaborate on a solution.
“Kennametal’s innovative approach with 3D printing excited and inspired us to take this path together,” says Friedrich Oberländer, Director of Production Technology at Voith.
The solution
As with the stator bore tool, Kennametal leveraged its expertise in metal additive manufacturing—plus the concept of generative design to meet the demanding requirements of Voith’s transmission tool.
With conventional subtractive manufacturing, weight is reduced by removing excess material. However, with 3D printing, manufacturers can start with nothing and put material only where it is needed, resulting in lighter-weight, more complex geometries not possible via conventional manufacturing processes.
To fully leverage additive manufacturing’s design freedom, Kennametal used generative design, an iterative process that optimises the design of 3D-printed parts to meet an application-specific set of constraints. The generative design process often results in complex, organic shapes reminiscent of natural structures.
In the case of the Voith tool, generative design directly addressed machining forces on the tool, enabling Kennametal to design a solution optimised for stability, stiffness, balancing and coolant supply—with a weight of just 11.5kg.
Kennametal applied its expertise in additive manufacturing and machining to produce the tool. The tool pockets are precision machined and designed to be used in combination with Kennametal’s proven RIQ inserts technology.
“Additive is one tool in our toolbox, but we also applied our deep expertise in precision machining to develop a novel solution that efficiently addresses the challenges of boring deep holes in conjunction with multiple large diameters,” Penkert.
The design of Kennametal’s 3D-printed transmission housing tool mimics the organic shapes found in nature, delivering reduced weight and a 50% reduction in machining time for the customer, Voith.
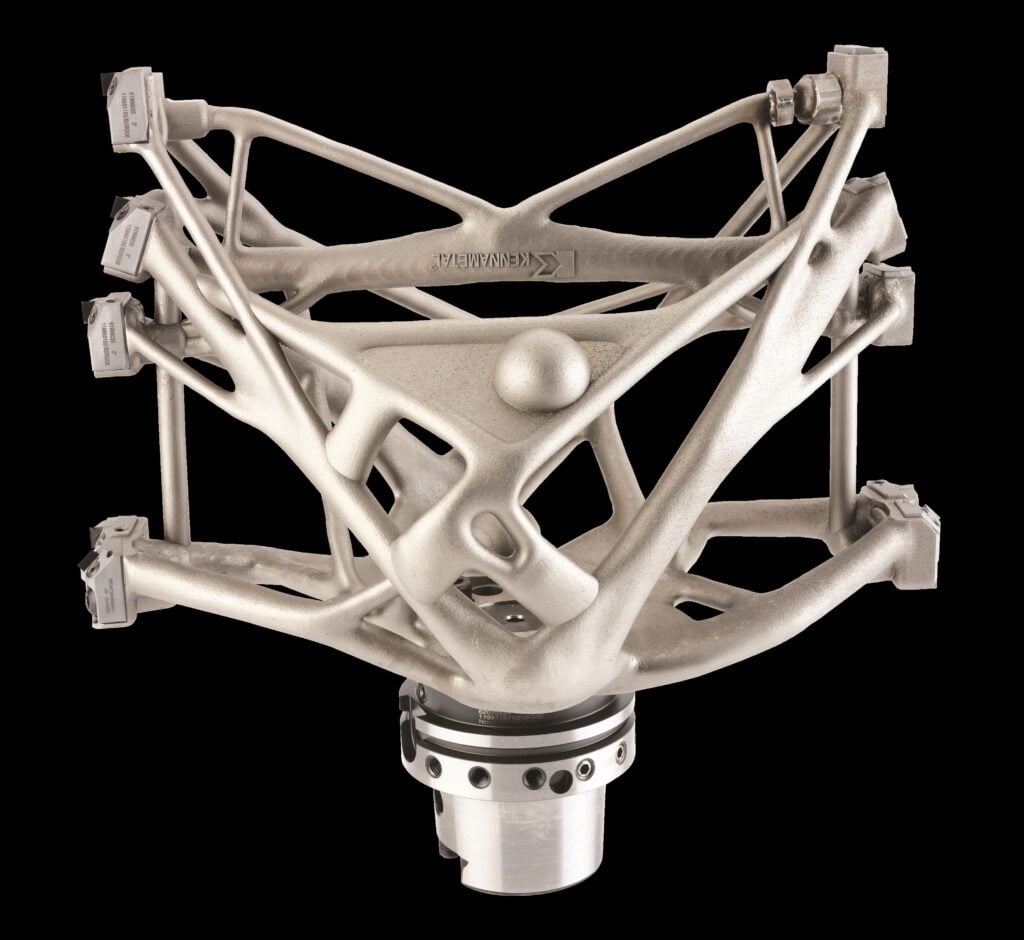
The Results: 50% reduction in machining time
Working in close collaboration with Voith, Kennametal manufactured a prototype tool and put it to the test in its demonstration centre in Fürth, Germany—part of a global network of test and demonstration centres where the company works with customers to design, iterate and validate machining solutions.
This solution was particularly challenging in achieving both manufacturing and part quality requirements. Design simulation, additive manufacturing, and practical tests in the demonstration centre allowed the team to validate the machining results. Voith then conducted the first tests on-site, followed by longer-term tests for series production. Further customer requirements were implemented, and the tool was jointly perfected and finalised.
“The Kennametal tool delivered outstanding quality and performance from the first use, achieving a 50% reduction in machining time while still meeting accuracy and surface finish requirements. Additionally, the reduced weight limits the load on the magazine, tool changer and spindle—effectively reducing maintenance costs,” said Oberländer. “Our collaboration with Kennametal clearly shows the enormous innovation potential of additive manufacturing when applied in such a cooperative partnership.”
Kennametal Additive Manufacturing (AM) offers a game-changing solution by utilising high-performance materials and parts that are produced faster and with the design flexibility of 3D printing.
Kennametal brings nearly a century of materials and manufacturing expertise to every layer of the AM process—from raw material to finished part. This helps customers unlock the full value of 3D printing for applications demanding wear, erosion, corrosion, and high-temperature performance.
Automation delivers results
Mills CNC has recently supplied Ayrshire Precision, a subcontract specialist based in Ayrshire, with two new SYNERGi systems. The systems, both derivations and highly customised versions of Mills’ standard SYNERGi ‘SPRINT’ solutions, were installed at Ayrshire Precision’s 14,000sq/ft site. In 2023, the first system was retrofitted to a Puma 2600SY lathe, and six months later, the second was retrofitted to a Puma 2100SY.
SYNERGi Sprint automation systems are compact, flexible, and cost-effective. Mills’ dedicated automation experts can integrate them with DN Solutions’ lathes, machining centres, and mill-turn machines to create high-productivity automated manufacturing cells.
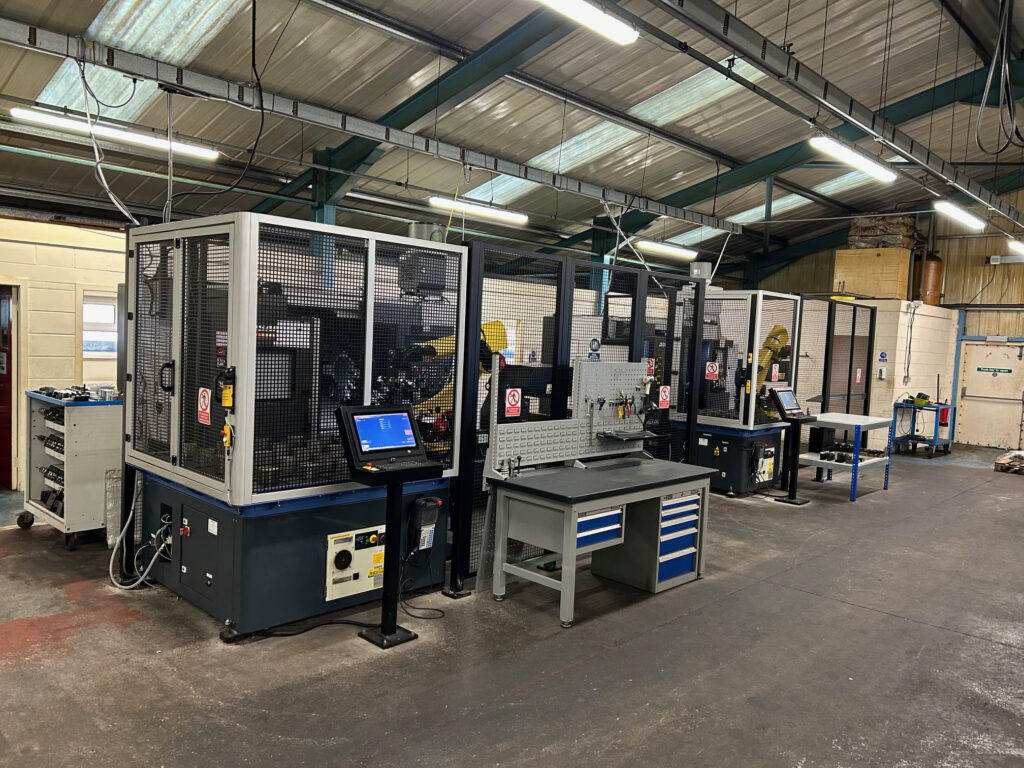
The essential elements of a SYNERGi Sprint system comprise an industrial FANUC robot with varying payloads and reaches, a two- or three-jaw pneumatic gripper, a 900 by 900mm part loading/unloading grid plate, and industrial safety guarding positioned around the system. Mills can also supply customers with multi-socket inserts to optimise each system’s capacity. These are sheet metal fabrications that customers can also choose to manufacture for themselves.
Ayrshire Precision serves customers in the oil and gas, subsea, renewables, power generation, and aerospace sectors. It has a well-resourced machine shop and regularly invests in its people, plant and equipment, processes, and systems as part of its ongoing continuous improvement programme. Since 2012, Ayrshire Precision has invested in various Doosan machines, from two-axis and multi-tasking lathes to large-capacity, heavy-duty vertical machining centres and horizontal borers.
“We rely on machine tools from Mills. They are powerful, fast and accurate and enable us to meet the highly-regulated, tight-tied up tolerances and exacting surface finishes that characterise a majority of the components we machine,” says Chris Hepburn, Ayrshire Precision’s Managing Director.
Ayrshire Precision’s decision to invest in automation was made for several reasons. The volatility of the markets served by the company and, as a consequence, fluctuating customer demand for the company’s machining services, combined with difficulty recruiting and retaining skilled labour, all contributed to Ayrshire Precision’s decision to ‘think outside the box’ and begin its automation journey.
“It’s either feast or famine in the markets where we operate. We can either be swamped or, due largely to external macro-economic factors that impact our customers’ business, can experience order cancellations and/or postponements that make it difficult to match our production capabilities and resources with changing customer requirements,” explains Chris Hepburn.
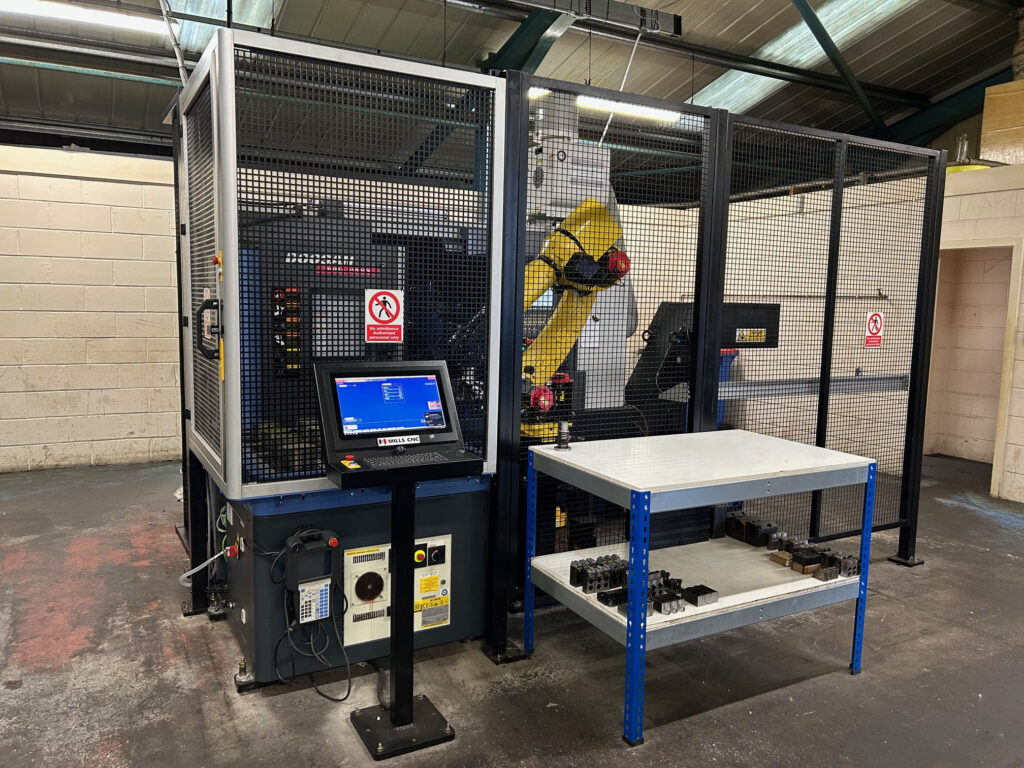
Rather than be at the mercy of market forces and to protect the company’s long-term viability and profitability, Ayrshire Precision decided in 2020 to explore new ways to improve its flexibility, performance, and competitiveness. The company’s focus was initially on its small part-turning operation, which, at that time, comprised two Puma lathes, running over two shifts and operated by four staff members.
To increase the productivity of its Puma lathes, the company had previously considered integrating a bar feeder into each machine. However, the diameters of the machined drop forged parts, the batch sizes required, and the limited diameter capacity of the bar feeders prevented this approach.
Ayrshire Precision discussed its requirements with several automation system suppliers, focusing on the proposed system’s configuration, availability, and cost. As part of its decision-making process, Ayrshire Precision visited Mills CNC, which had previously supplied it with eight Doosan machines.
After discussing its plans further with Mills’ automation application specialists and seeing a couple of different SYNERGi systems in action at Mills’ Technology Campus facility in Leamington, it was confirmed that two separate SYNERGi Sprint systems would better meet Ayrshire Precision’s manufacturing requirements.
“We liked the design and build of the SYNERGi Sprint system,” remembers Chris Hepburn. “It was simple.”
“We asked Mills to put forward their plans and proposals for two SYNERGi Sprint cells – one incorporating our existing Puma 2600SY for larger parts, and the second incorporating our Puma 2100SY for smaller components.”
Says Chris Hepburn: “Mills’ approach was responsive and helpful. They worked with us to tailor-make the SYNERGI Sprint systems and offered useful advice. We placed the business with Mills, not just because of their technical and automation expertise, but also because they had originally supplied the two Puma lathes and knew the machines inside out. We also thought that dealing with one supplier for our machine tool and automation system requirements would be easier and would simplify communications, servicing, training, etc.”
Ayrshire Precision’s first manufacturing cell was installed in March 2023. The cell comprises a Puma 2600SY multi-tasking lathe and a FANUC 35kg industrial robot with dual Schunk 3-jaw grippers. Other elements include Renishaw probing systems, safety caging, and the system’s HMI control driven by Mills’ proprietary SYNERGi software.
With individual part cycle times of approximately 10 minutes, Ayrshire Precision is now benefiting from up to an additional 16 hours of unmanned operation of its Puma 2600SY lathe. Since installation, the company has manufactured different sheet metal pocket inserts to accommodate larger parts and different batch volumes.
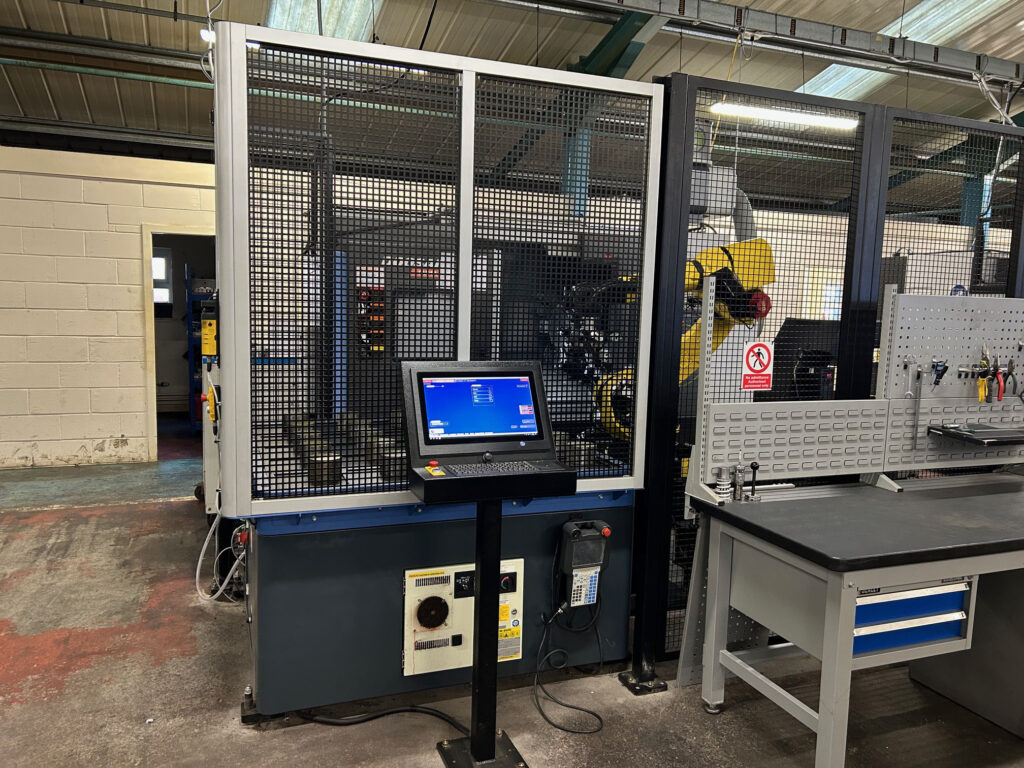
Ayrshire Precision’s second SYNERGi cell was installed in September 2023. This cell incorporates the Puma 2100SY lathe, a 20kg payload industrial robot and a 900 by 900mm table for processing smaller components. The automation process for both cells involves the robot picking up a workpiece from the grid plate in a programmed sequence and, using the lathes’ auto door opening facility, loading the part into the machine’s main spindle. The door closes to enable the machining of the part’s front end.
After all machining operations are finished, the robot picks up the next sequenced workpiece from the table and, in one continuous movement, loads it into the main spindle. Then, it removes the finished part from the sub-spindle and returns it to its designated position on the table.
Says Chris Hepburn: “Every time the auto door opens, a completed part is removed from the sub-spindle and a new part is loaded into the main spindle. The process is fast, seamless and continuous. Furthermore, one staff member can operate both cells simultaneously.”
With less labour intervention required, Ayrshire Precision’s small part turning operation is now more efficient and profitable. Creating its two cells has also helped free up a couple of its operators, enabling them to be deployed to other machine shop areas.
Chris Hepburn concludes: “The investment in our two SYNERGi cells is paying dividends. We have two inherently flexible automated cells that have not only helped us future-proof our small-turned-part operations but have also increased our overall capacity. Although there was initially some anxiety concerning our move towards automated production, the results exceeded our expectations.”
hyperMILL lights up productivity gains for medical manufacturer
Opening its doors with just four toolmakers 50 years ago, Smithstown Light Engineering Ltd is now a business with three manufacturing sites and over 165 employees. Working with the world’s leading medical device and orthopaedic companies, Smithstown extensively uses OPEN MIND Technologies‘ hyperMILL CAD/CAM suite to streamline its throughput and maximise efficiency.
Initially a toolmaking business supplying plastic injection moulds to the electronics industry, the Shannon-based business transitioned to medical manufacturing in 1990—and it hasn’t looked back since. With two sites in Shannon spanning 80,000sq/ft and a third 15,000sq/ft facility in Poland, 75% of the company’s technology is less than 5 years old. Certified to ISO: 9001, ISO:13485 and ISO:14001, Smithstown has a bank of Citizen sliding head turning centres, in-house heat treatment, Rollomatic, Jung and Jones & Shipman grinding centres, DMG MORI and Mikron machining centres, Trumpf 3D additive manufacturing and Makino EDM technology.
Working with renowned clients such as Stryker, Boston Scientific, Zimmer Biomet, and Cook Medical, to name a few, the company provides a turnkey service from concept and design through prototyping, machining, and validation of medical components and orthopaedic implants. With over 14 million components manufactured annually, the Irish manufacturer adopts stringent quality measures that are a necessity for ultra-precision medical device parts used in life-saving surgery.
Alluding to his role within the company and a background in Smithstown Engineering, Gerard Henn from Smithstown Light Engineering says: “I’ve been here now nearly three years in the role of CEO, and I support the principal director of the business in the running of the operation. Smithtown started in 1974, so we are now 50 years in existence. Our principal area of expertise is precision machining to impeccable quality levels with customer service. We really pride ourselves in supporting the customer in all their difficulties and all their successes.”
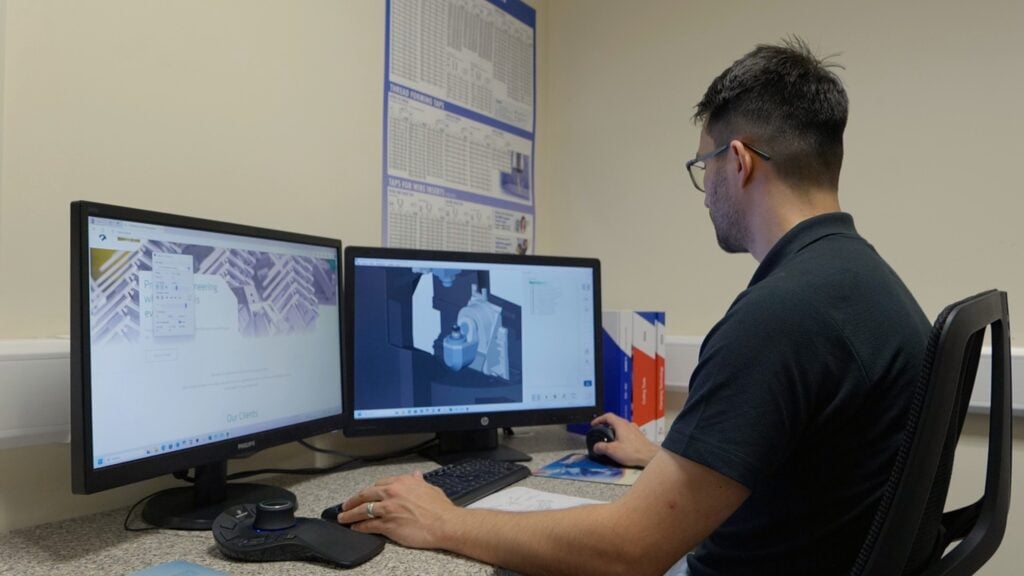
Manufacturing high precision parts to stringent standards, Gerard alludes to why the County Clare company opted for hyperMILL from OPEN MIND Technologies: “There are so many different options in the marketplace, but OPEN MIND made it much easier for us to work forward with hyperMILL. The explanation of the facets, the features, and how we could optimise our machining strategies and cutting paths – it has everything. That worked in our favour. The relationship with OPEN MIND and its hyperMILL system came together and created a partnership with us.”
When Gerard joined the company, one of his aims was to upskill the staff, which was a critical necessity considering the shortage of skilled engineers. Alluding to this, Gerard adds: “OPEN MIND were very enthusiastic and got behind us. They understood what we were trying to achieve, and it’s been a positive relationship all the way through. We’d recommend OPEN MIND to any companies out there who are interested in upskilling their internal workforce – the partnership has been extremely positive.“
Looking closer at the types of work the company is involved in, Gerard continues: “We operate in the medical space, and we support the orthopaedic and medical device companies in Ireland and also globally. We also do instrumentation for procedures, so it’s very much a medical-focused enterprise.”
Occupying a large floor area and two facilities, the company is continually evolving. Gerard adds: “So, we have over 200 employees and two sites here in Shannon. The second site is just literally 1 kilometre down the road, so you find us trekking up and down quite a bit, but you see the same technologies and approach in both buildings. We have a third facility in Rzeszów, Poland, a business that’s been operating for 3 to 4 years. We also recently announced a major expansion there.“
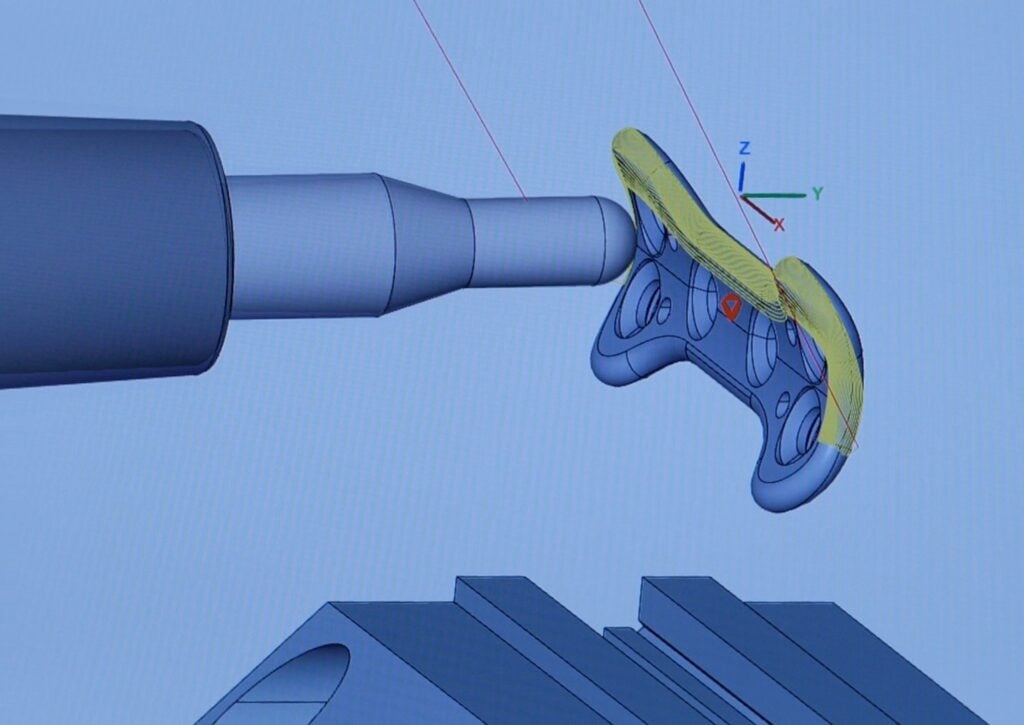
“What we find in any process development is you’re going through an iterative process. You’re optimising the machining and cutting process, checking dimensions back to the machine to the virtual CAD station, and bringing all that together. So, I think the fact that OPEN MIND has supported us so much means we have a great understanding of hyperMILL. The upskilling is well in parallel and enables us to bring all the strands together to succeed. By success, I mean that we can deliver parts to specification earlier. That is because that’s what everyone wants. Customers want parts in their hands, and having that collaboration of everyone allows us to achieve that.”
Lantek delivers for DMS laser profiles
For laser cutting specialist DMS Laser Profiles, fast and accurate quotation preparation, easy program generation for its Trumpf lasers, and responsive after-sales support were the key reasons it chose to replace its existing system with Lantek software in May 2024.
Based in Maidenhead, the company specialises in stainless fabrication, primarily in the petrochemical, process engineering, pharmaceutical, food and water sectors. Initially, it subcontracted the laser cutting but moved this in-house in the early 2000s to improve supply line security and reliability. Josh Hall, Sales Manager, says: “We generate around 230 quotations every month, and we have checked the costs and prices generated by Lantek against the actual costs, and it is really accurate. Additionally, during installation and commissioning, where the costs did not line up, Lantek engineers quickly fixed these discrepancies.” As well as costs for laser cutting, Lantek’s Integra Quotes software also generates prices for other operations, such as folding and welding and outsourced operations. It also generates invoices for completed work and integrates with the company’s accounting software.
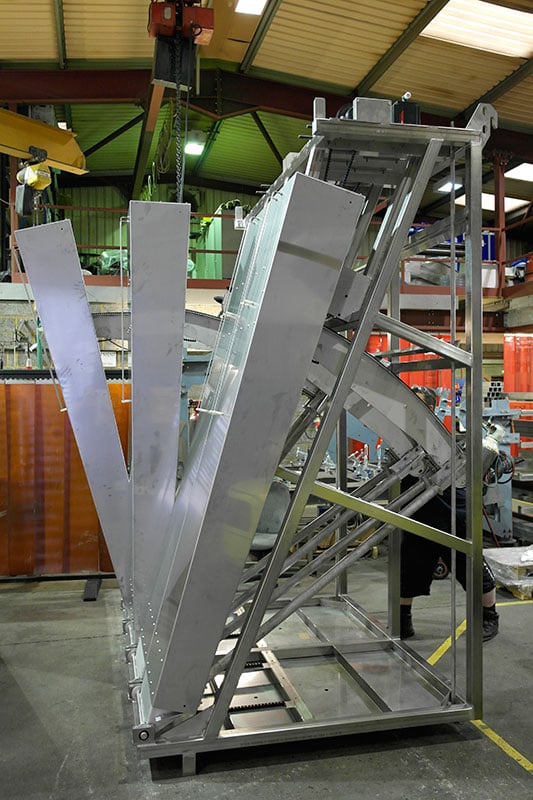
Typically, CAD data for a new job is fed into Lantek Expert for flattening or, where parts are assembled, processed in Solidworks to get the individual flattened components. Around 11 dedicated estimators and programmers use the Lantek software, overlapping responsibilities, pre-nesting parts into 2.5 by 1.25m or 3 by 1.5m sheets as part of the quotation process prior to the final nesting and programming when the job is released for production. Josh Hall adds: “With Lantek we can track parts back to the individual sheet it was made from, which is very important for our ISO traceability requirements. We can also use up remnant material and trace parts made in these remnant sheets, improving material utilisation while maintaining quality standards.”
DMS Laser Profiles has just upgraded its Lantek software to include Lantek MES. This will enable the company to trace parts as they move through the workshop. The laser machines are directly wired into the software so that real-time data is collected, further increasing cost accuracy and making it much easier to plan and execute the production process. Josh Hall says: “Expanding our Lantek software was an easy decision, as the support we get is very responsive, so we are confident that this next step will be a success.”
The addition of Lantek MES will help DMS Laser Profiles integrate and automate its production processes further. Material costs will be updated as they change and the company will be able to anticipate workloads for all its manufacturing stages, enabling it to generate even more accurate costings while scheduling manufacturing flow through the workshop. This will result in precise delivery predictions for its customers’ parts. Furthermore, as data is centralised and accessible, quotations and delivery status enquiries will always be consistent irrespective of who deals with the customer. Lantek’s software achieves all this while greatly reducing the administrative effort and non-productive hours required to maintain high-quality information.
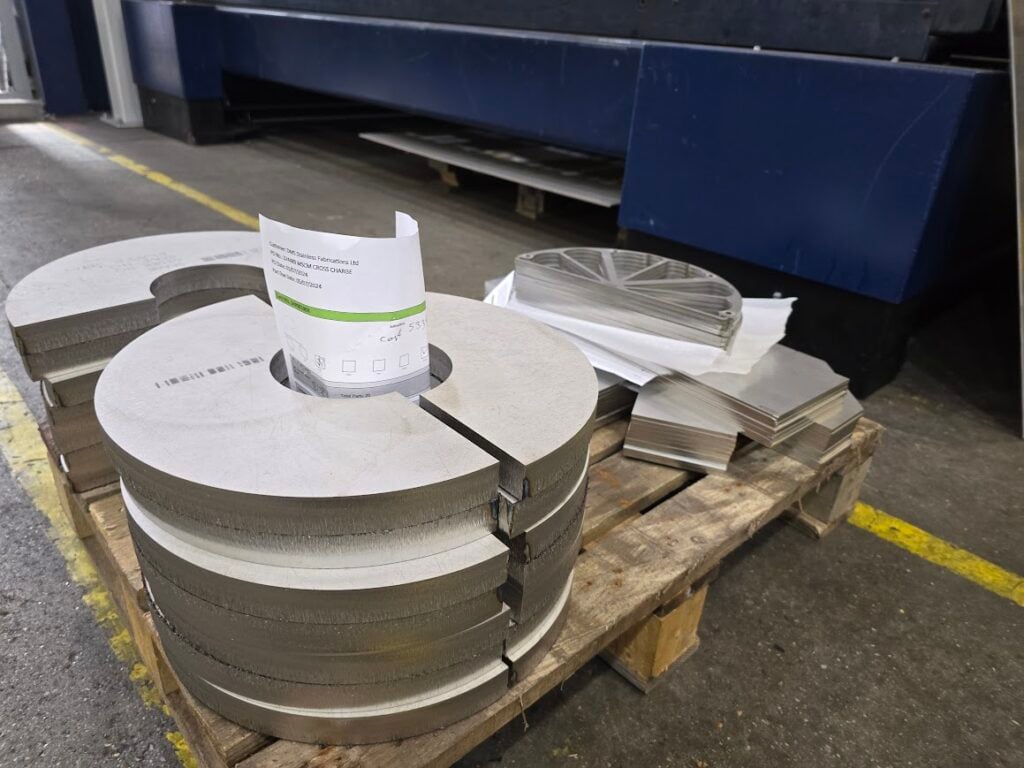
Josh concludes: “The Lantek software is nicely set out and user-friendly. It is much simpler than our previous system and a massive improvement. We will be able to easily track where parts are, and the improved traceability is very important for our ISO compliance. But the most important improvement for us has been the service and response we get from Lantek, quickly fixing any issues we have with the software and its use.”
Efficient milling
Milling is a fundamental process that shapes everything from complex aerospace components to critical automotive parts. But despite its ubiquity, successful milling hinges on some careful considerations. How can manufacturers consistently achieve high accuracy, impeccable surface finishes, and cost-effective results? Barry Cahoon, Product Solution Specialist Rotating Indexable—Europe at Sandvik Coromant, offers his advice.
Achieving optimal milling results necessitates selecting cutting tools specifically engineered to meet precise machining requirements. This must consider factors such as cutting geometry, material hardness, and machining strategies. Whether the task involves high-precision shoulder milling, high-speed face milling, or complex multi-axis contouring, the tool’s performance directly influences the efficiency and accuracy of the entire process.
What defines
successful milling?
Precision is paramount for any milling operation to be considered successful. Achieving tight dimensional tolerances and geometric accuracy is essential. Surface finish is another critical factor. A smooth, clean finish is not just an aesthetic requirement but often a functional one. In industries such as aerospace, where components such as turbine blades or compressor casings must meet stringent performance standards, even slight deviations in surface quality can lead to major problems. Efficiency also comes into play. Milling processes need to maximise material removal rates while keeping machining time to a minimum, all without compromising quality.
Then there’s the question of tool life. Manufacturers constantly seek ways to extend tool life, reduce tool changes, minimise downtime, and ultimately cut costs. However, tool life is closely linked to chip control and cutting forces. Poor chip evacuation or excessive force can cause rapid tool wear, reducing efficiency and producing suboptimal results.
Tool selection
With so many variables, selecting the right tool is often the biggest challenge. Different operations — such as shoulder, face, or high-feed milling — demand tools with specific geometries and cutting capabilities.
Accuracy and precision are the foundation of every milling process. From creating flat surfaces to machining 90-degree shoulders or complex contours, precision is non-negotiable. Proper tool path control, optimised cutting parameters, and stable machine dynamics are all essential to ensure that dimensional tolerances are met. Thanks to their true 90-degree shoulder capability, tools like CoroMill® MS60 deliver reliable performance, particularly for shoulder milling.
Efficiency and cost-effectiveness are key considerations in any manufacturing environment. Time saved on machining processes translates directly to reduced costs, making it essential to minimise cycle times without sacrificing quality. In this regard, CoroMill® MH20, specifically designed for lightweight milling, offers excellent performance in operations where high-speed material removal is required. Its insert design reduces cutting forces, allowing for faster feed rates while maintaining tool stability, particularly in deep cavity and pocketing applications. This increases machining speed and extends tool life, reducing the need for frequent tool changes and lowering overall production costs.
Chip control and cutting forces are often underestimated but profoundly impact the milling process. Efficient chip evacuation prevents heat buildup and ensures a clean cut, especially in applications involving deep cavities or pockets. Insufficient chip control can cause chips to re-cut, leading to poor surface finish and faster tool wear. Modern tool geometries are designed to optimise chip flow, reducing the risk of clogging and improving overall tool longevity. CoroMill® MF80 offers smooth chip flow and minimal cutting forces, making it highly reliable for roughing and finishing operations. Its ability to handle various materials and machining conditions enhances versatility and productivity across multiple applications.
Finally, precision and reliability are non-negotiable when selecting tools for demanding materials such as ISO M and ISO S. CoroMill® MS20, Sandvik Coromant’s new 90-degree shoulder milling solution, delivers exceptional edge-line security and dimensional accuracy. This ensures high productivity and consistent results, even in challenging aerospace and oil and gas applications.
Successful milling hinges on a deep understanding of the interplay between tool design, material properties and machining parameters. By carefully selecting tools that are purpose-built for the task at hand — whether that’s shoulder milling with high precision or high-speed face milling for rapid material removal —manufacturers can achieve their goals of improved productivity, lower costs and exceptional part quality. The balance between accuracy, efficiency, tool life and chip control ultimately defines a successful milling operation.
Renishaw cost effectively 3D prints expensive metal
Renishaw has enabled Cookson Industrial, a UK-based leader in precious metal additive manufacturing (AM), to reduce the cost of 3D printing platinum-rhodium significantly, one of the world’s most expensive metals. Cookson Industrial can now produce platinum-rhodium components on Renishaw’s RenAM 500S Flex AM system with exceptional material efficiency. High-temperature corrosion-resistant parts for industries like glass fibre manufacturing can now be manufactured viably with AM.
Cookson Industrial, a division of Cooksongold and a subsidiary of HM Precious Metals, brings over 30 years of expertise in the design and production of precious metal alloys. The company set out to redefine platinum rhodium’s use in additive manufacturing. However, with platinum rhodium prices averaging £80,000 per kilo, minimising material waste was crucial to commercially viable production.
Cookson Industrial selected Renishaw’s RenAM 500S Flex, a laser powder bed fusion system designed for research and development applications, to meet this challenge. Renishaw’s AM engineering team worked closely with Cookson Industrial to adapt the system to the specific demands of platinum-rhodium production. The RenAM 500S Flex can achieve powder waste levels as low as 1.5% as standard. However, to align with Cookson Industrial’s requirements, customisations were needed to reduce it to less than 0.5 percent.
“Achieving near-zero wastage of platinum-rhodium powder was a top priority,” said Jason Morgan, Senior Applications Engineer at Renishaw. “We collaborated with Cookson’s engineers to identify and eliminate potential ‘powder traps’ within the system, followed by rapid testing and redesigns to minimise waste while maintaining performance.”
Renishaw’s customisations included modifying internal system components to prevent powder accumulation, such as removing overflow bellows and optimising the rear overflow vent. Additional measures included chamber redesigns and the creation of specialised casings and covers, resulting in a 95% reduction in powder waste. The RenAM 500S Flex now allows Cookson Industrial to retrieve nearly all platinum rhodium powder, amounting to significant cost savings.
“Renishaw’s technology and expertise were crucial to this R&D success, enabling us to make platinum rhodium parts on a commercial scale,” commented Nikesh Patel, Head of Cookson Industrial. “Minimising powder loss not only brings down our production costs but also makes large-scale production feasible, saving millions over the machine’s lifetime.”
“This success paves the way for Cookson Industrial to explore new applications for platinum rhodium AM, including catalysts and aerospace engine nozzles,” Renishaw’s Morgan added, “Our collaboration with Cookson Industrial highlights Renishaw’s commitment to supporting customers in every step of their AM journey, especially when working with novel materials.”
Can the aerospace supply chain keep pace with demand?
The aerospace industry is experiencing unprecedented growth, driven by record demand for commercial jets, defence programmes and space exploration. To seize this opportunity, suppliers must find ways to ramp up output without compromising quality, innovation, or cost. By Will Stirling
The biggest hurdle facing the aerospace industry is how to scale up production. Airlines are investing heavily in new fleets, governments are increasing spending on advanced defence systems, and private companies are pushing the frontiers of space exploration and satellite technology. While this growth is a welcome rebound after years of turbulence, it has exposed bottlenecks in the supply chain, exacerbated by rising operational costs, material shortages and evolving regulatory requirements.
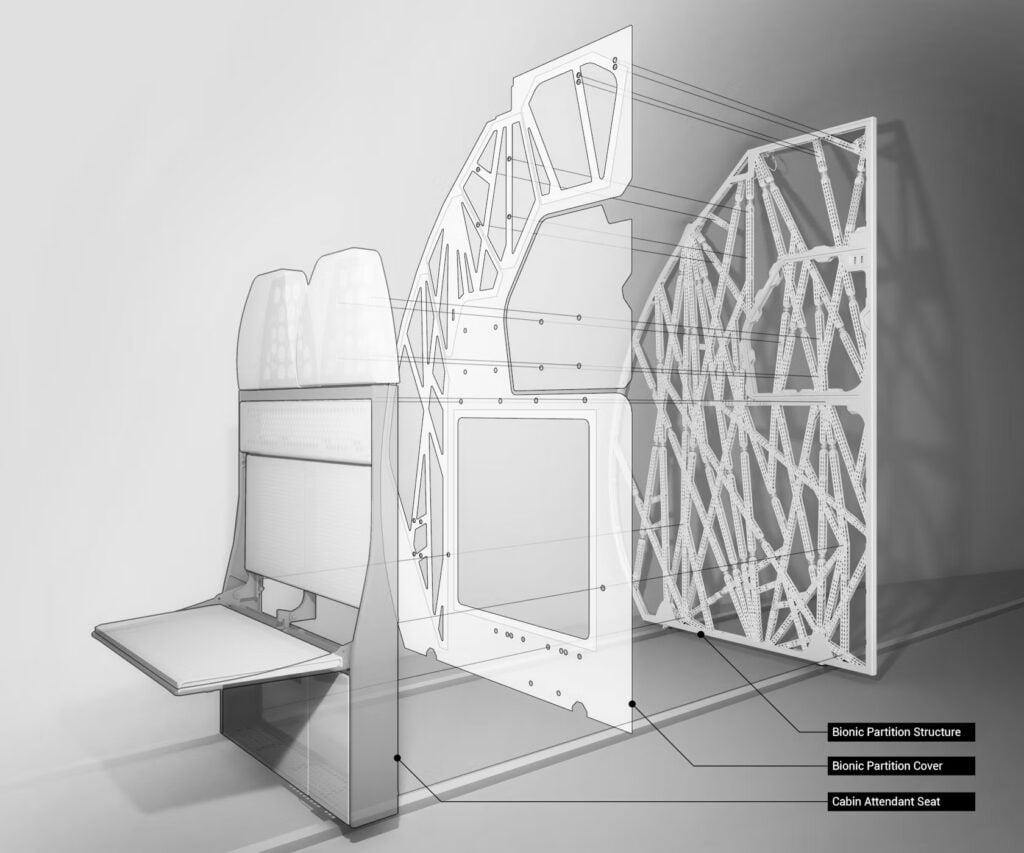
Nowhere is this challenge clearer than in the commercial aircraft backlog, which has ballooned to nearly 16,000 planes – valued at more than £250bn for the UK alone. At current production rates, clearing this backlog could take over a decade. Meanwhile, demand continues to climb as airlines place hundreds of new orders yearly.
Yet, this pressure brings opportunity. “The fact I can’t name another industry with a 10-year-plus backlog worth over US$1.5 trillion globally shows just how massive the growth trend is,” says Balaji Srimoolanathan, Director for Aerospace, Space and the Aerospace Growth Partnership at ADS.
“The primes and top tiers are diversifying their suppliers, sustainability is becoming ever-more critical, and new technologies are accessible and affordable. There is more business to be won by a greater number of suppliers than ever before, adding up to more opportunities, particularly for those with the right tools and technologies in place.”
Srimoolanathan explains that the key to unlocking these opportunities lies in integrating advanced capabilities, such as intelligent manufacturing systems, into today’s production processes. This move has been proven to drive greater efficiency and agility without comprising stringent quality standards.
Digital Innovation in Action
As production ramps up, shortages of critical components like semiconductors, electronics and raw materials like aluminium and titanium continue to cause delays. The pandemic’s ripple effects are still being felt, slowing assembly lines and affecting deliveries. Even seemingly minor components, such as fasteners, are in short supply.
Recognising this, LISI Aerospace partnered with the University of Sheffield Advanced Manufacturing Research Centre (AMRC) to explore how digital tools can drive process improvements. Together, they developed a cutting-edge smart production line at LISI’s Rugby facility.
The pilot line integrates five connected factory machines, each handling a distinct process. Key innovations include sensor data and data analytics to predict component quality, alongside an expanded apprenticeship programme to support new roles like software developers and data analysts.
The result is a more than 100% performance improvement, enabling the Rugby site to hit record turnover and win additional contracts worth over £2m. The project also spurred a dedicated process development department, created a dozen new jobs and paved the way for a further £6.5m investment to implement two more connected production lines by 2027.
An AMRC spokesperson said the project demonstrates how industrial digital technologies can transform operations. The success has ‘set a new benchmark for fastener production processes’ and clearly shows the potential of technology-driven innovation in aerospace.
Process Improvements Within Constraints
While LISI’s collaboration showcases the benefits of innovation, industry-wide progress is often hampered by a reliance on established processes and materials. “The industry is built on aircraft and parts certified to specific production techniques, many of which were designed decades ago,” explains Andrew Mair, Chief Executive of the Midlands Aerospace Alliance (MAA).
While this reliance on legacy methods may limit flexibility in core manufacturing processes, there’s significant scope for improvements in areas that run parallel to assembly. Upgrading to integrated software platforms for production planning, resource management and inventory tracking, for example, is an area where many smaller manufacturers lag, yet can unlock substantial efficiency gains. Similarly, using robotics and automation to move materials or load machines can streamline operations and reduce manual labour and downtime.
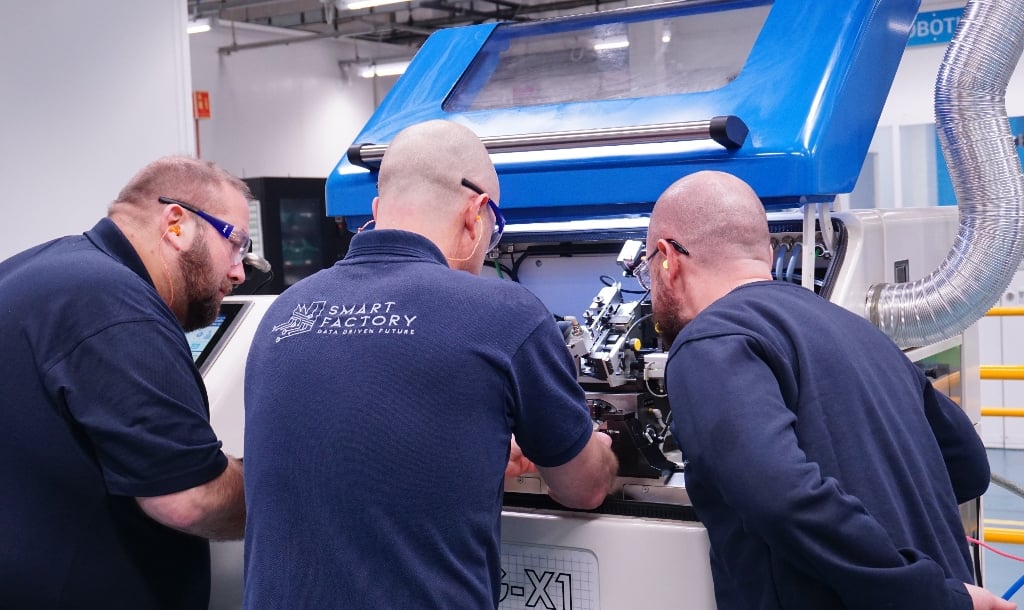
Design innovations also hold promise. Advances in simulation and digital twin technologies allow suppliers to optimise components and assemblies before physical production, compressing design cycles and identifying potential issues earlier.
Generative design, where AI-driven software explores thousands of potential configurations, is helping create lighter, stronger, more cost-efficient components. Combined with additive manufacturing, suppliers can prototype and produce highly complex parts faster and, importantly, with significantly less waste than traditional ‘subtractive’ machining.
For instance, Airbus and Autodesk have used generative design and additive manufacturing to produce the world’s largest 3D-printed cabin component. Inspired by cellular structures and bone growth, the latticed partition to separate the passenger cabin from the galley is structurally as strong as conventional designs but 45% (30kg) lighter. When scaled to the entire cabin, Airbus estimates that the new design approach could save up to 465,000 metric tonnes of CO2 emissions a year.
Government Backing Fuels Further Investment
Recognising the transformative potential of advanced technologies, recent government announcements are geared towards accelerating adoption. One such initiative is the expansion of Made Smarter, an industry-government programme aimed at helping SME manufacturers adopt technology and build digital skills. Since its 2019 launch in the North West, Made Smarter has engaged with 2,500 manufacturers, funded over 330 technology projects, created more than 1,500 jobs and upskilled nearly 2,800 workers.
Its upcoming national rollout to all nine English regions by 2025/26, followed by Scotland, Wales, and Northern Ireland in 2026/27, will extend those benefits to thousands of manufacturers across the UK.
“The programme has proven the value technology and digital skills can bring,” says Donna Edwards, Director of Made Smarter NW, who described the national roll-out as “a huge vote of confidence in the contribution SMEs make to UK manufacturing.”
Additionally, the government’s announcement of £975m to extend the Aerospace Technology Institute (ATI) programme to 2030 was welcomed – although many favoured a longer-term commitment. With matching industry contributions, the funding will exceed £2bn, providing critical support for ultra-efficient and zero-carbon technologies.
“This support for R&D is crucial at a time the sector is ramping up rates to meet today’s demand while delivering ambitious technology programmes to bring next-generation aircraft technologies to reality,” says Gary Elliott, CEO of ATI.
Plotting a Sustainable Flight Path
The UK is making significant strides in sustainable aviation. The latest development saw a new Sustainable Aviation Fuel (SAF) mandate come into force on New Year’s Day. The mandate requires that 2% of UK jet fuel demand be met by SAF, rising to 10% by 2030 and 22% by 2040—delivering up to 6.3 megatons of carbon savings annually.
The mandate will be bolstered by the introduction of a revenue certainty mechanism to de-risk investments in new SAF plants and provide the confidence needed to scale domestic production.
The potential of hydrogen-powered aviation is also gaining momentum, with Russ Dunn, GKN Aerospace CTO, recently named as the new chair of the Hydrogen in Aviation Alliance. The HIA’s first major report, published in 2024, outlined a clear roadmap for industry and government to drive adoption. Yet, realising this vision requires more robust support for R&D, particularly within the manufacturing supply chain.
Andrew Mair explains that nearly all the R&D support currently goes to large corporations or start-ups, leaving the existing supply chain underserved. “We need more regionalised support, particularly for clusters like the Midlands Aerospace Alliance, to ensure small companies get the backing they need.”
Srimoolanathan of ADS underscores that aerospace is uniquely positioned to deliver immediate and long-term benefits for the UK economy. “The backlog presents an opportunity for short-term growth, job creation and technological advancement,” he says.
“But this hinges on balancing the immediate demands of today with strategic investments in areas like zero-emission technologies. With sustained support, the UK can maintain its position as a global aerospace leader while delivering tangible economic and environmental benefits.”
On a roll
As a roll tooling and equipment design and manufacturing specialist, Bowers & Jones Ltd is increasing its in-house machining capacity and capabilities by investing in a new DN Solutions large-capacity, ram-type vertical turning lathe. The VTR 1216F machine from Mills CNC was acquired to fulfil a new steel mill order from a customer in the US that requires batches of high-precision straightening rings.
Additionally, owing to the machine’s size, power, precision and versatility, the new investment will also help generate new business opportunities and growth in the US and other markets, consolidate its supply chain position with existing steel mill customers, and improve its UK precision subcontract machining operations.
The new VTR 1216F machine is a large-capacity wide-column ram-type vertical turning lathe. It has been installed at the company’s 15,000sq/ft manufacturing facility in Bilston, near Wolverhampton, joining three previously acquired Mills machines supplied over the last four years. The existing machines are a Doosan Puma 5100B lathe installed in 2020, a Doosan DNM 750 II VMC with a 4th-axis unit installed in 2021, and a DN Solutions’ GT 3100L box guideway lathe delivered in 2023.
Commenting on the relationship, Jane Sommerville, Bowers & Jones’ Managing Director, says: “We have built strong relationships with Mills CNC, and the breadth of the machine tool ranges they supply combined with the company’s first-class after-sales service and support means that Mills is invariably our first port of call.”
Under new ownership since 2020, Bowers & Jones is committed to continuous improvement. It regularly monitors and benchmarks the performance of its manufacturing operations to identify and address current and future production inefficiencies and bottlenecks. The rollout of the company’s improvement programme, initiated four years ago when the change of ownership occurred, has been instrumental in streamlining and strengthening its in-house machining capacity and capabilities to deliver sustainable growth.
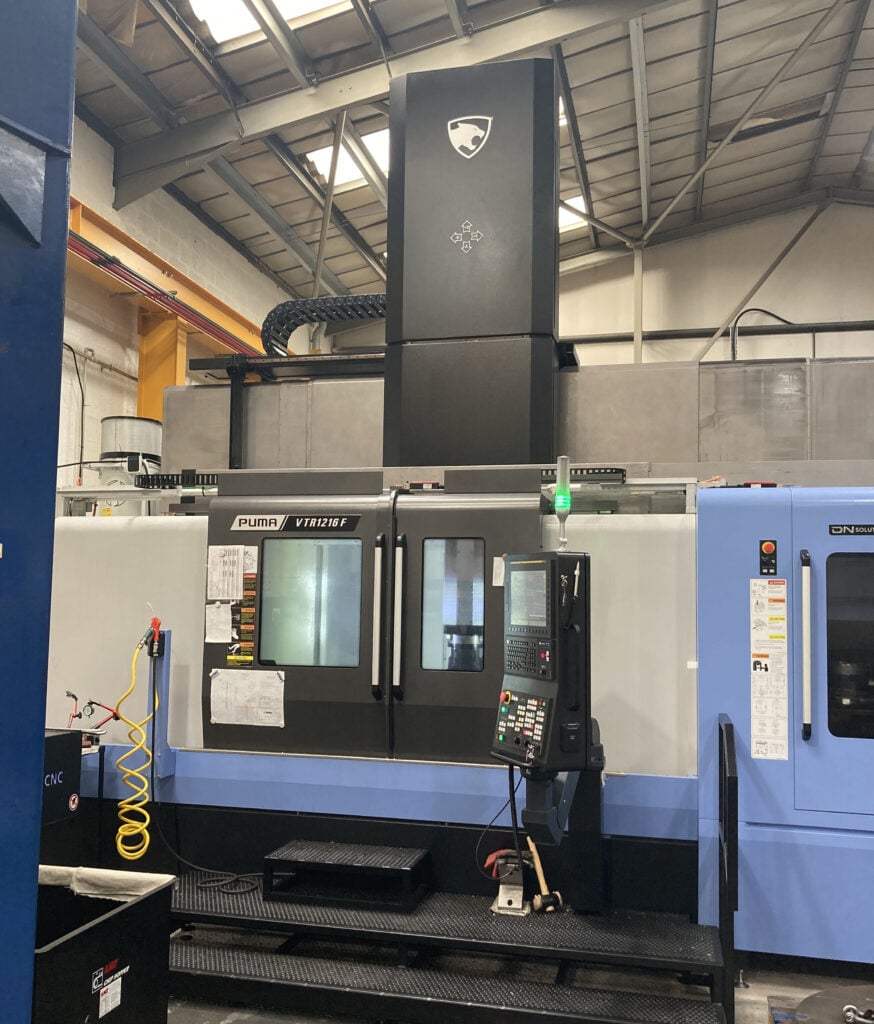
Bowers & Jones supplies its roll tooling and equipment to steel and copper mills in the UK and worldwide. The company has recently made inroads into the US steel market. Through direct sales approaches aided by a third-party agent, it is expanding its presence in North America. Indeed, the company’s new VTR 1216F investment was primarily made to meet the needs of a new US customer whose rail ‘I’ beam sections, medium bar sections and angled bar sections are used extensively in the US rail and construction sectors.
Jane Sommerville continues: “We needed a new large-capacity vertical lathe to machine large-diameter straightening rings for the customer. We won the business in Autumn 2023 and ordered the new VTR 1216F from Mills last October, expecting the machine to be delivered and installed in Spring 2024—just a few weeks before production of the rings was due to start.”
However, in early 2024, the safety and security of transporting freight through the Suez Canal were unexpectedly delayed due to geopolitical issues. “We had to revert to Plan B quickly”, remembers Jane Sommerville. “The customer’s deadlines didn’t slip, so we had to use our existing machines to manufacture the first batch of rings – basically ‘holding the fort’ until the VTR 1216F eventually arrived.”
The machine was delivered in early May 2024. To save time and minimise further disruption, it was delivered directly to Bowers & Jones’ facility from Felixstowe. Mills CNC performed its PDI, machine build, and installation on-site. Operator training followed soon after the machine was commissioned, and the VTR 1216F was cutting metal at the beginning of June.
Commenting on the machine, Jane adds: “We had been looking at investing in a vertical turning lathe for some time – partly to take pressure off an older, large-capacity Berry & Binns horizontal lathe that we had acquired some years earlier, and partly to help spearhead new business growth in the US market. We approached Mills and two other suppliers to discuss our requirements and, looking at the proposed investment package as a whole, decided to place the order with Mills.”
The FANUC controlled 50” chuck VTR 1216F machine boasts a maximum turning diameter of 1.6m and a maximum turning height of 950mm. It is equipped with a powerful 45kW 400rpm high-torque spindle, a servo-driven 12 tool ATC and an innovative quad tool holder with fast indexing that enables the use of four tools directly via the ram. The VTR 1216F delivers impressive processing speeds, improved machining flexibility, high accuracies and repeatability.
Like all roll tool types, straightening rings are performance-critical components used in metal forming processes to enable the steel to pass through one or more pairs of rolls located on stands to reduce the material’s thickness, making it uniform and consistent. Where required, straightening rings give the ‘rolled’ material additional mechanical and application-specific properties needed for the ultimate end-user.
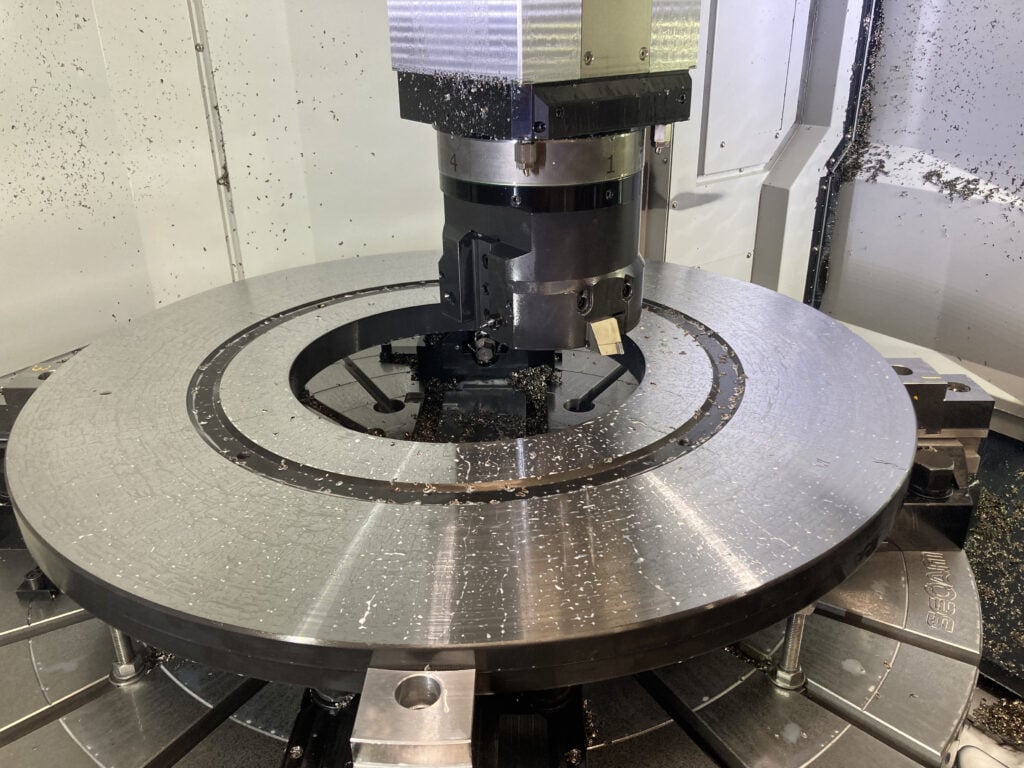
The rings process the material into bar stock, rails and structural steel beams, angle and channel stock. These are used across many industries and sectors, such as construction, rail, energy, oil and gas and automotive. The harsh and demanding environments subject rolls to high wear, thermal stress and mechanical fatigue. Consequently, they need to be monitored regularly to maintain their dimensional and profile quality and consistency, with a need for replacements over time. The straightening rings machined on the VTR 1216F are made from D2, an alloy tool steel that is difficult to machine. They are machined from solid round bars in relatively small batches, with part cycle times being long and turning operations performed at low speeds.
Roughing operations were undertaken on the company’s Berry & Binns lathe before the rings were sent for heat treatment. When the rings return, they are finish machined on the VTR 1216F to tight geometrical and dimensional tolerances with super-fine surface finishes. The heat treatment process gives the D2 rings their compressive strength, high wear resistance, toughness, and shock resistance properties—all crucially important for delivering high performance and long life in a demanding steel mill environment.
Established in 1954, the company’s knowledge of metal-forming processes is second to none. The bottom line is that Bowers & Jones’ roll tooling solutions last longer and perform better than those of its competitors. Explains Jane Sommerville: “Our high-quality designed and machined rolls may cost a little more, but they are an investment and help customers save time and money by reducing re-profiling and replacement costs, limiting potential downtime and ensuring that customers’ mills keep rolling.”
Bowers & Jones’ current five-year plan is ending, and the new five-year plan will be rolled out imminently. The company plans to upgrade its machine shop and further capitalise on new business opportunities in the US. The imminent change of administration in the United States, with its ‘Make America Great Again’ mantra, may well see the US steel market become stronger and more buoyant.
Ultrasonic deburring on manufacturers wavelength
Intercable Tools GmbH has been firmly rooted in Bruneck in the Italian province of South Tyrol since it was founded in 1972. Since then, the family-owned company has been one of the leading manufacturers of connection technology and tools for professionals and the industry. Since May 2024, Intercable Tools has been using ultrasonic deburring technology from Swabian company ultraTEC Innovation GmbH to remove burrs from hydraulic units in a contact-free manner automatically.
With Intercable Tec, a developer and manufacturer of automotive components, Intercable Tools forms a management-led family business with branches and over 600 employees worldwide. For some time, Intercable Tools had been looking for an automated solution to replace manually deburring hydraulic units of battery-powered hydraulic cutting tools made of aluminium and steel. Such hydraulic units are used in battery-powered perforators, which the company manufactures and distributes. These sheet metal punches are suitable for punching round, square and rectangular holes up to 3mm thick. The complex task for the ultraTEC was to remove all detachable burrs from the inside and outside of the components.
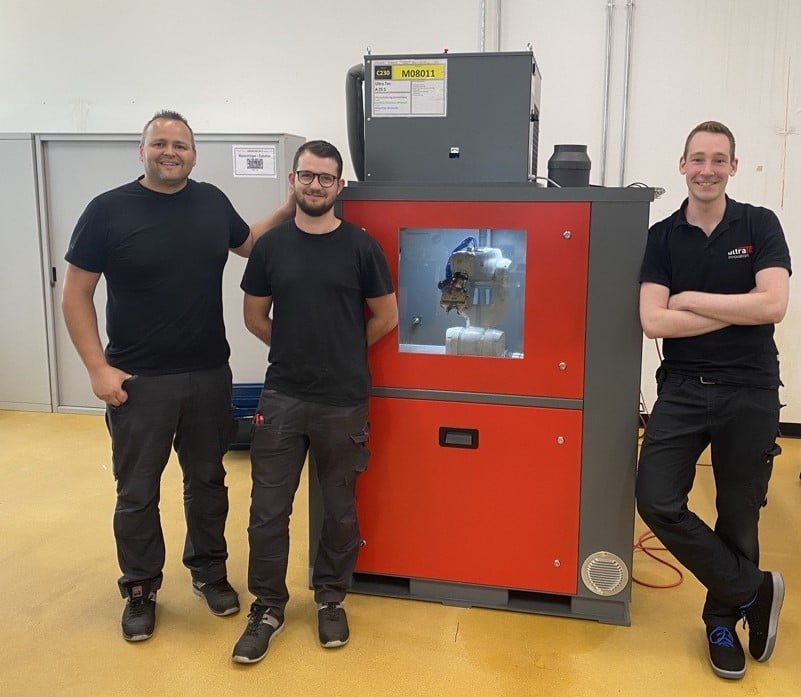
“We were looking for an innovative alternative to manual deburring. It’s also important for us to produce our variants without set-up time,” said Heinz Pramstaller, Team Leader of Metal Production at Intercable Tools. “The deburring process should also be optimally integrated into the process, and the components should be cleaned using the same product carrier as the parts cleaning system.”
The new ultraTEC A25 S system automates the manual process. The companies first contacted each other at the DeburringEXPO trade fair in Karlsruhe, Germany, in October 2023. Heinz Pramstaller brought the component to be deburred, so an initial deburring test was carried out on the trade show machine. The component was manually guided to the sonotrode, with a positive result. The advantages of this method over the previous manual deburring process quickly became apparent to Intercable Tools. Ultrasonic deburring means that the results remain the same, there is no damage to the drill holes, and uncontrolled material removal is generally avoided. It also guarantees that no holes are forgotten, which can happen with manual deburring. The ultrasonic deburring process has the advantage of cross bores being deburred and rinsed out simultaneously. The initial tests for Intercable Tools were, therefore, very promising.
Non-contact ultrasonic deburring with the patented sonotrode forms the foundation of technology. Components to be deburred are guided in a water basin along the tip of an ultrasonic sonotrode, whose generated vibrations cause the burrs and chamfers to break off in an automated and energy-efficient manner. Stimulated by a generator, the sonotrode oscillates back and forth 20,000 times per second over 0.1mm.
These generated vibrations move burrs and chamfers back and forth until they are broken off with sharp edges in a process-safe manner. Similarly, ultrasonic deburring does not apply temperature to sensitive components, which can lead to deformation and discolouration. In addition to deburring common metals, ultraTEC systems can be used with components made from various titanium and nickel alloys and fibre-reinforced plastics.
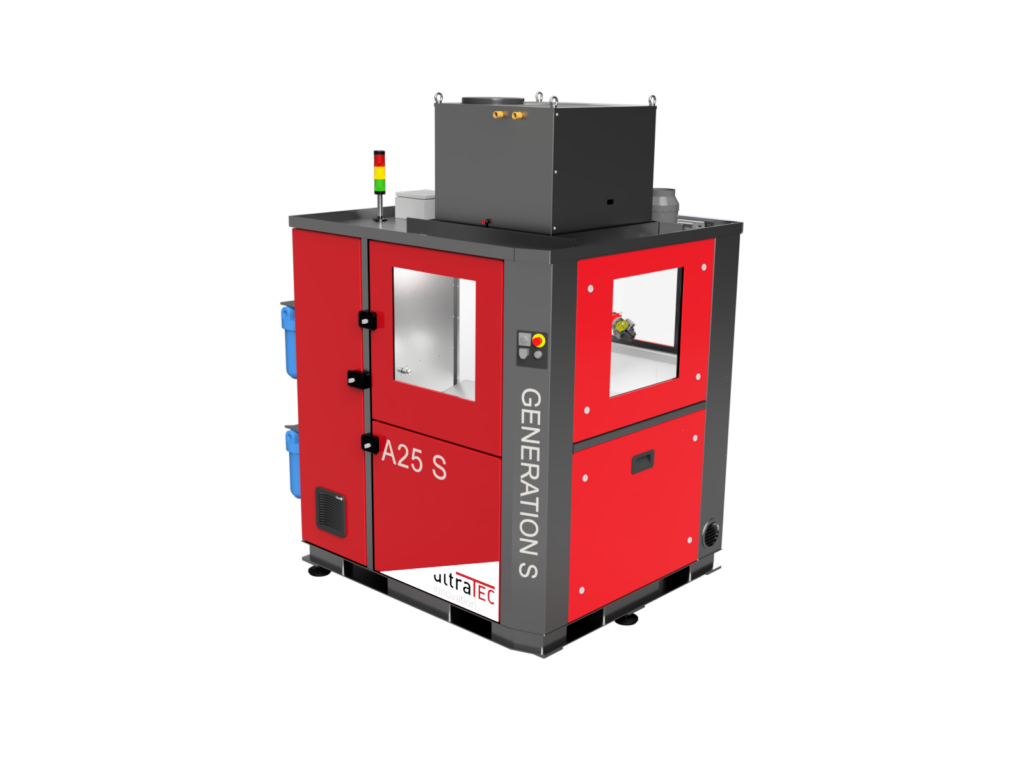
From the deburring tests in Laupheim to commissioning in South Tyrol, numerous automated deburring tests were carried out with components from Intercable Tools at ultraTEC’s premises in Laupheim. Detailed documentation was provided for each test so that the specialists from Intercable Tools could assess each one accordingly. Regular coordination meetings and a visit from South Tyroleans in Laupheim led to them placing an order for the A25 S ultrasonic deburring system in late March 2024. Two months later, the A25 S was showcased for the first time as an innovation at the GrindingHub trade fair in Stuttgart, Germany, before preliminary acceptance was already carried out at ultraTEC in mid-June 2024. Four weeks later, the A25 S was operated at Intercable Tools in Bruneck in South Tyrol.
“We’re delighted that we could implement the project quickly and that Intercable Tools chose ultraTEC to automate the deburring process,” says Thomas Benzing, Sales Manager at ultraTEC Innovation GmbH. “Maintaining a sense of partnership and trust when working with our customers is very important.”
It’s the attitude that counts
ARNO believes that machining is now something like Formula 1 racing: every little screw is tuned to increase performance. Thinking outside the box is essential, especially when considering cutting tools and turning. It would be helpful if users could always use the right combination of tools, inserts, and coolant supply.
In Formula 1, everything is constantly scrutinised to glean maximum performance. Yet only the driver and the manufacturer who have mastered the overall package can reap the world championship crown. Despite all the optimisations and specifications, cutting tools for turning have yet to reach the end of their potential. Responsible tool manufacturers think about selling as many cutting tools as possible and include the tool holders and cooling supply into the equation. On the other hand, users should be open to tips, let consulting manufacturers approach them, and allow them to enter the production process. The potential that can be achieved in this way can provide a decisive leading edge.
Be open to third-party expert tips
For example, ARNO Werkzeuge has long been involved in the continued development of tool holders and coolant supply. Thanks to its customer proximity, the family-run company has a wealth of expertise from numerous applications and a wide range of holders with and without coolant supply. Users can rely on the best overall packages for small and large batches, as well as Swiss and fixed headstock lathes. “Here, too, we are not interested in maximising sales figures for high-margin products. We aim to find the best solution for our customers,” assures Sales Manager Dieter Wollensack from ARNO Werkzeuge.
As an experienced technical advisor, he focuses on long-term and intensive customer relationships. He detests the promise of ‘double the service at half the price’ and pie in the sky. “I sometimes say to my customers: ‘No, that’s not possible’ or ‘We won’t do that’ and risk being turned down. I’ve always been successful with this approach – and ultimately, so have my customers.”
Advice or not, process optimisation products must be convincing in practice. For this reason, the overall package consisting of a cutting insert or indexable insert with a matching tool holder and high-performance cooling must always deliver the best customer performance. This is exactly what users should attach importance to their tool partners to understand the processes and have the right overall package for every production situation. For example, universal packages for small batches, high-tech solutions for large batches, and special products for difficult-to-machine materials. Exorbitant promises never help.
Innovative when it comes to ‘cost per part’
When tool manufacturers adopt this mindset, new products and solutions result. One example is the clamping holders with through-tool cooling for inserts that ARNO Werkzeuge developed in 2022. They are produced using a hybrid manufacturing process that combines additive technology with conventional CNC milling, achieving better surface quality.
