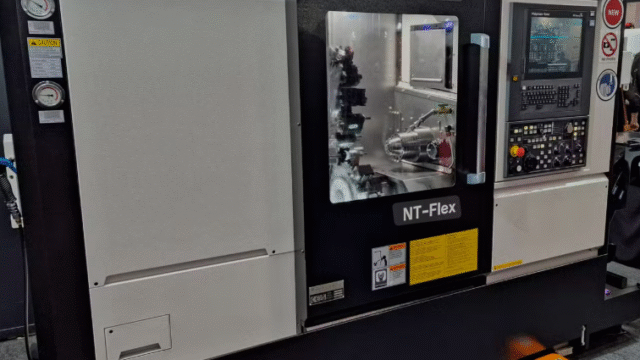
Cut Cycle Times, Make Parts Faster — With Nakamura NT-Flex and ETG’s Expertise
The Nakamura NT-Flex is the latest two-turret, two-spindle multitasking CNC lathe designed to bring “Compact Meets…
Since its inception in 1945, Northern Tool and Gear Ltd (NTG) have been producing high-quality gear at its facility in Arbroath. Nowadays, the company utilises a diverse range of high-end machine tools to manufacture everything from one-off to high-volume production of gears and transmission components – it is here that the company needed to invest in a Mitsubishi MV4800S wire EDM machine from the Engineering Technology Group (ETG).
With a team of upward of 50 staff, NTG manufactures spur, helical, straight and spiral bevel gears, hypoid bevel gears, precision ground gears, specialist bespoke gears, shafts and bevels on the latest CNC machinery to the highest quality standards. Supplying virtually all facets of industry from the renewables, mining, marine, oil and gas, printing and motorsport sectors to name a few, NTG has full CNC gear-checking technology as well as an on-site heat treatment facility to guarantee complete quality control of all projects. However, when it came to EDM machining particular features, the Scottish manufacturer was subcontracting work to external vendors. This led to the arrival of the company’s first wire EDM machine in March 2024.
Recalling the situation, Gordon Strachan from NTG says: “Previously, to produce things like keyways, we would use a broach which is a high-volume process or we would use an old-fashioned slotting machine, which was slow, laborious and it would have quality issues at times. Internal splines, external splines and external gears have dedicated machines for cutting the internal or external splines – these are fast and efficient but they require a lot of tooling and considerable set-up times. In fact, sometimes the tooling would cost more than the job. Now, if the customer needs something in a hurry, we can cut it on the new Mitsubishi wire EDM.”
Looking at the diversity of the gear components that NTG is manufacturing, Gordon adds: “We get approached by major motorsport companies that require specific gears, diff pinions or diff gears for the start of the season with designs that are a change from the previous season. If we are lucky, we have the tooling already and if we are not, we have to source it. Sometimes, the time it takes to procure tooling is more than the time that we have to deliver the job. So, going down the wire-cutting road allows us to meet customers’ expectations and it forewarns us of larger batch volumes that may be in the pipeline. This gives us time to manufacture the tooling in preparation for the pending work. This makes the wire EDM perfect for prototypes and small batches as it helps to get customers up and running quickly.”
Discussing the selection of the Mitsubishi MV4800S wire EDM machine installed at NTG, Gordon continues: “When we first started looking at wire cutting, we were looking at four or five main manufacturers. I cut this list down to two, and we eventually through the graces of Ross from RAM Engineering & Tooling, the Scottish distribution partner for ETG – we selected the Mitsubishi. I had been impressed with the Mitsubishi machines from the start and from visiting machines on manufacturers’ sites, I could see the quality of the product and the technology involved. Everything is state-of-the-art and the control system is very user-friendly. I have had exceptional backup and support from Ross at RAM and the team at ETG from the very beginning, it’s been second to none.”
The particularly large MV4800S machine was selected for its 1080 by 780mm table that can accommodate parts up to 1250 by 1020 by 505mm with a weight of up to 3,000kg. This is perfect for the Scottish company that manufactures hobbed gear components from 50mm to 1200mm. Additionally, the new arrival incorporates technology like automatic wire threading, linear shaft motors and an optical drive system for unparalleled precision and circular accuracy within 1µm. From a user-friendly perspective, the 19-inch screen and the ability for functions to be used in just one touch from the ‘home’ screen helps to reduce operations performed in the navigation menu from setup to machining by almost 40%.
Looking to the future and the potential opportunities for the Mitsubishi MV4800S to make an impact at NTG, Gordon adds: “With the technology and the Mitsubishi control system, it’s very powerful and user-friendly. So, anything we can program on that control system, we can also wire on the part. It gives us immense flexibility, especially if there is a change in specification in any splines and gearing, which is very common. If you don’t have the correct standard of cutter, you can’t use it. You may have the correct pitch and the right size, but it may not have the right profile and this makes it a redundant cutter as far as that job is concerned. However, if we can wire cut it on the Mitsubishi machine, we then have a huge level of flexibility that can also help us to compress lead times.”
Stay up to date with the latest industry news and events.
Be first to see all the updates from MTDCNC
Our newsletters frequency varies dependant on content
All the latest deals from the industry feature on our newsletters