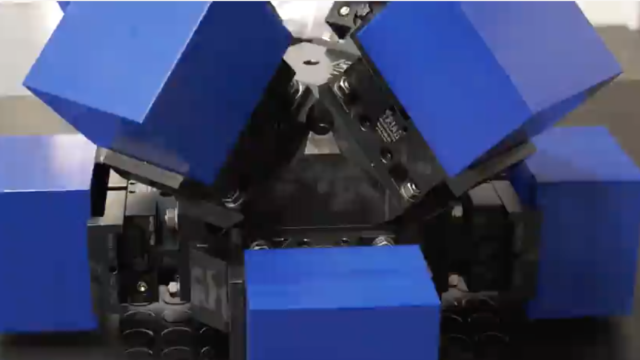
Triag Sputnik Workholding by REM Systems is out of this World
MTDCNC’s Tom Skubala is at REM Systems checking out their space age looking workholding. the Triag…
There are a number of key stages when automating a manufacturing process, and each step will result in specific efficiency gains and business rewards. The key stages are:
• Standardisation
• Organisation
• Automation
• Integration
With 8,760 TOTAL hours available each year the goal is to be productive for all of them.
Standardisation
The starting point for many machine shops. More often than not, each machine tool on the shopfloor is attended by an operator or setter. Working this way on a single shift, each year you will achieve 800 hours of production with 1,000 hours of machine downtime. The addition of a 'Zero Point' workholding system, such as the Erowa MTS (Modular Tooling System) will provide significant improvements, productive time will increase to 1,200 hours with machine downtime dropping to 600 hours per year.
Organisation
This involves using pre-setting systems, so the workpiece is set-up on the pallet and the cutting tool assemblies are pre-set with all the offset data sent to the machine tool's controller so it can start machining with confidence as soon as the guard door is closed. Operating this way on a single shift you can expect to achieve 1,600 hours production with just 200 hours machine down time.
Automation
Automation is an investment that offers many positive benefits to machine tool users, with robotic loading and unloading it takes the gains achieved in each of the previous stages and applies them around-the-clock. Now, you can expect 4,000 production hours from the same machine tool and manpower, with 800 hours of downtime.
Integration
This final stage uses JMS Pro, the ultimate software control system that gives you just about everything you need to control multi-machine automation systems. It integrates with CAD/CAM to give complete control of the work flow and transfers off-set data too. This final stage gets as close as possible to the productive goal, with up to 6,000 hours of production and just 200 hours downtime.
Investment
Of course, there is a cost to attaining this level of performance, but the rewards are far greater. If we compare the integrated results to the standalone we have increased production time from 800 hours to around 6,000 hours.
For just 25 to 30 per cent of the cost of a new 5-axis machining centre you can increase your capacity by more than seven-fold with no extra staff, no overtime and negligible floor space required.
Is it time for your business to start to think outside the box when it comes to maximising productivity and adopting lean manufacturing practises? Our typical automation customer manufactures high value components on 5-axis machines. Their production is predominantly complex components in high variety, low volume with 50-off being considered a large batch.
If you are still unsure about automation we are happy to provide a free of charge consultation to look at specific requirements and provide an honest assessment of how automation could bene?t your production needs
Be first to see all the updates from MTDCNC
Our newsletters frequency varies dependant on content
All the latest deals from the industry feature on our newsletters