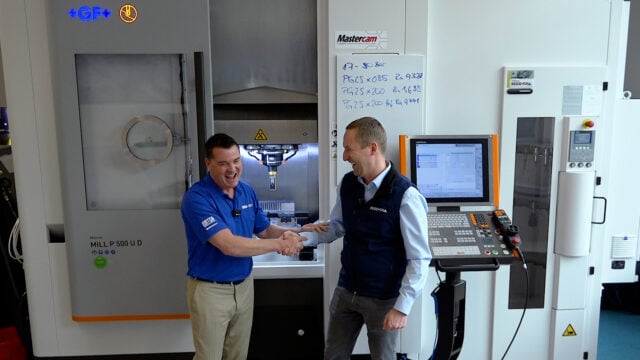
These products can change the way you do things in your machine shop!!
How safe is your toolholder inside the machine? With this new device from Rego-Fix, you can…
KUSUDA Co., Ltd., a venerable name in the manufacturing industry established in 1920, is proud to announce its latest technological advancement with the integration of DMG MORI’s INH 63, a state-of-the-art 5-axis machining center. This strategic move underscores Kusuda’s enduring commitment to innovation, efficiency, and excellence in manufacturing, further solidifying its position as a leader in the industry.
Founded over a century ago, KUSUDA Co., Ltd. began its journey as a casting provider before expanding into the machining sector in the 1980s to enhance business value. Since then, Kusuda has experienced significant growth by developing a unique system that manages the entire production process from casting to machining and direct product delivery. This comprehensive approach has enabled Kusuda to maintain high standards of quality and efficiency, catering to diverse manufacturing needs with precision and reliability.
Kusuda continues to uphold its philosophy of “Unity and Advance,” leveraging its advanced technology, machine tool parts, and castings to contribute directly to the development of the manufacturing industry. A longstanding supplier for DMG MORI, Kusuda has provided various parts such as spindle housings and flanges since the inception of this partnership. Additionally, Kusuda has been a dedicated user of DMG MORI machines since the 1980s, currently operating approximately 40 machines. The introduction of the INH 63 marks a significant milestone in Kusuda’s pursuit of innovation, utilizing DMG MORI’s latest 5-axis machining center to further enhance their manufacturing capabilities.
The INH 63 offers a revolutionary approach to machining by allowing process integration, which drastically reduces the number of setup changes required. Traditionally, handling large or heavy pieces on 3-axis and 4-axis horizontal machining centers involves time-consuming and potentially hazardous setup changes. With the INH 63, Kusuda can integrate multiple processes into a single, streamlined workflow, significantly improving productivity and ensuring higher safety standards for their operators.
Kiyoto Kusuda, Manager of the Sales Department at Kusuda, elaborates, “With large or heavy pieces, setup changes can be dangerous. Consequently, process integration leads to less hazardous work and higher safety for our staff.” The INH 63’s powerful spindle, boasting a standard maximum spindle torque of 808 Nm and a spindle output of 85 / 40 kW (10% ED / cont.), facilitates both heavy-duty and high-speed machining, thereby boosting productivity through increased machining speeds.
To maximize machine utilization and support high-variety production, Kusuda has implemented an 8-station CPP (Compact Pallet Pool) system in conjunction with the INH 63. Kusuda manufactures its own casting materials to closely match the final casting shape, enhancing machining efficiency and reducing lead times compared to machining from block-shaped materials. The ability to run unmanned night shifts with a high number of pallets has further optimized machine utilization. Mr. Kiyoto Kusuda remarks, “Actually, our factory floor space would have limited us to only 6 stations under the standard design, but thanks to DMG MORI’s special design, we were able to install the larger 8-station CPP.”
The INH 63 is equipped with CELOS Chatter Control technology, which automatically optimizes cutting conditions to avoid surface chatter, thereby reducing workload and improving productivity. Additionally, the machine’s tool management system ensures safe machining without overworking the tools, and tool breakage detection mechanisms prevent accidents during night shifts. These features collectively enhance both operational efficiency and workplace safety.
Addressing environmental and maintenance challenges, the INH 63 incorporates the new zero-sludge COOLANT pro, an evolved version of the original zero-sludge coolant tank with high-performance chip cleaning capabilities. This innovation prevents chip accumulation inside the machine, supporting long unmanned operations and reducing the need for frequent tank cleaning. Mr. Kusuda recalls, “Sludge accumulates quickly in the coolant tank because we mainly machine FC casting. In the past, three workers spent a whole day cleaning the tank two to three times a year.”
Furthermore, the built-in zeroFOG mist collector efficiently captures over 99.97% of particles as fine as 0.3 µm, ensuring a clear working environment and preventing mist-related issues. Mr. Yamanaka adds, “Thanks to zeroFOG, the machine is not filled with mist at all and the view is really clear. I can machine without worrying about cutting conditions, which improves production efficiency.” This cleaner environment not only enhances productivity but also promotes better operator health.
Under the visionary leadership of President Yoshinori Kusuda, KUSUDA Co., Ltd. continues to embrace innovation and sustainable production practices. “The INH 63 perfectly embodies our corporate identity: to grow together with our customers through the latest technology, equipment, and services. We believe that the INH 63 and its concept of process integration for high-speed, high-precision machining will be a powerful asset to further promote our unique strength, that is the full in-house casting production from raw material to machined products.”
Kusuda’s decision to adopt the INH 63 was influenced by its exceptional energy-saving performance and the machine’s high rigidity, which enhances machining speed and overall efficiency. “The machine uses a double fixation for the table to achieve high rigidity, and this shows how much the machine has evolved in terms of its basic structure and chip disposal performance. Also, the INH is stylish to look at and greatly motivates our operators,” adds Mr. Kusuda. The integration of the INH 63 has not only boosted productivity but also fostered a more motivated and efficient working atmosphere on the shop floor.
Stay up to date with the latest industry news and events.
Be first to see all the updates from MTDCNC
Our newsletters frequency varies dependant on content
All the latest deals from the industry feature on our newsletters