But why? Coolant flows directly where it’s needed. Three precisely aligned channels guide the coolant to the cutting edge from above and underneath without obstructing chip evacuation. The special geometry of the cooling channel creates a nozzle effect that greatly improves cooling compared to conventional channels. The outlet openings are always perfect—they need no adjustment. And since they are much closer to the cutting zone, the coolant significantly reduces the temperature.
Experienced users will recognise the benefits immediately: greater process reliability, less vibration, better surface quality and a much longer tool life. Users have sent reports about tool life that is three times longer. Of course, this is not at all suitable for small batches – but when it comes to large batch orders, it’s just the right ace in the calculation where everything has to do with the cost per part.
Hybrid holder: productive from additive
The secret isn’t rocket science, but you must figure it out first. The shanks of the hybrid holders from ARNO Werkzeuge are produced using conventional CNC milling. On the other hand, the complex head part of the holder is attached directly to the shank using a 3D printing process. “This gives us new design freedom and outstanding stability,” says Werner Meditz, Head of Technology at ARNO Werkzeuge.
The geometric design of the cooling ducts can be precisely optimised so that coolant is guided through the holder to the cutting tool at maximum efficiency and reaches the cutting edge directly from above and underneath. This cools the tool flanks in a way that was previously unthinkable. At the same time, the number of attachments required at the top of the head is reduced to the absolute minimum. The chip breaks as needed and is optimally evacuated – regardless of the cutting depth. “We get a lot more coolant to where it needs to go,” Meditz assures us. The innovative hybrid holder is exactly what clever users want – and this all comes from a tool partner thinking out of the box.
Not only high-tech but also ‘basic work.’
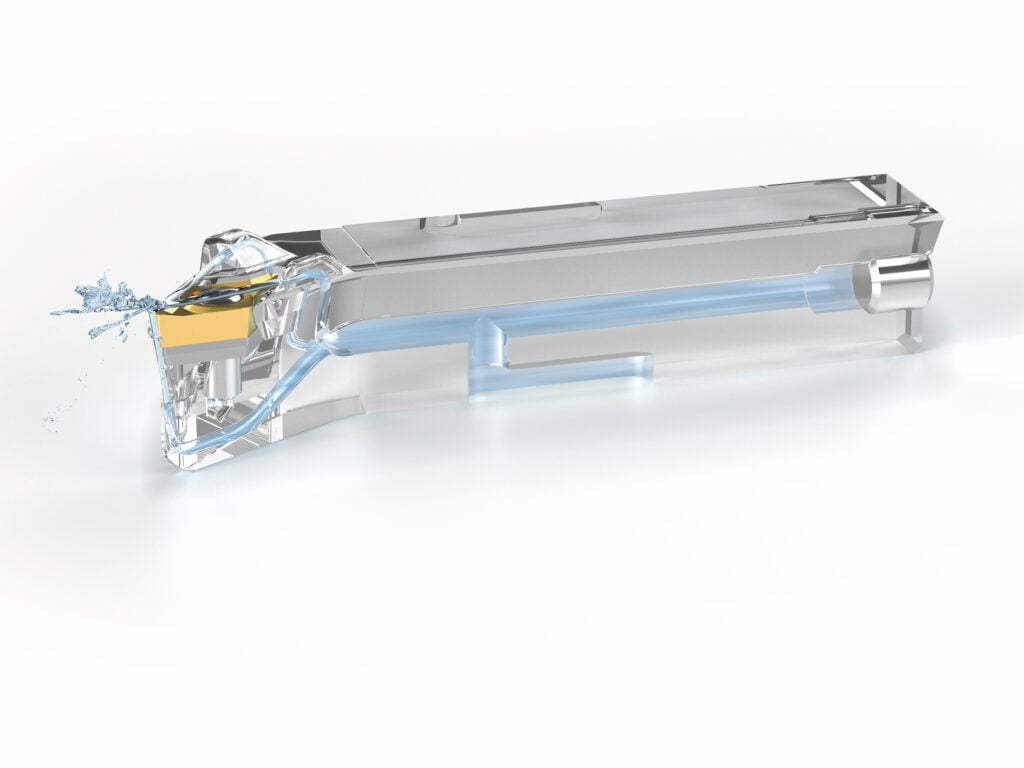
But even when it’s not high-end, machine shops welcome innovative turning tool manufacturers with well-thought-out products. Meeting someone who can also offer the right holders and complete systems for small batches with frequent workpiece changes is refreshing. At ARNO Werkzeuge, you will find a wide range of turning holders for external machining, where the length is easily adjustable using a scale. “The ARNO special design is extremely simple and practical when it comes to adjusting the length and coolant access,” confirms Meditz.
The holder and through-tool cooling are easy to install and ensure repeatable process reliability. Their nickel-plated, high-tensile, and precisely finished nature promises top quality and long tool life. The efficient cooling system, which feeds coolant directly to the cutting edge through three channels, not only ensures long tool life but also allows higher cutting speeds with optimised chip control. The machining time savings make the cost calculation look good.
Variety of boring bars for internal machining
Finally, we come to internal machining. Turning tool manufacturers have already given this much thought. First and foremost, the designers at ARNO Werkzeuge have also considered the customer’s situation and developed suitable boring bars for a wide range of applications. The range includes boring bars of steel and solid carbide, each with two possible coolant hole exits. Depending on the turning process, users can choose between a coolant channel from above (IKO) for through holes and a coolant channel from underneath (IKU) for blind holes. Accordingly, chips are guided forward away from the cutting edge (IKO) or behind the cutting edge and flushed out (IKU). This reduces wear.
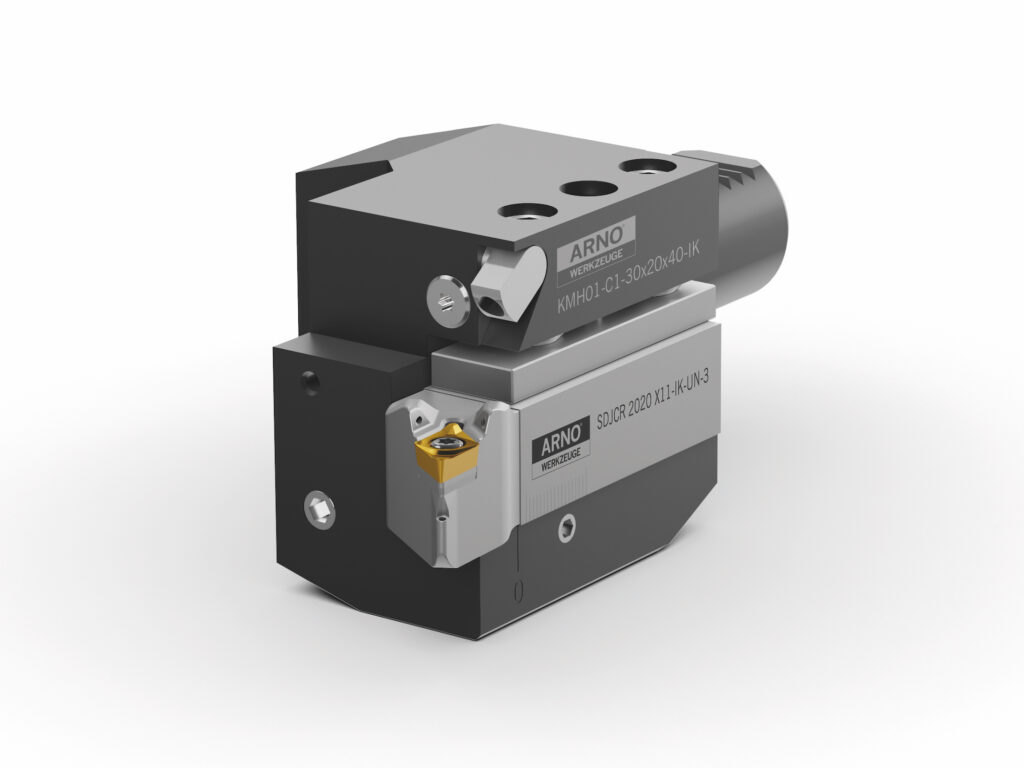
Boring bars come in right or left-hand versions with different shank diameters, a wide variety of clamping holders, and many approach angles. This variety alone shows that the manufacturer thinks from a user’s point of view. Combined with suitable mini indexable inserts from ARNO Werkzeuge, components from Dmin 4.8mm can be machined effortlessly, regardless of diameter and material. This is only the standard range, not customised products. This already promises long tool life because all ARNO boring bars are nickel-plated, high tensile and precisely machined, which certainly boosts confidence.
Users looking for suitable, long-life productivity-enhancing tools for all their turning operations and processes should be glad that some manufacturers have adapted their thinking to include their customers applications.
Drill sharpener pays for itself in five months
Archway Engineering has invested in a drill sharpener from 1st Machine Tool Accessories, and the savings have been incredible. Danielle Toner, Production Manager at Archway, a site drilling equipment manufacturer, is overjoyed with the benefits the company has enjoyed from the new Darex XT-3000.
A US-made Darex XT-3000 for repeatedly regrinding carbide and HSS drill bits to ‘as-new’ condition was delivered by sole UK sales agent 1st MTA to Archway Engineering’s Elland factory in July 2023. By November 2023, it had already paid for itself, as Mrs Toner had not purchased a single new carbide drill in all that time to replace broken or damaged bits. According to the work going through the factory, the saving was between £700 and £1,500 per month.
Mrs Toner said: “We did not previously send drills out for resharpening, so worn bits were discarded. The cost was significant, especially for solid carbide drills. One component we regularly machine involves using a 160mm long, single-flute carbide drill, and we previously needed four of them to complete the part. If we ran out of bits, we couldn’t finish the job until the next drill delivery, which delayed assembly of our products.”
“Now we simply resharpen a bit four times, and we are certain that the component will be finished on time. New carbide drills cost around £165 each, so the saving is considerable and contributes to lowering the cost of production.”
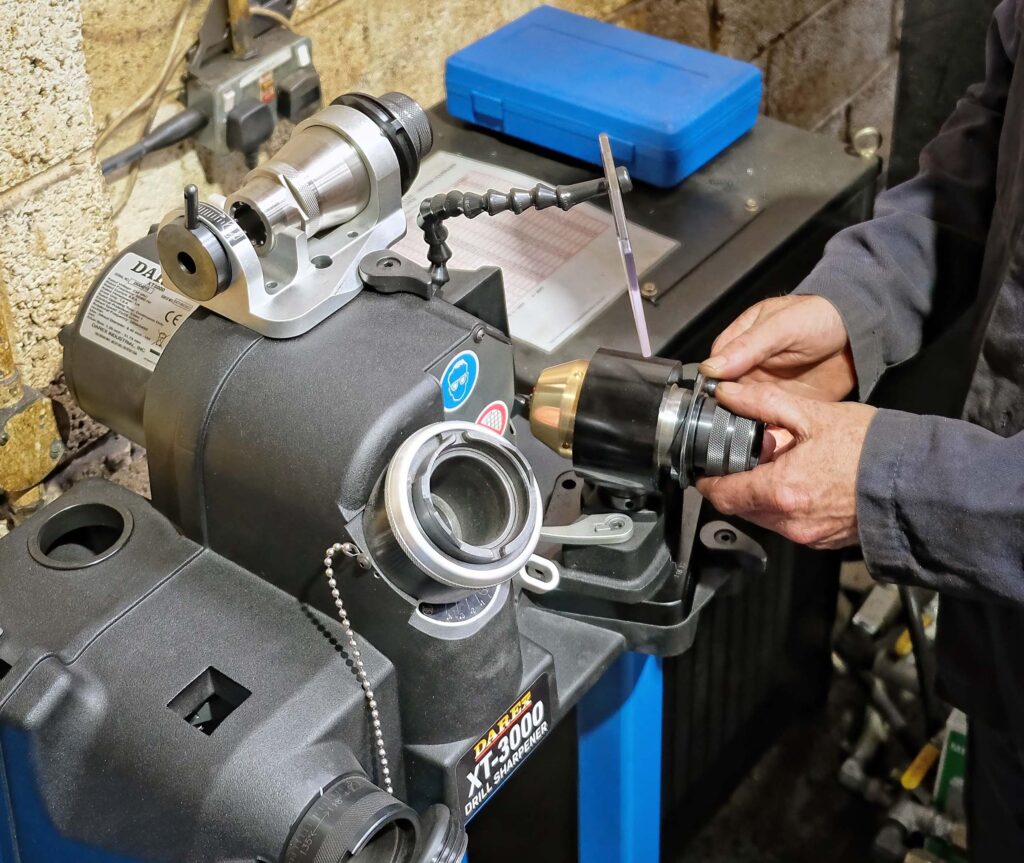
This example is by no means exceptional. Another job requires three new carbide drills to make two parts. In a different process, an HSS taper-shank twist drill is put through 30mm thick EN19 high-tensile steel. A TC shoe made from an S355 hot-finish stainless steel tube is drilled in up to 16 places using a split-point, single-flute carbide drill that has to be repeatedly resharpened before the component comes off completely machined.
Mrs Toner explained that some bits could be resharpened a dozen times or more, depending on their length, while maintaining top quality. It takes about one minute to sharpen the point, or a little longer if necessary to grind past a chip on a cutting edge. It happens quite often due to the toughness of the materials being machined and also because of a frequent need to drill cross holes at various angles into the wall of tubular components. This tends to damage the cutting edges of a drill as it breaks through.
HSS jobber drills from the assembly department are also regularly sharpened, which Mrs Toner describes as ‘a massive saving’. It requires the 220-grit diamond wheel used for sharpening carbide drills to be exchanged for a 180-grit CBN grinding wheel. The process takes about five minutes, so batches of around 20 HSS bits are set aside and resharpened simultaneously.
1st MTA demonstrated the XT-3000 in the Elland factory before Archway Engineering purchased it with an attachment to process bits up to 30mm in diameter. Left and right-hand drills can be processed, and attachments are available for sharpening step drills, countersink and spot drills, and others with a 90-degree point. Standard sizes of carbide drills used regularly by the site drilling manufacturer are 8, 10, 12 and 14mm in diameter and up to 6XD in length. However, bits from 3 to 21mm in diameter can be accommodated in normal use.
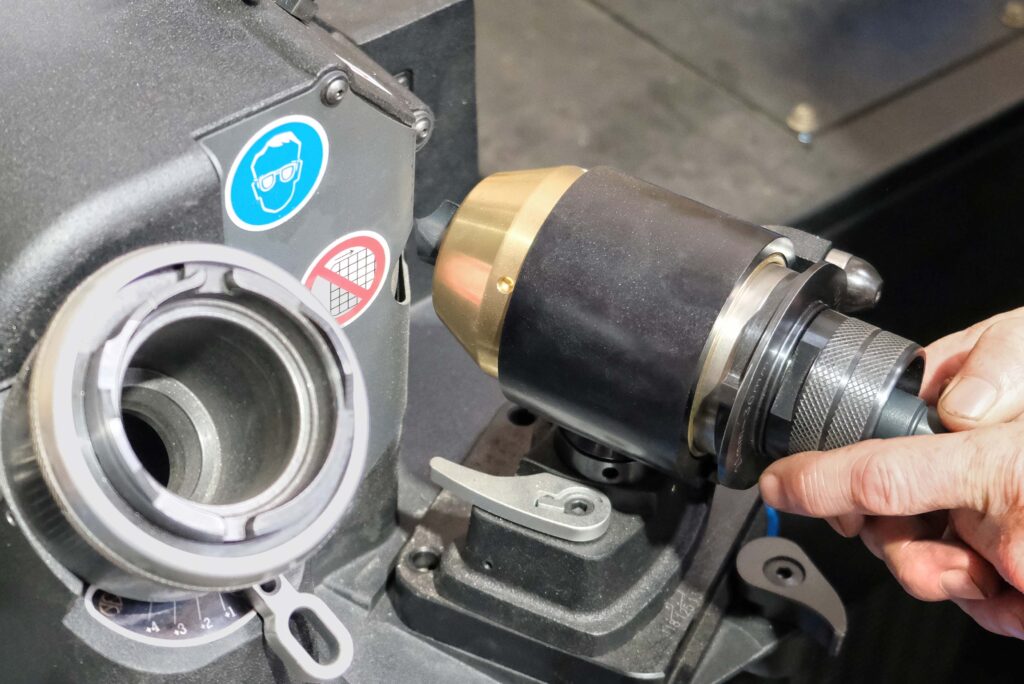
It resharpens bits in a three-step process. A drill is placed in a finger chuck, and the protrusion length is set at an alignment station. Carbide fingers enter the flute to fix the rotational orientation, and the drill is tightened in that position by rotating the chuck clockwise. The grinding motor is then started, and at a second station, the drill is sharpened on both sides while clamped in the same chuck. In an optional last operation, the chuck holding the sharpened drill is presented to a third station for point splitting to shorten the chisel line and lessen the force required for drilling components.
In conclusion, Mrs Toner observed: “The savings that the Darex XT-3000 brings make it an obvious investment once you realise the benefits. We wish we had done it much earlier. The sharpener paid for itself in less than six months, after which the ongoing monthly savings continue to add to the profit margin on all jobs that require drilling operations, which is most of them.”
“The sales arguments that 1st MTA make are difficult to ignore. We also purchase Chick workholding products from them, which have doubled productivity on one of our machining centres, and the supplier has also provided us with a new chuck for one of our lathes.”
The latest manufacturing technology on show
Southern Manufacturing & Electronics will open from 4th to 6th February 2025 at the Farnborough International Exhibition & Conference Centre. It is a venue where firms from across the engineering spectrum gather to show 9,000+ visitors their latest products and services. The new exhibition owner, Easyfairs, says that a high level of interest in the event has ensured it will be a sell-out.
As an indication of what to expect regarding machine tools, Ajax will promote a range of equipment, including manual mills and lathes, surface, cylindrical, and bench grinding machines and multi-axis CNC lathes. Colchester will be there to promote the Storm VL-550 VMC and the Tornado SL25 MSY CNC lathe, both designed to deliver productivity and accuracy. It will also show a permanent laser marker and a selection of Pratt Burnerd manual and power chucks.
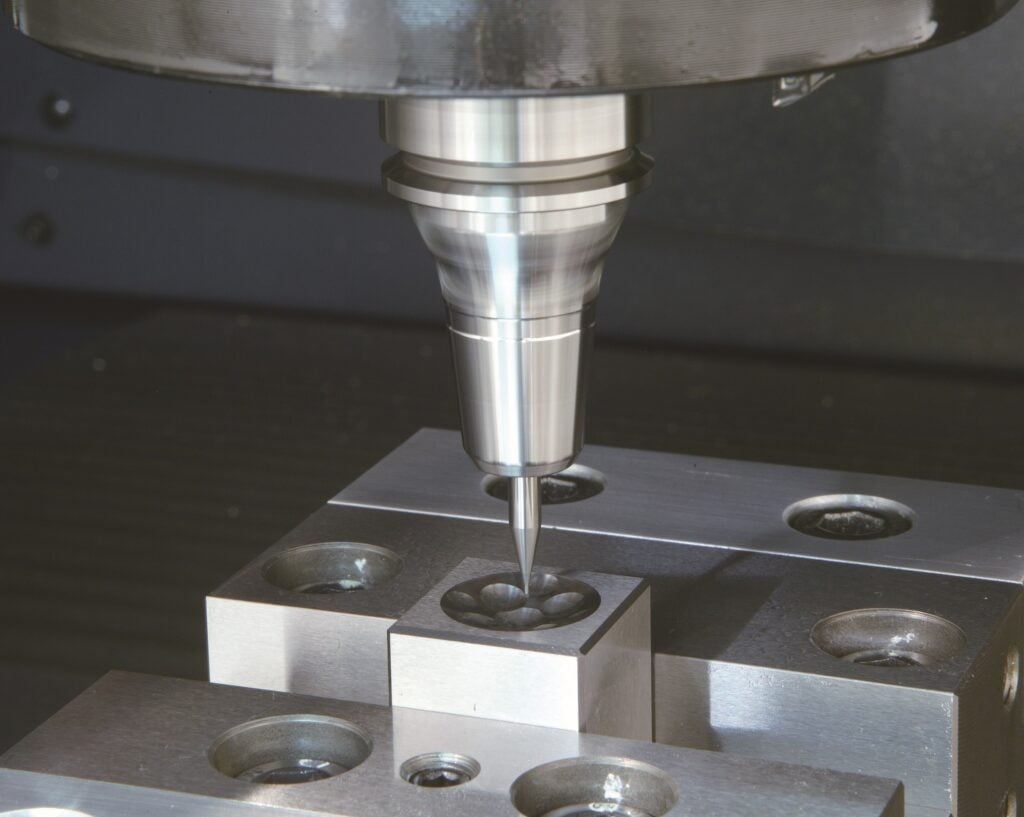
A compact UMC-500 5-axis VMC equipped with a robotic pallet loader on the HAAS stand will highlight the efficiency and flexibility of automation for high-mix, low-volume machining. The Super Mini Mill will also be cutting metal. Making machining more efficient and precise when producing one-offs and small batches will be Hurco’s theme. On display will be two of its most popular machines, the VM10i VMC cutting steel to demonstrate its power in a small footprint, and the TM8Mi 3-axis CNC VDI 30 turret having 12 driven tool stations. The latest Hurco Max 5 control developments will be highlighted.
The MX-520 PC4 five-axis VMC with integrated 4-pallet changer will make its debut on the Matsuura stand. It will be machining components throughout the show to demonstrate the automated production cell’s suitability for reliable unmanned running. Mills CNC, the exclusive distributor in the UK and Ireland of DN Solutions’ and Zayer machine tools, will exhibit the large-bore, multi-tasking, mill-turn centre, the Puma SMX 2100SB.
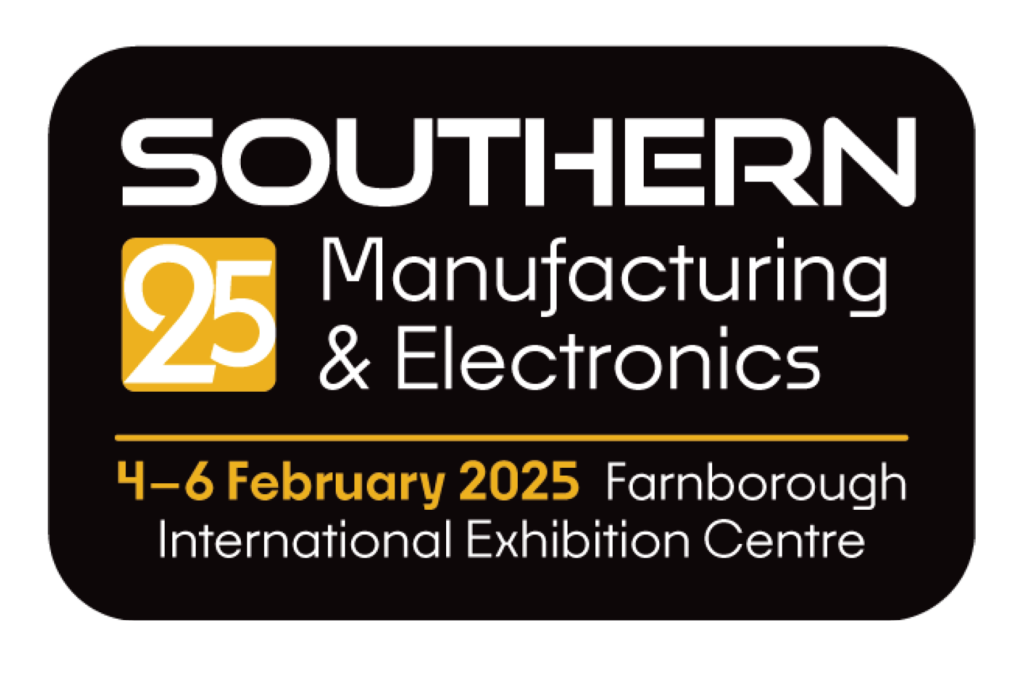
Hyundai-Wia, Hartford, Soraluce, Takisawa, Hankook, and Gurutzpe are some of the machine tool manufacturers represented in the UK by Ward CNC, whose stand will reflect the variety and affordability of the machines. Unison will present its British-built electric tube and pipe bending machines, as well as a recently introduced dual-stack, hybrid tube bender range that combines electric control with advanced hydraulic operation. Through Nukon Lasers UK, the company also offers fibre laser cutting machines.
The rigidity, thermal stability and machining capability of machine tools supplied by XYZ will be presented. This will include the 65 LTY-S twin-spindle turning centre. On the Yamazaki Mazak stand, there will be a live demonstration of the new HQR-200/3 NEO turning centre. The twin-spindle, triple-turret configuration is ideal for producing medium to large batches.
Car parking at the Farnborough site is free and it is easily accessible by road. For those travelling by train, a dedicated, complimentary bus service runs between Farnborough’s Main and North Camp railway stations and the show. Admission is also free of charge. Register today at: https://register.visitcloud.com/survey/00mf6xsmh61zw?actioncode=1052
It’s all about collaboration
On the 27th and 28th of November, Hexagon Manufacturing Intelligence invited MTD magazine to the official opening of its new Experience Centre in Holland. Located at the Brainport Industries Campus in the Northwest of Eindhoven, the two-day event was an opportunity to tour the new campus and participate in insightful presentations that demonstrated how Hexagon is driving innovation and, as a result, developing successful industrial partnerships.
Eindhoven is responsible for the Philishave, the automatic gearbox, the cassette tape and the compact disc. To foster this culture of innovation for future generations, the Dutch government funded the Brainport Industries Campus, which broke ground in 2017. At around 100,000sq/m, the innovation centre is virtually fully subscribed, and that is why construction of a 225,000sq/m phase two on the 17-hectare site will commence this year. With dozens of high-tech businesses collaborating at the campus, Hexagon is alongside cutting-edge companies with brands like Siemens and Meta (Facebook), just a few located at the facility.
MTD magazine attended and the itinerary for the innovation extravaganza promised an exciting lineup. The event started with a welcome from Jan Klingen, Vice President EMEA North, and Eric Veurink, Brainport Industries Campus Director, and a facility tour. As expected with a Hexagon LIVE event, the breadth and depth of technology and insights were so expansive that delegates could choose the most relevant content for their business.
Exemplifying this was one of the first panel discussions on the ‘Future of Mobility in Aerospace and Automotive’, hosted by Hexagon Senior Director for Industry Solutions, Johannes Mann, who was joined by speakers Rob van Loon, Additive Manufacturing Manager at KMWE and Thom Grobben, the Vice President of the Technology Hub at KLM Royal Dutch Airlines. The discussion flowed through the challenges of accelerating innovation and agility in the automotive sector to deliver the next generation of smart, connected vehicles. This conversation then moved on to the aerospace industry’s challenges in redefining aircraft architecture and propulsion systems to become more sustainable.
Other prominent seminars discussed ‘The challenges in production and collaboration’, ‘Extending asset lifecycles and improving productivity with HxGN EAM’, ‘Surfing the future now’ and ‘Innovation beyond silos: Transforming Manufacturing through connectivity, collaboration, and Cloud/AI’. There was a lot more on show, with panel discussions, presentations, workshops and roundtable debates encompassing every industry sector.
Nowhere was this more prominent than in Morgan Maia’s presentation, the Partnership Manager at Oracle Red Bull Racing. Hexagon has partnered with the F1 team since its inception. Flying in from the F1 Teams’ weekend win in Las Vegas, Morgan discussed how Hexagon supports the team in streamlining performance by ensuring compliance with FIA regulations, precision manufacturing, and ensuring the team ‘gets it right first time’. More than just a soundbite, Mike Hughes, Head of Quality Assurance and Manufacturing Engineering at Oracle Red Bull Racing, qualified the support of Hexagon with a statement: “With Hexagon’s help, we’ve managed to reduce our faults by 50% over the last two years.”
Morgan’s presentation alluded to how Hexagon is involved throughout the process chain, from 3D CAD modelling and CFD simulations in the virtual wind tunnel to simulation and physical wind tunnel testing. With over one million components handled throughout the season, Oracle Red Bull Racing combines exceptional hardware with efficient software and digital twins to deliver rapid inspection rates. The team has four QA departments encompassing mechanical, external, composites, and race support. They all utilise Hexagon tools, from CAM software to 3D scanners, laser trackers, portable measuring arms and CMMs.
The Leica AT960 scanner is a core element of the trackside equipment that improves accuracy and holistic measurement. Its custom orientation enables measurement from different perspectives. For legality checks, Oracle Red Bull Racing uses the AS1 scanner to scan the floor, front, and rear wings to extract key points of the car for performance set-up.
With the arrival of Red Bull’s first road car, the RB17, and the opening of its 5,000sq/ft powertrain manufacturing site in Milton Keynes, Red Bull’s number of components produced is set to expand significantly, as will its relationship with Hexagon.
The F1 car continually undergoes design cycles that follow the same structured path. With up to 100 projects in-cycle at any time, around 1,000 design cycles are completed yearly. It starts with developing a 3D CAD model and the subsequent digital twin, which is the foundation block for everything that comes after. With CFD, prototypes and a whole raft of processes before the team gets to a finished car, Morgan said: “When you work on a car in the factory and then take it to the track, if there is an issue in manufacturing – it’s too late to do anything about it. We must be sure the car is 100% correct before shipping it. That is why we need Hexagon: to ensure that everything leaving the factory is perfect for when it arrives at the track. We have thousands of parts that need to fit together perfectly. We work to the micron. It’s precision you would see in a high-end watch – but not typically in a 5m long vehicle.”
A presentation on Hexagon’s Nexus suite by Stephen Graham, Executive Vice President and GM of Nexus at Hexagon, followed this. Stephen explained: “Nexus is our cloud-based manufacturing platform. We initially conceived it to solve an internal problem. We have acquired over 150 companies in more than 25 years, which has helped us build this portfolio of technologies throughout the product life-cycle. Our challenge is a large portfolio of technology solutions that were never really intended to work together. We wanted to offer our customers a solution to join the dots and bring the next level of value with the technologies all being under one roof. Nexus was conceived to solve this problem of connectivity. As soon as we took the proposition to our customers, we found they had the same problem. Over decades, they had purchased different technologies to solve different problems.”
“Nexus directly solves that problem, and what we have found in the last few months is an ability to connect to different technologies from different vendors – it doesn’t just have to be Hexagon products. Since starting development, we have found that businesses are structured very hierarchically, with different disciplines arranged in different silos. The whole thing is very process-driven, and as we try to push the boundaries of manufacturing, this becomes a barrier to succeeding. The need to drive collaboration horizontally across an organisation is coming to the fore as a challenge that needs to be faced.”
To demonstrate this, Stephen provided a slide show showing a reverse-engineered workflow using 10 products from Hexagon that facilitate different elements of a product’s lifecycle. The demonstration alluded to new cloud-native apps, technologies and solutions connected to products in the portfolio for decades, such as PC-DMIS. Nexus creates an end-to-end solution that connects the dots. Stephen added: “Once these collaborative workflows have been strung together, engineers can work collaboratively. This provides the opportunity to bring automated and AI technologies into the workflow as automated collaborators in the workflow. A great example of this is ProPlanAI, which we just launched. This large NAPA language model provides precise engineering answers for CAM engineers who may be programming CNC machines. It automatically collates data and generates a G-Code to drive machines on the shop floor. This gives engineers superpowers to drive productivity to the next level.”
Hexagon claims that ProPlan AI cuts the time to program machine tools by 75%. The new AI technology enables machine shops to achieve operational excellence at scale, powered by Microsoft Azure services built into Hexagon’s cloud-based Nexus connectivity platform. Available in Q1 2025, ProPlanAI will ‘learn’ from the data created by a company’s CAM programmers. This will enable manufacturers to automatically explore existing programming information to predict ideal outcomes tailored to a company’s preferences, production capabilities, and needs. ProPlanAI will continuously learn and adapt, ensuring programs are as efficient and productive as possible. ProPlanAI can be trained with a company’s institutional knowledge to ensure machines can be quickly and efficiently programmed to their quality standards. Additionally, a Hexagon Copilot provides suggested pathways to advise on best practices without leaving their CAM software.
The innovation has been developed in collaboration with Microsoft, and Ygal Levy, the EMEA Manufacturing Managing Director at Microsoft, discussed the company’s strategic partnership with Hexagon in greater detail during an afternoon presentation on the ‘Transformation of manufacturing through Connectivity, Collaboration and Cloud/AI’.
Clare Barclay, President of Enterprise and Industry at Microsoft EMEA, said: “Microsoft’s collaboration with Hexagon is driven by a shared belief that we can transform manufacturing productivity. It’s rewarding for us to see how the AI capabilities provided by Azure are empowering CNC programmers with productivity-boosting automation while helping new users upskill faster. This is exactly the sort of transformation AI can bring to the industry, and we are excited to see Hexagon apply its manufacturing expertise to transform workplace productivity.”
Verifying the Solution
Just over a year ago, MTD magazine visited RODIN Machining. A few miles north of Amsterdam, the start-up company set out to develop an autonomous factory. Incorporating FASTEMS automation, robot-loaded Mazak machines, and integrated innovations that made the mind boggle, RODIN has been a beta-test customer, putting ProPlanAI through its paces before market introduction. Paul Mooij, Director of Digital at RODIN Machining, said: “Machine tool programming is complicated to automate and requires experience. ProPlanAI is exciting because we can leverage our human capital for greater machine utilisation. Our team can program machines in a fraction of the time by applying their valued skills in supervising ProPlanAI suggestions and finalising the programme specifics.”
Paul added: “We have built an autonomous factory but are limited by the engineering input we can put into it. This boils down to a race for talent, and we all know it isn’t easy to get good people. We have been working with Hexagon on the development of ProPlanAI, looking at how can we fill it with our data and train it with our models, our machines, tools and our way of working – providing a suggestion of how the model thinks our way of working should be. We can then position our engineer to supervise and undertake ‘prompt engineering’. ProPlanAI is very powerful and provides the right context for the features, model, machines, and tooling available. Using the given context, it then decides, ‘I think you should use these processes for this machining operation’’.”
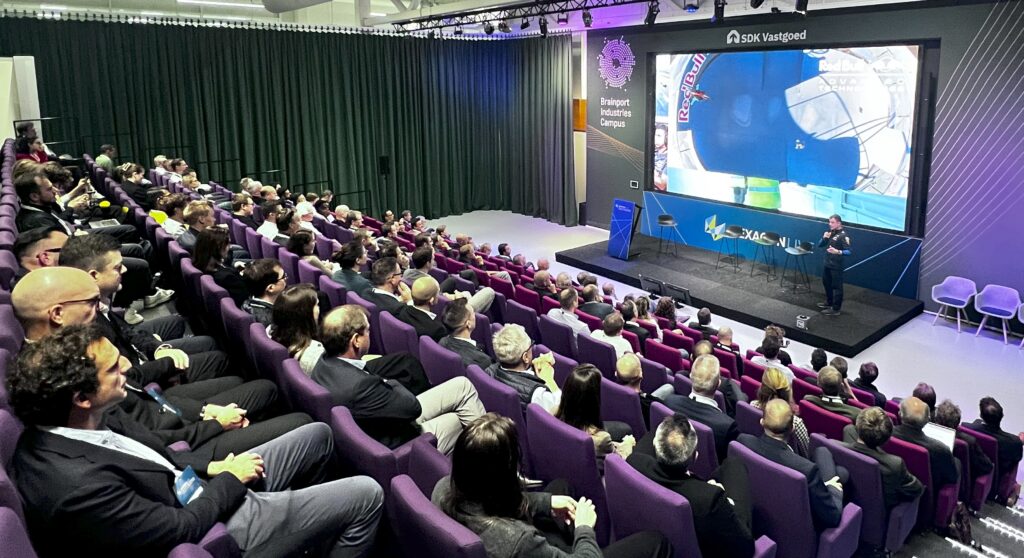
“This has become powerful, and we are progressing rapidly to make big savings. We are leveraging our human capital to achieve more by using AI to provide suggestions. Then, our engineers decide whether to accept the suggestion and proceed or refine the process. For example, we may have a 2D PDF drawing that needs to meet specific tolerances, and ProPlanAI may not know this – and this is the experience we can add to the system. It’s been a fantastic collaboration, and the system continually evolves.”
Discussing the current situation, Paul told MTD magazine: “Our engineers will consider how they approach a job and create the CAM file in Esprit. We then feed our models to our developers. Over the last 18 months, we have been feeding the data to ProPlan AI, which uses our approach, machining strategies, cutting tools, machines, characteristics and experience. ProPlan AI creates suggestions for the next job and pre-populates our program, so our engineers are validating and refining the suggestions to meet our specifications. It amplifies the output of our staff.”
“For example, if we have an aluminium job that needs a threaded hole with a chamfer, we would have a unique way of doing that with our machines and tools in our CAM files. Based on those patterns, the model learns our strategies and recognises the parameters for a threaded hole in aluminium, the feeds, speeds and so on.”
Looking at benefits during testing, Paul adds: “It is amplifying our output and boosting our efficiency. At present, the savings are impressive. We continuously add data to our ProPlanAI suite, so the savings will cascade into ever greater efficiencies as we progress.”
Precision tooling solutions for aerospace components
In the realm of cutting-edge aerospace applications, precision and performance are essential for transforming the toughest materials into high-flying components. Whether titanium alloys, nickel-based superalloys or advanced ceramics, these materials and the tools that machine them are the backbone of aerospace innovation. Kennametal’s tooling solutions are designed to tackle manufacturers’ challenges, helping them achieve higher precision, better surface finishes and increased productivity.
Reliance on high-temperature resistant materials presents challenges. Traditional tooling doesn’t stand a chance when used in this environment due to friction, deformation and other component failure. For example, engine parts made from titanium and superalloys must endure temperatures over 1,000°F. That’s why high-temperature machining solutions become critical. It also means that the materials being used demand more than just tough tools; they must thrive under extreme conditions.
High-Temperature Machining Goes the Distance
Components powering everything from jet engines to exhaust systems are built to withstand extreme environments. Machining these components requires tools that can perform without compromising an aircraft’s structural integrity. This is exactly where Kennametal excels, delivering tooling solutions that meet aerospace’s toughest demands head-on.
Innovative Tooling Solutions
Kennametal’s high-temperature machining tools are specifically engineered to tackle challenges such as high cutting forces, heat buildup, and work hardening. They use advanced coatings, precision geometries, and heat-resistant materials for efficient machining under extreme conditions.
Kennametal’s family of HARVI solid carbide end mills is a game-changer for machining tough aerospace materials like titanium and Inconel. HARVI™ Ultra 8X excels in airframe structural machining, while HARVI™ III is optimised for titanium applications. The HARVI I TE, with its twisted cutting edge, boosts corner stability and excels in ramping and helical interpolation. It features advanced anti-vibration and anti-friction technology. The innovative flute design with chip gashes reduces cutting forces, making chip evacuation super-efficient.
Building on the success of the HARVI series, the newly launched HARVI II TE end mills feature a 5-flute design for aggressive cutting in ramping and plunging, as well as a proprietary W-flute shape for better chip evacuation and a stronger core. Overall, the HARVI tools deliver significant time and cost savings in aerospace operations, with impressive Metal Removal Rates (MMR) and tool life.
Drilling composites like CFRP can effectively create fuselage, wing skins, and spoilers. Still, Kennametal’s KenTIP™ FS series of drills featuring a double-angle geometry is specifically designed for composites. Additionally, Kennametal offers KenShape™ MaPACS & MaxPACS and HiPACS countersink and drill solutions. These tools are engineered to handle the challenges of drilling composites, ensuring clean cuts and minimising issues like delamination and fibre breakout. By using these advanced tools, manufacturers can achieve high-quality results while maintaining the structural integrity of their components.
When it comes to precision turning, especially with tough materials, Kennametal’s Beyond Evolution™ line of carbide and ceramic inserts will be effective. These inserts are built to handle the high temperatures associated with turning operations, which are common when working with hardened steels in landing gear and other components.
Dealing with the hassle of frequent tool changes, especially when working on large components like wing sections, Kennametal’s KM™ and KM4X™ modular quick-change tooling systems come into play. They make tool changes super quickly without losing accuracy. For tasks that need high repeatability, like wing skin assembly, it’s crucial to calibrate tool holders to keep everything aligned perfectly regularly.
“Aerospace manufacturers can achieve exceptional precision and productivity with our tooling solutions, ensuring every component meets our aerospace customers rigorous demands,” said Eva-Maria Weber, Manager Aerospace Business Unit CE.
Overcoming Challenges in High Temp Machining
In high-temp machining, precision, reliability, and speed are key and always at the forefront. Sometimes, problems arise, such as in thin-wall applications, surface finishes, and milling applications.
Walking the Thin Line
Thin-wall applications are often used to reduce weight without sacrificing structural integrity. Parts like fuselage skins, wing sections and other structural components rely on this technique. However, machining thin walls can be challenging due to vibration, deformation, and heat. To address these challenges, adjusting the feed rate and depth of cut can help reduce vibration before resorting to complex setups.
Dampening tools at lower spindle speeds can improve stability without compromising finish quality. Kennametal’s high-feed mills and coated carbide inserts can successfully machine titanium for fuselage sections, maintaining wall stability and accuracy.
In relation to spar fittings, machining composite components and aluminium, which consist of thin walls, requires careful part movement and precise and rigid fixturing while managing machining around multiple pockets.
Milling Applications
Machining materials like titanium, Inconel, and CFRP can present obstacles due to their strength, lightweight, and resistance to high temperatures. Superalloys and hardened metals generate significant cutting forces, leading to vibration, deflection, and tool wear, especially when tight tolerances are required. Aerospace components are often complex and have 3D shapes, requiring multi-axis milling and customised tooling strategies to ensure accuracy in hard-to-reach areas.
“Our advanced milling solutions are specifically designed to address unique challenges, providing efficiency and accuracy when machining high-performance materials like titanium and Inconel,” said Patrick Mesnil, District Business Manager and aerospace business leader France & Benelux.
Advanced tooling coated with Diamond-Like Carbon (DLC) or PCD can improve cutting efficiency. Optimised cutting conditions, including adjusting speeds, feeds, and depths of cut, help manage heat and forces during machining. Effective cooling solutions, like high-pressure coolant, dissipate heat and prevent workpiece deformation. Multi-axis CNC machines allow for precise machining of complex 3D shapes, ensuring accuracy in hard-to-reach areas.
Surface Finish
When it comes to high-temp machining, achieving quality surface finishes is essential. It can be affected by factors such as tool wear, cutting speed, feed rate and the material being machined. Advanced multilayer coating technologies like TiAlN and AlTiN on their carbide tools help control the heat at the cutting edge. These coatings act as a barrier, reducing friction and heat transfer.
As new aircraft standards emerge, emphasising lighter, more heat-resistant, and sustainable components, continuous innovation in tool geometries and coatings plays a critical role in advancing component development.
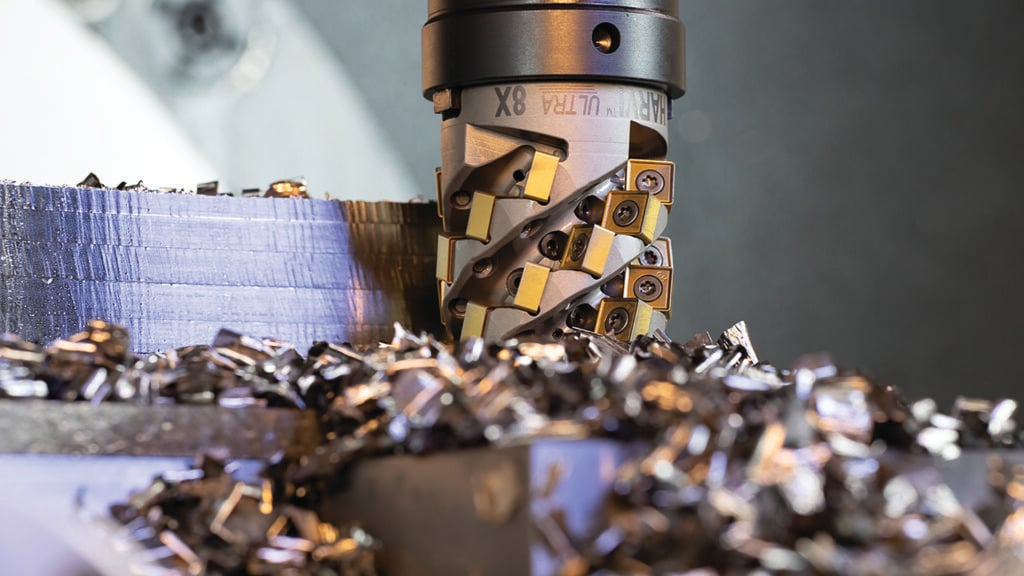
For example, larger components, such as engine cases, require challenging process controls and careful application with tool pressure in mind. Internal and external milling operations must also consider thin walls and fine surface finish requirements when working with tough materials.
Additionally, turbine disks require managing low thermal conductivity and vibration to avoid part deformation. This requires application-specific tooling to provide the required cooling capabilities and productivity.
As the industry continues to explore new materials and complex geometries, advanced tooling solutions must meet emerging challenges. In high-temperature machining, where precision, reliability and speed are crucial, Kennametal’s tools provide aerospace manufacturers with solutions to support the next generation of high-flying components. Designing and engineering tools that solve today’s challenges and anticipate tomorrow is essential.
Brother halves cycle times
In 2023, R&A Engineering won a contract to produce several hundred aluminium parts per month across six variants for assembly into sensors that optimise wind turbine orientation to maximise power output. The job involved tying up a pair of BT 40-taper VMCs, which impacted the Aylesbury-based subcontractor’s ability to do other work. So, the decision was taken to order and transfer production to a 30-taper, high-speed Brother M200X3 VMC with a 16,000rpm spindle.
Delivered in August 2023 by Whitehouse Machine Tools, the Speedio M200X3 5-axis VMC has, on average, halved the time it takes to complete post-anodising milling, drilling and tapping operations on the six components. Therefore, the machine can perform the same work as the two VMCs used previously, which are now free to carry out other work.
Ed Piotrowski, Operations Manager at R&A, said: “We approached a couple of 30-taper VMC suppliers, but Whitehouse was the obvious choice, even though we have never bought a machine from them before. It is a family-run firm like ours and has a similar ethos regarding service, which was obvious when we visited their showroom in Kenilworth for demonstrations.”
“The Brother performs very well. Cycle times are now between one-and-a-half and four minutes, half of what they were before, and the ±0.05mm tolerance is held all day long without any problem. It is an accurate machine.”
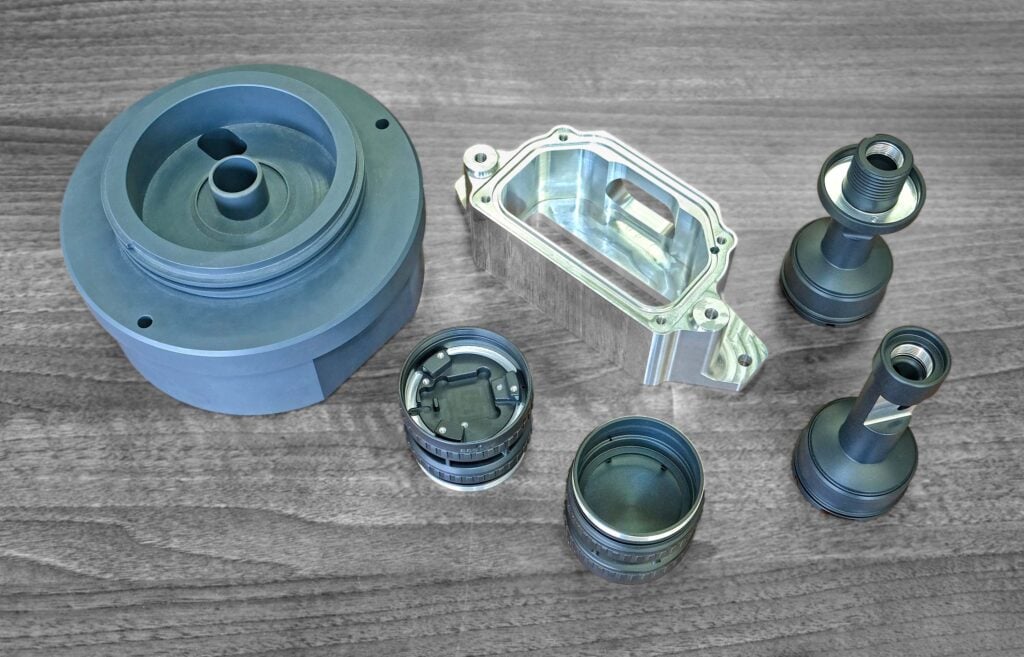
Established in 1985 by Ed’s parents, Richard and Alison, and currently employing 18 staff, R&A has grown by 50% since 2021. It has invested £800,000 in machine tools over the past couple of years and is looking to automate production in the turning and milling sections. The rationale is twofold: to take on extra work without compromising existing, long-running contracts; and to be more cost-competitive on the world stage to accelerate the flow of work already being reshored from Asia and elsewhere in increasing quantities.
Ed has some interesting insights into why a subcontractor should invest in a 30-taper VMC. An adage in contract manufacturing is that one never knows what work will come through the door next. Therefore, the wider applicability of a 40-taper machine due to its size and power makes more sense. The first advantage of a nimble milling machine with a smaller diameter tool interface is high-speed production, which translates into greater profitability. Not only does the elevated spindle speed combined with up to 30m/min cutting feed rate provide generous metal removal rates, but idle times are lower due to 50m/min rapids in the X, Y, and Z axes.
A less well-known benefit is the vastly lower power consumption of 30-taper machines. Ed advised that the M200X3 draws less than 10kVA, versus typically 50kVA for a 40-taper VMC or perhaps even more if it is an old machine. Energy bills are therefore lower and, as is the case at the Aylesbury facility, if a factory is close to its power supply limit, the lower kVA rating is a godsend.
Reviewing the characteristics of the respective BT spindle machines, Ed observes that while power and rigidity are higher in a 40-taper VMC, modern, smaller-taper counterparts such as the Brother have a reasonably well-specified spindle motor with good torque, even in the medium to high-speed range. The drive motors are also consistent with robust machining, and face-and-taper-contact tool retention assists further, as in R&A’s case.
“Although machining of light alloys is the province of this type of machine, using modern CAM software to create intelligent cycles involving light depths of cut and high-speed contouring means that tough and difficult-to-machine metals can also be tackled.”
The M200X3 has a further advantage for OEMs and subcontractors alike. It is equipped with a torque motor to drive the rotary table, allowing a component to be indexed and rotated at up to 2,000rpm so it can be machined with a static turning tool in the spindle. Completing this second operation in-cycle without the need to re-fixture the part in a lathe raises accuracy and productivity.
The mill-turn capacity in a small footprint holds much potential on the shop floor at R&A. Take, for example, the wind turbine sensor job for which the machine was purchased. All six parts undergo turn-milling on a lathe before being sent out for anodising. The Brother must only remove the insulative anodic layer in certain areas to provide electrical conductivity. With the latter machine’s turning capability, all parts could be completely machined. Richard and Ed are actively considering this possibility, which would require automated component handling to be retrofitted.
In addition to seizing opportunities in the renewable energy sector, R&A is also taking advantage of growth in vehicle electrification. Two aluminium parts have already been produced on the Brother VMC for the latter sector. One is an EV engine terminal block, which is milled, drilled and tapped in a 20-minute cycle. Another engine part has been transferred to the M200X3 from a 40-taper machine, with the part now machined in eight minutes rather than 12, again leading to more competitiveness, shorter lead times and more overall capacity on the shop floor.
Ed is already planning the next job for the Brother. Water purification work accounts for about one-third of the subcontractor’s turnover. One of the parts machined from Ertacetal, an electrically conductive plastic, is currently turned and milled in four set-ups on three other machine tools. On the Brother it will come off complete after two set-ups.
New development benchmarks in milling
Milling originated in the late 18th century and quickly became one of the primary machining technologies. Nowadays, it is easier to imagine any machine shop with milling operations on the shop floor; it’s an essential process in manufacturing. The increasing demands of manufacturing drive this integral part of machining technology. However, there are specific aspects that uniquely impact the advancement of milling.
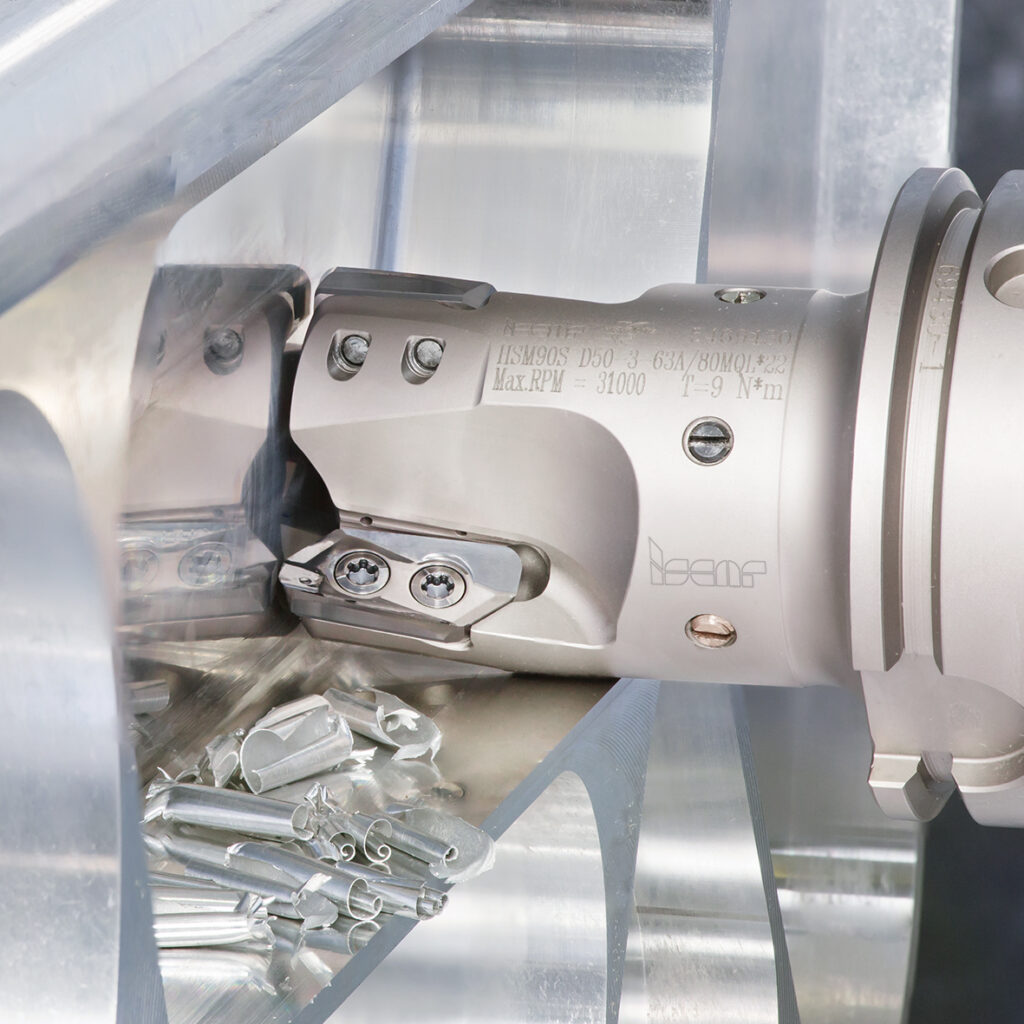
We are witnessing significant changes in manufacturing that will have profound consequences on the development of milling directions. These changes are driven by various factors, such as the increasing accuracy of metal forming through precision investment cutting and precision forging, the widespread adoption of 3D printing, and the growing usage of new composite and sintered materials. Furthermore, there is a need to enhance productivity in machining hard-to-cut superalloys and titanium grades, and the strong focus on electric and hybrid cars in the automotive industry contributes to these changes. In addition, advancements in multi-axis machine tools have opened new possibilities for the precise machining of complex parts and enabled the implementation of new cutting strategies to improve productivity. In modern technological processes, there is a tendency to significantly reduce the machining stock intended for milling operations while simultaneously increasing the requirements for surface finish.
Therefore, the advancement in milling is driven by the need for higher productivity, precision and sustainability in milling operations. Consequently, the main developments can be characterised as follows:
- Fast metal removal focuses on boosting the metal removal rate (MRR) to achieve higher productivity by significantly increasing cutting speed or feed per tooth. This is achieved through techniques such as high-speed milling (HSM) and, in rough operations, high-feed milling (HFM).
- Precision milling provides higher accuracy in milling operations.
- The utilisation of multi-axis machining centres characterises multi-axis milling to enable complex milling operations.
- Adaptive milling aims to develop intelligent systems that can adapt to changing conditions during machining.
- Sustainable milling strives to reduce the environmental impact of milling operations. It involves developing eco-friendly cutting fluids, recycling and reusing materials, and using energy-efficient machine tools and milling cutters.
Success in these areas relies on the synergy of several key components: machine tools, cutting tools, and CAM systems. High-speed milling necessitates machine tool technologies capable of handling exceptionally high rotational velocities and advanced cutting materials and coatings for milling tools. Simultaneously, enhancing the precision of milling operations requires milling cutters with tighter tolerances and improved control systems and linear motor drives. In the case of multi-axis milling, the breakthrough lies in effectively controlled axes movement, along with the application of appropriate cutting geometries for milling tools.
On the other hand, adaptive milling incorporates innovations such as using state-of-the-art monitoring systems, high-sensitive sensors, and efficient algorithms to optimise cutting data and tool paths in real-time. Moreover, sustainability advancements require energy-efficient milling strategies that employ suitable machine tools, cutting tools, and eco-friendly coolant techniques.
Indexable milling reflects the advancements that feature exchangeable cutting inserts in machining operations.
a) Advanced insert materials are an ongoing process to improve the cutting materials for indexable milling inserts, including the development of advanced carbide grades, ceramics, and ultra-hard cutting materials.
b) Coating technologies with continuous R&D focus on new coatings to improve wear and heat resistance while enhancing lubricity.
c) Progressive cutting geometry optimises cutting geometry and chip forming topology of inserts to improve cutting action and diminish cutting forces and chip flow in milling operations.
d) Effective cutting material uses an intelligent insert design to provide maximum indexable cutting edges without reducing cutting capabilities.
In addition, the distinct course on smart manufacturing requires the integration of digitisation into milling operations and tools. Regarding tools, digital twins and software applications have already become a ‘must’ feature of a comprehensive tool range.
How can cutting tool producers rise to the challenge? Which milling tool solutions will provide the right answer to the emerging trends? Is the field of cutting tool manufacturing, often considered conservative in metalworking, capable of delivering a timely response to current demands? The recent advancements from ISCAR provide greater insights into these subjects.
High-speed trochoidal milling involves following a curvilinear tool path to maintain a constant load on the cutting edge to eliminate spikes in load during material entry. This strategy is efficient for milling deep slots, pockets, and cavities. Additionally, trochoidal milling has shown excellent results when working with challenging materials such as high-temperature superalloys.
The CHATTERFREE EC-E7/H7-CF is a new family of multi-flute endmills for trochoidal milling techniques. The family’s geometric design includes different helix angles and variable angular pitches to improve dynamic behaviour. These endmills are available in a range of length-to-diameter ratios (Fig. 1).
Machine tools allow highly productive milling of aluminium alloys at extreme spindle speeds, reaching up to 33,000rpm. To meet this challenge, ISCAR has developed 90° indexable milling cutters that accommodate large inserts for a depths of cut up to 22mm (Fig. 2). The cutters have been designed to eliminate insert radial displacement, which may occur due to the high centrifugal forces generated during very high rotational speeds.
High-feed milling (HFM) has become a widely adopted method for efficiently rough machining complex and flat surfaces. ISCAR offers a comprehensive range of HFM products to meet the demands of various industrial applications. Recently, the range has been expanded with new additions. The LOGIQ-4-FEED family of HFM tools, featuring specific bone-shaped inserts (Fig. 3), now includes tools with larger inserts. These new products significantly broaden the application range, particularly in the mould and die industry’s high-feed milling of large-sized cavities. Another addition is NEOFEED, a family of HFM tools with double-sided inserts, providing eight cutting edges for improved cost-effectiveness.
Advancements in multi-axis machine tools and CAD/CAM systems have given rise to precise milling of complex shapes with minimal machining stock, using segment or barrel-shaped endmills. ISCAR’s program for these endmills encompasses three design concepts: a solid carbide design, an exchangeable MULTI-MASTER head, and a one-insert approach (Fig. 4).
When milling high-temperature superalloys, cutting ceramics can substantially increase cutting speeds, reaching 1000m/min. ISCAR’s latest ceramic tools include ceramic solid endmills and indexable milling cutters with double-sided round ceramic inserts. The double-sided design aims to maximise the utilisation of ceramic material grades, such as ‘black’ ceramic, whisker-reinforced ceramic, and SiAlON (a silicon-nitride-based ceramic). These selected examples serve as good illustrations of the main directions of advancement in milling tools. As new demands arise, new solutions are required, and these new challenges will fuel the search for innovative tool designs.
Ten benefits of apprenticeships
Over the past nine years, the Close Brothers SME Apprentice Programme has helped to fund 110 apprenticeships by partnering with the AMRC Training Centre, Make UK, and the Manufacturing Technologies Association (MTA).
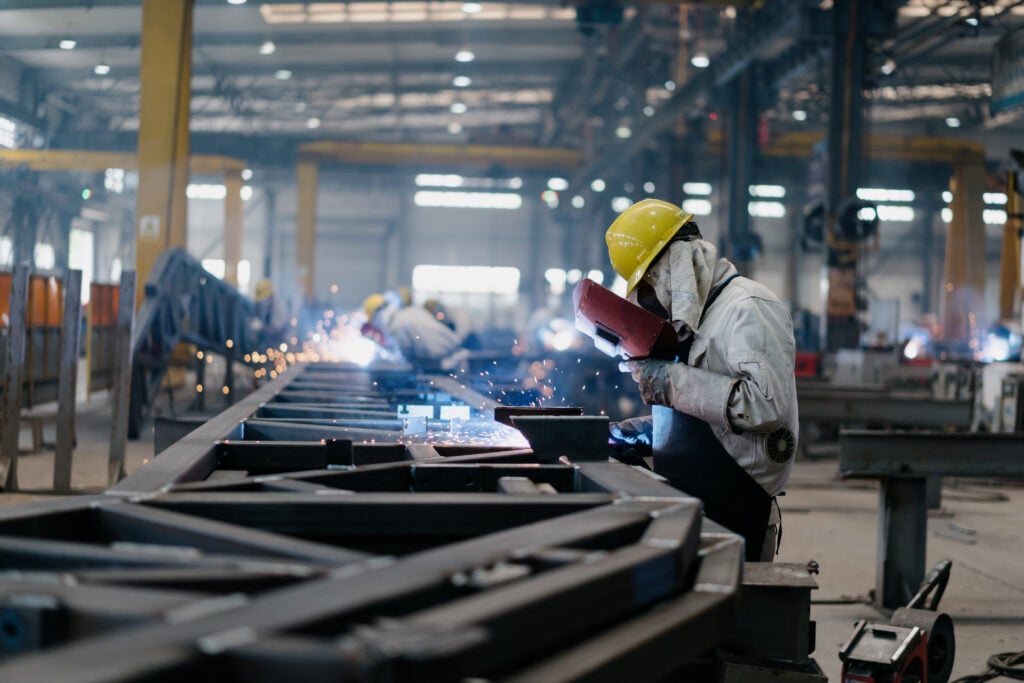
As part of its responsibility to help address the social and economic challenges facing businesses, the programme helps SMEs fill skills gaps, develop their future workforce and improve long-term growth prospects while providing a vital opportunity to invest in local talent.
In this article, we examine just some of the benefits apprenticeships offer both apprentices and their employers.
- Hands-on experience: Apprenticeships provide practical, hands-on experience that is invaluable in the engineering and manufacturing sectors. This real-world training helps apprentices develop the skills needed to excel in their chosen field.
- Earn while you learn: One of the most attractive aspects of apprenticeships is earning a salary while gaining qualifications. This financial support can make it easier to focus on learning without the burden of student debt.
- Industry-recognised qualifications: Apprenticeships often lead to industry-recognised qualifications that employers highly value.
- Career advancement: Completing an apprenticeship can open doors to advanced career opportunities. Many apprentices go on to secure higher-level positions within their companies or move into specialised roles.
- Mentorship and support: Apprentices benefit from the guidance and support of experienced mentors. This mentorship can provide valuable insights, advice, and encouragement, helping apprentices navigate their career paths more effectively.
- Job security: The skills and experience gained through an apprenticeship can lead to greater job security. Employers often prefer to hire individuals who have completed apprenticeships because they have proven their ability to perform in real-world settings.
- Networking opportunities: Apprenticeships provide opportunities to build professional networks within the industry. These connections can be beneficial for future job searches, career advice, and professional development.
- Skill development: Apprenticeships focus on developing a wide range of skills, from technical abilities to soft skills like communication and teamwork. This comprehensive skill set is essential for success in engineering and manufacturing roles.
- Pathway to higher education: For those interested in further education, apprenticeships can serve as a stepping stone to higher education opportunities. Many apprenticeship programs offer pathways to advanced degrees or additional certifications.
- Contribution to innovation: Apprentices in engineering and manufacturing often work on cutting-edge projects and technologies. This involvement in innovative work can be highly rewarding and can contribute to significant advancements in the field.
Apprenticeships offer multiple benefits that can help individuals build successful and fulfilling careers. These programs provide a solid foundation for professional growth and development, from hands-on experience and financial support to mentorship and job security. Whether you are just starting out or looking to advance your career, an apprenticeship can be a valuable and rewarding choice.
For more information please visit: closeassetfinance.co.uk
CERATIZIT delivers success that is ‘Made in Sheffield’
The term ‘one-stop-shop’ is often banded around the subcontract manufacturing industry.
It’s not until you find a company like Woodbrook Precision Ltd that you can truly understand what a single source solution provider looks like.
The Lancashire manufacturer ventures beyond rivals’ services and continually invests in the latest machine tools fully supported by advanced cutting tool solutions from CERATIZIT UK.
The company is located in Ashton-Under-Lyne on the Northeast edge of Greater Manchester.
It’s plant list includes a complete array of manual and CNC 3 to 5-axis machining centres and multi-axis turning centres from renowned brands such as Mazak, XYZ, Leadwell and Bridgeport.
The state-of-the-art plant list is supported by services such as grinding, plating, shearing, profiling, welding, laser cutting, gear cutting, heat treatment, powder coating and more.
Rightly proud of its comprehensive services and recent investment in Mazak machine tools, Managing Director Stephen Hogg from Woodbrook Precision says that CERATIZIT has been instrumental in enhancing the productivity of the new equipment.

