Listen here
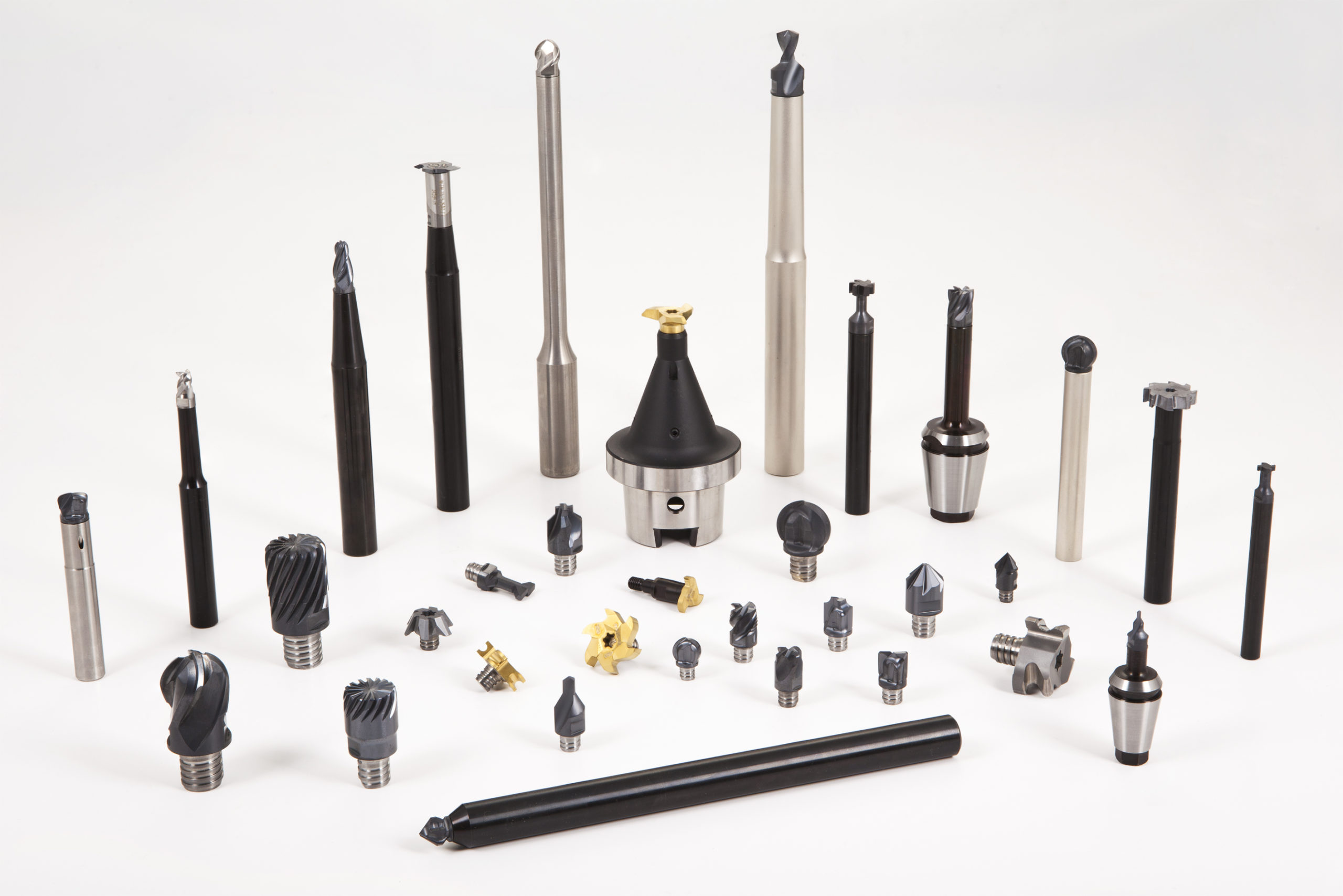
In the metalworking industry, ensuring a high-quality surface finish has always been one of the main focus points in cutting tool development. This is also true for indexable face milling cutters. Despite significant improvements in the high surface quality of milled components, tool designers still believe that available resources have not yet been exhausted and that intelligent applications of the latest generations of advanced milling cutters can substantially improve surface texture further.
When considering an indexable milling cutter, the key factors that determine the quality of a generated surface are the cutterâs geometry and accuracy. Both characteristics are mainly related to inserts carried by the cutter.
