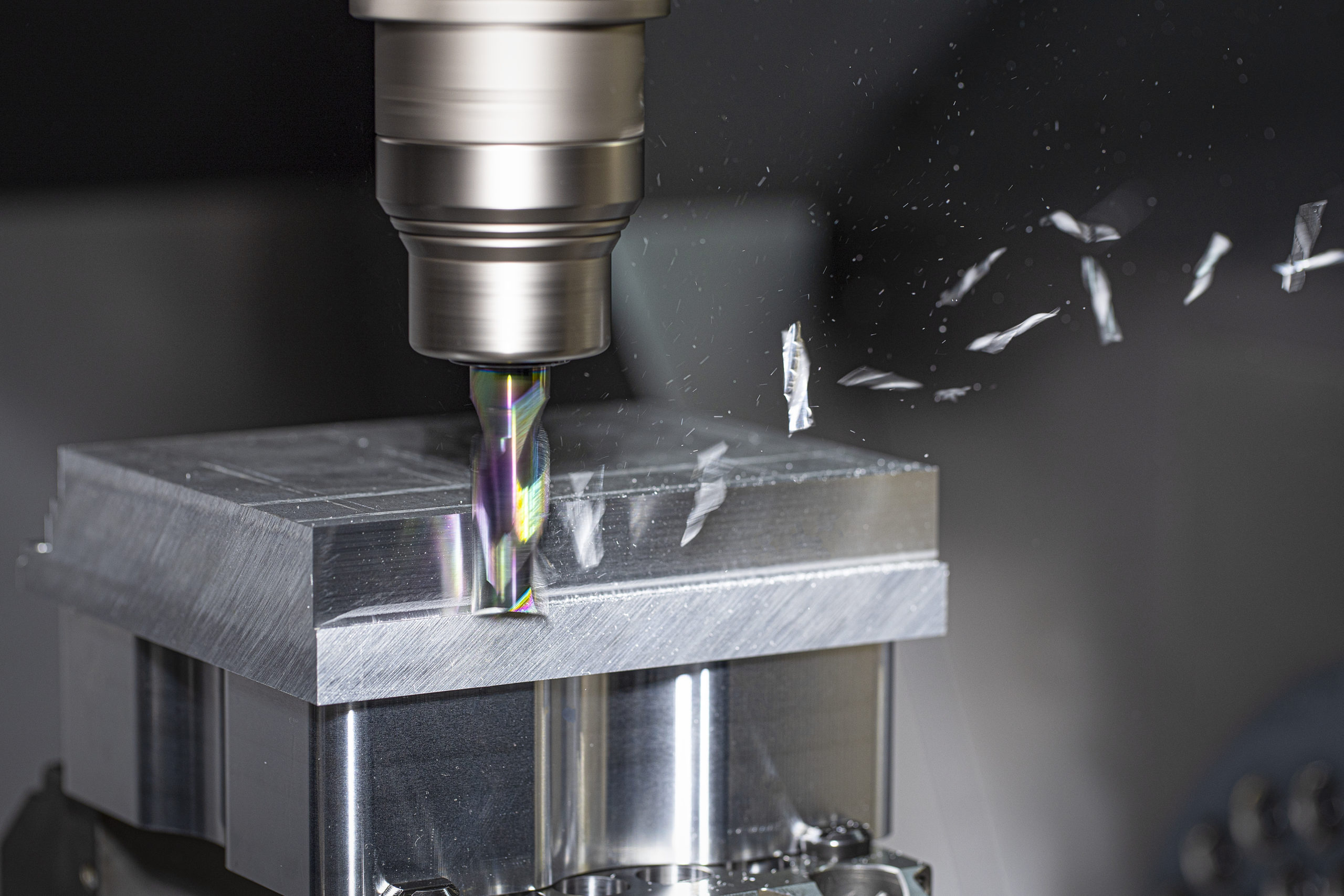
Hofmann & Vratny has now introduced its new EXN1 series of end mills for machining aluminium, plastics and other non-ferrous metals. The ‘EX’ stands for expert, the company’s highest quality level, ‘N’ is the ISO code for non-ferrous materials and ‘1’ stands for version 1.0.
The performance of the series has been successfully confirmed in wide-ranging field tests. The successful launch of the series is reflected not least by the feedback from enthusiastic customers from a wide range of industries from the food and automotive industry to the aerospace sector.
The H&V EXN1 series was developed to enable potentially easily machinable materials to be safely processed and meet the specific requirements of non-ferrous cutting. In the development of the new expert series, the focus was on increasing tool life, surface quality and process reliability. The milling cutters have a special cutting-edge preparation with a defined edge rounding that ensures homogeneous cutting edges.
The manufacturing tolerances for radius and concentricity have been optimised to a maximum of 0.003mm to 0.005mm to ensure the best possible accuracy. The new geometry with a refined grinding pattern and micro cutting edge ensures a sharp cut and excellent chip removal. The milling cutters are completed by using a fine-grain substrate specially designed for machining non-ferrous materials. The portfolio includes 35 product groups and 645 individual products that consist of end mills, roughing, finishing and trochoidal mills, single flute, torus and full radius mills and micro-milling cutters with diameters from 0.1mm to 20mm.
The test phase has shown that it is possible to reduce production times by switching to the H&V EXN1 series and with the use of the new Performmaker endmill, one customer was able to reduce production time per component by more than 50% – a result achieved through larger infeed’s and higher feed rates. Likewise, the use of the new Mirrormaker (finishing cutter) improved the surface quality on the machined parts to a roughness of less than 1 micron.
To optimise the surface quality and minimise built-up edges when using the milling cutters, an innovative coating of tetragonal carbon has also been designed. This novel coating process increases the sp3 bonds to over 85%, reduces the coating thickness to less than one micron and lowers the coating hardness to near 4500HV. In addition, the coating is characterised by a very high smoothness, as it forms almost no droplets and ensures a minimal coefficient of friction.