The second-generation business was founded by Stephen’s father more than 35 years ago.
When Stephen bought the company 16 years ago, Woodbrook operated out of a small unit with a single CNC turning centre and a series of manual mills—all supported by various cutting tool vendors, with WNT (a member of the CERATIZIT Group) being one of the many.
However, as Stephen has applied his vision and determination to the company, Woodbrook has evolved with a 2018 move to an 18,000sq/ft facility three times larger than the previous site.
Plans are also afoot to add another 10,000sq/ft.
This growth has stemmed from the business’s progress in general subcontract machining into the oil & gas, aerospace, rail, and motorsport sectors.
Woodbrook has evolved the sophistication of its machine tool purchases to serve these industries.
Initially investing in 3-axis Mazak VMCs with rotary tables and turning centres with live tooling, more recent acquisitions have included two 3.5m bed Mazak VTC800/30SR 5-axis machines and a 5-axis Mazak CV5-500.

This has seen work for overhead cranes, rail, and general subcon evolve to aerospace jigs and fixtures, critical subsea valves and manifolds, motorsport brake callipers, engine components and more.
With an evolution driven by the expanding capabilities of its machine tools, Woodbrook has needed to rely more heavily on the expertise of its cutting tool suppliers.
As the business has shifted from machining steel and aluminium to stainless, super duplex, titanium, inconel, carbon fibre, hastelloy and much more – CERATIZIT UK has risen through the ranks to be the cutting tool partner of choice.
Stephen Hogg from Woodbrook says: “Over ten years ago, CERATIZIT was one of many suppliers, and as I took control of the business.
It became evident that CERATIZIT had the best-performing tools and their service was far beyond anything else.
As we continually ventured into more complex work and more challenging materials, we needed greater support and new machining strategies.
CERATIZIT UK’s Technical Sales Engineer Matthew Darbyshire has been with us all the way to provide the solution.
It’s been seamless, and it’s pointless going elsewhere as Matt makes it so easy and ‘painless’ for us.”
“With numerous sales reps continually calling upon us, we asked Matt for a few tools to trial.
The tools initially performed well, but for the relationship to blossom to a position where we now have thousands of CERATIZIT tools.
This has been built on tool performance, product range diversity, supply chain continuity and most importantly, technical support, service and trust that has instantly been available.
I can WhatsApp Matt with any drawings and queries and he’ll deliver a solution imminently.”
As a machine shop that typically manufactures prototypes in small batches, tracking continuous tooling improvement isn’t always the priority for Woodbrook.
However, you don’t have to look far for quantifiable results with CERATIZIT products.
Stephen says: “We recently implemented the CERATIZIT facing and parting-off tools, and it reduced the cycle time on a 400-off job from 1 minute 58 seconds to 1 minute 26 seconds.
We also applied the Dragonskin CircularLine DLC-coated solid carbide end mills with impressive results.
The Dragonskin tools have cut cycle times on an aluminium part from 3 minutes to 1 minute 20 seconds whilst more than doubling our tool life.”
“On another 100-off repeat order stainless steel aerospace fixture, we needed to reduce our cycle times to maximise margins and reduce costs.
Matt introduced a CERATIZIT UK high feed indexable end mill, and this reduced our cycle times from 38 to 26 minutes per part, with a tool life improvement of more than 20%.
This was a significant saving on a long-running job.” However, the most significant saving wasn’t from the cutting tools….
With the 100-off stainless job running through the business frequently, Woodbrook set up six vices in a line on the spacious 3.5m bed of its Mazak 5-axis VTC800/30SR.
When each surface and cycle was completed, an operator would re-set the job to process the next face.
With a total of four operations, the process was laborious.
Stephen spoke with Matt from CERATIZIT, and the way forward was a bespoke workholding solution that was ‘Made in Sheffield’ at the CERATIZIT UK Technical Centre and Headquarters.
Stephen visited the CERATIZIT stand at MACH 2024.
He realised that the only cost for CERATIZIT’s bespoke service was the price of the aluminium tombstone billet and the cost of the four ZSG4-125 Centric vices that connect to the zero-point single riser tombstone system.
Immediately impressed, Woodbrook Precision ordered a pyramid system to clamp smaller parts in its 5-axis Mazak CV5-500.
The ZSG4-125 Centric vices with serrated jaws enabled Woodbrook to clamp on as little as 3mm of stock, permitting the subcontractor to hit all five sides of the stainless parts with confidence in the high-torque clamping forces of the vice.
With five faces machined in a single operation, the following operation was to turn the parts over to complete the sixth surface.
This reduced this 100-off repeat job from a four to a two-operation process, saving an additional 10 minutes per part.
Stephen says: “This job took over one hour per part from start to finish.
The tombstone and Centric ZSG vices immediately took more than 10 minutes off each part, with peripheral savings being longer running times without operator intervention.
Reduced set-ups also improved our precision, repeatability and consistency over an entire batch of parts.
We work 12 hours a day, six days a week, and the tombstone enabled us to set up a batch of four parts at the end of a shift to run unmanned for a couple of hours – giving us further savings.”
“We’re now using CERATIZIT for everything from our back-ends and collets to solid carbide and indexable tools ranging from drills and threadmills to end mills, turning and parting tools.
We never thought we’d be turning to CERATIZIT for our workholding solutions, but just like the cutting tools – the quality and performance of the workholding solutions that come with a ‘Made in Sheffield’ brand is far superior to anything else we’ve encountered.”
Quick holemaking
The design concept of assembled drills with exchangeable solid carbide cutting heads, adopted by ISCAR at the turn of the century, significantly altered the company’s holemaking product program.
As part of this concept, a precise carbide head is mounted in a steel holder using the ‘self-clamping’ principle, which relies on the holder’s elastic deformation without any mechanical clamping means.
This approach is characteristic of various successful ISCAR products, such as the SELF-GRIP and MULTI-MASTER tool lines.
These have substantially improved machining performance and revolutionised traditional perspectives on cutting tool design.
This is complemented with stoppers and locking sections for reliable security.
In the assembled drills with carbide heads, the cutting head has a specially shaped rake surface to optimise chip formation and a centring area to ensure high accuracy.
The drill body is produced from a high-strength steel grade and features the innovative design of the head pocket, helical flutes, and internal channels for coolant supply.
Advancements in technology, particularly in powder metallurgy processes and CNC machining, have made this design feasible.
The concept of assembled drills with carbide heads guarantees several key advantages:
1. With a rigid structure, reliable clamping principle, unique cutting geometry and advanced carbide grade of the heads, the drills guarantee productive results.
This significantly reduces cycle times and enables high-quality holes.
These drills can be used for machining a wide range of materials, including steel, stainless steel, cast iron, titanium and high-temperature alloys.
2. High repeatability and ISCAR’s ‘no-setup-time’ principle promise that a worn head can be replaced without removing the drill from a machine, eliminating additional setup operations and considerably decreasing downtime.
The simple change of the heads makes the drills user-friendly and easy to handle.
3. The drills are available in a wide range of diameters and overall lengths to suit various applications.
4. The use of interchangeable heads diminishes the need for a large drill inventory.
ISCAR’s drills with exchangeable carbide heads provide customers with a valuable tool solution to enhance the profitability of holemaking operations.
Over the past 20 years, these drills have undergone significant changes.
Beginning with the CHAMDRILL family, each new phase in the concept’s enhancement has led to new products that outperform their predecessors.
Today, SUMOCHAM is ISCAR’s most popular family of assembled drills with exchangeable carbide heads and is highly regarded by customers.
The continuous search to increase drilling productivity, mainly when machining materials that produce fine chips, has created the LOGIQ-3-CHAM – a family of three-flute drills that utilise the same self-clamping approach.
ISCAR’s development of carbide-headed drills continues to aspire.
Unsurprisingly, ISCAR’s latest product campaign, LOGIQUICK, has unveiled innovative designs that enrich the existing product families, broaden their scope, and pave the way for new application areas.
The new holder with three flute heads allows a 10:1 drilling depth-to-diameter ratio.
The holder’s main feature is a specific flute design that minimally affects the tool’s structural strength.
Another innovation is the expansion of the LOGIQ-3-CHAM family application to include counterboring.
The specially designed three-flute heads are mounted on existing tools and transformed into highly efficient counterbores.
The unique design features of the heads include a corner chamfer for rapid chipping, specialised deflectors for improved chip formation and a unique margin for enhanced support and guidance.
This significantly boosts performance when machining materials like sticky steel, stainless steel and high-temperature superalloys.
This design facilitates a broad spectrum of counterboring operations, ensuring high-quality holes, even when machining cross-holes with inclined surfaces.
The CHAM-SPADE-IQ is a new family of holemaking tools with exchangeable heads. Introduced as part of the LOGIQUICK, the family provides a solution for drilling steel profile construction beams.
Machining beams often occurs under non-rigid conditions, presenting a significant challenge for manufacturers.
To address this issue, drilling tools must have an adaptive cutting geometry to compensate for the lack of rigidity.
The newly introduced family, dedicated explicitly to profile construction, includes two flute carbide drilling heads and reinforced steel holders.
The heads feature a specific self-centring cutting edge for secure hole penetration and sharp corners to prevent deformation.
The holders’ durable structure maximises the tools’ dynamic stability when drilling at a depth-to-diameter ratio of up to 5.
New drills with MULTI-MASTER adaptations that carry exchangeable carbide heads essentially serve as a ‘bridge’, connecting the successful SUMOCHAM and MULTI-MASTER families.

