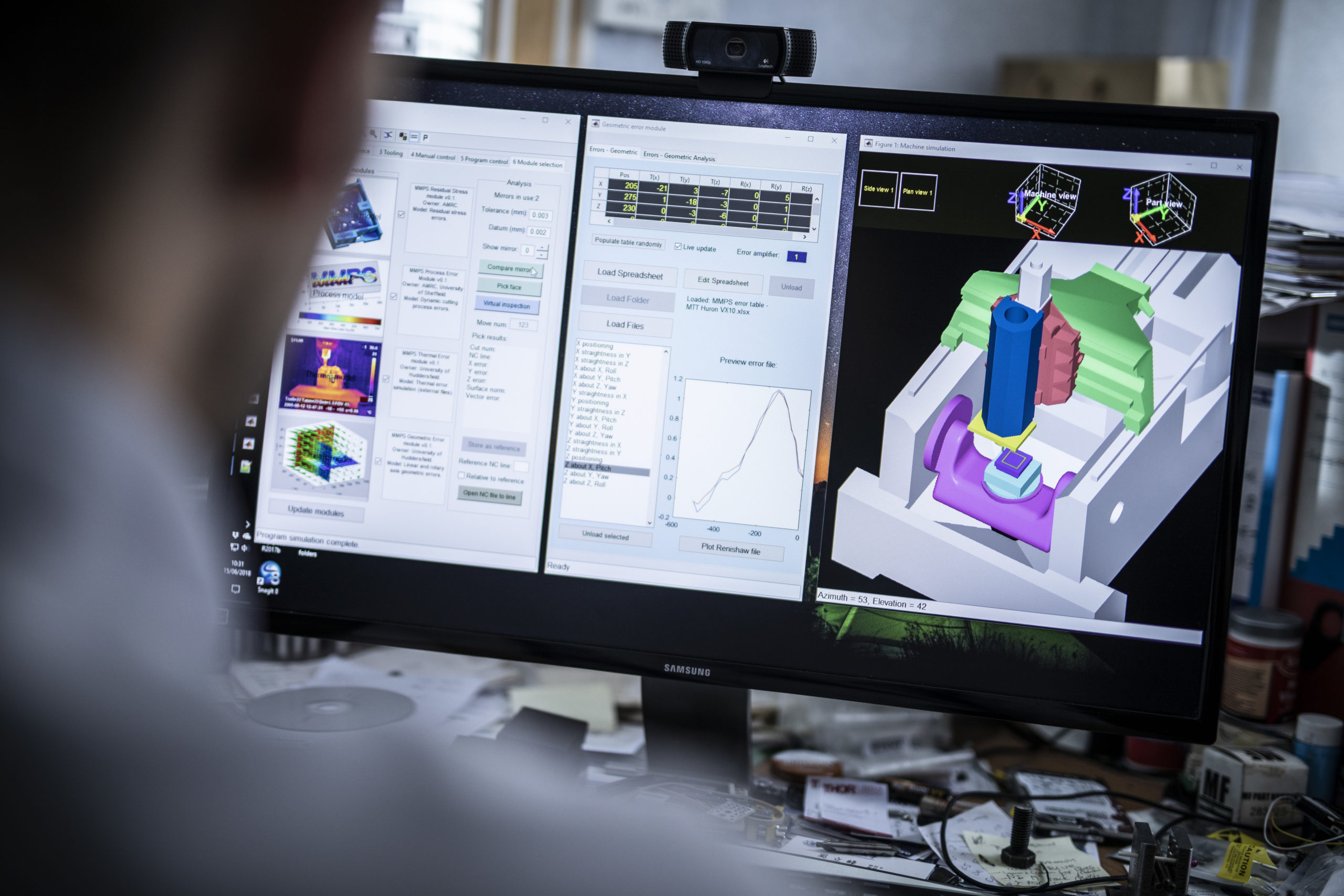
Environmentalism, Carbon Neutral, Green Manufacturing – no matter what the current popular terminology, it is quite clear that sustainability is high on the list of current social and governmental agendas. This is a fact that isn’t likely to change any time soon. Previous high profile green initiatives have often, and justifiably, focussed on consumer behaviours (e.g. subsidies for solar panels and electric vehicles or being encouraged to think about reducing our carbon footprint). However, attention is now shifting towards the manufacturing industries and the embedded emissions that are an inevitable and unavoidable aspect of all manufactured goods.
