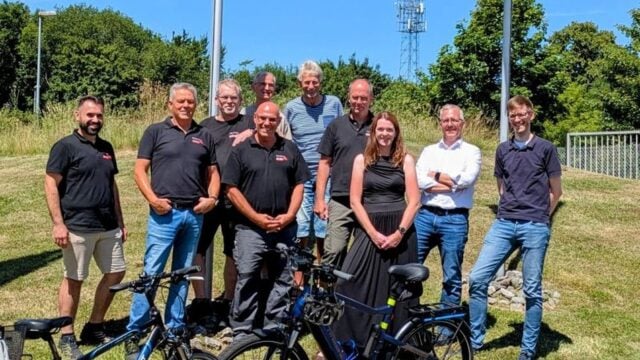
Starrag Team Excels in Stadtradeln 2025 Challenge
Starrag’s participation in the Stadtradeln 2025 event has concluded on a high note, with the team…
With over 100,000 gearboxes already produced for wind turbines, the NGC Group from China has eight Starrag machines at its main factory that have proven their valued position in the process. This historical success was reason enough for the Chinese market leader in wind turbine powertrains to increase the number of Berthiez, Dörries and Heckert machines to 20.
China wants to be carbon neutral by 2060 and wind power plays an important role in this plan. The country is already the world leader with an installed capacity of over 365GW, but it is still expanding this position. From 2026 onwards, wind turbines with a total capacity of 130GW are to be built year on year.
Chinese companies such as Nanjing High Speed Gear Manufacturing Ltd (NGC Group) play an important role in this. The company from Nanjing, the capital of the eastern Chinese province of Jiangsu, is the leader in gearboxes for wind powertrains in China with a market share of 60%. For years, the company has also been one of the three internationally leading manufacturers of drive technology for wind turbines.
The driving factor for NGC is the clear commitment: “Only a green future is a good future”. Founded in 1969, the company sees itself as well-positioned to follow this sustainable path thanks to its more than 50 years of experience in researching and developing high-quality and efficient drive solutions. Huai’an, the third factory in China in addition to the production facilities in Nanjing and Baotou, will set the course for a carbon-free future. Units for the large offshore wind turbines with 15, 18 and 20MW capacity have also recently been built there. This is where Starrag comes in, with its ‘Renewables’ market segment, which has made a name for itself as the industry benchmark worldwide for decades with machines for manufacturing drives for wind turbines. Since 2006, 100 machines have been delivered to China, of which about one in five went to NGC.
Direct on-site service in Shanghai and Beijing
However, the Swiss machine manufacturer also owes this success to its special attitude to service, which is also a distinguishing characteristic of its customer NGC. Consistent and direct on-site support from the Starrag headquarters in Shanghai and a branch office in Beijing is the recipe for success. A large, experienced team supports local customers on-site during the entire life cycle of a machine tool – from consulting, application engineering, and service to comprehensive on-site training.
The machining centres can process workpieces 25% faster than competitor machines.
The interplay of on-site service and high-tech paid off right from the start. “In 2007, we won NGC as our first Chinese customer in the wind power industry there. After successfully handing over the first machine, a Heckert horizontal machining centre in 2009, NGC immediately ordered three more Heckert machines,” recalls Jörg Heinrich, Director of the Application & Technology Department at Starrag Shanghai Co Ltd. In addition to precision, productivity was also a fundamental reason the company bought from the Starrag factory in Chemnitz. According to NGC, the machining centres can process workpieces 25% faster than competitor machines. The production technology and the special on-site service were well received in China and since 2022, NGC has increased the number of Starrag machines in its factories to 20.
A Dörries vertical turning machine has gone to Baotou and nine machines from Starrag’s Berthiez, Dörries and Heckert product ranges have been shipped to the new factory in Huai’an, which plays an important role in the further expansion.
The facts also reflect that NGC invested around five billion renminbi (€650m) in the first phase of the new plant – a factory for 1,000 employees built on an area of 315 hectares. At around 320,000m2 the production area where NGC installed 560 machine tools with the highest precision, one in three is a high-tech machine from overseas. The Starrag machines also play an important role here. They are used for machining the complex structures of cast components for wind power transmissions. The Starrag machines already meet the high-quality requirements for components for 20MW gearboxes in the first production phase. Extremely satisfied, a senior management representative from NGC says: “This is a strong guarantee of the highest gear stability.” This positive response to the nine newcomers in Huai’an points to the proven and long-standing cooperation between NGC and Starrag. “Once again, we were able to individually adapt the machine configurations to the wishes and requirements of our Chinese customer. Working as a team, we jointly developed machines in the right sizes and with the right configuration in each case for the production of new, customised components for the wind power drive train. We are now looking forward to continuing our trusting and successful cooperation with a view to China’s carbon-neutral future, in which we are happy to accompany NGC with our know-how and production technology,” says Dipl.-Ing. Hubert Erz, Senior Consultant Sales Renewables at Starrag.
Stay up to date with the latest industry news and events.
Be first to see all the updates from MTDCNC
Our newsletters frequency varies dependant on content
All the latest deals from the industry feature on our newsletters