The drills are a component of a versatile modular tool assembly that allows the mounting of drilling heads on a wide range of MULTI-MASTER tools.
This facilitates an easy and quick change of the heads and the drill bodies. Moreover, the modular concept provides straightforward customisation and flexibility regarding overall length and diameter and finding the optimal tool configuration.
It’s worth noting that the holemaking innovations in the LOGIQUICK campaign aren’t solely represented by assembled tools with exchangeable heads.
Several products of another design concept can also be highlighted.
The three-flute flat-bottom solid carbide drill with internal coolant channels is one such product.
The drill features a small isle for improved penetration, wavy cutting edges for assured chip control, an optimised core diameter to increase tool rigidity, and narrow wiper sections to reduce friction.
This improves surface finish and combines with an internal coolant supply that extends tool life and improves chip evacuation.
These incredible attributes contribute to the promising prospects of this product line.

In the boring line, a new series of boring heads with extra fine digital adjustment has replaced the existing heads with an MB connection.
In the milling line, the portfolio has been enhanced with the addition of the
The QUICK-D-MILL is a family of multi-functional indexable cutters.
These versatile ‘all-in-one’ cutters are suitable for various machining applications, embracing the milling of shoulders, slots, and pockets and drilling flat-bottom holes.
The overview of the mentioned products highlights that ISCAR’s focus on holemaking continues to drive its development efforts.
With the metalworking industry seeking solutions to enhance holemaking performance, ISCAR is confident that its latest LOGIQUICK drilling developments will effectively meet the industry’s demands.
Prima Additive and Comau respond to Euro 7 standards.
Prima Additive and Comau, two Italian companies and global leaders in their respective sectors have joined forces to showcase the advantages of dual-layer laser cladding.
This results from developing a high-speed, fully automated brake disc coating system for Stellantis.
The first in a series of robotic-driven Rapid Coating Process cells was presented during the Stellantis Factory Booster Day, held in Turin on September 18th.
By hard coating the raw brake discs with resilient steel and composite materials, the solution will enable Stellantis to significantly increase brake disc durability, reduce emissions pollution by up to 80%, and keep cycle times at a minimum.
This will allow the automotive manufacturer to fully comply with the Euro 7 standard, which requires a 27% reduction in particle emissions from brake discs by the end of 2026.

With a combined commitment to innovation that spans over 50 years, Comau and Prima Additive developed the robotic cell using a combination of advanced laser systems, high-speed robotic arms, additive manufacturing processes and safe powder management.
Furthermore, the full integration of Comau’s robotic arms with Siemens SINUMERIK Run MyRobot allows the industry-standard software platform to directly control the robotic arm without needing external or embedded robot controllers.
The modular system also allows maximum flexibility and productivity. Indeed, the cells are equipped with adjustable grippers that can handle different sizes of discs, from cars to trucks, to address evolving production mix scenarios.
Finally, besides being highly versatile and energy efficient, the solution is characterised by a reduced overall footprint.
Paolo Calefati, CEO of Prima Additive says “We believe that collaboration and innovation are the driving forces shaping the future of manufacturing.”
“Our collaboration with Comau joins two companies with deep expertise in their respective fields to develop a truly cutting-edge industrial solution in automation and advanced laser systems for material processing.
More importantly, the laser system developed for the brake disc coating application is one of the most profitable and sustainable cases of laser additive manufacturing/laser cladding technology applied in mass production for automotive.
This solution not only contributes to improving the performance of automotive brake discs but also plays a crucial role in promoting sustainability by reducing the overall environmental impact of motor vehicles.”
Pietro Gorlier, CEO of Comau says “This robotised solution represents a great example of innovation, led by two Italian companies who have developed advanced technologies to meet important sustainability targets.”
“In working together to automate high-speed laser cladding safely, Comau and Prima Additive are helping meet a growing demand in Europe and beyond for flexible, turn-key solutions that will help reduce particle emission pollution in response to recent regulations.
We’re confident there is significant market potential for this type of solution.”
The jointly developed Rapid Coating system is scheduled to be deployed at the Septfonds plant in France by the end of 2024, making Stellantis one of the first automakers to launch a fully automated line for the hard coating of brake discs in compliance with Euro 7 policy standards.
Research highlights impact of rising business costs
Recent research commissioned by Close Brothers Asset Finance has revealed the significant impact of rising costs on businesses across the UK, with a majority of respondents reporting adverse effects on their operations and financial health.
According to the research, 71% of businesses have been affected by the rising cost of doing business, while 25% reported no impact, and 5% were unsure.
Among those experiencing increased costs, 56% indicated that it has negatively impacted their cash flow.
Conversely, 27% reported no negative impact on cash flow, and 15% did not notice an increase in costs.
The survey also identified the top five primary inflationary cost pressures affecting businesses – in order of most impactful:
l Energy (gas, electricity)
l Supplier costs
l Fuel (petrol, diesel)
l Interest rates
l Rent
Additionally, 67% of businesses have seen their business insurance costs rise in the past 12 months, while 26% haven’t, and 7% are unsure.
In response to these increased costs, 24% of businesses have passed them on to customers completely, 61% partially, and 15% have not passed on any costs.
Regarding employee wages, 54% of businesses reported wage increases in the past six months, 34% did not, and 6% were unsure.
Anton Nebbe, Head of PR and Communications, and responsible for commissioning research at the firm says “These findings underscore the challenges faced by UK businesses in the current economic climate.
They highlight the need for strategic planning and support to navigate these pressures, and it’s clear the rising costs of doing business are presenting significant issues for many enterprises across the UK.”

“Our research highlights the critical areas where businesses are feeling the pinch, from energy and supplier costs to increased insurance premiums.
“At Close Brothers Asset Finance, we’re committed to providing the support and resources businesses need to navigate these pressures and continue to thrive.
By understanding these challenges, we can better assist our customers in developing strategies to mitigate these impacts and ensure long-term success.”
For more information please visit: closeassetfinance.co.uk
Stand and deliver: New industrial strategy must put the fizz back in UK manufacturing.
2024 was a mixed year, with some stellar announcements like Tata Group’s gigafactory investment offset by the cancellation of Phase 2 of HS2 and a budget black hole to pay for, but an Industrial Strategy may give the industry the long-term stability it needs.
This article is by Will Stirling
The Chancellor Rachel Reeves received a boost a week before her Autumn Budget when the IMF revised its forecast for UK growth this year to 1.1% (up from 0.7% in July) and 1.5% in 2025 – the biggest upward revision for any advanced country.
It’s a sign of better things to come, and 2024 was not a banner year in manufacturing, more one defined by steady stability, yet it still notched up a few memorable headlines for British industry.
Spiralling costs meant the previous Tory government cancelled Phase 2 of HS2 from Birmingham to Manchester, affecting hundreds of supply chain companies, which the new Labour government partly blamed for the cost overruns.
The Secretary of State for Transport Louise Haigh launched an independent review to ensure lessons will be learned and the costs for HS2 are controlled.
The cost of Phase 1, London to Birmingham, is expected to reach £66bn.
Covid and the semiconductor-shortage-affected UK automotive sector got a fillip in February when Agratas, the battery division of Tata Group, confirmed a new £4bn battery gigafactory in Somerset.
It was a relief for the car sector to see the UK stall on the global league table for gigafactory capacity, a key metric for car plant investment.
While carmaking recovered strongly in 2023 after semiconductor supply returned, it is slowing down.
By August, the UK had manufactured 522,833 cars, down 8.5% on production at the same point in 2023 when ythe figure was 571,671.
Interestingly, year-to-date vehicles for the domestic UK market had increased by 12%, but exports, representing over 84% of all car production, were down 13.6%.
The production of electric cars, including hybrids (EVs), fell by 26%.
Automotive business group SMMT said this decline is expected to be reversed in the longer term as new models come on stream.
Massive manufacturer discounting saved car sales in Europe in September, pushing BEV sales to 56,387 registrations.
Siemens opened its new train factory in Goole, Humberside, in October and announced a further £40m in addition to the £200 investment in the Goole Rail Village, which will now bring up to 1,000 new jobs to the region, as well as around 1,700 supply chain job opportunities.

