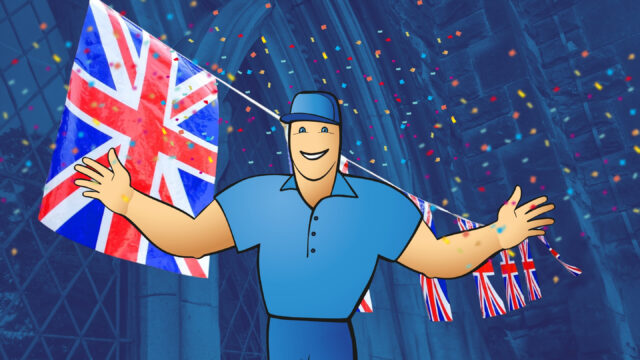
MRPeasy Celebrates Milestone of 400 Manufacturing Clients in the UK
Bournemouth, UK – MRPeasy, the leading cloud-based manufacturing software provider for small businesses, proudly announces reaching…
Total Manufacturing Cost is an essential metric for understanding the productivity and profitability of a business. Among other things, it can be used to adjust the selling price of your products and to identify and cut unnecessary expenses.
Total Manufacturing Cost is the total sum that has been spent on production activities during one financial period. Or in plain terms, it is the cost of manufacturing products.
Once the complete realm of accountants and productivity engineers, the Total Manufacturing Cost has now been revealed as an approachable and useful tool for organizations of all sizes and types.
It is an essential metric for understanding the productivity and profitability of a business. Managers or investors can compare the Total Manufacturing Cost to total revenue and get a quick overview of the company’s profitability. Companies can adjust the selling price of their products by analyzing the Total Manufacturing Cost. Additionally, knowing where your money is spent gives you the chance to identify and cut unnecessary expenses, thereby streamlining your manufacturing business.
Luckily, the busy manager doesn’t have to complete an accounting course to understand what needs to be done. They can simply use the guide below to get a grasp of the ins and outs of their company’s production pipeline.
Read more about Calculating the Selling Price of Your Products.
The Total Manufacturing Cost consists of three key business costs:
1. Direct material costs
2. Direct labor costs
3. Manufacturing overhead costs
Let’s dive deeper into these three areas.
Direct materials are the actual physical materials that need to be purchased, refined, and consumed in order to make the product. Keep in mind that direct materials are only those that are used in a significant, measurable quantity, i.e. the materials that are included in the bill of materials of a product.
Indirect materials are generally used in many types of products, in insignificant quantities per unit. These materials are accounted for in the manufacturing overhead.
For example, in a furniture manufacturing company, timber, paddings, and textile are the direct materials used in production. Glue, nails, sandpaper, etc. are indirect materials.
In a beverage company, water would be used as a direct material that goes into the bottle. But water could also be used as an indirect material to wash the bottles or equipment. It is necessary to keep these types of consumption separate for accounting purposes.
You can calculate your direct material costs by adding the cost of raw materials purchased to the beginning raw materials inventory, then subtracting the ending raw materials inventory.
You cannot just take the number of products manufactured and multiply it with the material quantities going into each product because you also need to account for Work in Process inventory, waste, and scrap. That is why raw material inventory and material purchases are used to calculate the Total Manufacturing Cost.
If you do things manually, with pen and paper, or spreadsheets, you will need to perform regular stock-takes and sum up all invoices for materials to get the numbers right.
ERP/MRP software, however, can calculate the direct material cost by summing up material costs of manufacturing orders that were executed during the period, thus eliminating the need to perform complex calculations.
Products are more than just the sum of their materials. Much of a manufacturing company’s resources are allocated towards labor that turns the direct materials into finished goods.
The direct labor costs that go into calculating the Total Manufacturing Cost are only incurred from staff that are directly involved in the production part of the business, e.g. line workers, craftspeople, machine operators.
Staff that are not handling the production of goods, such as management, accounting, maintenance, cleaning staff, etc. are not considered direct labor.
Note that it is important to include retirement funds, holiday pay, payroll taxes, or any additional fees that are incurred by paying direct labor. Some companies may also decide to include costs related to training the production staff.
