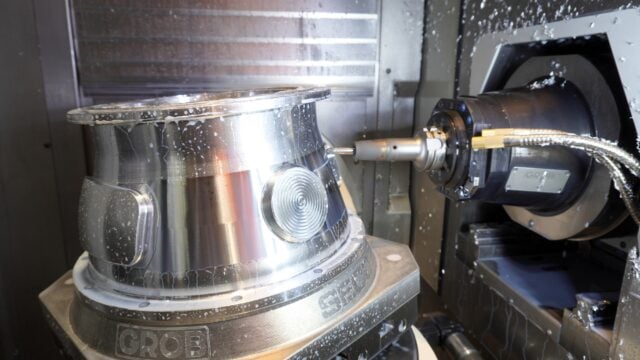
Do You Panic When You’re Machining Like This? 
That panic… you know the feeling. You’re watching the machine, hands hovering near the feed hold…
As a mechanical engineer who grew up around his father’s historical motorcycles, the stars were always aligned for Duncan Dunbar to follow his passion and start his own race engineering business. So, when Duncan returned to Scotland from studying and working in high-end motorsport, he got a unit, purchased a machining centre and invested in OPEN MIND Technologies hyperMILL CAM system to help drive his business forward.
As the Director and Owner of Dunbar Race Engineering Ltd which was founded in 2018 to deliver design and reverse engineering services, Duncan Dunbar rapidly realised that the company needed to make the next step into manufacturing. This led to the acquisition of a Hurco VM10i 3-axis VMC with a 4th-axis rotary table, a Mitutoyo CMM and a seat of the industry-leading hyperMILL CAM system. Specialising in the manufacture and design of components for racing motorcycles and high-efficiency internal combustion engines, Duncan’s expertise was initially carved from stints in British Superbikes and MotoGP before moving into F1. As an Engineering Team Leader responsible for eight design engineers at Mercedes AMG High-Performance Powertrains, Duncan contributed to the Lewis Hamilton and Jenson Button World Championships from 2008 to 2014. However, the draw of Scotland and following his motorcycle passion was too much of a pull for Duncan.
As Duncan recalls: “I’ve always had an interest in bikes and I’ve been riding since I was five years old. I have ridden in offroad and road race motorcycle competitions and worked in motorsport since I left university. I worked in the motorsport industry for the first 15 years of my career, initially in superbikes, MotoGP then for a leading F1 team in the engine design and development department. I then took some time out in Scotland when I started designing parts to help friends with their racing projects. From there it grew into a commercial operation. Initially, I was designing and then subcontracting out the production before finally realising we needed to do it all ourselves – and start manufacturing the parts that we were designing.”
“To bring manufacturing in-house, we needed a machining centre and a good CAD/CAM system – and this is where we use hyperMILL. We also bought a CMM and a part marker. My manufacturing experience in this context was ‘zero’. I grew up making parts for bikes on a small Boxford lathe with my dad. I never intended to go down the manufacturing route but when the realisation came about and we needed to make the next step and bring parts in-house, I wanted to have an approach where we could have no excuses.”
As Duncan states: “I wanted our business to aspire to the level that we wanted to be at and having a CAM system like hyperMILL from the ‘get-go’ meant that we had no excuses. hyperMILL gave us every opportunity to do the best we possibly could. We weren’t looking at parts thinking ‘we can’t make it’. Our mindset was all about thinking ‘How do we make it?’ With the support of OPEN MIND and hyperMILL, we’ve been able to make some fantastic parts, especially given our level of experience.”
Looking at the components the company manufactures, Duncan continues: “We are making a variety of chassis parts for racing motorcycles and chassis kits, and some of these are fabricated in. We also manufacture some suspension parts that often have scanned surfaces or difficult pockets to machine. hyperMILL makes these tasks quite easy and with the support that we get, OPEN MIND has us making parts that are way ahead of our years of experience.“
Ease of Programming
Fabricator Kevin McNulty from Dunbar Race Engineering Ltd adds: “I have been a fabricator for over 15 years, and I started working with Dunbar two years ago – learning how to become a machinist. It has been a steep learning curve, learning how to operate a CNC machining centre and programme the CNC with hyperMILL. It has been a fun process, and I would say that hyperMILL has made the journey a lot easier. hyperMILL has certainly helped me in several areas and part setup is one of those things. Getting all of that into my head as a non-machinist would typically be a challenge but seeing it all on a screen with hyperMILL makes it so much easier to figure out and interpret what setup is required for each part. The simulation has been perfect, and it gives you trust in what you are programming, and you can see that it is safe to run the program.”
Reflecting upon the journey of Dunbar Race Engineering, OPEN MIND UK’s Simon Docker says: “It’s inspiring to see small British companies grow with the help of hyperMILL. The majority of components on the racing bikes at Dunbar are manufactured here, and for OPEN MIND, we can help businesses small and large. To see the range of fantastic components being manufactured at Dunbar with the help of OPEN MIND and hyperMILL is amazing. As a company, we pride ourselves on our level of support and here we have an example of a team that has not even come from a machining background. They had no machining knowledge, no knowledge of G-Codes – but they have used our support desk to get them to this stage. Dunbar has come from nothing to a business making fantastic components in a short time.” Adding to this sentiment, Duncan concludes: “It has surprised us how quickly we have been able to develop our experience and the type of parts we are making. There are some parts that we initially looked at and were worried that we would never be able to make them. When you break jobs down into one face at a time and one machining cycle at a time, and then build that back into a job list with support from hyperMILL – it’s pleasing to see we have progressed quickly. We can now make parts that we are pleased with, the customer is very pleased with, and we are looking forward to taking on more machining challenges. hyperMILL is an enabler. It allows us to look at components and design things with the knowledge that we can make them. We know we have the backup from the applications engineers and the support centre at OPEN MIND and that allows us to take on these projects without any fear of not being able to deliver.”
Stay up to date with the latest industry news and events.
Be first to see all the updates from MTDCNC
Our newsletters frequency varies dependant on content
All the latest deals from the industry feature on our newsletters