In addition to maintaining the bogies from Siemens’ 572 trains running in the UK, it will also include new production lines for assembling bogies for new trains, which will be the first for Siemens in the UK.
Aerospace is battling delivery rate challenges: after Covid, orders poured in, and the industry is pulling on all levers to find ways to go above ‘Rate 60’ into the consistent 80s or even 90 aircraft per month to reduce long delivery times.
Ninety commercial aircraft were delivered in August, the highest in that month of the year since 2018.
But that’s not the whole story.
While the global backlog of aircraft on order is 15,651 planes according to the industry group ADS – an extraordinary number – aircraft orders in the year-to-date are two-thirds behind 2023 levels.
Perhaps it was a sign that Brexit was the past. The FA appointed Thomas Tuchel as the senior men’s coach, causing gossip as the first German coach of the England football team.
A week later, Britain and Germany signed a government-described “landmark’ defence agreement to boost security, investment, and jobs.
German defence giant Rheinmetall will build a new factory in the UK to make barrels for artillery guns, and German marine surveillance aircraft will supply patrols from RAF Lossiemouth.
The factory will need British steel and will create 400 jobs.
It’s the first defence pact with Germany of this scale, although both countries already collaborate on making armoured vehicles, for example.
In October, BAE Systems Maritime launched the sixth Astute class submarine, Agamemnon.
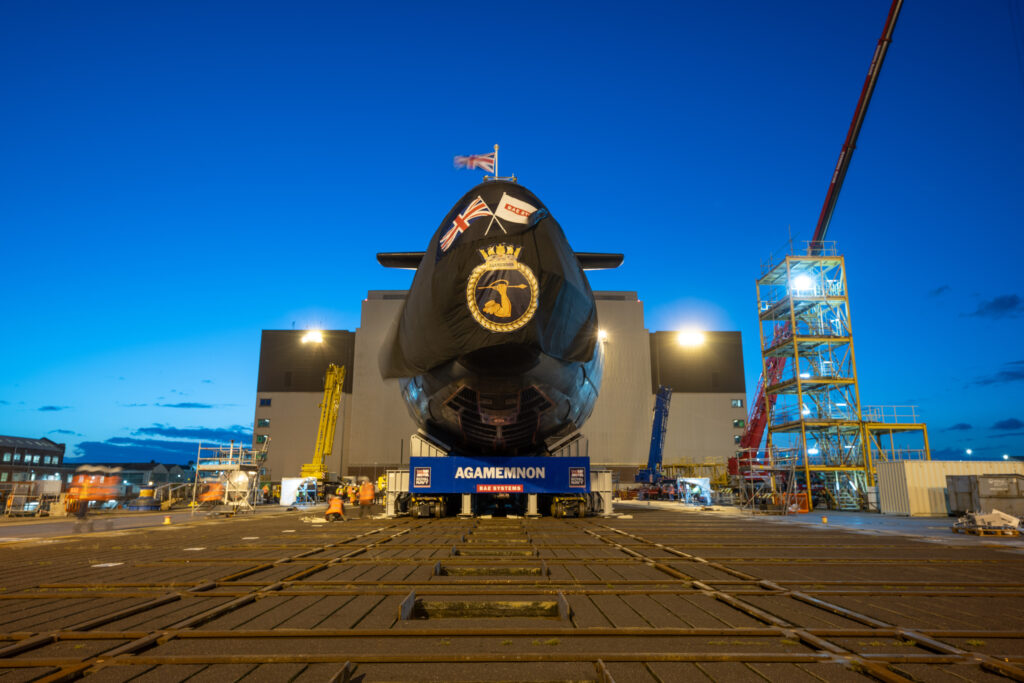
Attention will soon switch to the multi-billion AUKUS submarine (SSN-A) programme, where the boats will be built in the UK and Australia.
Fhaheen Khan, senior economist at Make UK says “Manufacturers this year experienced the most stable period of business conditions in almost a decade, despite still facing higher costs, tight interest rates and skills shortages.”
While it could be seen as a year of two halves – the first six months boasting strong production, order books and investment intentions, and the second looking far more mixed due to an inevitable domestic market slowdown –manufacturers remain buoyant in their expectations.” h
Accountants and business advisors are expecting more investment in the economy in 2025, following several years where major events and inflation have made business conditions that could be generally described as ‘sh*t’.
Fhaheen Khan thinks the new 10-year industrial strategy is an important milestone in achieving economic growth, although some seasoned business leaders will say they have heard it all before.
It’s hard to remember, but the UK has had at least four official industrial strategies since the 2008/9 recession: in 2009 (Mandelson), 2012 (Vince Cable), 2017 (Greg Clark) and now in 2024.
Khan says “It’s highly encouraging that advanced manufacturing will be a key sector driving that growth, and the Industrial Strategy Council will help lay the pipework needed to modernise UK industry through the wide adoption of AI, computing, and techniques like 3D printing.”
Of particular relevance to MTD readers, the numbers show that industries specialising in producing capital equipment like machinery, electronics and metal fabricators have experienced a positive year.
This is due to strong exports to the US and the EU as many Western countries are investing in the kit to modernise their manufacturing – for example, the US’s Inflation Reduction Act and, one could say, on the wave of ‘Make America Great Again’.
Khan says “These subsectors have much to look forward to in 2025 as economic conditions stabilise further, inflation cools, and interest rates are loosened.”
The manufacturing technology expo MACH 2024 organisers said visitors were up 6% on the previous show and reported a good vibe.
Greg Capp, sales director at EDM machinery firm Sodi-Tech, said: “Footfall has been the best in a long time. On Day One, we had enough enquiries for the next six months.”
Overall, investment in manufacturing in 2023 (last full year) is up by 4% on 2022, from £40.24bn to £41.8m, and economists expect this to rise in 2024.
Despite the numbers and late positivity, on the ground, some manufacturing machinery vendors and subcontractors report a frustrating year where the anticipated rush of orders failed to materialise.
That flat confidence from 2022-2023 seemed to be overspilled into the year’s first half.
Andrea Wilson at deep hole drilling and boring engineering company Hone-All Precision says
“2024 has been a challenging and varied year for most businesses.
“Uncertainty and political instability have created conditions that have not been beneficial to business and have created barriers to growth.
“The creation of the 10-year Industrial Strategy will hopefully give business and investors the confidence they have been lacking the last few years.”
The new industrial strategy focuses on eight sectors: advanced manufacturing, clean energy industries, creative industries, defence, digital and technologies, financial services, life sciences, and professional and business services.
High-tech, hard-tech, high-potential companies can benefit hugely from close government support.
The top two sectors in the strategy are advanced manufacturing and clean energy industries. “Tokamak Energy does both!” says David Kingham, the executive vice chairman and a co-founder.
He says that the company that designs, manufactures and operates a plant for nuclear fusion to generate power aims to accelerate the development of fusion energy, the most valuable technology of the 21st Century.
“We were delighted to see the new consultation on the Industrial Strategy. A company like Tokamak Energy, with over 250 employees and global ambitions, can grow rapidly if we have consistent strong backing from the government.”
The company has had spectacular success in recent years with the record-breaking ST40 high field compact spherical tokamak – which reached 100 million degrees Celsius plasma ion temperature, the threshold needed for commercial fusion energy.
Its high-temperature superconducting (HTS) magnet development has also set records for magnetic field strength at a temperature of 20,000C.
David says: “Our industrial strategy is to pursue fusion energy by assembling consortia around our core technologies to provide the complimentary capabilities necessary for the development and deployment of fusion.
This will require major investment by governments and consortium partners, but the prize is the elusive goal of commercial fusion energy.
The fastest achievable timeline for fusion is 10 years to a 50MW pilot plant, a goal set by the US Department of Energy milestone-driven fusion development program.
“So a bold, consistent industrial strategy from the Government could enable the UK to have its fusion “cake” in the long term and “eat” the economic benefits of the magnet spin-off technology in the short to medium term.”
In the supply chain, companies like Hone-All Precision want long-term stability, vision, and potential targeted support through programmes unafraid of ‘picking winners’ that have previously blighted attempts to assist the industry within state aid rules.
Managing Director Andrea Wilson says “The new Labour government must commit to long term strategic thinking and investment decisions, and the newly formed Industrial Council will hopefully achieve this.”
“The council’s success will be increased dramatically if it’s informed by business leaders, owners, and most importantly, if it includes SME representation.
The outcome of these two positive moves will hopefully result in us seeing the confidence and stability we all need to thrive.”
Machine tool and machinery suppliers need orders, and for that, their customers need confidence to buy.
Adrian Haller, managing director of Bruderer UK, a leading manufacturer of precision high-speed presses says “The UK has a fantastic opportunity in advanced engineering, and we have so many brilliant companies – at all levels of the supply chain – that are prospering despite the lack of a coherent Government strategy to support the sector.”
“This isn’t tubthumping; this is what we see every day when our sales engineers and installers commission precision high-speed Bruderer presses on shop floors across the country.
Imagine what we could do if we had a long-term Industrial Strategy that focuses on our strengths and invests in them?
And I don’t mean the odd grant here and there. It needs to be substantial and flow down to SMEs – that is the critical bit.
For industry to become more efficient, an area to improve is the education of manufacturing engineers about new, ‘smart’ technology.
Mark Weymouth, MD of PLUS Automation and UK representative for Contrinex and Satron, who runs a popular LinkedIn newsletter says “There’s a pervading tendency for engineers to buy and commission what they know and not look at new, better plant and equipment that can raise productivity.”
While PLUS Automation is in its fourth year of growth, many food and liquid process manufacturers are not explaining this technology to their site engineers.
He says “The UK is about seven years behind mainland Europe in adopting many process technologies.”
Although the increase in employers’ national insurance payments may dampen this optimism, the indicators are that this new strategy for industry will help businesses, especially those in advanced manufacturing areas.
The right direction of travel
Arnott Handling Equipment has invested in a multi-tasking lathe and bar feeder from Mills CNC to help automate its small-part processing operations. The acquisition by the precision conveyor system manufacturer will also improve productivity and process efficiencies.
The latest investment underscores the company’s commitment to continuous improvement and its business growth strategy that emphasises replacing older equipment and labour-intensive processes with sophisticated, multi-tasking technologies.

The Lynx 2600SY lathe with a FANUC CNC is a Y-axis sub-spindle variant with a Hydrafeed bar feeder installed at Arnott Handling’s facility in Brixworth. Since its installation, the Lynx 2600SY has machining a diverse range of high-precision, engineered components and accessories for the company’s UK-based conveyor and handling system customers.
Oliver Rippin, Arnott Handling’s Operations Director: “Our customers provide conveyor system solutions to end-users in the retail and e-fulfilment, warehouse and distribution, food, beverage, cosmetics, packaging, pharmaceutical and logistics industries.”
One of the main customers is sister company, Arnott Conveyors Ltd., a manufacturer of bespoke conveyor systems and turnkey solutions for customers.
Nick Howells, Commercial Director: “Sales for our handling and conveyor businesses have been upward. Consequently, we have invested in our people, plant and our processes to meet the increase in demand and achieve sustainable business growth.”
Arnott Handling regularly benchmarks and reviews its KPIs as part of its continuous improvement programme. The monitoring and evaluation process helps identify issues and potential ‘weaknesses’ that could affect future performance and profitability. At the beginning of 2024, the company’s existing machining capacity was under pressure because it won a new contract to supply a large volume of drums for conveyors.
Remembers Oliver Rippin: “The new drum contract brought machining capacity issues to the fore – specifically relating to machining our adjustable feet products.These feet, comprising two separately machined parts, required three different machining operations using two CNC machines to complete each component. The existing process was labour-intensive and required staff to be on hand continuously to perform part loading and unloading. Because the new drum contract would significantly eat into existing capacity and could cause production bottlenecks, we decided to streamline this process by investing in a new multi-axis lathe, with Y-axis and sub-spindle capabilities, to machine both the base and stem components of our adjustable feet.”

Having previously purchased a DN Solutions’ Puma GT 2600LM box guideway lathe from Mills CNC in 2021, the company was familiar with DN Solutions’.
“It was apparent that the machine’s sub-spindle, driven tooling, and Y-axis capabilities would enable us to machine our adjustable feet components in one set-up, removing the need to transfer parts between different machines.”
Furthermore, integrating a high-performance bar feeder, delivered to Arnott Handling as part of the investment package, would enable the company to create a flexible, high-productivity cell.
The machined materials vary according to the end application and include mild steels, stainless 314 and 316, aluminium, titanium and engineering plastics.
Machine cycle times are short (typically a couple of minutes for the base and stem components), and part tolerances and surface finish requirements can be tight. Since its installation, the Lynx 2600SY hasn’t missed a beat and is meeting its quality and productivity targets as intended.
The Lynx 2600SY features fast 30m/min rapids, a powerful 18.5kW high-torque spindle, and a 12-station servo-driven turret with 5,000rpm tooling capabilities. The Lynx 2600SY’s versatility is delivered, in part, via its integrated 6” chuck sub-spindle (4500rpm) and its +/-52.5mm Y-axis.
Six of the best
With 75% of its turning centres bought from Dugard Machine Tools, it’s safe to say that C&K Precision Engineers Ltd is reaping the rewards of working with the South Coast machine tool specialist.
The Stoke-on-Trent manufacturer is a subcontract machining, assembly and fabrication business serving the medical, aerospace, surveillance and general manufacturing sectors.
Working in these high-end segments, C&K Precision demands machine tools capable of delivering high-quality, tight-tolerance workpieces from the most challenging material grades.
Matthew Kelsall from C&K Precision Engineers says: “We moved to a new large facility in 2017, and since then, we have continually grown.
We’ve invested in new machines with a better working environment and aim always to increase productivity.

There is a skills shortage, and we are lucky to have a good team around us, but we have to maximise that with the most productive machines.”
This is why six of the company’s eight turning centres have been purchased from Dugard Machine Tools.
The second-generation business was founded in 1969 kand eeps returning to Dugard,
Matthew says: “One of the main things is reliability.

The first Dugard machine we bought has been with us for six years and has been remarkably reliable.
It’s a very robust and rigid machine with box guideways, and we need that as we machine many exotic materials – we have a lot of faith in the machine.”
The turning centres supplied by Dugard are all fitted with a Siemens CNC system.
“With a lot of machine tool manufacturers, if you want a machine built to order, it typically takes twelve months to wait, and we simply couldn’t wait for that.
Dugard had a machine in stock with many additional bells and whistles, such as a sub-spindle, that we never had before.
The success of that machine led us to buy two more machines. That’s because if something serves you well, you stick with what you know.”
“Since we purchased the first machine, we found that we could get more and more work through it, which eventually created a bottleneck.
We had to do something about the bottleneck, so we bought a second machine with a Y-axis last year.
We have now just had the third machine installed”.
As a turner operating four machines at C&K Precision Engineers, Matthew Gerrard says: “The machines are built extremely well, and they perform brilliantly on materials like inconel 625 and titanium – they fly through the material.
You can make massive cuts on the Dugard SMEC machines, whereas others can stall.
This is due to the really high quality and high specification motors and the box way construction.
We also love Siemens control as it is very user-friendly and has a lot of technical add-ons.
If we’re doing jobs out of titanium that may have just a 0.9mm wall thickness, the Dugard SMEC machines ensure that you don’t get any vibration.
Additionally, the machines have BMT65 toolholders that are very large and robust for heavy-duty cutting.”
“Looking at the first machine we bought with the Y-axis, it’s just so much more versatile and capable than our other machines.
We have other machines with live tooling, but the Dugard Y-axis is perfect for opening slots and counter-boring holes.
We were so impressed by the sub-spindle on the SMEC SL2500SY that we purchased a SMEC SL2500Y, which is an almost identical machine except for the sub-spindle.
We purchased this as we only needed one machine with the sub-spindle, but we still needed a machine with a Y-axis for doing one-off jobs.”
“We’ve just added a SMEC SL2000, and my son, who is just starting his apprenticeship, is on that machine.
It doesn’t have the live tooling facility, but it has a Siemens 828 CNC control and is perfect for learning.”
Matthew Kelsall says: “When you buy a machine, nobody wants to be stuck at the end of a phone talking to someone you’ve never spoken to before, but when you speak to Dugard, you have a great relationship that work well.”
KS Composites on FastTrack with hyperMILL
Embued in the motorsport industry from when Kelvin Smith opened the doors for business in 1985, KS Composites is a manufacturer with a pedigree of working with numerous F1, GT, Le Mans and BTCC teams. Throughout its history, Melton Mowbray-based KS Composites has worked at the very pinnacle of motorsport – and that is why the company has invested in CAD/CAM software from OPEN MIND Technologies.

Having formed many close relationships with some of the leading lights in design and consultancy through prototype and development projects, KS Composites offers design services, FEA, and CFD. This is complemented by a 48,000sq/ft manufacturing site that supports the design and consultancy services with everything from kit cutting, fitting and assembly to wet lay composites, autoclaves and ovens, a composite shop, machine shop and much more. Whether it’s the development of new lightweight wind turbines, the production of super-efficient alternative energy vehicles or the unique demands of the aviation and military industries, KS Composites approach all projects with the same enthusiasm and professionalism.
Dan Johnston, Business Development Manager at KS Composites: “A turnkey composite solution provider that offers a range of services, from engineering to 3D printing and CNC machining, as well as composite manufacturing. Each customer has an individual requirement that we really have to respond – everyone has nuances within their projects and programmes, and we need to be able to leverage every service we have to provide for our clients. Customers will initially come to us with a fully developed idea or just the genesis of an idea. What that journey looks like will depend on each client, but we can fundamentally take an idea, and our engineering division will deliver the solution. If someone has a blueprint for a project, we are agile and responsive enough to deliver on time.”
Discussing the relationship with OPEN MIND Technologies, Justin Tallboys-Cotton from OPEN MIND adds: “KS Composites came to us because of their needs, which are not only metallic but also composite machining. This encompasses everything from 3-axis vertical machines to complex 5-axis gantry-style machines. One thing that KS Composites liked about hyperMILL is that the licenses are very modular, so whilst they use our 5-axis licences that we are famed for worldwide, they don’t need all of it. So, KS Composites just chose the two or three modules that they needed in order to do their work. They know they can expand if needed, but they don’t need to invest in everything up front.”

Looking at a replica race car the company has manufactured, Dan Johnston adds: “On the vehicle itself, there is a multitude of things. We have carbon composite body panels and also machined, GRP and 3D printed elements. We are hitting on all our core services with this vehicle. One of the first things to come into our new building was CNC machines. At that point, we identified that we needed a CAM package that could get the most out of our machines. We went to the market and evaluated the options, and it was clear from the offset that hyperMILL was the obvious choice.”
Justin Tallboys-Cotton adds: “It makes me extremely proud to see how KS Composites are embracing the tools that we have within hyperMILL. For example, they colour-code their components and use bookmarks and templates. What this is giving them as a company is consistency throughout the process, especially when different guys’ program work in different ways. It also helps with time to market; KS Composites can reduce the programming time to a bare minimum, ultimately getting parts onto the machines quicker to keep their customers happy.”

In conclusion, Dan says: “hyperMILL is making our life so much easier, especially when we are making things like a show vehicle. We are representing the pinnacle of motorsport – it’s high-performance, high precision. So, when making the patterns for this vehicle, they had to be of the same quality – that is what we have achieved with hyperMILL.”
Spark of Innovation.
Anotronic Ltd is a well-recognised subcontract machining business and manufacturer of high-quality EDM fast-hole drilling and EDM die-sinking machine tools.
Founded in 1982, the Leighton Buzzard business started in ECM, ECD and EDM tooling and machining, evolving to the production and growth of its own ECM and ECD technology brand.
Along this journey, the company has worked with Sodi-Tech UK and the Sodick brand of machines.
Martin White, Managing Director of Anotronic Ltd, says: “My father started the business in 1982, and I joined the company in 1985.

We tend to machine a lot of difficult materials such as inconel, titanium, special stainless steel, and everything that is difficult to machine.
We take on the worst jobs because we can – and we have all the machines and processes in-house to do what we need.”
Over the years, Anotronic has continually expanded its factory footprint, services and range of machines.
This has resulted from an aggressive growth strategy, staff development, and investment in the latest machine tool technology.
The Bedfordshire manufacturer currently operates three Sodick machines, with the latest ALC600G Premium wire EDM with linear motor drive technology arriving recently.

The high-end plant list gives Anotronic the edge over its rivals.
The Sodick ALC600G Premium from Sodi-Tech UK, with its spacious X, Y and Z-axis of 600 by 400 by 500mm and the U and V-axis travel of 120 by 120mm, clearly gives the company an edge.
Martin recalls how Anotronic arrived at the ALC600G: “We always buy premium machines, and as the company has become more experienced, we always look to buy better machines.
This always comes down to reliability and the ability to run unmanned.
We have a Sodick AQ35L die sink machine that we’ve had for a very long time, and Sodi-Tech UK has looked after this machine for us for over 20 years.”
The reliability and performance of the Sodick AQ35L meant that when Anotronic was in the market for another EDM machine, it once again turned to the Sodick brand.
Martin says: “We bought a Sodick AG 600LH around seven years ago.
That machine enables us to do tool work up to 500mm high, which we regularly do.
We have a large bobbin on this machine, enabling us to run 70 to 80 hours unmanned.”
The remarkably high level of lights-out machining with the Sodick AG600LH and its incredible reliability persuaded Anotronic to invest in its latest EDM machine, the Sodick ALC600G Premium with linear motor drive technology.
“We bought this latest machine because we had a project with a sister part.
The project typically consists of 40 parts that would maybe take us three months to complete.
We suddenly had an order placed on us last year for 300 parts.
We couldn’t have done this without another machine, as we knew we would have had to have been machining 24 hours a day to get the parts done.”
Sodi-Tech UK Sales Manager Richard Bailey says: “Martin and Anotronic don’t just take on run-of-the-mill CNC jobs.
This company tackles the higher end of the industry and often the parts that companies don’t want to tackle themselves.
Anotronic looks at jobs from an application perspective rather than a ‘machining time’ point of view.
With the Sodick technology and the special characteristics within the machine, Anotronic can utilise this to run all of its applications and do jobs that are unique and out of the norm.
In this instance, the application that Martin has been working on requires some very steep angles.
The ALC600G Premium has very large U and V-axis travel, allowing the processing of tapered angles up to 45°.
So, when it comes to machining this part, it can be done in situ with the integration of a fourth and fifth axis.”
“Manufacturers can also use the on-board technology and IQ software system that brings Anotronic’s model into the machine and draws the profile on-board utilising the U and V-axis cutting technology.
The programme is generated, the parts machined, and the job is complete!”
“We’re using a very complex 4-axis programme to cut a rotary part with 45° slots in it.
The only way we could do that was to use the software we currently use and without it, we couldn’t manage to do the part.
So, we used the on-board software within the CNC control of the Sodick machine to create a 3D model and a tool path to cut the part.
This is machining at extreme angles.
We’re cutting at 45° and machining up to 40 to 50mm in the U and V-axis to create this particular part.
We also had to specify wide nozzles and wider guides to machine this part, and the ALC600G did a brilliant job.”
“I have been a Sodick user for 35 to 40 years, and the beauty of the Sodick machines is that you can jump straight into a point anywhere in the programme without editing the entire programme.
It makes things very easy as it is a powerful and user-friendly software system.
It has many benefits, such as the negative offsets – normally, you have to cut a comp on a machine, but with the Sodick, we can drive the comp the other way and cut the other side of the part using a negative value.
Most control systems would just throw that out, whereas the Sodick accepts it and gets the job done.”
“I was working 15 to 20 hours daily, which was too much. I wasn’t seeing my kids growing up, and something had to change, so we went down the automation route.
We have a great team that works very hard and helps us reach our common goal – we run a lot of machines with very few people through our application of automation.
Sodick is a very established brand, and they have a great customer base and exceptional knowledge with engineers who are really, really good.
I’ve known Peter at Sodi-Tech for over 35 years, and this relationship is based on our excellent support – it’s been a fantastic marriage between the two companies.”
Toolmaker invests in high-speed machining.
Based in the Ballymote Business Park in County Sligo, Mito Precision Engineering provides a toolroom service to manufacturers in the medical devices and automotive industries. The Irish manufacturer also produces jigs and fixtures for the medical and pharmaceutical sectors. The company now has 11 machine tools from Hurco.
Since Malachy Towey and Michael Taheny established the company in 2010, manufacturing capacity has steadily expanded and now encompasses surface grinding, wire and sink EDM, turning, and milling. The latter machines have mainly been sourced from the preferred supplier, Hurco.
Operating 11 Hurco CNC machining centres and two Hurco CNC lathes, Mito’s machine park ranges from early models of the compact VM10 milling centre to a TM8i turning centre purchased last year and the latest investment, a VMX42HSi vertical machining centre with 20,000rpm HSK63A spindle. The ease of programming, robustness and high power make Hurco machine tools ideal for manufacturing one-off, often complex parts in tool steels or stainless steel.

Mito now has three different model variations of the Hurco VMX42. Known as an industry workhorse, it is a one-metre X-axis machine with a generous 610mm Y-axis travel and the same in Z-axis with a table load capacity of 1,750kg, allowing the company to produce extensive mould tools.
Recent design enhancements mean that direct drives are provided in X, Y, and Z, and roller guideways are used on all axes for rigid dynamics. The machine cabinet has a full washdown and spindle coolant ring.
Mito provides customers with top-quality service, offering competitively priced tools, advice, and guidance. Having forged long-term relationships with customers of varying sizes from various industries, Mito has gained new business through personal recommendations. Attention to detail in the tools it supplies and ongoing investment in new machinery and technology underpin its success.
Automotive subby speeds-up productivity with Filtermist
One of the biggest challenges for any machine shop is workshop air quality and the impact coolant mist has on staff.
To stop coolant mist from impacting air quality in the workplace, Tooling 2000 Limited installed on-machine mist extraction systems from Filtermist.
In addition to COSHH compliant clean air, the Birmingham subcontract manufacturer is also benefitting in other less obvious ways….
Founded back in 1996, Tooling 2000 offers everything from prototyping and development to 5-axis laser cutting, CNC machining, precision tooling and presswork for marquee customers like Rolls-Royce, JLR, Aston Martin, Magna, Bentley and many others.
With a complete suite of Hurco CNC machines from the compact Hurco TM12i turning centre, and 3 and 5-axis VMX machines, to the large bed Hurco DCX42i, the company also invested in Filtermist extraction on its machines.
This has improved air quality and enhanced productivity too.
Senior Business Development Manager at Tooling 2000, Iain Bubb says: “To eliminate airborne particulate in our facility we installed Filtermist systems.
This enables us to take any atomised coolant out of the atmosphere inside the work enclosure immediately.
This then enables us to do two things. Firstly, it protects our workforce which is of paramount importance.
Secondly, it allows us to open the doors to our machine tools sooner which provides us with more machining uptime.”
With more machine shops employing high-speed machining and high-pressure coolant systems that deliver fluid to the cutting edge, airborne coolant mist is a significant and growing issue for manufacturers.
Iain says: “Before having the Filtermist systems, we would have to leave the machine tool doors closed for an extended period, giving any atomised cutting fluid time to settle within the machine.
The Filtermist system completely clears the enclosure of mist – this enables us to gain seconds on the production process and this helps our bottom line.”
If the doors of the machine tools are opened immediately after a cutting cycle with no mist extraction in place, the oil mist enters the air.
This creates an oily film on everything from the machines and the workstation to tools, the floor and anything else in the vicinity – causing a health and safety concern.
Iain says: “With the Filtermist system, we are removing all airborne particulates from the machine tool atmosphere.
This keeps the inside of the machine clean.
It also helps to remove the swarf as it does not stick to the tacky coolant that may be left on the machine bed, so it helps to keep the machines cleaner, and it helps with maintenance.”
Filtermist oil mist filters eliminate airborne particulate and subsequently the oily film from the machine tools, components and wider work area.
The machine-mounted Filtermist FX5002 draws oil into a perforated drum that rotates at high speed and causes the mist to coalesce.
Centrifugal force pushes the oil into the outer casing of the FX5002 where it drains back to the machine tool for re-use or collection.
Simultaneously, the clean air is passed through a secondary high-efficiency after-filter to remove submicron particles that may have passed through the unit.
Referring to the installation of the Filtermist technology, Iain says: “When we specify our machine tool purchases, we ask for the Filtermist system to be installed on the machines before delivery.
We are a family-owned business, and we take our investments very seriously.
So, when we specify a new machine, we want it delivered to specifications we require to support our business.”
With the Filtermist FX5002 mist extraction systems fitted to its range of Hurco machine tools, Tooling 2000 finds maintenance of the technology easy to manage.
Iain says: “We have a TPM (Total Productive Maintenance) System in place, so after a set number of hours of production the Filtermist filters are changed and cleaned with ease.
We take our employees’ welfare very seriously, so taking any ‘nasties’ out of the environment is very important to us.
Productivity is also very important to us as a business and that cascades down to the bottom line.
With the Filtermist technology we get more uptime from our machines and that gives us better productivity and profitability.”
Powerful lathe enables stainless broaching.
Architectural ironmongery manufacturer Instinct Hardware has recently invested in a host of equipment that includes an Italian-built Biglia bar-fed, twin-spindle lathe with a ± 45 mm Y-axis turret having and 15 driven tools.
Installed in the Stirchley factory where premium quality door knobs and handles, door stops, and accessories are manufactured, the latest turning centre was sourced in May 2024 from the Whitehouse Machine Tools.

The company supplied the machine as a turnkey package with a bar feeding unit and a gantry-type system for unloading components onto a conveyor.
This handling method was chosen to prevent damage to the components’ surface and preserve their aesthetic appearance.
Whitehouse also supplied programs and tooling for producing two key components and their prove-out in Kenilworth, plus comprehensive training.
Instinct Hardware products are either standard catalogue items or manufactured to bespoke designs and have been used in prestigious projects.

These include the ongoing refurbishment of Citibank UK’s London headquarters, Google’s new headquarters in King’s Cross, various London Underground stations, the recent renovation of Wembley Stadium and Liverpool FC’s modern training centre.
Until now, stainless steel has accounted for 80% of production, with the remainder mainly brass and bronze.
However, an increasing amount of aluminium is being processed due to its easy recyclability.
Director Nil Chohan says: “Since we moved to our current premises, we have been increasing our machining capacity to reduce our reliance on subcontractors.
All of our lever handles require a square hole to be broached.
This has always been done separately on a hydraulic press, as before the Biglia B 620 YS was installed, we did not have a rigid enough lathe.”
“We bought the Italian turning centre specifically because it can broach our stainless steel handles, which Whitehouse demonstrated before we committed to the machine.
So, we can now perform all operations in one hit rather than in five or six operations.
It significantly reduces scrap rate by avoiding repeated manual setups and greatly speeds manufacturing time, enabling us to fulfil our promise of a 10 to 14-day order turnaround.”
A case in point is machining a component assembled into a stainless steel, oval-profile, mitred lever handle.
It previously required six machining operations from turning on a 3-axis lathe, milling and drilling on a VMC, broaching on a hydraulic press, further prismatic machining on a different VMC, slotting on yet another VMC and mitring on a bandsaw before welding.
This consumed 15 minutes of machining time plus 10 minutes of handling and setup for each of the five additional operations.
On the Biglia, the part comes off complete in 8.5 minutes, representing an eight-fold time saving, with the added benefit of eliminating work-in-progress and the potential damage to components.
Nil Chohan needed a robust and powerful machine capable of broaching stainless steel, he was impressed by the specification of the B 620 YS, particularly the 30kW direct-drive, liquid-cooled main spindle motor offering 700Nm of torque.
The lathe has boxways in the X and Y axes to promote rigidity and accurate machining, with a linear guide rail in the Z-axis for traverse speed.
He says: “Reputation is hard to establish but even more challenging.
Through hard work and endeavour, we have become a leading European manufacturer of bespoke architectural ironmongery.
Today, our team is committed to continued investment and further developing our range and brand with an increased focus on sustainability of materials and logistics.
We are constantly looking at new machinery like the Biglia to develop and enhance our offering whilst maintaining our passion to continue driving the company and our industry forward.”
Hexagon and SEAT S.A. partner in digital transformation.
Hexagon, a world leader in digital reality solutions that combine sensors, software and autonomous technologies, has expanded its collaboration with the automotive manufacturer SEAT S.A.
The deal builds upon a 25-year partnership working with Hexagon’s Manufacturing Intelligence division.
The companies have signed a strategic agreement that aims to deepen the digital transformation of SEAT S.A, focusing on the digitalisation of vehicle components, the management of digitised information and advanced process simulation.
This agreement will enable SEAT S.A. to optimise production and make decisions on process adjustments in real-time.
Hexagon has successfully implemented SEAT S.A.’s measurement and quality control systems.
Through the extended collaboration, the team will integrate a digital twin that applies metrology data with process simulations to predict outcomes and improve efficiency.
The solution will use systems to digitise the car body and its components, manage their data and provide reports and analytics to drive efficiency and reduce costs.

The collaboration is based on three fundamental pillars: the digitalisation of the vehicle’s manufactured parts, the management of digitised information and the simulation of processes.
Under the new agreement, Hexagon’s PRESTO system will fully automate the high-precision 3D laser scanning of the entire body with high-speed robotic inspection.
The second pillar is managing digitised information, which uses Hexagon’s eMMA data management, quality planning and analytics platform.
This automatically captures metrology data and manages it in a standardised way.
The centralisation of all 3D measurement data captured during the digitalisation process facilitates informed and efficient decision-making, allowing SEAT S.A.’s production and quality managers to monitor the condition of the parts and optimise quality in all assembly phases.
The third key aspect is process simulation, which allows SEAT S.A.’s quality analysts to accurately predict problems and optimise critical vehicle manufacturing processes such as part alignment, assembly and subsequent welding operations.
Thanks to Hexagon’s simulation solutions, SEAT S.A. can optimise production and adjust the production settings using a virtual prototype of the product, speeding up the process of fine-tuning production methods used in series manufacturing.
This capability translates into a significant reduction in costs, a reduction in material waste, and an improvement in time-to-market for the new vehicle models.
Josh Weiss, president of Hexagon’s Manufacturing Intelligence division, says: “We’re committed to helping SEAT S.A. stay at the forefront of the automotive industry by implementing innovative digital processes that transform agility in manufacturing and take control of quality from the start.
By combining technologies such as automated quality inspection, connected quality workflows and virtual manufacturing, SEAT S.A. can supervise each production stage with significant savings in time, material waste and costs”.
Daniel Cortina, Director of Quality at SEAT says: “At SEAT we are at a time of unprecedented transformation for our company towards smarter, more connected and efficient production, which involves the digital transformation of our production processes.
Now, we’ll acquire data about the quality of our parts faster and more accurately, and will also be able to improve manufacturing performance with them.
This predictive approach to quality allows us to improve our customer satisfaction and significantly reduce the materials used in the manufacturing process, reinforcing our commitment to sustainability.”
Quickgrind slots into production at TSP
Founded in 1945, TSP Engineering was primarily established to serve the iron and steel industries by manufacturing mining machinery, mine cars and ingot moulds. Now, the company located on Britain’s Energy Coast in Workington delivers high-quality, innovative heavy engineering solutions to nuclear, oil and gas, defence, renewable energy and construction sectors. The company recently encountered a challenge with one of its nuclear and reactor engineering customers – this led the company to find its solution from Quickgrind.

With a colossal shop floor of 20,000m², TSP has the facilities to handle some of the biggest engineering and steel fabrication projects in the UK and beyond – but when it came to finding the right cutting tool solution, the company opted for a solution from the Tewkesbury based cutting tool experts.
TSP was met with a nuclear reactor challenge and what drew the company to Quickgrind was its ability to offer non-standard length carbide tooling that won’t be found in catalogues or brochures. During an initial consultation, Lewis Straughton, the Production Manager of TSP Engineering, revealed the company had always had a problem finish milling slots because the tools could never push to the required length.
In the past, TSP had tried high-speed steel end mills with flute lengths upwards of 220mm. However, they had issues achieving the required tolerances. To overcome this, TSP reverted to the chain boring method. The critical nuclear components required slots machined to a tolerance of +/-0.1mm at depths of 220mm. However, the existing tools were witnessing pushing-off problems as well as creating spindle issues. This was not acceptable for the machining of high-value components. Retaining the in-house machining of the £2.5m contract was of paramount importance for TSP and risking the scrapping and re-working of components worth more than £500,000 was not an option.
After partnering with Quickgrind, the two companies worked closely to develop a cutting tool solution and a suitable machining strategy that could finish the slots to the high surface finish and tolerance requirements.
By adopting a specialist solid carbide end mill from Quickgrind with a new toolholder, TSP could achieve the required surface finishes and tolerances whilst the exceptional quality of the Quickgrind tools delivered consistently high performance and service life. As a manufacturer that has immense pride in its quality and certifications, TSP is ISO: 9001, ISO: 3834 Part 2, ISO: 1090 at execution level 4, ISO: 14001 and ISO: 45001 certified. The company also claims to be the first in the world to achieve the ISO: 19443 standard.
Not only did the Quickgrind long flute end mills resolve the issues of meeting the tight tolerances, evacuating swarf from the deep slots and eliminating the spindle issue – the tools also delivered astounding cycle time savings. The Quickgrind end mills reduced the 260-hour cycle time to just 16 hours, yielding cycle time reductions of 244 hours per component.


Be QUICK in turning operations
Many people regard the lathe as the forerunner of modern machine tools. Its introduction which made turning operations possible, marked the dawn of machining. Today, turning is still one of the most commonly used machining processes, and lathes remain a substantial part of global machine tool sales. This is why turning tools make up a considerable portion of the product range for leading cutting tool manufacturers.
It is not surprising that LOGIQUICK, ISCAR’s latest campaign, brings new developments to the market with a significant focus on innovation in the field of turning. Some of the newly introduced products extend the existing families within ISCAR’s turning line, while others offer solutions for advanced manufacturing. Such novelties not only reflect the trends of modern metal cutting but also aim to enhance the profitability of machining operations, particularly in turning.
Several key features characterise the development directions in turning tools and this includes the following:
• Higher Efficiency and Precision: This involves turning tools that can enhance productivity and precision, accelerate the overall machining process and minimise waste.
• Advanced Cutting Materials and Progressive Coating Methods: Cutting-edge materials such as ceramics and cubic boron nitride (CBN) are becoming more common in turning tools. Through excellent heat resistance and durability, these extra-hard materials offer superior cutting speed when compared to traditional tungsten carbide. Concurrently, the need for rapid metal removal is driving interest in progressive coating technologies for cemented carbides. Innovative coatings can enhance cutting capabilities, extend tool life, and reduce wear.
• Multi-Directional Turning Tools: These high-quality, versatile tools not only increase productivity and machining efficiency by reducing the number of tool changes but also minimise tool inventory, decrease machine downtime and maintain tighter tolerances.
• Digitalisation: The Industry 4.0 approach underscores the importance of a turning tool’s digital impact as an integral part of smart manufacturing.
• Sustainability: Given the pressing nature of environmental issues, there is a growing demand for cutting tools that have a smaller environmental impact. This means they should be less energy-intensive and generate less waste.
With the above in mind, the new products in ISCAR’s turning tool line that are part of the LOGIQUICK campaign accommodate these criteria. Indeed, turning encompasses many external and internal machining applications, including longitudinal turning, facing, profiling, chamfering, grooving, parting and boring. Let’s study ISCAR’s most recent turning advancements and highlight their features.
Advanced Cutting Material to Boost Turning Efficiency
ISCAR has significantly broadened the range of available ceramic grades for ISO-standard turning inserts. The recent additions to the range have been designed to facilitate efficient machining of difficult-to-cut materials, particularly hard steel and cast iron (ISO H group of application). The newly introduced IC1017 carbide grade was specifically developed for machining challenging nickel-based superalloys. This complementary grade features a high-hardness submicron substrate and a PVD coating to enable turning superalloys at higher speeds. For cutting non-ferrous materials such as aluminium, copper, platinum, bronze, brass, and others (ISO N group of application). The product range has been enhanced with new turning and grooving inserts featuring a nano-composite diamond-like coating (DLC).
Multi-Directional Benefits
QUICK-T-LOCK is an innovative tool family designed for productive multi-directional cutting. This includes front and back turning, profiling, and facing operations, all achievable with just one tool. The family uses a new insert-clamping concept to provide exceptional stability during machining at extremely high feed

rates. A notable feature is the advanced chipformer, specially designed for high-feed turning, especially in backworking machining (Fig. 1).
V-shape CUT-V-GRIP inserts offer a versatile solution for bi-directional external turning operations. The inserts, suitable for installation on modified existing holders, are capable of entering narrow machining areas where common V-type ISO inserts cannot be used (Fig.2).

The Boring Line
When boring with a long overhang (usually more than five times bore diameters), vibration is a common issue. These vibrations can affect surface finish, reduce tool life, increase power consumption and limit performance. While changing cutting conditions is a typical method to reduce vibrations, it may not always be the best solution, as it can result in longer machining time. However, a new anti-vibration holder with an active vibration-damping mechanism offers an alternative approach to overcome this challenge. It enables a high level of productivity in various boring operations, from rough to finish.
ISCAR’s PICCO is a tool system primarily designed for machining small parts. This versatile system, which can be applied to a wide range of turning, boring, threading and drilling operations, is highly popular in workshops that manufacture various miniature components. A typical PICCO tool consists of a holder and a solid carbide cutting insert secured within the holder. The system has now evolved with the introduction of PICCO-INDEX, a family of steel and carbide boring bars designed to be mounted on existing

toolholders. The bars are specially engineered to carry small ISO-standard indexable inserts (Fig. 3). The new addition offers a viable cost-effective alternative, particularly for rough and semi-finish operations for compact part production.
Swiss-Type
CNC Swiss-Type turning centres play a crucial role in modern manufacturing due to their precision, efficiency and ability to perform multiple operations simultaneously, such as drilling, milling, turning and knurling. They are instrumental in the production of miniature components required in several industries. This includes watchmaking, medical devices, automation equipment and electronics. Consequently, the development of more advanced cutting tools and toolholders dedicated to Swiss-Type lathes is a top priority for most tool manufacturers, including ISCAR. The LOGIQUICK campaign has also highlighted Swiss-Type machining tools.

