What Has More Square Meters Than a Football Stadium and More Teeth Than a Shark Convention?
This week, MTDCNC’s Tony Gunn takes us on an incredible journey to one of Europe’s most awe-inspiring hubs of innovation and precision: Liebherr-Verzahntechnik GmbH, nestled in the scenic hills of Kempten in the Allgäu region of southern Germany.
The story of Liebherr’s gear technology division began in 1952, with the production of gear-cutting machines in Kirchdorf an der Iller. But by 1962, the company relocated to Kempten—a place that feels more like a setting for a fairy tale…if the Brothers Grimm were obsessed with bevel gears and CNC hobbing machines.
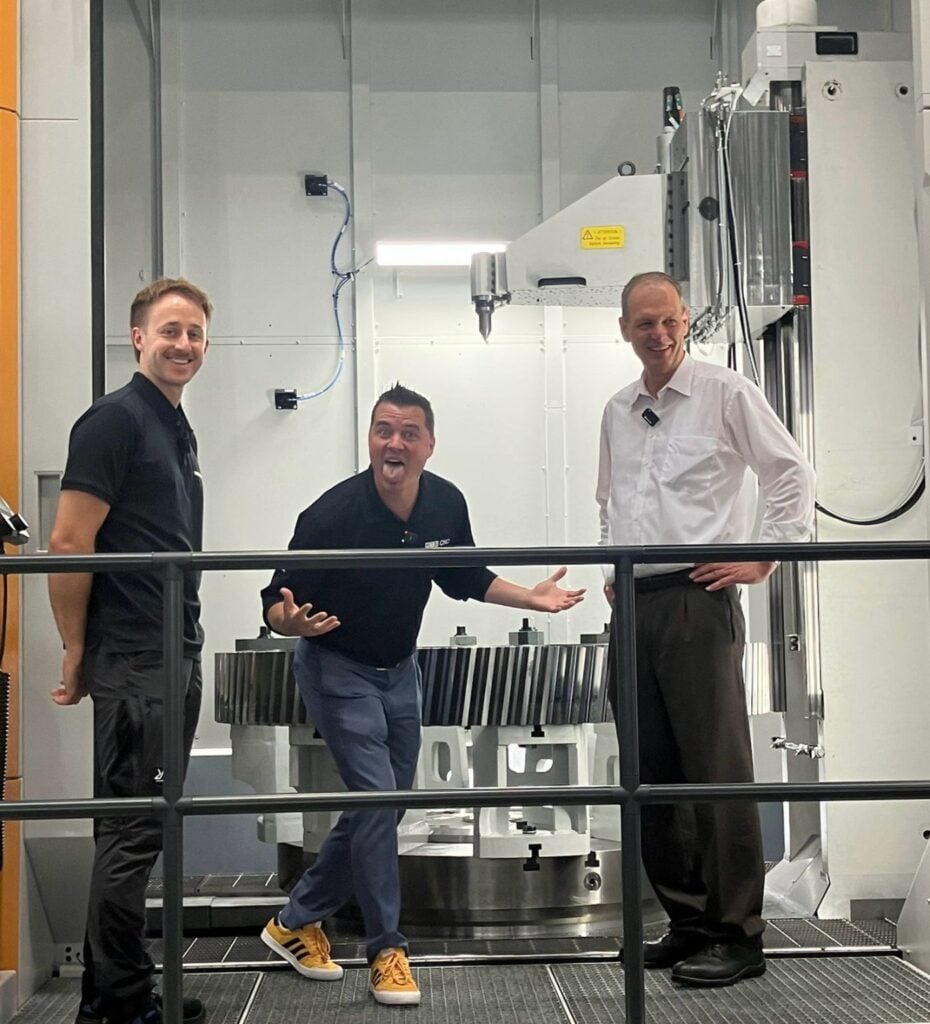
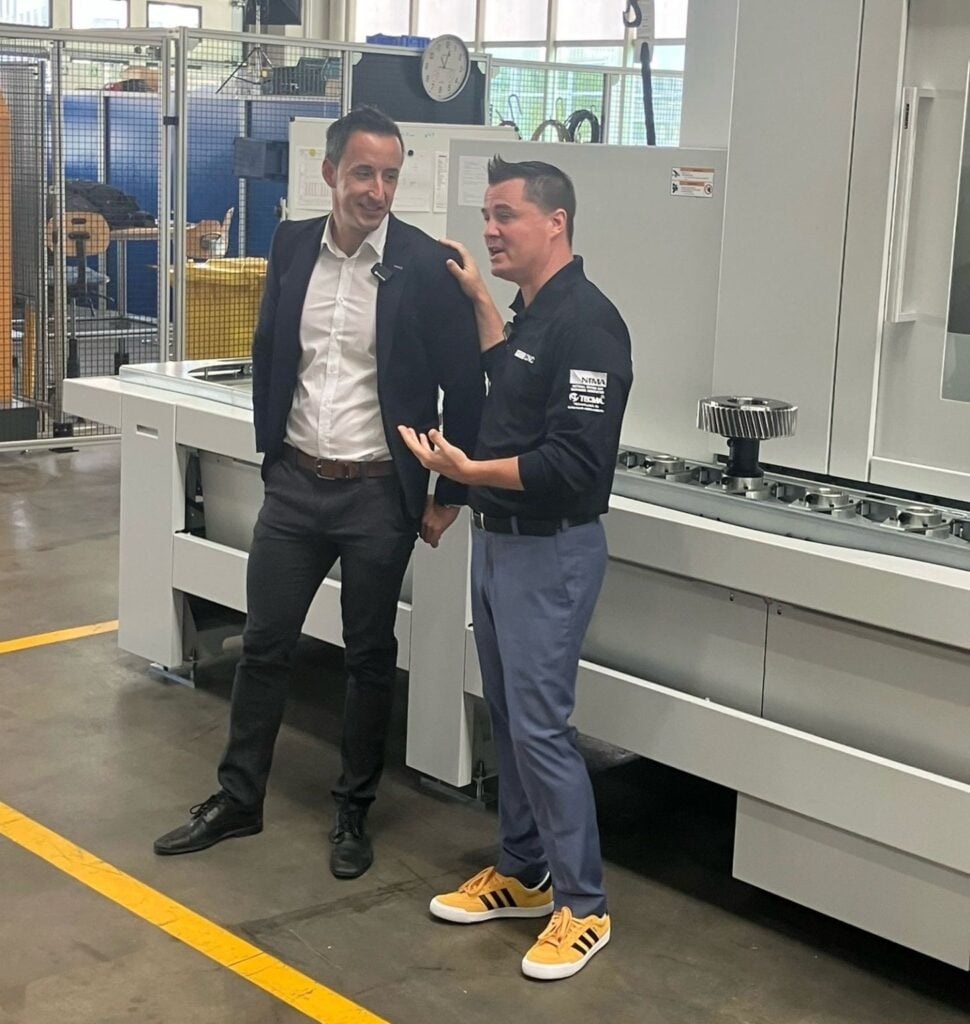
Today, Liebherr Kempten is less of a facility and more of a mechanical metropolis.
With over 145,000 square meters of total space—roughly 20 football fields—and 56,600+ square meters of covered production area, it’s a factory that looks like it could build the future…and it kind of does.
By 2024, the site employed 1,748 people, each contributing to the creation of gear-manufacturing solutions that power everything from aircraft to electric vehicles to offshore wind farms.
Whether it’s hobbing, shaping, profile grinding, or bevel gear machining, Liebherr doesn’t just manufacture machines—they engineer motion, making sure the modern world keeps turning, flying, and rolling.
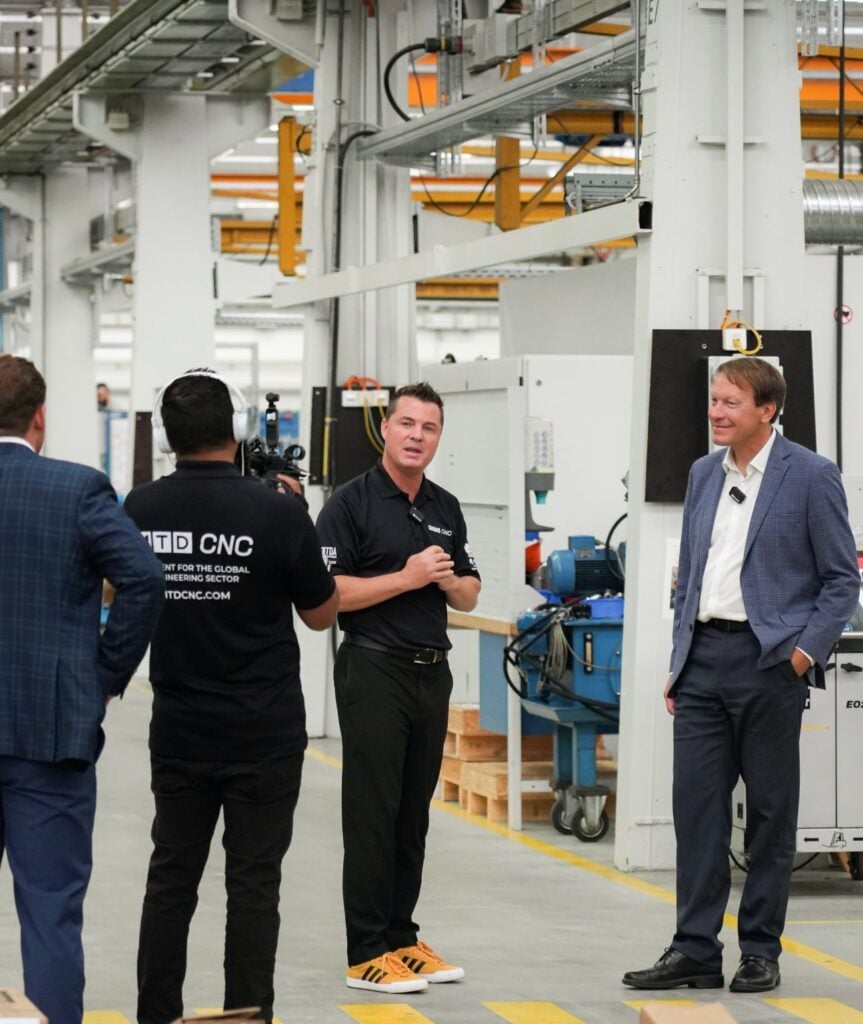
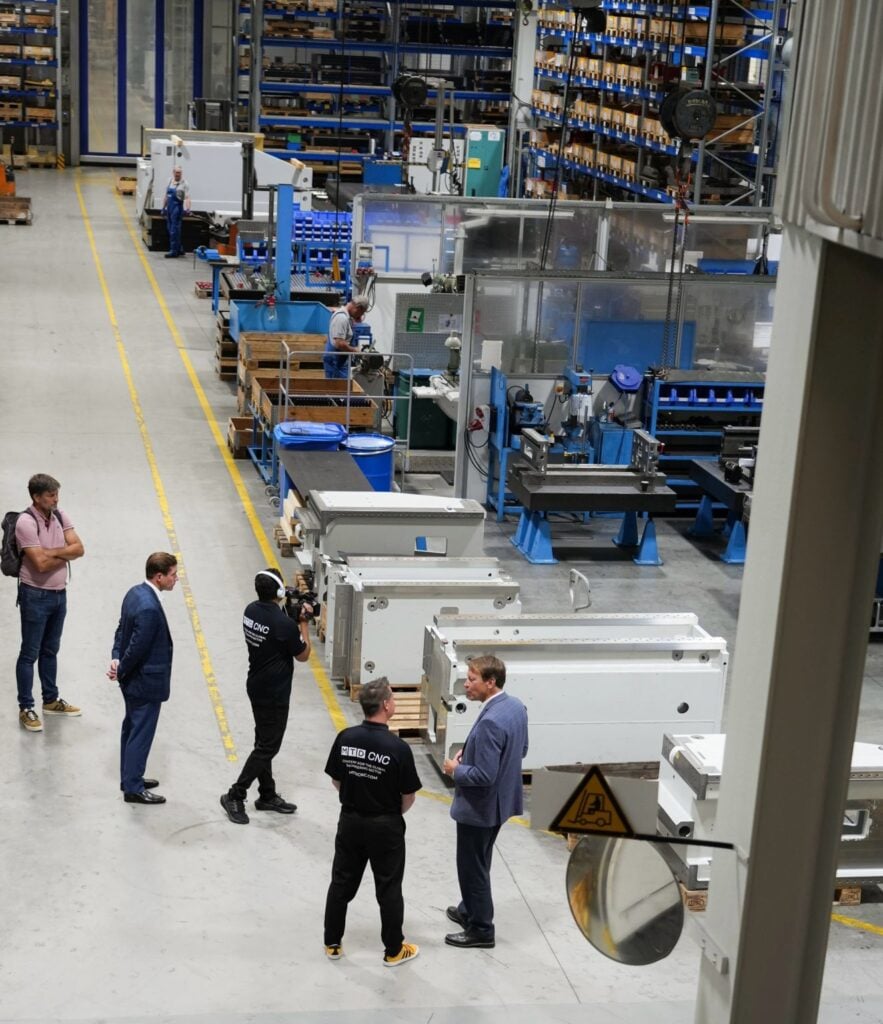
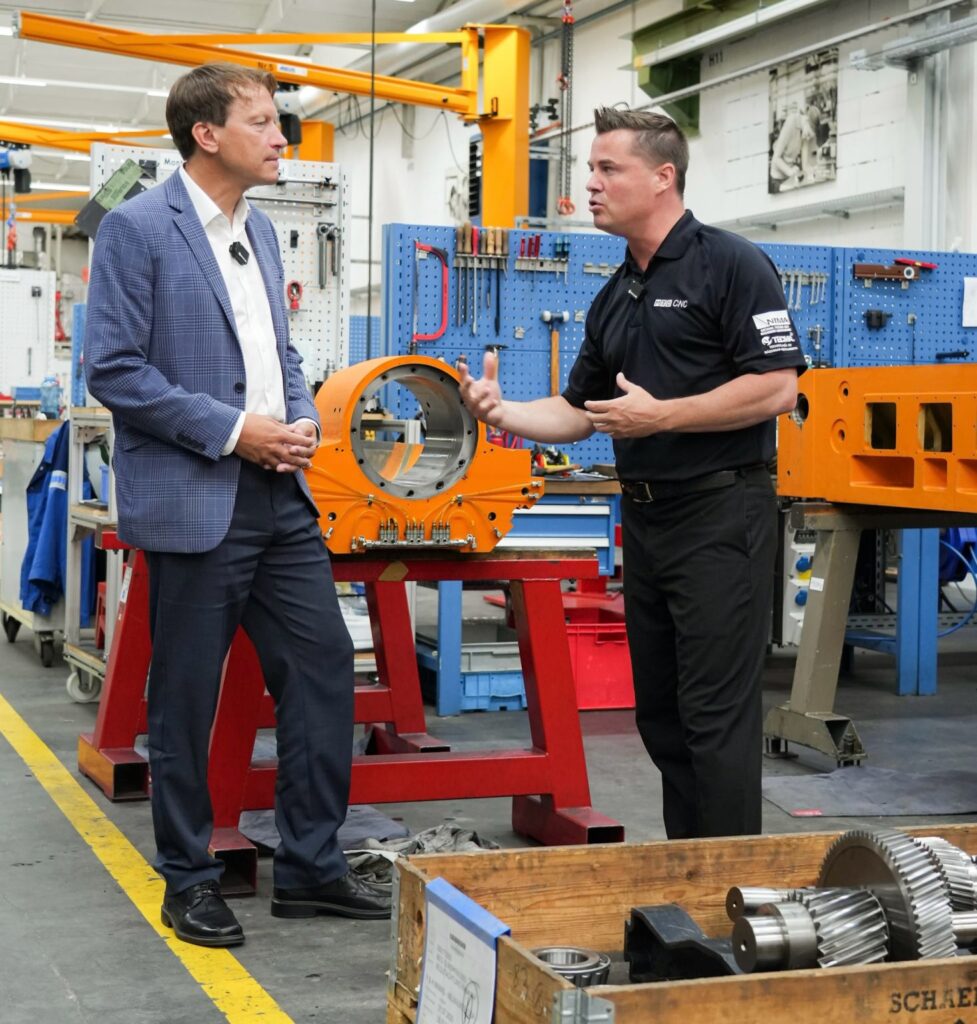
Oh, and let’s not forget their six-bay production hall completed in 2011—100m long, 150m wide, and 19m high. That’s enough room to build the kinds of machines that build the machines that build our world.
So, from all of us at MTDCNC: Danke schön, Liebherr. For showing us the art of precision and what it truly means to keep the world moving.
Catch Tony Gunn’s full tour of this epic facility right here on MTDCNC soon.
Guhring UK Unveils Comprehensive Milling Solutions
Guhring UK has launched a new range of milling tools designed for specific materials, delivering optimal performance across various industrial applications. The company, well-known in the manufacturing sector, is enhancing its product line to address the needs of machining industries working with diverse materials such as cast iron, steel, stainless steel, and aluminium.
The newly introduced milling solutions promise to improve efficiency and precision in manufacturing processes. Each tool is specifically crafted to tackle the unique challenges associated with different materials, offering tailored solutions that enhance productivity and minimize wear.
For cast iron, Guhring’s tools offer superior durability and chip evacuation capabilities, essential for maintaining cutting performance in demanding environments. Meanwhile, their steel-specific milling cutters are engineered to withstand high stress, ensuring longevity and consistent results.
When it comes to stainless steel, known for its toughness and work-hardening characteristics, Guhring provides tools designed to maintain sharpness and reduce the risk of thermal deformation. Additionally, their aluminium milling tools feature specialized geometries to prevent material build-up on cutting edges, a common issue when working with this lightweight metal.
The launch underscores Guhring UK’s commitment to innovation and excellence in the field of CNC machining. By catering to the specific demands of various materials, the company aims to support manufacturers in achieving higher precision and lower operational costs.
Guhring UK continues to strengthen its position as a leader in tool manufacturing, driven by a focus on quality and a comprehensive understanding of the complexities of modern industrial requirements. As the manufacturing landscape evolves, Guhring’s adaptive strategies and product innovations remain crucial for its sustained success.
GibbsCAM Unveils ToolManageriQ to Boost Manufacturing Efficiency
GibbsCAM, a prominent player in the computer-aided manufacturing software industry, has announced the release of a new datasheet highlighting the capabilities of their ToolManageriQ feature. Built specifically for GibbsCAM, ToolManageriQ aims to streamline and optimize manufacturing processes, making it an invaluable tool for professionals seeking to enhance their computer-aided manufacturing (CAM) workflow efficiency.
The datasheet, now available for download, details how ToolManageriQ integrates into the GibbsCAM environment. This innovation is poised to offer manufacturers advanced tool management solutions, potentially reducing time and resource wastage while maximizing productivity. As industries continue to shift towards digital manufacturing, the need for robust and efficient CAM solutions is more pressing than ever.
GibbsCAM’s focus on providing cutting-edge solutions is evident in its commitment to continuous improvement and addressing specific challenges faced by manufacturers. ToolManageriQ is designed to make tool management more intuitive, decreasing the complexity typically associated with CAM processes. It promises significant improvements in productivity by simplifying tool selection and management, aligning with the industry’s broader trend towards smarter, more integrated manufacturing systems.
The launch of ToolManageriQ comes at a crucial time as businesses seek to leverage digital tools to remain competitive. Companies can achieve increased efficiency and cost savings through optimized workflows, which are essential components in meeting the demands of modern manufacturing environments.
Manufacturers interested in exploring the capabilities of ToolManageriQ can access the datasheet through the link provided by GibbsCAM. This document will serve as a vital resource for businesses aiming to understand the practical benefits of enhanced tool management alongside GibbsCAM software.
GibbsCAM’s continuous innovation underscores its position as a leading provider of CAM solutions, tailored to meet the evolving needs of an ever-changing industrial landscape. By offering solutions like ToolManageriQ, the company reinforces its commitment to driving excellence and efficiency in manufacturing processes.
For more information and to download the ToolManageriQ datasheet, manufacturing professionals are encouraged to visit the GibbsCAM website.
FUCHS UK Showcases High-Performance Oils at NAPFM
FUCHS UK, a leading supplier in the lubrication sector, has further cemented its role in the BlueLight sector through its recent participation at the National Association of Police Fleet Managers (NAPFM) conference. The event, a key gathering in the UK for fleet management professionals, provided an ideal platform for FUCHS UK to exhibit its automotive and motorcycle engine oils, targeting enhanced fleet performance and protection.
The UK sales team took the opportunity to introduce attendees to the company’s flagship TITAN and SILKOLENE ranges. These products are engineered to deliver cutting-edge performance and reliability, crucial elements for fleet management, particularly in demanding sectors like emergency services.
FUCHS UK’s participation at NAPFM underscores its commitment to providing high-performance solutions that meet the rigorous demands of fleet managers. The TITAN range is known for its superior protection and efficiency, while the SILKOLENE series is specifically formulated for motorcycles, making them suitable for various service vehicles used within the BlueLight sector.
By meeting high-performance standards, FUCHS UK aims to assist fleet managers in safeguarding their vehicles and ensuring operational efficiency. Their oils are designed to extend engine life and improve reliability, critical factors in the uninterrupted service delivery expected in emergency contexts.
For those unable to attend the NAPFM conference, FUCHS UK has provided additional resources and information on their products online. Interested parties can explore the full range of offerings and detailed specifications tailored to various fleet types.
As an integral part of the FUCHS Group, which operates globally, FUCHS UK benefits from a wealth of research and development knowledge. This allows the company to continuously innovate and maintain its competitive edge in the lubrication market. The company’s focus on sustainability and advanced technology supports fleet operators in achieving their performance and environmental goals.
FUCHS UK’s role as an approved supplier to the BlueLight sector reflects its dedication to meeting the unique requirements of service fleets, ensuring safety and efficiency. This endorsement further enhances its reputation within the industry, affirming its position as a trusted partner for fleet managers across the UK.
The NAPFM show served not only as a showcase for FUCHS UK products but also as a testament to its commitment to serving the BlueLight sector with top-tier lubrication solutions, paving the way for a stronger association with emergency service fleet management.
HEIDENHAIN Launches UK Partner Service Network
HEIDENHAIN, a leading provider in precision measurement and control solutions, has announced the launch of its new PARTNER SERVICE Network across the United Kingdom and Northern Ireland. This initiative is set to enhance local access to sales, services, and support for HEIDENHAIN’s range of products, including TNC control systems, drives, motors, digital readouts, and both linear and rotary encoders.
The PARTNER SERVICE Network aims to provide manufacturers with faster response times and local expertise, ensuring that customers benefit from prompt and efficient service. With a network of trusted, expert partners, customers can expect the quality and precision that HEIDENHAIN is renowned for. The technicians within this network have been specifically trained by HEIDENHAIN, ensuring they are well-versed in the intricacies of the company’s technology.
In an industry where precision and reliability are critical, the availability of locally trained experts promises to be a significant advantage for manufacturing professionals. This strategic move is likely to reinforce HEIDENHAIN’s market position by offering tailored solutions and support, which are vital components in maintaining operational efficiency and product quality.
For technical and sales inquiries, customers are encouraged to contact the HEIDENHAIN UK sales team at the provided telephone number for assistance in finding the nearest local partner. This personalized approach highlights the company’s commitment to offering robust after-sales service, which is crucial in maintaining the integrity and performance of precision equipment.
HEIDENHAIN UK’s announcement is poised to strengthen the company’s footprint in the region, demonstrating their dedication to supporting the evolving needs of the manufacturing industry. By facilitating a more responsive and localized service, HEIDENHAIN underscores its commitment to excellence and innovation, which has been a hallmark of the company’s operations.
With its headquarters based in Germany, HEIDENHAIN has been at the forefront of developing highly accurate measurement and control technology, supporting various sectors including automation, automotive, and aerospace industries. The UK PARTNER SERVICE Network is the latest in its string of initiatives aimed at boosting accessibility and service quality for its expansive client base.
Grob Unveils Innovative Vario Rotary Table
Grob Machine Tools UK Ltd has announced the launch of its latest innovation, the Vario rotary table. This advanced piece of equipment is designed to meet diverse customer needs, offering both modularity and precision that is crucial in contemporary manufacturing environments.
The Vario rotary table is notable for its flexible design capabilities. It features a basic module that can be equipped with two highly dynamic, directly driven B-axes. This configuration allows for greater adaptability according to specific manufacturing demands.
One of the key advantages of the Vario rotary table is its independent B-axes, which significantly reduces stress during the roughing process. This independence also helps in minimizing component torsion during finishing, contributing to more accurate and efficient production cycles. The rotary table’s design is engineered to accommodate components up to 700 mm in blank length, thanks to its movable counter holder axle.
In addition to its flexible design, the Vario rotary table promises the highest surface quality. This is achieved through a stable design and optimized axle drives, which work together to ensure smooth and precise operations. These features make the Vario rotary table an attractive option for manufacturers seeking to enhance the quality and efficiency of their production processes.
The introduction of the Vario rotary table highlights Grob Machine Tools UK’s commitment to innovation and customer satisfaction in the machining industry. By offering solutions that address both flexibility and precision, the company continues to solidify its position as a leader in the field.
Grob Machine Tools UK Ltd, a prominent name in the manufacturing sector, has earned a reputation for delivering high-quality machine tools and services that cater to various industrial needs. With the unveiling of the Vario rotary table, the company is poised to provide even greater value to its clients worldwide.
For further information about the Vario rotary table and its applications, Grob Machine Tools UK Ltd has provided resources on their official platform, ensuring that interested parties can explore the full potential of this versatile product.
Hexagon and Thales Forge Strategic Partnership in EMEA
Hexagon’s Manufacturing Intelligence division has announced a strategic agreement with Thales Aerospace aimed at streamlining the supply chain of metrology equipment, software, services, and maintenance. This newly formalised partnership spans all Thales divisions across the Europe, Middle East, and Africa (EMEA) region, enhancing efficiency and standardising quality assurance processes.
The collaboration is designed to simplify procurement and expedite production capabilities for Thales, while ensuring consistency and traceability in their quality assurance protocols. By consolidating resources and expertise from Hexagon, Thales will be able to maintain high standards across its diverse operations. This alignment not only aims to boost productivity but also to enforce stricter quality control, reflecting both companies’ commitment to precision and reliability.
The agreement was officially signed at the International Paris Air Show, a premier event in the aerospace industry calendar. The signing ceremony saw the presence of Didier Perrigault, Global Expenses Procurement Director at Thales, and Stephen Chadwick, President of EMEA at Hexagon’s Manufacturing Intelligence division.
Both executives expressed enthusiasm about the collaboration, citing mutual benefits and the potential for innovation. Didier Perrigault noted that this agreement marks a significant step forward in Thales’ operations, as they leverage Hexagon’s advanced metrology solutions to enhance their manufacturing processes. Stephen Chadwick highlighted the strategic importance of this partnership, which aligns with Hexagon’s mission to deliver intelligent and sustainable manufacturing solutions.
This agreement not only reinforces Hexagon’s presence in the EMEA region but also underlines its strategic expansion into critical sectors like aerospace. The collaboration with Thales is a testament to Hexagon’s industry-leading capabilities in precision measurement and quality assurance.
Hexagon is known globally for its innovative manufacturing solutions, providing advanced technology that enhances productivity and efficiency. With operations in numerous countries, Hexagon focuses on integrating data, sensors, and technologies to create intelligent ecosystems.
Thales Aerospace, as a leader in aerospace innovation, continues to advance its technological and operational frameworks to meet the dynamic needs of the industry. This partnership with Hexagon is set to enhance Thales’ ability to deliver top-tier products and services to its clients, reinforcing its reputation for excellence and innovation.
The partnership between Hexagon and Thales is seen as a strategic alignment that will benefit both companies significantly. It represents a concerted effort towards operational excellence, setting new benchmarks in the aerospace manufacturing landscape.
Autodesk Leader Shares Career Growth Strategies
Natalie Ellis, a key figure at Autodesk, has shared insights into her profound career journey at the renowned company. With extensive experience across various roles, Ellis has transitioned from sales to developing leaders, offering a blueprint for professional growth.
Central to Ellis’s success is her emphasis on authenticity and genuine interest in others. She believes these qualities have been instrumental in expanding her professional network and enhancing her career. Her journey at Autodesk exemplifies how embracing these attributes can lead to significant opportunities for development within the manufacturing and industrial sectors.
Autodesk, a leader in software for the architecture, engineering, construction, manufacturing, media, and entertainment industries, provides an environment that fosters professional growth and learning. The company’s culture encourages employees to explore diverse roles and expand their skill sets, facilitating a vibrant space for innovation and leadership development.
Ellis’s approach aligns with Autodesk’s work philosophy. The company supports its employees in pursuing career progression through training, mentorship, and real-world experiences that encourage leadership skills. By promoting authenticity and meaningful connections, Ellis has set an example for aspiring leaders within the industry.
Manufacturing professionals and industry leaders looking to enhance their career trajectories can draw valuable lessons from Ellis’s experience. Her insights underscore the importance of building strong networks and engaging with colleagues on a genuine level—principles that are increasingly relevant in today’s interconnected work environment.
For those interested in learning more about Autodesk’s career opportunities and work culture, detailed information is available on the company’s official website. As Autodesk continues to innovate and lead in various sectors, the experiences of leaders like Ellis provide a compelling narrative of growth and potential.
This focus on leadership development is part of a broader strategy by Autodesk to maintain its status as an industry innovator. By cultivating leadership from within, the company ensures that its workforce is not only skilled but also aligned with its mission of driving progress through creativity and technology.
MSC Industrial Supply Co. UK team earns Great Place to Work Certification™ in 2025
MSC Industrial Supply Co. UK (MSC) is proud to announce that it has been Certified™ by Great Place to Work® for its outstanding workplace culture and impressive levels of employee satisfaction.
Awarded by the global authority on workplace culture and associate experience, the Great Place to Work Certification™ recognises organisations that demonstrate a commitment to fostering an exemplary employee experience. Based entirely on associate feedback, it illustrates MSC’s dedication to its ‘people first’ approach, with 85% of staff agreeing that it is a great place to work.
Through a culture and growth mindset built on collaboration, creativity, and camaraderie, the business has created an environment where employees feel valued, respected, and empowered in their chosen area. Meanwhile, MSC’s shared purpose ensures that each team member is aligned and working towards a common goal, with connectivity central to everything. All of this translates into a strong sense of belonging among teams, exceptional standards of customer service, and high levels of job satisfaction.
In addition to the UK division, both the Canadian and Mexican arms of MSC have also received Great Place to Work Certification™ for the first time, while the US business has achieved the accolade for a second consecutive year.
Speaking about the certification, Penny Davies, HR Director at MSC Industrial Supply Co. UK, said: ‘We are thrilled to be certified a Great Place to Work, which helps to cement our ‘people first’ approach. At MSC, our people really are at the heart of our business, and for them to have belief in our culture and purpose is just amazing.
‘We must now continue to focus on our people, ensuring we are attracting great candidates to our organisation, but also retaining the incredible talent we already have. However, it’s about mindset first, and we have our core attributes – thinking, creativity, connections and drive – all supported by accountability and selflessness. Skills can be taught, but having the right mindset is key.
‘Leadership is really important, and we want to create an environment where people feel recognised and have real purpose, with clear goals, direction, and support. This is all what makes our culture so special.
‘I am incredibly proud of all 220 people in the company for making this certification possible. Go Team MSC!’
For more information on MSC Industrial Supply Co. UK, please visit: https://www.mscdirect.co.uk/
SOLIZE, Farsoon, and Japan 3D Printer Join Forces to Drive Large-Format LPBF Adoption in Japan’s Automotive Industry!
In a bold step to advance industrial additive manufacturing in Japan, SOLIZE PARTNERS Co., Farsoon Technologies, and Japan 3D Printer Co., Ltd. have formed a strategic three-way alliance. This collaboration is focused on delivering cutting-edge large-format, open-platform Laser Powder Bed Fusion (LPBF) solutions to Japan’s automotive and manufacturing sectors—enabling faster innovation, smarter production, and greater design freedom.
Unveiled during the Next-Generation 3D Printer Expo held from July 9–11, 2025 at Makuhari Messe, the partnership highlights a strong synergy between the three companies. Japan 3D Printer, the exclusive distributor of Farsoon’s polymer PBF systems in Japan, brings deep technical and sales expertise. SOLIZE PARTNERS, a pioneer in Japan’s additive manufacturing landscape since the 1990s, contributes rich application knowledge and long-standing relationships with leading automotive OEMs. Farsoon Technologies, recognized globally for its scalable and high-performance LPBF machines, provides the technological backbone for this initiative.
The core focus of this collaboration is to accelerate the adoption of large-format LPBF solutions within Japan’s automotive industry. With the increasing demand for lightweight components, rapid prototyping, tooling, and complex geometries, Farsoon’s open-platform systems present a compelling solution. By combining Farsoon’s hardware innovation with SOLIZE’s end-to-end design and production expertise, the partnership aims to bridge the gap between prototyping and serial production in a more efficient and cost-effective manner.
Visitors to Japan 3D Printer’s booth (Hall 7, Booth 43-16) at the Expo witnessed live demonstrations of Farsoon’s LPBF technology and had direct access to experts from all three companies. These sessions offered insights into deployment strategies, materials innovation, and how to integrate additive manufacturing into existing production lines.
This partnership not only delivers industrial-scale 3D printing capabilities but also provides localized implementation support, a key factor for success in the Japanese market. Farsoon’s open material platform further enhances flexibility by allowing users to select from a wide range of materials, reducing costs and encouraging material experimentation.
With this collaboration, SOLIZE, Farsoon, and Japan 3D Printer are positioning themselves at the forefront of Japan’s digital manufacturing transformation. By providing manufacturers with powerful tools, deep domain expertise, and scalable solutions, they are setting the stage for a new era of agile, efficient, and intelligent product development in Japan’s automotive sector and beyond.
BEACON and Leo AI Launch India’s First AI Copilot for Mechanical Design—Redefining Engineering Workflows in Bengaluru, Pune, and Mumbai!
In a groundbreaking step for India’s engineering design landscape, BEACON, a premier engineering solutions provider and SOLIDWORKS partner, has teamed up with Leo AI to unveil the world’s first AI-powered mechanical design copilot. This next-generation tool, developed specifically for engineers, was showcased during a series of high-impact launch events across Bengaluru (July 8), Pune (July 9), and Mumbai (July 11)—drawing enthusiastic participation from CXOs, product designers, and mechanical engineers across India.