MRP software can calculate the direct labor cost by summing up reported work hours of manufacturing orders that were executed by workers and multiplying it with their wages, thus eliminating the need to perform complex calculations.
The last piece of the puzzle is the overhead. This comprises everything from the electricity used to the maintenance and depreciation of equipment.
Here is a brief list that will give you a good overview of what items to consider:
Manufacturing overhead does not include administration wages, sales, marketing, office rent, or other staff salaries.
Normally, manufacturing overhead costs are only clear after a financial period is over, and products long sold. ERP/MRP software can also pre-apply the manufacturing overhead costs to your products according to an estimated rate. This gives a better insight into cost and profit in real-time, without having to wait until the financial period end, and thus helps you to price your products better. At the end of an accounting period, you can compare if the overhead was under- or overapplied and adjust the rate accordingly.
Read more about Applied Overhead vs. Actual Overhead.
To find the Total Manufacturing Cost, just add together the aforementioned three key costs from the specified financial period.
Therefore, the Total Manufacturing Cost formula is this:
Total Manufacturing Cost = Direct Materials + Direct Labor + Manufacturing Overhead
At the start of a quarter, a furniture manufacturing company has $8,000 worth of raw materials waiting in inventory. During the period, $5,000 worth of stock is added to the raw material inventory. At the end of the period, however, there remains only $3,000 worth of raw materials. Using these numbers, we can calculate the Direct Materials used.
Direct Materials = $8,000 + $5,000 – $3,000 = $10,000
There are eight shop floor workers in the company that are directly involved in production. Four of them have seniority and/or special skills and make $2,600 a month, the other four make $2,200 a month. The sum of their quarterly pay is the Direct Labor Costs.
Direct Labor = [($2,600 x 4) + ($2,200 x 4)] x 3 = ($10,400 + $8,800) x 3 = $19,200 x 3 = $57,600
The Manufacturing Overhead is composed of indirect labor costs for maintenance (wages amount to $9,000 in a quarter) and warehouse (wages $12,000 in a quarter), additional materials such as glue and sandpaper ($800), rent ($6,000 per quarter), insurance ($200 per quarter), and an equipment depreciation of $2,400 a year, i.e. $600 per quarter. That is $28,600 altogether.
Manufacturing Overhead = $28,600
So, the Total Manufacturing Cost for the quarter is the sum of the direct material and labor costs, and manufacturing overhead.
Total Manufacturing Cost = $10,000 + $57,600 + $28,600 = $96,200
Total Manufacturing Cost is often conflated with the Cost of Goods Manufactured and the Cost of Goods Sold, which both are separate concepts, as well. Even though all of these terms are related, it is necessary to know their difference.
While the Total Manufacturing Cost shows how much money was spent on all production activities, COGM details the costs related only to the production of those goods that were finished during the period. This means that unfinished products that were transferred into Work in Process inventory are left out of the sum. When all production has finished, however, the TMC and COGM are equal.
COGS, however, accounts only for those finished products that were sold during the financial period.
As seen above, the Total Manufacturing Cost is the sum of three key costs:
The Cost of Goods Manufactured uses the Total Manufacturing Cost as a component in its own formula. However, as COGM shows how much was spent on manufacturing finished goods, we have to count out the WIP that was started during the period.
So, the COGM formula is this:
Subsequently, COGM is used to calculate COGS. While COGM shows the costs related only to producing finished goods, COGS is the cost of only those goods that were sold. When all of the finished goods have been sold, then COGS is equal to COGM.
This is the COGS formula:
Read more about the Cost of Goods Manufactured (COGM) and the Cost of Goods Sold (COGS).
Taking a look at your Total Manufacturing Cost is an important step when trying to make your business more cost-effective. While COGM and COGS are strictly accounting terms, Total Manufacturing Cost is also used to identify areas in the production process that need to be streamlined.
All of these aspects are important when trying to improve your manufacturing efficiency.
Article source: https://manufacturing-software-blog.mrpeasy.com/total-manufacturing-cost/
Be first to see all the updates from MTDCNC
Our newsletters frequency varies dependant on content
All the latest deals from the industry feature on our newsletters