The new modular system, QUICKSWISS, provides a solution for most applications on the sub-spindle of Swiss-Type lathes. This system (Fig. 4), which features a height adjustment option, offers a wide variety of bases, holders, and heads for various turning operations.
For grooving, parting, and recessing, the QUICK-2-CUT family shows promise. The tools in this family carry high-precision, narrow, double-sided inserts which are tangentially mounted on the tool from the side. The insert clamping concept ensures high rigidity and excellent dimensional repeatability. The targeted coolant, directed to the cutting zone, improves tool life and contributes to a better surface finish (Fig. 5).
The LOGIQ-4-TURN family of turning tools with indexable double-sided inserts has been well-received in the market. In response to this positive feedback, the company has expanded the family range to include smaller-sized inserts, providing a cost-effective solution for Swiss-Type and compact lathes.
In ISCAR’s electronic catalogue, two new filter search options specifically related to Swiss-Type lathes have been added. These options allow for the search of modular adaptations to find more efficient tools for main and back tool posts.
The LOGIQUICK campaign’s turning package encompasses far more than the products currently under consideration. The company is gradually introducing new product families in quick succession and plans to allocate more time to analysing these new arrivals. Will they boost productivity and contribute to a rapid increase in customer profitability? ISCAR firmly believes the answer is a resounding ‘yes’.
CERATIZIT puts Alitech in pole-position
Based in Silverstone, a short walk from the world-famous race circuit, Alitech Precision is a subcontract design, concept delivery and manufacturing company that specialises in the motorsport industry. To serve this demanding market, Alitech has invested in high-end machine tools, CAM software and cutting tools from CERATIZIT.
Alitech opened its doors for business in 2014 with a 3-axis machining centre and CAM package. As the business evolved, it moved to fully simultaneous 5-axis VMCs. Specialising in the design of motorsport solutions and taking concepts through to manufacture, the company works with everything from high-performance road cars to F1 teams in the ‘motorsport valley’. With high-precision and lightning-fast turnaround times a customer pre-requisite, Alitech demands the same from its suppliers – that is why the company relies on CERATIZIT for its cutting tool solutions.

Looking at how the company has grown since its inception, Alitech Precision Parts Ltd Managing Director Darren Cudd says: “We started with conventional entry-level machines and as we got into 5-axis machining, we quickly realised you get what you pay for. We haven’t looked back since we bought our first Hermle machine and we now have four with a fifth machine on order.”
Discussing CERATIZIT, Darren adds: “The relationship with CERATIZIT is not too different to what we have with our customers. We manufacture parts to a very high level and we need very good tooling to do that, especially some of the more specialised tools like long gun drills and bespoke cutters. We work closely with Nev, our CERATIZIT engineer, and we have an ongoing unofficial competition. If Nev gives me a number regarding machining parameters – I always have to try and beat it. Luckily, we know that our machines are more than capable of doing what Nev suggests, so we always try to push as hard as we can.”
The Northamptonshire company machines a diverse range of materials and CERATIZIT is always on hand to meet any challenge. As Darren says: “We are on board with a lot of racing teams and this has changed the nature of our machining. For example, our pallet-loaded Hermle C22 UP machine spent 4.5 months straight, just cutting titanium through the winter rush. It’s been a fantastic learning curve and Nev has been there all the way recommending the right tools. We got dialled-in on speeds and feeds pretty quickly and we are getting excellent tool life, which has been above what we were expecting to see.”
As a forward-thinking company, Alitech is happy to sacrifice tool longevity for productivity rates. Commenting on this, Darren says: “Being in the motorsport industry, parts are often required in less than 24 hours, so we are always looking at the bottom line. The hourly rate of the machine is typically more than the cost of the tool cutting the part. So, it’s simple math – if we’re going to blow two tools to make a job in half an hour instead of 1.5 hours, it’s a simple equation. However, the quality and longevity of the CERATIZIT tools always go beyond our expectations.”

Looking at specific tools, Darren highlights the performance of the CERATIZIT 3-flute rippers, saying: “We have some large parts that are roughed on a 3-axis before 5-axis machining. The roughing cycle was around 4 hours and this is now down to less than 1.5 hours. This is credit to the length of the flute and how hard you can push the CERATIZIT rippers. We now find that we are limited by the power of the spindle rather than the tools.”
As a company that operates around the clock, Alitech has invested in a CERATIZIT ToolSupply vending to ensure that production is always running. Darren says: “The vending has been a ‘game changer’. We can be running automated manufacturing on our 18 pallet machine and we may have 5 or 6 sister tools for each tool on that job. Even if we pre-order tools on what we think we will need, things don’t always work out as you wish. It is here that the vending machine comes in as a safety net to make sure our machines are always running – its removed tool breakages as a ‘failure mode’ from our business.”

It is often said that Centro-P or ER32 toolholders are not suitable for rough machining, Alitech has not only debunked the myth, but taken it a step further – applying Weldon Lock toolholders from CERATIZIT to eliminate tool ‘pull-out’. Darren suggests: “Traditionally, you look at two factors when roughing. Firstly, can the spindle turn the tool, and secondly, will the tool take the stress before it breaks? We found the limits on both factors. We were pushing so hard that a third concern arose – are you pulling the tool out of the collet during machining? Centro-P’s are fantastic but when you lean on them as hard as we do, they can pull out of the machine. To overcome this, Nev recommended the CERATIZIT Weldon shank collets. They drop straight into the Centro-P, lock onto the Weldon shank and we have achieved some pretty ludicrous numbers on how hard we can rough machine jobs.”
“We also use the CERATIZIT shrink-fit system for machining the large complex jobs that other machine shops will shy away from. This includes jobs like engine blocks where we need very long series heat shrink holders to reach ludicrous angles and depths.”

CERATIZIT tooling now accounts for 95% of the tooling supplied at Alitech. Recalling the incremental switch from a multitude of suppliers, Darren recalls: “Time is money and we are often here six or seven days a week. In the busy seasons, we really don’t have a spare hour to call around cutting tool companies for products and support. The CERATIZIT website and App just make it so easy to jump on, find exactly what you want within two or three minutes, click ‘buy’ and it’s here the very next day. CERATIZIT really is a ‘one-stop-shop’ and we now buy everything from end mills and ball nose cutters to specialist titanium drills, long gun drills, T-slot cutters, collets, shrink fit and much more.”
Adding to this, Sales & Production Manager at Alitech Ben Philips comments: “When I joined Alitech, we were predominantly buying Centric-P’s and heat shrink holders for HSK and BT40 machines, but CERATIZIT helped us to diversify from primarily aluminium machining to heavier metals and superalloys.”
Looking to the future, Darren concludes: “We cannot get another ounce of machinery into our factory, so we have been holding off for the last year or two to try and make a big leap. We will make this huge leap to a site that would be five times larger than what we currently have, from 3,500 to 14,000sq/ft. As we evolve, our success will be reliant upon the strong relationships we have with both our customers and our supply chain partners like CERATIZIT.”
Going for sustainable growth
Barrs Court Engineering has recently invested in a new DN Solutions’ DNM 6700 vertical machining centre from Mills CNC to increase its in-house milling capacity and capability.
The Hertfordshire precision subcontract specialist has acquired a DN Solutions’ Siemens 828D controlled DNM 6700 at the company’s 11,500sq/ft facility in Rotherwas in June 2024. It is being used to machine complex parts in low volumes for a range of customers in the marine, renewables, nuclear, steam, automotive and yellow goods sectors. The DNM 6700 is also being used to finish machine fabricated parts prior to assembly.
Barrs Court Engineering, established in 1983, regularly invests in new, advanced machine tools as part of a rolling, company-wide continuous improvement programme to increase productivity, performance and process efficiencies across all of its machining operations, and is no stranger to technologies supplied by Mills CNC.
In 2001, Barrs Court Engineering invested in its first Doosan lathe, a Puma 300 and it has also acquired a sub-spindle, Y-axis turning centre from Mills CNC to strengthen its in-house turning capacity and capabilities. The DNM 6700 is, however, the first milling machine the company has acquired from Mills in its 41-year history.

Almost 12 months ago, Barrs Court Engineering began a strategic process of rationalising and streamlining its business by creating three discrete machining areas in its machine shop – each one focused on a specific production model designed to meet different customers’ machining needs and requirements.
Explains Toby Kinnaird, Barrs Court Engineering’s managing director: “The new manufacturing strategy is focused on growth, and has imposed a discipline across all our planning and production operations. We analysed our existing business, including what our customers expected and demanded from us and identified three different production ‘models’ which would direct how we would organise our machine shop and manufacturing operations.”
Barrs Court Engineering has at its disposal several dedicated machine tools with integrated automation for its low mix high-volume manufacturing operation which is predictable and is characterised by ‘scheduled’ repeat business. Manufacturing bespoke, high-quality components in small batches has always been a particular strength of Barrs Court Engineering, and is perceived as a high growth area for the company.
Often requiring a ‘turnkey’ approach with machined parts characterised by their high precision, complexity and long cycle times, the company specifically acquired the new DNM 6700 machining centre to strengthen its performance in this high-value production area.
“To increase our high-mix low volume machining capacity, we decided to invest in a new high-performance machining centre to replace two of our older machines that had limited capacity”, remembers Toby Kinnaird.
“We were particularly looking for a machine with a larger X-axis to handle bigger parts which had been out of our reach.”
Barrs Court Engineering compiled a ‘must have’ technical checklist for its future machining centre investment and visited the MACH 2024 Show in April to identify a suitable machine. Continues Toby Kinnaird: “We visited Mills CNC’s stand on the first day of the show, and discussed our requirements with their sales staff. They provided details on the DNM 6700 that was in stock at their Leamington facility and would be available for immediate delivery. After a short while negotiating the deal, we placed the order for the machine later that week.”
The model acquired by Barrs Court Engineering is equipped with the 828D Siemens control with ShopMill software and features an 18.5kW directly-coupled spindle, a 1500mm x 670mm worktable and a 40-tool position ATC.
Says Toby Kinnaird: “Our new DNM 6700 is powerful, fast, accurate and flexible. The Siemens Control is intuitive and easy to use, making programming and job setups quicker and more accurate. The integration of the 4th-axis table enables us to machine complex parts with intricate features in a single setup, avoiding the time and cost involved in re-fixturing operations and the potential for losing accuracy, and the inclusion of Renishaw workpieces and tool probes improves process efficiencies.
Seeing clearly with Filtermist
As a leading manufacturer of steel windows, Crittall Windows manufactures bespoke windows, doors and screens that range from residential and commercial applications to architecturally significant historical buildings. With a history that dates back to 1849, the Essex company applies the latest manufacturing technologies. In the new machining department, the FX Series of compact oil mist collection systems from Filtermist has made a dramatic impact.
Crittall’s fascinating history includes producing windows for the fateful Titanic, munitions during World War 1 and prefabricated truss bridges for World War 2.
The Witham-based manufacturer has implemented a series of modernisation strategies to upgrade its machining division. Discussing this, Darren Joyce, Production Director at Crittall Windows says: “We cut the steel, machine it, weld it, galvanise it, powder coat and ship our products around the world. We are having a transitional period to more modern and flexible CNC machining to deal with one-offs a lot easier.”
One issue the company recognised from transitioning to CNC machining was coolant mist and fumes from the machine tools. This is where Filtermist stepped in. Darren continues: “Machining needs a lot of coolant and this gave us an issue with fumes. We rapidly found the factory starting to mist up. This wasn’t a good workplace environment and there was far too much coolant on our parts which are being welded further downstream –creating even more fumes.”
“We wanted to revise the way we work with coolant and cutting fluid on our machines. We needed to find something that would take the oil out of the air. If we could take the oil out of the air inside the machines, then when the machine doors open, you don’t get puffs of oil-laden air.”

Alluding to how the company started working with Filtermist, Darren recalls: “We did a lot of investigation work and we spoke to a lot of machinery manufacturers, which brought us to Filtermist. Filtermist effectively manufacture what is a drum that centrifugally spins and removes the oil out of the air and filters it out. We have now installed them in all of our CNC machining centres. The Filtermist FX5002 unit successfully spins the oil out of the air, but we have modified further, so we are recycling the oil and using it on our flood-based coolant machines, extending the service life of the oil.”
Crittall has gone from not knowing the Filtermist brand to having 12 of its FX5002 units installed in less than a year. Furthermore, Crittall has specified the Filtermist units with an F Monitor 2 that gives customers live readings of the Filtermist systems’ efficiency level.
Commenting upon the evident changes to the working environment at Crittall, Darren continues: “Not long after installation, we could see the difference. We could see the mist clouds dissipating. The health & safety and well-being of employees have always been our number one priority. In a steel window plant where you also have welding operations and pre-treatment processes, there are evidently fumes, so we have large extraction facilities to manage this. However, the localised filtration of oil out of the air was so important – its where we have seen the biggest improvement.”
Of course, the Filtermist systems can add so much more than an improvement to the working environment. Commenting upon this, Darren concludes: “We have also found economic benefits from the Filtermist systems. We take the oil from the Filtermist systems, recycle and use it on other machines – coolants and cutting fluids are not cheap, especially as we have moved to a water-based coolant as opposed to an oil-based coolant. We have also cut down on our oil consumption and expenses. Additionally, the Filtermist filters are cutting in and out to coordinate with our machine usage as opposed to constantly running like extraction units, so we are also seeing energy savings. All of this really does make the Filtermist extraction systems a ‘no-brainer’.”
Quaser fits the bill for Beechwood
As a family-run business that started trading from a small unit near Blackpool town centre, Beechwood Engineering Ltd has evolved into a major local manufacturer with a capital investment of more than £1m in the last 12 months. Part of this acquisition trail has seen the company invest in a Quaser MV184EH machining centre from the Engineering Technology Group (ETG).
Founded in 1977 and now managed by the third generation of the family, Beechwood is predominantly a 5-axis machine shop with ambitions of implementing automation throughout the shop floor. Despite manufacturing everything from simple to complex 5-axis parts for the F1, nuclear, offshore and food industries, the company that is now located in Poulton-le-Fylde needed a 3-axis VMC with a Heidenhain CNC control unit – ETG answered the call, delivering the Quaser in August 2023.
Labelling itself as a ‘one-stop-shop’ for machined components, Beechwood has a plethora of high-end machine tools. As Managing Director at Beechwood Engineering Ltd, Stewart Churchill summarises: “We produce everything from one-offs to batch runs in the thousands, machining materials from plastics to exotics. Whilst the majority of our machining is complex 5-axis work, we do machine quite a lot of jigs, fixtures and parts that do not warrant 5-axis machining – for this we wanted a new 3-axis machine to replace an older machine as part of our continuous improvement programme.”
With Heidenhain CNC control systems on its machining centres throughout the machine shop, Beechwood wanted a 3-axis Heidenhain-controlled VMC with a rapid delivery time that could fit into the floor area of an ageing outgoing 3-axis machine. As Stewart continues: “We have bought machines from ETG down the years and one of those machines was a Quaser MV204CPL machining centre that we bought back in 2012. Whilst that machine has since been moved on, we were very impressed with its performance, rigidity, stability and reliability. So, when it came to buying a new 3-axis VMC, we didn’t have to look any further than ETG.”

The 23-employee ISO: 9001 certified manufacturer still has other machines on its shopfloor from ETG such as a Nakamura-Tome NTRX-300 multi-axis turning centre, so it is fully aware of the quality and service from ETG – both factors in the latest acquisition. As Stewart adds: “The Quaser MV184EH has been brought in to replace an older 3-axis machine that needed to be upgraded. The key drivers in installing the new Quaser were an updated and more productive platform for programming, setting up jobs and holding tight tolerances. Since the machine was installed, it has been running day and night shifts, machining parts such as complex jigs and fixtures as well as valves, plates and other more simplistic parts for the oil & gas industry. This has alleviated capacity from our 5-axis machines whilst adding the production efficiency we need with maximum machine uptime.”
As standard, the Quaser MV184 has a spacious 1,200 by 600mm bed with X, Y and Z-axis travel of 1020 by 610 by 610mm with BT40 taper spindle options from 9,000rpm to 24,000rpm. From an optional extra perspective, the Quaser MV184 is available with 30, 48 or 60-position ATC, spindle oil chiller, BBT spindle attachment, 4th axis preparation, linear encoders, tool and workpiece probing, a choice of high-pressure coolant systems, filtration unit, oil mist collector and much more.
Concluding on the latest addition to the company’s plant list, Stewart says: “ETG has always been a supplier we can rely on with their choice of high-quality machine tools that are backed by exceptional service and support. The Quaser has been bought to specifically fill a position on our shop floor, which is to alleviate capacity from our 5-axis machines and provide a fast turnaround service for some of our simple work. The machine is more than fulfilling this role – and it is doing so with reliability, precision, quality and consistency. Consistently long-running machine hours were a challenge for us on ageing machines before we bought the Quaser. In the future, this machine will also fill the role of being a training machine for our apprentices – and I couldn’t think of a better machine to train the next generation of engineers on.”
‘The Beast’ devours everything placed before it
Many subcontract manufacturers have the challenge of knowing which machines to purchase to suit the diversity of work that comes through the door. For other businesses, it’s development and growth that dictate the purchasing decisions. For Ian Gibson, Managing Director of Vision Precision Engineering, the latter scenario led to investments in XYZ machine tools. Starting the business with his uncle, Dennis, they set about finding work – a significant challenge.
Using existing contacts, they found an unlikely source of work making parts for coffee machines in Costa Coffee stores. “We were approached to make improvements to the in-store machines so that the baristas could not make mistakes in loading the cleaning products used in the machines,” says Mr. Gibson. This influx of work prompted the business to seek improvements in their manufacturing processes, leading them to XYZ for a solution to make parts faster than on their traditional milling machine. Mr Gibson continues: “Steve Cox, the XYZ Area Salesman regularly called in and, when the company needed to invest in new equipment, he helped select the right machine which was an XYZ 710 vertical machining centre complete with a 4th axis.”
This investment created a new dilemma as making parts faster created a bottleneck in the secondary operations. This led to further investment in a smaller machining centre from XYZ to handle the increase in demand.
“Even with two machines and 4th axis fitted to the mill, we were still falling behind in supplying parts to our customers so again we contacted XYZ to see how we could improve our manufacturing further,” comments Mr. Gibson. The answer was to invest in an XYZ TC 320 LTY-driven tool lathe. “The ability to produce milled and drilled features on our turned parts was taking up capacity on the original mill, so it made sense to purchase a machine that could produce our parts in one hit which is why we decided to invest in the TC 320 LTY.”
With the hardened box way-built machine with its Y and C-axis, along with driven tool capability in place, Vision Precision set about getting the most out of its latest purchase. “Now we have this machine available to us, we have been able to quote for work that previously we could not tackle,” observes Mr Gibson. This is partly due to the maximum turning diameter of 320mm and the maximum turning length of 550mm. With a bar capacity of 78mm, it also means that Vision can produce more parts from bar rather than billets, and with a barfeed purchased for the machine, lights-out machining has now become a regular occurrence.
“The machine just seems to tackle everything we throw at it.” Mr. Gibson states. “Big or small, it does it all, and the material removal rates are phenomenal on jobs from 20mm depths of cut when turning to drilling a 70mm diameter hole with a modular drill in super duplex material. When you consider we were only running at 200rpm when performing the drilling and it was only using 25% of the available spindle power it’s a well-built machine with great power and it holds the tolerances we demand of it all day, every day”.
Mr. Gibson also notes: “It’s not only the machine that’s important to me but the whole package. From sales through to the installation, training and ongoing support from XYZ’, the whole experience has been second to none and that’s why I also purchased a CT65 HD.”
By posting about its work on social media, Vision has generated interest from companies looking to outsource jobs. Business is growing, which has led to a recent move to new premises. From modifications to coffee machines, Vision is attracting work from various sectors from green energy to defence.
The APCs of greener transportation
How is the automotive industry meeting the lofty government goals that new diesel and petrol cars and vans will no longer be sold from 2030, and that all new cars and vans must be fully zero emission at the tailpipe from 2035? Will Stirling interviews Ian Constance, CEO of the Advanced Propulsion Centre
Often mere words do not do the task justice. The transition to net zero automotive – think about that for a minute.
The easy part is to visualise switching powertrains from petrol and diesel to electric (EVs), then designing and building processes for the mass volume manufacture of EVs – a huge engineering challenge. But this complexity covers materials, batteries and gigafactories, electric machines and drives, rare earths, power electronics, fuel cells, and more, such as their supply chain viability.
Then there is the charging and hydrogen fuelling infrastructure. Supply chain security of key materials, including rare earth materials mined in just a few global locations, R&D investment in the right areas, technology scale-up, geopolitical risk, and market reaction to new technology. An important actor in this complex landscape is the Advanced Propulsion Centre (APC), the government agency tasked with managing funding programmes, judging applications and assisting companies that have good, low-carbon tech solutions.

The APC administers the Automotive Transformation Fund, a £1bn+ fund to help eligible companies make the low carbon transition. It has run a suite of projects, funds and accelerator programmes since 2013. CEO Ian Constance needs to juggle all these balls, and the clock is ticking, but he spared 30 minutes for MTD magazine.
Ian says: “The Advanced Propulsion Centre (APC)’s mission is to enable the UK to stay at the forefront of the global transition to smarter, safer, and importantly, more sustainable automotive and mobility solutions. The other part of APC is Zenzic, an agency investigating future-related, autonomous mobility – driverless vehicles.”
What are the net zero automotive trends as we head towards 2025? “In the last 12 months, we’ve gone from a position of very high growth to flatlining and a bit of stagnation in the EV market, so what you’re seeing there is a shift back towards HEVs (hybrid) and PHEVs (plug-in hybrids). I believe that is a short or medium-term shift and is driven by a few factors including rising populism in politics. But given the money and plans put into getting to net zero, we will find our way back to growth in BEV, battery electric vehicles.
MTD readers are interested in the net zero automotive shift generally, and in manufacturing opportunities specifically. Recently the APC produced a report on the electric motor market, and the change in motor technology – indicating there is a slow shift from the dominance of permanent magnet synchronous motors to non-magnet motors like induction motors. Do both provide good opportunities for UK engineering businesses?

“We have some very capable businesses that are scaling up here,” says Constance. “One of them is AEM, Advanced Electric Machines, based in the Northeast, who are developing magnet-free motors. In general, we have a very strong traction motor community in the UK comprised of various companies that are developing tech in this space, and a lot of them are using magnetic rare earth materials. There is Yasa in Oxfordshire, Protean in the Southwest who specialise in in-wheel electric motors, and there are plenty of others as well. So, the motor manufacturing opportunities are massive for the UK.”
“Ford is investing heavily in Halewood, with support from the APC. They are turning this big factory from a manual transmission plant, clearly a technology that’s intimately linked with internal combustion engines, over to electric drive units at high volume for export. Ford is doing that because it sees the UK as an important place to put that technology and create that mass volume.”
“On the motor technology shift: Permanent magnet motors are generally high performance and are lower cost (than rival tech) at this stage. They need rare earth materials. The non rare earth magnet motors, and non-magnet motors (induction and electrically excited synchronous motors), are an important hedge against the volatility of rare earth material prices and supply, which is expected to go through the roof. That volatility and the geopolitical angle is a hedge that that many people want to make sure that they’re on the right side of.”
Rare earth reliability, and gigafactories for specialist vehicles
A big, less visible part of the APC’s work is research and policy work into securing these essential materials. As rare earth supply is dominated by China and a handful of countries in much smaller volumes, supply security is paramount.
“You need to mine the ore, the raw stuff, in a clean and sustainable way, then you have to process the materials into rare earths, then into magnet materials, produce magnets, which are then used in the motor – it’s a classic supply chain, with risks. We (the UK) are looking to create those supply chains back to friendly nations that we feel we can make long-term strategic partnerships with. The processing part of it is as important as the availability of the materials.”
The mainstream net-zero automotive news has been dominated by gigafactories, so-called in reference to the capacity of the batteries made there. Building these factories in countries that manufacture EVs is essential, due to the dollar and carbon costs of shipping batteries, plus these are vast investments, and create thousands of jobs and supplier contracts. The UK’s gigafactory picture is, some might say, behind its European peers following the loss of Britishvolt in 2023.
Constance contests whether Britain is far behind the pack. “We (the UK) had the first gigafactory in Europe, a small one in the Northeast with just over one gigawatt hour (GWh) that supports the Nissan Leaf. Yes, the UK footprint is confined to two new massive gigafactory commitments, one which is Envision AESC and linked to Nissan, and the second is Agritas, part of the Tata Group, in the Southwest. Look at the potential of those two facilities, they could jointly produce over 70 GWh of battery cells.
Our forecast is that by 2030 we will need around 90-95 GWh, so we are well on our way to fulfilling these requirements.
“But these things are never that simple, are they? Two of our biggest vehicle manufacturers, Nissan and Jaguar Land Rover, will be certainly supported by those two gigafactories. We will need more to look after some of the bigger carmakers, but also very importantly, specialist vehicle manufacturers, which is such a strength of the UK; sports cars, luxury, and heavy-duty vehicles and off-road machines – all of those are going to need a supply of batteries. If people need a specialist vehicle, they might want a specialist battery. So getting into that specialist battery domain is a real focus for the future.”
With batteries also come materials, and lithium is the primary base material for battery anodes and cathodes. But lithium, like rare earths, has a limited supply chain. “There are several different flavours of lithium battery. Beyond that, sodium is the next best element, but it has limitations. We are going to be dominated by lithium, particularly in the UK that has medium-to-high mass production vehicles. That’s where the attention should be.”
Hydrogen’s changing role
Hydrogen has had an interesting story. It was the wonder material for about three years, then media interest seemed to cool as the hype cycle shifted. How is it now developing in the UK car market?
“We are increasingly asked to fund and look at projects involving hydrogen and hydrogen propulsion, much of that is around fuel cells,” says Constance. “Some of it is around hydrogen combustion that’s more suitable for off-highway and construction.”
“The APC’s view is that fast forward another 10 years, most light-duty vehicles (vans and cars) will be battery electric. Then medium-duty trucks will have a mixture of battery electric and potentially hydrogen fuel vehicles, and for heavy-duty, long distance 40 tonners, etc – there’s a big case for hydrogen combustion there.”
There are three legs to this stool: the availability of the technology on the vehicle to do the job cost-effectively and efficiently, the availability of the infrastructure to support the delivery of whatever the energy medium is – hydrogen or electricity. And the third bit is, making the conditions right for the market. You need the three legs together.”
Finally, what other manufacturing opportunities are there for subcontract companies in the EV transition?
“Three areas, I’d highlight,” says Constance. “Giga-castings is a rising area of light-weighting and efficient vehicle manufacturing. Tesla reimagined the way cars are built by using massive front end and rear end castings rather than spot welding or bonding aluminium sections together. Can we develop more of that?
Also the design of drives shafts is changing for an EV powertrain. There is growth of driverless pods operating in in secure space or in semi-secure space like airports. This is a step in completely reimagining a vehicle into lightweight, highly manoeuvrable modes of transport.
Although these are complex machines, the barriers to entry here are lower than for developing a mass-market vehicle.”

We play in the champions’ league every day
In recent years, Porsche Werkzeugbau GmbH in Schwarzenberg, Germany, has taken its mechanical machining to the highest technical level. Two large Starrag HSC machining centers Droop+Rein FOGS play a major part in this. The machines are used to finish press tools for moulding skin parts of vehicle bodies with the utmost precision and produce surfaces with grinding quality.

A premium car manufacturer should have a premium engineering plant. To ensure that the Porsche Werkzeugbau GmbH Schwarzenberg plant fulfils all of the preconditions for this, €40million was invested over the last five years to develop the tool-engineering plant to the highest possible level following the transition from KUKA. Among other things, the Schwarzenberg-based company used this money to set up two new production halls, purchase a new 25,000kN servo press for production-related tool try-outs and invest in retrofitting and new machine tools – including two Starrag HSC centres of the Droop+Rein FOGS 35 68 N40C type. In addition to this, mechanical production was completely overhauled and the production processes were restructured.

All of these measures were based on a solid foundation. Beforehand, the whole tool-engineering team analysed the entire process chain, from development and design to procurement, production and try-out of the tools, right through to the transfer to the operator pressing plant – including a fitness test for the pool of machines. An important detail that came to light was the realisation that when it came to mechanical machining, there was potential for improvement in the finishing of the tools, particularly in terms of accuracy, speed and surface quality.
Lightweight construction results in tougher requirements
Marco Franz, Head of Mechanical Production, points out some important reasons for this: “For some years, we have been experiencing a shift towards lightweight construction and, as the Porsche competence centre for forming technology in the moulding skin area, we were commissioned to develop the tools required for the conversion to an aluminium body. During forming, aluminium sheets respond much more sensitively than steel, which created big challenges for us when it came to tool engineering. Our existing machines were not able to meet some of the requirements”. Two new high-speed machining centres for finishing the pressing moulds should fulfil these new requirements regarding surface quality, accuracy and speed.

According to Marco Franz, they should also help to make the process more efficient and economical, as well as greatly improving quality. The list of requirements contains fundamental preconditions such as process stability, availability and ease of maintenance, as well as characteristics that cannot be compromised, such as temperature stability. In addition, future-oriented specifications for the performance data of the spindles were defined. Lutz Kramer explains: “When you buy this kind of machine, you expect to use it for the next 10 to 20 years. During this time, several generations of new milling tools were developed that are more efficient and allow higher speeds. We must take all of this into account at the early tendering process.”
With their list of requirements, the Porsche Werkzeugbau decision-makers set a high bar – and came to realise that not many manufacturers would be able to meet the requested standards. “During the technical discussions that we held with many different providers, we were soon able to tell who was able and willing to overcome the challenges. Some machine providers withdrew at an early stage, others were later unable to offer any acceptable solutions,” says the Head of Tool and Mould Making, Kramer.
Premium machine tools from Starrag
Ultimately, the decision-makers opted for two Starrag Droop+Rein FOGS 35 68 N40C high-speed machining centres. These 5-axis machine tools are designed for finishing, have an overhead gantry and offer traverse paths of 6.8 by 3.5 by 1.5m along the X, Y and Z-axes. The equipment includes a tool magazine with a total of 100 places that can be filled with HSK32, HSK63 and SK50 retainers, as well as an eccentric fork head with a 40kW milling spindle and a high torque of 700Nm, and three different motor milling spindles with speeds of 18,000, 40,000 and 65,000rpm. In addition, for one of the two machines, Marco Franz ordered a special 6,000rpm angular head that can be used for machining areas that are difficult to access. “With this range of spindles, the requirements of the coming years are covered”, Lutz Kramer is certain.
More than a machine – Engineering precisely what you value
There were other reasons for choosing the Starrag machines, in addition to the technical data, as Head of Tool and Mold Making Kramer explains: “We didn’t just want to buy a machine, we wanted a solution for our tool manufacturing process. That is one of the main reasons why Starrag seemed to be the right partner. With the Droop+Rein specialists, we had the impression right from the start that they were listening to us, wanted to understand us and the thinking behind our processes, and wanted to use their expertise to help us”

Once the machines were installed, the two companies began fine-tuning the workflow together, taking into account the characteristics of CAM, the control system and the machine. This was necessary because achieving the best surface quality requires a high level of accuracy on the path, even at the highest feed speeds. For this, it was important to illuminate the interfaces between CAM and NC and to work with experts from the control system manufacturer to optimally adjust their functionalities in line with the process requirements.
This interdisciplinary approach and the combination of sophisticated drive optimisation in conjunction with the proven machine technology of the FOGS series was extremely successful. The result was not only a class-A surface but also a very high level of accuracy – at the highest path speeds of up to 16m/min on the free-form surface. The processes have been running stable ever since. Lutz Kramer is delighted: “It took a long time to achieve stable processes, especially when it came to the forming tools for aluminium parts because there are many factors influencing this. But Starrag assisted us until we were sure we had reached our goal.”
Marco Franz adds: “I wouldn’t have believed it at the start but Starrag was able to implement more than 90% of our wish list. So it was a good decision to invest in the new Droop+Rein FOGS machines. We are now faster and more precise and achieve – depending on the component and the geometry – outstanding surface accuracy.”
The head of tool and mould-making confirms: “We are proud of what we have achieved with Starrag. With the Droop+Rein FOGS machines, we have attained the desired improvement in quality and were also able to reduce the manual bench work of the toolmakers by roughly 20% in the follow-up process. These are strengths that make us one of the top teams in the Champions League of large-tool-engineering plants.”
Coolant can achieve 20% increase in cutting speed
The demand for faster, cheaper, and greener aerospace solutions comes with challenges. CO2 emissions have been the main focus, but the impact of manufacturing operations is equally crucial. Fortunately, a solution is correctly applying coolant to maximise output, enhance process security and improve tool performance. Here, Henri Sevonen, Senior Industry Segment Manager – Sandvik Coromant, explains the benefits of high-precision coolant and tooling concepts.
The role of coolants has undergone somewhat of an evolution. Machine shops have used coolants by directing tubes that flood the machining zone, particularly on the materials that need coolant to be machined. But now, by applying coolant with high precision accurately into the machining zone, new advantages are available.
If coolant is to be applied effectively and make a difference, it needs to be applied as jets at high precision, in sufficient volume and directed correctly. Qualified applications can make a distinct difference in chip formation, heat distribution, surface integrity and tool wear. When applied correctly, precision coolant maximises output, increases process security and improves tool performance and component quality. The positive effects start at low coolant pressure, but the higher the pressure is, the more demanding material can successfully be machined.
Precision coolant application can make a difference to machining in general, but when machining more demanding materials, such as heat-resistant super alloys (HRSAs) and titanium alloys, the practice makes a dramatic difference.
Many modern CNC machines have coolant supplies at pressures of 70 to 100 bar. This is sufficient to incorporate high-precision coolant, which makes a noticeable performance difference.
An essential basis for high-precision coolant use is modular tools to ensure quick tool changes for minimising machine stoppages. The modular Coromant Capto® tooling system is the basis for new standard high-precision coolant tooling. This modular platform designed with an internal coolant supply is also suited as the means with which to supply coolant at high precision. It is an established ISO standard and an option on many CNC machines with stationary and rotating tools.
Turning tools with precision coolant are equipped to give accurate coolant jets with laminar parallel flow. The jets give rise to a hydraulic wedge between the insert and chip, affecting the chip form and flow and reducing the temperature in the machining zone. Employing nozzles, mounted close to the cutting edge, accurately projecting the high-velocity jets, forces the chip off the insert face and cools and breaks the chips into smaller lengths, helping to evacuate them.
Benefits in finishing operations have been established even at lower pressures, down to ten bars in material including steel, stainless steel, aluminium and heat-resistant superalloys. Apart from higher security brought about by better chip control, precision coolant can bring about considerable tool life improvement and a potential for higher cutting speed. By applying precision coolant, 50% tool life increases can be the result.
Precision coolant can play a vital role in ISO S machining. The effect of precision coolant can therefore provide the potential to raise performance by way of higher cutting speeds without the usual rise in temperature and loss in tool life. There is a clear cooling effect and not the higher cutting forces through higher feeds. For ISO S-classified materials, a 20% increase in cutting speed can be achieved while maintaining the same cutting length.
Internal turning is also an area where precision coolant can play an important role in helping ensure good chip formation, as well as improving shearing properties in demanding materials such as titanium. In this way, the concept adds higher security and longer tool life to boring operations. When machining relatively large, deep holes with boring bars, such as in landing gear components, modular tooling at the back as well as the front end of the tool can be advantageous.
Being able to change the small cutting head on the clamped bar provides quick, easy and accurate changing, adding considerable flexibility for various cuts in one set-up. The CoroTurn® SL combines damped boring bars with serrated locking heads for boring larger holes with depths of ten times the diameter and this is also equipped with precision coolant facilities.
Hexagon introduces factory optimisation with digital reality
Hexagon’s Manufacturing Intelligence division has launched its new digitalisation solution, Digital Factory that has been designed to help manufacturers build highly accurate digital replicas of their factories. It enables manufacturers to optimise floor plans and pivot production lines for smarter and more sustainable future factories.
With open interfaces that enable digital twins of shopfloor assets, this could save a global manufacturing company £35 million per year* by avoiding costly mistakes.
Hexagon has expertise in delivering accurate reality capture and surveying equipment, software to visualise, explore and simulate scenarios in 3D, and collaboration workflows. Digitalisation technologies are a proven technology and have been used for over two decades in civil infrastructure, architecture and public safety, but their potential has yet to be fully realised in manufacturing.
Digital Factory is a future-ready alternative to traditional factory planning that empowers more efficient collaboration between manufacturing and operations teams from anywhere in the world. Digital Factory leverages a comprehensive portfolio of hardware and software solutions that includes Hexagon’s range of reality capture technology – such as the Leica BLK2GO handheld imaging laser scanner, the Leica BLK ARC autonomous scanning module for robotic and mobile carriers and terrestrial laser scanners like the Leica RTC360. These systems allow manufacturers to capture and create dimensionally-accurate point clouds of the factory floor using the Leica Cyclone software portfolio and Hexagon’s Reality Cloud Studio, powered by the HxDR, manufacturers can easily collaborate and quickly process data from Hexagon or a customer’s preferred scanning hardware to recreate up-to-date 3D spaces.
Hexagon offers complete workflows to ensure manufacturers achieve the maximum value from scanning the factory and processing the data into actionable 3D models for various applications to managing the data in the cloud. It will also provide remote team collaboration, facilitating remote collaboration among key teams at any time, using cloud-based tools with analysis and modelling capabilities with on-demand data.
The system will facilitate the planning and remodelling of factory layouts with accuracy and detail, capturing precise measurements of a factory and creating an exact and reliable digital model that can be accessed anytime from anywhere.

Additionally, by testing out new machines, factory floor layouts and workflows in the virtual 3D environment, companies can quickly identify feasibility and emissions considerations, enabling them to better understand the potential benefits of new technology and make future-ready smart factories a reality.
Nicholas Lachaud Bandres, VP of Industry Solutions at Hexagon commented: “Hexagon has developed a deep understanding of manufacturers’ needs. Digital Factory allows users to bring the physical world into an accurate virtual sandbox of their factories on-demand. Collaborating with their team and suppliers, they can consider ‘what-if’ scenarios to shape more effective plant designs and layouts and oversee implementation with irrefutable and accessible 3D plans. We’re making the digital factory more affordable and accessible, and we’re excited to see how our customers apply this to ramp up and remain competitive with smarter factories.”
Manufax follows the Leader
As a leading name in the design, production and fabrication of engineered solutions, Manufax in Stockport manufactures jigs, fixtures and components primarily for the aerospace, defence, automotive and nuclear industries. Now in the third generation of the Rhodes family, Manufax has just invested in a large horizontal borer from Leader CNC Technologies.
The investment in a Fermat machine from Nuneaton-based Leader CNC is part of an ongoing diversification strategy. As David Baines, Group Production Director for Manufax Engineering says: “Up to and during Covid, we were heavily into the aerospace industry with around 90% of our work in the aerospace sector. We suffered hugely during the pandemic, so we needed to diversify and we now do a third of our business in the aerospace market with another third in defence and the remaining third in the nuclear sector. With this diversity, we have seen the need to invest heavily in new technology for the future.”
Looking at the company’s plans for diversification, David adds: “The criteria we were looking for was a good horizontal borer and I found that the Fermat machine was a very good replacement machine with modern capabilities such as the rotary table that we have built into the machine. The quality of this machine builder is excellent.”
Vince Heffernan, Leader CNC Technologies Technical Manager says: “The Fermat WFT 13 is the machine that has been supplied to Manufax. Fermat is a brand that has been around for over a hundred years and it now makes over 100 machines a year. As a machine builder, Fermat will cater to the specific needs of the customer, providing fully modular machines with up to 90 tools on the ATC or a robot loading system that can load an infinite number of tools. The Fermat WFT 13 has the option of different heads, so customers can have a 5-axis head.”