Leo AI stands apart from traditional AI platforms with its Large Mechanical Model (LMM)—a proprietary AI trained on over a million industry-specific documents including ISO standards, technical manuals, and engineering handbooks. Unlike generic AI tools, Leo AI delivers real-time, context-aware assistance directly within CAD environments like SOLIDWORKS, dramatically streamlining the product development process.
Key features include:
- Seamless SOLIDWORKS Integration for context-sensitive suggestions and smart automation.
- Text-to-3D Conversion, transforming sketches or descriptions into accurate 3D models and datasheets.
- Up to 70% Reduction in early-stage design time through automation of repetitive tasks.
- Error Prevention via real-time rule-based checks during the design phase.
- Enterprise-Ready Security, including on-premise deployment options for IP-sensitive organizations.
The three-city launch tour—part of BEACON’s CXO Innovation Forum—featured keynote sessions by Mr. Sean Manzanares, Head of Global Sales at Leo AI, and Mr. Arumuga Nainar Ramaswamy, CEO of BEACON. Live demos showcased how Leo AI is transforming the way mechanical engineers design, collaborate, and innovate.
“Leo AI is not just a tool—it’s a game-changing copilot redefining the future of mechanical design,” said Sean Manzanares.
“The overwhelming response from the Indian engineering community shows that the industry is ready for intelligent, AI-driven workflows,” added Arumuga Nainar Ramaswamy.
Already trusted by over 50,000 engineers worldwide at organizations like Bosch, Intel, MIT, and Toyota, Leo AI has generated over 100,000 AI-driven design concepts to date. Now, through its exclusive collaboration with BEACON, this transformative platform is accessible to India’s growing base of MSMEs, OEMs, and startups.
The successful launch of Leo AI marks a paradigm shift in India’s engineering capabilities, accelerating design innovation, shortening time to market, and elevating the competitiveness of Indian manufacturers on the global stage.
DN Solutions Unveils the PV 6300 Series: Bridging the Gap in Heavy-Duty Vertical Turning Solutions!
DN Solutions, South Korea’s powerhouse in machine tool manufacturing and the world’s third-largest CNC brand, has introduced a new benchmark in vertical turning technology—the PV 6300 Series. Officially launched from its Changwon headquarters, this new vertical turning center (VTC) is designed to deliver exceptional productivity, precision, and flexibility, especially for heavy-duty industrial applications.
Building upon the success of its established PV series—including the PV 400 and PV 9300—the PV 6300 addresses the critical size gap between the two models. It’s engineered to meet the growing demand for mid-to-large workpiece machining across the automotive, oil & gas, and energy sectors, providing manufacturers with a reliable and efficient solution for their evolving needs.
What sets the PV 6300 apart is its reinforced spindle motor, capable of delivering greater output and torque than its peers, enabling powerful, stable machining of large, heavy materials. For customers requiring even more cutting force, an optional high-torque spindle can be integrated seamlessly.
At the heart of its precision performance lies a rigid bed structure with box guideways that absorb vibrations, maintaining machining accuracy even during prolonged operations. For added versatility, the PV 6300M variant introduces milling capabilities, transforming the machine into a multitasking platform ideal for complex turning-milling operations.
Recognizing the need for automation on modern shop floors, DN Solutions has made the PV 6300 compatible with ROBOSOL, its proprietary robotic cell solution. This integration enables coordinated operation of multiple machines, boosting productivity through lights-out, unmanned manufacturing.
An Automatic Tool Changer (ATC) comes standard, further enhancing operational efficiency and enabling continuous production cycles with minimal human intervention.
DN Solutions emphasized its commitment to innovation with this launch:
“As demand increases for heavy-duty machining in the automotive and energy sectors, we’re proud to introduce a high-performance vertical turning center that incorporates our latest technologies.”
This launch reinforces DN Solutions’ reputation as a pioneer in smart manufacturing. With over 290,000 machines sold across 66 countries and a global support network of 140+ service and sales offices, the company continues to lead the charge in CNC machining, factory automation, and now, metal additive manufacturing.
For those looking to enhance their shop’s machining capabilities with a rugged, feature-rich VTC, the PV 6300 Series represents the next step in performance, reliability, and automation readiness.
Hexagon’s ESPRIT Edge Empowers Swiss-Type Machining with AI-Driven Precision and Productivity Boost!
Hexagon Manufacturing Intelligence has unveiled a game-changing update to its ESPRIT Edge CAM software, bringing advanced Swiss-type machining capabilities and AI-powered tools to the forefront of modern manufacturing. Designed to tackle the increasing complexity of multi-axis machine programming and the widening skills gap in precision machining, the latest release—ESPRIT Edge 2025.2—marks a pivotal step in making high-performance Swiss machining more accessible, efficient, and scalable.
For the first time, ESPRIT Edge introduces robust support for Swiss-type lathes, including complex platforms like the Citizen L-series and Star SR-series. At its core is a high-fidelity digital twin, offering real-time, collision-free simulation and intelligent control over key machine functions such as superimposition, composite axis synchronization, and automatic prepositioning. These enhancements allow manufacturers to streamline setup, eliminate trial-and-error, and optimize throughput while maintaining precision and safety.
Complementing its machine control capabilities, ESPRIT Edge simplifies hardware configuration with intuitive tools for collet, guide bushing, and tool mounting block setup. Features like automatic synchronization, adaptive machining cycles, and tilted plane rotation further reduce manual programming and help shops efficiently manage multichannel operations, cutting down cycle times and minimizing errors.
What truly sets ESPRIT Edge 2025.2 apart is its seamless integration with Hexagon’s cloud-based Nexus platform, which delivers AI-powered services to automate tasks and guide programmers:
- Hexagon Copilot: A smart, 24/7 virtual assistant that leverages natural language processing to offer expert advice, programming support, and contextual insights within the ESPRIT Edge interface—ideal for both seasoned and novice users.
- ProPlanAI: A self-learning process planning tool that uses historical machining data to optimize programs for new parts, reducing manual input and accelerating time-to-production.
Together, these AI tools democratize advanced machining by shortening training times, enhancing programming consistency, and enabling new users to achieve expert-level productivity with minimal ramp-up.
Tailored G-code output eliminates the need for postprocessor customization, ensuring seamless execution on OEM-specific machines. With a focus on standardization, simulation accuracy, and workflow reliability, ESPRIT Edge enables manufacturers to embrace complex Swiss machining without being hindered by technical limitations or resource constraints.
With the launch of ESPRIT Edge 2025.2, Hexagon not only addresses the legacy challenges of Swiss-type programming but also lays the groundwork for a smarter, more agile future in CAM—where innovation, precision, and productivity work hand-in-hand to drive manufacturing success.
Armstrong Dematic Showcases Cutting-Edge Warehouse Automation at India Warehousing Show 2025!
Armstrong Dematic, a leader in intelligent warehouse automation and material handling solutions, stole the spotlight at the India Warehousing Show 2025, held from June 26–28 at Yashobhoomi, Delhi, by unveiling two of its most advanced innovations: the Asterope 4D Robot ASRS and Rigel PT: The Forklift AMR. These next-generation solutions underscore the company’s ongoing commitment to redefining supply chain efficiency, precision, and adaptability in a rapidly digitizing logistics landscape.
The live demonstrations at the event generated considerable buzz, drawing in supply chain professionals, automation experts, and business leaders eager to witness the future of warehousing in action. Armstrong Dematic’s showcase provided attendees with an immersive experience, demonstrating how intelligent automation can unlock new levels of operational excellence, scalability, and safety—particularly in the context of booming e-commerce, omni-channel fulfilment, and high-velocity inventory environments.
The Asterope 4D Robot ASRS impressed with its advanced load management and AI-driven decision-making, offering real-time inventory tracking and seamless sequencing capabilities. Designed to optimize space and throughput, this automated storage and retrieval system integrates smart algorithms and business intelligence to enhance warehouse responsiveness and reduce human error.
Equally captivating was the debut of Rigel PT, Armstrong Dematic’s Forklift Autonomous Mobile Robot (AMR). Purpose-built for navigating dynamic and complex warehouse layouts, Rigel PT boosts throughput and safety while offering high-precision material handling—without the need for manual intervention. Its robust navigation and obstacle avoidance systems position it as an ideal solution for businesses seeking to scale operations with minimal disruption.
Armstrong Dematic’s presence at the show wasn’t just about showcasing products—it was about building partnerships. Their booth became a knowledge-sharing hub where company experts engaged one-on-one with visitors to explore tailored solutions that address unique operational challenges. From optimizing manpower to reducing errors and improving ROI, the conversations highlighted the brand’s customer-first mindset.
Commenting on the company’s vision, Chairman Vineet Majgaonkar remarked, “We go beyond automation. Our goal is to be long-term strategic allies for our clients by providing sustainable, high-impact solutions that drive operational excellence and business growth.”
With decades of domain expertise and a strong focus on eco-friendly, future-ready technologies, Armstrong Dematic continues to lead the charge in transforming warehouse ecosystems. Their solutions blend smart hardware with intelligent software, ensuring that customers stay ahead in an era where supply chain agility and digital transformation are non-negotiable.
As warehousing and logistics industries evolve at breakneck speed, Armstrong Dematic’s innovation-led showcase at India Warehousing Show 2025 served as a powerful testament to its role in shaping the future of intelligent, efficient, and resilient supply chain infrastructure.
Priya Nair Appointed CEO and MD of Hindustan Unilever, Ushering a New Era of Leadership from August 1!
Hindustan Unilever Ltd (HUL), one of India’s largest fast-moving consumer goods (FMCG) companies, has announced the appointment of Priya Nair as its new Chief Executive Officer and Managing Director, effective August 1, 2025, for a term of five years. This landmark appointment marks a significant leadership transition and underscores HUL’s ongoing commitment to strengthening its innovation-driven and consumer-centric growth strategy.
Priya Nair will succeed Rohit Jawa, who will step down from his role on July 31, 2025, after a successful tenure that began in 2023. According to the company, Mr. Jawa will be exploring new opportunities in both his professional and personal life. Under his leadership, HUL navigated complex market dynamics and delivered steady, volume-led growth, even amidst external economic pressures. “Rohit’s time at HUL was marked by strategic clarity and a sharper portfolio focus,” said Nitin Paranjpe, Chairman of HUL. “We thank him for his leadership and the strong position in which he leaves the company.”
Priya Nair brings with her an impressive 30-year journey with Unilever, having joined HUL in 1995. She has held several leadership roles across home care, personal care, and beauty segments. Notably, she served as Executive Director of Home Care (2014–2020), then went on to lead the Beauty & Personal Care business from 2020 to 2022. Her exceptional track record earned her a global mandate as Global Chief Marketing Officer for Unilever’s Beauty & Wellbeing division. Since 2023, she has been serving as President of Beauty & Wellbeing at Unilever globally—overseeing brand innovation and market strategies across international markets.
In her new role, Ms. Nair will also join the Board of Directors of HUL, pending regulatory approvals, and will continue to be part of Unilever’s global leadership team, further strengthening the integration of HUL’s India strategy within the broader global vision.
Commenting on the appointment, Chairman Nitin Paranjpe said, “Priya brings a wealth of experience and deep market insight. Her strong leadership will help drive HUL’s continued growth and innovation.” Her consumer-first approach, strategic brand building expertise, and global exposure are expected to play a pivotal role in navigating HUL through its next growth phase—particularly in evolving areas such as sustainable products, health & wellness, digital transformation, and inclusive innovation.
With operations spanning food & beverages, home care, personal care, and health & wellness, HUL remains a household name in India, known for its iconic brands and deep-rooted consumer trust. As the company prepares for this seamless transition, the leadership of Priya Nair signals not just continuity but also renewed momentum for innovation, purpose-driven growth, and inclusive leadership in India’s dynamic FMCG landscape.
HSG Laser Deepens India Commitment with Expanded Local Operations and Technology Tailored for Domestic Manufacturing!
HSG Laser, a global leader in intelligent laser cutting and automation solutions, has announced a major expansion of its localization efforts in India, reinforcing its long-term commitment to supporting the country’s manufacturing ambitions. Following a strong showing at ACMEE 2025, the company is accelerating its investment in local talent, infrastructure, and customized technology to deliver greater value to Indian manufacturers.
HSG’s India strategy is rooted in a deeply localized approach, focused on aligning its solutions with the specific operational realities and growth goals of India’s industrial ecosystem. Central to this initiative is the recruitment, training, and upskilling of Indian professionals, including engineers, technicians, and after-sales service personnel. This human capital investment ensures HSG’s customers benefit from faster response times, on-ground technical expertise, and reliable service support.
In tandem with talent development, HSG is customizing its advanced technology solutions for Indian production environments. Innovations include intelligent bevel cutting systems, smart nesting software for maximizing material utilization, and high-power fiber laser machines designed for the demanding needs of sectors like automotive, fabrication, electronics, and heavy machinery. These technologies not only enhance production efficiency but also empower Indian manufacturers to achieve world-class performance standards.
To anchor its long-term presence, HSG is executing a phased regional expansion strategy. This includes the establishment of new technical support centers, spare parts warehouses, and training facilities in major industrial zones across India. These investments are intended to build a responsive and reliable service ecosystem that supports customers from installation through ongoing operations, thereby reducing downtime and increasing productivity.
“Our journey in India began in 2012, and we see it as a long-term partnership,” said the Head of HSG India. “We are committed to going beyond product sales. Our goal is to become a true technology ally for Indian manufacturers. With operational spare parts centers already in Bangalore and Chennai, we’re significantly reducing turnaround times and elevating service delivery. We will continue investing in people and infrastructure to strengthen India’s industrial backbone.”
HSG Laser’s localization push comes at a time when India is scaling up its efforts to become a global manufacturing powerhouse. Strategic collaborations with forward-thinking technology providers like HSG will play a vital role in enhancing domestic productivity, technical know-how, and global competitiveness. By embedding itself more deeply in the Indian market, HSG is not only delivering cutting-edge machinery but also enabling the Make in India vision with sustained, ground-level impact.
Kinetic Communications Unveils Fully Automated Controller Manufacturing Line in Pune, Elevating India’s EV Electronics Capabilities!
In a bold move towards embracing Industry 4.0 and reinforcing India’s position in global EV electronics manufacturing, Kinetic Communications has inaugurated a fully automated controller manufacturing line at its state-of-the-art facility in Pune. This advanced production line is engineered to deliver high-throughput, precision manufacturing of Motor Controller Units (MCUs)—critical components that manage the interaction between the battery and motor in electric vehicles, controlling acceleration, braking, and overall energy efficiency.
The manufacturing setup integrates cutting-edge Surface Mount Technology (SMT) and automated assembly systems, managed through a combination of Human Machine Interface (HMI) and Programmable Logic Controllers (PLCs). This digital ecosystem ensures real-time process control, seamless data traceability, and near-zero manual intervention, resulting in significant reductions in errors while maximizing production efficiency.
The new line not only produces MCUs but also manufactures Power and Driver Board Assemblies and Complete Controller Box Assemblies. These components go through a meticulous validation process, including software flashing, IP67 leak testing, and functional testing—ensuring they meet stringent quality and durability benchmarks. Currently operating at a capacity of 300 units per shift, the plant is equipped to scale up to an annual output of 180,000 units under two shifts, reinforcing its role as a high-volume production powerhouse.
To guarantee world-class quality, the facility incorporates advanced testing tools such as 3D Solder Paste Inspection, Automated Optical Inspection (AOI), and In-Circuit Testing for comprehensive electrical validation. It uses lead-free dual-wave soldering technology for through-hole components and employs robust Poka Yoke mechanisms to eliminate the possibility of human error. With synchronized HMI-PLC integration, every production station ensures smooth digital communication and traceable software implementation.
Each unit undergoes End-of-Line Testing and Pre-Dispatch Inspection (PDI), while Incoming Quality Control (IQC) aligns with JESD22 reliability standards, validating the performance of every component. The ultimate goal: zero PPM defects, increased productivity, elevated customer satisfaction, and cost optimization through smart automation.
Ajinkya Firodia, Vice Chairman of Kinetic Group, emphasized the transformational nature of this launch: “The new fully automated controller line marks a significant stride toward Industry 4.0-driven smart manufacturing. It’s a high-throughput, precision-engineered facility that brings intelligence, speed, and scalability to our operations. Every stage is data-driven and benchmarked to global quality standards. This is more than a technological leap—it’s a statement of our commitment to innovation and operational excellence.”
Echoing this sentiment, Deepak Shikarpur, Director of Kinetic Communications Ltd, added, “This facility is a true reflection of Make in India at its most advanced. With its automation, precision, and capability to manufacture smart, feature-rich motor controller units, it positions India on the global map for next-generation EV electronics manufacturing.”
With this milestone, Kinetic Communications sets a new benchmark in smart manufacturing, reinforcing its role as a pioneer in India’s electric mobility ecosystem and showcasing how advanced automation can drive both quality and scale in future-ready production systems.
Arrow Electronics Launches Engineering Solutions Centre in Bangalore to Power Next-Gen Innovation Across Asia!
In a major boost to the technology ecosystem in India and the wider Asia-Pacific region, Arrow Electronics has inaugurated its new Engineering Solutions Centre (ESC) in Bangalore. This strategic initiative is designed to empower companies in India, Southeast Asia, South Korea, and Japan by making critical technologies like AIoT, edge computing, intelligent sensing, and system-level design more accessible and actionable.
The ESC marks a significant expansion of Arrow’s engineering capabilities in Asia and aims to strengthen innovation pipelines across sectors such as industrial automation, automotive, aerospace, transportation, defence, and energy. By supporting regional companies at every stage of the product development lifecycle, the ESC is set to become a critical enabler for organizations navigating the increasingly complex demands of digital transformation.
Dr. Raphael Salmi, President of Arrow Electronics’ Components Business for South Asia, Korea, and Japan, highlighted the importance of this initiative: “By leveraging our global network of resources, deep engineering expertise, and strong local presence, Arrow acts as a trusted technology partner, bridging the gap between innovation and execution.”
The centre is staffed with skilled application engineers who provide end-to-end support in design engineering, helping customers move from concept to production with greater speed, confidence, and cost-efficiency. Core services include:
- Component Engineering & System Design
- Reference Design Solutions
- Bill-of-Materials (BOM) Optimisation
- System-Level Design Reviews
- Technology Selection Support for MCU/MPU/FPGA, SoC, wireless connectivity, power, analog, and IP&E components
This holistic approach ensures that product developers, OEMs, and startups alike can access the critical tools, guidance, and technical know-how required to accelerate innovation and meet market demands.
Located in Bangalore—India’s tech innovation capital—the ESC will also serve as a key platform for cross-border collaboration between engineering teams across Arrow’s global network and regional clients, fostering a culture of knowledge-sharing and co-creation.
With this new Engineering Solutions Centre, Arrow Electronics reaffirms its commitment to becoming a driving force behind Asia’s growing technology landscape, offering businesses the engineering muscle and insights needed to turn bold ideas into world-class products.
Škoda Auto Volkswagen India Launches Bentley India, Expands Portfolio to Ultra-Luxury Segment!
Škoda Auto Volkswagen India Private Ltd (SAVWIPL) has taken a bold leap into the ultra-luxury automotive segment by officially adding Bentley to its brand portfolio. Effective 1 July 2025, SAVWIPL will handle import, distribution, and servicing of Bentley vehicles across India under a newly established entity—Bentley India. This move positions Bentley as the sixth marque under SAVWIPL’s growing umbrella, joining Volkswagen, Škoda, Audi, Porsche, and Lamborghini.
At the helm of this new chapter is Abbey Thomas, who will lead Bentley India’s strategic direction and retail network expansion. His extensive experience in the Indian automotive market makes him ideally suited to guide Bentley’s foray into a territory where demand for exclusivity, heritage, and ultra-premium experiences is on a rapid rise. SAVWIPL will retain full responsibility for marketing, sales, and after-sales operations, ensuring consistent service quality and brand alignment across all touchpoints.
To bring the essence of British luxury and craftsmanship to India’s Ultra High Net Worth Individuals (UHNI), Bentley India will launch three flagship dealerships in Mumbai, New Delhi, and Bengaluru. These hubs will deliver Bentley’s hallmark combination of performance, timeless design, and customisation to a clientele that expects nothing less than the extraordinary.
Piyush Arora, Managing Director and CEO of SAVWIPL, expressed pride in this milestone move, stating, “Welcoming Bentley into the SAVWIPL family is a proud milestone that completes our portfolio — from the precision of German engineering to the timeless elegance and unmatched performance of British craftsmanship. India’s appetite for uncompromising luxury is growing rapidly. Additionally, Abbey’s deep understanding of the Indian market makes him the ideal leader to steer Bentley India toward new milestones.”
The integration of Bentley into SAVWIPL’s operations comes at a time when India’s UHNI population is expanding rapidly, driving a surge in demand for personalized and prestigious automotive experiences. Jan Bures, Executive Director, Sales, Marketing and Digital at SAVWIPL, reinforced this sentiment, stating, “The ever-growing UHNI segment in India will benefit from this new association, and we, along with our new dealer partners, will ensure the best of luxury and performance for our customers.”
With Bentley India now part of its comprehensive brand portfolio, Škoda Auto Volkswagen India is uniquely positioned to cater to every segment of the Indian automotive market—from mass-market offerings to the absolute pinnacle of automotive luxury. This launch not only strengthens the group’s brand equity but also reflects the shifting dynamics of India’s luxury automobile landscape, where global icons like Bentley are finding a thriving audience.
BMW Group India Appoints Hardeep Singh Brar as New President & CEO, Signalling Fresh Growth Momentum!
In a strategic leadership move aimed at accelerating its expansion in one of its fastest-growing global markets, BMW Group India has appointed Hardeep Singh Brar as its new President and CEO, effective 1 September 2025. This significant transition marks a new chapter for the German luxury automaker in India, as Brar takes the reins from Vikram Pawah, who will be relocating to head BMW Group Australia and New Zealand.
This leadership realignment underscores BMW’s long-term commitment to the Indian market and its ambitions to deepen its presence in the region. Jean-Philippe Parain, Senior Vice President for Asia-Pacific, Eastern Europe, Middle East, and Africa, highlighted India’s pivotal role in the BMW Group’s strategic roadmap. He noted that Brar’s seasoned industry experience and nuanced understanding of Indian market dynamics make him ideally positioned to lead the next phase of BMW’s growth story in the country.
Brar brings to the table over 30 years of leadership experience across top-tier automotive brands including Maruti Suzuki, Volkswagen, General Motors, Nissan, Great Wall Motors, and most recently Kia India, where he served as Senior Vice President – Sales and Marketing. His expansive career spans critical verticals such as sales, marketing, customer experience, dealer development, and corporate strategy. A Mechanical Engineering graduate from Thapar Institute of Engineering and Technology, Brar further honed his leadership skills at Harvard Business School’s Senior Executive Leadership Program.
His appointment comes at a time when BMW India is scaling operations with an increased focus on local assembly, premium product offerings, electric mobility, and digital transformation. Under Vikram Pawah’s leadership since 2017, BMW India achieved major milestones, including a stronger foothold in the luxury segment, deeper localization efforts, and the launch of cutting-edge EVs and digital retail platforms. His dual role in India and Australia helped align cross-market strategies and strengthen BMW’s regional presence.
BMW Group India’s operations span across its luxury car brand BMW, lifestyle brand MINI, and premium motorcycle division BMW Motorrad. Since its inception in 2007, the Indian arm has built a strong local ecosystem, including a manufacturing facility in Chennai, a distribution center in Pune, a training academy in Gurugram, and a robust dealership network across major metropolitan cities. Ten BMW models are locally assembled in India, while MINI and Motorrad continue to carve out their own niche customer bases in the market.
With Hardeep Singh Brar stepping into this pivotal role, BMW Group India is set to enter a new era of innovation, localization, and consumer-focused growth, aimed at reinforcing its position as a leader in the Indian luxury automotive space.
Elektrobit Unveils EB tresos AutoCore Light: Powering Smarter, Scalable Peripheral ECU Integration for Software-Defined Vehicles!
In a significant leap toward enabling more intelligent and cost-effective vehicle electronics, Elektrobit has launched EB tresos AutoCore Light, a lightweight yet powerful software solution crafted specifically for peripheral ECUs like smart sensors and actuators. Tailored for the evolving demands of Software-Defined Vehicles (SDVs), this new offering empowers OEMs to streamline the integration of distributed vehicle components within modern zonal and domain E/E architectures—all while slashing development costs and complexity.
At its core, EB tresos AutoCore Light is scalable, modular, and designed for resource-constrained environments, making it ideal for microcontroller-based ECUs that don’t require heavy compute capabilities. Built to support signal-based communication, the solution is ASIL-B ready and CSMS certified, ensuring a high standard of functional safety and cybersecurity compliance across applications.
A defining advantage lies in its modular architecture, which promotes code reuse, simplifies software updates, and significantly shortens development timelines. This is particularly crucial for automakers transitioning from traditional monolithic ECU frameworks to zonal architectures, which centralize computing power while distributing simpler peripheral ECUs throughout the vehicle.
The new software also aligns with Elektrobit’s existing portfolio—EB tresos AutoCore and EB zoneo—which serve as the foundation for zonal ECUs. When combined, these tools offer a comprehensive software stack that enables OEMs to consolidate functionality, standardize designs, and reduce E/E hardware and R&D costs by up to 30% compared to traditional AUTOSAR-based implementations.
Peripheral ECUs powered by EB tresos AutoCore Light can run efficiently on smaller MCUs, like Cortex M0+ and M4F, leading to reduced hardware costs without sacrificing performance or compliance. Additionally, OEMs have the flexibility to tailor solutions with extension packages and add-on components, including protocols like J1939 and DLT, to cater to diverse automotive use cases.
Jagan Rajagopalan, Head of Strategy & Portfolio at Elektrobit Automotive GmbH, highlighted the significance of this release: “The Software-Defined Vehicle is a complex ecosystem, and EB tresos AutoCore Light offers a smart, efficient entry point for customers aiming to build scalable, future-ready software. Tailored for resource-constrained peripheral ECUs, it breaks away from traditional monolithic architectures with a lightweight, modular design. By building on proven EB tresos AutoCore components, it empowers customers to accelerate development, reduce integration complexity, and confidently scale their SDV strategies.”
Currently available for select Cortex M0+ and M4F microcontroller platforms, EB tresos AutoCore Light represents a vital addition to Elektrobit’s forward-thinking software suite, helping automakers build the vehicles of tomorrow—smarter, faster, and with greater efficiency. Further platform support and updates are expected later this year.
Audi India Unveils Smart Dash Cam: 24/7 Vehicle Security with Cutting-Edge Tech for All Models!
Audi India has taken a significant step toward enhancing vehicle safety and customer confidence with the launch of its new Audi Dash Cam, a state-of-the-art surveillance system offering intelligent, round-the-clock protection. Designed for both existing and new Audi models, this compact yet powerful device ushers in a new era of smart mobility and automotive security.
Priced at ₹68,000, the Audi Dash Cam is more than just a camera—it’s a vigilant co-pilot. Equipped with QHD video resolution, motion and impact detection, and intelligent battery protection, it operates seamlessly whether the car is in motion or parked. The camera records footage directly to an SD card and connects effortlessly to a dedicated mobile app available on both iOS and Android platforms. This ensures Audi owners can remotely access video recordings at any time, offering real-time updates and instant incident reviews from anywhere.
One of the most noteworthy features is the parking surveillance mode, which activates automatically upon detecting motion or impact while the vehicle is stationary. This functionality offers robust protection against potential hit-and-run incidents or acts of vandalism—an essential feature for urban drivers and high-traffic environments.
For drivers on the move, the dash cam functions as an unbiased witness, capturing driving footage that can prove invaluable in insurance claims or legal matters. It also helps deter fraudulent accident claims by providing clear, timestamped evidence—thereby reinforcing Audi’s reputation for safety, trust, and innovation.
Speaking about the launch, Balbir Singh Dhillon, Head of Audi India, stated, “The Audi Dash Cam represents our unwavering dedication to integrating advanced safety technologies into the Audi experience. It brings peace of mind to our customers, ensuring their vehicle is protected around the clock, regardless of whether it’s on the road or parked. With smart recording and seamless connectivity, this dash cam sets new benchmarks in automotive security.”
The Audi Dash Cam can be retrofitted into older Audi models and is also available as an add-on for new purchases. It is now available across all Audi dealerships in India, reinforcing the brand’s customer-centric approach and focus on delivering advanced, value-added features.
Whether you’re an Audi enthusiast or a daily commuter, this smart dash cam ensures that your luxury ride is guarded at all times—elevating safety from a feature to a promise.
Italian Machine Tool Industry Eyes Modest Recovery in 2025 After Difficult Year
After a turbulent 2024, Italy’s machine tool, robotics, and automation industry is cautiously optimistic about 2025, anticipating a slight recovery across key performance indicators. Despite a sharp contraction in the domestic market last year, the sector maintained its global relevance, ranking fifth worldwide for production and fourth for exports, according to Ucimu-Sistemi Per Produrre.
At the organisation’s annual Members’ Meeting, Ucimu President Riccardo Rosa described the past year as “extremely challenging.” Italian production of machine tools, robots and automation systems dropped by 16.9% to €6.3 billion. Domestic deliveries fell nearly 40%, due to a collapse in internal consumption. Imports also declined sharply by 31.8%, to €1.65 billion.
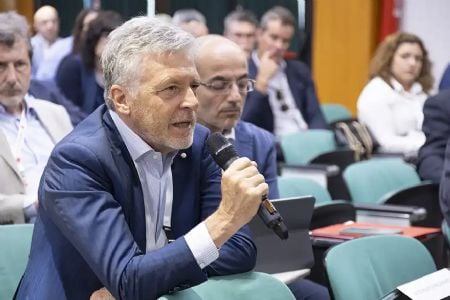
In stark contrast, exports were the sector’s only bright spot, growing 1.2% to a record €4.27 billion. Key markets included the USA (+10.9%), Germany (+1.6%), and India (+58.3%), though others like China (-16.3%) and France (-17.6%) saw sharp declines. Notably, Spain (+21.1%) and Sweden (+71.4%) showed strong demand for Italian technology.
Looking ahead, 2025 forecasts from Ucimu’s Economic Studies Department suggest a modest turnaround:
- Production expected to rise 2.6% to €6.49 billion
- Exports to increase 1%, reaching another record of €4.31 billion
- Domestic deliveries projected to grow 5.9%
- Imports expected to rebound by 4.9%
However, Riccardo Rosa stressed that uncertainty remains the biggest threat, citing ongoing trade tensions, geopolitical instability, and tariff concerns. “We must use the conditional mood when talking about growth,” Rosa warned. “The global situation demands resilience, collaboration, and renewed competitiveness.”
He called for continued investment in innovation, digitalisation, and skills development, highlighting the importance of government incentives like Transition 4.0 and 5.0. With Germany set to launch its own reindustrialisation plans, Rosa emphasised Italy must be ready to “stay coupled to the train” of Made in Germany supply chains.
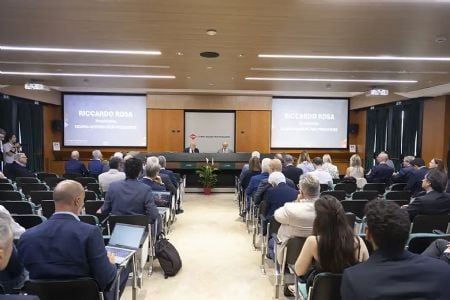
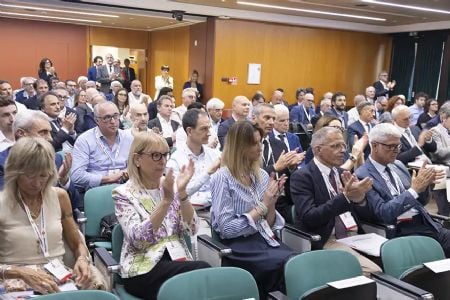
The UCIMU Academy initiative was spotlighted as a key driver in narrowing the skills gap, fostering partnerships with high schools, universities, and technical institutions to prepare the next generation of skilled professionals.
Rosa also addressed the impact of automotive electrification and potential tariff changes, particularly in relation to the U.S. market. While tariffs are not currently expected to harm direct exports, indirect impacts via global supply chains remain a concern.
He concluded by underlining the need for long-term structural policies to stabilise investment cycles and support Italy’s SME-driven manufacturing base: “We cannot afford to lose orders because lead times clash with short-term incentives. We need predictability, not peaks and panic.”
René Güntner Appointed as New Chief Financial Officer of the MAPAL Group
The MAPAL Group has announced the appointment of René Güntner as its new Chief Financial Officer (CFO). In his new role, Mr Güntner takes on leadership responsibility for several critical business functions, including financial accounting, controlling, purchasing, and facility management.
Bringing a wealth of international experience to the MAPAL Group, Mr Güntner expressed his enthusiasm about the new opportunity. “With many years of management experience and in-depth expertise in international companies, I will contribute valuable impetus to the strategic development of the MAPAL Group,” he said. “We are very much looking forward to working together.”
Prior to joining MAPAL, Mr Güntner served as Executive Vice President of Finance, where he was responsible for Group accounting, controlling, IT operations, and the business management of international subsidiaries. His role also included oversight of contract and risk management — experience that aligns well with his new responsibilities at MAPAL.
In addition to his financial acumen, Mr Güntner emphasized his commitment to open communication and teamwork. “I see myself as a financial officer as well as a sparring partner for all areas of the company,” he noted. “Open dialogue and cross-divisional collaboration are key success factors.”
His approach reflects MAPAL’s emphasis on transparency, operational efficiency, and strategic alignment across the organisation. With his strong background in both finance and interdepartmental leadership, Mr Güntner is well-positioned to support MAPAL’s ongoing transformation and growth strategy.
Mr Güntner takes over from Matthias Cöster, who has left the company by mutual agreement. MAPAL thanked Mr Cöster for his contributions and wished him well in his future endeavours.
The appointment marks a new chapter in MAPAL’s executive leadership and underlines the company’s continued focus on strengthening its global operations through experienced and visionary leadership.
Tapway Expands into Indonesia with Three Strategic Channel Partnerships!
