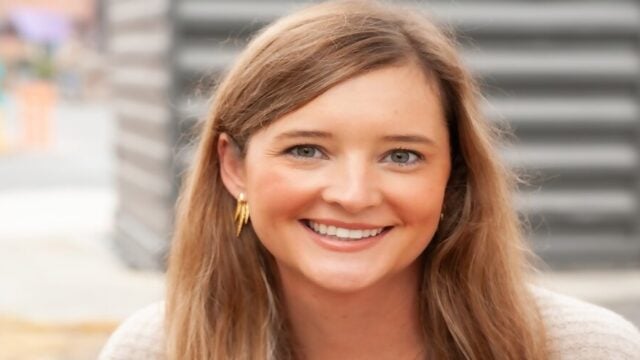
ProShop ERP Appoints Alison Hawkins as New CEO to Focus on Customer-Centric Growth!
ProShop ERP, a leading provider of manufacturing management software, has announced the appointment of Alison Hawkins…
Gear chamfering, a pivotal step in gear manufacturing, entails precision material removal from gear edges to form a chamfer or bevel. This sloping surface facilitates seamless transitions between gear surfaces, safeguarding against potential damage to adjacent parts. Let’s delve into the gear chamfering process and the requisite equipment.
Gear Chamfering Process:
Equipment Used in Gear Chamfering:
Gear chamfering is integral to achieving precision gear manufacturing, ensuring seamless transitions and preventing damage. With diverse methods and specialized equipment like chamfering machines, grinding wheels, milling cutters, and cutting tools, mastering gear chamfering is essential for top-notch gear production.
Original source Cutting World Tools
Stay up to date with the latest industry news and events.
Be first to see all the updates from MTDCNC
Our newsletters frequency varies dependant on content
All the latest deals from the industry feature on our newsletters