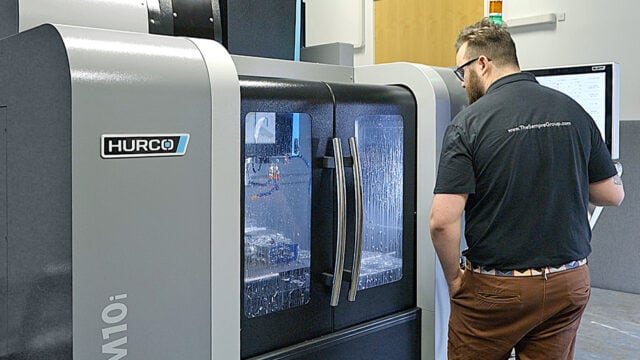
Metrology solutions supplier brings manufacturing in-house with first machine tool purchase
The Sempre Group, a provider of metrology products and services to industries such as aerospace, medical…
Steve Holmes, owner of subcontract machining company Pro-Cut Precision Engineering (www.procutprecision.co.uk), Milton Keynes, founded his business in 2010 and bought a second-hand Hurco VMX30 3-axis vertical machining centre (VMC) to carry out prismatic machining operations.
Today, specialising in a mixture of prototyping and small batch work as well as longer production runs, he has on the shop floor seven modern machines from the same supplier. One of the most recent additions was the first full 5-axis model on site, a trunnion-type VMX30Ui for producing more complex components.
It joined an existing VM30i 3-axis machining centre in an adjacent unit that has benefitted from the addition of a Kitagawa rotary-tilt table with Lang workholding. The machine provides further 5-axis capability while retaining the possibility of using the full 1,270 mm X-axis for processing larger components. When carrying out 5-sided metalcutting operations, the machine is often programmed using Hurco’s powerful transform-plane software in the Max5 control.
Steve advised that the move towards 5-axis was a natural progression for the company and having two different configurations of machine allows him to produce a greater variety of workpiece sizes and shapes. He is impressed with the reliability and performance of the Hurco machines and says they produce components of high accuracy and surface finish.
On-site also are three smaller VM10i 3-axis VMCs, which he described as “absolutely brilliant”, as they run every day for up to 15 hours making production parts for the agricultural industry. “The machines never, ever stop and they don’t go wrong”, he added.
He regards the VM10i models as having a good specification for their size, with 20 tool pockets in the magazine and a 10,000 rpm spindle in addition to such control system features as pocketing cycles, 3D cycles and rigid tapping. Moreover he was able to squeeze all three VMCs as well as the two 5-axis machines into two adjacent 980 sq ft units.
He recently added a further 1,500 sq ft of factory space to start his next expansion phase and in early October 2021 installed another 3-axis VM30i and a larger VMX42Ui 5-axis machine.
Speaking of his first full 5-axis acquisition, Steve said, “Compared with other models on the market, the VMX30Ui can handle surprisingly large sized components, considering the relatively small footprint of the VMC.
“We are happy to machine 5-sided components in 3+2 axis mode or undertake fully simultaneous 5-axis work, the more complex parts presently being required mainly for the motorsport sector.
“Flexibility to be able to serve a variety of customers is key to our business success and the latest, larger capacity 5-axis model will help us further in this respect.”
Pro-Cut has recently added two seats of Open Mind hyperMill CAD/CAM for programming complex work, but the Max5 control on the 3-axis machines and the WinMax twin-screen control on the latest 5-axis model are used for creating cycles for simpler work and are regarded as a perfect way of getting into CNC.
With the benefit of having used Hurco machines for more than two decades, including in previous employment, Steve describes the proprietary control as having become better and faster over the years. Its outstanding conversational programming capabilities and the quality of the graphics are nevertheless undiminished.
He concluded, “To keep the spindle’s turning during our longer production runs, all machines have either augers or swarf conveyors that easily manage the build-up of swarf.
“We are known for our fast turnaround of high quality CNC machined components, whatever the batch size, and the inherent reliability of the Hurco machines underpins that reputation.”
Be first to see all the updates from MTDCNC
Our newsletters frequency varies dependant on content
All the latest deals from the industry feature on our newsletters