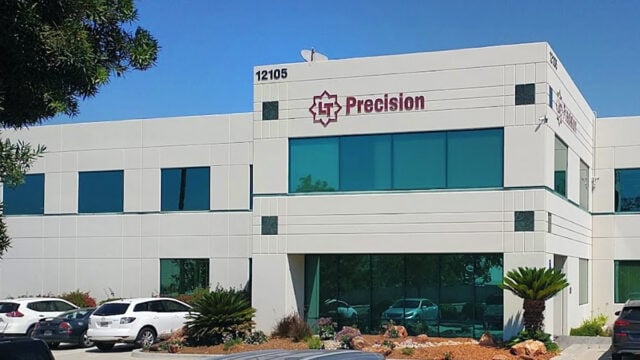
L&T Precision Expands Tijuana Operations and Achieves ISO 9001 Certification!
L&T Precision, a subsidiary of TPC and a recognized manufacturer of precision sheet metal and machined…
The Formula SAE competition, organised annually by SAE International, is a globally recognised engineering challenge for university students. It requires teams to design, build, and race a single-seat race car using an internal combustion engine — all within a single academic year and under strict resource constraints. Among the many challenges teams face, manufacturability of performance-critical components often determines success on and off the track.
For Samuel McCarthy, suspension lead for USC Racing (the Formula SAE team from the University of Southern California), one such challenge was the exhaust collector — a notoriously complex part where performance and manufacturability have traditionally been at odds.
“The exhaust collector joins each cylinder’s exhaust into one stream,” McCarthy explains. “It directly affects engine performance and efficiency, and its shape is incredibly complex. Normally, it’s welded from nine thin-walled titanium tubes, all hand-cut and shaped. It takes hours from a skilled fabricator and there’s still a high margin for error.”
McCarthy and his team knew there had to be a better way — and they found it in Huddersfield-based Wayland Additive Ltd, pioneers of the NeuBeam® additive manufacturing process.
After meeting Wayland at Rapid + TCT in August 2024, the USC team began a collaborative relationship that led to the creation of a fully additively manufactured titanium exhaust collector using Wayland’s NeuBeam technology — a groundbreaking electron beam AM process that offers significant advantages over both traditional fabrication and established metal AM methods like DMLS.
“The ability to print this part in titanium, with low thermal stresses and minimal post-processing, was essential for our race car,” says McCarthy. “Conventional DMLS would struggle in high-vibration environments due to the residual stress, which can cause cracks. But with NeuBeam, the stress profile is much lower — and that’s a game-changer for motorsport applications like ours.”
Not only did the NeuBeam process reduce the fabrication complexity and improve part integrity, it also opened new avenues for performance optimization — previously limited by what could be manually welded or conventionally printed.
This collaboration exemplifies how next-generation AM technologies are empowering young engineers to innovate without compromise, and how industry partnerships are helping solve real-world problems — even on student racing teams.
For USC Racing, the result is not just a better part — it’s a demonstration of what’s possible when engineering ambition meets cutting-edge manufacturing.
Stay up to date with the latest industry news and events.
Be first to see all the updates from MTDCNC
Our newsletters frequency varies dependant on content
All the latest deals from the industry feature on our newsletters