Tapway Sdn Bhd has announced its expansion into the Indonesian market, forging partnerships with three leading local companies: ICS Compute, Metrodata, and Syspex. This collaboration aims to accelerate the adoption of Tapway’s SamurAI Vision AI platform, a cutting-edge solution designed to enhance operational efficiency, safety, and intelligence across industries such as retail, manufacturing, logistics, and smart infrastructure in Southeast Asia.
The partnerships were formalized recently at the Malaysian Embassy in Jakarta, marking a pivotal milestone in Tapway’s regional growth strategy. As official channel partners, ICS Compute, Metrodata, and Syspex will be responsible for distributing Tapway’s innovative AI technology, leading its implementation in various industries, and providing ongoing support to customers.
Lim Chee How, CEO of Tapway, expressed excitement about the opportunities in Indonesia, stating, “Indonesia represents one of Southeast Asia’s most promising markets for Vision AI. The MoUs mark the start of real-world transformations across logistics, retail, and manufacturing landscapes in Indonesia.”
Each partner brings specialized expertise that will support Tapway’s efforts in driving Vision AI technology forward in the region. ICS Compute focuses on real-time automation and system integration, helping businesses to respond more quickly and efficiently. Metrodata leverages its extensive ICT network to deploy Vision AI solutions within retail and manufacturing sectors. Syspex, with its focus on improving safety and efficiency in industrial environments, is well-positioned to apply AI technology to factory operations.
Budhi Wibawa, CEO of ICS Compute, highlighted the value of Vision AI, saying, “We see Vision AI as a way to make operations smarter, not just by seeing, but by acting.” Erwin Gunawan from Syspex echoed this sentiment, emphasizing how the partnership aligns with Syspex’s commitment to innovation and operational excellence.
With over 2,000 deployments across Southeast Asia, Tapway is rapidly expanding and positioning itself as a leader in AI-powered automation solutions. Supported by its trusted local partners, Tapway is set to revolutionize industries in Indonesia and beyond, helping businesses leverage artificial intelligence to optimize their operations and drive long-term success.
Thomson to Showcase Advanced Motion Technologies at Automation India Expo 2025!
Thomson Industries is set to exhibit its cutting-edge motion control solutions at the Automation India Expo 2025 in Mumbai, India. The event, taking place from August 11 to 14 at the Bombay Exhibition Centre, will feature Thomson’s latest innovations aimed at improving energy efficiency and reliability in industrial applications. Visitors to Hall 6, Booth R-05 will have the opportunity to explore a range of motion control technologies designed to meet the needs of industries such as factory automation, packaging, robotics, medical devices, and mobile machinery.
The Automation India Expo 2025’s theme, “Sustainable and Safe Automation,” aligns perfectly with Thomson’s commitment to promoting electric motion control solutions as a cleaner, more efficient alternative to traditional hydraulic and pneumatic systems. The company, alongside its Regal Rexnord brands Kollmorgen and Portescap, will showcase a variety of motion control products, including linear bearings, guides, ball and lead screws, and electric linear actuators, all designed for improved performance, sustainability, and safety.
A key highlight at the exhibition will be Thomson’s Electrak® XD, a heavy-duty electric actuator designed to match hydraulic power while offering the added benefits of electric control. This advanced technology is built to withstand tough industrial environments and enhances energy efficiency while simplifying machine design and reducing maintenance requirements. The Electrak XD is ideal for manufacturers who aim to lower their environmental impact without compromising on performance or durability.
Håkan Persson, Director of Product Marketing at Thomson, emphasized the importance of the event, stating, “Our presence at Automation India shows the growing demand for motion solutions that not only support sustainability but also deliver the precision, flexibility, and reliability today’s applications require.” Thomson experts will be available throughout the event to engage with visitors, discuss specific industry challenges, and demonstrate how their innovative motion control technologies can optimize machine design and operational efficiency for the long term.
With its focus on energy-efficient solutions and sustainable automation technologies, Thomson Industries continues to lead the way in providing high-performance motion control systems for a wide range of industries.
Team Industries Appoints Tom Panetti as VP of Sales, Estimating, and Supply Chain Management!
Team Industries Inc., a leading provider of pipe fabrication and fabricated vessels based in Kaukauna, Wisconsin, has announced the promotion of Tom Panetti to Vice President of Sales, Estimating, and Supply Chain Management. Panetti, who has been with the company for over 23 years, has played a pivotal role in various departments, including production, receiving, shipping, and estimating. Since 2019, he has served as the Estimating Manager, gaining a deep understanding of the company’s operations and customer needs.
In his new role, Panetti will be responsible for overseeing the estimating, sales, procurement, and receiving departments, where he will lead strategic initiatives aimed at driving growth and operational efficiency. His extensive experience within the company has equipped him with the knowledge and expertise necessary to promote and streamline processes across these critical functions. Panetti’s leadership will be essential in fostering collaboration across departments to enhance customer satisfaction and expand Team Industries’ market reach.
Under Panetti’s leadership, Team Industries is poised to strengthen its sales and estimating capabilities while optimizing its supply chain to ensure timely delivery and high-quality standards for its clients. The promotion reflects the company’s commitment to fostering internal talent and aligning its leadership with strategic goals for continued growth and success in the pipe fabrication and vessel manufacturing industry.
FARO Unveils the Super 6DoF TrackArm: A Portable Solution for Precise 3D Measurements!
FARO Technologies Inc. has introduced the FARO Super 6DoF TrackArm, a portable 3D measurement system designed for high-demand metrology applications. This advanced system combines the extended range capabilities of the company’s Laser Tracker with the versatility and detailed precision of the Quantum X FaroArm series, making it a powerful tool for a wide range of industrial and manufacturing environments.
The FARO Super 6DoF TrackArm is engineered to provide flexibility and accuracy, offering a comprehensive solution for complex 3D measurement tasks. By integrating probing and scanning technologies, it allows users to inspect intricate assemblies with ease, ensuring high-quality measurements even in challenging environments.
One of the standout features of the Super 6DoF TrackArm is its ability to measure both large and small components with exceptional detail, making it an ideal solution for industries where precision and versatility are crucial. Whether it’s for inspecting large structures or conducting detailed scans on intricate parts, the system adapts to a variety of measurement needs.
This portable solution is designed to increase productivity and accuracy in metrology processes, making it easier for manufacturers to perform high-precision inspections and quality control tasks. The Super 6DoF TrackArm’s portability allows it to be used in various locations, offering flexibility in the shop floor or field settings, which is vital for companies seeking to optimize their manufacturing operations.
Overall, the FARO Super 6DoF TrackArm represents a significant advancement in 3D measurement technology, helping companies achieve faster, more reliable, and more cost-effective inspections, leading to improved product quality and operational efficiency.
Wheelabrator Appoints Matt Schweitzer as Director of OEM Sales for North America!
Wheelabrator, a leading manufacturer of shot blast equipment based in LaGrange, Georgia, has appointed Matt Schweitzer as the new Director of OEM Sales for North America. Schweitzer, who brings over two decades of experience in the surface preparation industry, will be responsible for overseeing and growing the company’s equipment sales in the region.
Schweitzer’s extensive career includes leadership roles at several prominent companies in the industry. He has held key sales leadership positions with Fastenal, Black Hawk Industrial, Empire/Gibson, and Winoa Abrasives. At Winoa Abrasives, Schweitzer served as Director of Sales, contributing to the company’s success in the marketplace. He also held the position of Director of Sales and Marketing at Spark Power Corp., further sharpening his expertise in driving business growth and customer engagement. Schweitzer’s most recent experience includes an executive-level role at a shot blast equipment manufacturer, where he gained invaluable insights into both the technical and strategic aspects of the industry.
In his new role at Wheelabrator, Schweitzer is set to leverage his vast industry experience and leadership skills to expand the company’s presence in North America, further enhancing its reputation as a premier provider of surface preparation solutions. His appointment aligns with Wheelabrator’s ongoing efforts to strengthen its position in the market and deliver advanced, efficient equipment to its customers.
With his proven track record in sales, business development, and market strategy, Schweitzer is expected to drive growth for Wheelabrator, build stronger customer relationships, and support the company’s ambitious goals for expansion in North America.
Andrews Fabricators to Invest $3 Million in Facility Expansion, Creating 40 Jobs in Kingstree, SC!
Andrews Fabricators, a well-established steel fabrication company, has announced a major $3 million investment to expand its operations in Kingstree, South Carolina. This expansion is poised to create 40 new jobs in the region, significantly contributing to local employment and economic growth.
The company, which offers a wide range of services including mill maintenance programs, waterjet cutting, and plasma cutting, is further solidifying its reputation as a leader in the steel fabrication industry. As part of the expansion, Andrews Fabricators will add an additional 30,000 square feet to its existing facility, enhancing its production capacity and providing greater space for future growth. This added space will house a new, state-of-the-art precision sheet metal fabrication line, enabling the company to improve its manufacturing efficiency and expand its service capabilities.
The company’s expansion comes as part of a strategic effort to meet the growing demand for steel fabrication services, while also enhancing its ability to serve its clients with more advanced manufacturing technologies. The expanded facility will also reinforce Andrews Fabricators’ status as a distributor and erector of Nucor Metal Building Systems, which continues to be a key part of its business.
Moreover, the company is an authorized dealer and repair provider for Kohler Generators, adding another layer of service to its offerings. The new investment will ensure that Andrews Fabricators can continue providing top-quality products and services to its clients in the power generation industry, as well as in sectors requiring specialized fabrication work.
The facility expansion, scheduled to be completed by spring 2026, is expected to increase production capabilities and streamline operations, supporting the company’s long-term growth goals. With the addition of 40 new jobs, this investment also underlines Andrews Fabricators’ commitment to the local economy and its ongoing efforts to create valuable career opportunities in the region.
Rhoads Industries Announces $100 Million Expansion at Philadelphia Navy Yard!
Rhoads Industries is set to make a major $100 million investment to expand its manufacturing operations at the Philadelphia Navy Yard. This expansion is expected to create at least 450 new jobs while also preserving 541 existing full-time positions, strengthening the company’s footprint in the region.
The expansion will include the construction of a new 95,000-square-foot manufacturing facility aimed at boosting production capacity to support the U.S. Navy’s Maritime Industrial Base, particularly its submarine program. The new facility will enable continuous fabrication processes, and its location provides direct access to a pier, facilitating the efficient barge shipping of completed products.
Rhoads Industries, known for its large-scale industrial fabrication, mechanical, and maritime maintenance services, will expand its capabilities in the Navy Yard. The company already operates over 300,000 square feet of heavy manufacturing space and offers a range of services including field support and skilled labor for maritime projects. This investment not only enhances Rhoads Industries’ operational capacity but also plays a key role in strengthening the local economy through job creation and support for naval defense projects.
National Skilled Trades Competition Concludes with Top CNC Machining Winners!
The 2025 Skills Canada National Competition (SCNC) wrapped up, bringing together over 500 students and apprentices from across Canada to compete in more than 40 skill areas. The event, which is Canada’s largest multi-trade and technology competition, concluded with winners in various categories, including CNC Machining. These winners will have the opportunity to represent Canada at the 48th WorldSkills Competition in Shanghai, China, scheduled for September 2026.
In the CNC Machining competition, Ontario’s Noah Rittenhouse took home the gold, New Brunswick’s Joshua Bradford earned the gold in Precision Machining, while Félix Lafrance (silver) and Richard Lewis (bronze) secured top spots in CNC Machining. These victories demonstrate the skill and dedication of Canada’s rising trades professionals.
The SCNC serves as a key platform to engage youth and promote rewarding careers in the skilled trades and technologies. In addition to the intense competitions, the event featured hands-on activities such as the Skills Showcase highlighting First Nations, Inuit, and Métis Skills, as well as initiatives like Empowering Women in the Trades. Over 50 Try-A-Trade and Technology activities allowed students to explore different career paths in a practical, engaging setting.
Shaun Thorson, CEO of Skills/Compétences Canada, emphasized that the event connects the next generation of skilled professionals, showcasing the numerous opportunities available in skilled trades and technologies. He also stressed the importance of hands-on activities in helping students explore these in-demand career paths.
The SCNC event is made possible with the support of the Government of Canada and several sponsors, including UA Canada, Cenovus Energy, Home Hardware, and the Regina Hotel Association.
The next SCNC will take place on May 28-29, 2026, at Exhibition Place in Toronto. The event continues to provide a platform for young Canadians to explore, compete, and pursue successful careers in the trades and technology sectors.
Additionally, the event continued its longstanding partnership with the Gene Haas Foundation, which provided cash awards for CNC Machining and Precision Machining competitors. Gold, silver, and bronze medalists in these categories received awards starting at $1,350, reinforcing the Foundation’s commitment to supporting the next generation of machinists.
Vericut 9.6 Enhances CNC Simulation with AI and Smarter Features!
CGTech has unveiled Vericut 9.6, the latest update to its CNC simulation, verification, and optimization software. The new version introduces advanced artificial intelligence tools and several usability and productivity enhancements designed to streamline workflows, improve user interaction, and make learning Vericut more efficient.
Vericut 9.6 includes two significant AI-powered features: Vericut Assistant (VA) and Vericut Intelligence (VI). Vericut Assistant is an interactive guide built into the software that offers real-time, context-sensitive help. Users can ask questions like “How do I set up a simulation?” and receive immediate, relevant answers, significantly reducing training time and enabling users to fully leverage the software’s capabilities.
Vericut Intelligence, a web-based knowledge platform, provides users with AI-powered insights across all Vericut products, including Force, Composites, and Optimizer. This resource allows users to access high-level explanations, detailed feature support, and helpful learning materials anytime, offering a smart way to understand and utilize Vericut.
Another notable update in Vericut 9.6 is the enhanced Vericut Reviewer, CGTech’s free NC program viewer. The new version supports AUTO-DIFF results, improving collaboration between programming and verification teams. Additionally, the user interface has been updated with new heads-up display (HUD) status indicators and customizable hotkeys, making simulation reviews faster and more intuitive.
The latest version also features several improvements to increase efficiency and accuracy:
- PMI Data Support: Vericut 9.6 now allows users to view and document 3D Product Manufacturing Information (PMI), including dimensions and notes that follow ISO 10303/STEP AP242 standards, enhancing precision and traceability.
- Turning Upgrades: The update offers more accurate definition of driven points and automated tool qualification, speeding up lathe setups and improving overall accuracy.
- Simplified Optimization: The redesigned Optimization Control window, combined with default tool data, makes feedrate tuning and performance adjustments more efficient by reducing the number of steps required.
- Expanded Interfaces: Vericut 9.6 adds support for Siemens Run MyVirtual Machine and Fanuc Robot T.P. language, broadening integration capabilities with various manufacturing systems.
- CAD/CAM Compatibility: The update also supports NX auto-loading of stock, fixtures, and design models, reducing manual setup for CAM users and improving workflow efficiency.
Additional improvements in Vericut 9.6 include new report templates, enhanced machine connectivity, support for solid model textures, and better tool import options from MachiningCloud.
With these updates, Vericut 9.6 brings cutting-edge AI tools, smarter simulation features, and enhanced capabilities to the table, helping manufacturers optimize their CNC machining processes, increase productivity, and reduce errors, all while providing easier-to-learn tools for both new and experienced users.
Hermle USA Unveils GEN2 C Series 5-Axis Machining Centres for Multi-Process Capability!
Hermle USA has introduced its new GEN2 C 650, C 32, and C 42 5-axis machining centres, which represent a major leap in advanced manufacturing technology. These new machines are designed to handle up to 13 different processes on a single machine, improving operational flexibility, minimizing downtime, and optimizing workflows. The GEN2 C series will also serve as the platform for future Hermle machines, engineered with an emphasis on automation, sustainability, and maximizing spindle uptime to meet the growing demands of modern manufacturing.
A key feature of the GEN2 C series is the complete overhaul of its electrical architecture. This includes significant upgrades to both hardware and software components, allowing the machines to meet the demands of future-ready manufacturing environments. Notable advancements include the introduction of a new ProfiNet communication bus, IO-Link-compatible sensors, and the latest generation of drive converters on HEIDENHAIN models. These improvements enhance precision, reliability, and adaptability, making the machines well-suited for a wide variety of complex applications across industries.
The GEN2 C series also brings several advanced capabilities to the table. For instance, Contour Broaching allows for the machining of deep, high-precision sealing grooves, offering excellent accuracy for demanding applications. Additionally, the system supports Grinding for complex materials and fine surface finishes, which is particularly crucial in industries such as aerospace, automotive, and medical manufacturing. The machines are also capable of Power Skiving, enabling complete gear production in a single pass, significantly reducing cycle times and enhancing production efficiency. Furthermore, the Diamond Polishing feature enables the polishing of hardened components up to 60 HRC, providing high surface quality on tough materials.
In addition to these machining capabilities, the GEN2 C series incorporates Temperature and Ultrasound Measurement, which offers real-time process feedback, ensuring high levels of monitoring and quality control throughout the production process. The machines also feature Synchronous Deburring and Reverse Countersinking, both of which are designed to improve the quality of finished components by removing burrs and enabling precise countersinking, respectively.
The machines also come equipped with a newly redesigned coolant system, which enhances filtration, extends coolant life, and reduces maintenance requirements, leading to greater operational efficiency.
One of the standout features of the GEN2 C series is the ZM 30 ultra-compact tool magazine. This innovative tool magazine adds 30 additional tools while occupying nearly 50% less space than traditional magazines, improving tool management and reducing the need for valuable floor space.
With these upgrades, the GEN2 C series 5-axis machining centres from Hermle USA provide manufacturers with an efficient, reliable, and highly adaptable solution that can handle diverse and complex machining tasks, all while ensuring sustainability, reducing operational costs, and maximizing machine uptime.
ProShop ERP Appoints Alison Hawkins as New CEO to Focus on Customer-Centric Growth!
ProShop ERP, a leading provider of manufacturing management software, has announced the appointment of Alison Hawkins as its new CEO. Previously serving as the company’s Chief Operating Officer and Chief Financial Officer, Hawkins has been instrumental in driving transformative initiatives that enhanced operational alignment and customer success. Her leadership is expected to further propel ProShop’s mission to create innovative solutions tailored to the needs of manufacturers.
With Hawkins at the helm, ProShop is committed to deepening its customer-first approach. The company emphasizes that every product enhancement, feature, and strategic decision will prioritize the success and needs of its users. ProShop’s robust software platform will continue to evolve with this customer-centric philosophy, and the company plans to further strengthen its engagement with users by hosting regional events across North America. These events will provide hands-on learning experiences, real-world strategies, and peer-to-peer collaboration. The next educational event is scheduled for September 2025 in Chicago.
“We exist to serve our customers — it’s that simple,” said Hawkins. “We understand the responsibility that comes with being trusted with the operational heartbeat of a manufacturer’s business. Every interaction, whether it’s product improvement or support, is designed with the goal of helping our clients achieve greater success.”
During her tenure as COO and CFO, Hawkins played a key role in transforming ProShop’s operations and fostering customer success. She joins the founding team, including Paul Van Metre (Chief Evangelist), Kelsey Heikoop (Chairman of the Board), and Matt Carrico (Chief Architect), to reinforce ProShop’s customer-focused culture and drive the company’s innovation roadmap.
Paul Van Metre, ProShop’s Chief Evangelist, praised Hawkins’ leadership, saying, “Alison brings a relentless focus on customer value. She listens carefully, acts with purpose, and keeps the needs of our clients at the center of everything we do.”
Kelsey Heikoop, co-founder of ProShop, added, “Alison’s leadership will help us serve more manufacturers, more effectively, at every stage of their journey. Our customers don’t just use ProShop, they rely on it to grow.”
Matt Carrico, ProShop’s Chief Architect, highlighted Hawkins’ unique leadership style, noting, “Alison is a systems thinker and a servant leader. She understands that scaling responsibly means staying close to our customers and ensuring that our software solutions meet their evolving needs.”
With Hawkins now at the helm, ProShop is expanding its leadership team and reinforcing its commitment to providing manufacturing businesses with the tools they need to succeed.
Whitehouse Machine Tools Strengthens Sales Team with New Appointment in the South East
Whitehouse Machine Tools, a leading supplier of advanced CNC machining solutions in the UK, has expanded its national sales team with the appointment of Owen Gibbons. Bringing years of industry experience and a strong technical background, Owen will be responsible for supporting manufacturers across the South East region.
With a proven track record in engineering and machine tool sales, Owen joins Whitehouse at a time when the company continues to grow its footprint in key sectors such as aerospace, automotive, medical, and precision subcontracting. Known for his personable approach and deep understanding of customer needs, he’s set to play a pivotal role in strengthening relationships and driving growth in the region.
Whitehouse Machine Tools has long been recognised for supplying premium machine tools from globally renowned manufacturers. Their product portfolio includes Brother’s high-speed machining centres, Biglia lathes and SPINNER machines, among others. These machines are chosen for their precision, reliability, and ability to deliver competitive performance across a wide range of applications.
In his new role, Owen will be working closely with customers to help identify the right equipment for their production challenges.
Commenting on the appointment, Peter Smith from Whitehouse said:
“We’re delighted to welcome Owen to the team. He brings a strong mix of technical knowledge and customer-first attitude that fits perfectly with our company ethos. Customers in the South East can expect a high level of support and expertise moving forward.”
Owen is now fully up and running in the role and available to speak with customers across the South East who are considering new investments in CNC technology or looking to improve existing operations.
He can be contacted directly at: 07436 163 081
oweng@wmtcnc.com
Whitehouse Machine Tools continues to expand its support network throughout the UK, ensuring customers receive not just world-class machines, but also expert guidance and long-term service partnerships.
Sodi-Tech EDM Reports Unprecedented Trading Milestone
Sodi-Tech EDM, the exclusive distributor of Sodick EDM machines in the United Kingdom, has announced its busiest trading period in the company’s history. This landmark achievement underscores the growing trust among manufacturers in Sodick’s cutting-edge EDM technology, as well as the relentless commitment of the Sodi-Tech team to providing superior service and technical support.
Greg Capp, Sales Director at Sodi-Tech EDM, expressed his enthusiasm about the company’s recent performance. He stated, “This is a standout period for the business. We’re seeing increased demand across key sectors, with manufacturers continuing to invest in precision EDM solutions that deliver performance, reliability, and efficiency.”
The surge in trading activity highlights a broader trend within the UK manufacturing sector, where companies are keenly focused on enhancing precision, efficiency, and reliability in their operations. This growth can be attributed to the strategic partnerships Sodi-Tech has built over the years and the organization’s continuous adaptation to the evolving market needs.
Capp also took the opportunity to extend his gratitude to Sodi-Tech’s customers and partners. “I’d like to thank all our customers and partners for their continued support,” he said. “This momentum is only possible because of the relationships we’ve built.”
This period of unprecedented activity comes as the industry sees a shift in demand patterns, with manufacturers recognizing the importance of investing in top-tier technology. Sodi-Tech’s approach of combining industry-leading EDM machinery with responsive and localized support appears to be a key factor in driving their recent success.
As the market continues to evolve, Sodi-Tech remains committed to its mission of delivering state-of-the-art EDM technology to manufacturers across the UK. The company’s focus on customer satisfaction and technical excellence ensures that they not only meet but exceed the expectations of their client base.
In this exciting time for Sodi-Tech EDM, the firm maintains a clear focus on supporting its customers’ ambitions to enhance manufacturing capabilities through cutting-edge technology. The company plans to continue investing in its services to further strengthen its position in the competitive EDM market.
Sodi-Tech EDM’s success story is a testament to the company’s dedication to excellence and innovation in the manufacturing industry. With continued support and collaboration from customers and partners, Sodi-Tech is well-positioned to maintain its leadership role in the supply of precision EDM solutions.
Mastercam 2026 Launches with AI-Driven Tools and Enhanced Machining Capabilities!
Mastercam has unveiled Mastercam 2026, an advanced release packed with productivity-boosting tools, AI-powered CAM intelligence, and improvements that promise to streamline operations, reduce programming time, and eliminate common bottlenecks on the shop floor. Developed in close collaboration with customers and supported by comprehensive industry research, Mastercam 2026 is designed to optimize manufacturing workflows, enhance machining precision, and support complex operations with greater efficiency.
One of the key updates in Mastercam 2026 is the complete redesign of its Solid Hole Functionality, which enhances hole-making operations in solid models. The new feature includes a three-panel interface—comprising geometry selection, hole style, and advanced options—making the creation of complex hole configurations easier. This update not only reduces programming time but also improves the accuracy of these operations.
Tool management is another area that has seen a significant upgrade. The Mill Tool Holder Designer now features a panel-based design with intuitive visual feedback, streamlining workflows and improving the tool selection process. Additionally, Lathe Generic Tool Catalog Support speeds up tool creation and helps standardize tools across different machines. The Planes Manager has also been revamped, offering drag-and-drop functionality, group creation, and enhanced search and filtering in a modern tree structure, which makes setup management more efficient. Similarly, the Levels Manager allows for greater customization and better organization of part modelling, workholding, and toolpath entities.
Safety and efficiency are paramount in Mastercam 2026, as demonstrated by the introduction of Safety Zone Motion Priority. This new feature adds three prioritization options that optimize toolpaths intelligently, reduce unnecessary air cutting, and enhance machining efficiency, ultimately helping reduce cycle time and improve part quality.
For machining complex geometries, Mastercam 2026 brings powerful enhancements, such as OptiRough Critical Depths, which optimizes flat area roughing to reduce cycle times without sacrificing surface quality. Tapered Helix Entry improves deep pocket machining by offering better chip evacuation and coolant access, contributing to extended tool life. Additionally, Enhanced Loft Surface Creation allows for smoother transitions and more predictable surface results through improved blending algorithms and dynamic sync tools.
The update also brings expanded mill-turn capabilities with Classic Mill Toolpath Support, which allows legacy toolpaths like Surface Rough and Wireframe Finish to be used in mill-turn environments. Updates to PrimeTurning include enhanced angled cuts, pinch turning, and finishing improvements, addressing the needs of more complex turning operations.
Another exciting feature in Mastercam 2026 is the debut of its early access program for Mastercam Copilot, an AI-powered assistant designed to guide users through programming tasks. Although currently in Beta, Mastercam Copilot promises to simplify workflows by offering a Help function with natural language answers to programming questions and a Command function that automates elements of the user interface. Early feedback has been promising, with users noting that the tool has the potential to lower the learning curve and speed up programming tasks.
Mastercam 2026 represents a significant leap forward in CAM software, integrating AI-driven tools with powerful machining capabilities and making the programming process faster, smarter, and more efficient. With these updates, Mastercam continues to solidify its position as a leader in the manufacturing software industry.
Universal Robots Unveils UR15 Cobot to Accelerate Productivity Across Multiple Industries!
Universal Robots has introduced the UR15 cobot, designed to enhance motion capabilities, reduce cycle times, and increase overall productivity across various industries. As the fastest model in the UR series, the UR15 boasts a maximum TCP (Tool Center Point) speed of 5 m/s, enabling significant improvements in cycle times—up to 30% faster compared to other UR models. This speed enhancement is achieved without sacrificing the cobot’s lightweight design or compact footprint, making it suitable for applications requiring both precision and high-speed performance.
A key feature of the UR15 is its integration with OptiMove, Universal Robots’ proprietary motion control technology. OptiMove ensures smooth trajectory movements and precision, even under high-speed, high-payload conditions. Whether performing tasks such as pick-and-place or complex operations, the UR15 delivers accurate and consistent results, improving both efficiency and the quality of work.
The UR15 operates on PolyScope 5 and PolyScope X, Universal Robots’ advanced software platforms. This makes the UR15 highly compatible with AI-powered applications, enabling manufacturers to fully harness the cobot’s potential. The cobot can be integrated with the UR AI Accelerator, a powerful toolkit developed in collaboration with NVIDIA, utilizing NVIDIA Isaac’s CUDA-accelerated libraries. This allows the UR15 to perform advanced tasks with the flexibility and adaptability of AI, providing manufacturers with a highly usable, smart robotic solution.
With a payload capacity of 15 kg (33 lbs), and the ability to handle 17.5 kg (38.58 lbs) in wrist-down orientation, the UR15 is highly adaptable for a wide range of applications. This versatility is particularly valuable in industries such as automotive, metal and machining, and electronics. In the automotive industry, the UR15’s small footprint and full work envelope make it ideal for high-speed applications such as automated bin picking, machine tending, and inspection, providing significant productivity boosts while maintaining precision. In metal and machining industries, the UR15’s IP65 ingress protection and high payload capacity make it perfect for demanding environments, while in the electronics sector, its cleanroom-class excellence and exceptional motion control capabilities allow for seamless integration with Autonomous Mobile Robots (AMRs) and Automated Guided Vehicles (AGVs).
The UR15 cobot is a breakthrough solution for manufacturers looking to enhance productivity, reduce costs, and achieve high precision in their operations. By combining advanced motion technology, AI capabilities, and easy integration with UR’s PolyScope platforms, the UR15 is setting new standards for collaborative robotics in industries that demand speed, efficiency, and flexibility.
Starrag Launches New Heckert X Series Five-Axis HMCs for Heavy-Duty Machining!
Starrag has introduced the larger models of its Heckert X series of five-axis horizontal machining centers (HMCs), with the new X70, X80, and X90 machines tailored for the complete machining of large, heavy-duty components. These models are designed to deliver high precision and efficiency for industries dealing with large workpieces such as gearbox housings, cylinder heads, axles, and other complex components. The machines offer an ideal solution for companies involved in the production of mechanical parts like valve and pump housings, planetary gear carriers, and pallets, headstocks, and spindle frames.
The Heckert X70, X80, and X90 HMCs come with pallet sizes ranging from 24.8″ x 31.5″ for the X70 to 31.5″ x 39.4″ for the X80 and X90 models. These machines are designed to handle heavy parts, with weight capacities ranging from 2,204.6 lb. (1,000 kg) for the X70 to 4,409.2 lb. (2,000 kg) for the X90, making them well-suited for industries requiring heavy-duty machining. Despite the large workpiece capacity, these machines maintain a compact design, with the X70 requiring 18% less installation space than its predecessor, the Heckert HEC 630 X5, offering excellent space-saving benefits while retaining full workpiece capabilities. The working area and displacement circle, as well as permissible workpiece weight and height, remain unchanged from earlier models, ensuring efficient utilization of available space without compromising performance.
What sets the Heckert X70, X80, and X90 apart is their ability to perform integrated turning operations, which adds another layer of versatility to the machining capabilities. With the use of specially developed assemblies and software modules, these machines can execute both classic and complex turning operations, offering the productivity of a machining center with the flexibility of a lathe. Unlike traditional turning lathes, these five-axis machines allow for diverse setup options. Workpieces can be clamped both vertically and during the machining process using the pallet changer, enhancing the flexibility of operations.
The X90 model can handle turning diameters of up to 55.1″, further expanding the machine’s versatility for large components. Additionally, these machines support the use of large tool magazines, ensuring a wide variety of tools can be utilized in the production process.
Starrag’s Heckert X70, X80, and X90 machines are built on a compact, low-vibration machine bed made of grey cast iron, which ensures excellent mechanical accuracy. The thermo-symmetrically designed columns contribute to high performance by minimizing thermal distortion during operations. The use of trimmed guides also ensures that the machines can maintain consistent precision, with software compensation applied to finalize the finishing touches, optimizing overall accuracy.
The rotary/tilt table of these models is robust and designed with two equally sized bearings and a thermally stable construction. This ensures highly dynamic and efficient five-sided machining, enabling operators to handle complex components with precision, speed, and reliability.
The X series machines are also designed with automation in mind. With extended 13-channel clamping hydraulics and optimized interfaces to pallet storage systems and robot cells, the new models are easier to automate than their predecessors. The machines are also compatible with pallets from the older Heckert HEC 630 / 800 X5 models, enabling smooth transitions and greater flexibility in production.
For control, the Heckert X70, X80, and X90 machines come equipped with the Siemens Sinumerik One control system. This cutting-edge system features new hardware and fast sensor technology, ensuring enhanced control over the machining process and greater precision.
In conclusion, the Heckert X70, X80, and X90 models from Starrag represent a significant step forward in the world of five-axis machining, combining high capacity for large and heavy workpieces with a compact design, integrated turning functionality, and advanced automation capabilities. These machines offer a versatile, efficient, and precise solution for heavy-duty industries, from automotive to aerospace, making them ideal for the most demanding manufacturing applications.
ESAB Launches OK Autrod 42 LSW Solid MIG Wire for Robotic Welding Applications!
ESAB, a global leader in fabrication technology, has introduced its latest product, the OK Autrod 42 LSW—a copper-coated ER70S-9 solid wire specifically designed for robotic MIG welding applications. This new welding wire aims to enhance productivity while reducing overall costs in industries such as automotive and yellow goods manufacturing.
The OK Autrod 42 LSW is engineered to create minimal slag and silica islands on the weld bead, which in turn reduces the need for time-consuming post-weld cleaning. This feature is especially beneficial for industries where the welds are followed by painting or galvanizing processes, as it ensures a smoother and more efficient finish. ESAB’s innovative metallurgy has made it so that the slag produced by the wire is easier to clean compared to traditional welding wires. The self-releasing slag, primarily composed of manganese and titanium oxides, significantly eases clean-up compared to the silicon oxides found in conventional wires.
Available in diameters of 0.9, 1.0, and 1.2 mm (0.035, 0.040, and 0.045 inches), the wire is offered in standard spool weights of 18 kg (39 lbs.) or ESAB’s Marathon Pac™ bulk wire system, which comes in a more cost-effective 250 kg (551 lbs.) option. This adaptability allows businesses to scale their operations according to their production needs while benefiting from a reliable, high-quality welding solution.
The OK Autrod 42 LSW is especially well-suited for single-pass welding applications, such as those found in the automotive and yellow goods industries, where robust corrosion and paint protection are applied after welding. In these industries, manual removal of silicon islands and slag is necessary to prevent rust formation. However, with the introduction of the OK Autrod 42 LSW, this need for additional cleaning is drastically reduced, offering companies both labor savings and faster cycle times.
One of the standout features of this new wire is its good wetting action, which results in a smoother transition at the weld toe, contributing to a better bead profile and superior surface finish. Additionally, the wire generates minimal spatter, a crucial factor when working in high-speed, robotic environments. The tensile strength of the OK Autrod 42 LSW is a minimum of 71 KSI, with typical impact values of 93 ft-lbs at -22°F, ensuring strong, reliable welds in challenging conditions.