The machine has a 2.6 by 1.8m table with 4 by 2.5 by 1.5m of travel in X, Y and Z axes with an additional W-axis that expands by 600mm. “The advantage of the W-axis is that customers can do some deep hole boring. The machine also has a large capacity where you can fit anything on the machine. You can always do a small part on a big machine but you can’t always do a big part on a small machine,” continues Vince.
David from Manufax adds: “The relationship with Leader CNC has been fantastic and they have helped us with the implementation of the machine and getting Fermat engineers over here to install and commission the machine.”
Adding to this, James Leet from Leader CNC Technologies says: “We work closely with Manufax as the company trusts Leader CNC Technologies as a business that they can consult with on quite a complex issue. If we were positioned to sell hundreds of machines a year, we couldn’t consult and support our customers – we are not positioned to do that. We are positioned to help companies like Manufax. The word ‘partnerships’ is used a lot in this industry, but you cannot make installations like this happen without a partnership approach.”
Concluding on the installation, David says: “This is our first machine from Leader CNC Technologies and it’s very exciting for us to be collaborating with them – and we are looking forward to the future with Leader CNC.”
Kanyana delivers exceptional service
Kanyana Engineering has followed a policy of providing sheet metal services at its Greenfields, Western Australia manufacturing facility since its formation in 1997. Graham Dawe, Managing Director says: “We started this process with a 100-ton press capable of bending 6mm material when our competitors could only bend 3mm material.”
This policy is continuing and now the company has progressed from high tolerance plasma cutting to fibre laser cutting with a 15kW 1.5 by 3m Bystronic Bystar and the first Bystronic 20kW Penta laser with 2.5 by 6m bed in Western Australia. This machine can cut 50mm mild steel, stainless steel and aluminium, giving the company the largest job shop capacity in the region. The capabilities of the company make it sought after for supplying civil, mining, industrial, construction and creative arts projects. The variety is huge and includes balustrades for the Kalbarri Skywalk which soars 100m above the Murchison River Gorge and mining refuge chambers which are designed to protect miners in an emergency.
As part of its pursuit of excellence, it understood that software and the integration of the company’s systems were crucial to its plan. “I had experience from a previous computer business and wanted a fully integrated CAD/CAM and ERP system. With Lantek, this was all possible and we went for the full suite of Lantek Expert, Flex 3D and Integra. We can take DXF files and 3D models directly from the customer and use the system to nest parts, program the lasers and calculate a consistent and accurate price for the job, irrespective of who creates the quotation, offering our best price in a matter of a few minutes.”

Stock material is stored within the system as are remnants from previous jobs so the company knows what is available, what has been earmarked for a job, and what needs to be ordered and can trace the material down to the individual sheet used by its tracking number to produce material certificates for the customer.
Once a quotation becomes an order, all the details and history of the job are released to the workshop ready for manufacture. Lantek’s MES software keeps control of where parts are in the shop, the time taken for each operation and any lost or damaged parts which need to be remanufactured. The live information is collected via workshop PCs and iPads on the laser machines, the press brakes and in the six fabrication bays, where the operators log in to record and validate what is happening and the state of each part running through the factory, even subcontracted operations and bought in items are tracked. Graham Dawe adds, “We have put in two extra processes, quality control and pack and dispatch. These are a final check, allowing us to find and remedy any faults, control the status of the customer, for example, any credit limits, prepare delivery documentation and material certificates, create the invoice, and finally share the information with our Xero accounting software.”
Lantek’s Integra Sales Module helps Kanyana see where its orders are coming from, showing sales by staff member or by customer enabling it to analyse which quotations are working best. It also uses information about capacity in the workshop to provide realistic delivery times and looks through material stores to find how much extra material may need to be ordered. “We aim for a 3-day lead time if possible. We run a 1½ shift system which is 12-14 hours per day, so we can increase this to double shift if we need to create more capacity. With our exact knowledge of production capacity in the factory and automation on the lasers we get much higher beam-on times than most manufacturers can achieve. Similarly, with Lantek MES Manager we can always answer the customer’s questions about where their part is just by looking at the system, keeping them in the loop for realistic and accurate delivery dates even though we have thousands of parts going through the workshop at any one time.”
Kanyana installed the Lantek software in 2019 during Covid so all the training and installation was online. Graham Dawe says: “Now that we have had the system for a few years we get the full benefit and, if Lantek tells us that a job will take 5 days, we know that this is accurate as are the costs involved. This means that we can alter our quoting style where necessary to get valuable or prestigious projects. Overall, the integration and accuracy of the system is the key to our success, enabling us to be highly responsive and competitive, achieving much more with considerably fewer people than our competitors.”
On the right track with VISI
As one of the world’s leading manufacturers of model railways, PECO is a forward-looking family business that started trading back in 1946. Initially concentrating its manufacturing skills on the production of trackwork for model railway enthusiasts, the company has grown exponentially. To support its expansion, the Devon company relies on VISI CAD/CAM/CAE software from Hexagon in its design and manufacturing facility.
Located on the idyllic South Devon coast, PECO is a company that has expanded from its humble beginnings of manufacturing individual components to producing HO/OO ready-made track and then on to all things ‘model railway’. This includes ‘Pecorama’ one of Devon’s leading tourist attractions that has a model railway exhibition and model shop, a ride-on miniature steam railway, a gallery and award-winning gardens as well as industry-leading model railway publications. As a company with a ‘fan base’ as well as a customer base, PECO is a world-renowned brand in the model rail industry. From the foundations that stem from manufacturing a simple coupling, PECO now runs a facility that makes over 3,000 product lines.
Discussing this, Simon Cockerham from PECO says: “We make everything that is part of the hobby building model railway industry. We have been in business since the 1940s and we started as a company making very small couplings that hook two pieces of rolling stock together. It has expanded from there to a business that makes everything from concepts right through to the final product.”

With a manufacturing site that hosts state-of-the-art technology, PECO relies on VISI CAD/CAM/CAE software for its workflows. As Simon continues: “We use VISI throughout our manufacturing facility, from concept through to the final press or mould tool being created. We have numerous licences of VISI throughout our many departments and we also use VISI to generate laser-cut wooden kits for customers with textures upon them. It is also used to create the instructions that will guide enthusiasts and users on how to assemble the equipment.”
“VISI has always been very good for our business as it focuses on just what you need to do the job. Some other software packages that we had before VISI had caused issues due to the high tolerancing of our components and the very deep nature of the machining processes that we have to undertake to achieve the geometries that we require in our press and mould tools.”

As one of the world’s leading PC-based CAD/CAE/CAM software solutions, VISI incorporates modules such as Modelling, Analysis, Mould Design, Flow, Electrode Design, Die Tool Design, 2.5, 3 and 5-axis Toolpaths, Blanks and Reverse. This provides PECO with the facility to create solid models; design, analyse, validate and prepare mould tool geometries as well as the pre and post-production analysis of plastic parts. With dedicated modules for creating electrodes, designing dedicated progressive die design and press tools, comprehensive machining strategies and even reverse engineering of editable solid models from scanned data – VISI provides the complete package for the company.

As Simon adds: “One of the key reasons that we have VISI in our environment and we have been customers for almost 17 years – is because it is very reliable and comprehensive. We have an intimate knowledge of the VISI environment and systems throughout our experienced generations of designers and toolmakers who are here. This means we have the experience to support more junior members of the team here – but even we need assistance now and again because every engineer looks at things differently from time to time.”
“Another key reason why we use VISI is down to the complexity of our products. We need jobs to be correct the first time. We also use very expensive machine tools from Roders, Sodick and Hurco as well as high-end peripheral equipment and cutting tools, and VISI has always kept us safe throughout the entire process of generating these tools.”

The holistic Hexagon mould and die workflow removes blockers so the team can try new ideas. Simon explained: “We use VISI throughout most of our departments, especially within the wider ‘innovations department’. This means we use VISI for everything from design to producing wooden laser-cut kits for the factory to producing custom machinery for our production facilities. We also use VISI for all of our press and mould tooling too. The benefits of having VISI in the workplace are the integration between plot view, CAD/CAM, and the ability to create surface translations for mould flow analysis and laser ablation files. It streamlines integration between departments.”
Many other features the business needs are all connected within a single environment, which makes PECO’s training and application of VISI a lot easier for everybody concerned.

Over the 17 years PECO has standardised its workflows on Hexagon’s mould and die software its had a positive impact on its business. Simon concludes: “We know we have saved a lot of time and money with VISI. The savings are down to the VISI software having all of the components and modules that we require to take our products from concept through to production and export all around the world – all from under one roof.”
Rapid inspection of large parts
Founded in 1989, CMS Cepcor supplies aftermarket crusher spares, manganese-steel wear liners and other equipment to the mining and aggregate industries worldwide. In February, the company took delivery of its first CMM, an Altera M from LK Metrology to enhance the quality control of its products.
Previously, CMS Cepcor had been using a pair of manually-operated, portable, 6-axis arms with a 2.5-metre and a 3-metre reach to check components by touch-probing. This was a lengthy process, as well as being insufficiently precise to measure some parts. For example, it was challenging to inspect bearing seats with tolerances of 30 microns and shafts up to 500mm diameter that need to be accurate to within 20 microns. Additionally, some parts up to 400mm in diameter by 700mm long have eccentric tapers with drawing tolerances down to 15 arcseconds, which were problematic to check by hand.
A further difficulty was that sometimes an arm would be set up on a metrology fixture table and in the process of measuring multiple items, an urgent request would be made by shop floor staff for the arm to be transferred to a machine tool to evaluate the dimensions of a part in situ before it is removed from the machine. Les Hickens, Quality Manager at CMS Cepcor commented: “The LK CMM has a maximum permissible first term error of less than two microns, so is able to measure very large parts exactly and repeatably. It is at least an order of magnitude more precise than a portable arm, giving us confidence in the results. The high level of accuracy is particularly useful when we are discussing the dimensions of a lead-bronze bushing with a high coefficient of expansion. In such cases, both close-tolerance inspection and careful temperature management are important when reconciling our respective measurements. Our Altera M has thermal compensation, with a sensor built into each axis and a temperature probe supplied for attaching to the component under investigation. It would not be practical to wait 24 hours while a large, heavy casting normalises its temperature with that of the CMM.”
Many parts undergoing quality control are turned on a Doosan lathe and then milled and drilled in a second operation on an Honor Seiki vertical boring mill or a Norma machining centre. Consequently it was considered expedient for LK to supply the Altera M 30.15.10 with a Renishaw PH10MQ PLUS motorised indexing head and an SP25M probe for analogue contact scanning, capable of measuring up to 1,000 points per second. The system is able to verify any out-of-roundness much faster than if a touch probe is used to capture a succession of discrete points.

Innovmetric’s PolyWorks Inspector software was also supplied with the CMM. It is a facet of the installation that has delighted the CMS Cepcor metrology team, as it is simple to learn and use and makes training new operators easy. The same software is being retrofitted to the portable measuring arms, as well as a handheld optical scanner on site employed for checking very large castings, so only one seat of PolyWorks is needed, saving expense.
Mr Hickens concluded: “At CMS Cepcor, we are committed to excellence. Although we have been using the CMM for only a few months, it has resulted in a step-change in our metrology capability and the benefits are already tangible. The heightened precision ensures components are controlled carefully to the relevant specifications.”
Fastener manufacturer orders Italian-built lathes
As a leading global manufacturer and distributor of high-specification fasteners, bolts and other precision machined components, LoneStar Fasteners Hydrobolt Ltd has placed a repeat order for turning centres to further expand CNC turn-milling capacity at its Wednesbury facility.
The company is investing £1.5 million in a total of six twin-spindle Y-axis lathes built by Biglia in Italy, supplied through sole UK and Ireland agent Whitehouse Machine Tools, Kenilworth (www.wmtcnc.com). The reason for LoneStar Fasteners buying the more modern production plant is to manufacture nearly every component more efficiently and to have tighter tolerances in one hit, rather than in two, three or even four operations, which was previously the case.
The decision to invest in the Biglia brand was based on the rigidity of the lathes and the high power of their spindles and driven tools, which enables the manufacture of components in tough metals such as stainless steel, titanium and high nickel alloys. These materials are commonly used in the oil and gas, petrochemical and power generation sectors, all of which are supplied by LoneStar Fasteners. To preserve the surface finish on components and prevent damage after machining, a parts catcher and conveyor has been fitted to every lathe.

Robbie Beckett, Operations Director at LoneStar’s Wednesbury facility commented: “The first two machines installed in early 2023 were B620YS single-turret turning centres with an 80mm bar capacity. This has enabled us to reduce production costs, improve surface finish on components and increase productivity. The machines performed exceptionally well over their first year of operation, so we decided to order four more turn-mill centres from the same supplier.”
The next pair of lathes to arrive in May 2024, were a Biglia B750YS with a single turret and 100mm bar capacity and a B465T2Y2, the first with twin turrets. They were followed in August by an additional B750YS and another twin-turret lathe, a BMX45T2Y2 with superimposed machining capability, allowing three tools to be in-cut simultaneously.
Mr Beckett continued: “Before we opted for these lathes, I visited the factory in Italy to see them being manufactured and meet the people. I was impressed with the quality of the build and also the fact that the company concentrates exclusively on making lathes. Good after-sales service was also crucial for us. We were satisfied that it would be forthcoming from the OEM and from the UK agent, which offers unlimited training and applications support.”
“This significant investment reinforces our commitment to technological advancement and maintaining our position as a global leader in our field. The Biglia lathes allow us to produce complex parts with exceptional precision. This enables us to raise operational efficiency significantly and deliver consistently high-quality products to customers, on time and cost-effectively.”
Laser Radar aligns with new automotive VDA standards
As a subsidiary of the Nikon Corporation, Nikon Metrology has welcomed the recent comprehensive update to Volume 5.1 of the automotive measurement standards issued by the German Association of the Automotive Industry (VDA). The newly updated VDA standards cover a more comprehensive array of measurement applications within the automotive sector, addressing the industry’s growing demand for more diverse and sophisticated metrology solutions.
As Andreas Fuchs, Application Engineer at Nikon Metrology explains: “We already offer innovative, traceable measurement solutions based on national and international standards for the automotive industry. The new standard defines very precisely the procedures for evaluating the precise technology that we provide. After all, with the APDIS Laser Radar, our portfolio has featured a product for some time now that can also deliver traceable inline measurements as described in VDA Volume 5.1. Incidentally, those who use this technology no longer need a dedicated measuring room for a fixed CMM – enabling them to save a great deal of money, time and space.”
The APDIS Laser Radar represents a USP with its proven ability to measure details at a distance without needing handheld probes, targets or surface preparation. This makes it ideal for automating repetitive inspection tasks with high accuracy. The system covers many manufacturing, industrial and research applications, including those that involve hard-to-reach features and are complex, delicate, or labour-intensive.
The additional benefits of the APDIS Laser Radar include fast and accurate automated measurements with minimal set-up time for maximum productivity with flexible and portable installation. This allows for the absolute and accurate measurement of parts during production or wherever required, including directly on the production line. The APDIS Laser Radar, in particular, displays its strengths in the automotive industry. For example, the system can measure automotive features with absolute accuracy at high speed with no part preparation, whether inline or offline.
With inline measurement, data can be collected in a much larger sample, resulting in a much more extensive data volume for process control. Therefore, it is wise to develop and use smart evaluation methods or systems and, in the process, adapt the reaction speed to the increased data volume.
“These days, inline measuring technology tends to measure 100% of the parts, giving a very dense test sample with an extremely short response time and close to production,” says Fuchs. “When the part goes through, a real-time statement regarding the quality of the part is delivered immediately – meaning the response time, as well as statistical and general process control, are far better than before. A measuring room, on the other hand, only provides information about ongoing quality with a delay. In addition, there are no statements about the ongoing process, and production continues.”

VDA Volume 5.1 appears to consider the trend that measurements are increasingly being made using traceable inline measuring systems instead of offline in the measuring room, making the implementation of suitability certificates for inline measuring processes in accordance with VDA Volume 5 more critical. VDA Volume 5.1 introduces an eight-stage model for evaluating inline measuring systems throughout their lifecycle. This model generates suitability certificates crucial for system release, ensuring compliance with automotive manufacturing standards. These certificates are significant in procurement as tenders for measuring systems regularly reference VDA volumes, highlighting the importance of standards in guiding industry-wide quality control and measurement practices.
Innovation fit for a King
In AML’s digitally enabled ‘war room’ the firm’s co-founder and Managing Director, Gareth Morgan, is discussing the good news with his colleagues: the 100-strong precision engineering team has just won the coveted King’s Award for Enterprise Innovation. The award recognises ‘leaders in their field who adopt exemplary working practices and inspire other businesses.’ It’s one of the UK’s highest accolades for business excellence.
Fittingly for an MTD aerospace issue, the award is in recognition of AML’s ability to apply technologies and lean processes more often seen in the automotive sector to unlock a staggering two-fold productivity increase in the aerospace sector: enabling a leading UK jet engine manufacturer to expand into the lucrative business aircraft market which is expected to grow to $36.4bn by 2030.

“We are all so proud of what we have achieved and that our skills and talents are recognised at the highest level. It sends a powerful message to our customers that we are constantly seeking better and smarter ways of delivering products to three sectors that are critical to the success of UK Plc – energy, aerospace and defence,” says Gareth, who established the company as a spinout from the Advanced Manufacturing Research Centre (AMRC)16 years ago.
The engines for this market require many novel design elements, materials and technologies to achieve the necessary performance levels demanded by manufacturers, regulators and governments. But behind every challenge, lies an opportunity.
“This combination of high demand and high technological requirements for an existing customer presented an opportunity for AML to develop a new aerofoil manufacturing process that meets the stringent demands of the next generation of business aircraft engines. This opportunity drove the subsequent R&D to develop this innovation project,” Gareth said.
“Our success in delivering this innovation has accelerated our growth by creating eight new roles – six machine operators and two manufacturing engineers – supporting the new robotic production cell built to manufacture these components. Several employees working on the cell have been trained to program and operate it, extending their knowledge and experience,” says Gareth, proving that robotics can increase the demand for skilled roles, rather than remove them.
Gareth acknowledges the role that others have played in helping the embryonic AML go from two co-founders and £90,000 turnover in 2008, to a 100-plus workforce and a turnover of £11m and growing today.
In the case of the King’s Award, he pays special tribute to the Aerospace Technology Institute (ATI) which, over the last decade, has invested £3.6bn in UK manufacturing in “a long-term plan to produce more than 400 cutting-edge aerospace R&D projects across the UK, driving world-class research in sustainable aviation and supporting thousands of jobs”.
Funding from the ATI for the Automotive Excellence in Aerospace (AXIS) project, along with R&D support from former colleagues at the nearby AMRC were critical in giving Gareth and his team the financial and technical support they needed to turn this challenge into an opportunity.

As with all innovations, this required a venture into the unknown. For AML it meant the adaptation and deployment of robotics using advanced automation simulation tools. It also required the development of a bespoke clamping design, which illustrates the value of having a world-leading R&D partner on your doorstep in the shape of the AMRC’s automation experts in Factory 2050.
“Working with the AMRC gave us the confidence to be bold as they have R&D strengths in both precision machining and robotics in the aerospace sector. Having such talent on the doorstep gives us a huge advantage as a business,” said Gareth.
It is also a reason why South Yorkshire is consolidating its reputation as global player in the aerospace, energy and defence sectors, which was recognised as it is the first Investment Zone in England with a focus on advanced manufacturing. This has been accompanied by an announcement that ATI is investing close to £30m in the AMRC-led COMPASS project to accelerate composite aerostructures with Boeing and Spirit AeroSystems.
For Gareth, the big message to government is that ATI’s long-term strategic R&D funding is key to expanding what UK aerospace OEMs and their supply chains can achieve when manufacturers have a public sector partner with a consistent vision for the sector and the financial firepower to fund innovation projects.
These investments, all match funded by the private sector, are essential to maintaining the UK aerospace industry’s position with a staggering 70% of domestic aerospace production being exported around the world.

As thousands gather for the Farnborough Air Show it is also worth reflecting that the sector directly employs 108,000 people and supports over 5,200 apprenticeships across the UK: delivering high-value jobs for a highly skilled workforce. The UK exports £18.6bn with a turnover of £27bn last year.
AML, and innovative supply chain firms like them, are key to the UK retaining its position as a leading player in this global market. But they are also key to driving inclusive economic growth in the regions and nations of the UK. The success of firms like AML shows that regions don’t need a major OEM to drive innovation and growth.
“You don’t need to produce or innovate the complete product to unlock a significant profit share of the final sale. It’s the same in tech. Ask HP or Dell whether it is them or Samsung and Intel who enjoy the best profit margins when a consumer buys Dell or HP computers?” Gareth said.
AML is now a digitally driven tech business. Cloud-based data analytics informs everything they do. But getting there required support. For Gareth, this meant engaging with what he describes as the ‘brilliant Sharing in Growth programme’ whose vision is ‘growing great businesses, by developing great people, for this generation and the next.’
“Our war room is the result of that collaboration giving us the manufacturing equivalent of the Starship Enterprise flight deck. No more Monday morning mayhem where people spend hours sifting through data, turning it into graphs and charts. It’s all there in real-time dashboards, freeing us to interpret the data and make much better, informed decisions.”
But digital is not confined to the war room, it runs like a thread through the whole business: from its extensive quality management system to its adaptive machining algorithms that enable AML to achieve the tightest of tolerances across a range of materials from titanium and nickel-based superalloys, to softer alloys such as aluminium.
For the King’s Award-winning project AML developed bespoke algorithms to generate efficiencies and ensure that each component’s features perfectly blend with the other components’ surfaces, increasing manufacturing performance and reducing rejected parts.

But not every innovation is entirely high-tech. As part of the ATI-funded project, AML looked to the centuries’ old manufacturing technology of forging to deliver big savings in time, energy and cost. This required collaboration between Redditch-based forging specialists, Mettis Aerospace, the AMRC and AML to overcome many hurdles, making this a fully integrated manufacturing process that provided consistency throughout the whole manufacturing chain.
The lesson from this for policymakers and manufacturers is the need to identify niche capabilities in fragmented global production supply chains that open up new markets and products. But broad economic surveys of regions and sectors alone will not reveal where these gaps and opportunities can be found – that requires real manufacturing intelligence-gathering activity.
As AML’s success demonstrates, innovation can have a major impact on productivity. And productivity, which has flatlined in the UK since the 2008 financial crash, is what drives wealth creation, economic growth and personal prosperity.
Back in the war room, Gareth reflects on the importance of being part of the bigger advanced manufacturing cluster or innovation district taking shape in South Yorkshire. For him, it puts fast-growing companies like AML on the global stage. As Gareth says: “AML doesn’t win it on its own, it wins it by being an integral part of this growing advanced manufacturing cluster. If you’re going to compete globally, then you have to be part of a bigger team. When we are successful that means a win for AML is a win for South Yorkshire and a win for UK plc.”
Guhring ‘powers-up’ productivity for EVs
As a machine tool builder that manufactures high-end machines for the global market, Heller UK is frequently involved in turnkey projects for prestigious OEMs. On a recent project, the Redditch company enlisted the support of the cutting tool experts at Guhring.
There has been a wide spectrum of tools used on this project for a leading manufacturer of Electric Vehicles (EVs), including the Guhring tool holders and tool vending technology. As part of the package to accompany the cutting tools, the EV manufacturer has selected a vast range of standard shrink chucks, hydraulic chucks and synchro-tapping chucks.
The cutting tools incorporated in this project included a huge range of standard products, all carefully selected and tested to minimise cycle times while achieving tight tolerances. Whilst the standard range of Guhring products accounted for a significant element of the system integration project, it was the bespoke PCD combination tools that demonstrated Guhring UK’s expertise as a one-stop solution provider.
With the PCD combination tools manufactured at Guhring UK and Guhring Germany, the bespoke solutions were developed to achieve ‘one shot’ plunging. The bespoke tooling aimed to reduce cycle times and adhere to the high surface finishes required – and maintain this over the life of the tool.
Discussing the project, Guhring UK’s National Sales Manager Chris Bush says: “It is a project and industry that is at the very forefront of technology. The end user typically specifies a machine builder and cutting tool supplier – in this instance, it was Heller and Guhring for the cutting tools.”
Looking at how the process delivers a solution for the customer, Chris continues: “In Germany, we have a large project engineering team with over 200 employees. So, when we receive a CAD model of the customers’ component and the machine capabilities, we can develop the cutting tools and machining strategy from that and create an optimised solution in conjunction with Heller.”

“This requires several meetings to discuss the machining strategies and how we develop the tooling to create a seamless solution from machine tool to cutting tool. At Guhring, we supply everything from toolholder to the cutting-edge and that also entails all the speeds, feeds and cutting strategies in conjunction with the machine builder. Once we supply all the cutting data and tooling sheets, we will then visit Heller and do all the initial run-offs to ensure all the cutting data is optimised and the machining strategy is working well.”
Alluding to the overall project, Chris adds: “It has been a great partnership between Guhring and Heller and the current EV project is the biggest project we have collaborated on in the UK.”
Discussing the project from a Heller perspective, Tad Forys from Heller Machine Tools UK says: “We delivered 22 machines in this project. That includes eleven 5-axis machines and 11 4-axis machines – all built in the UK. With this project, we have gone from a customer drawing to a fully automated production line. From the initial enquiry with the customer, our engineers here in the UK conducted comprehensive cycle time studies. Following on from that, we developed custom hydraulic fixtures to hold the parts; and we have used these fixtures because it is a high-volume electric vehicle application.”
“This recent project that we collaborated on with Guhring has been a perfect demonstration of team work. When we talk about collaboration, it isn’t just about working together – it’s about aligning our values and expertise. The first two machines for the production line are here at Heller, so we can do the initial production ‘prove off’ before the machines land on the customers’ shop floor. Guhring has been with us for every step of the journey, clocking in tools, optimising speeds and feeds to make sure we have the most efficient process for the customer before the machines are delivered.”
“From a Heller perspective, this project has been an outstanding success. Our end user is very happy. Everything has been delivered on time to a particularly demanding customer – and this has been made possible by a close working partnership with Guhring who have helped us every step of the way,” adds Tad.
Discussing the tooling solution further, Guhring’s Chris Bush adds: “Even though we are supplying the tools and tool holding for this project, we are also supplying the tool management vending solution. As this is a significant project with a large number of tools, we are supplying the vending machine with some add-on units. The proprietary software that Guhring programs and supplies with this can also be linked to the customer’s ERP system. This provides complete synergy and automation for the end user from tool ordering with complete transparency of costing and cost centres by the operation, the individual machine and even by the operator. This system provides unparalleled transparency, so everyone can see the costs and where the costs are going.”
“From a Guhring point of view, this project has been a great success and working together with Heller has been a true partnership, and a fantastic example of delivering a proven process to the customer on time,” concludes Chris Bush.
Brother opens a valve to automated machining
From 2019 to the present, turnover at Oswaldtwistle-based Ross Pneumatrol doubled to £7m with growth across most industry sectors into which it supplies its pneumatic and electro-pneumatic valves, actuators and other products. The oil and gas industry is proving especially buoyant currently and sales growth in Asia has exceeded expectations, raising exports to more than 60% of turnover.
This success was putting pressure on the prismatic machining department, which was using six 40-taper, 3-axis VMCs of various makes and three Brother 30-taper machining centres with twin pallet change supplied by Whitehouse Machine Tools. To meet the increased demand for valve bodies and pilot end caps, Ross Pneumatrol returned to WMT CNC for two more Brother 30-taper machines, this time with automated component handling.
The first cell, installed in the aluminium machining section in September 2022, comprised a Brother Speedio S700X2 VMC equipped with a Feedio robotic system, including vision equipment, for handling components. Designed to automate, the plug-and-play unit communicates with the S700X2 via a Profibus interface and incorporates a 6-axis robot. A camera vision system and built-in PC allow the robot to detect where on an upper conveyor a workpiece has been placed. After machining, components are returned to an output conveyor.
Tommy Cooney, Ross Pneumatrol’s Operations Manager explained: “We liked the ability of the Feedio unit to handle components in and out of a second Brother VMC when the need arises in the future. No other supplier was able to offer that facility.”
Encouraged by the success of the first cell, Ross Pneumatrol installed a second to produce similar components in stainless steel. Whitehouse proposed a Brother Speedio F600X1. Rather than choosing another Feedio for automation, the manufacturer chose a CubeBox from the Turkish OEM Tezmaksan, for which Whitehouse has recently been appointed a UK sales agent and integrator.
As with the Feedio unit, CubeBox has a 6-axis robot to handle parts directly, rather than basing the automation on a more expensive exchange of pallets with fixtured components. Moreover, as the 20 or so variants of stainless steel valve body and pilot end cap are fundamentally cuboid in shape, the parts are easy and quick to grip for transfer to and from a machine tool.
Mr Cooney commented: “The F600X1 fits well with our production pattern, as stainless steel products account for about 10% of throughput, so we can maximise the F600X1’s utilisation by cutting aluminium as well. The entire cell did not cost much more than fitting a cobot to a 40-taper machine would have done.”

Cycle times on the two latest Brother high-efficiency machines with their higher specifications are about 40% shorter than on the older 30 and 40-taper machines on the shop floor. Aluminium pilot end caps and bodies take seven minutes and 10 minutes respectively to complete, while cycle times for the stainless steel versions are 15 minutes and 18 minutes.
Ross Pneumatrol values the engineering support from Whitehouse who has been closely involved in time studies, applications engineering, provision of mainly Ceratizit carbide tooling, and off-line programming strategies using Fusion 360 CAM software.
A Tezmaksan CubeBox increases production output by up to 50% compared with manual loading and unloading and additionally allows long periods of unattended machine running, including overnight. It is 20% less expensive than a company-specific robot integration system. The plug-and-play solution can be implemented on a shop floor the same day as it is delivered, without the need for robot programming knowledge. The unit installed at Ross Pneumatrol is a CubeBox Blues DR whose FANUC M10ID12 robot has a maximum payload of 12kg.
Everything’s going according to plan
Mills CNC has recently supplied Tufcot Engineering Ltd with a new, large-capacity, multi-tasking lathe to enhance its machining capabilities. The 24” chuck DN Solutions’ Puma 700LM II equipped with driven tooling and FANUC 0iTP control is one of the largest machines acquired by Tufcot in its 43-year history.
Tufcot’s relationship with Mills CNC began in 2005 with a Puma 240LC and now the company has purchased the Puma 700LM II, installed at the company’s 50,000sq/ft facility in Sheffield in April 2024.
Over the years, more investments with Mills have followed to consolidate its supply chain position and acquire new business. It ordered the new Puma 700LM II as well a new 21” chuck Puma 4100MC lathe to be installed in August. The latest additions will take the CNC lathes acquired from Mills CNC to 11 in total.
“The high-performance lathes that Mills sells and supports are real workhorses. They are reliable and deliver the fast processing speeds and accuracies we need to meet our customers’ demands,” says Tufcot’s Managing Director, Greg Majchrzak.
Since being installed, the new Puma 700LM II has been used to machine small batches of high-precision large diameter Tufcot® composite bushes and bearings for customers in the marine sectors. Tied up to tight tolerances, these parts have long cycle times and a range of intricate milled features.
Tufcot® is a composite engineering material manufactured from synthetic fibres and thermos-setting resins. However, the company’s core business is supplying finished products such as wear pads, bushes and bearings.
The marine sector is important to Tufcot’s growth ambitions. Says Justin Krebs, Tufcot’s Operations Manager: “Our knowledge of composites and their application has helped highlight significant new business opportunities that we could exploit if we had larger and more sophisticated in-house turning capabilities.”
Tufcot always had the capacity to machine large parts on its existing lathes, but the processes involved were more labour intensive and required more work handling. This had a knock-on and detrimental effect on the cost-per-part.
As Justin Krebs continues: “Owing to the increased demand for Tufcot® composites, it made perfect sense to strengthen our turning operation by investing in a new large-capacity lathe to machine these larger parts. As a consequence, we approached machine tool suppliers with our plans and asked them to recommend their preferred solution.”
Having gone through what was a comprehensive and detailed decision-making process, Tufcot ultimately opted to go for the Puma 700LM II from Mills CNC. The Puma 700LM II is a large-capacity lathe with a 900mm maximum turning diameter and a 3200mm maximum turning length.
Says Greg Majchrzak: “The Puma 700LM II can handle large and small parts, and the driven tooling capability enables complex, high-precision features to be machined in a single set-up.”
Delivering fast part cycle times and eliminating the need to transfer components between machines has helped improve productivity and process efficiencies. It has enabled Tufcot to win new machining contracts for larger components from new and existing marine customers that, before the Puma 700LM II investment would have been out of its reach.
Continues Greg Majchrzak: “To protect the new business won on the back of the Puma 700LM II acquisition, we also decided to duplicate the investment by ordering a new, similarly specified 21” chuck Puma 4100MC lathe. This will enable us to continue to meet our production and delivery schedules should the Puma 700LM II be out of action for any reason. In effect, we are future-proofing this new business, and leaving nothing to chance.”
In addition to investing in the two new lathes from Mills CNC, the company has also recently acquired two, new state-of-the-art CNC routers in 2022 and increased the size of its facility with the purchase of additional premises.
Taking off with bespoke solutions
The UK aerospace industry encompasses everything from design to the manufacture of aircraft, satellites, missiles, engines and much more. With global manufacturers such as Airbus, Rolls Royce, GKN, BAE Systems, Boeing, Safran, Leonardo, Lockheed Martin and Honeywell based in the UK, the aero industry is known for its quality and expertise.
This sector plays a vital role in providing a highly skilled workforce and all of these companies depend on a robust and reliable supply chain, which includes over 250,000 subcontract engineering companies. These OEM and SME companies produce components from airframes to landing gear, jet and turbofan engines to wings and spars – all made from a wide range of materials, that we at Quickgrind have the expertise to process.
Materials such as aluminium, titanium, steel, stainless steel, nickel alloys, cobalt alloys and composites are the mainstay of these components, but there is one common thread – and that is cycle times and cost per part. At Quickgrind, we help customers realise their production requirements in both cost and production throughput. By applying our services, be it the tools, the machining strategy, remanufacture or vending; we provide a vital link as a strategic partner.
As a leading UK manufacturer of solid carbide cutting tools, Quickgrind is very well positioned to supply high-quality standard tools from stock and produce bespoke tools in a rapid turnaround. It is all about communication, understanding what our customers are trying to achieve, and coming up with solutions.
Rather than looking into the bewildering array of parts manufactured within the aerospace industry; we need to know four things. The type of tool required, the material to be machined, the machining conditions and when you need the tools.
By taking this rather simplistic approach, we narrow down the requirements into two categories. This is ‘Will a standard tool satisfy’ or ‘Would a bespoke tool be better suited’.
Let us look at bespoke tooling. Our reputation has been built by providing solutions to manufacturing challenges, listening to our customers and engaging our highly trained and motivated staff. To this aim, we developed an in-house strategy, known as ‘Infinite Possibilities’. This encourages customers not to be restricted by catalogue items but to work with us to develop the optimised cutting tool for the job. This can ring alarm bells with price, but in truth, the cost of the tool can often be fractionally higher than a standard tool. When looking at the cost of using an inferior tool compared with a bespoke tool that solves the issue, the price is swallowed up by a stable and secure production process.
Standard tooling. Many solid carbide tool manufacturers have large ranges of standard tools, which can be bewildering. We have a smaller range to satisfy your immediate requirements and keep your machines running. With around 500 tools in 40 different types, you will likely find the tool you want, be that an end mill for steel, a high feed tool for die steels or HPC for trochoidal milling in HRSA materials, we have them available.
Our Samurai and Warrior ball nose ranges for hard machining applications and our Eliminator range of barrel tools can save up to 90% cycle time when finishing. We also have the Orbis lollipops that are fast becoming a favourite with many a decerning programmer for those difficult-to-reach features.
Drilling in some of the aerospace materials and applications requires the best. At Quickgrind, we have specially designed features on our tools to cope with HRSA, deep holes and step drills. Last, but certainly not least, one of the most cost-saving and environmentally friendly services we offer is that of re-manufacture. When implemented and managed correctly, savings of 25 to 40% off your tooling budget can be realised. Our QuickEdge service offers regrinding of our tools and other manufacturers’ tools to such a high degree they provide a ‘good as new’ tool life and performance, time and time again. Just think of the savings you can achieve with 4 to 9 times more uses from your tools. More in-depth knowledge and insights can be found on our website www.Quickgrind.com
Helical Motion
The introduction of the ISCAR HELIMILL in the 1990s marked a significant milestone in milling tools. It changed the design of milling tools with indexable inserts, establishing a new approach that would help to shape the industry.
The breakthrough was achieved using a parallelogram-shaped carbide insert, featuring a helical cutting edge formed by the intersection of the insert’s helical side and shaped top surfaces (Fig. 1). The HELIMILL concept offers several advantages. Firstly, the consistency of the rake and relief angles along the insert’s cutting edge, when mounted on a tool reduces cutting force variations and ensures a smooth cutting action. Secondly, the uniformity of the insert’s cutting wedge enhances its strength. Lastly, the helical cutting edge’s proximity to the imaginary cylinder generated by a rotating tool improves accuracy compared to the straight edge found in previous-generation milling inserts. These advancements have elevated milling performance.
Over the years, continuous improvement has led to significant changes in the HELIMILL inserts. The helix of the cutting edge has become more aggressive, and the top surface topology has become more intricate. Combined with advanced carbide grades, these new designs have ushered in a new level of performance. However, the parallelogram insert shape limits the number of indexable cutting edges to two.
To maximise the efficiency of cemented carbides, a new round of insert development was initiated. The successful adaptation of the helical cutting edge to triangular inserts addressed this limitation. The triangular insert concept not only provides three cutting edges but also offers additional benefits. When compared to other shapes with equal cutting-edge lengths, the triangular shape provides a wider central area. This allows for an increase in the central bore size, enabling the use of a clamping screw with a larger thread. As a result, the insert securing is strengthened, contributing to the overall durability of the milling tool assembly. Additionally, the triangular shape enhances the ramping-down cutting capability.
Overall, the introduction of the ISCAR HELIMILL and its subsequent advancements have revolutionised the milling tool industry. The use of helical cutting edges and triangular inserts has significantly improved performance, accuracy and durability, pushing milling capabilities to new levels.
A proximate successor to the HELIMILL is the HELI-3-MILL, a family of milling tools introduced by ISCAR that features triangular indexable inserts (Fig. 2). The advantages of the ‘helical triangle’ highlight why this family has gained popularity in the market. However, it is important to note that this does not mean the triangle shape will completely replace the traditional parallelogram contour with helical cutting edges soon. The parallelogram shape still possesses a competitive edge.
Paradoxically, the narrow width of the parallelogram-shaped insert, which is considered a drawback when compared to the triangular shape, also offers certain advantages. Firstly, a narrower insert allows for an indexable design suitable for smaller tool diameters. Secondly, this insert geometry reduces the depth of the chip gullet, strengthening the cross-section of the tool body. This feature is particularly important for extended flute cutter designs where higher strength and rigidity of the body are crucial. The parallelogram insert structure also permits increased corner radii. Additionally, the classical shape is well-suited for high feed milling (HFM) inserts, which can be mounted in existing pockets, effectively transforming a 90-degree tool into an efficient HFM cutter. Moreover, the ‘helical parallelogram’ has a smaller overall length compared to the ‘helical triangle’ for the same cutting length. Therefore, it would be premature and incorrect to dismiss classical parallelogram inserts.
As a result, the development of 90-degree indexable milling cutters harmoniously combines both approaches, utilising both triangular and parallelogram-shaped inserts. While the triangular insert concept dominates modern designs, the parallelogram insert principle remains relevant. The HELIMILL platform continues to be updated with new advantageous products. ISCAR’s recently developed products relating to milling cutters with parallelogram-shaped inserts demonstrate that the traditional design approach remains effective and capable of meeting the demands of modern manufacturing. Milling high-temperature superalloys and titanium (ISO S group of applications), as well as difficult-to-cut austenitic and duplex stainless steel (ISO M group), presents challenges. Effective coolant supply, particularly pinpointed high-pressure cooling (HPC), can significantly reduce the heat load on the cutting edge, enhancing lubrication and chip removal.
This leads to higher cutting data and enables larger radial engagements, resulting in a higher metal removal rate (MRR). Moreover, HPC facilitates the production of tighter and curled chips, allowing for tool designs with smaller chip gullets and higher tooth density. Taking these factors into consideration, ISCAR has expanded its HELI2000 family (the latest version of the HELIMILL) by introducing new tools that incorporate an HPC option within the tool body. The design of these tools has been optimised using computational fluid dynamics (CFD). They are available in both integral-body configurations and as relatively small-sized exchangeable heads with indexable inserts, which are compatible with ISCAR’s modular systems MULTI-MASTER and FLEXFIT (Fig. 3).
HELI2000 integrates the HELIMILL and HELIPLUS families, combining their latest developments into a single portfolio. This includes the introduction of two new highly efficient carbide grades: IC5600, designed for machining steel (ISO P group), and IC716, specifically tailored for cutting titanium. Additionally, the insert range has been expanded with new cutting geometries. This includes inserts with a high positive chipformer for milling titanium, chip-splitting cutting edges for productive roughing, and other designs. Furthermore, the range now includes inserts with reinforced cutting edges for high feed milling of hard materials up to HRc 60 hardness (ISO H group, Fig. 4). These new products are also part of ISCAR’s HELIALU family, which consists of milling tools with parallelogram-shaped inserts for machining aluminium alloys (ISO N group). The expansion of this family includes indexable endmill heads with threaded adaptations for both MULTI-MASTER and FLEXFIT systems, providing the option for high-pressure cooling (HPC). The screw-in design configuration of the heads significantly enhances the customisation capabilities of HELIALU tools, allowing for a wide range of MULTI-MASTER and FLEXFIT shanks, adaptors, extensions, and reducers to be utilised. Therefore, the development of the ‘helical parallelogram’ has not ceased, and the traditional HELIMILL continues to gain momentum. This development follows a gradual upward helix, revisiting past turns but at a more advanced stage.
What comes next?
In the May issue, we featured our European trip with Ceratizit that took in the fantastic sights of Ruette, Kreckelmoos and Kempten in Austria and Germany to see the investment in new production sites, a new logistics facility and the brand new tech centre. In the run-up to the Autumn exhibition season with AMB and IMTS on the horizon, we take a closer look at some of the innovations shown during the tour that will be making an appearance at these September events. By Rhys Williams
The May issue of MTD magazine covered Ceratizit’s major investments, the sustainability targets and how they are being achieved. We also captured some of the new technology in the pipeline. This month, we take a closer look at the innovations that were put through their paces during the event – this is particularly pertinent as some will have been seen at MACH whereas others will be uncovered for the first time during the Autumn exhibition season.

