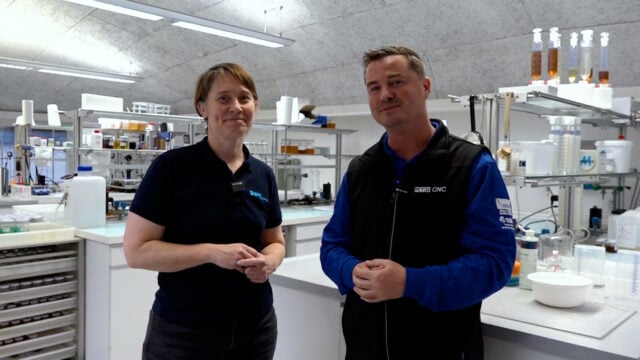
Behind the scenes: How coolant helps you cut better and earn more!
Why should coolant be a top priority for machinists? Simply put – you can’t make things…
Sandvik Coromant, a global leader in cutting tools and tooling solutions, announced the launch of its latest innovation, the CoroCut 2 with RF geometry. This advanced parting and grooving tool is specifically engineered to deliver secure and high-precision profiling, effectively eliminating the traditional trade-off between chip control and optimized surface finish.
The CoroCut 2 with RF geometry is designed to accommodate large-diameter tools and aggressive machining applications, making it ideal for creating blind or through holes in a variety of materials, including mild or stainless steel, light alloys, and superalloys. Constructed from high-speed steel (HSSZ) using a powdered metal process and coated with either Titanium Nitride (TiN) or Red MAXX, the CoroCut 2 offers enhanced durability and extended tool life, meeting the high production demands of today’s manufacturing environments.
One of the standout features of the CoroCut 2 is its ability to provide total indicated runout (TIR) under 3 microns (0.0001″) for tool lengths up to three times the tool diameter (3 × D). Additionally, the toolholder offers length preadjustment with a repeat accuracy of less than 10 microns (0.0004″), ensuring consistent and precise machining results. The incorporation of a special cap nut effectively eliminates cutter pullout during heavy material removal operations, enhancing both safety and reliability.
Fredrik Selin, Product Application Specialist at Sandvik Coromant, emphasized the tool’s advanced capabilities: “The RF geometry combines a sharp edge with a high-precision chipbreaker, making it ideal for finishing operations in ISO S materials, where chip control can be an issue. With this tool, we can meet high demands from the aerospace industry, ensuring both precision and efficiency in critical machining tasks.”
To further enhance chip control for small depths of cuts, the CoroCut 2 employs a chipbreaker geometry positioned close to the cutting edge. This design maintains a sharp insert edge and extends tool life, even when machining challenging materials. The GC1205 grade, recently introduced for parting and grooving operations in aged nickel-based heat-resistant superalloy (HRSA) components, offers enhanced process security and consistent tool life. Featuring a hard, fine-grained substrate and the latest Physical Vapor Deposition (PVD) coating technology, the GC1205 grade provides increased flank wear and notch wear resistance, edge-line security, and reduced tool flaking.
Sandvik Coromant’s innovative rail interface ensures precise insert positioning and resilience against side forces, providing stability in all machining operations. This feature is crucial for maintaining high surface integrity and ensuring the structural integrity of threaded components.
The CoroCut 2 with RF geometry is part of Sandvik Coromant’s commitment to advancing cutting tool technology, offering manufacturers enhanced stability, superior chip control, and improved surface finishes. These advancements enable secure machining with high surface integrity results, making the CoroCut 2 an invaluable tool for industries such as aerospace, automotive, heavy equipment, and general manufacturing.
Stay up to date with the latest industry news and events.
Be first to see all the updates from MTDCNC
Our newsletters frequency varies dependant on content
All the latest deals from the industry feature on our newsletters