Joe Cacioppo, Director of Global Product Management at ESAB, emphasized that the demand for low-slag wires, like the OK Autrod 42 LSW, is growing in industries where reducing labor costs and cycle time is a priority. By minimizing post-weld cleaning, manufacturers can achieve greater efficiency and maintain high-quality welds.
ESAB’s Marathon Pac bulk wire system is also a significant addition to this new product, as it allows for extended production runs, reducing the need for frequent spool changes and improving overall workflow efficiency.
With over 120 years of innovation, ESAB continues to lead in providing cutting-edge welding and fabrication technology. Their extensive range of products and solutions serves industries worldwide, ensuring high-quality manufacturing outcomes. For more information about ESAB’s welding products, visit their website or contact a local ESAB representative.
In summary, the OK Autrod 42 LSW offers an efficient and cost-effective solution for robotic welding applications by reducing slag formation, simplifying cleaning processes, and improving weld quality. This product aligns with the growing need for automation and fast-paced manufacturing environments, especially in the automotive sector.
SHINING 3D Launches the Revolutionary EinScan Rigil Tri-Mode Laser 3D Scanner!
SHINING 3D, a prominent name in the 3D scanning industry, has launched the EinScan Rigil, the world’s first tri-mode laser 3D scanner. This cutting-edge scanner is designed to offer high-quality, fast, and reliable scanning capabilities for a variety of applications, from prosumers to professionals in diverse industries. It incorporates hybrid light technology, a wireless solution, and built-in computing, setting a new standard for 3D scanning.
The EinScan Rigil represents a significant advancement in the 3D scanning field, providing up to 0.04 + 0.06 mm/m volumetric accuracy and a high geometric resolution of 0.05 mm. These features ensure that users can capture highly detailed and accurate models across different scanning environments, making it ideal for applications like automotive, engineering, and reverse engineering.
One of the standout features of the EinScan Rigil is its three different scanning modes: Standalone Mode, Wireless PC Mode, and Wired PC Mode, providing versatility for various work environments. In Standalone Mode, the scanner operates independently without needing a PC, making it exceptionally portable and convenient for on-the-go scanning. The Wireless PC Mode allows users to connect to a computer wirelessly using built-in Wi-Fi 6, optimizing the performance for more complex tasks. Finally, Wired PC Mode ensures maximum scan speed and data volume, ideal for intricate and high-performance tasks in a networked environment.
These three modes unlock the full potential of the EinScan Rigil, giving users flexibility without compromising on performance. Whether it’s scanning a small object on the go, or tackling a large-scale project with high precision, the EinScan Rigil can handle it all.
The EinScan Rigil integrates both blue laser and infrared (IR) VCSEL technology, providing a hybrid light source that ensures efficient scanning in varying light conditions. This unique combination allows the scanner to perform marker-free laser scanning with greater efficiency than traditional marker-based methods while maintaining superior data quality. This hybrid approach is especially useful in environments where traditional scanning systems may struggle with accuracy or lighting conditions, such as outdoor applications or in bright sunlight.
The scanner’s IR Rapid Scan Mode, utilizing VCSEL infrared technology, offers versatility for scanning medium to large objects without the need for markers. This function ensures high efficiency and wide coverage, making it an excellent solution for scanning automotive parts, sculptures, or other large components.
The EinScan Rigil is tailored to meet the specific needs of consumers in the automotive aftermarket industry, providing high-quality 3D modeling solutions with faster scanning capabilities. Its compact design and versatile features allow users to generate precise 3D models of car parts, tools, and other equipment quickly and efficiently. The system streamlines the professional workflow while offering rich data editing functions, making it a powerful tool for automotive enthusiasts and professionals alike.
SHINING 3D, with almost two decades of experience in developing high-accuracy 3D technologies, continues its commitment to making professional-grade 3D scanning accessible to a wide range of users. The EinScan Rigil exemplifies the company’s dedication to advancing 3D technology, helping both professionals and prosumers alike create detailed, accurate models for a variety of applications.
SHINING 3D’s vision of democratizing digital 3D technology continues as the company leads the charge in innovation and accessibility, empowering users to explore new dimensions in their fields.
Nimble Adopts PTC’s Onshape and Arena to Scale Autonomous Logistics with Next-Gen Superhumanoids!
Nimble, a leader in AI robotics and autonomous logistics technology, has made a strategic shift to enhance its development process by adopting PTC’s cloud-native Onshape CAD and PDM platform along with Arena PLM and QMS solutions. This transition marks a significant upgrade from Nimble’s legacy computer-aided design (CAD), product data management (PDM), product lifecycle management (PLM), and quality management system (QMS) tools, which were file-based and became bottlenecks as the company scaled its operations.
After conducting an initial evaluation, Nimble moved quickly, making the switch in less than 60 days. The decision was driven by the need to streamline collaboration, reduce latency, and improve system reliability across various teams, ensuring that the company could continue its growth trajectory without disruption. With the new cloud-native tools from PTC, Nimble is now equipped with a seamless, connected development process, which is essential for scaling the production and research & development (R&D) of its superhumanoid mobile-manipulator robots, designed to meet the rising demand for faster and more cost-effective logistics solutions.
Simon Kalouche, Founder and CEO of Nimble, expressed his satisfaction with the new system, noting, “With Onshape and Arena, we now have a connected, cloud-native development process that eliminates the bottlenecks we faced with file-based tools. This is a critical step as we scale manufacturing and R&D for our superhumanoid robots to meet the growing demand for faster, more cost-effective logistics.”
David Katzman, General Manager of Onshape and Arena at PTC, commented on the trend of shifting away from file-based tools to cloud-native platforms. “Nimble’s adoption of Onshape and Arena underscores a notable trend in the industry where leaders are replacing file-based tools with connected, cloud-native platforms. Onshape and Arena are key enablers of this change, allowing teams to improve workflows, increase agility, and scale efficiently.”
As Nimble continues to develop its next-generation robotics solutions, the integration of PTC’s cloud-native platforms is expected to enhance product development timelines, improve team collaboration, and ensure better scalability in its manufacturing operations. This step aligns with Nimble’s mission to innovate and lead in the rapidly evolving logistics technology space, positioning the company for continued success in meeting future demands.
Elegoo Launches Fiber-Reinforced Filament Series to Enhance FDM 3D Printing Performance!
Elegoo, a rising star in the world of smart manufacturing, has unveiled its Fiber-Reinforced Filament Series, significantly enhancing the performance and versatility of FDM (Fused Deposition Modeling) 3D printing. The new product line includes Carbon Fiber Reinforced PETG (PETG-CF), Glass Fiber Reinforced PETG (PETG-GF), and Carbon Fiber Reinforced High-Temperature Nylon (PAHT-CF). These high-performance filaments are designed to provide improved strength, durability, and professional-quality results, all starting at a competitive price of $9.99 USD for 0.5KG of filament. Additionally, more filament variants are under development and will be released based on user feedback and specific application needs.
Elegoo’s new Fiber-Reinforced Filament Series is a response to growing demand for materials that can deliver superior mechanical properties for functional parts. According to a recent survey conducted by Elegoo, the main barriers to adopting fiber-reinforced filaments have been low familiarity and higher costs. “With Centauri Carbon, we pushed the limits of our FDM performance. Now, with these new filaments, we aim to meet the needs of users seeking high-quality, reliable materials for practical applications,” said Chris Hong, Founder and CEO of Elegoo. The company’s goal is to elevate consumer 3D printing beyond just hobbyist items and demonstrate its true potential in producing everyday, functional items.
The PETG-CF filament, available in black and grey, combines the toughness of PETG with the rigidity of carbon fiber. This combination results in a material that offers high strength, rigidity, and abrasion resistance. Its low-gloss, matte surface finish hides layer lines, making it ideal for creating functional parts that require durability and strength, such as fixtures, lightweight brackets, bicycle parts, gears, latches, automotive components, and mechanical enclosures. The filament’s excellent abrasion resistance makes it particularly useful for outdoor applications.
The PETG-GF filament, available in black, grey, and white, is infused with glass fiber to enhance its hardness and abrasion resistance. The glass fibers also provide excellent electrical insulation, making PETG-GF ideal for functional parts that need both durability and non-conductivity. This filament’s premium matte surface minimizes layer visibility, making it a perfect choice for electrical enclosures, tooling fixtures, bicycle pedals, connectors, and terminals that require high mechanical strength and electrical insulation.
The PAHT-CF filament, available in black, combines carbon fiber with high-temperature nylon to deliver exceptional heat resistance, mechanical strength, and chemical corrosion resistance. Withstanding temperatures of up to 194°C, PAHT-CF retains its structural integrity under thermal stress, making it an excellent choice for applications in high-temperature environments. The filament’s excellent interlayer adhesion, dimensional accuracy, and abrasion resistance make it suitable for motor housings, engine components, heat-resistant fixtures, gears, bearings, and structural parts in automotive and industrial settings. PAHT-CF is also a viable material for metal-replacement parts, offering durability and resilience for critical applications.
Elegoo’s Fiber-Reinforced Filament Series is designed to provide users with high-quality, functional materials at a competitive price point, making it accessible for both beginners and professionals alike. These filaments open the door to a range of new applications in industries such as automotive, aerospace, electrical, and manufacturing. With plans for more variants in the future, Elegoo is positioning itself as a key player in advancing 3D printing technology, offering users a comprehensive solution for high-strength, durable, and precision parts. Whether for personal use, small businesses, or industrial applications, Elegoo’s new fiber-reinforced filament lineup is set to redefine the possibilities of FDM 3D printing.
Strategic decision to streamline quoting
Preview of PSL Datatrack’s latest newsletter;
Springfort Precision Engineering Ltd has made the strategic decision to invest in PSL Datatrack production control software to streamline quoting, scheduling and inventory management – all areas that were previously consuming significant amounts of time at the Portadown-based subcontract precision engineering company.
“We were spending far too much time on quoting, administration and general paperwork. Managing our expanding list of part numbers and keeping track of raw material stock was becoming a logistical nightmare. We knew we needed a better solution,” explains Graeme McCoy, co-owner of Springfort.
Starrag presents new 5-axis Heckert machine
Starrag has now launched the Heckert X70, a versatile new 5-axis machining centre designed to deliver exceptional precision and productivity within a compact footprint. Building on the exceptional features of the acclaimed Heckert HEC X5 series, the Heckert X70 incorporates a swivel unit on the workpiece side, facilitating high-dynamic 5-axis machining from a single clamping position.
Receiving its world premiere at the EMO show in September on Stand C35 in Hall 12, the Heckert X70 offers impressive technical specifications with X, Y and Z axis travel of 1200 by 1100 by 1200mm. The compact machine requires 18% less installation space than its predecessor, the Heckert HEC 630 X5. It accommodates workpieces with a core contour diameter of 960 mm and a maximum height of 800 mm, supporting a loading mass of up to 1000 kg, demonstrating no change to the working area. Within its robust and spacious dimensions of 8,150 mm by 3,700 mm, the Heckert X70 offers exceptional space utilisation without compromising performance.
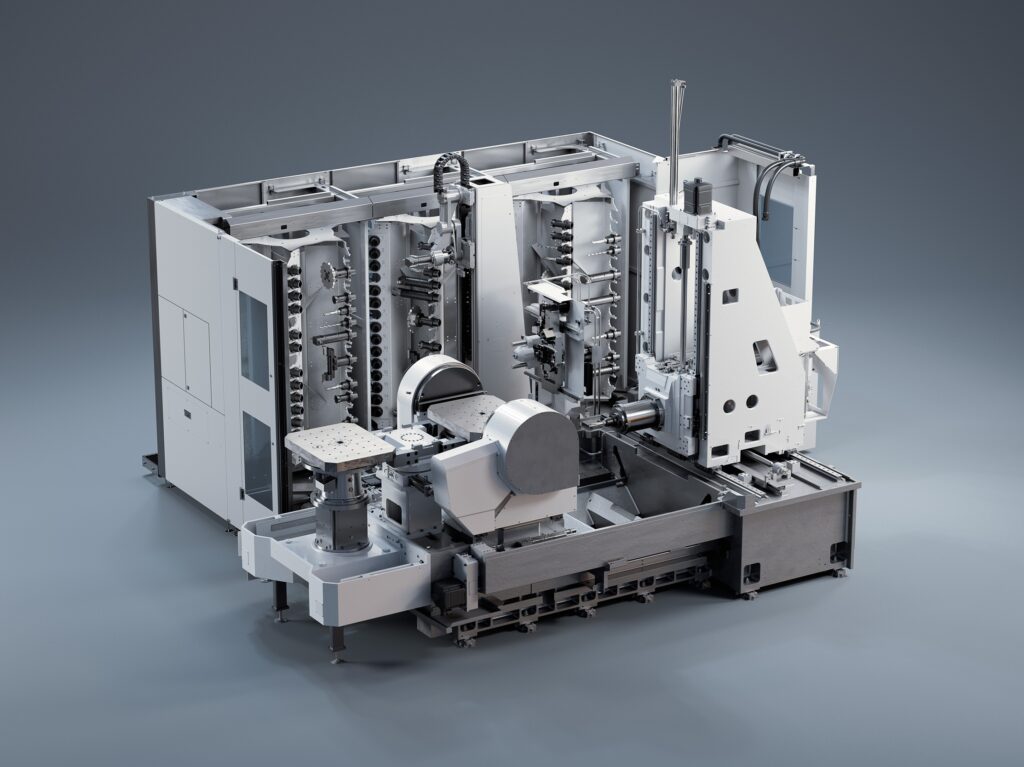
Furthermore, turning as a technology is an integral part of the machine concept and can be configured as an option. Using specially developed assemblies and software modules, both classic and complex turning operations can be performed with the unrivalled productivity of a machining centre. Unlike a turning centre, the machine benefits from various setup options. Not only can the workpieces be clamped vertically for added convenience, but they can, in fact, be clamped during the machining operation thanks to the pallet changer.
The Heckert X70’s lightning-fast traverse rate of 65 m/min and industry-leading component changeover times enhance productivity. Pallet changes are completed in just 17.5 seconds, and a tool changer provides a chip-to-chip time of only 7.4 seconds. The machine’s standard pallet dimension of 630 by 800 mm incorporates Starrag’s precision-engineered concave surfaces with a curvature depth of 6 µm, ensuring stable workpiece positioning of large parts. It features Starrag’s innovative tool change system, available in both lightweight and heavy-duty versions. The lightweight option accommodates tools weighing up to 22kg, while the heavy-duty version supports tools as heavy as 50 kg. The machine can handle tools with a maximum length of 800 mm and a diameter of 340mm.
Customers can choose from a range of tool magazine options, including a timing belt magazine with 45 or 60 positions for HSK-100 tools, an chain magazine with a capacity of up to 120 HSK-100 tools, and a tower magazine capable of supporting up to 440 HSK-100 tools. The Heckert X70 also offers a broad range of spindles to meet specific application requirements, with options varying from a 12,500rpm hollow shaft spindle up to a 15,000 rpm motor spindle and different gear spindles with more torque for heavy machining.
For optimal operator experience, the Heckert X70 features Starrag’s ergonomic 24-inch touchscreen HMI. The control system supports the powerful Siemens SINUMERIK ONE, ensuring intuitive operation even when wearing gloves. The touch-sensitive display remains responsive to gloves and has a scratch-resistant, easy-to-clean surface. Operators can effortlessly access PDF construction plans and sequence sketches while maintaining a clear view of the workspace through an integrated camera. With new hardware and fast sensor technology, the new machine is also easier to automate than its predecessor. This is partly due to the extended 13-channel clamping hydraulics and optimised standard interfaces to pallet storage systems and robot cells.
Efficient chip management is accomplished through a thermo-symmetric design and steep-angled fixed plates, complemented by an internal coolant supply operating at up to 80 bar pressures. This system ensures effective cooling and chip evacuation, with an additional flushing capability of up to 280 litres per minute for applications involving high chip volumes.
The Heckert X70 can be integrated with Starrag’s comprehensive automation solutions, including Fastems FPT round pallet store systems, different linear storage systems, or robotic cells, catering to various production requirements from small to large batch sizes. The Fastems FPT system provides an economical entry into production automation, enabling workpiece changes for small and medium batch sizes. In contrast, linear storage systems offer maximum flexibility for production processes with integrated master control for effective task planning and distribution.
The new Heckert X70 is based on the comparable four-axis Heckert H-series machine envelope. Instead of the NC rotary table installed in the Heckert H-series, the new Heckert X-series models feature a robust rotary/tilt table – an in-house development that is also manufactured at the Starrag plant in Chemnitz. Not only does the tilting unit have two equally sized bearings, but also a thermally stable design. This means that the machines can complete five-sided, highly dynamic machining of complex components.
Ensuring the compatibility of the pallets on the new Heckert X70, as well as the Heckert X80 and Heckert X90 models, was particularly important to the developers. The pallets are interchangeable with those from the H series. Furthermore, the pallets from the older Heckert HEC 630 / 800 X5 machines can also be used on the new Heckert X models. The Heckert X70 is now available as part of Starrag’s expanded Heckert X-series line of 5-axis machining centres. Manufacturers are invited to see the new machine at EMO Hannover in September. The Heckert X-series also includes the smaller Heckert X50 and the larger Heckert X80 and Heckert X90 variants for manufacturers seeking larger work envelopes and enhanced capacity.
Axil and Bostik Partner to Deliver Smarter, More Sustainable Total Waste Management
Axil announces a new partnership with Bostik, the adhesive solutions division of Arkema, to deliver total waste management across UK sites. This collaboration is focused on enhancing operational efficiency, boosting recycling and reuse, and using data-driven insights to ensure full compliance and transparency.
As part of the arrangement, new on-site waste equipment will be rolled out to streamline operations, reduce environmental impact, and improve the overall customer experience. Axil will work alongside Bostik’s workforce, acting as an extension of their team – identifying better waste routes and ensuring that materials are moved up the waste hierarchy in line with each site’s specific needs.
Just as Bostik encourages customers to ‘Don’t bin it, fix it,’ Axil will be working with Bostik to focus on recycling, reuse, and re-engineering waste streams for more sustainable outcomes.
“At Axil, we see waste as a valuable resource, and this partnership is an important step toward improving environmental performance,” said David Short, Operations Manager at Axil. “Even just a few weeks in, it’s been fantastic to see the Bostik team fully engaged – Building on existing efforts by embracing smarter, more sustainable approaches to waste and improving segregation practices.”
Axil is passionate about understanding customer needs. With extensive experience across manufacturing, logistics, retail, and food sectors, Axil provides comprehensive waste management solutions driven by technology, innovation, and a commitment to service excellence. The company tailors its approach to each client’s unique requirements, delivering bespoke solutions whilst ensuring sustainable and efficient waste management at every step.
Alex Ratcliffe, Country Purchasing Manager at Bostik UK, added: “At Bostik, we’re committed to driving continuous improvement in our sustainability journey. Partnering with Axil supports our ambition to manage waste more responsibly, and we’re pleased to see early progress through strong collaboration and shared values.”
As a single supplier, Axil removes the complexity of managing multiple vendors. Customers benefit from having all their data, support, and waste management solutions in one place, making operations simpler, more efficient, and fully integrated. Axil’s customised approach ensures clients achieve sustainable and effective waste management across all their operations.
Bostik, a global leader in high-performance adhesives, is best known for its iconic reusable adhesive, Blu Tack®. With 25 R&D centres worldwide, the company is agile and innovation-driven, serving industries such as construction, consumer, durable goods, packaging and hygiene. Committed to achieving net zero by 2050, Bostik leads the way in responsible manufacturing and science-based actions to drive sustainability.
Axil and Bostik are driving meaningful progress together, delivering smarter waste solutions for a more sustainable future. For Axil, supporting Bostik’s ‘Conscious Performance’ goes beyond processes—it’s a shared mindset that guides how we think, work, and collaborate to create lasting change.
For media enquiries, please contact:
Rebecca Miller –Communications and Partnerships Manager
rebecca.miller@axil-is.com 07523 696645
Please connect with us onLinkedIn
GUIDANCE AUTOMATION LAUNCHES PAY-PER-HOUR AUTOMATION MODEL TO UNLOCK PRODUCTIVITY IN MANUFACTURING
Guidance Automation has launched Automation by the Hour – ‘Autonomous GO’, a flexible, no-risk robotics model helping manufacturers, warehouse, and logistics operators boost productivity. The pay-per-hour model eliminates upfront costs by offering autonomous vehicles as a scalable, operational expense. Businesses only pay for hours worked, making automation more accessible while freeing skilled staff for higher-value tasks.
Leicester, UK – 3 July 2025 – Guidance Automation, a pioneer in autonomous solutions, has launched a groundbreaking model that makes automation more accessible than ever. Automation by the Hour – ‘Autonomous GO’ allows manufacturers and logistics providers to deploy autonomous vehicles without capital investment. Businesses only pay for the hours worked, aligning cost directly with output. This flexible, no-risk approach turns automation into an operating expense, providing immediate cost savings and productivity gains while allowing skilled staff to focus on the work they’re best at.
Across the UK, manufacturers and logistics operators lose thousands of labour hours to repetitive, non-value-adding tasks like moving materials or fetching supplies. Traditional automation has often been out of reach due to high costs, complexity, and risk. Guidance Automation is changing that with its new pay-per-hour Autonomous GO service.
Instead of large capital outlays, businesses trial a robot in their own facility for six months with full support. After that, they pay only for the hours the robot works — typically at half the cost of equivalent manual labour. With customisable payload options and minimal disruption, Autonomous GO offers a low-risk path to quick and measurable ROI.
This solution is designed to help businesses reduce wasted motion, improve task allocation, and increase productivity. By handling repetitive, low-value tasks, robot workers enable skilled teams to focus on higher-impact work – enhancing output without replacing people.
VisionLab-150 3D Fastener Gauging System Enhances Precision in Dimensional and Defect Inspection!
The VisionLab-150 3D Fastener Gauging System by General Inspection LLC. introduces a cutting-edge solution for fast, precise, and comprehensive part dimensional inspections. Leveraging patented 3D gaging technology, this system offers complete part inspection in less than 5 seconds, making it an ideal choice for industries where time-sensitive and high-quality inspection is essential.
The VisionLab-150 is designed to perform 360-degree dimensional inspections, delivering detailed data reporting. This feature ensures that every aspect of a fastener or part is accurately measured and checked for defects, significantly improving quality control processes. With optional enhancements, the system also provides visual defect detection, end-view inspections, and the capability to measure recess depth and concentricity, all critical for maintaining high manufacturing standards.
One of the standout features of the VisionLab-150 is its advanced thread measurement capability. Using a high/low thread measuring algorithm, the system can perform detailed thread analysis, including the evaluation of pitch diameter, functional diameter, and lobular shaped threads. The system complies with system-22 requirements, ensuring that every thread is thoroughly inspected, meeting industry standards for quality and performance. This makes it a valuable tool for fastener manufacturers who need precise and reliable measurements.
In addition to thread measurements, the VisionLab-150 excels in measuring straightness and other Geometric Dimensioning and Tolerancing (GD&T) characteristics. The system’s optional End-View feature allows for inspection and detection of defects on both ends of parts, including features like recesses, inner and outer diameters, through holes, and counterbores. This capability ensures that no aspect of the part goes unchecked, enhancing the system’s versatility in quality control.
For surface inspection, the VisionLab-150 offers optional surface control features that can detect visual defects such as poor plating, thread patch presence and quality, as well as measuring knurl width, gap, and height. These additional features make the system suitable for more complex part inspections, ensuring that even the smallest imperfections are identified before products reach customers.
The VisionLab-150 also includes slewing optics, which automatically tilt to provide a clearer view of the threads, enabling accurate root radius measurements. This ensures that fasteners with complex thread patterns can be measured with the same precision as simpler designs.
With the addition of optional upper tooling and bit kits, the VisionLab-150 can accommodate parts with a recess drive, broadening its application across various industries that require high-precision fastener and part inspections.
Overall, the VisionLab-150 3D Fastener Gauging System offers manufacturers a comprehensive, efficient, and highly accurate solution for ensuring the dimensional integrity and visual quality of their products, significantly improving the reliability of their production processes.
Hypertherm Introduces XPR460 Plasma Cutting System for Enhanced Precision and Productivity!
Hypertherm has unveiled its latest plasma cutting system, the XPR460, designed to deliver exceptional performance across various metals, including mild steel, stainless steel, aluminum, and steel. This advanced system is engineered to handle multiple cutting applications, providing improved productivity and precision for industries that rely on high-quality metal cutting.
One of the standout features of the XPR460 is the integration of SureCut technology, which automatically enhances cutting capabilities through advanced software. SureCut technology ensures smooth and precise cuts by embedding several specialized features directly into the plasma cutting process. Among these features are True Hole, True Bevel, and Rapid Part, which are designed to improve the overall efficiency of the cutting process.
The True Hole feature allows for bolt-ready holes, which is essential for many industrial applications where precision and quick fitment are critical. The True Bevel functionality enables smooth 45-degree bevel cuts, making it ideal for applications that require angled cuts. Meanwhile, the Rapid Part feature helps accelerate cutting operations, increasing overall productivity by streamlining the process.
Another key aspect of the XPR460 is PlateSaver technology, which combines the XPR arc stability and moving pierce to optimize material usage. This technology can increase material utilization by up to 14%, helping to reduce costs per part while minimizing waste. This makes the XPR460 a cost-effective solution for businesses looking to improve their cutting operations without sacrificing quality.
The system is particularly well-suited for robotic cutting applications, where automation is critical for maintaining high production rates and consistent cut quality. Additionally, the XPR460 is future-enabled for Smart Factory integration and connectivity, positioning it as a versatile and scalable solution for manufacturers looking to stay ahead of the curve in the evolving world of industrial automation.
With its advanced cutting capabilities, superior arc stability, and intelligent technologies, the XPR460 plasma cutting system offers a comprehensive solution for businesses seeking to enhance their manufacturing operations, reduce material waste, and achieve superior cutting precision.
Datanomix Enhances Delivery Track Software for Real-Time Predictive Insights and Universal ERP Connectivity!
Datanomix has recently upgraded its Delivery Track software to offer a more comprehensive solution for manufacturers seeking to improve on-time delivery (OTD), scheduling accuracy, and overall operational efficiency. With the inclusion of predictive job completion insights, smart job placement recommendations, and universal ERP connectivity, Delivery Track is designed to provide a unified, real-time view of job status, helping manufacturers stay on top of production goals and streamline their processes.
Delivery Track was developed to address a common challenge in manufacturing: determining the exact timeline for job completion. The software connects live machine data with ERP-driven scheduling to offer a clear, real-time snapshot of job progress, showing precisely when jobs will be done and what comes next. This integration allows teams across the shop to have access to the same data, reducing confusion and improving communication between departments.
One of the key features of Delivery Track is its ability to provide manufacturers with real-time insights into job performance. The software now includes a Universal ERP Connector, which enables seamless integration with any ERP system. This update allows manufacturers to pull in work orders, quantities, and due dates automatically, eliminating the need for manual data entry and ensuring that job tracking is always aligned with real-time performance on the shop floor. As a result, manufacturers can stay on top of production schedules and meet deadlines with confidence.
The upgraded Delivery Track software also features enhanced analytics that provide key metrics such as overall equipment effectiveness (OEE) and on-time delivery by customer, part number, and part family. This allows manufacturers to monitor performance and make data-driven decisions to improve efficiency and reduce risks. Additionally, the software offers live job monitoring and projected completion times, so manufacturers can see how jobs are progressing and identify potential issues before they impact delivery.
Another critical capability is the Job History Scorecards feature, which allows manufacturers to review past performance by customer, part number, work order, or timeframe. This feature helps pinpoint wins and losses in previous jobs, enabling manufacturers to learn from past experiences and refine their processes for future jobs. The Machine Availability Planner also helps manufacturers identify the best machine for upcoming jobs based on availability and performance forecasts, ensuring that resources are used efficiently and jobs are completed on time.
The universal ERP connectivity also extends beyond just data integration. It helps align different departments—engineering, operations, planning, and sales—by providing everyone with the same up-to-date information. With this integration, all teams can plan smarter, improve coordination, and work towards shared production goals. This synchronized approach is crucial for improving operational flow and minimizing delays in the production process.
According to Greg McHale, Datanomix’s founder and CEO, “Delivery Track is about more than just schedules — it’s about creating a single source of truth for your shop. By connecting your ERP to real-time machine data, we’re giving manufacturers a complete, accurate picture of what’s going on and what needs to happen next. That’s how great teams stay on track and deliver with confidence.”
With these new updates, Delivery Track empowers manufacturers to make informed decisions, optimize production processes, and ensure timely delivery—all while minimizing manual effort. This software solution not only provides real-time tracking but also enhances overall operational efficiency by seamlessly connecting machine data with ERP systems, helping manufacturers improve accuracy, reduce errors, and maintain a steady flow of work on the shop floor.
Renishaw’s RCS Product Line: Revolutionizing Robotics Automation for Improved Efficiency and Productivity!
Renishaw, a leader in precision engineering and automation solutions, has introduced its RCS product line to address key challenges faced by industries using robotic systems. The RCS series is designed to streamline robot setup, calibration, and maintenance, providing a significant boost to operational efficiency, accuracy, and repeatability in industrial automation. This new offering is set to transform how robots are integrated and managed in manufacturing processes, helping businesses reduce downtime and improve overall productivity.
The RCS product line includes three innovative products: the RCS L-90, the RCS T-90, and the RCS P-series. Each of these products is equipped with advanced technologies such as sensors, controllers, robotics, and sophisticated software, all aimed at enhancing the performance of robotic systems. These solutions are specifically designed to solve the challenges of manual intervention, ensuring that robots can be more reliable, easier to manage, and capable of performing with minimal human oversight.
One of the flagship products in this line is the RCS L-90 ballbar, which improves the accuracy of robotic systems by reducing deployment time and monitoring robot health. The L-90 ballbar runs simple routines controlled by its accompanying software suite, which makes it easier to identify and address any performance issues. This results in more precise operations, ensuring that robots perform at their best over extended periods. The ability to monitor robot health in real-time also helps anticipate potential failures before they occur, preventing costly downtime and disruptions.
The RCS T-90 system is another key product in the RCS line. This advanced tri-ballbar system enables robotic users to identify the root causes of poor performance by conducting in-depth tests. These tests include remastering joint offsets, recovering from master errors, and plotting 3D path performance. With the T-90, users can gain a clearer understanding of the underlying issues that affect robot precision, allowing them to make necessary adjustments to improve performance. The ability to perform comprehensive tests and gather critical information in real-time enhances the robot’s operational lifespan, ensuring that they continue to deliver high-quality results for longer.
The RCS P-series completes the lineup by integrating Renishaw’s permanent probing solution within a robot cell. This product facilitates in-process metrology, enabling automatic recovery of robotic applications following collisions or other disruptions. This makes it an ideal solution for industries where continuous, high-precision operation is critical. By implementing automated recovery features, the RCS P-series minimizes downtime and ensures that robotic processes continue to operate efficiently even after a disturbance, reducing the need for manual intervention.
All of these products are supported by Renishaw’s intuitive RCS Software Suite, which provides easy integration with robots from a wide variety of manufacturers. Whether used for simple setups, health checks, or recovery processes, the RCS product line helps companies simplify robot management and optimize performance across their automation systems. This is especially important in fast-paced manufacturing environments where minimizing downtime and maintaining operational consistency are key factors in overall productivity.
In addition to enhancing robot performance, the RCS series also supports businesses in optimizing resource efficiency. With fewer manual interventions and better performance tracking, these tools enable more sustainable manufacturing processes. The RCS products not only improve accuracy but also contribute to cost savings and higher production outputs by reducing machine downtime and the need for frequent repairs.
In conclusion, Renishaw’s RCS product line is a groundbreaking solution that elevates the capabilities of robotic systems in industrial automation. By addressing critical challenges such as accuracy, repeatability, and recovery after disruptions, the RCS series enables businesses to run more efficient, sustainable, and cost-effective operations. As industries continue to integrate more robotics into their workflows, tools like the RCS products will be essential for maintaining high-performance standards and ensuring long-term success in the competitive world of manufacturing.
United Machining Solutions Emerges as Global Powerhouse Following GF Machining Solutions Takeover
The merger of the GF Machining Solutions Division of George Fischer AG with the United Grinding Group has created one of the world’s largest machine tool manufacturers. Now operating under the new name United Machining Solutions, the group boasts total sales exceeding USD 1.5 billion and employs around 5,000 people across more than 50 locations worldwide. The company’s headquarters remain in Bern, Switzerland.
Stephan Nell, CEO of the United Grinding Group and the new group, expressed enthusiasm about the union: “There has been a long-standing desire to merge the two companies. Our lead shareholders have shown full confidence in this strategically important step, which combines two highly complementary businesses.” Nell emphasized that the partnership goes beyond product portfolios to shared values and company cultures, positioning the group to deliver significant benefits to customers.
Fred Gaegauf, chairman of the United Grinding Group’s board, echoed this sentiment: “The merger has created a Swiss powerhouse in machine tool manufacturing.” With a broad international footprint, an extensive product range, and 15 leading industry brands, the foundation is set for continued growth and innovation.
Ivan Filisetti, CEO of GF Machining Solutions and a member of the new management board, highlighted the complementary nature of the products: “Our portfolios do not overlap; they complement each other, making integration straightforward. Both companies share Swiss roots and a strong commitment to innovation and digitalization, enabling us to deliver customized solutions beyond just high-end machines.” The group’s international presence and technological expertise provide unmatched support to customers on site.
Collaboration in research and development is a key advantage of the merger. It enables joint innovation efforts and allows the group to respond proactively to evolving industry standards and regulations, ensuring future-proof machine tools.
United Machining Solutions will continue to showcase its established brands, preserving their market identities and customer trust. The two divisions—United Grinding and United Machining—operate under the group umbrella but maintain their individual brand strengths.
United Grinding’s portfolio includes Mägerle, Blohm, Jung, Studer, Schaudt, Mikrosa, Walter Ewag, and IRPD, specializing in surface and profile grinding, cylindrical grinding, tool machining, and additive manufacturing. The division offers deep application expertise and a wide product and service range for precision components.
United Machining, formed from GF Machining Solutions, incorporates brands such as Agie Charmilles, Charmilles, Mikron Mill, Liechti, Step Tec, and System 3R. It focuses on high-speed milling, EDM (Electrical Discharge Machining), laser texturing, laser micro-machining, as well as advanced spindles, automation, and digital solutions with extensive customer support.