Following an initial presentation, a tour of the Reutte manufacturing facility in Austria and a spot of lunch, our touring press party was invited to participate in technical demonstrations. These presentations covered everything from the sustainability journey and the roadmap for the future, additive manufacturing and of course the live machining demonstrations. The first demonstration conducted on a DMG MORI CTX1250 involved the turning of a steel billet with the use of the EcoCut multi-functional tool for face and profile turning.
Considered the ‘Swiss Army Knife’ in Ceratizit’s toolbox, Ceratizit customers will know that this range has been around for some time. However, the demonstration was of the new Dragonskin ISO-P steel grade launched in February. This new grade has proven to extend tool life by 15% under trials. Alternatively, users can increase their cutting data and retain the same longevity as their existing Ceratizit grades. An impressive start, but what came next was somewhat different…
Following the profiling of a billet with EcoCut was FreeTurn. Initially launched in 2019, this gem was a lightning rod innovation that won awards when it landed. However, machine tool manufacturers, CNC control manufacturers and CAM developers were somewhat caught napping with only OPEN MIND’s hyperMILL and a few machine tool brands having the capability to work with FreeTurn. Capable of making huge productivity gains and equally impressive tool life savings, this groundbreaker was waiting for the industry to catch up. While the industry has been catching up with High Dynamic Turning (HDT), Ceratizit went ahead and developed and evolved CERASmart – but we’ll circle back to that.
High Dynamic Turning (HDT) is now available with most CAM developers with CNC control manufacturers having some functionality, but still playing catch-up. Why is everyone starting to sit up and pay attention? Well, FreeTurn can increase feed rates by 40%, reduce ‘air-cutting’ toolpaths by 90% and reduce machining times by at least 25%. However, to take advantage of this, manufacturers need a turning centre with a Y-axis milling spindle and an HSK-T or PSC interface.

Running Free With Innovation
Ceratizit ran FreeTurn on the DMG MORI CTX1250 TC as it fulfils all the requirements of HDT. It is both HDT-ready and counts among the most commonly used turn/mill centres on the market. “This means we can confirm that it’s already possible for many manufacturing companies to use HDT and FreeTurn,” explains Product Manager Paul Höckberg.
The component, the base body of an indexable insert drill was optimised and entered using the Siemens Sinumerik 840D control system and a 5-axis simultaneous cycle from OPEN MIND, resulting in astounding cutting speeds. Just to highlight the benefits of this demo – It ran at a cutting speed of 220m/min, a feed of f0.48mm/rev and a depth of cut ap 4mm. During finishing, a cutting speed of 400m/min was applied. “We knew our FreeTurn was good, but we never thought it was possible to machine structural steel (X40CrMoV51) at such high cutting speeds,” marvels Höckberg.
Instead of using three different tools that would usually have been required, the component is now produced with only one FreeTurn tool, saving the use of two tools and reducing the production time from 5:10 to 2:45 minutes.
For manufacturers that can see the merits of this technology, Ceratizit has developed CERASmart – a system that enables manufacturers to quickly and easily generate NC code to create tool paths for HDT with FreeTurn tools….and much more! This ‘plug and play’ system can be installed on a PC or directly to a machine tool CNC and customers can then import DXF files to the software. CERASmart permits dialog-based programming and generation of standard NC code for machines regardless of component complexity and it also allows the dynamic cutting angle adjustment for tool paths along the component contour. With Ceratizit tool data pre-defined in the software, optical simulation and optimisation of tool paths and movements are available in the software without requiring a 5-axis ‘option’ that is normally needed for simultaneous turning.
The CERASmart software for HDT FreeTurn programming is not available to download yet, but Ceratizit expects this to be available for the autumn exhibition season. Why should you be looking at it? If you are heavily involved in turning, the benefits of HDT and FreeTurn have already been emphasised, but concerning CERASmart, it now incorporates HDT with FreeTurn tools specifically for customers to take full advantage of. It allows shop floor programming without CAM and integrates smoothly without interrupting existing programming processes. Furthermore, it incorporates collision avoidance via its simulation and optimisation capabilities and this is all available at a minimal investment when compared to a full CAM solution. The demonstration on the DMG MORI machine was concluded with the FreeTurn tool being replaced by the MaxiMill Slot-SX grooving, parting and slotting system.
Moving to a Mazak MTV815/15 machining centre, the Ceratizit team presented the MaxiMill extended flute porcupine cutter that ran at a cutting speed of 160m/min at a feed rate of 50mm/rev. Utilised by Airbus in France for titanium structural parts, both the Ceratizit engineers and the MaxiMill tool were not shirking away from the challenge of cutting P35 steel in anger. The demo part then underwent slotting and shoulder milling with the MaxiMill 211-15 Shell Mill at a cutting speed of 180m/min before the MaxiMill Shell End Mill was applied to complete the part with helical milling and contouring.
Heading off the shop floor to the solace of a quiet meeting room, Ceratizit then presented more of its latest cutting tool innovations. This included the new MaxiLock N-DC introduced to the industry in February. The (DC) DirectCooling product range has now been added to the MaxiLock-N turning tool holders and this provides two coolant holes that aim coolant directly at the cutting edge, preventing wear and ensuring stable processes.
With three nozzles aimed at the clamping flat of the turning tool from above, another is directed at the flank from below – specifically at the cutting edges. This targeted cooling system is suitable for all materials, although it delivers advantages with ISO-P, M and S in particular due to the rapid heat development in the cutting process. “It is precisely this flank cooling that makes the difference. It extends tool life by 60% compared to cooling that is exclusively aimed at the clamping flat,” explained Stefan Karl, Product Manager of Cutting Tools.
This (DC) DirectCooling has also been added to the Ceratizit range of tried-and-tested MaxiLock-S turning tools. Similar to the MaxiLock-N, the MaxiLock-S holders feature two internal holes ensuring that the coolant is applied precisely to the cutting edge. One hole targets the rake face from above and the other hits the flank from below. Again, this flank cooling system is said to boost service life by 60% compared with cooling exclusively on the rake face.
The final tooling innovation for the day was the Multilock exchangeable head system. Ceratizit customers will know the name has been around for several years, however, the company now offers both steel and carbide tool bodies with exchangeable heads, now offered as precision sintered cutting heads that are not ground. The benefit is a reduced manufacturing cost that is passed to customers who can now acquire reduced-cost sintered cutting heads whilst retaining performance characteristics. The application of carbide and sintering processes was particularly pertinent considering our next presentation.
Turning the impossible to…
….making the additive printing of cemented carbide products possible. Demonstrating its position as a pioneer in carbide research and production, Ceratizit analyses trends to offer optimal solutions. It has now developed additive manufacturing technologies for its cemented carbide grades that enable it to offer carbide-manufactured parts with unlimited design possibilities. The 3D printing of carbide products delivers technological possibilities to overcome design limitations and create designs with minimal batches. Offering simulation and modelling, design adaptation and material selection support, Ceratizit can take manufacturers from the ore to the ready-to-use tool.
With the facility to print every cemented carbide grade from coarse to ultrafine and offering a complete variety of binding agents and levels of binder content, Ceratizit can manufacture everything from wear-grade carbides to grades for cutting tools. Utilising a complete range of printing technologies to provide maximum flexibility with both the powder and binder composition, the design freedom, turnaround times and scalability of production volumes are making this technology a genuine opportunity area.
And of course, there are the environmental benefits. During a presentation, Dr Manuel Walch discussed a formed tool from a sintered block that required EDM processing to attain the final net shape. This example highlighted how eroding a form tool from a carbide block with a weight of 574g required erosion of starter holes, cavity cutting, the removal of scrap and re-wiring the wire EDM machine. With all this effort, the process left 341g of scrap whereas a 3D printed carbide form tool could be printed near net shape with a weight of 260g requiring a finishing cut that resulted in just 28g of scrap. With a material saving of more than 60% over conventional methods, it is evident why Ceratizit is pursuing this route.
Building for the Future
On the final day of the tour, the press delegation crossed the border to Kempten in Germany where we visited the brand new sales and technical centre. When I say ‘brand new’, this site opened on a Monday and we toured it on Wednesday. Some of the staff in this facility with 5,000m2 of meeting rooms and 725m2 of tech centre hadn’t yet learnt where the bathrooms were.
The second tech centre of the tour was of course filled with brand new machines and the first set of demos was conducted on a DMG MORI DMC90 U. This provided an opportunity to showcase the WTX-TB UNI 50XD deep hole drills. Available in diameters from 0.8 to 2.9mm, the WTX micro-drills may be a name familiar to customers who have previously purchased 5XD to 20XD variants and the more recently introduced 25XD and 30XD drills. However, pushing the envelope even further, Ceratizit showcased the new 50XD drill. Anybody applying 50XD micro drills can appreciate the potential for drill breakage, so this was an opportune moment to give the audience a demo of its ToolScope suite that sits within CERASmart to measure everything from the tool load and cutting parameters to machine usage, hours, number of stops, the programmes running, alarms and usage by specific tool – and much more.
Trochoidal milling followed with the CCR-UNI 5XD tool and then came the revelation that the next tool was manufactured from 99% recycled carbide substrate. The ProACT-Mill UNI solid carbide milling cutters are a new independent upGRADE product line of universal milling cutters that combine performance with sustainability. The ProACT-Mill features the same performance as all-around high-performance milling cutters with the most sustainable carbide substrate, providing an economic and ecological advantage. You’ll be able to discover more during the autumn exhibition season on these tools.
Circular Economy
The new recycled ProACT milling line is supplied with data matrix codes on the tools and this connects to the ToolCycle module that feeds back to the previously mentioned CERASmart suite that has the facility to provide the entire life-cycle of the tool via its ‘digital twin’. Within the CERASmart suite sits ToolScope which has been available for several years. Like any software platform, if it receives the right level of investment and innovation the growth can be exponential. Now, the system offers complete process monitoring of tools and with fast-acting mechanisms, tool defects can be detected and machining stopped before any tool is damaged.
ToolScope collects, displays and evaluates data and detects deviations in real-time, allowing customers to intervene in production processes. The machine condition is also monitored for maintenance purposes, making ToolScope act like an airbag inside the machine. It also prevents overloading of the tool and the machine with data recorded for full tool service life analysis. ToolScope incorporates process monitoring, wear detection, adaptive feed control and collision detection, and with functions individually tailored to the customer, tool life improvements and cycle time reductions are easily achievable. Ceratizit is continually evolving the system and it has now introduced a series of iTENDO hydraulic toolholders with sensors that can communicate directly with ToolScope to enhance the feedback loop and machining performance further.
As a critical element in the overall CERASmart suite, ToolScope is an impressive data collection tool that feeds back to CERASmart which itself has been expanded to incorporate data from ERP systems, tool and quality management systems and also ToolCycle. This central portal of information is an Industry 4.0 solution that enables customers to collate data to make better-informed decisions, automate and streamline processes and also create a feedback loop with experts from Ceratizit. A fascinating system, Ceratizit is continually evolving this portal and the HDT FreeTurn programming suite is just one in a long pipeline of innovations to come.
Sodick meets the challenge
When Wall Colmonoy needed to modernise its EDM machining capacity, the manufacturer turned to Sodi-Tech UK and the Sodick brand of wire EDM technology. As the industry benchmark in the manufacture of Colmonoy® surfacing and Nicrobraz® brazing products, precision castings, coatings and components, Wall Colmonoy had three key areas of concern in its wire EDM department. Installing a Sodick ALC800G Premium wire EDM machine resolved them all.
The Michigan-based company with European headquarters in Pontardawe, South Wales had two machines with table sizes of around 300 by 400mm, so any large work outside this envelope either had to be subcontracted out or turned away.

THE CHALLENGES
Wall Colmonoy had deadlines and capacity challenges – it needed a more productive solution that could improve cutting times. The third challenge was overcoming poor precision levels. With existing EDM machines over 10 years old, Wall Colmonoy needed precision levels to within +/-5 microns. It was Sodick that had the answer with its ALC800G Premium wire EDM machine. Looking at why the company invested in a Sodick ALC800G Premium wire EDM machine, Wall Colmonoy Process Engineer Kevin O’Connor recalls: “Our existing machines were ageing, and the programming side of manufacturing became very dated. We were also facing increasing maintenance costs and machine downtime.”

Supporting this opinion, Aaron Patton, EDM machinist at Wall Colmonoy says: “The programming was taking too long and the cutting process was extremely time-consuming. Another issue was capacity, we needed to put large parts on the machine, and we couldn’t do this with our existing machines.”
As Kevin O’Connor continues: “Sodick has had a relationship with Wall Colmonoy dating back 30 years. We went on a fact-finding tour of Sodick as well as other manufacturers to see if they could supply us with a suitable machine. We needed to know if they had a machine capable of cutting our specialist alloys. So, we took samples to Sodick for them to prove that the machines could do ‘exactly what they say on the tin’.”
Adding to this, the Business Development Manager at Sodi-Tech, Mr Tony Berry says: “Wall Colmonoy needed a machine with a capacity to accept their diversity of parts in both dimensions and complexity. The existing machines were too small and the Sodick ALC800G Premium wire EDM machine has a worktable of 800 by 600mm, more than double the bed size of existing machines. By purchasing the Sodick ALC800G Premium wire EDM machine, Wall Colmonoy can manage larger parts, eliminating the need to subcontract work to external sources.”
“The new ALC800G Premium has replaced one of the previous EDM machines and it is more productive than the two previous machines combined. This is a credit to both the productivity increase and the ability to run unmanned for extended periods overnight due to technology like the Smart Pulse electrical discharge power supply unit, Sodick’s Smart Linear technology, the fixed Jet AWT wire threading and the iGroove Plus wire rotation technology. From a programming and operational perspective, Wall Colmonoy can now process up to four different parts simultaneously in a single set-up – and even multiples of those parts.”
Confirming these points, Sodi-Tech UK Technical Sales Manager, Mr Conor Plaskitt adds: “The reason Wall Colmonoy decided to invest in the Sodick ALC800G Premium supplied by Sodi-Tech is to increase the capacity of what they can cut on the machine and take on larger components. This is one of only two machines of its type in the UK and from a market perspective, it really gives Wall Colmonoy an edge over their competition.”
Tony continues: “They have now had the machine for almost a year and it has performed very well. I think Wall Colmonoy are now ready to progress. As part of the free packages that we provide, we can offer advanced training that incorporates things like angle cutting, cutting compound angles, machining unusual shapes and moving on to the machining of specialist alloys, which is exactly what they do here at Wall Colmonoy.”
Looking back at the installation of the Sodick ALC800G Premium wire EDM, Aaron Patton, EDM machinist at Wall Colmonoy says: “When we took delivery of the machine there was quite a steep learning curve, but now we are running the machine confidently, the benefits are impressive. There is still an advanced course that we can undertake to further enhance our capabilities as well as maximise what we can get out of the machine.”
One-stop subby relies on Hurco
Considering itself as a ‘one-stop-shop’, Wolverhampton-based Varlowe Industrial Services Ltd is a subcontract manufacturer that specialises in machining, specialist pipework, steel fabrication, Class 1 coded welding and electrical services. For a ‘one-stop-shop’ of everything from prototypes to small batch manufacturing, pride of place is a host of CNC machine tools from Hurco.
Celebrating its 20th anniversary in 2023, the company works with everything from hospitals and theme parks to automotive and more. With specialist pipework, fabrication and welding being the foundation blocks of the business, precision machining was a bolt-on, as Steve Varden from Varlowe Industrial Services Ltd says: “From a commercial point of view, we needed to keep control of our processes and delivery dates, price points and customer satisfaction. We manufacture everything from jigs and fixtures, prototypes, design and build everything from the basic shaft or gear to specialist projects.”
Looking at why the company invested in Hurco machines, Steve says: “They are very reliable and come at an excellent price point. They are fit for purpose and the company is relatively local to us. Additionally, the service is excellent.”

Adding to this, Mike Boylan from Varlowe says: “We are predominantly making small batch work and one-offs. The parts have to be precise and are often quite complex, so there is a wide variety of components made from engineering steels such as ferrous and nonferrous materials as well as plastics. We primarily manufacture prototypes through to small batches of 10 or 20-off.”
Discussing what the company needs to produce such components, Mike says: “This is one of our newest machines, the VMX60i is the largest machine we have and we bought it because our existing machines did not have the capacity to machine our large parts. This machine has the same characteristics as our other machines, we have the tool carousel, through spindle coolant and lots more.”
“Hurco machines are great quality with a small footprint – they give us everything we need for comprehensive 3 and 4th-axis machining and turning.” Alluding to the programming, Mike continues: “We have a mixture where we program with CAD/CAM and we also have operators and setters programming at the machine. This is feasible as the system is very user-friendly and easy to use. Additionally, being able to program on the machine gives us flexibility and speed. On our newest Hurco machines, we now have dual screens and this allows us to look ahead and remove any potential errors as we can run both screens at the same time.”
“The machines are regularly serviced by Hurco, we also have CMM inspection to ensure we are hitting the tight tolerances our customers require. The inspection department also qualifies that the machines are hitting their tolerances and delivering what we need.”
Concluding on the Hurco machines, Steve says: “As a result of having these machines, sales and productivity have improved and we can control our margins better. We now have 10 Hurco machines.”
Workholding upgrade doubles productivity
At Archway Engineering, a Leadwell V-50L 3-axis VMC performs some of the more arduous machining operations at the Elland-based company. On the shop floor of the West Yorkshire factory that manufactures drilling equipment for site investigation, mineral exploration, water well construction and environmental monitoring, the productivity of parts going through this machine has been doubled simply by changing the way workpieces are clamped.
The transformation has been achieved by the September purchase of three US-made Chick OneLOKs from sole UK agent 1st Machine Tool Accessories, Salisbury. One of the units remains permanently at one end of the machine’s 1,420 by 610mm table, where it has been clocked into a known position to within 10µm across the 152mm face of the clamp’s fixed hard jaw. The other two OneLOKs may be removed to make room to mount a 4th-axis indexer, but they are quick to set up again relative to the permanently positioned clamp using a parallel bar.
During frequent small-batch runs, it is a simple matter to secure three parts side by side, write a sub-program to machine the workpiece in the permanent OneLOK, probe the position of the parts in the other two clamps, repeat the sub-program twice at the appropriate offsets and run the complete cycle in one go.
This process differs markedly from previous practices involving either bulkier conventional vices, only two of which would fit on the table or a lathe chuck for holding round parts, an arrangement so large that just one could be accommodated in the working area. The positions of all these former workholding setups were slow and laborious to establish accurately and in practice each machining cycle was executed individually.
Another advantage of the Chick product is that it has a time-saving ratchet mechanism to allow the operator to adjust the position of the rear, moveable jaw in one swift action so that it almost touches the workpiece. A few turns of a handle move the jaw in the same direction over the last few millimetres to complete the clamping action quickly, contributing further to short setup times. The mechanism’s novel squeeze clamping action with pull-down as the jaws close applies an equal and opposite force on both sides, resulting in repeatability to within 20 microns.

A practical example of the time savings is in the production of a so-called TC shoe for a drilling machine, produced from an S355 hot-finish steel tube weighing 50kg. Setting up three billets in machined aluminium jaws side-by-side in the OneLOK takes 1.5 hours, compared with a total of four hours previously needed to clamp the parts individually one after the other in the lathe chuck on the VMC table.
Furthermore, clamping forces were lower using this workholding equipment, as well as when employing conventional vices, compared with up to 26.7kN of retaining force exerted by a OneLOK. Therefore, feed rates previously needed to be slower, lengthening cycle times. The versatility of the new units to hold prismatic parts in hard steel jaws, or round parts in soft aluminium jaws machined to match the shape of the component being secured, sets the Chick product apart from conventional vices and underpins the elevated gripping pressure.
Danielle Toner, production manager at Archway Engineering commented, “Most of our production involves one-offs or small batches, with individual cycles generally running for several hours. Being able to clamp parts of any shape so firmly in the OneLOK allows us to mill much more aggressively using high-feed inserted end mills and solid carbide drills. In one instance, an EN8 steel drive unit end plate that previously took six hours to machine is completed in one hour.”
She explained that it is now possible to feed at 7m/min a 32mm diameter end mill rotating at 1,200rpm, whereas the previous maximum feed rate was 2 to 3m/min. At the same time, higher quality tools may be employed and the depth of cut has increased from 0.3 to 1mm. Additionally, because parts are held more rigidly and the OneLOK is of low-profile design, there is less vibration so tools last longer and the machined finish is better. It helps particularly with the production of the TC shoe as well as phosphor bronze sliding plates, both of which require features with a near-polished surface.
Mrs Toner concluded: “The quicker setup times using the Chick OneLOKs and the faster machining cycles that their secure clamping means that a typical short batch of parts can be produced on the Leadwell in two days, compared with up to one week previously. I estimate that productivity across the parts produced on this VMC has increased by 100% and probably more. The machine operator is also more productive, as he has extra free time and can plan his work around the factory more effectively.”
What role does tool holding play in sustainability?
Sustainability considerations are currently ‘trendy’ and Individual elements such as toolholding are often considered. However, if you want to act sustainably, you should not focus too much on finite details and look at the overall process. When it comes to sustainability, the product life cycle and the process in which it is integrated are critical factors.
In machining, there are a lot of variables to consider such as the material, component geometry, quantities, type of machine, tools and clamping devices used. External circumstances such as the production location, the qualifications of the employees and automation must also be considered.
Apart from materials, energy efficiency is probably the main factor that determines a sustainable process. Therefore, a promising approach is to look for the largest consumers and optimise their use. The machine tool offers savings potential as it consumes the majority of the energy used with its spindle and axis drives, peripherals and auxiliary units.
When purchasing new machines, the user can significantly reduce consumption by paying attention to energy-saving components. Andreas Haimer, Managing Director and President of the HAIMER Group, explains: “In our production, we have learned that replacing an old machining centre with a new one using the same machining process requires around 30% less energy. As a family business, we pay a lot of attention to sustainability. In the last financial year, we invested a total of over €1m and we have saved over 250 tons of CO2.”
Machining savings can be made with examples like CAD/CAM-optimised machining strategies. Andreas Haimer says: “A customer provided us with data on how he reduced machining time by 75% from 71 to 18 minutes per part by trochoidal milling with our HAIMER Power shrink fit chucks and the HAIMER MILL cutters. The change in machining strategy was accompanied by energy savings due to significantly lower power consumption. While the spindle load was 80-85% for 10 parts with a face mill that had a total energy cost of around €150, the trochoidal milling strategy with a spindle load of 8-10% and shorter cycle time reduced energy costs to €5 for 10 parts. This was a higher output with lower energy consumption per part produced.”
The sustainability
of toolholding
Have you ever thought about how a tool holder could contribute to sustainability? Where a milling machine consumes an average of around 30kW, plus the power of hydraulic and pneumatic devices, automation equipment and robots – toolholding only plays a subordinate role. This is because the tool holder is a comparatively small detail, even if using a shrink-fit chuck with a marginal energy consumption.
Looking at other clamping systems, the energy consumption during shrinking is higher in operational use than with a hydraulic or milling chuck. Looking at the entire product life cycle of a tool holder, which includes production, maintenance and disposal, a completely different picture emerges.
The production of a hydraulic chuck requires significantly more effort and energy due to its complicated structure. There is also the soldering of the expansion sleeve, additional heat treatment to prevent the solder joint from breaking, as well as the effort required for cleaning, assembly and filling with oil. “From our experience, the energy required for production is around three times higher for the shrink-fit chuck,” explains Andreas Haimer.
“In addition to shrink-fit chucks, we also have hydraulic chucks. Although their list prices are higher than shrink-fit chucks, they are the right solution for certain applications. However, they are not more sustainable. Our analyses show that a hydraulic chuck requires around 25kWh more energy to manufacture than a shrink chuck. In product life cycle terms, a shrink fit chuck with an energy requirement of 0.026kWh per shrink fit and the cooling cycle can be shrunk almost 1,000 times before it requires more energy than a hydraulic chuck.”
The same applies to milling chucks, which are much more complicated and contain more components as well as grease and lubricants. Life cycle and process reliability are crucial. Haimer shrink chucks are maintenance-free and can be shrunk in and out an unlimited number of times, whereas hydraulic chucks and milling chucks have to be serviced every 2-3 years to check the clamping force. The contained hydraulic fluid or grease also makes environmentally friendly disposal more difficult than with shrink-fit chucks. As well as the life cycle, there are differences in terms of process reliability.
But how is energy consumption calculated during the shrinking process? Heating a shrink-fit chuck takes about 5 seconds. The maximum output of a HAIMER Power Clamp shrink-fit machine is 13kW, but the average is 8kW. This means that a single, complete shrinking process consumes around 0.011kWh and cooling consumes 0.015kWh resulting in a total of 0.026kWh. If a kilowatt-hour costs 20 cents, shrinking and cooling costs a marginal 0.5 cents. How should the energy consumption be classified when considering the machining process with a power consumption of around 30kW? Assuming that a tool is in use for an hour and 1% machining time can be saved thanks to the high concentricity and rigidity or the improved milling strategies due to the slim contour holder, that would be 0.3kWh of energy saved.
Andreas Haimer summarises: “The energy consumption per clamping process plays a negligible role compared to the issues of life cycle and machining strategy. Modern CAD/CAM-optimised milling strategies can save 75% of machining time. Machinists must focus on such processes if they want t sustainability and productivity.”
Your benchmarking tool for brilliance
It was Johann Wolfgang von Goethe who said ‘The hardest thing to see is what is in front of your eyes’. For some of us, that scotoma is everywhere in our business and we just don’t know it. But what if you could find the ‘blindspots’ and unlock the utopia of perfect process flow and profitability? Now, Hexagon Manufacturing Intelligence is offering manufacturers that opportunity with its ‘7 Steps to Machine Shop Excellence’.
Almost every business has bottlenecks that are obvious to identify, but to dig into the deepest darkest corners, you would probably need a comprehensive audit by the likes of Deloitte or KPMG. Thankfully, Hexagon has done all the hard yards. It hasn’t just developed an ecosystem of solutions, but it has also created a ‘global’ platform to incorporate all manufacturing stages into a seamless, streamlined workflow. Essentially, Hexagon has the tools to provide a full transformational journey – and it all begins with its benchmarking tool.
The benchmarking tool has two questions for each of the seven steps – and each question takes less than 30 seconds to answer. Once you complete the survey, you will receive a business performance report with a ‘playbook’ on how to map your route to success. The benchmarking tool has been rolled out worldwide to give manufacturers a true indication of how healthy their technology ecosystem is in comparison to their peers. The playbook will provide suggested areas for improvement whilst a ‘follow-up’ consultation with a Hexagon expert will identify your blindspots.
With this new tool, the 7-steps and its digital platforms, Hexagon is empowering machine shops to optimise operations across their workflows, allowing for streamlined and more efficient ‘Design, Make and Inspect’ practices. Commenting upon the roll-out, VP of General Manufacturing at Hexagon, Jason Walker says: “A typical manufacturing business consists of several different ‘silos’ with design, quoting and planning all being far removed from the production floor, which in itself often works with different processes and systems to manufacture, manage quality control and conduct inspections – and these are just a few of the many silos. When quoting for jobs, businesses often work from spreadsheets and tribal knowledge of the business and processes.”
“Challenges at the early quoting stage can arise from a disconnect between evaluating the design and the preparation for the manufacturing step, without calculating accurate cycle times relevant to the correct resources, such as machines and tools available. With machine and tool library information stored in Hexagon CAM suites, this is just one process that can be streamlined. Likewise, the same CAD file can be converted and utilised differently in the production department to the inspection department, causing further discrepancies. Our aim is to break down the departmental silos, eliminate discrepancies and find the hidden value in the seams between the processes,” Jason continues.
Taking your first step…
The first step for any manufacturer is to access the free benchmarking tool (https://machineshop.hexagon.com), complete the survey and then start an exciting journey. In essence, the benchmarking tool takes manufacturers through the complete life cycle, starting with quoting and planning. At step 1, machine shops need to adopt more strategic quoting and planning processes that are connected. Striving to balance resource allocation, synchronised machine schedules and seamless work order tracking can be a challenge – so optimising the workflow from the start is critical. Here, Hexagon has technology like DESIGNER that offers design-for-manufacturability capabilities for smarter manufacturing, the Nexus digital reality platform also breaks departmental silos by connecting people and technologies across departments and integrates with tools such as Datanomix, the automated production intelligence system.
Many of Hexagon’s platforms stretch across all 7 steps and in step 2 (design and review), Nexus and DESIGNER work together seamlessly to enable real-time collaboration on design reviews . At Step 3, Hexagon leverages the latest technology to ensure design integrity is maintained throughout manufacturing. Even the planning of downstream processes such as measurement and inspection can be managed here.
Steps 4 through 7 incorporate production intelligence, shop-floor operations and quality inspection, with the final step being reporting and analytics that provide insights into the health of all prior stages. Throughout the 7 steps to manufacturing excellence, Hexagon’s hardware and software works harmoniously with existing solutions to break down departmental ‘silos’ and deliver the hidden benefits of digital manufacturing throughout each step and department.
Cylindrical and non-circular grinding
For 50 years, the Dutch machining centre manufacturer Unisign has been developing machine concepts adapted to special machining requirements. With over 80% of production in-house – the company relies on KELLENBERGER for its grinding technology.
Today, Unisign portal machines, travelling column machines and multitask machining centres go to logistics and energy companies, commercial vehicle manufacturers and general engineering companies all over the world, a large proportion are special machines. Parts machined on these machines includes truck axles, chassis side rails, lift mast profiles, excavator frames, crane beams and railroad bogie frames, which are often produced in a single clamping operation on Unisign machines. The machining length often exceeds 25m. The Unisign Technology Center houses an R&D department where new machine concepts are continuously developed.
“Here, we can demonstrate the performance of our machines,” says Operations Manager Paul Lennaerts, who is responsible for design, production and assembly. “We show customers how our machines can increase productivity. In our production, we manufacture the components for our machines mainly on Unisign machines, at least that goes for machining processes. For other operations, we use machines whose quality awareness is similar to ours, like KELLENBERGER”
For grinding operations on high-precision parts such as tie rods, mandrels and spacer rings, a KELLENBERGER KEL-VARIA (the predecessor model of the premium KELLENBERGER 1000 series) was purchased back in 2003. The performance is oriented to the precision production of prototypes as well as small and medium series. A solid machine table with a reinforced machine bed brings very high static and dynamic rigidity and stability, both decisive factors for quality, precision and great productivity.
In 2021, a KELLENBERGER 1000 was purchased, partly for capacity reasons and partly due to performance requirements. René van der Peet from the sales company BMT Machine Tools BV, which represents KELLENBERGER in the Netherlands guided the selection process for the new machine. “We weigh all parameters very carefully when buying a machine and leave nothing to chance. Our workpieces vary greatly in size and we mainly machine small batches and individual parts, which means the machine must be very flexible.”
The KELLENBERGER 1000 is equipped with hydrostatic guides in all main axes for maximum form accuracy in grinding tasks with interpolating axes. The CNC-controlled B-axis for the grinding head is hydrostatic and wear-free. It has a direct drive with a water-cooled high-torque motor and an angle encoder with a 0.1” resolution. The turret grinding head swivels about three times faster and positions with an accuracy of less than one angular second. This reduces non-productive time and increases productivity.
The company decided on a machine with a 1,600mm centre width and a centre height of 250mm. “We make full use of the working space when grinding long mandrels,” says Paul Lennaerts. Of the more than 30 different grinding head variants with external and internal grinding spindles that are available for the KELLENBERGER 1000, Unisign chose the UR 1-6-7 grinding head arrangement with an external grinding spindle and two high-frequency internal grinding spindles with speeds of 42,000rpm and 60,000rpm, respectively.
The purchase of the KELLENBERGER 1000 was well prepared with various grinding tests at the KELLENBERGER factory in St. Gallen. Among the acceptance parts were Capto C8 receptacles that Unisign manufactures in-house. The necessary grinding know-how for the Capto tool holders was supplied with the machine after the grinding tests. “That helped us a lot at the beginning,” says Paul Lennaerts.
“We are very satisfied with the new machine”, Paul Lennaerts sums up. “It has given us the required increase in performance. And we also appreciate the KELLENBERGER machine service, which has short distances due to its location. Overall, KELLENBERGER is not only a machine supplier, but also a consultant for manufacturing processes in the grinding sector.”
Zero Point clamping systems from LANG
There are many quick-clamping systems and that’s good because every machinist’s day-to-day work is different. They all have a common machining job that follows the process of either turning, milling, grinding or a hybrid combination of these tasks.
Once the job or a machining sequence is finished, changeovers take place and everything starts again from the beginning. The most important task of a clamping system is to lock the part in place to handle the machining forces in the turning or milling process. The clamping system must match the component geometry and the machining process. Typical shapes for components in an industrial environment are cuboids, cubes, prisms, pyramids, cones, spheres and cylinders. If workpieces are manufactured individually or in series, part quality is assured by using a zero-point clamping system. This ensures the necessary accuracy and repeatability of the machining processes using a pre-defined reference point. Choosing the right clamping device has a significant impact on the efficiency of the machining process, as the machine can be set up more quickly.
Zero-point isn’t always the best direction
However, the potential is still being wasted here too, as the zero-point clamping system is often only placed in the centre of the machine table for simple single clamping. The remaining space often remains unused. As safe as zero-point clamping systems are, efficiency can certainly diminish at this point.
The Quick•Point® Rail clamping system puts an end to this and can be used more efficiently than many zero-point systems. It can be installed in any CNC machining centre and does not require a base plate.
Expanding the range of tasks
Quite simply by moving the clamping device variably using the Quick•Point® Rail clamping bars. The length will depend on the component length as anything is possible with combinations – especially when two clamping devices are in use. The distances between the two clamping devices can be flexibly adjusted using the Quick•Point® Rail clamping system. This is made possible by a 4mm grid that can be moved back and forth as required.

Risers are also frequently used in the zero-point clamping system to increase the distance between the machine table and the workpiece. Once inserted in the zero-point clamping system, these are firmly locked in place on the automation pallet or machine table. With the Quick•Point® Rail quick clamping system, a zero-point riser can now be moved for the first time and still leave the desired space. The Quick•Point® Rail takes just a few minutes to install and turns a reliable zero-point clamping system into a movable zero-point system with a wide range of options.
The quick-clamping system makes use of the existing conditions in the machine tool. Quick•Point® Rail can be fastened in the grooves of the machine table. This is done with the aid of sliding blocks. The clamping bars are fixed above this using cylinder head screws. If you are working with automation pallets, simply screw the clamping bar of the Quick•Point® Rail clamping system directly onto the automation pallet using the existing threaded holes. The clamping rails are available in different versions so that it can always be guaranteed that the available width of the base is ideally utilised. The Quick•Point® Rail starts with performance improvements where every machining task begins – increasing the clamping efficiency.
Getting to grips with aero engines
Brown and Holmes in Tamworth have a fantastic reputation for designing bespoke fixturing around the world, and recently they made a fixture that helps to produce jet engine turbine blades halfway around the world in Singapore. MTDCNC went along to find out more.
Asking Mick Waller from Brown and Holmes how the company has earned its remarkable reputation, Mick tells MTDCNC: “I think a lot of credit for our reputation has to do with making sure that we have customer satisfaction. That’s key to backing up our fixturing solutions and making sure that our customers are happy with those solutions. Brown and Holmes have over 75 years of experience designing and making bespoke workholding solutions. I’ve been with the company for 18 years managing the design team. The design team’s got a lot of experience with this sort of thing and there’s a lot of more mature designers, so in years of experience there is quite a lot of experience here.”
Discussing a fixture that has been in operation for some time, Mick continues: “This is part of a suite of fixtures that manufacture aircraft turbine blades and this is half of the 20 fixtures, the other half of it is for machining the tip which sits above the component when it’s in the machine and this is the root holding part of that fixture.”
With a lot of complexity around manufacturing turbine blades like achieving good surface finishes and meeting impeccable precision levels, Mick explained how Brown and Holmes worked with this customer to develop the process. As Mick says: “The customer had a pretty good idea of what they wanted to machine at the different operations and our challenge was to make sure the component was held in a repeatable and accurate manner. This meant that they could carry out complex machining. The geometry involved in these types of components is very complex and the key requirement was accuracy and repeatability. This particular operation is to machine all of the aerofoil. It machines both sides round and the lead-in and trailing edges of the aerofoil. The platform machining is also done on this fixture. As time developed, because this fixture has been in service for a long time, it also involves machining the tip of the blade as well in the same process.”
“The key thing is working with the machine tool and with the cutting tool engineers because you see some nice rads that flow all around this part and access is key to being able to produce this part in a single operation.”
Talking a little more about the fixture, Mick says: “The dovetail at the bottom of the root is key to the accuracy. The accuracy of that dovetail when you’ve got the tip of the blade far away from the base is critical. If it’s not right to within microns at the root end, then we’re going to be millimetres out at the top of the blade. When we’re holding the tip in the other half of the fixture, obviously that’s got to be totally in line with the base. Otherwise, when we’re machining the aerofoil, you’re going to get a variation in the thickness of the finished machine part. So yes, they’ve got to be perfectly right between the two halves of the fixture.”
Discussing the service life of the project, Mick recalls: “This particular operation has been in place for approximately 10 years and there are 19 of these fixtures. At the end users facility, these are running on a lot of machines and as time has developed, it became a three-op process that required three fixtures that we designed and manufactured and we’ve since as the process has developed as the ‘condition of supply’ of the components has developed, we’ve managed to eliminate one of those fixtures.”
“Initially, there were various cutting trials done with this in the UK, then out in Italy and then down to the end user in Singapore. So yes, it’s a well-travelled process and we support that process whether it be at a partner in Birmingham or a machine tool manufacturer in Italy or the end-use customer which is out in Singapore where this particular facility is for that company.”
Looking at the life-cycle of the component and the long-term support provided by Brown and Holmes, Mick says: “This is a great example of the way that we can support fixturing over a long period. A lot of our bespoke workholding is one-off and you see the fixture. If it works successfully, you never see the fixture again. However, with the production demands on this component, there’s been a long process over ten years of supporting the customer and developing things with the customer.”
In conclusion Mick says: “We try to be as diverse as we can, covering as many industries as possible. So this is an aerospace fixture that’s going out to Singapore and we have got medical customers in Ireland and there is a significant UK customer base. They all get the same level of support whether they are in the UK, Ireland or halfway around the world.”