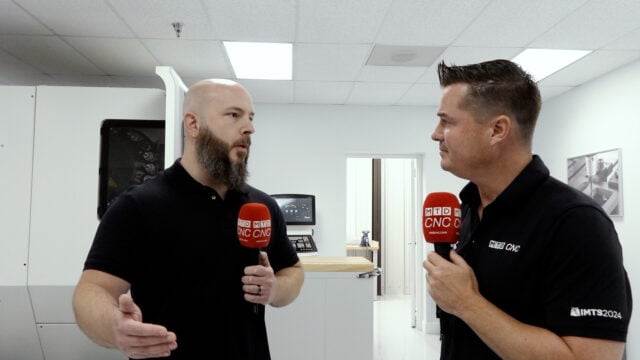
They’re solving some of the biggest challenges with aerospace parts.
MAPAL is a well-known name in the automotive industry, and what they’re doing for the R&D…
As a world leading manufacturer of high-end cutting tool solutions for the automotive industry, MAPAL has once again stepped-in to improve productivity, performance and cost reductions for one of the UK’s leading Tier 1 automotive manufacturers. Helping a UK manufacturer chase the automotive holy grail of reducing ‘cost per part’, MAPAL has demonstrated its competence with this particular Yorkshire manufacturer.
With manufacturing facilities on three continents, the Huddersfield automotive experts have an unparalleled reputation for manufacturing turbocharger, transmission and engine components for the global automotive market. It was the winning of a new long-term contract to manufacture cast aluminium CAM carrier components that led the company to instigate tooling solutions from MAPAL. With MAPAL’s reputation in the global automotive industry preceding the MAPAL engineer that first made contact with the client, the partnership has certainly reaped rewards.
The initial contact instigated with MAPAL over five years ago was due to a requirement to retain tight tolerance parameters and SPC values during production machining and secondly, to reduce tool inventory on its machine tools. Referring to the situation, MAPAL’s Application Engineer Mr Frank Gallagher says: “This customer is producing over 7000 cast aluminium CAM carrier parts each week. To do this, they opted for a series of high-speed FANUC RoboDRILL machining centres with a BT30 spindle, Nikken rotary trunnion and 21 tool ATC. Unfortunately, the extremely complex parts required upwards of 100 different tools per part – our initial remit was to reduce inventory to meet the tool capacity of the machines.” Of course, a result of this lean investigation would reduce inventory costs and reduce cycle times – both areas of expertise at MAPAL.
Implementing the Cost Down Strategy
Demonstrating its unrivalled expertise in the automotive sector, MAPAL has dozens of continuous improvement examples at this automotive leader. As Mr Gallagher recalls: “We had one challenging hole that initially required three different drills and with limited tool pockets on the machine, our aim was to reduce tool inventory and operations. The three previous steps included a pilot hole, a 12XD drill and then a 7mm diameter finishing drill at 40XD. The three drills were initially required to negate the challenge of entering a cast surface, drill wander and breakage. However, we identified opportunities to improve the process that was relatively time consuming with swarf removal being a key challenge. Even with a 40XD hole, we found a single tool solution.”
“This success was replicated on a 25mm diameter bore that is machined to a 70mm depth. Initially, this was rough and finish bored with a chamfer tool finishing the process. We eliminated this 3-tool process by introducing a single multi-stepped tool capable of rough, semi and finish machining the precision bore with a chamfer at the end of the tool.” Whilst these applications exemplify the reduction of tool inventory, they also reduced cycle times considerably. An example was noted on a non-critical 25mm bore, which was machined with a MAPAL PCD boring tool. As Frank continues: “We had a 25mm bore that was taking 90 seconds to machine because swarf clearance and surface finish were an issue; we changed the machining parameters on numerous occasions to improve cycle times. However, the process required a complete strategy shift and we manufactured a special version of the 3-flute Tritan Drill to reduce cycle times from 90 seconds to 10.”
Top Down Approach to Quality
The 400mm by 250mm CAM carrier components require a range of MAPAL drills, multi-function step drills, PCD grooving, boring and face milling tools as well as a selection of roll taps. To meet many of the tight tolerances in the region of +-/-5 microns, MAPAL guarantees this customer a +/-3micron tolerance on the tools to ensure all components are 100% compliant with dimensional demands. To guarantee this compliance, MAPAL manages tool inventory with its UNIBASE Tool Management System and a weekly visit from a MAPAL engineer.
MAPAL has installed a UNIBASE tool management system with a second slave unit that houses tools in a vertical position to protect the tools and increase tool capacity whilst reducing floor area. The vertical tool holding drawers have BT30 toolholding pots in the drawers to minimise tool movement and subsequent damage. Alluding to this, Frank says: “All tools are pre-set by MAPAL at our Rugby headquarters and supplied in the various BT30 and shrink-fit toolholding units, meaning the tools in the UNIBASE are pre-set to the required tool lengths and ready to install directly into the machine, eliminating the tool pre-setting process for the customer. It also eliminates the opportunity for error.”
The weekly MAPAL visit will see the engineer check all tools and take worn or damaged tools back to MAPAL for re-grinding, re-setting and return to the UNIBASE vending system at the automotive facility. The re-grind service certainly reduces tool inventory and costs, giving the end user complete visibility of tooling consumption and costs. However, the MAPAL service is not just about cost reductions, inventory management and simplification. As Frank continues: “Our PCD face mill tools have a series of cartridges that each requires precision setting. Our in-house team will set the tools to a height, diameter and concentricity of less than +/-3 microns. This very high level of precision is a necessity when the customer has a number of +/-5micron tolerances that are tied together on the CAM carrier parts. This can be a challenge for any customer, but having it managed by the MAPAL experts will eliminate any opportunity for error.”
In conclusion, Frank says: “From the outset, we have exceeded the needs of this customer. We started by reducing tool inventory and non-cutting times. From this, we have worked to continually reduce cycle times and ‘cost-per–part’ parameters. When we installed the UNIBASE system at the end of 2017, we supplied a management system that enables the customer to calculate the contribution of cutting tool costs to the overall cost-per-part. I am delighted to say that MAPAL is well below the cost-per-part parameters as well as the continuous cost-down expectations of the customer – something that are essential in the global automotive industry.”
Be first to see all the updates from MTDCNC
Our newsletters frequency varies dependant on content
All the latest deals from the industry feature on our newsletters