The group’s leadership team combines decades of experience: Stephan Nell leads strategic sales and customer care; Ivan Filisetti drives technological vision; Michael Horn manages operations and IT; and Heinz Poklekowski oversees finance and group services.
United Machining Solutions will debut as a combined entity at EMO Hannover 2025, the world’s premier production technology trade fair, held from September 22–26. Representing 15 brands, the group will unveil eight world-first innovations, marking a significant milestone for the newly formed industry leader.
Renishaw Launches Equator–X 500: A Dual-Mode Breakthrough in Shopfloor Metrology
Renishaw, a global leader in precision measurement and manufacturing systems, has unveiled its latest innovation for shopfloor process control—the Equator–X 500 dual-method system. Designed to meet the fast-evolving demands of modern manufacturing, this pioneering device combines two powerful inspection modes—Absolute and Compare—within a single, compact solution. The result is unprecedented flexibility for manufacturers needing to optimize speed, accuracy, and adaptability in quality control.
The Equator–X 500 responds to a key industry challenge: how to efficiently inspect parts on shopfloors where frequent product changeovers and varying batch sizes demand both speed and flexibility. By offering both Absolute and Compare modes, the system allows users to tailor the measurement method to the specific application—essentially deploying two high-performance systems in one.
In Absolute mode, the Equator–X 500 scans parts at speeds of up to 250mm/s, enabling rapid verification of small to medium batch sizes with high part variation. This mode is ideal for first-off inspections next to the machine or for full verification of components in variable production runs. The high-speed scanning significantly improves throughput without sacrificing precision.
Alternatively, Compare mode offers ultra-fast scanning at speeds up to 500mm/s, making it the go-to choice for high-volume production of identical parts. This mode is especially beneficial in thermally unstable environments, where the system’s built-in thermal compensation ensures consistent measurement reliability.
Structurally, the Equator–X 500 features a robust hexapod design with separate metrology and drive frames. Components like carbon fibre metrology struts, linear motor drives, and the Renishaw SP25M scanning probe enable rapid movement while maintaining high measurement accuracy. The system can operate as a standalone inspection station or be seamlessly integrated into automated production cells, adapting to evolving manufacturing needs.
Supporting the hardware is Renishaw’s advanced MODUS™ IM metrology software, which provides a powerful, user-friendly platform for programming, measurement execution, and data reporting. The intuitive operator interface simplifies complex tasks, while delivering the performance and traceability manufacturers demand on the shopfloor.
The Equator–X 500 sets a new benchmark in shopfloor gauging, combining speed, adaptability, and precision in a single system. With its dual-mode capability, it empowers manufacturers to maintain process control and quality assurance in even the most demanding production environments.
Compact Precision: OTT-JAKOB Launches Power-Check Micro for Small Spindles
OTT-JAKOB Spanntechnik, the renowned German specialist in tool clamping systems, has introduced a new spindle clamping force measurement device—the Power-Check Micro. Designed for compact machine tools, this new addition complements the existing Power-Check 2 and Power-Check Magazine systems, which are commonly used for measuring drawbar force in larger spindle tapers such as HSK 160, BT, SK, and CAT formats.
The Power-Check Micro, by contrast, is purpose-built for smaller spindle interfaces—specifically HSK E15, E16, and E20—commonly found in high-speed, precision machine tools. These machines are prevalent in sectors such as dental and jewelry manufacturing, micro-electronics, aerospace, medical technology, and miniature tool and die production, where accuracy and repeatability are paramount.
Exclusively distributed in the UK and Ireland by Gewefa UK, the Power-Check Micro supports the growing demand in micro-manufacturing for process reliability, condition monitoring, and preventative maintenance. Compact and lightweight—measuring just 48.8 x 43 x 41.5 mm and weighing around 200g—the device is ideal for use in tight working environments. It operates independently of mains power using two replaceable lithium batteries, offering up to 1,000 hours of use.
The system supports interchangeable screw-on adapters for different HSK sizes and is compatible with clamping systems from all tool manufacturers. Like its larger counterparts, it measures the axial pull-in force exerted by a machine’s drawbar to ensure secure tool clamping. Deviation from optimal clamping force can lead to tool wear, vibration, surface quality issues, or tool failure—issues that are particularly critical in high-precision applications.
Notably, the Power-Check Micro can simulate variations in tool holder dimensions using a unique adjustment ring graduated in 0.05mm increments, allowing the user to mimic tolerance differences up to ±0.2mm—ensuring more realistic testing conditions than systems that rely solely on nominal dimensions.
The device is manually inserted and should never be used with an active spindle or during automatic tool change. Once in place, it transmits data wirelessly (2.4GHz) at one reading per second to a compatible receiver. Several transmission modules are available, including USB and IO-Link options, for seamless integration with digital manufacturing systems.
Offered as a standalone device or in a complete kit—with rugged case, batteries, PC software, and USB receiver—the Power-Check Micro brings simplicity, precision, and reliability to small-format spindle force monitoring. Annual recalibration and regular checks are recommended to maintain peak performance.
MC Machinery Names Mitch Foley as Finishing Product Manager!
MC Machinery Systems Inc., a leading provider of advanced machinery solutions, has announced the appointment of Mitch Foley as the new Sales and Product Manager, Finishing. Foley brings with him a wealth of experience in engineering, product development, and sales, making him a valuable addition to the company’s team.
Foley’s career trajectory has seen a seamless transition from engineering to sales, allowing him to effectively combine his technical expertise with a deep understanding of market dynamics. This unique blend of skills positions him well to guide MC Machinery’s finishing product strategy, ensuring the company’s products meet the evolving needs of its customers.
In his new role, Foley will be responsible for supporting full sales cycles, working closely with customers to develop both standard and customized finishing systems. His extensive experience managing dealer networks and supporting customers throughout North America, particularly in the U.S. and Canadian markets, will allow him to drive sales growth while strengthening relationships with existing clients and partners.
MC Machinery’s appointment of Mitch Foley highlights the company’s commitment to innovation and customer-centric service, ensuring that their finishing product portfolio continues to meet the diverse needs of industries across the region. With his technical knowledge and sales acumen, Foley is poised to play a pivotal role in shaping the future of MC Machinery’s finishing solutions.
Phoenix Manufacturing Announces Expansion Plans with $1.1 Million Investment in Automated Equipment!
Phoenix Manufacturing, a well-established name in the industrial manufacturing and fabrication industry, has unveiled its plans for a major expansion in Glasgow, Missouri. The expansion, backed by an investment of over $1.1 million, will see the company enhance its production capabilities by incorporating automated equipment, further streamlining its fabrication processes.
The investment will not only modernize the company’s operations but also contribute to the local economy by creating 14 new jobs. These roles will primarily focus on supporting the expanded manufacturing capacity, reinforcing Phoenix Manufacturing’s commitment to local job creation and its community in Glasgow.
Phoenix Manufacturing has built a reputation for providing commercial fabrication services in a wide range of industries. The company specializes in vertical and horizontal fabrication and offers services in energy, industrial fabrication, and the production of special one-off and miscellaneous metals. Their job shop fabrication services cater to a variety of sectors, providing high-quality products tailored to customer specifications.
The incorporation of automated equipment is part of Phoenix’s strategic effort to improve efficiency, increase production speed, and enhance product quality. The automation will also support the company’s ability to meet growing customer demands while maintaining its competitive edge in the industrial manufacturing market.
This expansion demonstrates Phoenix Manufacturing’s commitment to innovation and continuous improvement, ensuring it remains a trusted partner for industries in need of high-quality, customized metal fabrication solutions. As the company continues to invest in advanced technologies, it aims to strengthen its position in the market while contributing positively to the Missouri economy through job creation and technological advancement.
Pemamek Appoints Fernanda Saldaña as Area Sales Manager for Mexico to Strengthen Local Presence!
Pemamek Ltd., a recognized leader in welding and production automation, has announced the appointment of Fernanda Saldaña as its new Area Sales Manager for Mexico. This strategic move is aimed at bolstering Pemamek’s market presence and providing enhanced support to customers in key industries such as energy, heavy equipment, and general manufacturing within the region.
Fernanda Saldaña brings over a decade of experience in the heavy industry sector, including five years of expertise in managing automation projects with Pemamek’s partner, IP Grupo. Her deep understanding of both the industrial landscape and Pemamek’s high-precision robotic welding equipment positions her as a valuable asset to drive the company’s growth and customer engagement in Mexico.
In her new role, Saldaña will focus on expanding Pemamek’s footprint in Mexico by assisting customers in optimizing their welding processes with the company’s state-of-the-art solutions, including custom systems for thick materials. Pemamek’s technologies, known for their precision and reliability, are expected to address the growing demand for automation in welding across industries that require advanced solutions for complex and high-demand applications.
Pemamek, which has a strong reputation in the global manufacturing landscape, offers cutting-edge automation solutions that enhance production efficiency and ensure the highest levels of quality in welding. With Saldaña’s leadership, the company is poised to strengthen relationships with existing clients while exploring new opportunities in Mexico’s rapidly developing industrial sectors.
The appointment highlights Pemamek’s ongoing commitment to supporting its customers with local expertise and tailored solutions, ensuring they can maintain competitive advantage and improve operational efficiency. With Saldaña’s expertise in automation and industrial systems, Pemamek aims to continue delivering innovative solutions that meet the needs of the Mexican market.
Gweike Laser Unveils M Series Six-in-One Laser System for Cutting, Welding, Cleaning, and Engraving!
Gweike Laser, a leading name in advanced laser technology, has introduced its new M Series six-in-one laser system, designed to revolutionize multiple industrial applications by integrating six distinct functions into a single, compact unit. The M Series combines fiber laser CNC cutting, hand-held laser welding, hand-held laser cutting, hand-held laser cleaning, CO₂ cutting, and CO₂ engraving, offering an unparalleled level of versatility for modern manufacturing processes.
Powered by both a 1,200-W fiber laser and a 130-W CO₂ laser, the M Series laser system is engineered to provide outstanding performance across a variety of demanding applications. The system boasts a cutting speed of up to 800 mm/sec, ensuring fast and efficient processing. Furthermore, the ±0.02-mm repeat positioning accuracy ensures precision and consistency, even in complex tasks. Capable of cutting 10-mm carbon steel and 6-mm stainless steel, the M Series is particularly suited for heavy-duty applications that require both high power and high precision.
The laser system produces an ultrafine-focused spot, allowing for high-precision cutting with clean edges and sharp lines. This capability makes it ideal for intricate and detailed designs, offering manufacturers the ability to achieve complex curves and fine details without compromising on quality. The system’s smooth cutting feature ensures that even the most challenging parts can be cut with minimal burrs or imperfections, which is crucial for applications requiring high aesthetic and functional quality.
In addition to its cutting capabilities, the M Series integrates hand-held laser welding, hand-held laser cutting, hand-held laser cleaning, and CO₂ engraving, providing a complete range of solutions for various production needs. The inclusion of multiple functions in a single machine significantly enhances flexibility and minimizes the need for additional equipment, making it a valuable asset for businesses looking to streamline operations and optimize production costs.
The hand-held laser welding and cutting features allow for easy operation and mobility, enabling workers to perform high-quality welds or cuts on-site, making the system suitable for both large-scale factory settings and more localized applications. Similarly, the hand-held laser cleaning function allows for efficient rust, paint, and coating removal, providing a sustainable alternative to traditional cleaning methods.
By combining all these functions into a single, powerful unit, the M Series six-in-one laser system offers manufacturers greater operational efficiency, cost savings, and space optimization. The flexibility to switch between cutting, welding, cleaning, and engraving processes with a single machine makes the M Series an invaluable tool for industries ranging from automotive manufacturing to metalworking, aerospace, and beyond.
Overall, the M Series laser system by Gweike Laser sets a new standard for multi-functionality, precision, and efficiency in laser processing, helping manufacturers tackle diverse challenges while maintaining high levels of performance and productivity.
Otto Aviation Expands with New Florida Manufacturing Facility and Headquarters for Phantom 3500 Jet Production!
Otto Aviation, an innovative leader in the aviation industry, has announced plans to build a state-of-the-art manufacturing and production facility at Cecil Airport in Jacksonville, Florida. This move marks a significant step in the company’s growth and its commitment to advancing the aviation industry with its cutting-edge Phantom 3500 next-generation business jet.
The new manufacturing facility will occupy between 80 to 100 acres of land at Cecil Airport, and will serve as the central site for the final assembly of the Phantom 3500. The Phantom 3500, an advanced business jet designed for the future of aviation, will be a critical player in Otto Aviation’s long-term vision to lead the market with sustainable, high-performance aviation solutions. The project is expected to generate hundreds of manufacturing and engineering jobs, driving economic growth in the Jacksonville area.
Initially, Otto Aviation will begin operations in Hangar 825, which was originally constructed by the U.S. Navy for aircraft fleet operations. This facility will serve as the starting point for the manufacturing process, with plans to develop a dedicated, fully-equipped production plant specifically designed for the Phantom 3500 assembly. The company’s headquarters will also be relocated to Jacksonville, establishing the region as the focal point for Otto Aviation’s future growth and innovation in the aviation sector.
Production of flight test vehicles for the Phantom 3500 is expected to begin in 2026, with flight tests slated to commence in early 2027. Otto Aviation aims to achieve full certification and entry into service for the Phantom 3500 by 2030, marking a significant milestone in its quest to revolutionize business aviation with cutting-edge technology and superior performance.
This strategic move not only strengthens Otto Aviation’s commitment to innovation and quality but also bolsters Florida’s aerospace and aviation industry with a focus on advanced manufacturing techniques and high-tech job creation. The new facility at Cecil Airport is poised to become a cornerstone of Otto Aviation’s future success, enabling the company to take the next big leap in the development of the Phantom 3500 and other future aviation projects.
With the combination of new manufacturing capabilities, strategic workforce development, and the relocation of the company headquarters, Otto Aviation is positioning itself at the forefront of the evolving aviation landscape. The Phantom 3500, with its advanced capabilities and sustainable design, is set to redefine business jet travel for the next generation of aviation leaders.
Universal Robots Launches UR Studio: Simplifying Robot Cell Customization with Online Simulation Tool!
Universal Robots, a leader in collaborative robotics, has unveiled its latest innovation, the UR Studio, an advanced online simulation tool designed to streamline robot cell customization. Built on the company’s AI-ready PolyScope X software platform, the UR Studio allows users to easily create 1-to-1 simulations of workcells, enabling them to test and optimize robot operations before implementing them in real-world settings.
The tool offers an intuitive interface that enables users to simulate and interact with a variety of key workcell components, including robot movements, reach, speed, and workflow, helping users to assess the system’s performance. Additionally, the UR Studio allows users to calculate cycle times and refine setups, ensuring that every element of the robotic cell operates at peak efficiency.
One of the standout features of UR Studio is its flexibility. Users can interact with Universal Robots’ diverse robot portfolio and configure essential workcell components, such as pallets, machines, workpieces, and end effectors like standard grippers. The tool also allows for the easy import of custom components, ensuring that the simulation mirrors the user’s actual workspace.
This innovative tool is designed to simplify the setup and optimize workflows, enabling manufacturers to tailor their robot systems to their specific needs. By using UR Studio, companies can eliminate potential inefficiencies before the actual implementation of the workcell, cutting down on setup time and improving overall productivity.
Universal Robots’ UR Studio leverages the latest advancements in AI-driven simulation, providing users with a high degree of flexibility and control. Whether creating simple robot tasks or configuring complex workcell setups, UR Studio offers a seamless way to customize and refine automation systems in a user-friendly, virtual environment.
This release is part of Universal Robots’ broader strategy to make automation more accessible and efficient for businesses of all sizes, from small startups to large enterprises. With UR Studio, companies can enhance their design process, boost productivity, and ensure the reliability of their robotic systems before deployment.
Fastems Unveils Revolutionary Automation Solutions at EMO Hanover 2025
Krefeld, Germany – June 20, 2025 – Fastems is set to unveil groundbreaking innovations at EMO Hanover 2025, the world’s premier trade fair for the metalworking industry. Visitors to booth B54 in Hall 12 can expect to see a wide range of automation solutions for milling, turning and other processes– including a genuine innovation making CNC automation more accessible than ever.
At their “Automate Machining and More” showcase, Fastems will demonstrate the possibilities of FMS in 2025. Not only does FMS automate 4 and 5 axis machining centers – it can also integrate a variety of surrounding process operations such as cutting tool changes, washing, quality and traceability. In addition to physically integrating machines and devices, the FMS production control software MMS can also schedule and guide the work of stand-alone machines and other operations, such as sawing or finishing.
Flexible Pallet System (FPS) – Experience 360-Degree Flexibility
The space-efficient milling automation Flexible Pallet System (FPS) is a modular solution designed for payloads ranging from 500 to 1,500 kg. Thanks to its 360-degree design, machine tools, pallet storage, and operator stations can be flexibly arranged on all four sides of the system. This makes FPS ideal for production environments with limited space.
“Our newest automation FPS is compatible with hundreds of 4- and 5-axis machines from over 90 manufacturers – and we are continuously expanding our integration capabilities. In addition to the physical system on display, visitors can try out our new FPS Studio to find the best configuration for their own machines,” explains Janne Kivinen, Product Manager of Milling Automation at Fastems.
Automating Single-Table Machining Centers Economically
Fastems is introducing a revolutionary eLock solution that enables cost-efficient automation for milling machining centers without pallet changers or zero-point pallet technology. Based on electromagnetic power transmission, eLock is a patent-pending bolt-on pallet changing solution that requires no media leadthrough or wiring on the machine tool table.
“High-quality 4 and 5 axis machining centers without pallet changing capability are very common, and we constantly get requests to automate them. We are super proud to now launch a simple and economical solution to automate the pallet changes in these machines as well,” says Janne Kivinen of Fastems.
Work Cell Operations (WCO) – Paperless Production with Manual and Stand-Alone Operations
Many manufacturers have standalone operations within their processes that are not connected to any automation. These operations are often managed manually using Excel spreadsheets or paper. To digitize and automatically schedule these tasks to play together with FMS efficiently, Fastems showcases Work Cell Operations (WCO) – a software module that significantly extends MMS by enabling automated production planning even for non-automated workflows.
“WCO helps eliminate bottlenecks, digitize operations, and streamline manufacturing – it reduces unnecessary WIP and ensures everyone on the shop floor knows exactly what needs to be done next,” says Bulza Krajkova, Product Manager of Digital Services at Fastems.
More Productivity through Tool Automation
Cutting tool changes are one of the key bottlenecks in high-mix-low-volume manufacturing. Fastems will present its tool automation solutions, Gantry Tool Storage and Central Tool Storage, which enable continuous machining and long lights-out periods in high tool usage. “Frequent tool changes not only consume machine capacity, but also valuable time. Our tool automation solutions free up operators for other tasks by automatically sharing tools between machines. This reduces the need for large tool magazines as well as sister tools,” explains Teemu-Pekka Ahonen, Product Manager of Integrated Robotics at Fastems.
For more information, visit fastems.com/emo-2025
Seco Tools Strengthens Commitment to Sustainability with Circular Manufacturing Strategy!
Seco Tools, a leading provider of cutting tools and solutions, is taking a significant step towards advancing sustainability in the manufacturing sector with the expansion of its circularity initiatives. The company is reshaping how value is created, retained, and recovered across its operations, marking a shift towards long-term environmental sustainability in the cutting tools industry. By integrating circular principles into product design, manufacturing, business models, and customer engagement, Seco aims to transform the manufacturing process and drive sustainability across its entire value chain.
Circularity has become a core business approach at Seco Tools, influencing every stage of the production process. The company is embracing new business models that extend beyond traditional recycling to focus on durability, repairability, and reuse. Seco’s efforts are not limited to recycling; instead, they emphasize optimizing resource efficiency, improving recovery systems, and working closely with its supply chain and customers to create a more sustainable and circular operation.
One of the key components of Seco’s strategy is the design of products that support multiple use cycles. With a focus on extending the lifespan of tools, Seco works to refurbish and recondition products, reducing waste and decreasing environmental impact. This circular approach also brings cost benefits to customers, who can maximize the lifespan of their tools and reduce the need for frequent replacements. Furthermore, Seco collaborates with its partners and customers to enhance tool performance and process efficiency, offering engineering support and lifecycle services to optimize tool use over time.
In addition to improving product lifecycles, Seco is focused on increasing the traceability of its products. The company has implemented data matrix codes on inserts and round tools, enabling both Seco and its customers to track tools throughout their lifespan. This system provides valuable insights into tool usage, maintenance, and end-of-life management, allowing for more informed decisions. By ensuring that tools are used efficiently and are reconditioned appropriately, Seco helps its customers reduce underutilized tool capacity, extend tool longevity, and ultimately make more sustainable choices.
Seco has set ambitious sustainability goals, with the company aiming to achieve 90% circularity in its products, packaging, and waste by 2030. This includes integrating circularity principles into its internal operations and encouraging suppliers and customers to adopt similar sustainable practices. By working collaboratively across its supply chain, Seco seeks to create a more circular ecosystem that maximizes resource efficiency, reduces environmental impact, and promotes the long-term sustainability of manufacturing.
Through these forward-thinking efforts, Seco Tools is positioning itself as a leader in sustainable manufacturing, advancing circularity in the cutting tools industry, and setting an example for other manufacturers to follow. By focusing on extending product life, improving resource recovery, and embracing sustainable practices at every stage of its operations, Seco is helping to build a more sustainable future for manufacturing and contributing to the broader global effort to address environmental challenges.
As part of its ongoing commitment to sustainability, Seco Tools continues to explore innovative solutions, work closely with its customers, and lead by example in adopting circularity principles throughout its operations. This strategy not only drives environmental benefits but also helps Seco and its customers create value while supporting a greener, more sustainable manufacturing industry.
Dusty Alexander Celebrates 35 Years of Leadership at Global Shop Solutions, Driving Expansion and Innovation!
Dusty Alexander, the President and CEO of Global Shop Solutions, has reached an extraordinary milestone of 35 years at the company. Throughout his tenure, Alexander has been instrumental in the company’s remarkable growth, strategic expansions, and its evolution into a global leader in enterprise resource planning (ERP) software solutions. Under his visionary leadership, Global Shop Solutions has not only scaled its operations but also reinforced its core values of being a family-owned, privately held company with zero reliance on debt or external investment.
When Alexander first took the helm at Global Shop Solutions, the company was primarily focused on providing ERP software to the manufacturing industry. Over the years, he guided the company’s expansion into international markets, successfully establishing a strong presence in regions like Canada, Latin America, and the Asia-Pacific. This expansion included setting up offices in Mexico, Singapore, Indonesia, Australia, New Zealand, and the United Kingdom, among others, bringing Global Shop Solutions’ products to a wider global audience and solidifying its reputation as a trusted ERP provider for manufacturers around the world.
A key element of the company’s growth was the expansion of its headquarters in The Woodlands, Texas, which now boasts a dedicated research and development excellence center and a customer training center. These additions were pivotal in driving continuous innovation and enhancing customer engagement through hands-on training and product development. Under Alexander’s leadership, the company’s workforce grew substantially, tripling in size, and revenue saw a nearly tenfold increase, reflecting the success of its global expansion efforts.
Alexander’s leadership philosophy is rooted in three key principles: attracting and retaining top talent, listening to customers, and fostering continuous product improvement. These principles have not only guided the company’s strategic direction but also ensured that Global Shop Solutions remains agile and responsive to the ever-changing demands of the manufacturing sector. His emphasis on customer feedback has led to the establishment of dedicated customer care and continuous improvement teams that work to enhance service quality and customer satisfaction, ensuring that Global Shop Solutions remains a reliable partner for manufacturers worldwide.
Another significant achievement during Alexander’s tenure was the development of Global Shop Solutions’ comprehensive ERP platform that caters specifically to the needs of manufacturers. The company’s ERP system is designed to help manufacturers streamline operations, reduce costs, and increase efficiency, making it an invaluable tool for businesses across a variety of industries. This platform continues to evolve, thanks to Alexander’s focus on long-term strategic planning and constant product enhancements driven by customer needs.
Looking toward the future, Alexander remains committed to continuing the growth trajectory of Global Shop Solutions. He plans to expand the capabilities of the company’s ERP tools, with a particular focus on helping customers optimize their operations and enhance their efficiency. His goal is to continue delivering adaptable and customer-driven solutions that enable manufacturers to achieve their goals, whether that’s delivering quality parts on time or driving operational efficiency across the supply chain.
Reflecting on his 35 years at the company, Alexander shared his deep passion for the manufacturing industry, noting that it has always been the people they serve and the impact they make that fuels his passion. “I fell in love with manufacturing from my first day on the job. It has always been the people we serve and what we do for them that keeps me revved up every day,” he said. “I come to work determined to make a great product and great services that benefit our customers and their employees. My 35 years here have been an honor.”
As Global Shop Solutions continues to evolve, Alexander’s leadership will undoubtedly remain a guiding force in shaping the future of ERP solutions for the manufacturing sector, further enhancing the company’s global footprint and innovation in the years to come.
Dillon Manufacturing Introduces Reversible Hard Jaws to Optimize Turning Operations!
Dillon Manufacturing has launched a new line of reversible hard jaws designed to streamline turning operations and reduce setup times. These high-precision jaws are engineered for both internal (ID) and external (OD) workholding, making them ideal for use in first-operation setups where fast, accurate part gripping is critical.
The new reversible jaws provide users with the ability to quickly adapt to different part sizes, ensuring secure and stable clamping. This flexibility is especially beneficial for industries that handle a range of part sizes in various production runs, as it eliminates the need for frequent jaw replacements or adjustments. With the ability to hold a specific range of part sizes, these jaws not only reduce setup time but also help improve overall efficiency on the shop floor.
Dillon’s reversible hard jaws are designed to be compatible with all major chuck brands, making them a versatile solution for most machining setups. Available in multiple configurations, including serrated, Acme key, square key, and tongue-and-groove styles, these jaws cater to various clamping preferences and provide users with multiple options to meet their specific workholding requirements. For enhanced gripping and precision, the jaws feature diamond-shaped serrations that ensure strong, slip-resistant gripping power and precise part alignment.
Constructed from 8620 case-hardened steel, Dillon’s hard jaws are built for durability and long-lasting performance. Precision-ground locating surfaces further enhance the accuracy of each jaw, ensuring reliable part positioning during turning operations. The jaws are coated with black oxide to improve corrosion resistance, ensuring that they remain in top condition even in challenging work environments.
The introduction of Dillon’s reversible hard jaws marks a significant step forward in optimizing workholding solutions for turning operations. By reducing setup times and providing a range of durable, precision options, these jaws are designed to meet the demands of modern manufacturing processes, where both speed and accuracy are critical.
HORN Unveils the DM 50 Series Modular Milling System for Efficient Aluminum Machining!
HORN has introduced the DM 50 series, a cutting-edge modular milling system designed specifically for high-efficiency machining of aluminum. This new product promises to meet the demands of industries that require precision and speed in aluminum processing, offering significant advantages in terms of versatility, ease of maintenance, and cost efficiency.
The DM 50 series utilizes a modular PCD (Polycrystalline Diamond) milling system with a replaceable head configuration, a design that provides flexibility and reduces downtime. In this system, the key components that typically experience wear—the milling head and inserts—can be independently replaced, allowing users to replace only the worn parts rather than the entire tool body. This reduces operational costs and contributes to a more sustainable machining process.
An intermediate sleeve is included in the system, which provides flexibility in adapting to different application requirements. This sleeve enables users to adjust the cutting height without having to change the entire tool, offering the capability to fine-tune the milling operation for various specifications and improving efficiency. Whether a slight adjustment or a more significant change is required, the modular system ensures minimal disruption to the machining process.
One of the standout features of the DM 50 series is its ability to be quickly reconfigured to accommodate different corner radii and chamfer specifications, all at the required cutting height. This adaptability makes the DM 50 series an excellent choice for shops that handle a wide variety of aluminum parts and need tools that can be adjusted rapidly for different requirements.
The cutter of the DM 50 series is designed with a 2:1 insert arrangement, with inserts positioned across the face and periphery of the tool. This configuration supports various milling strategies, enabling users to efficiently mill complex parts while maintaining high levels of precision and surface finish. This modular system also offers reliable indexing, ensuring consistent performance during tool changes. The precise indexing helps improve overall operational efficiency and reduces the potential for errors, making it ideal for high-volume production environments.
Another important feature of the DM 50 series is its optimized axial geometry, which reduces cutting forces while maintaining a high-quality surface finish. This contributes to the longevity of both the tool and the workpiece, allowing for smoother cuts, reduced vibration, and better overall results in aluminum milling operations. The reduction in cutting forces also contributes to lower energy consumption and longer tool life, further enhancing the system’s cost-effectiveness.
With the introduction of the DM 50 series, HORN is offering a tool that combines high efficiency, flexibility, and sustainability. The system’s modular nature and ability to adapt to various application requirements make it a versatile solution for manufacturers in sectors like automotive, aerospace, and general machining, where aluminum is a primary material. By providing users with the ability to customize their tools for different milling needs and quickly replace only the worn parts, HORN’s DM 50 series represents a significant advancement in aluminum machining technology, helping businesses improve productivity and reduce operational costs.
Fixtureworks Introduces Versatile QLRCW Thrust Clamp for Efficient Workholding!
Fixtureworks has expanded its Stablelock Clamp series with the introduction of the QLRCW series, a versatile clamp designed for both thrust and pull clamping applications. This innovative clamp combines simplicity with high functionality, offering manufacturers an easy-to-use solution for securing workpieces during machining processes.
The QLRCW clamp operates through a straightforward handle-turn mechanism that grips a bar or pin shaft securely. When the handle is turned, balls within the mechanism are pushed outward by a tapered surface, which in turn compresses the collet to hold the shaft tightly in place. The spring-loaded clamping system ensures that the clamping force remains constant, enhancing the reliability of the fixture throughout the machining process.
One of the key features of the QLRCW clamp is its ability to function both as a thrust clamp and a pull clamp, depending on the workholding requirements. When used as a thrust clamp, it requires an additional clamping bar (sold separately) to achieve the necessary gripping force. The handle is released to retract the clamping bar, allowing for easy removal of the workpiece once the operation is complete.
In addition, when paired with a clamping pin (not included), the QLRCW clamp can also be used as a pull-type clamp. In this configuration, turning the handle locks the base clamp onto the pin, providing another option for secure and precise workholding.
For ease of use and accuracy, the QLRCW series features an indication line on both the body and the base of the clamp. This visual aid clearly shows when the clamp is in the engaged or disengaged position, while a distinct “click” sound further confirms when the clamping process has been completed successfully. This attention to detail ensures users can quickly and confidently verify the clamp’s status, reducing the chances of errors during setup.
The QLRCW clamps are made from durable materials, with the body and collet constructed from electroless nickel-plated pre-hardened steel, while the cover and lever arm are made from electroless nickel-plated 1045 steel. The handle is crafted from black phenolic plastic, ensuring a robust design that is built to withstand rigorous industrial use.
The clamps come in two clamping directions: clockwise (QLRCW40R0) and counterclockwise (QLRCW40L), providing flexibility depending on the specific needs of the operation. With up to 112 pounds of clamping force and a 150-degree rotation travel, the QLRCW clamp offers strong performance in a compact form factor, measuring less than two inches in height when in the clamped position.
This new addition to Fixtureworks’ product lineup is designed to meet the demands of industries that require reliable, efficient, and space-saving clamping solutions, such as automotive, aerospace, and other precision machining sectors. The QLRCW series offers manufacturers an easy-to-operate yet powerful tool for securing components during machining, improving efficiency and ensuring consistent results.
Chevalier CNC Slant-Bed Lathe Automates Small-Part Production with Advanced Features!
Chevalier Machinery Inc. has introduced the FCL-130RP, a high-precision CNC lathe designed specifically for small-part automation. This new model is engineered to meet the growing demand for space-efficient, high-speed turning solutions across various industries, providing a reliable and compact solution for production lines with limited space.
At a machine length of 70.9″ (1802 mm), the FCL-130RP is designed to maximize floor space usage, making it ideal for tightly packed production lines or flexible plant layouts where space optimization is key. The lathe features a 30-degree slant bed, which not only provides a rigid and stable performance but also improves chip removal and enhances long-term machining stability. This ensures that the machine can maintain consistent, high-quality production even during extended operations.
One of the standout features of the FCL-130RP is its integration with a two-axis gantry robot, enabling fully automated part handling. This automation significantly reduces cycle times, with workpiece swapping occurring in just 5.5 seconds. The use of parallel-type grippers allows for simultaneous loading and unloading operations, further optimizing efficiency. The intuitive setup process requires only three input values, making it easy to handle diverse workpieces. Additionally, the integrated workpiece counter helps track job progress accurately, ensuring precise job management throughout the production process.
The FCL-130RP is capable of handling small to medium-sized components with specifications including a maximum cutting diameter of 9.29″ (236 mm) and a maximum cutting length of 9.17″ (233 mm). The lathe supports parts up to 3.15″ (80 mm) in diameter, 3.94″ (100 mm) in length, and 6.6 lbs (3 kg) in weight, offering great versatility for a wide range of applications. Whether for producing complex components or simple parts, the FCL-130RP can handle a variety of machining tasks, making it suitable for industries such as automotive, electronics, and medical device manufacturing.
To ensure smooth, precise cutting at high speeds, the lathe is equipped with roller-type linear guideways and high-precision 3.15″- (80-mm) diameter spindle bearings. These components allow the machine to operate smoothly and accurately, with minimal vibration even at high spindle speeds of up to 6,000 rpm. The spindle motor provides 5/7.4 hp (3.7/5.5 kW) power, supporting consistent performance during demanding operations.
The machine also boasts an intuitive graphical user interface for its robotic system, with controller options from FANUC and Mitsubishi. These controllers offer features such as 3D machining simulation and manual guide and ShopTurn options, making it easier for operators to set up and control the system. In addition to its standard equipment, which includes a 6″ hydraulic chuck, toolholders, soft and hard jaws, and a moveable coolant tank, the FCL-130RP also offers optional accessories to enhance workflow integration. These include an automatic door, toolsetter, parts catcher, and oil-mist collector, allowing for increased functionality and improved overall performance.
The FCL-130RP represents a significant advancement in automated turning solutions, offering manufacturers an efficient, high-speed, and space-saving CNC lathe that meets the demands of modern production environments. With its combination of precision engineering, automation capabilities, and versatile features, the FCL-130RP is poised to support the production of high-quality, small to medium-sized components with greater efficiency and reliability.