Efforts to reduce the environmental impact of industry are of course nothing new. The use of recycled materials, shifting to alternative energy sources and changing production methods are all common practice. Practices that largely mirror the kind of changes that individual consumers are encouraged to make. The benefits presented by these large, structural changes are obvious and require little explanation, but consider one activity that is abundant in the industry but rare in your personal life: Measurement. As manufacturers, we are constantly measuring parts and products to ensure they are acceptable and that processes are working effectively. How can metrology contribute to manufacturing sustainability?
For most companies, metrology is an aspect of Quality Assurance, an end of line process that takes place after the bulk of manufacturing activities. In this respect, current practice is limited in its ability to affect the production process, with only periodic changes possible if defect rates start to rise, as this indicates a process moving out of control. A core concept at the heart of Industry 4.0 is a shift towards metrology becoming an ‘In-Line’ (incorporated into the manufacturing environment with measurements between stages) and ultimately ‘In-Process’ (continuous measurement throughout manufacturing). These developments have largely been driven by a desire to enable greater automation and allow more flexible manufacturing processes while also increasing quality, but the same factors allow metrology to significantly impact on a company’s sustainability.
Embedding metrology throughout the manufacturing environment allows continuous monitoring of the individual manufacturing processes, rather than a single final assessment of the finished product. This approach has several obvious advantages but thinking specifically about sustainability, it enables intelligent data-driven decisions about process parameters to be made rapidly. The result is the ability to improve process efficiency in real-time. The benefits include:
Efficient Energy Use
Reducing reliance on fossil fuels for energy is a core part of any sustainability programme, often through a move to renewable energy sources. However, as is often the case in engineering, there are no perfect solutions – only compromises. All energy sources have positive and negative factors, therefore any reduction in energy use can be equally beneficial. Gathering data at each stage of manufacture allows individual processes to be tracked and inefficiencies to be identified. For example, monitoring the surface quality of machined parts can quickly identify rates of tool wear. Worn tools not only affect finished product quality but also require greater cutting force (hence increasing energy use while machining is often used as an indicator of worn tooling). Using data derived directly from the manufactured part combines aspects of both process control and quality; reducing both the energy used in the manufacture and the energy used by multiple processes.
Reduced waste and scrappage
When it is possible to carry out detailed measurements at the end of a process or with true in-process systems throughout the process; the manufacturing process and sources of potential defects can be identified quickly. Remedial action can then be taken immediately to correct the issue if possible or if necessary, scrap the part before any further energy is expended on manufacture. By reducing the need for rework or corrective machining, energy use is further reduced. Reducing waste through optimised stock removal and fewer scrapped parts will yield further downstream benefits in the form of reduced embedded emissions as a result of raw material manufacture and transport.
Optimised designs and processes
The ability to autonomously control manufacturing in real-time, as a result of an in-process measurement can offer the potential for further efficiency gains. This is because processes can be kept in their optimum range throughout changing manufacturing conditions. The energy efficiency of any manufacturing process is directly linked to the operating efficiency of that process. If a process can be completed more quickly or with fewer stages, less energy will be used overall.
Additionally, gathering comprehensive data about the manufacturing process is an important first stage in developing an accurate simulation model and ultimately enabling the creation of a true digital twin. This allows a process to be optimised in advance of machining and is fundamental in facilitating agile manufacture, optimally choosing the right machine and process within a set of given performance constraints. This is especially attractive to companies engaged in the low volume or even one-off manufacture of extremely high-value components. In these scenarios, there is little opportunity to observe the manufacturing process and make incremental improvements; efficiency must be present from the outset.
We can see how decision making that is informed by metrology has the potential to substantially improve process efficiency and positively impact on manufacturing sustainability. This applies to both existing processes but also by extracting maximum benefit from wider scale initiatives. For most companies, metrology is an aspect of Quality Assurance, an end of line process taking place after the bulk of manufacturing activities. In this respect, it is easy to see why many people regard measurement as a costly process, indeed how often do we hear the phrases ‘the cost of conformity’ or ‘the cost of quality’ with additional processes and rework/scrappage affecting the all-important bottom line.
The reality of course is that QA engineers don’t really add unnecessary costs. Parts must be measured to ensure process performance and incorrect parts were always that way, the QA engineer just confirmed the fact. As with all technological improvement, there is an initial trade-off to be made. Developing integrated metrology systems for an established manufacturing environment requires significant investment by industry in terms of capital outlay and upskilling of the workforce. However, a subtle change of mindset, and the adoption of a new approach to measurement, can shift metrology from a source of cost generation to a net cost reduction, both financially and environmentally.