Powder metallurgy advancements have enabled the production of carbide inserts with complex shapes to ensure optimal cutting geometries while maintaining substantially increased accuracy of sintered inserts. Not surprisingly, such advancements in technology have significantly improved the surface finish in face milling. However, when indexable milling cutters were successfully applied to machining high-strength materials, and manufacturers started to notice hard milling as an alternative to grinding, the metalworking industry started to demand higher surface finishes through their milling applications â obviously led by the cutting tool.
An indexable face milling cutter is a multi-tooth tool. More teeth = more productivity. This is an undeniable advantage of the cutter. But, in terms of surface texture, a large number of teeth may be a problem. A fine distinction in teeth protrusion leads to irregular feed for the teeth and contributes to chatter, which will ultimately affect the surface finish.
It is perfectly clear that insert accuracy can considerably be increased by grinding. Moreover, grinding provides a sharp cutting edge that is very important in maintaining cutting action and preventing plastic deformation of the metal in fine milling, which features shallow depths of cut. Ensuring a highly accurate cutting edge requires grinding both the top and side surfaces of an insert. This may cancel the advantages of powder metallurgy in generating complicated surfaces to provide the required rake and clearance angles along a cutting edge. To avoid such an adverse impact, tool engineers should be very resourceful when designing the inserts intended for fine grinding.
An important factor regarding the tooth accuracy diminishing is the insert pocket in a cutter that has its own
ring a high-quality surface finish has always been one of the main focus points in cutting tool development. This is also true for indexable face milling cutters. Despite significant improvements in the high surface quality of milled components, tool designers still believe that available resources have not yet been exhausted and that intelligent applications of the latest generations of advanced milling cutters can substantially improve surface texture further.
When considering an indexable milling cutter, the key factors that determine the quality of a generated surface are the cutterâs geometry and accuracy. Both characteristics are mainly related to inserts carried by the cutter.
Powder metallurgy advancements have enabled the production of carbide inserts with complex shapes to ensure optimal cutting geometries while maintaining substantially increased accuracy of sintered inserts. Not surprisingly, such advancements in technology have significantly improved the surface finish in face milling. However, when indexable milling cutters were successfully applied to machining high-strength materials, and manufacturers started to notice hard milling as an alternative to grinding, the metalworking industry started to demand higher surface finishes through their milling applications â obviously led by the cutting tool.
An indexable face milling cutter is a multi-tooth tool. More teeth = more productivity. This is an undeniable advantage of the cutter. But, in terms of surface texture, a large number of teeth may be a problem. A fine distinction in teeth protrusion leads to irregular feed for the teeth and contributes to chatter, which will ultimately affect the surface finish.
It is perfectly clear that insert accuracy can considerably be increased by grinding. Moreover, grinding provides a sharp cutting edge that is very important in maintaining cutting action and preventing plastic deformation of the metal in fine milling, which features shallow depths of cut. Ensuring a highly accurate cutting edge requires grinding both the top and side surfaces of an insert. This may cancel the advantages of powder metallurgy in generating complicated surfaces to provide the required rake and clearance angles along a cutting edge. To avoid such an adverse impact, tool engineers should be very resourceful when designing the inserts intended for fine grinding.
An important factor regarding the tooth accuracy diminishing is the insert pocket in a cutter that has its own dimensional and form tolerances. As a result, even for ideally precise inserts, teeth protrusion will vary within acceptable limits. Although it cannot ensure an extra fine surface finish when compared to grinding. A way to overcome this problem is by using a fly cutter that carries only one insert. The fly cutter that is successfully used in various milling applications facilitates a smooth and clean cut, providing excellent surface texture parameters. But then again, productivity, in this case, is far below multi-tooth indexable face mills.
How do we solve a difficult situation and find an acceptable balance between surface quality and productivity? The cutting tool manufacturer has developed several answers to this challenge.
An integrated wiper flat with a specially shaped minor cutting edge is a classical element of various milling inserts. Its width should be greater than the feed per revolution. Despite being called flat, the minor edge sometimes has a complex geometry to compensate for the negative effect of wear development. When an insert is mounted on a cutter, the wiper flat sits parallel to the machined surface. Hence, the surface will be formed by the most protruding insert of the cutter. Introducing a wiper flat in an insert design is an effective way to improve the surface finish. And even today, rough milling inserts may have an integrated wiper.
ISCARâs DOVEIQMILL family face mill carries double-sided inserts with a wide wiper flat. These tools are intended for rough and semi-rough milling with a surface roughness that usually features semi-finish to finish passes. The DOVEIQMILL cutters have successfully delivered the hopes of their designers â and the adoption of the cutters in various processes has resulted in the cancelling of finish milling operations. The cutters provide a roughness Ra up to 0.4”m (16”in) when milling steel and cast iron.