SW North America Open House Showcases Advanced Machining Solutions for Key Industries!
SW North America is set to host its highly anticipated 2025 Open House at its Michigan headquarters, located in New Hudson, on Friday, August 8, 2025. The event will provide attendees with a firsthand look at the latest in machining technology, showcasing cutting-edge solutions that support industries such as medical technology, automotive and electric vehicles (EVs), aerospace, agriculture, and construction.
As part of the open house, SW North America will feature live demonstrations of their advanced BA 322i and BA Space3 machining centers. These high-performance machines are specifically designed to meet the demanding precision and quality requirements of industries like medical and aerospace. The BA 322i twin-spindle CNC machining center will perform live machining of a tibia spacer, a critical component in total knee prosthetics. In addition, the BA Space3 will demonstrate its capabilities by machining a wing rib, a vital part for aircraft manufacturing. These demonstrations will highlight the machining centers’ versatility in size, speed, and stability, offering real-world examples of their effectiveness in high-precision applications.
The open house will also provide attendees with the opportunity to explore SW North America’s state-of-the-art 33,000-square-foot facility. Visitors can tour the facility, which showcases SW’s advanced machining and automation technologies. The company will also provide insights into its multispindle machining capabilities and its self-sufficient production cells, emphasizing the benefits of automation and precision manufacturing for various applications.
In addition to the live machining demonstrations and facility tours, attendees will have the chance to network with SW engineers, executives, and vendor partners. The event promises a relaxed and engaging atmosphere, with lunch, live entertainment, and a raffle to make the experience even more enjoyable. Special guests and speakers will also be announced closer to the event, further enriching the knowledge-sharing and networking opportunities.
Andrew Rowley, General Sales Manager at SW North America, emphasized that the event would not only showcase SW’s technical expertise in precision manufacturing but also offer an interactive and informative experience for all attendees. “Our open house is designed to provide a comprehensive look at how SW’s advanced machining solutions support industries that require the highest level of precision and efficiency,” said Rowley. “We look forward to connecting with industry professionals and showcasing our latest innovations in machining technology.”
SW North America is known for its commitment to compliance with ITAR (International Traffic in Arms Regulations), FFL (Federal Firearms License), and ISO standards. This ensures customers can rely on SW for high-precision, regulated work that meets the strictest industry requirements.
The open house is free to attend, and registration is open to anyone interested in smart manufacturing, automation, or advanced machining. Those interested in attending can request a pass by emailing contact.na@sw-machines.com or visiting the company’s website for more information.
This event is a must-attend for professionals interested in exploring the latest machining technologies and advancements in the fields of medical, aerospace, automotive, and other high-precision industries. It offers a unique opportunity to learn, connect, and witness the future of smart manufacturing and automation.
Bharat Forge Successfully Acquires AAM India Manufacturing to Strengthen Automotive Portfolio!
Bharat Forge Limited (BFL), a global leader in automotive manufacturing, has officially completed the acquisition of AAM India Manufacturing Private Limited (AAM India), marking a significant milestone in the company’s growth strategy within the automotive sector. This acquisition, announced initially on October 17, 2024, received regulatory approval from the Competition Commission of India (CCI) on April 22, 2025, clearing the way for Bharat Forge to consolidate its position as a key player in both traditional and emerging mobility technologies.
The acquisition is valued at Rs 7,464.6 million, which includes Rs 1,894.8 million in cash held by AAM India, available for future growth initiatives and expansion. The final equity value of the transaction is subject to adjustments based on the Net Working Capital as of June 30, 2025. This acquisition will help Bharat Forge tap into new technological advancements, diversify its product range, and enhance its capabilities to meet the evolving demands of the global automotive sector.
AAM India Manufacturing, a well-established name in the automotive sector, is known for producing advanced automotive components, serving both traditional internal combustion engine (ICE) vehicles and the rapidly emerging electric vehicle (EV) segment. The company has built a strong reputation for delivering high-quality products and solutions to a diverse set of Original Equipment Manufacturers (OEMs) both in India and internationally. AAM India’s specialization in precision manufacturing, along with its deep technical expertise, makes it a valuable addition to Bharat Forge’s expansive automotive portfolio.
With the automotive industry undergoing a major transformation driven by the shift towards electric mobility, the acquisition strengthens Bharat Forge’s ability to cater to both conventional automotive customers and emerging mobility technology players. The addition of AAM India’s manufacturing facilities and product portfolio enables Bharat Forge to diversify its operations and offer a wider array of products to OEMs involved in electric vehicles, autonomous driving technologies, and advanced powertrain systems. This acquisition not only enhances Bharat Forge’s position within the Indian automotive market but also provides a strategic foothold in international markets.
AAM India’s manufacturing capabilities span multiple product categories, including high-strength automotive components, precision-engineered parts, and specialized technologies that support the production of both ICE and electric vehicles. The company has focused its efforts on continuous innovation, sustainability, and meeting the evolving needs of the global automotive industry. Its expertise in manufacturing for hybrid and electric vehicle systems allows Bharat Forge to enhance its capabilities in the rapidly growing EV sector, which is expected to dominate the automotive market in the coming years.
Bharat Forge’s acquisition of AAM India is a key part of its long-term strategy to position itself as a diversified automotive and technology solutions provider. This acquisition not only strengthens Bharat Forge’s leadership in the automotive sector but also bolsters its product portfolio to meet the future needs of mobility solutions worldwide. As the automotive industry transitions towards alternative powertrains, electric vehicles, and autonomous systems, Bharat Forge is well-positioned to capitalize on these advancements through its expanded manufacturing and technological capabilities.
By incorporating AAM India’s technological expertise, Bharat Forge continues to pursue its vision of becoming a comprehensive provider of innovative solutions in the automotive space, with a commitment to sustainability and cutting-edge technology. The acquisition is expected to accelerate the company’s growth trajectory and its ability to deliver high-performance components to a broad range of global customers, strengthening its competitive edge in the fast-evolving automotive landscape.
Yueyang Paper Commissions ABB Systems to Enhance Production Capacity and Quality!
Yueyang Forest & Paper has successfully integrated a suite of ABB’s advanced drive and testing technologies as part of a significant paper mill upgrade at its facility in Yueyang, Hunan Province, China. This upgrade marks a key milestone in the company’s multi-phase investment project aimed at boosting production capacity while maintaining high-quality product standards.
The newly commissioned paper machine, with a paper width of 10,515 mm and an operational speed of 1,700 meters per minute, is designed to produce up to 450,000 tons of fine paper annually. This development follows a substantial investment of over $430 million in the first phase of the project.
To ensure optimal performance and quality, the facility is now equipped with ABB’s Paper Machine Drive systems and the L&W Autoline automated paper testing platform. The latter includes specialized laboratory equipment for testing various quality metrics, including felt moisture, air permeability, freeness, and fiber analysis. These tools are essential for producing fine and specialty papers, such as copy and offset printing paper.
The L&W Autoline system is integral to assessing critical quality indicators, including air permeance, roughness (Bendtsen), smoothness (Bekk), thickness, tensile stiffness orientation, formation, color and brightness (Elrepho), tensile strength, bending resistance, and grammage. ABB engineers collaborated closely with Yueyang Paper and the paper machine supplier during both the planning and commissioning phases, tailoring the solution to meet operational demands and site-specific requirements. The team’s focus was on achieving high reliability and control under high-speed production conditions.
Qin Jijin, Project Manager at Yueyang Paper, emphasized ABB’s contribution to the project’s success, stating, “ABB’s team demonstrated deep technical knowledge, attention to detail, and strong commitment throughout the project. Their support was crucial in overcoming key challenges during critical stages of implementation.”
Liu Yueming, the Local Business Line Manager for ABB’s Pulp and Paper division in China, also highlighted the success of the partnership, saying, “We’re proud to support Yueyang Paper in delivering a high-performance and stable solution. This project not only improves capacity and quality but also sets a benchmark for industrial growth and technological advancement in the region.”
The successful startup of the upgraded plant is expected to stimulate broader economic activity, benefiting industries such as logistics, printing, packaging, chemicals, machinery, forestry, and environmental services. This initiative also represents a significant leap in adopting new technologies, strengthening the paper manufacturing value chain, and advancing sustainability in the sector.
Yueyang Forest & Paper, originally founded as Yueyang Paper Mill in 1958, operates under the China Paper Investment Corporation, a subsidiary of China Chengtong Holdings Group. The partnership between Yueyang Paper and ABB began in 1998 and has since included multiple drive systems, electrical infrastructure for pulp production lines, and automation systems across various projects.
ABB, a global leader in electrification and automation solutions, continues to support industrial operations through advanced engineering, digital tools, and a strong focus on improving performance, efficiency, and sustainability. With over 110,000 employees worldwide, ABB remains committed to helping industries navigate the evolving landscape of modern manufacturing.
Do You Panic When You’re Machining Like This? 
That panic… you know the feeling.
You’re watching the machine, hands hovering near the feed hold button. Will the tool hold up? Is the path safe? Did I miss something in the program?
If you’re relying on blind trust, you’re not alone—but there’s a better way. With Virtual Machine from OPEN MIND, that uncertainty disappears.
A big thanks to Kalvin Clark
This clip shows what so many machinists and programmers face every day: What you can’t see, you don’t know. But when you use Virtual Machine, you do know.
Because what you’re seeing on screen…Is exactly what your machine is going to do in real life.
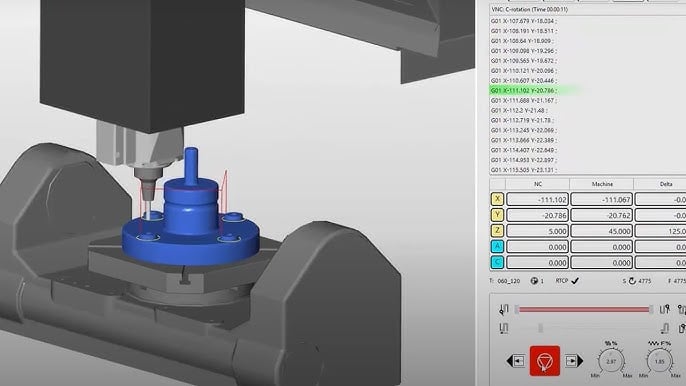
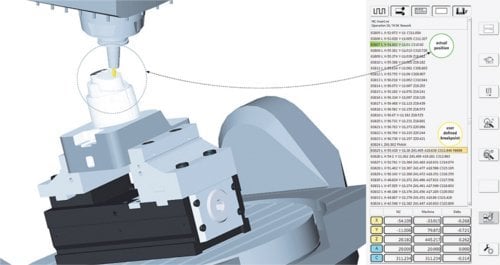
So, what is Virtual Machine?
Virtual Machine is part of the powerful hyperMILL® CAM software suite from OPEN MIND Technologies.
It’s not just a toolpath viewer or basic simulation.
It’s a true NC code-based simulation system—designed to show the exact behavior of your machine, using the actual G-code that will run on your controller.
With Virtual Machine, you get:
- A complete digital twin of your machine tool
- Real NC-code simulation—not approximations
- Full-axis movement visualization (3, 4, or 5-axis)
- Advanced collision detection across all machine components, tooling, and fixtures
- Verification of real-world machine logic and limits
- Cycle time estimation and program validation
Why it matters
When you’re running tight tolerances, complex geometries, and expensive setups, you can’t afford surprises.
Virtual Machine eliminates the guesswork by giving you complete visibility—before a single chip is made.
The result?
- Less downtime
- Fewer scrapped parts
- Safer operations
- Faster programming-to-production
- And most importantly—peace of mind
That panic? Gone.
With Virtual Machine, you go from “I think this will work…”
To “I know this will work.”
Mills CNC publishes its latest Summer 2025 edition of Insight.
Mills CNC, the exclusive distributor of DN Solutions’ and Zayer machine tools in the UK and Ireland, has just published its latest Summer 2025 edition of Insight – the company’s popular, biannually-produced customer magazine.
Available in digital format, and accessible to read from the company’s website (www.millscnc.co.uk), this Summer edition is packed with the latest news from Mills CNC.
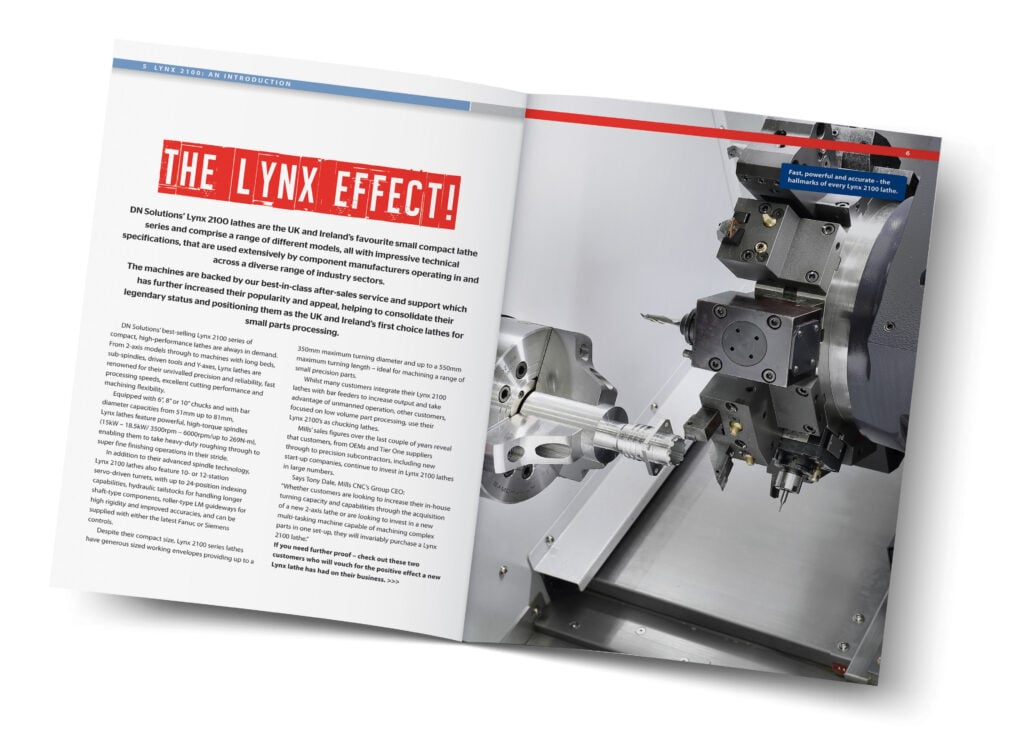
Since the last edition of Insight was published six months ago more hits (i.e., tariffs, tensions in the Middle Est etc.), to the stability and security of the global economy and to established international supply chains have occurred, threatening to dampen business confidence and make the future less predictable.
Covering these global uncertainties in his introduction to this edition of Insight, Tony Dale, Mills CNC’s Group CEO, acknowledges the realpolitik, but remains positive citing the recently-signed UK/US trade deal as being ‘good news’ for UK manufacturing – particularly for the aerospace and automotive sectors.
Indeed, the whole tenor of this edition of Insight is one of optimism and inspiration, and positions Mills CNC, through its advanced machine tools and automation systems, as being the natural and bright choice for UK and Irish component manufacturers everywhere, irrespective of their size or the scope and scale of their operations, looking to improve their productivity and increase their competitiveness.
Four recently completed customers case studies focusing on the motorsport, materials handling, oil and gas and architectural fabrication sectors are cases in point and have pride of place in the edition.
Continuing with the positivity, details of a new, eagerly-anticipated best-practice ‘one-hit’ machining technology event are provided in the Summer edition.
Titled ‘THE ONE SHOW’, this two-day machine tool technology fest (15th & 16th October) taking place at Mills’ Campus facility in Leamington will, through challenging machining demonstrations and in-depth technical seminars, appeal to component manufacturers looking to find out more about one-hit machining and how it can improve their productivity, performance and profitability.
Two multi-axis and multi-tasking DN Solutions’ machine tools (e.g., a recently-launched DVF 5000 Second-Generation 5-axis machining centre, and new DNX 2100SB mill-turn machine), will be the ‘stars of the show’ at the event.
In addition to customer case studies and events, the Summer edition also includes information on Mills’ revamped and relaunched ‘SMART Options’ machine tool rental scheme – a proven and popular route for component manufacturers to acquire additional machining capacity and capabilities, as well as a couple of features on two of Mills’ best-selling DN Solutions’ machine tool ranges – the Lynx 2100 compact lathe series and the new DNM 4500/5700 and 6700 (Fourth-Generation) range of 3-axis vertical machining centres.
Says Tony Dale:
“The latest edition of Insight is really all about looking forwards and how our advanced technologies can help component manufacturers maintain their competitive edge and achieve real and tangible growth.
“The launch our new DNX 2100 range of entry-level, multi-tasking mill-turn machines in October, and THE ONE SHOW Technology Event where a new DNX 2100SB will make its UK debut, are particular highlights occurring in the second half of the year.
“To make sure you don’t miss out on these and other developments, remember to visit our website and check out our social media channels.”
The latest edition of Insight can be accessed at https://www.millscnc.co.uk/mills-cnc-publishes-its-latest-summer-2025-edition-of-insight/
Sandvik Coromant Expands Next-Gen Silent Tools Turning Adaptors with New Sizes and Tailor Made Customisation
Sandvik Coromant, a global leader in cutting tools and tooling systems, has introduced an expanded range of its next-generation Silent Tools turning adaptors, enhancing vibration-damping performance for internal turning operations. The update adds new sizes and configurations, including adaptors with Coromant Capto and HSK-T couplings, alongside the launch of Tailor Made customisation options for greater process optimisation.
Åke Axner, Global Product Manager at Sandvik Coromant, said:
“These upgraded adaptors enable safer, faster, and more productive machining at long overhangs. Tailor Made customisation meets specific customer needs and helps optimise cutting processes for improved performance.”
Key features and benefits include:
- Expanded offering: 75 new Coromant Capto adaptors (32–100mm diameter) and 6 new HSK-T adaptors (32–60mm diameter) added to the portfolio, now totaling 187 tools across cylindrical, Coromant Capto, and HSK-T variants.
- Advanced vibration damping: The upgraded Silent Tools feature a sophisticated damper body precisely machine-assembled and calibrated for optimal frequency tuning, replacing the earlier manual adjustment process.
- Consistent, reliable performance: The enhanced damping mechanism ensures stable vibration control across various length-to-diameter ratios, boosting machining repeatability and reliability during long-overhang internal turning.
- Broader industrial applicability: Ideal for internal turning, parting, grooving, and threading in sectors such as aerospace, power generation, oil and gas, general engineering, and machine tool manufacturing.
- Cost and productivity gains: By reducing vibrations and minimizing interruptions, Silent Tools increase metal removal rates, improve surface finishes, enhance process security, and lower cost per part — contributing to higher profitability and competitiveness.
Sandvik Coromant’s Silent Tools continue nearly 50 years of leadership in vibration-damping technology, delivering cutting-edge solutions that address key machining challenges and support advanced manufacturing needs worldwide.
L&T Technology Services and thyssenkrupp Steering Forge Strategic Partnership to Launch Global Software Hub in Pune, India!
thyssenkrupp Steering, a global leader in steering technologies, and L&T Technology Services (LTTS), a prominent player in engineering and technology services, have entered into a strategic partnership to establish an advanced software development center in Pune, India. This collaboration marks a significant milestone for both companies, fueling innovation in automotive software solutions.
The new facility will leverage LTTS’ expertise in mobility, with a focus on developing safety-critical software for cutting-edge steering technologies. This strategic initiative also supports thyssenkrupp’s global expansion in automotive engineering, further solidifying LTTS’ reputation for delivering intelligent and sustainable mobility solutions. The software hub will be managed by LTTS, overseeing the development of next-generation automotive technologies, ranging from core vehicle engineering to advanced software systems.
LTTS has established itself as a leader in automotive engineering, with significant expertise in electrification, hybrid systems, and software-defined vehicle architectures. The company’s portfolio includes over 250 programs, 350 patents, and 45 labs globally. This partnership with thyssenkrupp Steering strengthens LTTS’ position as a trusted partner driving innovation in the mobility sector.
Richard Hirschmann, Senior Vice President of R&D at thyssenkrupp Steering, expressed his excitement about the collaboration: “Partnering with LTTS to expand our software development capabilities in India is an exciting step for thyssenkrupp Steering. This new center will play a crucial role in advancing steering solutions and delivering innovative technologies to our global customers.”
Patrick Vith, CEO of thyssenkrupp Steering, added, “Our goal is clear: to be the most trusted partner in steering solutions worldwide. This partnership with LTTS will help us lead the future of mobility with operational excellence, innovative solutions, and strong global collaborations.”
Amit Chadha, CEO and Managing Director of LTTS, shared, “This collaboration with thyssenkrupp Steering highlights our leadership in the mobility sector. Our expertise in electric and hybrid systems, combined with our experience in safety-critical software, ensures we can deliver innovative, sustainable mobility solutions to our customers.”
The Pune software hub will focus on developing embedded systems, functional safety, and cybersecurity—critical areas essential to the evolution of intelligent and connected vehicle technologies. With the increasing demand for autonomous driving and enhanced vehicle safety, this facility will play a pivotal role in shaping the future of automotive software.
Rajkumar Ravindranathan, Chief Business Officer – EMEA & RoW at LTTS, stated, “We’re thrilled to be part of thyssenkrupp’s transformation journey. Our collaboration will deliver rapid innovation, scalability, and faster time-to-market, strengthening thyssenkrupp’s competitive edge in the global market.”
This software hub will be crucial for advancing embedded system technologies, ensuring safety, and supporting the development of autonomous vehicles, contributing significantly to both companies’ leadership in the evolving automotive software landscape.
L&T Technology Services (LTTS) is a global leader in engineering and technology services, offering design, development, testing, and support services for a wide range of industries, including industrial products, medical devices, transportation, telecom, and high-tech. As a subsidiary of Larsen & Toubro (L&T), LTTS operates with over 24,000 employees across 23 global design centers and 108 innovation labs, making it a key player in digital transformation.
Weird and wonderful clamping! #kopal
Kopal, known for their innovative workholding and chamfering equipment, showcased a wide range of solutions at the recent exhibition in Lyon. In this video, Matt Jenness from MicroLoc, the UK distributor for Kopal, gives us an exclusive walkthrough of their stand and highlights the flexibility and practicality of the products on display. Whether you’re in need of clamping systems or precision chamfering tools, Kopal’s solutions are designed to boost efficiency across various machining setups. Filmed live at the Lyon Exhibition
Presented by: Matt Jenness, UK Distributor
Discover how these tools can transform your workholding processes
Remsons Partners with AUSUS Automotive Systems do Brasil LTDA to Transfer Technology and Empower Brazilian OEMs!
Remsons Industries Limited, a leading provider of advanced engineering solutions and automotive components, has entered into a Strategic Technical License Agreement with AUSUS Automotive Systems do Brasil LTDA, a prominent player in Brazil’s technology and manufacturing sector. This collaboration is set to bring innovative engineering technologies to Brazil, significantly enhancing the capabilities of local Original Equipment Manufacturers (OEMs) in the country.
The agreement will see Remsons India collaborate with AUSUS Brazil to transfer proprietary technologies aimed at improving the development and production of high-quality automotive products tailored for the Brazilian market. This partnership is a testament to Remsons’ commitment to technological advancement and its ongoing support for the growth of Brazil’s automotive and electronics industries.
The strategic collaboration between Remsons Industries and AUSUS Automotive Systems do Brasil LTDA will facilitate the transfer of advanced engineering and manufacturing technologies to Brazil. By doing so, it will enhance local production capabilities and enable AUSUS Brazil to leverage cutting-edge innovations, ultimately improving the efficiency and quality of automotive components produced in the region.
This technology transfer will empower Brazilian Original Equipment Manufacturers (OEMs) by giving them access to new solutions, which will help them enhance their product offerings. The initiative aims to elevate the competitiveness of local OEMs, allowing them to adopt new technologies that improve their manufacturing processes and product quality. This, in turn, will contribute to the overall growth and modernization of Brazil’s automotive sector.
Furthermore, this partnership strengthens international ties and promotes industrial growth within Brazil. The collaboration is poised to foster greater technological independence in the country, enhancing Brazil’s manufacturing capabilities. It is expected to drive the creation of new job opportunities, contributing to a more robust and self-reliant industrial ecosystem in Brazil.
Rahul Kejriwal, Executive Director of Remsons, expressed excitement about the partnership: “We are thrilled to partner with AUSUS Brazil to bring our technological expertise to the Brazilian market. This collaboration represents a key milestone in supporting local OEMs and enhancing the industrial ecosystem in Brazil.”
Remsons Industries Ltd is a globally recognized manufacturer of automotive OEM components, supplying to two, three, and four-wheeler vehicles, commercial vehicles, and off-highway vehicles worldwide. With over 50 years of experience, Remsons operates state-of-the-art manufacturing facilities in India, as well as in Stourport and Redditch in the UK. The company’s portfolio includes a wide range of high-quality automotive components, such as control cables, gear shifters, pedal boxes, winches, lighting systems, sensors, and more. Remsons has also been awarded the Great Place To Work® certification for four consecutive years, underscoring its commitment to employee satisfaction and workplace excellence.
Bridgestone India Strengthens Retail Presence with New Outlet in Nashik!
Bridgestone India, a prominent player in the tyre and mobility sector and part of the global Bridgestone Group, has further expanded its retail network by inaugurating a new Select Store, M/s Nashik Tyres, in Nashik. This move aligns with the company’s ongoing strategy to improve accessibility to quality tyre services across India.
The new outlet, strategically located in Nashik, was officially launched by Rajarshi Moitra of Bridgestone India. The store features advanced facilities and aims to become a one-stop destination for tyres and related services, catering to the growing demand for high-quality tyre solutions in the region.
As tyres play a crucial role in vehicle performance and road safety, Bridgestone continues to prioritize road safety and driver confidence through its expanding retail outlets. The Select Store model is specifically designed to assist customers in choosing the right tyres while offering a comprehensive service experience. The store aims to simplify and enhance the tyre purchasing process for modern-day drivers.
“We are committed to improving the tyre purchasing experience through our Select outlets,” said Mr. Moitra. “Expanding our network and enhancing our services helps us deliver quality products and reliable customer support.”
Bridgestone India has built an extensive network of over 900 Select Stores across the country. This broad network not only ensures product availability but also provides professional advice and dependable service to meet the needs of today’s drivers, who prioritize convenience and safety in vehicle maintenance.
Currently holding around 20% of the passenger car tyre aftermarket in India, Bridgestone India continues to focus on expanding its presence with well-equipped service centres nationwide. The addition of M/s Nashik Tyres and Services marks a significant step in bringing top-quality tyre solutions closer to Indian consumers while strengthening its retail footprint across the country.
Since its inception in 1996, Bridgestone India has played a key role in India’s tyre industry. The company began its manufacturing operations in Kheda, Madhya Pradesh, in 1998, and by 2013, it expanded its presence with a second plant in Chakan, Pune. In 2023, Bridgestone India achieved a major milestone with its Indore plant producing the company’s 100 millionth tyre. Today, Bridgestone India stands as a leading player in both the OEM and replacement tyre markets.
BEML Opens Aerospace SEZ Facility in Bengaluru; Begins Work on Expansion to Support Defence and Aviation Sectors
BEML Limited has officially opened a new warehousing facility at the Karnataka Industrial Areas Development Board (KIADB) Aerospace Special Economic Zone (SEZ) in Bengaluru. Covering an area of 0.12 acres, the facility was inaugurated by Shantanu Roy, Chairman and Managing Director of BEML, alongside company directors, senior staff, and officials from the Karnataka Industrial Areas Development Board (KIADB).
The facility is part of BEML’s strategy to scale up its aerospace operations, aligning with the growing needs of the aerospace and defence sectors. As a key step in its efforts, BEML also laid the foundation for Phase II of the project, which will involve developing an additional 1.15-acre area within the same SEZ. The company has secured a total of 25 acres within the zone and plans to gradually transform it into a manufacturing and logistics hub dedicated to the aerospace and defence industries.
At the event, Shantanu Roy highlighted the strategic importance of the new warehouse, stating that it marks a significant milestone in BEML’s efforts to support aerospace and defence production in India. He emphasized the facility’s role in enabling advanced manufacturing capabilities, maintenance and repair operations (MRO), and ensuring support for global export standards. The development aligns with the company’s broader vision to contribute to the growing domestic aerospace industry while positioning itself as a competitive player on the global stage.
The SEZ, strategically located near Kempegowda International Airport, will be a cornerstone of BEML’s broader vision to establish a dedicated aerospace production unit spanning 20 acres. This unit will focus on manufacturing aerostructures, drones, components, and systems for air defence. As part of the initiative, BEML plans to collaborate with leading international aerospace companies to build its production and supply chain capabilities.
To handle warehouse management and related services, BEML has entered into a partnership with LOM Logistics India Pvt. Ltd., a company with significant experience in SEZ and Domestic Tariff Area operations. In addition to serving BEML’s own needs, the facility will also provide services to other Original Equipment Manufacturers (OEMs), as well as Tier-1 and Tier-2 suppliers.
The SEZ’s strategic location near major highways, the Outer Ring Road, and the airport makes it an ideal hub for logistics and trade activities. BEML estimates that the project will generate over 500 jobs, significantly contributing to the local economy. Looking ahead, BEML plans to establish a Centre of Excellence for Aerospace Technologies at the site, fostering local innovation and enhancing India’s competitive position in the global aerospace and defence sectors.
Godrej Enterprises Group (GEG) Accelerates India’s Shift to Smart, Sustainable Logistics!
As India aims to strengthen its position as a global manufacturing and logistics hub, Godrej Enterprises Group (GEG) is playing a pivotal role in the evolution of the logistics sector with its innovative solutions in intralogistics. Through its Material Handling Equipment (MHE) and Storage Solutions divisions, GEG is revolutionizing warehouse and factory operations by integrating cutting-edge technologies such as IoT, automation, and AI, thereby setting new standards for efficiency and sustainability in the industry.
GEG has firmly established itself as a market leader in the intralogistics sector, holding a significant 20–25% market share in Storage Solutions and Material Handling over the past three years. The company has made substantial investments in research and development (R&D) and innovation, with a strong focus on making manufacturing processes more sustainable. This commitment is not only reflected in their products but also in their dedication to sourcing approximately 85% of their intralogistics procurement domestically, reinforcing their commitment to India’s ‘Atmanirbhar Bharat’ initiative and sustainability throughout the supply chain.
Through its focus on indigenous product development, safety innovations, and sustainable technologies, GEG is reshaping the logistics ecosystem. Their work goes beyond merely modernizing factory floors and warehouses; they are building systems that are agile, efficient, and designed for the future. As Vikas Choudaha, Business Head of Storage Solutions at GEG, stated, “We’re helping 3PLs, quick-commerce businesses, and large manufacturers create warehouse ecosystems that reduce costs and improve delivery times. Today, every third delivery you receive at home is touched by Godrej.”
In a similar vein, Anil Lingayat, Business Head of Material Handling Equipment, emphasized the importance of efficient warehouse operations in streamlining logistics. He added, “Every second saved boosts the entire supply chain. Our sustainable, digital-first solutions—from electric forklifts to automated racking platforms—are enhancing efficiencies across the ecosystem.” GEG’s upcoming launch of IoT-enabled forklifts in July, along with its focus on expanding R&D and manufacturing capabilities, underscores its efforts to meet the growing demand for smart, high-performance logistics infrastructure.
GEG’s intralogistics division is providing scalable, tech-driven, and sustainable solutions that are empowering high-growth sectors like e-commerce, FMCG, cold chain logistics, retail, and quick commerce. The company’s offerings are in alignment with the National Logistics Policy, which aims to drive green logistics, cost efficiency, and digital integration across India’s logistics operations.
On the sustainability front, GEG’s Storage Solutions facility in Chennai is a leader in green manufacturing, achieving impressive milestones such as 3x water positivity, a 30% reduction in carbon emissions, and a commitment to zero waste to landfill. The facility’s use of real-time monitoring for energy and water consumption helps ensure operational efficiency at every level.
Furthering its commitment to sustainable operations, the MHE division at GEG’s Vikhroli plant in Mumbai has focused on improving energy productivity, reducing its carbon footprint, and increasing the use of renewable energy and water conservation. As a pioneer in electric forklifts in India, the MHE division recently launched the country’s first lithium-ion battery-powered forklift. This forklift features an indigenously developed Battery Management System (BMS) designed to enhance performance, safety, and battery life under demanding Indian conditions. With over 82% of its forklift portfolio now electric, the MHE division continues to drive the shift toward smarter and greener logistics.
Through these efforts, GEG is leading the way in transforming India’s logistics sector, promoting sustainability, innovation, and efficiency, and positioning itself as a key player in the future of smart, sustainable manufacturing and logistics in India.
Ganesh Mani Appointed CEO of Switch India, Following S Mahesh Babu’s Departure!
S Mahesh Babu, the CEO of Switch Automotive Mobility Ltd (Switch India), has announced that he will step down from his role, effective August 31, 2025. Babu will be exploring new opportunities outside of the group. In response, Ganesh Mani, the current Chief Operating Officer (COO) of Ashok Leyland, will take over as the CEO of Switch India starting September 1, 2025.
This leadership transition aligns with Switch India’s strategy to leverage Ashok Leyland’s operational strengths to optimize costs while maintaining its focus on the development of cutting-edge battery-electric buses and light commercial vehicles. Dheeraj G Hinduja, the Chairman of Switch Mobility, expressed gratitude for Mahesh Babu’s significant contributions, stating, “We thank Mr. Mahesh for his impact during his tenure with us. With EBITDA breakeven achieved in FY25, Switch India is now positioned to scale its business and move towards positive profit after tax (PAT) in the near future.” Hinduja also noted that Ganesh Mani’s expertise in operational excellence and large-scale transformations will guide the company towards its next phase of profitable growth.
Under the leadership of Mahesh Babu, Switch India has built a competitive portfolio of electric commercial vehicles. The company’s offerings in the light commercial vehicle category include the 1.25-tonne IeV3 and the 1.75-tonne IeV4, which are available for commercial purchase through select Ashok Leyland LCV dealers. In the electric city bus segment, Switch India provides 12-meter buses in standard and low-floor versions, offering a range of up to 200 kilometers on a single charge. With a robust order book of over 1,500 buses, Switch India is aiming to double its revenue in FY26, further solidifying its position in the growing electric vehicle market.
