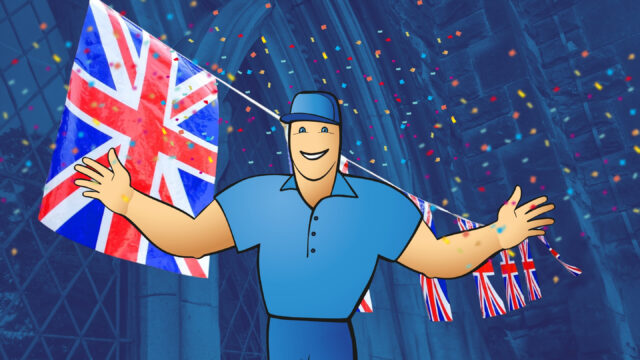
MRPeasy Celebrates Milestone of 400 Manufacturing Clients in the UK
Bournemouth, UK – MRPeasy, the leading cloud-based manufacturing software provider for small businesses, proudly announces reaching…
Traceability essentially means having insight into the chain of events that is your business. But how to achieve it and what are the mechanisms that support it?
The journey of a product leads from the source of the raw materials all the way through the supply chain to the end consumer. In most cases in the modern world, it takes a long time and multiple accountable parties to get a product from the first phase to the finish. Suppliers, component manufacturers, transporters, manufacturers, distributors, retailers – all of these links are responsible for their own part in the chain.
Traceability gives you the chance to pinpoint the exact place where something has gone wrong, and to organize product callbacks whenever a pervading fault in a batch is detected. Even more importantly, having certain traceability-related policies in place could give you the chance to avoid product non-conformity that could be traced back to your company.
Traceability essentially means that every action and every change leaves a trail that allows us to come back to a specific process to see what might have gone wrong. With today’s highly regulated markets, it is an important aspect of doing business, especially in industries such as food, healthcare, automotive, etc., where one mistake could have a large impact. Traceability should, however, be a priority for all modern manufacturers regardless of their industry and its specific regulations.
Apart from handling product non-conformity issues, traceability helps to improve the processes of different departments of your business in the day-to-day thanks to constantly generating data regarding the performance, costs, lead times, and other aspects of your business. In inventory management, traceability also ensures that you know exactly where and in what quantity your materials and goods are, and how long it would take until they expire.
In a nutshell, traceability can aid in constantly improving your production processes, customer retention, brand image, and bottom line.
In manufacturing, achieving traceability requires you to keep track of all your raw materials, WIP inventory, finished goods, workstations, factory floor and stockroom workers, and any other parties directly handling the products at some point. This means marking your inventory and documenting the actual production and inventory handling process.
There are two types of inventory tracking: stock lot tracking and serial number tracking. Lot tracking usually deals with goods in bulk (i.e. process manufactured goods like food, pharmaceuticals, fabric, etc.) while serial tracking is used when handling individual items (i.e. discrete manufactured goods such as electronics, furniture, etc. as well as parts and components).
Whichever the case, for the tracking system to properly work, all SKUs need to be allocated specific areas in the warehouse or stockroom, each individual item must be properly labeled, and each stock movement needs to be recorded.
In the case of lot tracking, stock lot numbers are assigned to each batch produced or procured that would allow tracking their origin, quantity, value, expiry dates, certificates of conformity, and other information deemed necessary. When a part of the lot is found to be faulty (e.g. a client says that a loaf of bread they bought at the supermarket was moldy), it would be easy to know which batch it was from, and where other parts of the same batch are.
For example, a batch of raw materials is procured and it is assigned a unique number L-001, and goods are labeled accordingly.
These raw materials are used in two production runs, products from one run are assigned the lot number L-002, and the second gets the number L-003.
These products may go out to hundreds of customers, and you write down exactly from which lot the products were issued, from lot L-002 or L-003.
In case you become aware that there had been an issue with these raw materials, you have the means to identify in which production runs these raw materials were used specifically. And if necessary, you can identify which customers received those products, for a potential callback. This is called forward traceability.
Alternatively, in case you receive information from your customer that there is an issue with a product, you are able to trace back step-by-step and identify where something went wrong – was it during shipping, in production, or something to do with raw materials. And take action accordingly. This is called backward traceability
Read more about What Is Lot Tracking and How to Use It?
In the case of serial number tracking, however, serial numbers are assigned to individual items rather than groups of items. This would allow tracking items separately, to more effectively manage warranty or insurance queries, returns, and repairs.
There are several levels of how to implement serial number tracking.
This information will provide a clear overview of each item’s status, location, and history. When dealing with large quantities of products with serial numbers, it would also be feasible to use barcodes and barcode scanners.
Quality inspections can be performed to check the conformity to standards of your raw materials, WIP inventory, and finished goods. This implies that definite specifications have been set for each SKU inspected in order for the tangible item to be compared to the ideal one.
Whether you track items by lot or serial number, the quality inspection results are stored with the lot and/or serial number’s information.
Quality checks performed at the reception of raw materials from your suppliers may reveal errors on their part, while quality checkpoints after certain internal processes or at the end of the production line can point to problems in your own facility.
Few companies can, however, afford to inspect every item they receive and produce. For that reason, it is necessary to account for the cost of quality and determine which items are so valuable that they merit regular quality checks.
Read more about the Cost of Quality and How to Calculate It.
Worker and workstation reports can give you invaluable insights into your processes and provide you with the necessary paper trail that would allow you to trace back errors and inconsistencies to specific events, people, or parts of production. With proper reporting policies in place, you can receive accurate information about the materials consumed, the employees tasked with different activities, equipment usage, any hiccups in the process, etc.
When you identify a certain employee as the culprit for recurring inconsistencies, you might want to provide them with additional training or assign a senior worker to supervise and instruct them.
Going further from your internal processes such as production and inventory, traceability can also be achieved externally to a certain degree. Apart from propagating traceability policies among your suppliers and distributors, you can also perform quality inspections directly after receiving materials and directly prior to shipping out your finished goods. This allows you to minimize the chance of errors on your part, and to use concrete data in order to communicate to your partners about inconsistencies that can be attributed to them.
Read more about Supplier Performance Management.
The above-mentioned prerequisites for achieving traceability might seem like a lot of work – because they are. Organizing it all on paper or in spreadsheets is a horribly time-consuming endeavor and that is why most small businesses opt for only doing the bare minimum in order to not over-stretch themselves with administrative tasks. That is also why SME manufacturers often say they do not have the resources to achieve full traceability.
Implementing a manufacturing ERP software, however, allows small manufacturers to take a huge leap towards better transparency. Modern ERP systems are perpetual inventory systems that track and update inventory and financial data with each movement. They allow for stock lot or serial number tracking, expiry or best before date tracking, barcoding, quality inspection management, and other inventory control methods, while also providing you with the capacity to plan out and schedule production in the most efficient way possible.
The best solutions also provide workers with the capability to report their activities, giving you the chance to track their work time and actions. An ERP system uses all the information provided by different departments of your business to create meaningful statistics about your production efficiency, equipment effectiveness, supplier performance, inventory movements, etc. that you can use to trace back inconsistencies and to improve your processes.
Article source: https://manufacturing-software-blog.mrpeasy.com/traceability/
Be first to see all the updates from MTDCNC
Our newsletters frequency varies dependant on content
All the latest deals from the industry feature on our newsletters