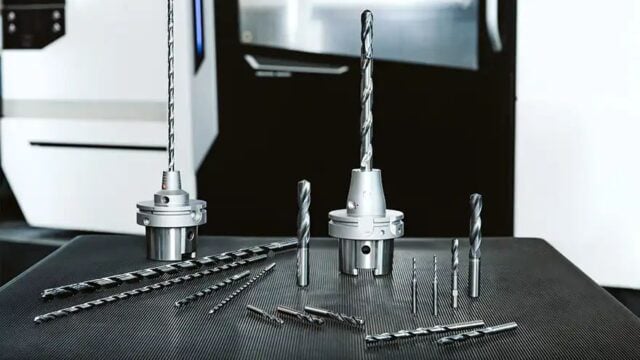
Ceratizit’s New WTX-UNI Drill Range: Precision, Flexibility, and Sustainability Combined
Sheffield-based Ceratizit UK and Ireland Ltd has launched the WTX-UNI range of solid carbide drills, designed…
With one eye on its existing business as a leading manufacturer of thermoforming tools for the food processing sector, and one eye on future opportunities in sectors such as nuclear and aerospace, TMB Patterns is working closely with Ceratizit UK & Ireland through its WNT brand, to develop machining strategies that will radically improve cycle times.
“TMB Patterns has been manufacturing thermoforming tools since 1977, but there are always opportunities to develop processes to improve things for ourselves and our customers,” says Graham Alford Production Manager, TMB Patterns. “Like many companies it is easy to continue to do the same things day in day out, because they work. However, we recognised that there may be better ways and began to develop the relationship with Ceratizit UK & Ireland through WNT Technical Sales Engineer, Iain Tattersall and Applications Sales Engineer Vince (Vinny) Whitham.”
Ceratizit’s team of sales and applications engineers provide customers with on-site support for projects, using their practical experience and detailed knowledge of the WNT range to help implement tooling developments. The initial project that was looked at saw major improvements in cycle time for the machining of large cavities in pressure vessels for mould tools. These large aluminium billets require large volumes of material to be removed, with a typical cavity measuring 420 by 315 by 70 mm deep. Traditionally TMB patterns had used a 50 mm shell mill to rough out these cavities, with a 2mm depth of cut and 35 mm step-over. Rough machining took 33 minutes to complete, then multiple passes with a finishing cutter brought the total machining time to 45 minutes. Reviewing the process Vinny suggested a change to a WNT Circular Line CCR AL end mills with diamond-like coating. Choosing a 20 mm diameter cutter with a 0.2 mm corner radius and 80 mm flute length. With this cutter held in WNT’s positive lock chuck, which has a clamping power of up to 600 Nm of torque, TMB Patterns’ programmers could then switch to a trochoidal milling strategy that allowed full 70 mm depth of cut with a 1 mm step-over. Using the Trochoidal method where a shallow infeed is combined with a high feedrate, 17 m/min in this case, allowed TMB Patterns to maximise the 16,000 revs/min, 32 kW spindle on their Grob G750 five-axis universal machining centre. The result of this switch of cutter and machining strategy was that the part could be rough and finish machined with just one cutter, with the complete process only taking 12 minutes, with an improvement in surface finish.
“We were taken aback at the metal removal rate that we could achieve by using the CCR cutters and Trochoidal milling. It allowed us to fully utilise the capabilities of our Grob five-axis machine’s spindle power and speed,” says Dave Meaker, Programmer, TMB Patterns. “Having Vince from Ceratizit UK & Ireland stood at the side of us while we did this was reassuring, as we were certainly pushing cutters and machine way beyond anything we had done before.” This confidence provided by having an Applications Sales Engineer available for cutting trials was also witnessed on the next project, when TMB Patterns was asked to quote for a job manufactured from titanium, a material it had never machined before. “Vinny stood by the machine and gave us the confidence to run at the speeds and feeds he suggested. As a result of these test cuts we knew we could achieve a good cycle time and quoted accordingly. Without that advice and assistance we probably would have either declined or been to expensive to win the contract.”
The pattern of success and reducing cycle times continues, with the next project calling on the combined knowledge of Ceratizit’s Technical and applications teams in the UK and Ceratizit’s technical centre in Germany. The challenge was to reduce milling times on mould cavities. “The assistance provided by Iain and Vinny has been invaluable and has opened our eyes to the potential of modern cutting tools and techniques. This latest project is a case in point, making use of the latest tooling from WNT,” says Graham Alford. “Iain and Vinny came along, looked at the drawings, and gave their advice. From there they offered to make available the expertise at Ceratizit’s German headquarters in Kempten, where programs were written and test pieces produced to the drawing. They really work with us as a true partnership and are giving us the confidence to go forward and look for work that we would not normally consider.
As a result of this co-operation the existing cycle time for these TMB Pattern mould cavities was dramatically reduced from the original five hours using conventional milling techniques, down to 50 minutes. These parts will be machined on the Grob G750 making use of the full five-axis interpolation provided by the three linear (1000 by 1100 by 1,170 mm in X,Y and Z) and a swivel range of 230 degrees in the A-axis and 360 degrees in the B-axis, which is ideal for this machining strategy. “This partnership with TMB Patterns is typical of what we can provide to customers undertaking new machining projects or looking to develop their machining capability. Our investment in a team of Applications Sales Engineers who have the time to work alongside the existing Ceratizit Technical Sales Engineers is fully justified when you see the results that they can deliver for customers such as TMB Patterns,” Tony Pennington, Managing Director, Ceratizit UK & Ireland.
Be first to see all the updates from MTDCNC
Our newsletters frequency varies dependant on content
All the latest deals from the industry feature on our newsletters