Switch Mobility, a part of the Hinduja Group, continues to advance the electric vehicle sector with a focus on zero-emission commercial mobility. The company was established from a collaboration between Ashok Leyland and the British bus manufacturer Optare. Switch’s product range includes the SWITCH EiV series of electric buses, which features India’s first electric double-decker, the SWITCH EiV22, as well as the SWITCH IeV series of light commercial vehicles designed for last-mile logistics. With over 1,000 electric buses and 1,000 electric light commercial vehicles (e-LCVs) on the road, Switch vehicles have collectively covered over 150 million green kilometers, contributing to a reduction of over 100,000 tons of CO₂ emissions.
The company is experiencing strong demand for its electric vehicles, with an order book exceeding 1,800 electric buses. Switch’s in-house telematics platform, SWITCH iON, plays a crucial role in the company’s operational success. The platform provides real-time fleet monitoring, performance optimization, and proactive maintenance, backed by a 24/7 Command Centre that processes over 2 TB of data daily. This enables the generation of more than 90,000 alerts to ensure safety and operational efficiency across the fleet.
Accenture and IIT Madras Collaborate to Train Talent for Software-Defined Vehicles!
Accenture and the Centre of Excellence in Advanced Automotive Research (CAAR) at IIT Madras have partnered to offer specialized skill development programs for Software-Defined Vehicles (SDVs) through Accenture’s LearnVantage SDV Academy. This collaboration aims to address the growing demand for skilled talent in the rapidly evolving SDV sector, enabling automotive Original Equipment Manufacturers (OEMs) and Global Capability Centers (GCCs) to advance in this space. As the automotive industry increasingly embraces digital integration, this initiative will help close the skills gap and equip professionals with expertise in automated driving technology, advanced driver assistance systems (ADAS), electrical and electronic architecture, connectivity, and infotainment systems.
The curriculum offered by the program is tailored specifically for professionals in the automotive technology sector. It includes domain-specific modules and hands-on learning opportunities, delivered through a combination of self-paced and instructor-led sessions by IIT Madras faculty. The topics covered in the program include advanced IoT, embedded systems, vehicle safety, communication protocols, cybersecurity, edge computing, cloud virtualization, and industry standards like AUTOSAR and ASPICE, ensuring that participants are well-prepared for the complexities of SDVs.
According to Accenture’s research, the market for software-defined digital services in the automotive industry is expected to reach $3.5 trillion by 2040, accounting for 40% of global automotive revenues. In response to this shift, the Accenture LearnVantage SDV Academy aims to provide the targeted training necessary to help the industry meet these challenges. Kishore Durg, the global lead of Accenture LearnVantage, highlighted that as vehicles become increasingly reliant on software, there is a critical need for talent proficient in AI, machine learning, cybersecurity, and safety systems. The partnership with CAAR at IIT Madras represents a significant step in addressing this talent gap, enabling large-scale upskilling and reskilling across OEMs and GCCs.
Professor Krishnan Balasubramanian, the Professor-in-Charge of CAAR at IIT Madras, emphasized the importance of collaborations between academia and industry in creating a skilled workforce for the SDV sector. He stated, “This partnership with Accenture LearnVantage is a win-win for everyone involved, particularly as we focus on upskilling the workforce in emerging fields like SDVs.” Thiruppathy Srinivasan, CEO of CAAR at IIT Madras, echoed this sentiment, noting that the automotive industry’s transition toward electrification, connectivity, and advanced technologies has created an urgent need for digital skills. He highlighted that this collaboration will play a crucial role in bridging the talent gap and preparing professionals for the changing landscape of the industry.
Accenture and IIT Madras also have an ongoing partnership through their joint Centre of Excellence (CoE), which focuses on research and development in autonomous robotics systems, Industrial Internet of Things (IIoT), digital twins, and other advanced automotive technologies. This collaboration aims to bring together the strengths of both organizations to drive innovation and provide valuable expertise in cutting-edge areas. Additionally, TalentSprint, part of Accenture LearnVantage, offers an advanced postgraduate certification in Data Science and Machine Learning in collaboration with IIT Madras, further enhancing the education and training opportunities available to professionals in the automotive sector.
Accenture, a global leader in professional services, is dedicated to helping businesses, governments, and organizations build their digital capabilities and accelerate growth. With a workforce of over 791,000 employees serving clients in more than 120 countries, Accenture is at the forefront of technological transformation, specializing in cloud, AI, and data solutions. The company’s diverse portfolio also includes services in Strategy & Consulting, Technology, Operations, Industry X, and Song.
The Centre of Excellence in Advanced Automotive Research (CAAR) at IIT Madras plays a key role in fostering technological innovation in the automotive sector. With its focus on developing emerging technologies, providing consulting services, and offering specialized training programs, CAAR is helping to build the skilled workforce needed to drive the future of automotive technology, including software-defined vehicles.
SKF India to Invest ₹5,000 Crore in Major Expansion to Meet Growing Automotive Demands!
SKF India, the local subsidiary of the Swedish industrial giant SKF Group, has announced an ambitious expansion plan with an investment ranging from ₹4,600 crore to ₹5,000 crore between 2025 and 2030. This strategic move aims to enhance production capacities at SKF India’s three key manufacturing plants located in Haridwar, Pune, and Bangalore. The expansion will help SKF India address the growing demands of India’s automotive industry, particularly as the market shifts towards electric vehicles (EVs) and more environmentally sustainable mobility solutions.
The Haridwar facility will see a significant 50% increase in production capacity. This plant will focus on manufacturing bearings for two-wheelers and EV powertrains. As the demand for electric vehicles rises, this facility’s upgrades will help meet the growing need for high-quality components. The investment allocated for this expansion is estimated to be between ₹1,000 million and ₹1,500 million, with the upgrades expected to be completed by 2029.
In Pune, the expansion will result in a 30% increase in capacity. This facility will focus on producing unitized wheel end bearings for both passenger and commercial vehicles, covering both ICE and EV platforms. The investment for Pune’s expansion is projected to be between ₹3,000 million and ₹3,500 million, and the expansion is expected to be finished by 2030. These upgrades will ensure that SKF India is well-positioned to cater to the evolving automotive sector’s needs.
The Bangalore facility will receive a 10% boost in its production capacity, primarily focused on bearings for two-wheelers and EV powertrains. With an estimated ₹100 million investment, the Bangalore facility upgrades are expected to be completed by 2026. These improvements will further support the company’s role in India’s automotive growth, especially in the electric vehicle segment.
This investment plan underscores SKF India’s commitment to supporting the transformation of India’s automotive sector, particularly the shift to electric mobility. As the Indian automotive industry evolves, SKF India is positioning itself to meet the demands of both traditional internal combustion engine (ICE) vehicles and the rapidly growing EV market. The upgraded facilities will produce a wide range of essential automotive components, including Deep Groove Ball Bearings (DGBB), Cylindrical Roller Bearings (CRB), Hub Bearing Units (HBU), and Tapered Roller Bearings (TRB), all of which are critical for the performance and efficiency of vehicles.
The expansion plan will enable SKF India to play a pivotal role in India’s growing automotive sector while contributing to the country’s electric mobility goals. The Indian government’s push for electric vehicle adoption, supported by various incentives and policies, aligns with SKF India’s investment in modernizing and expanding its manufacturing capabilities. This growth will help meet the rising demand for automotive components and ensure that the company can deliver high-quality products to support India’s transition to cleaner, more sustainable mobility.
SKF India’s investment also highlights its confidence in India’s manufacturing potential and the country’s strategic importance as a hub for automotive components. By expanding production capabilities at key facilities, SKF India is ensuring that it remains a competitive player in both the domestic and global automotive markets. The investment not only demonstrates SKF’s commitment to India’s growth but also supports the nation’s broader goals of reducing its carbon footprint and accelerating the adoption of electric vehicles.
With this ₹5,000 crore investment, SKF India is poised to strengthen its position as a key supplier of critical automotive components and support the country’s transition to a more sustainable future. The expansion will enhance the company’s ability to meet the evolving needs of the automotive sector, contributing to both the growth of India’s automotive industry and the global shift towards cleaner, more efficient transportation solutions.
LAPP India Expands Cable Gland Portfolio with SKINTOP® Range for Versatile Industrial Applications!
LAPP India, a leading provider of cable and connectivity solutions, has significantly expanded its industrial cable management offerings with the introduction of the SKINTOP® range of cable glands. This versatile line is designed to meet the diverse needs of industrial environments, ranging from critical operations to general-use applications. The SKINTOP® series is available in two distinct product groups—SKINTOP® ST / STR and SKINTOP® SMART—offering high-performance, durability, and ease of installation for a wide array of industries.
The SKINTOP® range includes polyamide glands engineered to address the growing demands for safety, reliability, and operational efficiency in today’s fast-paced industrial environments. Whether it’s for heavy-duty or standard applications, LAPP ensures that the SKINTOP® glands offer reliable solutions to meet the most stringent industry requirements. Through this new offering, LAPP continues its tradition of providing tailored solutions that align with application needs, environmental conditions, and compliance standards, ensuring a robust cable management system.
The SKINTOP® ST and STR series are ideal for high-demand industrial environments. Designed with globally certified standards, these glands are perfect for use in sectors where strict performance and safety standards are necessary, such as cleanrooms, energy networks, automation systems, food and beverage production, pharmaceuticals, oil and gas, and data centers. The glands are built to withstand harsh conditions, including high levels of UV exposure, ozone, and aggressive chemicals, offering robust protection and operational continuity.
Crafted from durable polyamide, the SKINTOP® ST and STR glands are available in both metric-threaded and PG-threaded versions, providing compatibility across a wide range of cable diameters, from M12 to M63 and PG 7 to PG 48. They are designed with superior ingress protection ratings of IP68 (up to 5 bar for 30 minutes) and IP69 (resistant to high-pressure, high-temperature water jets), ensuring their suitability for environments exposed to water, dust, and contaminants. Furthermore, the glands feature flame resistance up to 650°C, making them ideal for high-temperature environments.
The glands’ ability to resist severe environmental factors, such as exposure to chemicals and UV radiation, enhances their appeal in industries requiring long-term reliability. Certified by international standards such as CE, UL, DNV, VDE, and UKCA, the SKINTOP® ST and STR series meet global requirements, making them a reliable choice for multinational operations.
On the other hand, the SKINTOP® SMART series, manufactured at LAPP’s state-of-the-art facility in Dharuhera, is designed specifically for general-purpose industrial applications. This range is well-suited for use in applications such as control panels, junction boxes, limit switches, parking systems, and surveillance setups. The SMART series features ingress protection up to IP68 and carries the UR (UL Recognized) certification, making it ideal for routine industrial environments.
One of the key advantages of the SKINTOP® SMART glands is their compact design, which allows for quick and efficient assembly in both compact and standard installations. With clamping sizes ranging from M12 to M32 and PG 7 to PG 29, these glands offer excellent flexibility. The user-friendly design features precision-engineered sealing rings, gaskets, and locking components that guarantee strong cable fixation and reliable sealing, ensuring optimal protection for cables and connections.
The SKINTOP® SMART series is particularly valued for its rapid availability, making it a practical solution for businesses that need efficiency without compromising performance. The glands’ ease of installation is one of their standout features. The simple turn of the nut enables quick assembly, eliminating the need for additional tools and reducing setup time, which is especially beneficial in high-speed industrial environments where time is critical.
The SKINTOP® cable glands are designed with several features that enhance their usability and longevity. One of the most important features is their hermetic sealing, which provides maximum protection for electrical connections. The ingress protection ratings of IP68 and IP69 ensure that the glands effectively shield against dust, water, and other environmental contaminants, crucial in industries like food processing, pharmaceuticals, and marine applications.
Furthermore, the glands provide optimized strain relief, which reduces the risk of vibration-related damage to cables, preventing mechanical failure and extending the lifespan of cables. Their low-maintenance design and robust construction ensure a long operational life, even in challenging environments, minimizing downtime and improving efficiency in various industries.
The SKINTOP® glands are available in a range of materials, including plastic, brass, and stainless steel, offering solutions for a wide variety of industrial applications. These materials ensure resistance to extreme temperatures, UV exposure, ozone, and aggressive chemicals, making them perfect for industries like oil and gas, food and beverage, pharmaceuticals, and marine applications.
LAPP India’s introduction of the SKINTOP® range reinforces its commitment to providing high-quality, versatile solutions to meet the diverse needs of industries globally. The combination of advanced design, high-quality materials, and ease of installation makes SKINTOP® the ideal choice for companies seeking reliable and efficient cable management solutions.
LAPP India’s SKINTOP® range provides industries with innovative, reliable, and flexible cable gland solutions that address the increasing need for high-performance, safety, and ease of installation in various industrial sectors. From high-demand applications in harsh environments to more general industrial uses, the SKINTOP® series ensures that companies have access to top-tier cable management solutions that improve operational efficiency and safety. With the expanding demand for cable glands across different sectors, LAPP India continues to lead the way in providing durable, effective, and easy-to-install products that meet global standards and performance requirements.
LAPP India is a wholly-owned subsidiary of LAPP, a global leader in cable and connectivity technology, and continues to contribute to India’s growth through its innovative solutions, helping industries maintain safe, efficient, and sustainable operations.
Servotech EV Infra Partners with NPCL to Expand Electric Vehicle Charging Network in Greater Noida!
In a significant move to strengthen India’s electric vehicle (EV) infrastructure, Servotech Power Systems’ EV arm, Incharz (Servotech EV Infra), has entered into a strategic partnership with Noida Power Company Limited (NPCL). This collaboration is aimed at expanding the EV charging network in Greater Noida, a vital area that is seeing increased demand for cleaner mobility solutions.
The partnership, formalized through a Memorandum of Understanding (MoU), was signed by Sanket Srivastava, Head of PMS & Sustainability at NPCL, and Prem Prakash, CEO of Incharz. The collaboration is part of India’s larger goal to improve accessibility to EV charging stations and accelerate the adoption of electric vehicles, aligning with the nation’s clean mobility objectives.
Under this agreement, both organizations will jointly identify and develop strategically placed EV charging stations across Greater Noida, focusing on high-traffic areas such as corporate offices, residential complexes, commercial centers, and hospitals. NPCL will leverage its knowledge to recommend ideal locations and coordinate with electricity distribution companies, ensuring efficient setup processes and minimizing costs and setup time.
As a part of the first phase of the project, the partnership has already installed EV chargers in two prominent residential complexes in Greater Noida. At Stellar Jeevan, the installation includes 7.4 kW and 10 kW AC chargers. Meanwhile, Ace Divino benefits from a more powerful setup, featuring a 40 kW DC charger and a 10 kW AC charger, capable of simultaneously charging three two-wheelers, showcasing the potential of scalable and efficient charging solutions.
Prem Prakash, CEO of Incharz, expressed his enthusiasm for the partnership, stating, “This collaboration with NPCL marks a major milestone in our mission to develop a smart, scalable EV charging network across India. It aligns with our broader goal of promoting solar energy and contributing to cleaner urban environments. By accelerating infrastructure growth and providing convenient access to charging stations, we are making electric vehicles a more feasible option for Indian consumers.”
He further added, “Our ambition extends beyond carbon neutrality—we want to contribute to India’s goal of becoming a carbon-negative country, and this partnership is a key step toward realizing that vision.”
Sanket Srivastava from NPCL echoed similar sentiments, highlighting the importance of the partnership in advancing clean mobility. “We are thrilled to work with Servotech EV Infra to strengthen the EV charging ecosystem in Greater Noida. As part of our continued efforts to push for green energy solutions, this collaboration will be instrumental in making EV charging stations more accessible, reliable, and widespread, paving the way for the broader adoption of electric vehicles.”
The collaboration between Servotech EV Infra and NPCL is a promising development in India’s pursuit of a sustainable, low-emission transportation system. By making EV charging infrastructure more accessible, this partnership is helping to meet the rising demand for electric vehicles while simultaneously driving the nation’s green energy goals. The initiative is expected to accelerate the transition towards clean energy mobility in Greater Noida, contributing significantly to the country’s climate and sustainability objectives.
Ceratizit MaxiMill – S-Power: Tackling Cast Iron Machining Challenges with Precision and Stability
Machining cast iron often presents hurdles such as heavy tool wear, burr formation, and breakouts along workpiece edges—factors that can slow production and reduce efficiency. Ceratizit’s MaxiMill – S-Power milling cutters are engineered specifically to overcome these challenges, delivering stable, high-performance milling with reduced vibration and superior surface finish.
Featuring a high tooth count and double-sided indexable inserts, the MaxiMill – S-Power system combines efficiency with durability. Its innovative double wedge clamp design ensures quick, secure attachment of inserts, simplifying tool changes while maintaining precision.
Robert Frei, Technical Product Manager at Ceratizit, highlights:
“With the MaxiMill – S-Power, manufacturers can achieve higher feed rates thanks to the optimal 12 cutting edges on a 63mm diameter tool and positive cutting edge design. This not only enhances surface quality but also significantly reduces burr formation—benefitting industries machining braking systems or high-performance motor mounting surfaces.”
Key features include:
- High tooth count with 12 teeth (Ø63mm) enabled by an 88° setting angle, maximizing cutting edges while maintaining small chip spaces for smooth chip evacuation.
- Double-sided indexable inserts provide 8 cutting edges per insert, crafted from carefully selected substrates with advanced Dragonskin coatings for long tool life and smooth cutting.
- Robust construction: a sturdy insert seat and double wedge clamp with anti-twist protection provide secure clamping and excellent axial and radial run-out accuracy.
- Ease of maintenance: a single screw fastens each double wedge, allowing fast, accurate insert replacement. Separate clamping wedges for each holder diameter optimize clamping force.
Available in diameters from Ø56 to Ø125, the MaxiMill – S-Power is specially suited for cast iron grades GJS, GJV, and GJL. With a recommended maximum depth of cut around 8mm and feed rates between 0.08 and 0.15mm, it balances minimal breakout risk with high productivity.
The indexable inserts cover ISO P/K applications with cutting edge geometry M and come in corner radii of 0.4, 0.8, and 1.2mm. Substrate grades offered include CTPK220, CTCP230, and ceramic, allowing users to tailor performance to their specific machining requirements.
Ceratizit’s New WTX-UNI Drill Range: Precision, Flexibility, and Sustainability Combined
Sheffield-based Ceratizit UK and Ireland Ltd has launched the WTX-UNI range of solid carbide drills, designed to bring reliable, precision drilling across steel, stainless steel, and cast iron while delivering outstanding cutting performance and impressive tool life. These cost-effective drills stand out not only for their flexibility and long life but also for their sustainable construction, offering manufacturers a highly efficient solution for machining multiple materials with fewer tool changes.
In today’s manufacturing environment, companies face the challenge of machining a diverse range of materials quickly and accurately. Frequent tool swaps and the need for specialised drills often drive up costs and reduce productivity. Ceratizit’s WTX-UNI range addresses this with a completely new geometry featuring patented innovations, enabling precision drilling across steel, stainless steel, cast iron, and even hardened steels up to 54 HRC — all with a single drill family.
“Thanks to its versatility and performance, the WTX-UNI range reduces the number of tools needed and increases machining efficiency,” explains Manuel Keller, Technical Product Manager at Ceratizit. “This lowers costs and boosts productivity.”
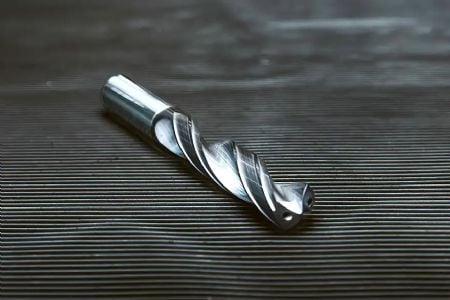
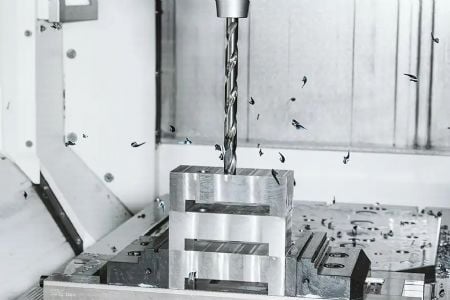
Made from Ceratizit’s most sustainable carbide grade to date — CT-GS20Y — the drills offer longer tool life and better cutting data than previous generations, marking a significant step forward in both performance and environmental impact.
The WTX-UNI drills come in diameters from 3 to 20mm, with hole depths of 3xD and 5xD, available with or without through-coolant and in several shank variants. Their patented convex main cutting edge and a 140° point angle deliver excellent self-centring and stability, while an expanding flute design ensures efficient chip evacuation, reducing risks of jams and breakage.
For deeper holes, Ceratizit offers the WTX-Quattro version with four guide lands and built-in coolant holes. These drills cover hole depths from 5xD up to 12xD, and feature a slightly modified 135° point angle on deeper versions to maintain stability and accuracy. This variety ensures that even specialised drilling tasks can be tackled with precision.
The WTX-Deep UNI line expands the capabilities further, focusing on maximum process reliability for deep hole drilling up to 50xD. Its polished chip spaces, four guide lands, and innovative DPX74-M coating increase chip flow, reduce hole deviation, and extend tool life—perfect for machining steel, stainless steel, cast iron, and heat-resistant alloys.
Importantly, the WTX-UNI drills are designed with sustainability in mind. Made from the upGRADE CT-GS20Y substrate, they offer not only excellent performance but also reduced environmental impact, complete with a Product Carbon Footprint (PCF). Plus, these drills can be reground and recoated, extending their usable life and reducing waste.
“Our new WTX-UNI range updates our portfolio with a truly universal machining solution,” adds Keller. “Alongside these, our extensive range includes everything from micro drills and high-feed drills to specialist tools for aluminium and nickel alloys, ensuring we can meet nearly any machining challenge.”
For manufacturers looking to improve efficiency, cut costs, and operate more sustainably, Ceratizit’s WTX-UNI drills offer a versatile and powerful tool for today’s diverse machining demands.
France Signs Framework Agreement for VSR700 Naval UAS Programme
In a major step forward for European naval aviation, Sébastien Lecornu, French Minister for the Armed Forces, has signed a framework agreement with Bruno Even, CEO of Airbus Helicopters, and Marie-Laure Bourgeois, Executive Vice President of Sales and Marketing at Naval Group, for the future acquisition of the Systèmes de Drone Aérien pour la Marine (SDAM) – uncrewed aerial systems (UAS) designed specifically for the French Navy.
The agreement also opens the door to future international collaboration through government-to-government arrangements, with other nations invited to participate in the programme via the French Armament General Directorate (DGA).
Each SDAM system will feature the Airbus VSR700 UAS, operated using Naval Group’s Steeris Mission System (MS). Naval Group will oversee the full integration of the SDAM onto French Navy frigates. Developed over 15 years, the Steeris MS is a sea-proven combat system interface designed specifically for integration into naval platforms, enhancing situational awareness and operational capability.
“This framework agreement is a key milestone for the VSR700 programme,” said Bruno Even, CEO of Airbus Helicopters.
“With our partners, we have already demonstrated the VSR700’s capabilities at sea, including successful deployment from a French Navy frigate. This programme is also helping build a sovereign and scalable UAS ecosystem that will serve both domestic and international partners. The VSR700’s versatility is clear—from naval ISR missions to armed scout configurations, as we showcased recently at the Paris Air Show.”
Pierre Eric Pommellet, Chairman and CEO of Naval Group, highlighted the broader strategic importance:
“This signature reflects the close cooperation with our partners and Naval Group’s deep expertise in integrating uncrewed systems aboard surface ships. SDAM will significantly boost the operational capabilities of the French Navy and, potentially, those of our partner navies around the world.”
The serial production VSR700s destined for the French Navy will be equipped for intelligence, surveillance, and reconnaissance (ISR) missions. This includes integration of a radar, electro-optical system, and an Automatic Identification System (AIS) receiver. Designed to operate in challenging maritime environments, the VSR700 can autonomously take off and land on ships in rough seas, operate in dense electromagnetic conditions, and support missions exceeding eight hours of endurance—all while carrying up to three onboard sensors.
As the programme moves forward, it represents not only a significant enhancement to French naval capability, but also a clear opportunity for allied nations to adopt a common, interoperable UAS solution tailored to modern maritime defence requirements.
New Janet Harvey Hall Opens in Glasgow, Ushering in a New Era for Clyde Shipbuilding
A major milestone in the future of UK naval shipbuilding has been reached with the opening of the Janet Harvey Hall, a cutting-edge ship build facility at BAE Systems’ shipyard in Govan, Glasgow. Named in honour of Janet Harvey, one of the many women who took on vital industrial roles during World War II, the hall represents both a tribute to the past and a significant investment in the future.
The opening ceremony celebrated this legacy, culminating in a ribbon-cutting led by Janet Harvey’s nieces alongside the Lord Provost of Glasgow. Their symbolic gesture officially launched the state-of-the-art facility, which is set to transform the way warships are constructed on the Clyde.
Measuring 170 metres long and 80 metres wide, the Janet Harvey Hall features two 100-tonne cranes and two 20-tonne cranes, and is large enough to accommodate the simultaneous construction of two Type 26 frigates. It marks the first time warships will be built entirely undercover in Glasgow, providing consistent working conditions year-round and helping to improve build schedules and quality.
Currently, the hall houses the construction of HMS Belfast and HMS Birmingham, while HMS Glasgow and HMS Cardiff are undergoing outfitting at BAE Systems’ Scotstoun site further up the River Clyde. Meanwhile, steel has recently been cut for HMS Sheffield, continuing the momentum behind the Royal Navy’s eight-ship Type 26 programme.
“This facility marks a major step forward for shipbuilding in Glasgow,” said Simon Lister, Managing Director of BAE Systems’ Naval Ships business.
“The Janet Harvey Hall will enable efficient and safe shipbuilding for decades to come. It is a symbol of pride not just for our skilled workforce who bring these ships to life, but for the entire city.”
The hall is designed to accommodate up to 500 workers per shift and is a central component of BAE Systems’ £300 million investment in the digitalisation and modernisation of its Glasgow shipyards. The goal is to support more efficient ship assembly and delivery, reduce delays, and meet the evolving requirements of the Royal Navy.
Stephen Charlick, Type 26 Resident Project Officer at MoD DE&S, added:
“The Janet Harvey Hall brings an improved approach to warship assembly and outfit, driving quality throughout the build. This supports timely delivery of the Type 26 frigates, ensuring the Royal Navy receives the cutting-edge capability it needs to meet global threats.”
As a symbol of technological advancement and industrial heritage, the Janet Harvey Hall signals a bold future for naval manufacturing on the Clyde—reaffirming Glasgow’s historic place at the heart of British shipbuilding.
Eurofighter Typhoon Gets Boost as Italy Orders 54 New EJ200 Engines
A new chapter in European defence aviation has been opened with Eurojet Turbo GmbH signing a major contract with the NATO Eurofighter and Tornado Management Agency (NETMA). The agreement will see up to 54 new EJ200 engines delivered to the Italian Air Force, supporting the nation’s Eurofighter Typhoon fleet as part of a Tranche I replacement programme.
The contract represents a resurgence in interest across Europe in the Eurofighter programme, following the Spanish Halcón II order announced late last year. It underlines both the operational relevance of the Typhoon platform and the continued strategic importance of the EJ200 engine at its heart.
Production of the EJ200 will once again be a collaborative effort between Eurojet’s four partner companies: Rolls-Royce (UK), MTU Aero Engines (Germany), ITP Aero (Spain), and Avio Aero (Italy). Final assembly for the Italian engines will be carried out by Avio Aero, reinforcing Italy’s direct industrial role in the programme.
Ralf Breiling, CEO of Eurojet, welcomed the announcement:
“This agreement, coming so soon after the Spanish Halcón II acquisition, underscores the strong, ongoing trust from the nations in the EJ200 engine and the Eurofighter platform. It strengthens our European defence cooperation. The EJ200 is a proven, world-class engine that significantly enhances the Eurofighter Typhoon’s performance, range and operational efficiency. This new Italian order further cements the critical partnership between government and industry, ensuring continued technological leadership in defence for the Italian nation.”
AVM Simon Ellard, General Manager of NETMA, echoed the sentiment:
“The new order for Italy is yet another fantastic achievement for the Eurofighter programme. Following the Halcón II contract, this marks a new era and shows how vital the Eurofighter Typhoon is to the collective security of Europe. The EJ200 continues to deliver the performance needed to keep the aircraft at the forefront of NATO air power.”
As tensions remain elevated across NATO’s eastern flank, the renewed investment into the Typhoon fleet—and the propulsion technology that powers it—demonstrates a clear commitment to maintaining readiness, interoperability, and technological edge across Europe’s air forces.
Mitsubishi Materials at EMO 2025 – An all-round, service-oriented experience
Mitsubishi Materials will have a strong presence at this year’s EMO exhibition with a booth in Hall 5 at stand location A14. Visitors will find the latest generation of high-tech tooling and special application areas.
This year, a specially dedicated section, the Circular Economy Area, will be highlighting exciting new areas of service and sustainability, such as project engineering and special tools, top-class tool reconditioning and remanufacturing services as well as advanced production capabilities in Europe. Mitsubishi Materials is evolving into to a full-service provider, offering a full range of tooling solutions, from the original manufacturing and sales through to custom made tools and comprehensive after sales support.
A particular highlight will be the importance of material recycling and the latest innovative recycling programme, which has been accelerated by the recent addition of H.C. Starck, a global leader in recycling services, to the Mitsubishi Materials Group. Customers will be given details of the recently launched project for the collection and reprocessing of used carbide tools, and the significant benefits for their production processes and their environmental footprint.
Another key part will be the demonstration of Mitsubishi Materials’ reconditioning and tailored tool design capabilities. With the acquisition of U.F.P. s.r.l., one of Europe’s largest and most well-established providers of reconditioning services and customized cutting tools in Europe, Mitsubishi Materials will significantly reduce response and delivery times for European customers in the increasingly important area of reconditioning of their existing cutting tools.
Furthermore, there will be extensive information available on Mitsubishi Materials’ portfolio of facilities, including its European manufacturing plant and the advanced technology and education centres (MTEC). Customers will be able to find out about turnkey tooling packages and process optimisation that can be provided by the engineers and manufacturing professionals at these state-of-the-art facilities. Visitors can look forward to a special, attractive workpiece on display, featuring selected parts manufactured at MTEC. This will highlight the capabilities of the engineering team, their design expertise and machining precision.
Cutting tools and bodies highlighting next generation technology in carbide substrates, advanced geometries and coatings will also be prominently displayed. The latest PcBN tools along with the innovative MV series of indexable inserts for turning applications, will be strongly featured on the new style tooling stands.
Solid carbide end mills such as the new small diameter VQ long neck series will be on show and highlight the extreme precision required for manufacturing such small diameter end mills. Also on display will be the latest drills, including both the solid DVAS and DFAS types, as well as the new, innovative exchangeable head type DXAS drills for efficient drilling of steel and cast iron.
Leading the discovery of the future – Sustainable machining through data intelligence
Fagersta, July 1st – At Seco, our purpose is “Together we make manufacturing fast, easy and sustainable.” As manufacturing companies work towards more sustainable manufacturing, there are challenges regarding the collection, analysis and management of relevant data. As highlighted by future legislation, data connected to the machine and machining environment will become key to drive sustainability in the most effective way.
The project
To address this challenge, Seco has partnered with the Advanced Manufacturing Research Centre North West (AMRC), in Samlesbury, UK, which plays a key role in driving recovery, growth, productivity, and innovation. The collaboration aims to drive utilization of Internet of Things (IOT) hardware, various industrial communications, and IOT Protocols to produce a single source of truth for facility use and machine data, relevant for environmental impact assessments and improvements.
This project segments the manufacturing ecosystem into three interrelated domains: the machining process itself, the immediate machine environment, and the broader facility context. By monitoring each area individually and then analyzing how they influence one another, stakeholders gain both detailed diagnostics and a holistic perspective on sustainability challenges.
- For the machine – The approach enables monitoring and hotspot analysis of the machining process directly. This includes information on the energy consumption of the machine, broken down by sub-process, cutting fluids and other material consumption. This can then be directly converted into real time costs and CO2 impact through live grid carbon intensity factors and cost per kilowatt hour.
- For the machine environment – The monitor tracks the humidity and temperature, which can impact the energy required to ensure environment stability for the machine.
- For the facility – The monitor tracks the entire manufacturing plant and identifies high level patterns that can negatively impact energy and cost.
- The relationship between – Did the humidity around the machine increase the required energy for cooling? Are open windows requiring more energy? Or are closed windows not providing sufficient natural ventilation and thereby increasing cost to maintain the required temperature? Are the machines optimized?
This approach will help to identify patterns and factors that can help companies reduce their CO2 and costs most relevant to the customer’s specific context. Within this monitored environment, Seco UK can analyze a machining program and processes in fine detail – and further refine the programs by associating power consumption and CO2 emissions within the machine.
The future
By harnessing independent monitoring of power consumption and facility usage, we can pinpoint the hidden costs of inefficiency and translate every kilowatt hour into real-time CO₂e and expense metrics. This level of insight allows us to compare the energy demands and carbon footprints of any two products, programs or machines – empowering our teams to make data-driven decisions and embed sustainability at the heart of manufacturing design.
The test environment, complete with integrated monitoring for both Seco products and guest supplier machines, bridges Life Cycle Assessment of Seco with live machine data. By doing so, we gain precise, component-level environmental scores and open the door to targeted innovation and validation of greener machining strategies.
Looking ahead, we are building toward an AI-powered, automated feedback system that continuously optimizes processes in real time. This solution will balance productivity and cost imperatives with environmentally responsible best practices, ensuring every adjustment drives us closer to net-zero goals. Together with the AMRC and our customers, we’re turning comprehensive data intelligence into actionable sustainability, living our purpose of making manufacturing fast, easy and sustainable.
With its origins in Fagersta, Sweden and present in more than 75 countries, Seco is a leading global provider of metal cutting solutions for indexable milling, solid milling, turning, holemaking, threading and tooling systems. For nearly 100 years, Seco has driven excellence throughout the entire manufacturing journey, ensuring high-precision machining and high-quality output.
For the latest innovations and cutting-edge products, visit our website.