Increasing the number of teeth in large-diameter face mills and fine pitch cutters determines the appropriate growth of the integrated wiper width, which has a natural bound due to the design and dimensional limitations. In such cases, a high surface finish can be achieved with the use of a specially designed wiper insert (or two inserts for large-sized tools), whereby the wiper flat is significantly wider than the standard one. This insert is mounted in the same pocket but protrudes several tenths of a millimetre axially relative to the standard insert.
Very good results can be reached by applying adjustable milling cutters that utilise different mechanisms to adjust the position of an insert cutting edge within very strict limits (only several microns). But the beneficial adjustability of cutting tools also has a flip side as well; it is spider work, which takes time.
A desirable solution looks like a tool that after mounting an insert has no adjusting requirements needed to achieve high surface quality grade. That is why improving accuracy and advanced geometries remain the mainstream aim in updating indexable cutters for finish face milling.
At the same time, cutting tool manufacturers offer unique solutions that attract attention with their originality. An example is ISCARâs TANGFIN family of milling cutters with tangentially clamped inserts with wide integrated wiper flats. The inserts are positioned in a TANGFIN cutter with a gradual displacement in both radial and axial directions, and therefore, each insert cuts a small section of the machined material providing an extra fine surface finish with roughness Ra up to 0.1ÎŒm (4ÎŒin).
For ensuring a high surface quality in milling relatively small faces, mainly bounded by shoulders, ISCAR has developed dedicated exchangeable solid carbide heads in the diameter range of 12 to 50mm for its MULTI-MASTER and T-FACE families. The heads are fully ground and provide high precision, facilitate a sharp cutting edge and enable a greater number of teeth when compared to mills with indexable inserts of the same diameter. In combination, these features guarantee high-performance and high-quality finish milling.
A tendency to decrease machining allowance due to the active introduction of technologies for precise workpiece production and 3D printing makes the issue of obtaining a high surface finish by face milling particularly relevant. Can toolmakers find a prompt, simple, and effective answer to the new needs of manufacturing?
As well as having concerns over surface finishing, another issue for the modern machine shop is the selection of the right tool for the right application. Like with the surface finish challenge, it can be difficult for manufacturers to determine whether a standard tool or a special tool is preferable. The ideal tool selection is contingent on various factors, such as the nature of the business situation, the manufacturing program, the production type, and sometimes personal preferences. Standard cutting tools, produced by a specific tool manufacturer, offer high versatility and are appropriate for machining a diverse range of parts that come in different shapes.
Furthermore, the tool exhibits excellent performance capabilities when cutting various engineering materials. To ensure seamless production processes, it is crucial to have the cutting tools delivered promptly. This is why standard tools are the foundation of tool stock management on metalworking production floors.
A special cutting tool is designed for specific operations on a particular part, made of a specific material, and used on a machine that requires a specific workholding fixture. This custom-engineered tooling solution aims to provide the best possible performance and outcome. However, there is a downside to this solution as it limits the toolâs versatility, making it less adaptable to different applications. As a result, special tools are primarily used for high-volume mass production, especially in the automotive industry.
Special tools vary in their design complexity. Some are simple modifications of standard tools, such as changes to the corner radius or tool length. These modifications fall under the category of âsemi-standardâ products, which can be manufactured relatively quickly. The design complexity of a special tool is determined by a pre-design study that assesses the customerâs manufacturing limitations, accompanied by cost calculations and production time. The results of the study determine the limits and cost-effectiveness that correlate to the special toolâs delivery time. However, there are additional ways to reduce the delivery time of special tools, such as using solid tools with exchangeable heads, bodies of indexable cutters, or replaceable inserts. The tool manufacturerâs delivery times and production abilities play a significant role in the final decision on how to proceed.
One alternative to engineered special tools is modular tooling, such as ISCARâs MULTI-MASTER. It features rotating tools with exchangeable solid carbide heads. This tooling system includes a wide range of tool bodies, adapters, extensions, and reducers that enable the configuration of the required tool for diverse machining operations.
Additive manufacturing also presents new opportunities for special tool solutions. This technology allows for the quick production of tools with complex profile designs. Although finish cutting and grinding operations are still necessary, the fast manufacturing of pre-shaped products that are very close to a final shape is fascinating. Additionally, 3D printing can be used to fabricate carbide inserts without the need for a die-set, which significantly reduces production time and costs. This process is an excellent way to create insert prototypes during the development stages and produce low-batch special inserts. AM of carbide inserts and heads is gaining momentum and is highly capable of ensuring fast delivery of customised tools and their components.
Milling for high surface finishes
0:00 / NaN:NaN