EMO 2025: SW launches Sfix system and BF 12-21D
Waldmössingen, July 2, 2025 – The right solution for every application, from small to large series production: At this year’s EMO in Hannover, Schwäbische Werkzeugmaschinen GmbH (SW) is presenting two new products at its stand C05 in Hall 12. The innovative Sfix system (Smart Fixture) is capable of automatically assembling modular clamping fixtures for workpieces, enabling efficient and precise clamping even for small batch sizes. With the new BF 12-21D machine tool, SW is responding to the current trend in automotive engineering toward die-cast aluminum body parts.
In line with this year’s trade fair motto, “Innovate Manufacturing,” Schwäbische Werkzeugmaschinen GmbH is presenting its response to current trends and requirements in production technology at EMO. “Especially outside the automotive industry, we see great potential for optimization in medium- and small-series production, which requires greater flexibility and modularity from manufacturers,” says Michael Kreuzberger, Product Manager at SW. “To address this, our new Sfix system revolutionizes clamping technology: through automation, it enables higher productivity even in production lines with smaller batch sizes.”
Modular and automated clamping
The Sfix system offers a solution to one of the biggest time wasters in the clamping of small- to medium-sized product series: While companies with high production volumes typically use dedicated clamping fixtures for each product, this approach is not economically viable for small batch sizes. Storing multiple fixtures over the long-term is often impractical due to space limitations and escalating costs. As a result, many manufacturers are forced to manually create a new clamping fixture for each new product series. The Sfix system offers a flexible solution to this challenge: it automates the assembly of the appropriate clamping technology for each workpiece – and provides users with a virtually unlimited number of clamping fixture for a one-time investment. At the core of the system is SW’s patented Sfix plate, which features retractable pins that allow for flexible positioning of components. Various clamping modules can then be attached to these pins to build the individually required fixture.
The advantages of the Sfix system extend beyond its modular mechanical design: in the so-called S-cell, which SW is presenting at its EMO booth, the clamping fixture is assembled quickly and fully automatically. The cell is equipped with all necessary clamping components and workpiece carriers as well as a robot. Users only need to define the clamping points within the CAD model and configure the fixture setup. The smart, AI-supported system then generates a bill of materials for the required elements and automatically programs the robot for assembly. “The Sfix system eliminates the time-consuming manual preparation of clamping fixtures entirely,” emphasizes Kreuzberger. “Processes that previously required several hours are now completed within minutes. In addition, the S-cell requires very little floor space, making the storage of existing large fixtures obsolete.” SW will demonstrate the system’s rapid fixture assembly in live presentations at EMO.
New machine for current trends
SW’s booth at the trade fair offers not only solutions for small batch sizes: with the BF 12-21D, the company is also presenting a new machine tool for high production volumes. As part of SW’s BF series, the system is specifically designed for the fast machining of frame and structural components. “In automotive engineering, we are seeing a clear trend toward the use of aluminum die-cast parts in vehicle body construction,” explains Kreuzberger. “These parts require less manufacturing precision than, for example, gearbox or stator housings. With the BF 12-21D, we offer an economical and dynamic machine concept for precisely these applications.”
The BF machine series differs from other SW machines in its structural design: to fit the specific market conditions, it features a hybrid axis configuration, utilizing a linear drive for the X-axis, i while the Y- and Z-axes are driven by ball screws. SW also relies on proven twin-spindle technology to easily meet high productivity requirements: with two three-axis units and one spindle per working area, the BF 12-21D can replace two conventional single-spindle machines – and achieve higher output with a smaller footprint. When components are changed in one working area, the second spindle in the other working area can be used to achieve even higher productivity.
Maximum output per footprint
For maximum productivity requirements, SW is also exhibiting a proven machining center at EMO: The BA 442 is one of SW’s fastest and most sustainable machines. With four spindles, it offers maximum effectiveness per space while also being energy-efficient. Compared to four single-spindle machines, users can save around half the energy required with the BA 442 and need significantly less floor space. SW’s patented monoblock design ensures high machine rigidity and correspondingly high accuracy. The tool magazine is one of the largest in the entire SW portfolio, with up to 232 tools.
At EMO, the BA 442 will demonstrate its capabilities through two distinct applications: while one side of the table will machine a hydraulic valve, the other side will showcase free-form surface milling using 5-axis simultaneous machining. “The BA 442 is suitable for all industries where maximum productivity meets high quality standards,” emphasizes Kreuzberger. “Our objective at EMO is to showcase solutions for every need. After all, as a system provider, we strive to achieve the best results for our customers in every application – or as we put it: best per part.”
Install NOW, Pay Later – Matsuura…
At MTDCNC, we’re always highlighting real opportunities that help UK manufacturers stay competitive—and right now, there’s a strong one on the table. Premium-spec Matsuura 4- and 5-axis multi-pallet machines are in stock here in the UK, and available with a flexible “Install NOW, Pay Later” option.
This means you can bring powerful automation-ready technology onto your shop floor immediately—without the upfront financial pressure. It’s a timely chance for any machine shop looking to boost output, improve efficiency, and futureproof production.
These Matsuura machines are built for unmanned, lights-out machining, offering reliable and repeatable performance across long cycles. Multi-pallet capability allows for smoother workflows, reduced setup times, and higher spindle utilisation—translating to tangible gains in productivity.
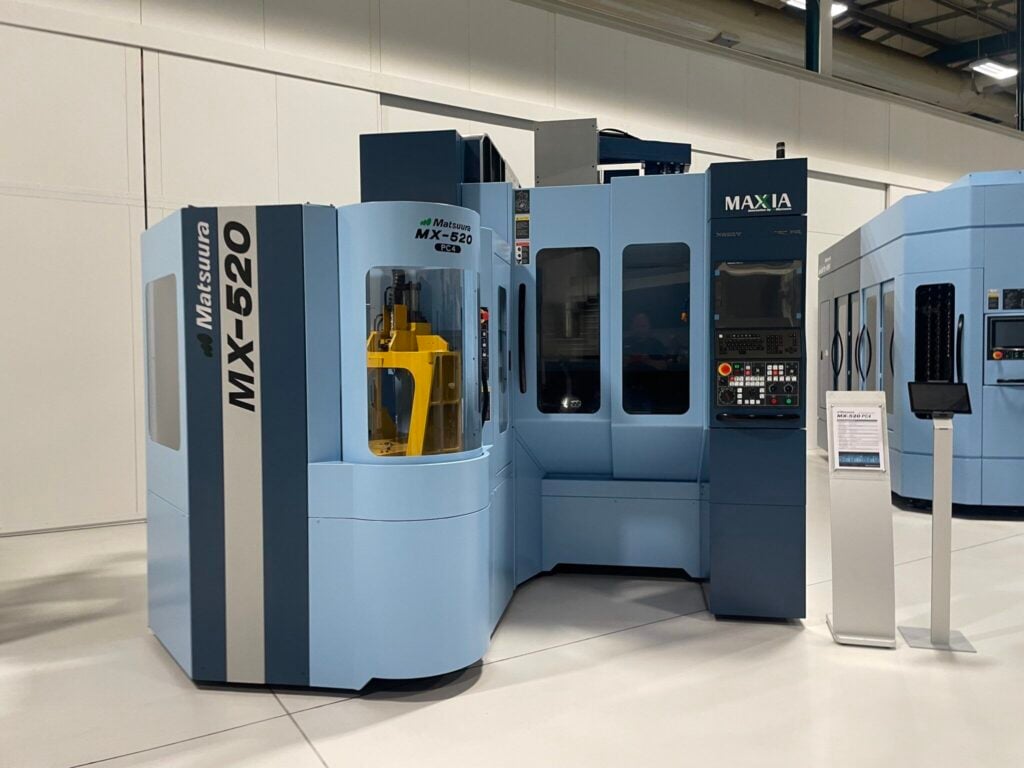
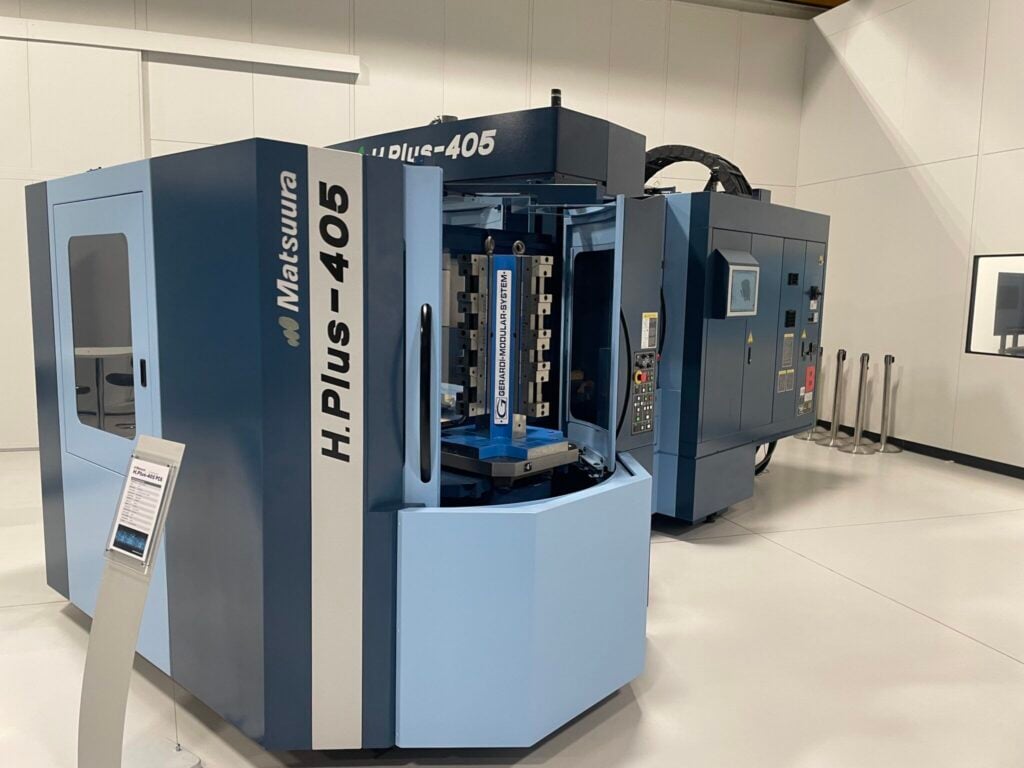
From what we’ve seen across the UK, shops running these systems are seeing real results: consistent part quality, shorter lead times, and the freedom to reallocate skilled operators where they’re needed most. Whether you’re machining complex components or running batch work, this type of platform supports scalable, high-performance manufacturing.
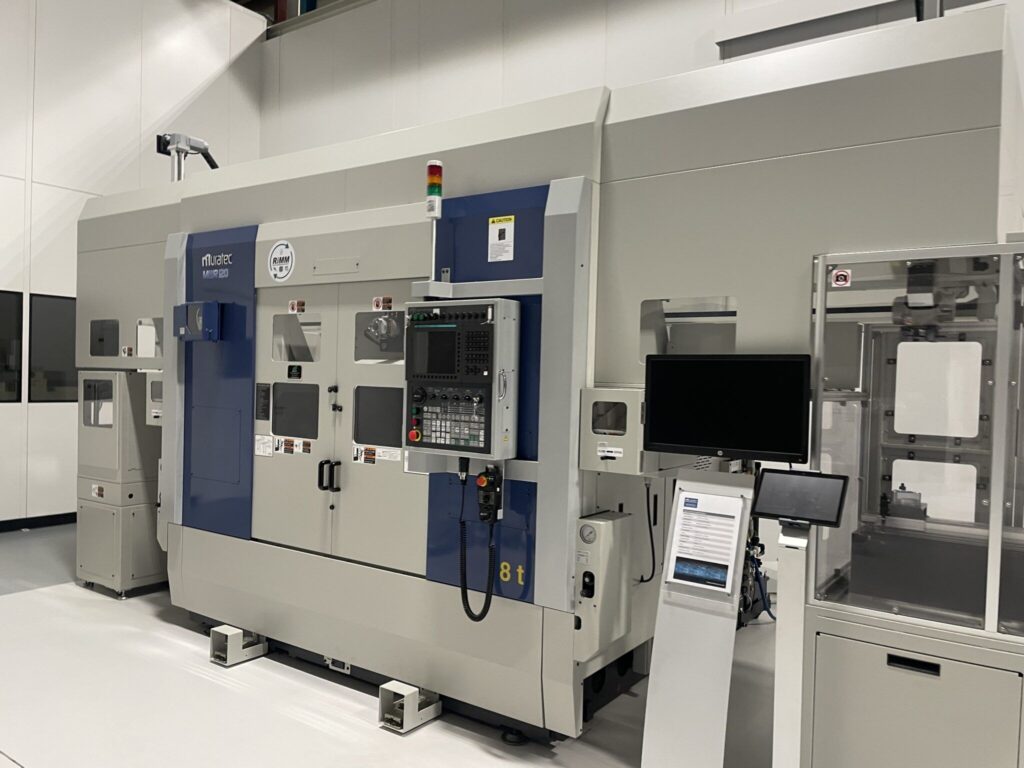
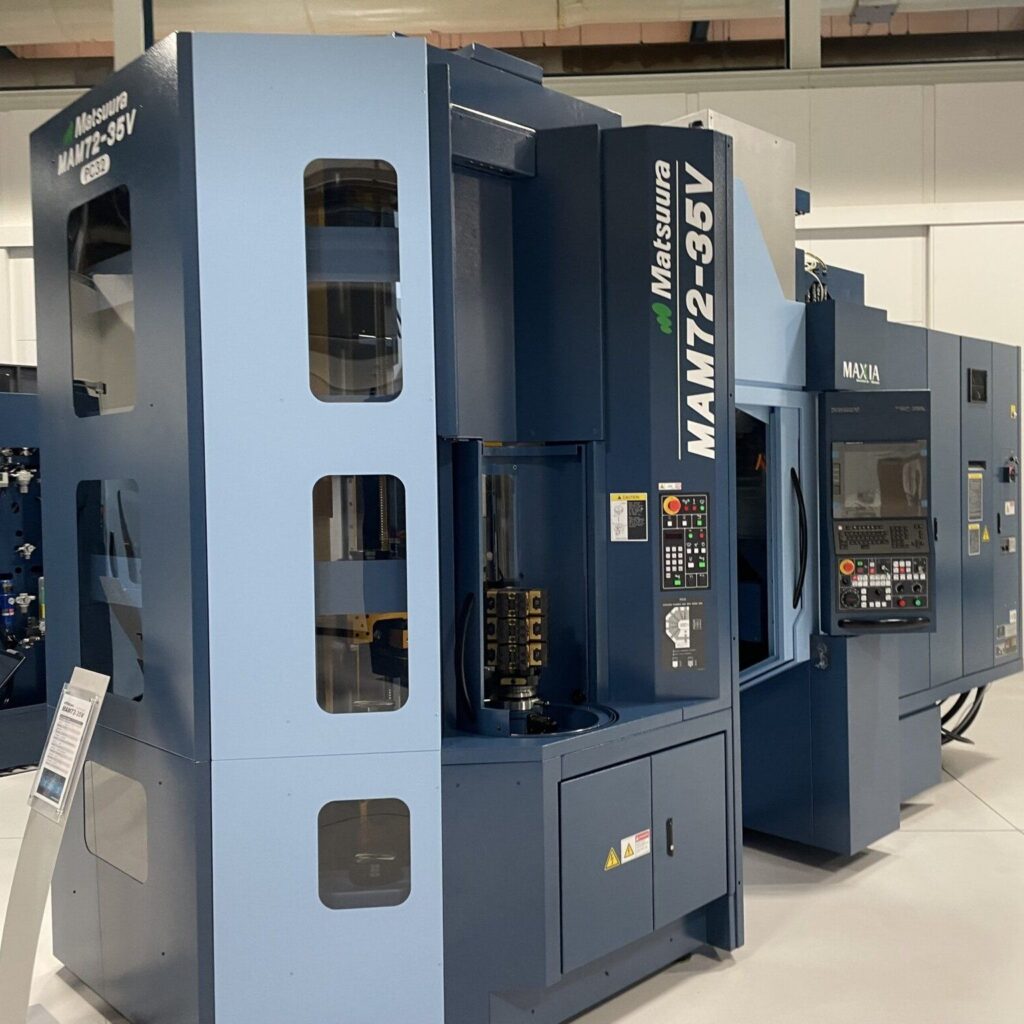
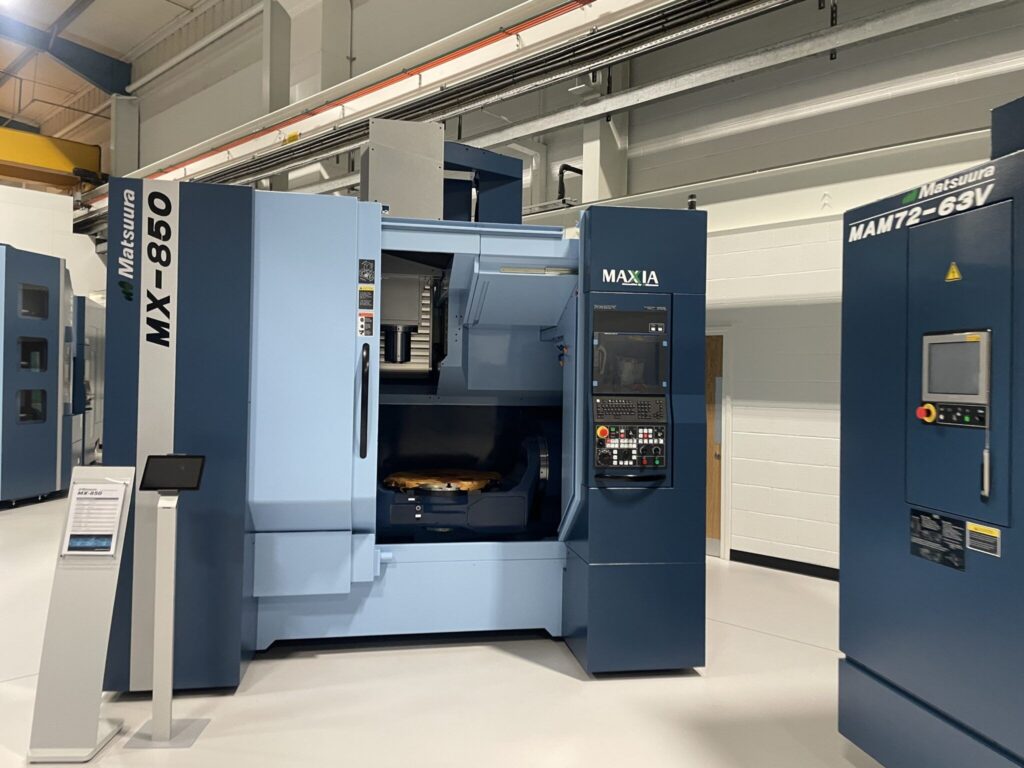
With stock available now—and installation ready to go—this is more than just an offer; it’s a practical route to higher efficiency and smarter working.
Install NOW, Pay Later. Machines in stock. No long lead times.
If you’re thinking about adding multi-axis automation or upgrading capacity, now’s a great time to explore what’s on offer.
UK Manufacturing Downturn Shows Signs of Easing Amid Cautious Optimism
The UK manufacturing sector showed signs of stabilising at the end of the second quarter, according to the latest S&P Global UK Manufacturing Purchasing Managers’ Index (PMI) report. While key indicators such as output, new orders, and employment remained in contraction territory, the pace of decline slowed notably. The seasonally adjusted PMI registered 47.7 in June, marking its highest reading in five months and maintaining the improvement seen since March’s near 18-month low.
Although four of the five PMI components—output, new orders, employment, and stocks of purchases—signalled continued deterioration in operating conditions, all showed weaker rates of contraction. Vendor lead times also extended for the 18th straight month but to the least degree since March.
June marked the eighth consecutive monthly drop in manufacturing output. Firms scaled back production in response to ongoing economic uncertainty, subdued demand, and inflation-related cost pressures. New orders also declined, although at the slowest rate in the current nine-month streak. Weaker demand came from both domestic and international markets, with export orders falling for the 41st month in a row, primarily due to reduced activity from the US, Europe, and China. Tariff concerns further dampened international client confidence.
Despite these challenges, business sentiment improved. Around 46% of manufacturers expect output to increase over the next 12 months, compared to just 10% predicting a decline. Optimism is driven by plans for new product launches, expansion into new markets, increased investment, and efforts to boost organic growth. Additionally, the new orders-to-finished goods ratio—a key forward-looking indicator—rose to its highest level since August 2024.
Nevertheless, employment in the sector continued to fall, marking the eighth consecutive month of job cuts. Reductions were reported across all manufacturing categories and company sizes, with the steepest declines at larger firms. Job losses were attributed to efforts to reduce excess capacity amid falling backlogs of work and streamlined stock levels.
Input costs continued to rise for the 18th straight month, influenced by inflation, higher labour costs, and supply chain disruptions. Price increases were particularly noted in chemicals, metals, packaging, and food products. However, both input cost and selling price inflation eased slightly, hitting their lowest levels in several months.
Rob Dobson, director at S&P Global Market Intelligence, cautioned that while the outlook has brightened slightly, uncertainty surrounding tariffs, government policy, and geopolitical instability could still hinder a full recovery.
LK Metrology Altera SF CMMs Provide High-Precision Inspection for Large Workpieces!
LK Metrology has unveiled its latest innovation in coordinate measuring machines (CMMs) with the introduction of the Altera SF series. Designed for high-precision inspection of bulky and large workpieces, these bridge-type CMMs offer impressive laboratory-grade accuracy and large measuring volumes that range from 1,000 × 1,000 × 800 mm up to 4,000 × 1,500 × 1,500 mm. This expansive measurement capability allows for the inspection of large components directly at the production site, providing operational flexibility and enhancing quality control across a variety of component sizes.
The Altera SF models are engineered with a ceramic bridge and spindle, offering superior stiffness-to-weight ratios, thermal stability, and dimensional consistency. These materials ensure that the machines perform consistently over extended periods of time, making them ideal for high-precision measurements in demanding industrial environments. The air-bearing friction drives ensure smooth axis movements, which are crucial for achieving high-accuracy laser or analogue scanning as well as touch-trigger probing.
These CMMs are equipped with advanced probe heads such as the Renishaw PH10MQ PLUS indexing probe head and the REVO2 head, which converts the CMM into a five-axis scanning model. These heads support multisensor technology, allowing users to perform a wide range of measurements with enhanced flexibility and accuracy.
Temperature management is a critical factor in ensuring consistent measurement accuracy. To address this, the Altera SF CMMs come with thermal covers that protect the guideways from thermal influences and accidental damage. In addition, the machines feature fans beneath the granite table to maintain ambient air circulation, mitigating thermal imbalances, especially in environments without precise temperature control. Integrated temperature sensors monitor heat fluctuations, and all measurements are compensated to a 20°C reference, ensuring reliable results even in fluctuating conditions.
The Altera SF models also incorporate glass-ceramic optical scales that have zero thermal expansion and are highly resistant to contamination. These low-maintenance scales ensure long-term stability, reducing potential sources of measurement errors and enhancing the overall accuracy of the machine.
Vibration and shock are often major challenges in maintaining precision during measurements. To counteract this, the Altera SF machines feature elastomer antivibration mounts that isolate the CMM from mechanical disturbances, such as those caused by nearby machine tools. For even greater stability and accuracy, users can opt for the active intelligent antivibration system, which uses built-in magnetic field sensors to adjust the table’s height and level automatically, ensuring the highest measurement accuracy.
In terms of automation, the Altera SF models come with the LK NMC300 multipurpose controller and the CAMIO software suite, making them ready for integration into in-line or line-side automation for large-volume production environments. Real-time monitoring of quality data, CMM performance, and system status is available through smart devices, providing operators with immediate access to critical information.
In addition, the EcoAir function, which reduces compressed air consumption by up to 95% when the CMM is idle, helps reduce operating costs, further enhancing the cost-effectiveness of the Altera SF machines.
With its advanced features and robust design, the Altera SF series from LK Metrology offers an ideal solution for manufacturers needing reliable, high-precision inspection capabilities for large, complex workpieces. Whether for aerospace, automotive, or heavy machinery applications, these CMMs deliver enhanced operational efficiency and support higher productivity, meeting the growing demands of modern manufacturing.
Eurotech Elite Seeks Partners for U.S.-Made CNC Lathes to Strengthen Local Manufacturing!
Eurotech Elite, a family-owned provider of high-precision turn-mill technology since 1992, is expanding its operations by seeking partnerships with U.S.-based, family-owned manufacturers to help build a new line of American-made CNC lathes. This initiative marks a significant step in Eurotech Elite’s evolution, as it plans to bring its advanced, precision machining designs together with the strength and expertise of American manufacturing.
Headquartered in Florida, Eurotech Elite has built a reputation for delivering innovative multiaxis machines that cut cycle times and provide excellent ROI for manufacturers. The company is renowned for its commitment to quality and offers free lifetime training for every machine it produces, ensuring that customers have the support they need to maximize the value of their equipment.
The new line of CNC lathes aims to combine Eurotech’s decades of engineering excellence with the skill and capabilities of U.S. manufacturers. Eurotech Elite is looking to partner with U.S.-based manufacturers who specialize in machining large components with tight tolerances and who have the capacity to produce 50 machines per year, with a target of reaching 200 units annually.
Eurotech Elite will provide its partners with the following:
- Design and plans for a high-precision, five-axis turn-mill center, incorporating Eurotech’s advanced design features.
- Decades of engineering leadership and expertise, including its well-known Eurotech Multiflex model, which has set standards in the industry.
- A comprehensive distributor base offering sales and local service across North America.
- Lifetime training and technical support, ensuring partners have the necessary resources to maintain and operate the machines effectively.
By reshoring production, Eurotech Elite aims to reduce lead times, strengthen local supply chains, and support American manufacturers in becoming more competitive in the global market. The company believes that its U.S.-made CNC lathes will help American manufacturers maintain their competitive edge and meet the increasing demand for high-quality, precision-machined components.
Eurotech Elite’s move to produce CNC lathes in the U.S. is part of a broader effort to foster local manufacturing capabilities, reduce dependence on foreign suppliers, and ensure that American manufacturers have access to the latest technologies for machining large and complex components. With this new initiative, Eurotech Elite hopes to build lasting partnerships and drive the future of manufacturing in the United States.
Allied Machine Appoints Bill Ruegsegger III as Western Regional Manager!
Allied Machine and Engineering, a recognized leader in the design and manufacturing of holemaking and finishing cutting tools for the metal-cutting industry, has announced the promotion of Bill Ruegsegger III to the role of Western Regional Manager. With this new position, Ruegsegger will oversee operations across Allied’s Western region, where he aims to cultivate a culture of accountability, continuous improvement, and collaboration to drive operational excellence.
Ruegsegger brings a diverse skill set and a wealth of experience to his new role. His background spans across various facets of manufacturing, including hands-on experience with CNC machines, programming, and application engineering. Over the past five years, he has served as a product manager, concentrating on product development and understanding market needs. His comprehensive expertise in the manufacturing process makes him well-equipped to lead and drive growth in the Western region.
In his new role, Ruegsegger intends to tailor strategies that address the unique demands of each territory. He is focused on fostering strong customer relationships, improving operational efficiencies, and driving revenue growth. A core aspect of his vision is to position the Western region as a benchmark for operational excellence, employee engagement, and innovation, with a long-term goal of contributing significantly to Allied Machine’s overall success.
Ruegsegger expressed enthusiasm about his promotion, stating, “I’m excited about the opportunity to join the exceptional team of sales engineers in the Western region. Throughout my time with Allied, I’ve been consistently impressed by their professionalism, respect, and drive to succeed in the marketplace. I’m looking forward to connecting with our valued distribution teams in the region, as well as building strong partnerships with the end users who are putting our tools to work. The West Coast offers incredible opportunities, and I’m eager to explore all that it has to offer.”
As the Western Regional Manager, Ruegsegger will leverage his knowledge of Allied Machine’s products and services to build lasting relationships with key distributors and end-users, further solidifying the company’s presence in the competitive metal-cutting market.
Hexagon Live Global 2025 Highlights the Future of Autonomy and Manufacturing Innovation!
Hexagon AB, a global leader in digital solutions, held its annual Hexagon Live Global conference from June 16 to 19, 2025, at the Fontainebleau Resort in Las Vegas. This year marked a significant milestone as the company celebrated a quarter-century of measuring technology development, which began with the acquisition of metrology tool manufacturer Brown & Sharpe in 2001. The event, titled “Beyond Measure – Unlocking the Next Frontier of True Autonomy,” showcased Hexagon’s advances in the realms of digital transformation, automation, and artificial intelligence (AI), with a focus on the evolution of true autonomy in manufacturing processes.
During the keynote address, Ola Rollén, chairman of the board at Hexagon AB, emphasized the profound impact measurement technologies have had on human achievements. He referenced how vital it is to measure distances accurately to even perform a task as complex as landing on the moon, illustrating the importance of precision and innovation in technology. Rollén also looked back on Hexagon’s journey, noting the company’s transition from sensor development to bridging the physical and digital worlds in 2010—a shift that today is known as the concept of digital twins, which has revolutionized industries like med tech, mechanical engineering, and electronics.
A key highlight of the event was the announcement of the new division, Hexagon Robotics, led by Arnaud Robert. Robert’s presentation on the importance of true autonomy featured the Aeon humanoid robot—a cutting-edge development for industrial applications. Aeon is designed to adapt to existing infrastructure, which Rollén sees as a critical advantage since the world was designed by humans for humans. Aeon is powered by AI and has 12 cameras, 22 sensors, and the ability to perform self-swapping of batteries for continuous operation. Its versatile design enables it to conduct tasks like asset inspection and reality capture, marking a significant step forward in automation and AI integration.
Hexagon also announced the spin-off of its divisions into Octave, a new company focused on mission-critical assets and infrastructures. Octave, which combines four key software companies (ALI, SIG, ETQ, and BRICSYS), will focus on providing solutions for industries like energy, transport, and advanced production facilities, with an emphasis on improving asset management, operation, and protection.
Throughout the conference, the attendees had the opportunity to explore innovations at The Zone, where Hexagon displayed technological advancements across defense, industrial facilities, manufacturing, mining, and safety sectors. One standout exhibit was the Kuzma self-playing guitar, a demonstration of autonomy and automation at work.
Another critical session was the Advanced Manufacturing Report 2025, presented by Paul Miller, Vice President at Forrester Research. The commissioned study highlighted key trends shaping the future of manufacturing, focusing on agility, sustainability, and AI adoption. The study revealed that agility remains a significant concern for manufacturing leaders, with many executives reporting that rigid processes hinder adaptability. Furthermore, Miller identified four primary trends that will define the future of manufacturing:
- Integrating digital technology with physical products—referred to as “a shift from grease to code.”
- Embracing local, near, and far manufacturing capacity.
- Balancing the automation triangle, which involves people, hardware automation, and software automation.
- Electrifying and decarbonizing manufacturing processes to achieve sustainability.
Hexagon Live Global 2025 was an important event that not only highlighted Hexagon’s advancements in measurement and automation but also underscored the company’s commitment to shaping the future of manufacturing with a focus on autonomy, AI, and digital innovation. As industries across the globe continue to face challenges and opportunities driven by technological progress, Hexagon’s innovations are poised to play a pivotal role in shaping the manufacturing landscape in the years to come.
GROB Systems to Host 5-AXIS LIVE! Technology Event Showcasing Machining and Automation Innovations!
GROB Systems, a leading developer of manufacturing systems and machine tools, is set to host a groundbreaking technology event, 5-AXIS LIVE!, at its North America headquarters and production facility in Bluffton, Ohio, on August 5, 2025. The event will run from 9:00 a.m. to 4:00 p.m. and will focus on The Future of Manufacturing – Made in the USA, bringing together industry leaders, experts, and manufacturers to explore the latest advancements in machining and automation technologies.
This one-day event promises to provide valuable insights into new machining strategies, particularly those optimizing the production of complex aerospace, medical, and mold/die parts. Manufacturing professionals and industry stakeholders are invited to attend the event, which is complimentary and designed to showcase cutting-edge innovations in the manufacturing sector.
Key features of the event will include informative seminars and live demonstrations of 5-axis machining on a full range of GROB machining centers. These demonstrations will highlight the integration of advanced machining technologies with the latest in automation systems, providing attendees with a comprehensive understanding of how to optimize production processes. Additionally, attendees will have the opportunity to tour GROB’s expansive 500,000-square-foot facility, which houses vertically integrated manufacturing of machining centers and automation systems.
GROB Systems will be joined by twenty-one industry partners, each contributing expertise in their respective areas. The participating companies represent leaders in machining applications, software, cutting tools, automation design, and integration. Some of the prominent partners include Allied Machine & Engineering, Benz Tooling, Blaser, BLUM, Caron Engineering, Concepts NREC, EMUGE-FRANKEN USA, Haimer, Harvey Performance Company, Heidenhain, Lang Technik-USA, Mapal, Koma-Precision, OPEN MIND Technologies, Rego-Fix, Renishaw, SECO, Siemens, Third Wave Systems, and Zoller. The event will feature presentations from SECO, OPEN MIND Technologies, and Lang Technik-USA, offering deeper insights into the latest tools and software driving industry innovation.
Attendees will witness live demonstrations on various GROB 5-axis machining and automation solutions, including models such as the GROB G150, G350, and G550 5-axis Universal Machining Centers, as well as a Mill/Turn system. Additionally, GROB will showcase its cutting-edge automation solutions, including pallet and part handling/storage systems, and robot systems, which streamline manufacturing processes and improve operational efficiency.
A key highlight of the event will be a customer panel, where attendees will have the chance to hear firsthand from GROB machine owners about their experiences with the company’s machining systems and solutions. This will offer valuable insights into the practical applications of GROB’s technology in real-world manufacturing settings.
The event will also spotlight the GROB Apprenticeship Program, a successful initiative aimed at addressing the ongoing skills gap in the manufacturing workforce. The program continues to be a cornerstone for workforce development, providing the next generation of manufacturing professionals with the skills they need to thrive in the rapidly evolving industry.
The 5-AXIS LIVE! event promises to be an invaluable experience for those in the manufacturing sector, offering opportunities to learn about the latest technologies, engage with industry experts, and discover new ways to optimize production and stay competitive in the ever-evolving manufacturing landscape.